Особенности изготовления отливок из различных сплавов
Наибольшее количество отливок массой от нескольких граммов до нескольких сотен тонн изготовляют из чугуна. Он имеет высокие литейные и антифрикционные свойства, достаточно высокую прочность и невысокую стоимость. В машиностроении широко распространены чугуны всех модификаций (серый, высокопрочный и ковкий).
Серый чугун характеризуется высокой жидкотекучестью и малой усадкой (0,9…1,2%). Благодаря этому отливки из серого чугуна получаются качественными, без усадочных раковин, пористости и трещин. Минимальная толщинка отливок может доходить до 3…5 мм. Отливки из серого чугуна изготовляют в песчаных формах и специальными методами.
Высокопрочный чугун имеет такую же жидкотекучесть, как и серый чугун, но усадка его более значительна (1,25…1,7%). Отливки могут иметь усадочные дефекты. Отливки из этого чугуна получают теми же способами, что и из серого.
Детали из ковкого чугуна получают путём отжига отливок из белого чугуна, Белый чугун обладает пониженной жидкотекучестью. Поэтому для него необходима повышенная температура заливки. Усадка белого чугуна значительно больше, чем серого, что вызывает образование усадочных раковин, пористости и трещин.
Фасонные стальные отливки из углеродистой стали и из различных легированных сталей разнообразной конфигурации массой от 10 г до 120 т широко применяют в машиностроении. Из стали изготовляется около 20% всех отливок.
|
|
Стальные отливки обладают более высокими прочностью и вязкостью, чем отливки из чугуна. Однако по литейным свойствам сталь уступает чугуну: она имеет большую усадку (до 2,5%), низкую жидкотекучесть. Это приводит к образованию усадочных раковин и пористости в отливках. Маркируются литейные стали как конструкционные, но в конце марки стоит буква Л.
Для изготовления фасонных отливок используют обе главные разновидности медных сплавов – латуни и бронзы. Наилучшими литейными свойствами среди медных сплавов обладают оловянные бронзы (хорошая жидкотекучесть, усадка 1,4…1,6%), но они затвердевают в широком интервале кристаллизации (150…200º С) Это приводит к образованию пористости в отливках. Безоловянные бронзы имеют хорошую жидкотекучесть, но большую усадку (1,6…2,4%), что приводит к образованию усадочных раковин.
Латуни имеют удовлетворительную жидкотекучесть и сравнительно высокую усадку (1,6…2,2%)/
Все медные сплавы склонны к образованию трещин. Около 80% отливок медных сплавов получают литьём в песчаные и оболочковые формы.
Наилучшими литейными свойствами из алюминиевых сплавов обладают силумины марок АЛ2, АЛ4, АЛ9. Они характеризуются хорошей жидкотекучестью, низкой усадкой (0,8…1,1%), узким интервалом кристаллизации; не склонны к образованию трещин.
|
|
Обработка давлением
Обработка давлением основана на способности металлов необратимо изменять свою форму без разрушения под действием внешних сил. Она обеспечивает получение заготовок для производства деталей, а в некоторых случаях и самих деталей требуемых форм и размеров с необходимыми механическими и физическими свойствами.
Обработка давлением – прогрессивный, экономичный и высокопроизводительный способ металлообработки.
Обработке давлением подвергают ~90% всей выплавляемой стали, ~55% цветных металлов и сплавов.
Существуют следующие виды обработки металлов давлением: прокатка, волочение, прессование, ковка и штамповка.
Прокатка, прессование и волочение применяются для получения заготовок постоянного поперечного сечения по длине (прутки, проволока, ленты, листы). Ковка и штамповка применяются для получения заготовок, имеющих приближённо форму и размер готовых деталей.
Пластическая деформация, её влияние на структуру металла. С возникновением остаточных деформаций от удара или давления металл меняет свою форму в желаемом направлении без разрушения. Одновременно происходит изменение структуры металла и его механических и физических свойств. Такое необратимое изменение формы называют пластической деформацией. Для создания пластической деформации металл необходимо подвергнуть напряжениям, которые больше предела упругости, но меньше предела прочности.
|
|
Обработка давлением применима только к сплавам, обладающим достаточной пластичностью, и неприменима к хрупким сплавам, например к чугуну. Давлением обрабатывают сталь, медные, алюминиевые, магнитные и другие сплавы. Этот вид обработки является высокопроизводительным.
Обработку давлением можно производить как в холодном, так и в горячем состоянии. В процессе пластической деформации металла в холодном состоянии вследствие изменения микроструктуры твёрдость и хрупкость металла непрерывно увеличиваются, а пластичность и вязкость уменьшается. Эти изменения свойств называют упрочнением (наклепом). Они могут быть устранены, например, с помощью термообработки (отжига).
Нагрев металла при обработке давлением. Нагрев заготовок производится с целью уменьшить сопротивление деформации. При горячей деформации сопротивление деформированию примерно в 10 раз меньше, чем при холодной. Это позволяет снизить стоимость изготовляемых деталей. Для каждого металла и сплава температура горячей обработки имеет свой верхний и нижний пределы, образующие область нагрева, называемую температурным интервалом обработки.
|
|
Температуры зоны горячей обработки значительно превышают температуру рекристаллизации, поэтому получаемый от механического воздействия наклеп немедленно уничтожается вследствие рекристаллизации и образования новых зерён.
Прокатка –это вид обработки давлением, при котором процесс деформации металла осуществляется сдавливанием его между вращающимися цилиндрами (валками) (рис. 7.1). Сдавливаемый металл вытягивается в продольном направлении, сжимаясь в вертикальном и уширяясь в поперечном. Вследствие возникновения трения между прокатываемым металлом и валками валки одновременно с деформированием осуществляют подачу заготовки до тех пор, пока она полностью не пройдёт в зазор между валками.
Окончательные размеры и форма поперечного сечения полученного прокаткой изделия определяются профилем отверстия между сжимающими металл валками. Прокаткой обрабатываются сталь, цветные металлы и их сплавы.
Прокатку осуществляют на специальных машинах – прокатных станах, устройство которых зависит от вида прокатываемых изделий и их размеров.
Продукцией прокатного производства являются как готовые изделия (например, балки, трубы, рельсы и др.), так и заготовки для последующей обработки ковкой, штамповкой и др.
Волочение и прессование. Особым видом обработки металлов давлением, при котором обрабатываемый металл обычно в холодном состоянии, протягивается через постепенно сужающееся отверстие, является волочение (рис.7.2). При этом сечение отверстия меньше сечения протягиваемой заготовки. Волочением обрабатываются сталь, цветные металлы и их сплавы. Этим способом изготовляют проволоку от 0,002мм, калиброванные прутки и тонкие трубы. Изделия получаются с гладкой поверхностью и точными размерами. Исходными заготовками для волочения может быть сортовой прокат, прутки, трубы. При волочении длина заготовки увеличивается, а поперечное сечение уменьшается и приобретает форму отверстия. Инструментом, через отверстие в котором протягивается заготовка, является волока 2 (рис ). Волока работает в тяжелых условиях, поэтому изготовляются из инструментальной стали или твёрдого металлокерамического сплава, состоящего из карбидов вольфрама, титана, бора и др. При волочении особо тонкой проволоки (диаметром менее 0,2мм) волоку изготовляют из технических алмазов. Для уменьшения трения, усилия волочения и повышения стойкости инструмента применяются жидкие или сухие смазки (минеральное масло, эмульсии, мыло, графит).При волочении может выделяться теплота, поэтому производится охлаждение заготовки.
Если исходное сечение заготовки необходимо уменьшить значительно, то применяют волочение через ряд постепенно уменьшающихся отверстий. Такое повторение может доходить до 20 раз.
Оборудованием для волочения являются волочильные станки.
Прессование. Вид обработки металлов давлением, при котором материал, заключенный в замкнутую полость, выдавливается через отверстие меньшей площади, чем площадь сечения исходной заготовки называется прессованием. Прессуемый металл принимает форму прутка простого или сложного, сплошного или полого сечения по форме и размерам отверстия в матрице (рис.7.3).Заготовка 1 заключена в контейнер. С одной стороны контейнера закреплена матрица 3, через отверстие которой с помощью пуансона 4 выдавливается металл заготовки.
Прессованию подвергают слитки алюминия, меди и их сплавы, а также цинка, олова, свинца и др. Для прессования стальных профилей заготовкой служит прокат. Процесс протекает обычно при температуре горячей обработки давлением.
Прессование – единственный способ обработки давлением, при котором можно обрабатывать специальные стали, цветные металлы и сплавы с низкой пластичностью. Кроме того, прессованием можно получить изделия весьма сложного поперечного сечения, которые не могут быть получены другими видами обработки металлов давлением.
Основной недостаток прессования – значительные потери на отходы металла, так как весь металл не может быть выдавлен из контейнера и в нём остаётся пресс-остаток, масса которого может достигать 40% массы исходной заготовки.
Ковка. Процесс деформирования металла ударами молота или давлением пресса называют ковкой. Ковка всегда осуществляется в горячем состоянии. Полученные ковкой изделия разнообразной формы и массы называют поковками. Заготовками для крупных поковок служат слитки, а для средних и малых – прокатные заготовки. При ковке металл свободно течёт в стороны, не ограниченные рабочими поверхностями инструмента. Заготовка помещается между нижним (неподвижным) и верхним (подвижным) бойками молота или пресса. Контактирующие с заготовкой поверхности бойков и подкладных инструментов определяют направление течения металла заготовки.
Оборудованием для ковки являются молоты, деформирующие металл ударами, и прессы, деформирующие металл статической нагрузкой (без удара).
По способу приведения в движение молоты делят на приводные (механические), работающие от электродвигателя, пневматические и паровоздушные.
Штамповка. Штамповкой называют способ изготовления изделия сложных очертаний давлением с помощью специального инструмента – штампа.
Различают объёмную и листовую, горячую и холодную виды штамповки. При объёмной штамповке в качестве заготовки используется обычно пруток, а металл заполняет всю полость штампа, приобретая её форму и размер. При листовой штамповке заготовкой является лист и толщина полученных плоских и пространственных деталей незначительно отличается от толщины исходного листа.
Объёмная штамповка чаще бывает горячей, а листовая – холодной.
Горячая штамповка. Горячей объёмной штамповкой в специальных штампах из нагретых заготовок получают изделия, называемые штампованными поковками. Штамп – металлическая форма, состоящая обычно из двух частей, в которых имеются полости, по конфигурации соответствующие изготовляемой поковке. Эти полости называются ручьями. Одна часть штампа закрепляется в подштамповой подушке, установленной на шаботе (основание нижней части механического ковочного молота) молота или плите пресса, другая – в подвижной части молота или пресса. Каждый штамп годен для изготовления лишь одной определённой поковки, поэтому штампы применяют преимущественно в крупносерийном и массовом производстве.
Холодная штамповка. Холодной штамповкой изготовляют разнообразные металлические детали из стали, цветных металлов и их сплавов при массовом производстве. Широкое применение холодной штамповки связано с высокой производительностью процесса (30…40 тысяч деталей за смену с одного штампа листовой штамповки), низкой стоимостью, точностью и взаимозаменяемостью деталей, возможностью получения деталей как простой, так и сложной формы. Наибольшую производительность при холодной штамповке обеспечивают автоматические линии.
Черновик
В процессе литейного производства расплавленным металлом заполняется специальная литейная форма. Литейная форма представляет собой систему элементов, образующих рабочую полость, при заливке которой расплавленным металлом формируется отливка. Внутренняя полость литейной формы имеет конфигурацию будущей отливки. Она образуется с помощью вставок в литейные формы, называемыми стержнями. В случае необходимости последующей механической обработкой отливкам придают точные размеры и форму. Во многих случаях литьё – единственный способ изготовления нужных деталей. Особенно это существенно при изготовлении деталей больших размеров и массы, сложной конфигурации, а также в случае, когда сплав (например, чугун) малопластичен и не поддаётся обработке давлением (ковке, штамповке). В машиностроении около 50% всех деталей изготавливают литьём.
Отливки получают различными способами: литьём в песчаные формы, по выплавляемым моделям, в оболочковые формы, в металлические формы (кокили), литьём под давлением, центробежным литьём и др.
Бόльшая часть отливок изготавливается литьём в песчаные формы. Остальные способы получили название специальных способов литья. По количеству заливок литейные формы делятся на разовые и многократные (постоянные). Разовые формы разрушаются при извлечении отливок.
Лекция №8
Сварка, резка и пайка
Дата добавления: 2018-04-15; просмотров: 880; Мы поможем в написании вашей работы! |
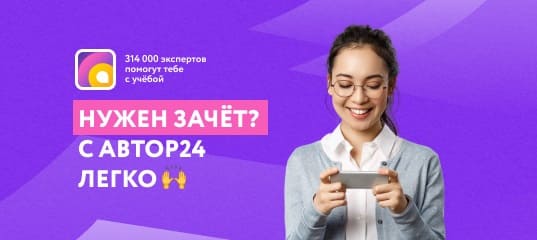
Мы поможем в написании ваших работ!