ОПРЕДЕЛЕНИЕ МЕХАНИЧЕСКИХ ХАРАКТЕРИСТИК ОБРАЗЦОВ ИЗ КОНСТРУКЦИОННЫХ МАТЕРИАЛОВ ПРИ РАСТЯЖЕНИИ
Введение
Вопросы прочности, упругости, пластичности и жесткости материалов занимают важное местов различных областях машиностроении, приборостроенияи прочих отраслях промышленности. Ошибки при определении механических свойств материалов, неудачный выбор материалов для изготовления деталей или конструкций, неправильный расчет деталей машин и механизмов, элементов судостроительных конструкций может привести к их непригодности или разрушению. Следует отметить, что характеристики прочности, упругости и пластичности материалов можно определить только опытным путем.
В лабораторных работахизучаются механические свойства материалов - прочность, пластичность, жесткость, а также определяются некоторые расчетные характеристики. При выполнении лабораторных работ студенты изучают методику испытания материалов, знакомятся с устройством и принципом действия некоторых измерительных инструментов, приборов, испытательных установок и машин.
Навыки, полученные при выполнении лабораторных работ, необходимы инженерно-техническим специалистам в различных областях промышленного производства.
1. ТЕХНИКА БЕЗОПАСНОСТИ
При проведении лабораторных работ по сопротивлению материалов на студентов могут воздействовать опасные для жизни и вредные для здоровья производственные факторы – это электрическое напряжение, подвижные части испытательных машин и установок, острые кромки, заусеницы и шероховатости на поверхности образцов и др. В лаборатории используется оборудование, в электрических цепях которого проходит ток высокого напряжения опасного для жизни человека, а также устновки, имеющими дви-гающиеся рабочие детали, которые являются травмоопасными Для предотвращения травм студент обязан соблюдать следующие основные правила.
|
|
1. Выполнять требования по соблюдению правил техники безопасности.
2. Приступать к выполнению лабораторной работы только после разрешения преподавателя или персонала лаборатории.
3. Студенту запрещается приводить в действие машины, механизмы и другие, находящиеся в помещении лаборатории, установки.
4. Во время выполнения лабораторной работы не отвлекаться, не разговаривать друг с другом и по телефону.
5. В случае обнаружения студентом неисправностей немедленно сообщить об этом преподавателю либо работнику лаборатории.
6. Запрещается производить какие-либо действия с установками, не относящимися к выполняемой лабораторной работе.
7. Студенту запрещается самостоятельно включать рубильники, нажимать на кнопки пульта испытательных машин или осуществлять их компьютерное управление, вставлять вилки приборов в розетки электросети, поворачивать рычаги испытательных установок, заводить руки в опасные зоны испытания.
|
|
8. К лабораторным работам допускаются студенты, ознакомленные инструкцией по охране труда и только после записи в журнал по охране труда.
2. ПОРЯДОК ПРОВЕДЕНИЯ ЛАБОРАТОРНЫХ ЗАНЯТИЙ
1. Перед выполнением очередной лабораторной работы студент обязан теоретически подготовиться по соответствующему разделу курса, используя учебники и пособия.
2. Для выполнения лабораторных работ необходимо иметь бланк протокола лабораторной работы, который следует оформить или ксерокопировать по образцу. Недостаточная подготовка и/или отсутствие бланка протокола лабораторной работы дает право преподавателю не до-пустить студента к занятию.
3. Опоздание или пропуск лабораторных занятий не допускается. Пропущенная лабораторная работа расценивается как невыполнение учебного плана и студент в этом случае не допускается к экзамену или зачету по сопротивлению материалов. В случае пропуска лабораторных занятий студент должен отработать их согласно установленному порядку.
4. В начале занятия под руководством преподавателя и в исполнении хаведующего лаборатории (учебного мастера) проводится испытание образца или демонстрация законов механики на испытательной установке. Студенты обязаны находится на безопасном расстоянии от места испытания и наблюдать за ходом опыта.
|
|
5. После окончания испытания студенты занимают свои места в помещении лаборатории, выполняют обработку полученных данных и оформляют протокол.
6. В конце занятия студент предъявляет преподавателю для проверки оформленный протокол лабораторной работы.
7. В соответствии с графиком проведения занятий студенты защищают лабораторные работы, отвечая преподавателю на поставленные вопросы, давая пояснения установленным законам и закономерностям механики твердого деформируемого тела, принципам работы приборов и испытательных установок.
3. лабораторный практикум
1. Характеристика основных материалов, используемых при проведении лабораторных работ
Чугун. Чугуном называется сплав железа с углеродом, который содержит более 2% углерода. Чугун может быть передельным и литейным. Передельным чугун используется для производства стали, а литейный для литья фасонных изделий. Исходными материалами для доменного производства чугуна являются руда, флюсы, топливо и воздух. Железная руда – это горная порода, содержащая железо в таких количествах, при которых ее технически и экономически целесообразно перерабатывать. Руда состоит из смеси железосодержащих минералов с пустой породой. Для производства чугуна используются руды – магнитный железняк, красный железняк, бурый железняк, шпатовый железняк.
|
|
Обогащение руды. Перед производством чугуна руду обогащают, удаляя пустую породу и повышая содержание железа. Для этого используются два способа – промывку и магнитную сепарацию.
Топливо. Основным видом топлива в доменных печах является кокс. Кокс получается сухой перегонкой некоторых сортов каменного угля при 1000-1200оС без доступа воздуха. Такие сорта угля называются коксующимися. В специальных коксовых печах происходит спекание угля в течение 15-20 ч. При этом удаляются летучие вещества. Предварительно уголь измельчается в дробилках до размера зерен 2-3 мм. Отсутствие летучих веществ и большая пористость кокса обеспечивают высокую температуру его горения. Доменная печь представляет собой вертикальное сооружение шахтного типа. Современные доменные печи имеют общую высоту до 80 м с полезным объемом до 5000 м3.
Плавка чугуна. Агломерат, руда, флюс и кокс, поступающие в печь в определенном соотношении, называют шихтой. Через загрузочное устройство шихта попадает в доменную печь. Доменные печи, как и все шахтные печи, работают по принципу противотока. Сверху сходят шихтовые материалы, а снизу им на встречу движутся газы, образующиеся в процессе горения топлива. В шахте происходят процессы восстановления окислов железа и его науглероживание. В нижней части домны накапливается жидкий чугун, а выше жидкая пустая порода. Их периодически сливают в ковши. Чугун используют для дальнейшей переработки.
Стали.Сталь – это сплав железа с углеродом, который содержит менее 2% углерода (обычно не более 1,3%). Постоянными примесями в стали являются марганец, кремний, фосфор и сера.
Кроме углеродистых, в машиностроении и строительстве широко применяют легированные стали, в состав которых для улучшения тех или иных свойств дополнительно вводят хром, никель, молибден и другие элементы.
Исходными материалами для получения стали служат передельный чугун, стальной лом и ферросплавы. Основная задача передела чугуна в сталь состоит в удалении избытка углерода и примесей с помощью окислительных процессов, протекающих в сталеплавильных агрегатах. Основными способами производства стали являются кислородно-конверторный, мартеновский и элек-тродуговой.
Кислородно-конверторное производство стали. В основе конвертерных процессов лежит обработка жидкого чугуна газообразными окислителями. Кислород под давлением 0,8–1,0 МПа (8–10 атм.) подается сверху через водоохлаждаемую фурму. После окончания продувки и получения заданного содержания углерода берут пробу и сливают металл в ковш. В ковше сталь раскисляется за счет окисления марганца, кремния и алюминия. В зависимости от степени раскисленности различают кипящие, полуспокойные и спокойные стали.
Кипящие стали раскисляются только ферромарганцем. В таких сталях частично остаются растворенные окислы железа. При кристаллизации продолжает идти процесс ―кипения из-за реакции восстановления железа. Газовые пузыри остаются в теле затвердевшего слитка и завариваются при последующей прокатке. Кипящая сталь дает наиболее высокий выход годного металла, наименьшие отходы, благодаря чему она обладает самой низкой стоимостью, но и самым низким качеством. Спокойная сталь раскисляется комплексно ферромарганцем, ферросилицием и алюминием. В металле нет растворенного окисла железа. Процесс кипения прекращается, сталь ―успокаивается‖. Значительная часть стального слитка идет в отход. Поэтому такая сталь, обладая высоким качеством, является наиболее дорогой Полуспокойная сталь раскисляется ферромарганцем и уменьшенным количеством ферросилиция. По качеству и стоимости она занимает промежуточное положение между кипящей и спокойной сталью.
Мартеновское производство стали. Мартеновская печь является пламенной регенеративной печью. В рабочем пространстве печи сжигается газообразное или жидкое топливо. Через завалочные окна в печь загружают шихту и дополнительные материалы по ходу плавки. Через отверстие в задней стене производят выпуск готового металла и шлака.
Если выплавляется легированная сталь, то добавляют легирующие эле-менты – никель, медь, молибден, хром, марганец, кремний, титан, ванадий, алюминий, бор.
Производство стали в электропечах. Электроплавка – наиболее совершенный способ получения стали, имеющей ряд преимуществ по сравнению с производством стали в конверторах и мартеновских печах. Шихта, загружаемая в электропечь, состоит из стального лома, легированных отходов, чугуна флюсов, железной руды, легирующих добавок и рас-кислителей. Нагрев в индукционных печах осуществляется за счет джоулева тепла, выделяемого в твердом или жидком металле вихревыми токами, индуцируемыми переменным электромагнитным полем. Через индуктор, представляющий собой катушку из медной трубки, охлаждаемой внутри водой, пропускают ток, возбуждающий вокруг переменное магнитное поле. В металле, находящемся в тигле, индуцируются мощные вихревые токи, обеспечивающие его нагрев и плавление.
Алюминий. АлюминийAl является химическим элементом серебристо-белого цвета и относится к лѐгким металлам.
Физические, химические и механические свойства. Алюминий сочетает весьма ценный комплекс свойств: малую плотность, высокую теплопроводность и электрическую проводимость, пластичность, хорошую коррозионную стойкость и достаточную прочность. Он легко поддаѐтся ковке, штамповке, прокатке, волочению. Алюминий хорошо сваривается газовой, контактной и др. видами сварки.
Алюминий обладает относительно невысокой прочностью (предел прочности 50-60 МН/м2), твѐрдостью (170 МН/м2 по Бринеллю) и высокой пластичностью (до 50%). При холодной прокатке предел прочности алюминия возрас-тает до 115 МН/м2, твѐрдость ‒ до 270 МН/м2, относительное удлинение снижа-ется до 5% (при σ = 1 МН/м2). Алюминий стоек к действию атмосфернойкоррозии, морской и пресной воды, практически не взаимодействует с концентрированной или сильно разбавленной азотной кислотой, с органическими ки-слотами, пищевыми продуктами.
Алюминиевые руды. В природе имеется большое количество минералов и горных пород, содержащих алюминий, однако лишь немногие из них могут быть использованы для получения металлического алюминия. Наиболее широкое распространение в качестве алюминиевого сырья получили бокситы. Для получения алюминия применяются также нефелин-сиенитовые, нефелин-апатитовые и др. породы.
Получение алюминия. В промышленности алюминий получают электролизом глинозѐма, растворѐнного в расплавленном криолите при темпе-ратуре около 950°С. (Криоли́т — минерал из группы природных фторидов, имеющий хи-мический состав Na3AlF6). Электролитная ванна представляет собой железный кожух, футерованный внутри тепло- и электро-изолирующим материалом – огнеупорным кирпичом, и выложенный угольными плитами и блоками. Рабочий объѐм заполняется расплавленным электролитом, состоящим из 6-8% глинозѐма и 94-92% криолита. Катодом служит подина ванны, анодом - погружѐнные в электролит угольные обожжѐнные блоки или же набивные самообжигающиеся электроды. При прохождении тока на катоде выделяется расплавленный алюминий, который накапливается на подине, а на аноде ‒ кислород, образующий с угольным анодом окислы углерода. Из ванн алюминий извлекают обычно с по-мощью вакум-ковша. Расплавленный алюминий чистотой 99,7% разливают в формы.
Алюминиевые сплавы. В машиностроении используется не сам алю-миний, а его сплавы. Поворотным моментом в развитии алюминиевых сплавов явились результаты исследований А. Вильма (Германия, 1903-11 гг), который обнаружил процесс старения алюминиевых сплавов, приводящее к резкому улучшению их свойств (главным образом прочностных). Этот улучшенный алюминиевый сплав был назван дуралюмином. К самым прочным относятся сплавы алюминево-марганцево-кремневый, алюминиево-цинко-магневый; к наиболее жаропрочным – алюминево-медно-марганцевый; к лѐгким и высокомодульным алюминиево-берилливо-магневый.
Титановые сплавы. В настоящее время титан широко используется в ракетно-космической технике, в судостроении и транспортном машиностроении, где особенно важную роль играют малая плотность в сочетании с высокой прочностью и сопротивляемостью коррозии. Первым потребителем титана стала авиационная промышленность. Применение для изготовления ряда узлов и деталей высокопрочных титановых сплавов вместо алюминиевых позволило создать самолеты, преодолевающие звуковой барьер.
Титан и сплавы на его основе обладают высокой коррозионной стойкостью и удельной прочностью. Недостатки титана: его активное взаимодействие с атмосферными газами, склонность к водородной хрупкости. Азот, углерод, кислород и водород, упрочняя титан, снижают его пластичность, сопротивление коррозии, свариваемость. Титан плохо обрабатывается резанием, удовлетворительно – давлением, сваривается в защитной атмосфере.
Легирующие элементы влияют на эксплуатационные свойства титана (Ре, А1, Мп, Сг), повышают его прочность, но снижают эластичность и вязкость; А1, Zr увеличивают жаропрочность, а Мо, Zr, Та – коррозионную стойкость. Большинство титановых сплавов легировано алюминием, повышающим жесткость, прочность, жаропрочность и жаростойкость материала, а также снижающим его плотность.
Промышленный способ производства титана состоит в обогащении и хлорировании титановой руды с последующим восстановлением из четыреххлористого титана металлическим магнием. Полученная при этом титановая губка маркируется по твердости специально выплавленных из нее образцов. Полученный в результате последовательного дробления губки, прессования, спекания и переплавки брикетов технический титан маркируется в зависимости от содержания примесей.Отличительными особенностями титана являются высокие механические свойства, небольшая плотность и поэтому высокая удельная прочность при 20—25 °С и криогенных температурах, хорошая коррозионная стойкость.
По технологии изготовления титановые сплавы подразделяются на деформируемые, литейные и порошковые.
Деформируемые титановые сплавы применяют для ковки и штамповки заготовок и деталей, воспринимающих и несущих при эксплуатации тяжелые нагрузки при высоких и сверхнизких температурах.Титановые сплавы применяются для изготовления поковок и штамповок ответственных деталей современных двигателей и механизмов, работающих с высокими нагрузками в агрессивных условиях и средах при высоких и очень низких температурах, доходящих до минус 200 С. К ним можно отнести ВТЗ, ВТЗ-1, ВТ4ВТ8 и др.
По сравнению с деформируемыми литейные сплавы имеют меньшую прочность, пластичность и выносливость, но более дешевы. Сложность литья титановых сплавов обусловлена активным взаимодействием титана с газами и формовочными материалами. Литейные сплавы ВТ5Л, ВТ14Л и ВТЗ-1Л по составу в основном совпадают с аналогичными деформируемыми сплавами.
Применение методов порошковой металлургии для производства титановых сплавов позволяет при тех же эксплуатационных свойствах, что и у литого или деформируемого материала, добиться снижения до 50 % стоимости и времени изготовления изделий. Титановый порошковый сплав ВТ6, полученный горячим изостатическим прессованием (ГИП), обладает теми же механическими свойствами, что и деформируемый сплав после отжига. Закаленному и состаренному деформируемому сплаву ВТ6 порошковый сплав уступает в прочности, но превосходит в пластичности.
Основные механические характеристики некоторых материалов
Таблица 1. Некоторые механические характеристики материалов
Материал | Предел прочности, МПа | Предел текучести, МПа | Остаточное удлинение, % | Модуль упругости, ГПа | Коэффициент Пуассона |
Сталь | |||||
Ст2 Ст5 | 320-400 380-470 | 190-220 210-240 | 28 21-23 | 196-206 196-206 | 0,3 0,3 |
Чугун серый | |||||
СЧ21-40 СЧ35-56 | 210 350 | 158 298 | – – | 85 145 | 0,23-0,27 0,23-0,27 |
Чугун ковкий | |||||
КЧ30-8 КЧ37-12 | 300 370 | 190 230 | 6 12 | 155 198 | 0,23 0,36 |
Алюминиевые сплавы | |||||
АМцМ АМг6М | 130 300 | 50 150 | 23 18 | 71 71 | 0,30 0,31 |
Титановые сплавы | |||||
ВТЗ ВТ5 | 930 -1180 690 - 930 | 830 - 1080 590 - 830 | 10 - 16 10 - 15 | 115 105 | 0,30 0,30 |
Другие материалы | |||||
Каучук Стекло Бетон Сосна Дуб | 16-38 30-90 5-48 9,31-11,5 128,8 | – – – 61 74 | 600-700 – – – – | 0,6 10-7 48-75 14,6-23,2 10,2-14,5 7,8-15,1 | 0,47 0,18-0,32 0,16-0,18 0,49 0,43 |
Контрольные вопросы по разделу
1. Какой сплав называется чугуном?
2. Для чего предназначен передельный и литейный чугун?
3. Какие руды используются для производства чугуна?
4. Как происходит обогащение железной руды?
5. Что служит топливом для выплавки чугуна?
6. Как происходит выплавка чугуна в домне?
7. Какой сплав называется сталью?
8. Чем отличаются легированные стали от углеродистых?
9. Какие способы применяют для выплавки стали из чугуна?
10. Как выплавляется сталь конверторно-кислородным методом?
11. Какие недостатки и преимущества имеют кипящая, спокойная и полуспо-койная стали?
12. Как выплавляется сталь мартеновским методом?
13. Как производится сталь в электропечах?
18. Особенность физико-механических свойств алюминия?
19. Какими механическими характеристиками обладает алюминий?
20. Как получают алюминий?
21. Чем отличаются алюминиевые сплавы по своим механическим свойствам?
22. Преимущества и недостатки титановых сплавов.
23.На какие группы подразделяются титановые сплавы.
24. Перечислите основные легирующие элементы сплавов.
ЛАБОРАТОРНАЯ РАБОТА № 1
ОПРЕДЕЛЕНИЕ МЕХАНИЧЕСКИХ ХАРАКТЕРИСТИК ОБРАЗЦОВ ИЗ КОНСТРУКЦИОННЫХ МАТЕРИАЛОВ ПРИ РАСТЯЖЕНИИ
Цель работы
1. Целью испытаний образцов из малоуглеродистой стали и чугуна на растяжение является исследование характера зависимости между деформацией образца и растягивающей силой.
2. Определение механических характеристик материалов.
Используемое оборудование и инструменты:испытательная машинаWDW-100E, штангенциркуль с ценой деления 0,1 мм, измерительная линейка
Испытания на растяжение образцов материалов проводятся сцелью экспериментальногоопределения механических характеристик: предела пропорциональности σпц, предела текучести σт,предела прочностиσв, истинного сопротивления разрыву σ0, относительногоудлинения δ и относительного сужения ψ после разрыва.
Дата добавления: 2018-04-15; просмотров: 332; Мы поможем в написании вашей работы! |
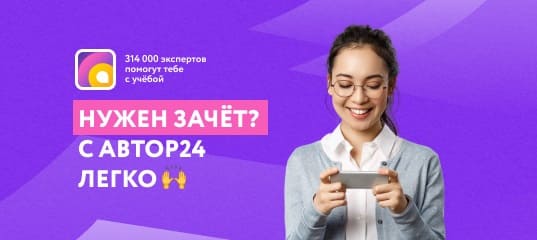
Мы поможем в написании ваших работ!