Дефекты кристаллической решетки. Виды дефектов.
Дефект крист структуры – любое отклонение от ее идеального атомного строения.
Различают точечные, линейные, поверхностные и объемные дефекты структуры. Простейший точечный дефект – вакансия – узел кристаллчической решетки в которой либо отсутствует атом, либо заменен чужеродным. Дислокация – линейные и поверхностные дефекты, т. Е. разориентированные участки крист решетки.
Дефектность кристалл структуры отражается прежде всего на прочности.
Процессы измельчения. Дробление и помол.
Измельчением называется процесс разрушения кусков твердого тела под действием внешних сил с целью уменьшения их размера до величины, необходимой для промышленного использования продукта измельчения.
В зависимости от начальной и конечной крупности кусков различают два основных вида процесса измельчения: дробление (продукт размером более 5 мм) и помол (продукт размером менее 5 мм).
Рис.5.1. Виды нагрузок, используемые при измельчении
В машинах для измельчения материалов в зависимости от их назначения и принципа действия используются следующие виды нагрузок:
а) раздавливание - кусок материала зажимается между двумя поверхностями и раздавливается при сравнительно медленном нарастании давления;
б) удар
в) раскалывание - кусок материала измельчается в результате раскалывающего действия клиновидных тел;
г) излом;
д) истирание - материал измельчается путем трения между движущимися поверхностями или мелющими телами различной формы, а также при трении кусков (частиц) материала друг о друга.
|
|
Свойства материалов, влияющие на процесс измельчения.
Основными свойствами, характеризующими качество материалов, применяемых в ПСМ, являются прочность, разрыхленность, модуль упругости и др. Эти свойства имеют большое значение при определении затрат энергии на измельчение материала.
Прочность - свойство горных пород и материалов сопротивляться разрушению под действием внутренних напряжений, возникающих при приложении нагрузки.
Прочность горных пород характеризуется разрушающим напряжением при сжатии. Материалы по прочности при сжатии делятся на следующие категории:
- мягкие породы- МПа;
- породы средней прочности- МПа;
- прочные породы- МПа;
- особо прочные породы - МПа.
Материалы, обладающие большой прочностью, целесообразно измельчать раздавливанием или ударом, а вязкие - в сочетании излома с истиранием.
Твердость материала характеризует способность горных пород сопротивляться истиранию. Чем выше эта способность, тем более прочен материал.
Хрупкость - способность тел разрушаться при механическом воздействии, без заметной пластической деформации.
|
|
Противоположностью хрупкости является пластичность - способность тел перед разрушением претерпевать значительные пластические деформации.
Разрыхляемость грунтов - свойство горных пород увеличиваться в объеме при их добыче или дроблении.
Показателем разрыхляемое™ является коэффициент разрыхления -отношение объема породы в плотном теле к разрыхленному ее объему
(5.1)
где - объем разрыхленной породы, м3;
- объем породы в твердом теле, м3.
Коэффициент разрыхления скальных пород в зависимости от прочности принимается равным 0,25...0,70.
Абразивность - способность перерабатываемого материала изнашивать рабочие органы машин.
Абразивность горных пород особенно важно знать при определении рациональной области использования оборудования, применяемого для переработки пород. По методике, разработанной ВНИИСтроймашем, абразивность выражают в граммах износа эталонных бил, отнесенных к одной тонне дробленного материала.
По показателю абразивности И, г/т, материалы делятся на:
- неабразивные И 1;
- малоабразивные И = 1...8 (известняк, каменный уголь, мелкозернистый песчаник);
- средней абразивности И = 8...65;
|
|
- высокой абразивности И = 65...500 (гранит, базальт, кварцит, прочный песчаник, известняк высокой прочности);
- очень высокой абразивности И> 500.
Степень измельчения.
Степень измельчения определяется как отношение размеров кусков (зерен) исходного продукта к размеру кусков (зерен) конечного продукта.
(5.2)
где - степень измельчения;
- средневзвешенный размер кусков исходного продукта, м;
- средневзвешенный размер кусков конечного продукта, м.
Средневзвешенный размер куска определяется следующим образом. Смесь материала конечного (или исходного) продукта с помощью сит или решет разделяют на несколько фракций. В каждой из фракций определяется средний размер куска как полусумма размеров максимального и минимального кусков:
, (5.3)
где dmax- средний размер максимального куска, м;
dmin- средний размер минимального куска, м. Средний размер отдельного куска определяется по одной из формул:
или
, (5.4)
где ,
,
- геометрические размеры куска, м.
Затем определяется средневзвешенный размер куска в конечном или исходном продукте:
, (5.5)
где ,
,
,…dср.n, -средние размеры кусков каждой фракции;
|
|
,
,
, …,
-процентное содержание каждой фракции в продукте.
Дата добавления: 2018-04-15; просмотров: 516; Мы поможем в написании вашей работы! |
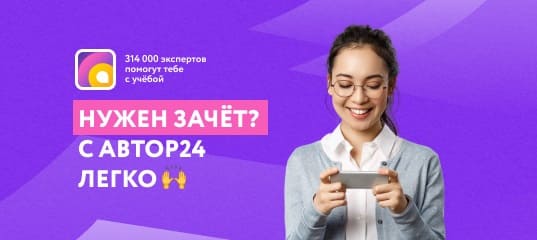
Мы поможем в написании ваших работ!