Проверка передачи винт–гайка на износостойкость
Работоспособность передачи по износу условно оценивается по среднему контактному давлению на рабочих поверхностях витков
, (51)
где d2 – средний диаметр резьбы, мм;
h – рабочая высота профиля резьбы, мм;
zв – число витков;
[р] – допустимое межвитковое давление в резьбе, МПа.
р= =8,01 МПа.
Значения допускаемых давлений [р] для пар винт–гайка из закаленной стали и бронзы составляют 10…13 МПа; незакаленной стали и бронзы 8…10 МПа; незакаленной стали и антифрикционного чугуна 6…7 МПа; незакаленной стали и серого чугуна 4-5 МПа. Для механизмов точных перемещений (делительных и др.) значения [р]принимают в 2-3 раза меньше, чем для механизмов общего назначения.
Проверка винта на устойчивость
Проверка винта на устойчивость осуществляется исходя из неравенства
, (52)
где Fa – осевая нагрузка, Н;
Fкр – критическая сила, определяемая по формуле
, (54)
где Jпр – приведенный момент инерции сечения винта, определяемый по формуле
, (55)
d – наружный диаметр винта, мм;
d1 – внутренний диаметр резьбы винта, мм;
E – модуль упругости, МПа;
m – коэффициент закрепления концов винта (m = 1,5, если винт закреплен по концам шарнирно, и m = 1,0, если винт закреплен консольно);
L =300 – длина винта, мм.
Коэффициент запаса устойчивости
. (56).
Jпр= 2679 Н∙м;
Fкр= =3738693 Н, условие устойчивости выполняется.
nу= =72879.
На рис. 11 показаны варианты конструктивных решений установки невращающейся гайки в корпус.
|
|
Рис. 11 ─ Невращающаяся гайка, установленная в корпус
В механизмах, к которым предъявляются жесткие требования компенсации износа с целью уменьшения «мертвого» хода (зазора между витками винта и гайки), применяют разрезные гайки (рис. 7.3) или специальные устройства (например, пружинные), обеспечивающие радиальную или осевую выборку зазора [3, 8, 9].
Рис. 12 ─ Разрезная гайка, обеспечивающая осевую выборку зазора
Направляющие
Различают направляющие для прямолинейного перемещения с трением скольжения и с трением качения. Конструктивно их выполняют открытыми или закрытыми [2, 3, 8, 9].
Направляющие с трением скольжениябывают с плоскими и с цилиндрическими поверхностями.
На рис. 12 приведены различные примеры конструктивного решения направляющих с плоскими поверхностями.
а |
б |
Рис. 12 ─ Направляющие с плоскими поверхностями:
а – призматические с регулируемой планкой; б – типа «ласточкин хвост»
В цилиндрических направляющих роль направляющего элемента выполняет цилиндрическая поверхность деталей (рис. 13).
|
|
Рис. 13 ─ Цилиндрические направляющие
Выбор материала направляющих
Основными критериями при выборе материалов для деталей направляющих поступательного движения с трением скольжения служат требуемая долговечность механизма и характеристика трения. Для уменьшения износа и сил трения желательно применить различные материалы для ползуна и направляющих планок. Находят применение комбинации материалов сталь–бронза, сталь–латунь, сталь–чугун и т.д., однако для неответственных направляющих возможно и применение одноименных материалов для трущихся поверхностей, при этом желателен перепад твердости, т.е. одна из деталей делается закаленной, другая – незакаленной.
Наиболее часто встречается сочетание сталь–бронза. При невысоких требованиях к износостойкости выбор марки бронзы и стали, а также термообработка стальных деталей не имеют существенного значения. На первый план выступают стоимость и дефицитность бронзы той или другой марки, сталь же применяется со средним содержанием углерода (например, стали 30, 40 или 45 ГОСТ 1050-88).
Направляющие качения
В направляющих качения предусматривают планки с дорожками, заполняемыми телами качения: шариками, роликами или иглами. При перемещениях деталей по этим направляющим тела качения катятся по дорожкам. Тела качения выбирают из применяемых тел в подшипниках качения.
|
|
Основными достоинствами направляющих качения являются малые силы сопротивления движению (меньшие до 20 раз, чем в направляющих скольжения), малая их зависимость от скорости перемещения и незначительная разница между силами трения покоя и движения. В связи с этим на направляющих качения могут быть достигнуты как быстрые, так и весьма медленные равномерные перемещения и установочные перемещения высокой точности.
К недостаткам направляющих качения относят большую сложность изготовления, чем направляющих скольжения, необходимость термической обработки дорожек качения до высокой твердости, повышенные требования к защите от загрязнений.
Направляющие качения применяют, если необходимо:
1) уменьшить силы сопротивления движению для перемещения деталей вручную и для перемещения тяжелых деталей;
2) медленно и равномерно перемещать или точно устанавливать детали;
3) перемещать детали с высокой скоростью.
По форме тел качения направляющие разделяют:
– на шариковые, применяемые при малых нагрузках;
|
|
– роликовые, применяемые при значительных нагрузках;
– игольчатые, применяемые при ограниченных по высоте габаритах и средних нагрузках;
– роликовые на осях, применяемые при малых нагрузках, больших ходах и нестесненных габаритах (обычно в качестве вспомогательных).
По направлению воспринимаемых нагрузок направляющие разделяют на разомкнутые плоские и угловые (рис. 14, а); замкнутые в одной плоскости; замкнутые в двух плоскостях (рис. 14, б–г); цилиндрические.
![]() |
![]() |
![]() |
![]() |
Рис. 14 ─ Направляющие качения, примеры конструкций
Несущая способность роликовых направляющих больше, чем шариковых (с плоскими гранями), имеющих те же габаритные размеры; жесткость больше в 2,5…3,5 раза.
При перемещении деталей по направляющим качения со скоростью υ движение тел качения сводится к поступательному перемещению (вместе с сепаратором) со скоростью υ/2 и к вращению вокруг собственной оси.
Материалы тел качения – подшипниковые стали типа ШХ 15.
Оптимальные материалы направляющих – закаленные до высокой твердости (58…63 HRC) сталь ШХ15, хромистые и другие легированные стали, цементированные на достаточную глубину.
Расчеты направляющих качения производят по формулам Герца. Наибольшее контактное напряжение в шариковых направляющих с плоскими рабочими гранями
(57),
где Q – сила действующая, на наиболее нагруженный шарик;
E – приведенный модуль упругости материала; МПа;
r – радиус шарика, мм.
Конструкцию и типоразмеры направляющих выбирают по справочной литературе [2 ,3].
σН=0,388 =83,59 МПа.
Список литературы
1. Соломахо, В.Л. Приборостроение. Дипломное проектирование: учебное пособие для высших учебных заведений / В.Л. Соломахо, Р.И. Томилин, Л.Г. Юдовин. – Изд. 2, стер. – Минск: Дизайн ПРО, 2002.
2. Справочник конструктора-приборостроителя. Детали приборов / В.Л. Соломахо [и др.] –Минск: Вышэйшая школа, 1990. – 440 с.
3. Анурьев, В.И. Справочник конструктора-машиностроителя:
в 3 т. / В.И. Анурьев. – 6-е изд., перераб. и доп. – М.: Машиностроение, 1982. – Т. 1–3.
4. Решетов, Д.Н. Детали машин: учебник для студентов машиностр. и механич. спец. вузов / Д.Н. Решетов. – Изд. 4-е, перераб.
и доп. – М.: Машиностроение, 1989. – 496 с.
5. Томилин, Р.И. Передачи зубчатые цилиндрические: учебно-методическое пособие: в 2 т. / Р.И. Томилин, Б.В. Цитович. – Минск: БГПА, 1993. – Ч. 2. Разработка эскизного и технического проекта. – 95 с.
6. Зубчатые передачи: справочник / Е.Г. Гинзбург [и др.]; под общ. ред. Н.Г. Гинзбурга. – 2-е изд., перераб. и доп. – М.: Машиностроение, 1980. – 416 с.
7. Скойбеда, А.Т. Детали машин и основы конструирования / А.Т. Скойбеда. – 2-е изд., перераб. – Минск: Вышэйшая школа, 2006. – 560 с.
8. Дунаев, П.Ф. Конструирование узлов и деталей машин: учебное пособие для машиностроительных вузов / П.Ф. Дунаев, О.П. Леликов. – Изд. 4-е, перераб. – М.: Высшая школа, 1985. – 368 с.
9. Орлов, П.И. Основы конструирования: справочно-методическое пособие: в 2 кн. / П.И. Орлов. – М.: Машиностроение, 1988. – Кн. 1, 2.
10. Допуски и посадки: справочник: в 2 ч. / В.Д. Мягков [и др.]. – Л.: Машиностроение, 1983. – Ч. 1. – 543 с.
11. Кудрявцев, В.Н. Детали машин: учебник для студентов машиностроительных специальностей вузов / В.Н. Кудрявцев. – Л.: Машиностроение, Ленингр. отд-ние, 1980. – 464 с.
12. Перель, Л.Я. Подшипники качения. Расчет, проектирование и обслуживание опор: справочник / Л.Я. Перель. – М.: Машиностроение, 1983. – 543 с.
13. Комиссар, А.Г. Уплотнительные устройства опор качения: справочник / А.Г. Комиссар. – М.: Машиностроение, 1979. – 702 с.
14. Лариков, Е.А. Узлы и детали механизмов приборов: Основы теории и расчета / Е.А. Лариков, Т.И. Вилевская. – М.: Машиностроение, 1974. – 328 с.
15. Батанов, М.В. Пружины / М.В. Батанов, Н.В. Петров. – М.: Машиностроение, 1968. – 216 с.
16. Андреева, Л.Е. Упругие элементы приборов / Л.Е. Андреева. – 2-е изд., перераб. и доп. – М.: Машиностроение, 1981. – 392 с.
17. Технологичность конструкции изделия: справочник / Ю.Д. Амиров [и др.]; под. общ. ред. Ю.Д. Амирова. – 2-е изд., перераб. и доп. – М.: Машиностроение, 1990. – 268 с. – (Библиотека конструктора) .
18. Справочник конструктора-приборостроителя. Проектирование: Основные нормы / В.Л. Соломахо [и др.]. – Минск: Вышэйшая школа, 1988. – 272 с.
19. Курмаз Л. В. Детали машин. Проектирование: справочное учебно-методическое пособие/ Л. В. Курмаз, А. Т. Скойбеда. ─ 2-е изд., испр.: М.: Высш. Шк., 2005. ─ 309 с., ил.
Дата добавления: 2018-04-05; просмотров: 82; Мы поможем в написании вашей работы! |
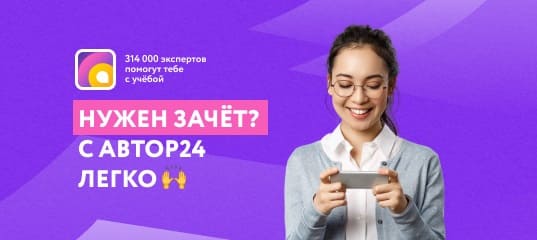
Мы поможем в написании ваших работ!