Figure 5.3. Front panel of LabVIEW program used for PTO calibration.
Torque and Speed channels for the DUT were set up in NI Measurement and
Automation Explorer (NI MAX). This prevented the user from changing the physical channels during testing. In the block diagram (Appendix C), the channels from NI MAX were initialized with the log file information. A while loop allowed the program to continue to run until the Stop control was selected.
Conclusion
The portable data acquisition systems developed as part of the research presented, were successful in measuring hydraulic power, drawbar draft force, and PTO torque with minimal alterations to the tractor. The systems were developed using analog instrumentation to allow for future integration into a single system. Each system could be utilized for implement field tests to collect measurements under field conditions to determine implement load and work cycles. These tests would provide necessary data to support updates to the agricultural machinery standards (ASABE D497.7).
Following this research, the next step of the project is to combine the systems into a single DAQ and collect operational profiles for fieldwork. The most important task in the future is creating a single LabVIEW program to measure and record all three energy flows through the implement interface. An additional system parameter of value to collect is Controller Area Network (CAN) bus data (Stone et al., 2008). Engine speed, fuel consumption, and engine torque provides details on implement load cycles; such as:headland turn load, working load, contour load, and transport load (Pitla et al., 2016).
List of sources used
1. ASABE Standards. (2011). D497.7: Agricultural Machinery Management Data. St. Joseph,
Mich.: ASABE
2. Burgun, C., Lacour, S., Delacroix, A., Descombes, G., and Doyen, V. (2013). Computingtime and fuel requirements to assess efficiency of a field work from conventionallaboratory tests: Application to a plowing operation. Agric. Food Sci., 22(2), 247-261.http://ojs.tsv.fi/index.php/AFS/article/view/7629/6310
3. ISO. 2014a. ISO 500-1: Agricultural tractors - Rear-mounted power take-off types 1, 2, 3, 4– Part 1: General specifications, safety requirements, dimensions for master shield andclearance zone. Geneva, Switzerland: ISO.
4. ISO. 2014b. ISO 500-3: Agricultural tractors - Rear-mounted power take-off types 1, 2, 3, 4– Part 3: Main PTO dimensions and spline dimensions, location of PTO. Geneva,Switzerland: ISO.
5. Pitla, S.K., N. Lin, S.A. Shearer and J.D. Luck. (2014). Use of controller area network(CAN) data to determine field efficiencies of agricultural machinery. Appl. Eng. Agric.
6. Pitla, S.K., J.D. Luck, J. Werner, N. Lin and S.A. Shearer. (2016). In-field fuel use and loadstates of agricultural field machinery. Electronics Agric.
Дата добавления: 2018-04-15; просмотров: 158; Мы поможем в написании вашей работы! |
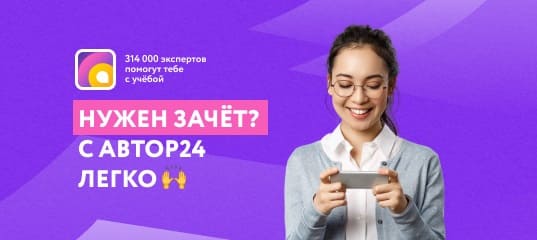
Мы поможем в написании ваших работ!