Виды измельчения. Классификация измельчителей.
Основные требования к качеству измельчения:
- получение продукта заданного зернового состава;
- требуемая удельная поверхность;
- оптимальная конфигурация зерен;
- необходимая прочность.
в производстве строительных материалов измельчение разделяют на дробление и помол. В зависимости от размеров продуктов измельчения, различают виды измельчения, представленные в табл. 5.1.
Виды измельчения
Вид измельчения | Размер кусков, мм | Степень измельчения | |
до измельчения | после измельчения | ||
1 | 2 | 3 | 4 |
Дробление | |||
Крупное | 1500…300 | 300...1000 | 2…6 |
Среднее | 300…100 | 50…10 | 5…10 |
Мелкое | 50…10 | 10…3 | 10…50 |
Помол | |||
Грубый | 10…3 | 3…0,1 | 5…100 |
Тонкий | 3…0,1 | 0,1…0,05 | ![]() |
Сверхтонкий | - | 0,05…0,001 | >100 |
При выборе метода измельчения необходимо учитывать свойства материала, например его склонность к комкованию, влажность и др.
Дробление и особенно помол - весьма энергоемкие операции, на которые расходуется около половины энергии, потребляемой, например, обогатительной фабрикой. Поэтому стремятся в возможно большей степени сократить объем материала, направляемого в эти операции, руководствуясь принципом - не дробить ничего лишнего.
В материалах, подлежащих дроблению или помолу, всегда имеются куски (зерна) мельче того размера, до которого идет измельчение в данной стадии. Такие куски целесообразно выделить из исходного материала перед измельчительными машинами.
|
|
Машины для измельчения (дробления и помола) делят на дробилки и мельницы. Классификация машин для измельчения по конструктивным особенностям приведена на схеме (рис. 5.3).
Рис. 5.3. Классификация дробильно-помольного оборудования
Схемы измельчения.
Рис. 5.2. Циклы измельчения: а - открытый; б – замкнутый
Открытый цикл применяют при крупном и среднем дроблении, когда требования к максимальному размеру зерен нормируются не строго. Измельчение по замкнутому циклу применяют при более высоких требованиях к зерновому составу.
Щековые дробилки. Определение угла захвата.
Рис. 7. Схема щековых дробилок
По характеру движения подвижной щеки— на дробилки с простым (см. рис. 7, а) или со сложным движением (см. рис. 7, б).В дробилках со сложным движением подвижная щека подвешивается на эксцентриковом валу и качается не только около оси вала, но и движется вдоль плоскости щеки.
Определение угла захвата. Чтобы определить предельное значение этого угла, рассмотрим усилия, действующие в щековой дробилке.
Угол между щеками при работе дробилки изменяется (рис. 13) от α до α1вследствие качания щеки относительно линии подвеса. Изменения угла при наибольших удалениях и сближениях захвата щековых дробилок незначительны, поэтому пренебрегаем разностью α— α 1 и принимаем угол захвата равным углу при сближенных щеках.
|
|
При движении подвижной щеки влево (рис. 13, а) на кусок материала массой М действуют сила тяжести Gматериала, сила Р нажатия щеки на кусок материала, силаТтрения куска материала о подвижную плиту, реакция Т1 неподвижной щеки и сила Т, трения куска материала о плиту неподвижной щеки.
а)
Рис. 13. Схема к определению угла
Силой Gпренебрегаем, так как она по сравнению с остальными силами мала.
Силы трения будут равны:
(41)
где f – коэффициент трения материала о щеки.
Составляем условия равновесия относительно осей x и y куска, зажатого между двумя щеками:
(42)
(43)
Находим P, из уравнения (42) и подставляем найденное значение в уравнение (43):
(44)
(45)
Разделив все члены уравнения (44) на Рcos α, получим:
(46)
(47)
(48)
|
|
Коэффициент трения f заменим равной ему величиной тангенса угла φ трения и получим
(49)
поскольку
получим
(50)
(51)
При α=2φ кусок будет находиться в неустойчивом равновесии, следовательно, нужно принимать α<2φ. В этом случае будет устранена возможность выдавливания кусков дробимого материала вверх. Коэффициент трения каменных материалов о сталь f=0,3, при этом φ=16°40', α=33°20 . На практике с целью полной надежности работы угол захвата принимают в пределах 18—22°.
24.Валковые дробилки. Определение угла захвата.
Валковые дробилки классифицируют по следующим трем признакам:
по методу установки валков: дробилки с одной парой подвижных; другой парой неподвижных подшипников; дробилки с подвижно установленными подшипниками;
по конструкции валков: дробилки с зубчатыми валками; дробилки ребристыми валками; дробилки с гладкими валками;
по принципу действия: валковые дробилки, действующие раздавливанием; валковые дробилки, в которых раздавливание сочетается систиранием, раскалыванием или разрыванием материала; валковые дробилки, действующие раздавливанием и частично ударом.
|
|
Дробилки с одним подвижным валком (рис. 26, а) наиболеераспространены.
Рис. 26. Схемы валковых дробилок
Рис. 34. Схема к определению угла захвата и отношения D/d
Определение угла захвата в валковыхдробилках и соотношениямежду диаметром валка и размером поступающего куска. Рассмотрим условия, при которых возможно втягивание куска материала и последующее его дробление. Для простоты расчетов допустим, что поступающие на дробление куски имеют форму шара.
В момент втягивания куска валками действуют следующие силы (рис. 34):
т— масса куска; из-за малой величины она практически незначительно влияет на работу вальцов, поэтому ею можно пренебречь;
Р — давление валков на кусок дробимого материала;
Pf— сила трения (f— коэффициент трения дробимого материала о валки).
Сила Ри вызываемая ею сила Pfдействуют в обеих точках касания (для простоты эти силы показаны на рис. 34 действующими только в одной точке касания).
Кусок дробимого материала втягивается валками при условии
2Pfcosα 2Psinα. (167)
Разделив правую и левую части формулы (167) на 2Рcos α , получаем
(168)
Заменив коэффициент трения f углом трения φ, получим
, (169)
откуда
(170)
Таким образом, для затягивания материала валками необходимо, чтобы угол а, называемый углом захвата, был меньше угла трения. Иногда углом захвата называют угол β образуемый касательными к валкам в точках прилегания куска материала. Нетрудно убедиться, что угол βравен 2α, и тогда
Для определения соотношения между размерами поступающего куска и диаметром валка также воспользуемся схемой, представленной на рис. 34:
(171)
(172)
где D— диаметр валка;
d— диаметр куска;
а— ширина выходной щели.
Преобразуем уравнение (172), разделив правую и левую части его на d:
(173)
Учитывая, что степень измельчения в валковых дробилках принимается в среднем равной 4, можно записать, что a/d=0,25. Сделав необходимые преобразования в уравнении (173), получим
(174)
Коэффициент трения f кусков твердых пород (известняка, песчаника, гранита и т. д.) о поверхность стального валка равен в среднем 0,3, а для кусков влажной глины — 0,45.
При указанных значениях f предельный угол захвата будет равен соответственно 16°40' и 24°20'.
Таким образом, отношение D/dбудет равно:
при дроблении твердых пород
(175)
при дроблении глин карьерной влажности
(176)
Дата добавления: 2018-04-15; просмотров: 3881; Мы поможем в написании вашей работы! |
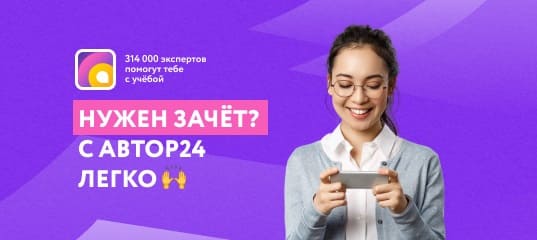
Мы поможем в написании ваших работ!