Полиморфные превращения в железе
Технология конструкционных материалов
Лекция 1. (2 часа)
Введение.
Технология конструкционных материалов представляет собой совокупность современных знаний о способах производства материалов и изготовления изделий различного назначения. Её основные разделы: металлургия, литейное производство, обработка резанием и давлением, сварка и др. Она является частью материаловедения: – науки о связях между составом, строением и свойствами материалов, и закономерностях их изменений привнешних физико-химических воздействиях.
Конструкционными называют материалы, применяемые для изготовления деталей машин, конструкций и сооружений. Все материалы по химической основе делятся на две основные группы: металлические и неметаллические. К металлическим относятся металлы и их сплавы. Металлы составляют около 80% всех известных химических элементов.
В свою очередь металлические материалы делятся на черные и цветные. К черным относятся железо и сплавы на его основе – стали и чугуны. Все остальные металлы относятся к цветным. Чистые металлы обладают низкими механическими свойствами по сравнению со сплавами, и поэтому их применение ограничивается теми случаями, когда необходимо использовать их специальные свойства (например, магнитные или электрические).
Практическое значение различных металлов не одинаково. Наибольшее применение в технике приобрели черные металлы. На основе железа изготавливают более 90% всей металлопродукции. Однако цветные металлы обладают целым рядом ценных физико-химических свойств, которые делают их незаменимыми. Из цветных металлов наибольшее промышленное значение имеют алюминий, медь, магний, титан и др.
|
|
Кроме металлических материалов, в промышленности значительное место занимают различные неметаллические – пластмассы, стекло, древесные материалы, композиционные материалы, резина, лакокрасочные и вспомогательные материалы, керамика и др. Их производство и применение развивается в настоящее время опережающими темпами по сравнению с металлическими материалами. Но использование их в промышленности в качестве конструкционных материалов относительно невелико (около10%) и предсказание того, что неметаллические существенно потеснят металлические, не оправдались.
Общие требования, предъявляемые к конструкционным материалам
Конструкционными называют материалы, применяемые для изготовления деталей машин, конструкций и сооружений.
Для правильного применения материала необходимо знать его механические, физико-химические, технологические и эксплуатационные свойства.
|
|
1.1.Механические свойства
Механические свойства определяют способность материалов сопротивляться воздействию внешних сил (нагрузок). Они зависят от химического состава металлов, их структуры, способа технологической обработки и других факторов. Зная механические свойства, можно судить о поведении металла при обработке и в процессе работы конструкций и механизмов.
1.1.1.Нагрузки, деформации и разрушения.
По характеру действия на тело различают три вида нагрузок: статические – действующие постоянно или медленно возрастающие; динамические – действующие мгновенно, принимающие характер удара; циклические, или знакопеременные, изменяющиеся или по величине, или по направлению, или одновременно и по величине, и по направлению. В результате воздействия на тело нагрузок в нём возникают деформации – изменение его первоначальных форм и размеров. Деформации, исчезающие после снятия нагрузки, называются упругими, а сохраняющиеся – пластичными.
В зависимости от наличия пластической деформации перед разрушением различают хрупкое и вязкое разрушение. Разрушение, перед которым тело испытывает значительную пластическую деформацию, называется вязким. Разрушение, пластическая деформация перед которым отсутствует или незначительна, называется хрупким. Один и тот же материал может разрушаться как по хрупкому, так и по вязкому механизму. Вид разрушения зависит от многих факторов: типа кристаллической решетки, химического состава, формы и размеров детали, наличия надрезов и дефектов, условий и скорости нагружения и особенно от температуры. Для многих материалов вязкое разрушение с понижением температуры сменяется хрупким. Температура изменения характера разрушения называется порогом хладноломкости.
|
|
Чтобы не допустить разрушения и образования остаточных деформаций, необходимо знать механические свойства материала.
К основным механическим свойствам материала относят прочность, твёрдость, упругость, пластичность, ударную вязкость. Прочность – способность материала сопротивляться разрушению под действием внешних сил. Твёрдость – способность материала детали сопротивляться поверхностной деформации под действием более твёрдого тела. Упругость – способность материала возвращать детали первоначальную форму и размеры после снятия нагрузки. Пластичность – свойство материала изменять первоначальную , форму и размеры детали под действием нагрузки, не разрушая её. Ударная вязкость – способность материала сопротивляться разрушению под действием динамической (ударной) нагрузки.
|
|
Для установления характеристик механических свойств материала производят их испытания.
1.1.2. Методы механического испытания.
Статические испытания на растяжение
Для таких испытаний изготовляют круглые или плоские образцы (рис1.1,а, б), форма и размеры которых установлены ГОСТом. Цилиндрические образцы диаметром d0 = 10 мм, имеющие расчётную дину l0 = 10d0, называют нормальными, а образцы, у которых длина l0 = 5d0 – короткими. При испытании на растяжение образец растягивается под действием плавно возрастающей нагрузки и доводится до разрушения.
Испытания проводят на специальных разрывных машинах, которые снабжены самопишущим прибором, автоматически вычерчивающим кривую деформации, называемую диаграммой растяжения.
На рис.1.2 показана типичная диаграмма растяжения в координатах: нагрузка F – удлинение Δl. Эта диаграмма может быть преобразована в диаграмму: напряжение σ – относительное удлинение ε, т.к. напряжение – это величина нагрузки F, отнесённая к площади A0 поперечного сечения образца (σ= F/A0), а относительная деформация при растяжении – отношение удлинения образца Δl к его начальной длине l0 (ε = Δl/ l0). Диаграмма отражает характерные участки и точки, позволяющие определить ряд свойств материала. На участке О-А удлинение образца происходит прямо пропорционально возрастанию нагрузки. При повышении нагрузки свыше Fп на участке А-В прямая пропорциональность нарушается, но деформация остаётся упругой (обратимой). На участке выше точки В возникают заметные остаточные деформации и кривая растяжения значительно отклоняется от прямой. При нагрузке FТ появляется горизонтальный участок диаграммы – площадка текучести C-D.
Такая площадка наблюдается главным образом у деталей, выполненных из пластичных материалов. На кривых растяжения хрупких материалов площадка текучести отсутствует. Выше точки D нагрузка возрастает до точки М, соответствующей максимальной нагрузки FМ, после которой начинается её падение, связанное с образованием шейки (место утонения образца) и разрушением образца. После образования шейки происходит падение нагрузки до точки К, образец удлиняется и происходит его разрушение. С образованием шейки разрушаются только пластичные материалы.
Усилия, соответствующие основным точкам диаграмма растяжения, позволяют установить следующие характеристики сопротивления металла деформации, выраженные в мегапаскалях, МПа:
предел пропорциональности σП – наибольшее напряжение, до которого сохраняется прямая пропорциональность между напряжением и деформацией:
;
предел упругости σу – напряжение, при котором пластические деформации впервые достигают некоторой малой величины, характеризуемой определённым допуском (обычно 0,05%):
;
предел текучести σТ – напряжение, начиная с которого деформация образца происходит почти без дальнейшего увеличения нагрузки (материал течёт):
;
(если площадка текучести на диаграмме растяжения отсутствует, то определяется условный предел текучести σ0,2 – напряжение, вызывающее относительную пластическую деформацию, равную 0,2%);
предел прочности (временное сопротивление) σВ – напряжение, которое равно отношению наибольшей нагрузки, предшествующей разрушению образца, к первоначальной площади его сечения:
.
Пределы текучести и прочности являются обязательными характеристиками в стандартах марок стали.
Показателями пластичности металлов являются относительное остаточное удлинение δ и относительное остаточное сужение ψ.
Относительное остаточное удлинение рассчитывается как отношение удлинения Δl образца после разрыва к его первоначальной расчётной длине , выраженное в процентах,
,
где l – длина образца после разрыва; l0 – расчётная (начальная) длина образца.
Относительное остаточное сужение определяется отношением уменьшения площади поперечного сечения образца после разрыва к первоначальной площади его поперечного сечения, выраженное в процентах,
,
Здесь А0 – начальная площадь поперечного сечения образца; А – площадь поперечного сечения образца в месте разрушения.
1.1.3. Методы определения твёрдости. Определение твёрдости получило широкое применения в производственных условиях представляя собой наиболее простой и быстрый способ определения механических свойств. Так как для измерения твёрдости испытывают поверхностные слои металла, то для получения правильного результата поверхность детали не должна иметь наружных дефектов (трещин, крупных царапин и т.д.).
Существуют различные методы измерения твёрдости. Остановимся на двух наиболее распространённых методах.
Измерение твёрдости методом Бринелля. Сущность этого метода заключается в том, что в поверхность испытуемого материала вдавливается стальной закалённый шарик диаметром 2,5; 5 или 10 мм под действием нагрузки соответственно 1,87; 7,5 и 30 кН. На поверхности образца остаётся отпечаток, по диаметру которого определяют твёрдость. На практике пользуются специальными таблицами, которые дают перевод диаметра отпечатка в число твёрдости, обозначаемое НВ. Этот способ применяют главным образом для измерения твёрдости незакалённых металлов и сплавов.
Измерение твёрдости методом Роквелла. Измерение твёрдости по этому методу осуществляют путём вдавливания в испытуемы1 материал стального шарика диаметром 1,6 мм или конусного алмазного наконечника с углом при вершине 120º. В отличие от метода Бринелля твёрдость по Роквеллу определяют не по диаметру отпечатка, а по глубине вдавливания шарика или конуса.
Вдавливание производится под действием двух последовательно приложенных нагрузок: предварительной, равной 100 Н, и окончательной (общей) нагрузки, равной, примерно, 1000 Н (шарик), 600 Н (конус) или 1500 Н (конус). Твёрдость определяют по разности глубин вдавливания отпечатков. Для испытания твёрдых металлов необходима нагрузка 1500 Н, а вдавливание стальным шариком нагрузкой 1000 Н производят для определения твёрдости незакалённой стали. Испытание сверхтвёрдых материалов производят алмазным наконечником нагрузкой 600 Н. Глубина вдавливания измеряется автоматически, а твёрдость после измерения отсчитывается по трём шкалам: А, В и С. Твёрдость (число твёрдости) по Роквеллу обозначается следующим образом: HRC (1500 Н), HRA (600 Н), HRB (1000 Н).
Определение твёрдости по Роквеллу имеет широкое применение, так как даёт возможность испытывать мягкие и твёрдые материалы; размер отпечатков очень незначителен, поэтому можно испытывать готовые изделия без их повреждения.
1.1.4. Определение ударной вязкости. Определение ударной вязкости производят на специальном маятниковом копре. Для испытаний применяется стандартный надрезанный образец, который устанавливается на опорах копра. Маятник определённой массы поднимают на высоту Н, отпускают, он падает и разрушает образец, подымаясь с другой стороны на высоту h. Удар наносится по стороне образца, противоположной надрезу. По разности высот H и h определяют работу Р, затраченную на разрушение образца. Ударную вязкость а определяют как отношение работы Р к площади А поперечного сечения образца
.
Для облегчения расчётов пользуются таблицами, в которых для каждого угла подъёма маятника после разрушения образца указана работа удара.
Определение сопротивления усталости. Многие детали машин в процессе работы, кроме воздействия статических нагрузок подвергаются знакопеременным (циклическим) нагрузкам. В результате длительной службы материал постепенно переходит из пластичного состояния в хрупкое («устаёт»). Это объясняется тем, что знакопеременные нагрузки приводят к образованию в деталях микротрещин, которые постепенно расширяются и ослабляют связь между зёрнами металла, вследствие чего разрушение наступает при меньших напряжениях, чем предел текучести. Способность материала противостоять действию знакопеременных нагрузок называют его выносливостью Пределом выносливости считается наибольшее напряжение, которое материал, не разрушаясь, выдерживает заданное число циклов нагружения. Число циклов может колебаться от 106 до 107.
1.2. Физико-химические свойства.
К физическим свойствам материалов относят плотность, температуру плавления, теплопроводность, тепловое расширение, теплоёмкость, электропроводность, магнитные свойства.
Химические свойства. Химические свойства – это способность материалов противостоять окислению и разрушению под действием внешней среды: влаги, воздуха, кислот и т.д. Химические разрушения под действием указанных факторов называют коррозией.
1.3. Технологические свойства.
Технологические свойства характеризуют способность материала подвергаться обработке различными способами (литьём, давлением, сваркой, резанием). Сплавы, предназначенные для получения деталей литьём, называются литейными. Сплавы, предназначенные для получения деталей обработкой давления, называются деформируемыми.
Литейные свойства материалов характеризуют их способность образовывать отливки без трещин, раковин и др. дефектов. Основными литейными свойствами является жидкотекучесть, усадка, трещиностойкость, газонасыщение.
Деформируемость – способность материала обрабатываться давлением при ковке, штамповке, прокатке и др.
Свариваемость – способность материала образовывать прочное сварное соединении.
Обрабатываемость резанием – способность материала поддаваться обработке резанием.
Технологические свойстваопределяются при технологических испытаниях (пробах), которые дают качественную оценку пригодности материала к различным способам обработки.
1.5. Эксплуатационные свойства.
К эксплуатационным свойствам относятся жаростойкость, жаропрочность, износостойкость, радиационная стойкость, коррозионная и химическая стойкость и др.
Жаростойкость характеризует способность материала сопротивляться окислению в газовой среде при высокой температуре.
Жаропрочность – способность материала сохранять механические свойства при высокой температуре.
Износостойкость – способность материала сопротивляться разрушению его поверхностных слоёв при трении.
Радиационная стойкость – способность материала сопротивляться ядерному облучению.
Вопросы для самопроверки
1. Конструкционные материалы, применяемые в машиностроении, их свойства и виды.
2. Механические свойства. Нагрузки, деформации и разрушения.
3.. Определение основных механических характеристик Статические испытания на растяжение.
4. Определение твёрдости и ударной вязкости.
5. Физико-химические, технологические и эксплуатационные свойства конструкционных материалов.
Лекция 2
Металлы.
2.1. Металлические сплавы
Применение чистых металлов в промышленности крайне ограничено. Их использование не всегда экономически выгодно, часто они не отвечают требуемым свойствам. В металлах не всегда сочетаются одновременно несколько необходимых свойств. Их прочность невысока, имеют высокий коэффициент теплового расширения.
Сплавы в отличие от чистых металлов можно получить почти с любыми заданными свойствами.
2.2. Строение сплавов.
Сплавом называется материал, полученный сплавлением двух или более металлов. Металлический сплав получают сплавлением металлов или преимущественно металлов с неметаллами. При этом металлический сплав обладает комплексом характерных металлических свойств. Вещества, которые образуют сплав, называются компонентами. Компонент, количественно преобладающий в сплаве, называется основным. Сплавы часто называет по основному компоненту: медные, алюминиевые, магниевые и т.д. По числу компонентов различают двухкомпонентные, (двойные) трёхкомпонентные (тройные) четырёхкомпонентные и многокомпонентные сплавы.
Фазой называют однородную часть сплава, характеризующуюся определённым составом и строением и отделённую от других частей сплава поверхностью раздела, при переходе через которую состав или строение вещества изменяется скачкообразно.
Под структурой понимают форму, размер и характер взаимного расположения фаз в сплавах.
Структурными составляющими называют обособленные части сплава, имеющие одинаковые строения с присущими им характерными особенностями. Структурными составляющими могут быть как фазы, так и смеси фаз.
Строение сплава зависит от того, как взаимодействуют между собой компоненты. В расплавленном состоянии в большинстве случаев сплавы представляют собой однородные жидкие растворы, то есть компоненты неограниченно растворяются друг в друге. В твёрдом состоянии компоненты могут никак не взаимодействовать, либо взаимодействовать с образованием твёрдого раствора или химического соединения. Поэтому в сплавах могут образовываться следующие фазы: жидкие растворы, твёрдые растворы, чистые компоненты, химические соединения. По строению в твёрдом состоянии все сплавы подразделяются на три основных типа: механические смеси, химические соединения и твёрдые растворы.
Механическая смесь двух компонентов А и В образуется, если они не способны к взаимодействию или взаимному растворению. Каждый компонент при этом кристаллизуется в свою кристаллическую решётку. Структура таких механических смесей неоднородна, состоит из отдельных зёрен компонента А и компонента В. Свойства механических смесей зависит от количественного соотношения компонентов: чем больше в сплаве данного компонента, тем ближе к его свойствам смеси. Обычно механические смеси образуют металлы, заметно отличающиеся друг от друга по атомному объёму и по температуре плавления. Механические смеси не обязательно состоят из чистых компонентов. Образовывать механические смеси могут также твёрдые растворы и химические соединения.
Химическое соединение образуется, когда компоненты сплава А и В вступают в химическое взаимодействие. Химическое соединение имеет свою кристаллическую решётку, отличную от кристаллических решёток компонентов. Свойства химического соединения резко отличается от свойств образующих его компонентов.
При образовании твёрдого раствора атомы одного компонента входят в кристаллическую решётку другого. Твёрдые растворы могут быть твёрдыми растворами замещения и твёрдыми растворами внедрения. Твёрдые растворы замещения образуются в результате частичного замещения атомов кристаллической решётки одного компонента атомами второго. Твёрдые растворы внедрения образуются, когда атомы растворённого компонента внедряются в кристаллическую решётку компонента-растворителя. Твёрдый раствор имеет однородную структуру, одну кристаллическую решётку. В отличие от химического соединения твёрдый раствор существует не при строго определённом соотношении компонентов, а в интервале концентраций. Различают твёрдые растворы с ограниченной и неограниченной растворимостью. Неограниченная растворимость возможна только в твёрдых растворах замещения, а ограниченная растворимость бывает как в твёрдых растворах замещения, так и твёрдых растворах внедрения.
Полиморфные превращения в железе
Некоторые металлы в зависимости от температуры могут существовать в различных кристаллических формах. Различные формы одного вещества называются полиморфными модификациями. Процесс перехода от одной кристаллической формы к другой называется полиморфным превращением. Полиморфные превращения протекают при определённой температуре. Полиморфные модификации обозначают строчными греческими буквами α, β, γ, δ и т.д.
Большое значение в технике имеют полиморфные превращения (перекристаллизация) в железе. На рис. 2.1 представлена кривая охлаждения чистого железа от расплавленного состояния до комнатной температуры. До температуры 1539ºС железо остаётся жидким. При температуре 1539 ºС начинается кристаллизация и образуется δ-железо, имеющее кубическую объёмно-центрированную решётку; между температурами 1392 и 911ºС происходит перестройка этой решётки в новую модификацию – γ-железо с образованием кубической гранецентрированной решётки. Ниже температуры 911ºС железо переходит в новую форму – α-железо с кубической объёмно-центрированно1 решёткой, отличной от δ-железо расстоянием между атомами . При температуре 768ºС происходит последняя температурная остановка с образованием магнитной формы α-железо, в которой сохраняется объёмно- центрированная решётка. Магнитное превращение при 768ºС не является полиморфным, так как при нём не происходит изменения кристаллической решётки.
Дата добавления: 2018-04-15; просмотров: 682; Мы поможем в написании вашей работы! |
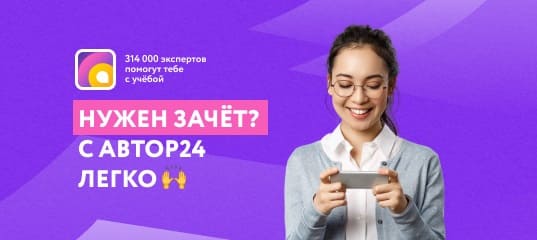
Мы поможем в написании ваших работ!