Выбор рационального способа восстановления изношенных поверхностей детали
При решении вопроса о выборе рационального способа восстановления изношенной детали нужно рекомендовать такой способ, который обеспечивает максимальный срок службы детали, т. е. эксплуатационную надежность, при наименьшей стоимости восстановления, а также учитывать производственные возможности ремонтного предприятия.
Из существующих методик выбора рационального способа восстановления деталей наиболее приемлемой является методика, предложенная профессором В.А.Шадричевым и доктором технических наук М.А.Масино.
Согласно этой методике при выборе способа восстановления деталей руководствуются тремя критериями: применимости, долговечности и технико-экономическим.
Критерий применимости является технологическим критерием и определяет принципиальную возможность применения различных способов восстановления по отношению к конкретным деталям.
По этому критерию предварительно выбирают один или несколько способов восстановления. При этом учитывают условия работы детали, получаемую твердость поверхности, конфигурацию деталей, материал, характер нагрузки, вид трения, величину износа. Этот критерий численной величины не имеет. Области применения способов ремонта деталей по этому критерию приведены в таблицах 1 и 2.
Расшифровка способов восстановления (таблица 2; 3):
РР -обработка под ремонтный размер; ВДН - вибродуговая наплавка; Х -
|
|
электролитическое хромирование; Ж - электролитическое железнение (осталивание); ПД - пластическое деформирование; КП - контактная наплавка (приварка металлического слоя); НФ - наплавка под слоем флюса; НУГ - наплавка в среде углекислого газа; ДМ - дуговая металлизация; ГН - газопламенное напыление; ДР - установка дополнительной ремонтной детали; АДН - аргонно-дуговая наплавка; РН - ручная наплавка; КК - нанесение клеевых композиций; ЭМО - электромеханическая обработка (высадка и сглаживание).
На основании технологических характеристик способов восстановления устанавливаются возможные способы восстановления различных поверхностей детали по технологическому критерию. Так, для приведенного выше примера предварительно устанавливаем, что поверхности оси могут быть восстановлены следующими способами:
поверхность А - контактной приваркой ленты; электромеханической обработкой, вибродуговой наплавкой проволоки; наплавкой в среде углекислого газа,
поверхность Б - контактной приваркой ленты; электромеханической обработкой, вибродуговой наплавкой проволоки; наплавкой в среде углекислого газа;
поверхность В - наплавкой проволоки в среде углекислого газа; вибродуговой наплавкой проволоки.
|
|
Следующим критерием, который выражается в зависимости от способа восстановления определенным числом, является критерий долговечности. Критерий оценивает каждый способ (выбранный по критерию применяемости) устранения дефектов детали с точки зрения восстановления свойств
Таблица 1- Области применения способов ремонта деталей
Способ восстановления | Область применения |
Хромирование Железнение (осталивание) Химическое никелирование Наплавка под слоем флюса без термообработки Наплавка под слоем флюса с последующей термообработкой Наплавка в среде водяного пара Наплавка в среде углекислого газа Вибродуговая наплавка Ручная электродуговая сварка и наплавка Пластическое деформирование Восстановление полимерными материалами | Ремонт деталей с износом до 0,1 -0,3мм и твердостью выше HRC55, требующих повышенной износостойкости (предезионные детали топливных насосов и гидроусилители, валы, оси и т. д.) Ремонт деталей с износом 0,8мм и твердостью доНКС50...55 Ремонт мелких деталей сложной конфигурации с равномерным износом 0,05мм (распылители форсунок и др.) Ремонг деталей с износом более 0,5...0,8мм и диаметром более 50мм. Для получения высокой твердости применяется высокоуглеродистая или легированная проволока (или малоуглеродистая проволока в сочетании с керамическими флюсами) Ремонт деталей твердостью более HRC50 с износом более 0,5...0,8мм и диаметром более 50мм. Целесообразно применять на крупных специализированных предприятиях Ремонт деталей с износом более 0,5... 0,8мм и диаметром более 40мм Ремонт деталей с износом более 0,5мм и диаметром более 10мм, а также тонкостенных деталей и внутренних поверхностей, когда невозможно применять наплавку под слоем флюса Ремонт деталей с износом более 0,8мм и диаметром более 15мм. Не рекомендуется применять для деталей, испытывающих при работе большие знакопеременные нагрузки (коленчатые валы и др.) Заварка трещин и пробоин. Наплавка быстроизнашивающихся поверхностей деталей с высокой твердостью (тарелки толкателей, кулачки распределительных валов и др.) электродами Т-590, Т-620 и др. Ремонт наружных размеров пустотелых деталей раздачей (поршневые пальцы и др.), внутренних размеров обжатием детали (корпуса насосов гидросистем, гладкие и шлицевые втулки и др.), внутренних и наружных размеров осадкой детали (втулка верхней головки шатуна и др.), восстановление ширины шлицев путем раздачи их Заделка трещин и восстановление сопряжений корпусных деталей с подшипниками качения. Склеивание деталей (приклейка фрикционных накладок тормозов, муфт сцепления и др.) |
поверхностей, т.е. обеспечения работоспособности за счет достаточной твердости, износостойкости и сцепляемости покрытия восстановленной детали. Этот критерий дает комплексную качественную оценку, выражающуюся коэффициентом долговечности Кд, который определяется по формуле
|
|
|
|
Кд=Ки ∙Кв ∙Кс (9)
где Ки- коэффициент износостойкости;
Кв- коэффициент выносливости;
Кс- коэффициент сцепляемости.
Численные значения этих коэффициентов представлены в таблице 3.
По физическому смыслу коэффициент долговечности пропорционален сроку службы деталей в эксплуатации, и, следовательно, рациональным по этому критерию будет способ, у которого Кд max.
Так как ресурс восстановленной детали должен обеспечивать нормативный пробег того агрегата, в конструкцию которого входит деталь (не менее 80% от нормы для новых автомобилей и агрегатов), численные значения Кд не должны быть ниже 0,8. Если установлено, что требуемому значению коэффициента долговечности для данной поверхности детали удовлетворяют два или несколько способов восстановления, окончательное решение о целесообразности способа восстановления принимают по технико-экономическому критерию, который связывает стоимость восстановления детали с ее долговечностью после устранения дефектов. Окончательному выбору подлежит тот способ, у которого коэффициент технико-экономической эффективности будет иметь минимальное значение
Ктэ = min
где Св - себестоимость восстановления соответствующей поверхности, руб.
При обосновании способов восстановления поверхностей значение себестоимости восстановления Св определяется из выражения
Св=Су*S, (10)
где Су - удельная себестоимость восстановления, руб/ Д м 2 ;
S - площадь восстанавливаемой поверхности, ДМ2 ,
Таблица 2 - Признаки применимости способов восстановления деталей
Характеристика параметров детали | Условные обозначения способов восстановления | ||||||||||||||
РР | ВДН | Х | Ж | ПД | КП | НФ | НУГ | ДМ | ГН | ДР | АДН | РН | КК | ЭМО | |
Материалы, по отношению к которым применим способ | сталь,чугунСЧ,чугун КЧ | сталь,чугун СЧ,чугун КЧ КЧ | сталь | сталь,чугун СЧ | сталь, цветные сплавы | все материалы | сталь | сталь | сталь,чугун СЧ и др. | все материалы | сталь,чугун и др. | алюминевые сплавы | сталь,чугун, цветные сплавы | сталь,чугун, сплав АЛ-4 | сталь |
Виды поверхностей, по отношению к которым применим способ | наружные и внутренние цилиндрические | наружные цилиндрические, плоские | наружные, внутренние цилиндрические, плоские | наружные цилиндр | |||||||||||
Минимальный наружный диаметр поверхности, мм | 10 | 15 | 5 | 12 | - | 10 | 35 | 15 | 30 | 30 | 6,0 | 5,0 | 10 | не ограничено | 15 |
Минимальный внутренний диаметр поверхности, мм | 10 | 55 | 40 | 40 | не ограничено | 60 | - | - | - | - | 12 | 100 | 40 | 10 | - |
Минимальная толщина покрытия, мм | - | 0,5 | 0,15 | 0,1 | - | 0,1 | 1,5 | 0,5 | 0,3 | 0,3 | - | 0,3 | 1,0 | - | 0,05 |
Максимальная толщина покрытия, мм | - | 3,5 | 0,4 | 2,0 | - | 1,5 | 5,0 | 3,5 | 7,0 | 1,5 | - | 5,0 | 6,0 | 3,0 | 0,15 |
Значения Су для наиболее распространенных способов восстановления, при ведены в таблице 3.
Предварительно отобранные способы восстановления для каждой изнашиваемой поверхности ранжируются по значению коэффициента технико-экономической эффективности и сводятся в таблицу 4.
Для примера в эту таблицу сведены расчеты по технико-экономическому обоснованию восстановления изнашиваемых поверхностей оси колодок ручного тормоза.
Из таблицы видно, что оптимальными способами восстановления изнаши ваемых поверхностей являются следующие:
для поверхности А - электромеханическая обработка;
для поверхности Б - электромеханическая обработка;
для поверхности В - наплавка в среде углекислого газа.
Дата добавления: 2018-04-04; просмотров: 1233; Мы поможем в написании вашей работы! |
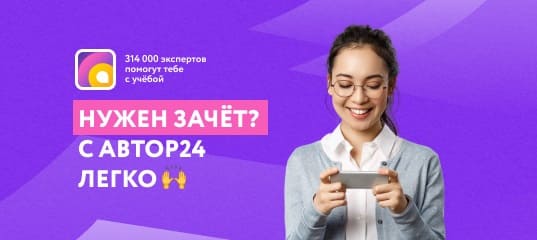
Мы поможем в написании ваших работ!