Подшипники, смазки, уплотнители
5.1. Опоры на стандартных подшипниках качения.
Конструирование и расчет
5.1.1.Конструкции и обозначения
Как правило, опорами для валов в данном курсовом проекте служат подшипники качения.
Опоры на стандартных подшипниках качения нашли самое широкое применение как в машиностроении, так и в приборостроении и освещены в учебной литературе [2, 4, 11, 12].
Подшипники качения нормированы следующими стандартами:
· ГОСТ 3189-89 «Подшипники шариковые и роликовые. Система условных обозначений»;
· ГОСТ 3395-89 «Подшипники шариковые и роликовые. Типы и конструктивные разновидности»;
· ГОСТ 520-2002 «Подшипники качения. Общие технические условия»;
· ГОСТ 3325-85 «Подшипники качения. Поля допусков и технические требования к посадочным поверхностям валов и корпусов. Посадки»;
· ГОСТ 20226-82 «Подшипники качения. Заплечики для установки подшипников качения. Размеры».
5.1.2.Типы и условное обозначение подшипников
Условное обозначениеподшипника состоит из семи цифр (справа налево) (рис. 3).
В обозначении подшипника первые две цифры (1 и 2)определяют внутренний диаметр подшипника следующим образом:
· внутренние диаметры подшипников от 20 мм и болееобозначают частным от деления значения этого диаметра на 5(например, подшипник 305, внутренний диаметр подшипника 25 мм);
· внутренние диаметры подшипников от 10 мм до 17 ммопределяются из табл. 6.1 (например, подшипник 102);
· подшипники с внутренними диаметрами до 9 мм – серия диаметров располагается на 2-м месте, а на 3-м месте стоит цифра «0». В этом случае внутренний диаметр подшипника определяется цифрой на 1-м месте (например, подшипник 1000096).
|
|
Рис. 3 ─ Условное обозначениеподшипника
Таблица 5
Внутренние диаметры подшипников
Внутренний диаметр подшипника, мм | 10 | 12 | 15 | 17 |
Обозначение | 00 | 01 | 02 | 03 |
Серия диаметров может быть сверхлегкая, особо легкая, легкая, средняя, тяжелая.
Тип подшипникаопределяется (табл. 6):
· направлением воспринимаемой нагрузки (радиальный воспринимает нагрузку, перпендикулярную оси вращения подшипника; радиально-упорный воспринимает комбинированную нагрузку; упорный – осевую);
· формой тел качения (шариковый, роликовый).
Таблица 6
Типы подшипников
Тип подшипника | Обозначение |
Шариковый радиальный | 0 |
Шариковый радиальный сферический | 1 |
Роликовый радиальный с короткими цилиндрическими роликами | 2 |
Роликовый радиальный со сферическими роликами | 3 |
Роликовый радиальный с длинными цилиндрическими или игольчатыми роликами | 4 |
Роликовый радиальный с витыми роликами | 5 |
Шариковый радиально-упорный | 6 |
Роликовый конический | 7 |
Шариковый упорный, шариковый упорно-радиальный | 8 |
Роликовый упорный, роликовый упорно-радиальный | 9 |
|
|
Конструктивная разновидность подшипника состоит из двух цифр от 00 до 99.
Серия ширин может быть узкая, особо узкая, нормальная, широкая, особо широкая.
Выбираем шариковый радиальный подшипник лёгкой серии с внутренним диаметром 17 мм.
Классы точности подшипников качения
ГОСТ 520-2002 устанавливает следующие классы точности подшипников качения: нормальный, 6, 5, 4, Т, 2.Установлены дополнительные классы точности(7, 8) для применения по заказу потребителей в неответственных узлах. Нормальный класс точности для шариковых и роликовых радиальных и шариковых радиально-упорных подшипников обозначается «0», для роликовых конических подшипников – «N».
Классы точности подшипников характеризуются значениями предельных отклонений размеров, формы, расположения и шероховатости поверхностей подшипников. Числовые значения данных параметров определяются номинальными размерами и классом точности подшипника.
Поля допусков и посадки подшипников качения
ГОСТ 3325-85 распространяется на подшипниковые узлы машин, механизмов и приборов, посадочные поверхности которых предназначены для монтажа подшипников качения с номинальным диаметром отверстий до 2500 ммпри выполнении следующих условий:
|
|
· валы сплошные или полые толстостенные ( , где d – диаметр внутреннего кольца подшипника, D – диаметр отверстия вала);
· корпуса толстостенные;
· материал валов и корпусов – сталь или чугун;
· нагрев подшипников при работе до 100 °С.
Общее обозначение полей допусков подшипников:
· для среднего диаметра внутреннего кольца подшипника – Ldm;
· для среднего диаметра наружного кольца подшипника –lD m.
Поля допусков колец подшипника обозначаются буквами Lили lпо классам точности, например: L0, L6, …, l5, l4, …
Диаметры наружного и внутреннего колец подшипника приняты соответственно за диаметры основного вала и основного отверстия. Однако поле допуска внутреннего кольца располагается вниз от номинального размера (перевернуто относительно нулевой линии). Такое расположение поля допуска позволяет получать посадки внутреннего кольца подшипника с валами с небольшим натягом без применения дополнительных полей допусков валов, используя основные отклонения n, m, k, js .
Схемы расположения полей допусков при посадках подшипников на валы и в отверстия корпусов представлены на рис. 6.2.
|
|
Выбор посадок внутреннего кольца подшипника на вал и наружного кольца подшипника в отверстие корпуса зависит:
· от вида нагружения кольца подшипника;
· режима работы подшипника;
· соотношения эквивалентной нагрузки Р и динамической грузоподъемности С;
· типа, размера и класса точности подшипника.
Различают следующие виды нагружения колец подшипника:
· местное – М;
· циркуляционное – Ц;
· колебательное – К.
При местном нагружении действующая на подшипник результирующая радиальная нагрузка воспринимается одним и тем же ограниченным участком дорожки качения кольца и передается соответствующему участку посадочной поверхности вала или корпуса.
При циркуляционном нагружении действующая на подшипник результирующая радиальная нагрузка воспринимается и последовательно в процессе вращения передается всей дорожке качения, а следовательно, и всей посадочной поверхности вала или корпуса.
Рис. 4 ─ Схемы расположения полей допусков при посадках подшипников
При колебательном нагружении неподвижное кольцо подшипника подвергается одновременному воздействию радиальных нагрузок: постоянной по направлению и вращающейся, но меньшей или равной по величине первой нагрузке. Равнодействующая этих нагрузок совершает периодическое колебательное движение, которое передается ограниченному участку посадочной поверхности.
Между режимами работы подшипника и соотношениями Р/С установлена зависимость, приведенная в табл. 7:
Таблица 7
Режимы работы подшипника
Режим работы подшипника | Отношение нагрузки к динамической грузоподъемности |
Легкий | Р/С ≤ 0,07 |
Нормальный | 0,07 < Р/С ≤ 0,15 |
Тяжелый | 0,15 < Р/С |
Рис. 5 ─ Шариковый радиальный подшипник
Радиальные шариковые подшипники (тип 0) – наиболее распространенный тип подшипников. Они предназначены для восприятия радиальных нагрузок, но могут воспринимать и осевые. Вследствие точечного контакта тел качения они имеют меньшие потери на трение.
Радиальные роликовые (тип 2) и игольчатые (тип 4) подшипники дают экономию в размерах, обеспечивают более высокую жесткость опор, но не способны воспринимать осевые нагрузки.
Упорные подшипники (тип 8) способны воспринимать только осевые нагрузки. В опорах они устанавливаются совместно с радиальными, обычно в случаях, когда те не способны нести осевую нагрузку или когда осевая нагрузка является превалирующей.
Сферические подшипники (типы 1 и 3) допускают значительные перекосы вала в опорах и применяются либо при невозможности добиться нужной соосности посадочных мест (опоры, установленные в раздельных корпусах), либо при длинных нежестких валах, имеющих большие перекосы сечений на опорах.
Радиально-упорные шариковые (тип 6) и роликовые конические (тип 7) подшипники предназначены для восприятия комбинированных нагрузок, но пригодны для чисто радиальных и чисто осевых. Особенностью этих типов является необходимость обеспечения регулировки зазора по дорожкам качения, что усложняет конструкцию. Одновременно это делает рациональным их применение в опорах, требующих минимальных регулируемых зазоров или даже натягов.
Габаритные размеры подшипников стандартизованы ГОСТ 3478-79 «Подшипники качения. Основные размеры».
5.2. Схемы установки опор, конструктивные элементы,
смазка, уплотнение
Различают две принципиальные схемы установки опор – с одной фиксированной опорой и другой «плавающей» (схема Ф, рис. 6.4) и с подпертыми опорами «враспор» или «врастяжку» (схема Р, рис. 6.4), каждая – с двумя вариантами крепления колец подшипников.
Рис. 6 ─ Конструкция опор
В схеме осевые нагрузки воспринимает фиксированная опора; наличие плавающей опоры необходимо для компенсации неточности продольных размеров и деформаций.
Фиксированной обычно назначают ту опору, которая расположена ближе к функциональному элементу, требующему точного осевого расположения, или же из соображений прочности опор (осевая нагрузка добавляется туда, где радиальная меньше, если это не противоречит принятой схеме или условиям сборки).
Фиксация положения колец на валу и в отверстии может осуществляться с помощью заплечиков. Размеры заплечиков стандартизованы ГОСТ 20226-82 «Заплечики для установки подшипников качения. Размеры» [2, 3, 12].
Галтели, фаски и канавки на валу и в отверстии назначаются в зависимости от координат центра скруглений колец подшипников. Их размеры можно найти в справочной литературе [2, 3, 12].
Смазывание подшипников качения обычно осуществляется той же смазкой, что и передач. В ответственных случаях предусматривается специальный подвод смазки с помощью смазочных устройств.
Данные о свойствах стандартных марок масел и рекомендации по их выбору приведены в [3, 12].
Рекомендации по выбору способа смазки содержатся в литературе [3, 9, 12]. Там же даны и конструктивные решения узлов с различными системами смазки.
В сравнительно быстроходных узлах при скоростном показателе (dn = (20…40)∙104 мм∙об/мин) рекомендуется применять капельную или фитильную систему смазки. При очень высоких скоростях (dn = (150…200)∙104 мм∙об/мин) рекомендуется подача масляного тумана.
При невысоких скоростях (dn = (2…5)∙104 мм∙об/мин) применяется смазывание окунанием (уровень масла – до середины тел качения) или разбрызгиванием (наиболее распространенный способ).
Пластичные смазки рационально вносить в полость узла при сборке, в расчете на периодическую замену при профилактическом уходе за изделием. Более совершенна система направленного продавливания: свежая смазка, подаваемая в полость подшипника под давлением, через зазоры в уплотнении вытесняет отработанную. При конструировании таких систем необходимо предусматривать направление подачи и выхода смазки, исключающее образование застойных зон.
В ответственных опорах применяется автоматическая подача смазки от централизованной системы.
Конструктивные решения узлов с применением консистентных смазок содержатся в литературе [3, 12, 13].
Конструкции смазочных устройств – масленок, насосов, маслораспределителей и др. приведены в [3, 8, 12, 13].
При конструировании подшипниковых узлов особое внимание уделяется их уплотнению, т.к. необходимо обеспечить отсутствие вытекания смазки из полости подшипника и предохранение от попадания влаги и пыли, что часто бывает причиной потери работоспособности опоры.
В настоящем курсовом проекте рекомендуется применять манжетные уплотнения.
Манжета представляет собой выполненное из мягкого упругого материала кольцо с воротником, охватывающим вал. Под действием давления в уплотняемой полости воротник манжеты плотно охватывает вал с силой, пропорциональной давлению. Для обеспечения постоянного натяга воротник стягивают на валу кольцевой пружиной.
Манжеты ранее изготовляли из кожи. В настоящее время манжеты чаще всего изготовляют из пластиков типа поливинилхлоридов и фторопластов, превосходящих кожу по упругости и износостойкости. Поливинилхлоридовые манжеты выдерживают температуру до 80 °С. Фторопластовые манжеты могут работать при температурах до 300 °С.
в машиностроении широко применяют армированные манжеты для валов (рис. 7). Эти уплотнения представляют собой самостоятельную конструкцию, целиком устанавливаемую в корпус; манжету изготовляют из синтетических материалов, что позволяет придать ей любую форму; воротник манжеты стягивается на валу кольцевой витой цилиндрической (браслетной) пружиной строго регламентированной силой.
Манжеты изготовляют прессованием или пресс-литьем (с опрессовкой внутренних металлических элементов) из эластичных, износостойких, масло- и химически стойких пластиков и резины. Браслетные пружины изготовляют из пружинной проволоки диаметром 0,2…0,5 мм и подвергают закалке и среднему отпуску, защищают кадмированием, цинкованием или делают их из бронзы.
а б
Рис. 7 ─ Конструкции армированных манжет
Способы установки манжетных уплотнений в корпусах показаны на рис. 8 При способе установки, показанном на рис. 8, а, соединение с корпусом достигается за счет упругого радиального сжатия манжеты при вводе в корпус, однако соединение получается ненадежное. В конструкции на рис. 8, б уплотнение, предварительно сжатое, вводят в выточку в корпусе; высота буртика у входа в канавку не должна превышать допустимого пробела упругого сжатия манжеты.
а б
Рис. 8 ─ Способы установки манжет
Поверхности, по которым работают манжеты, должны обладать твердостью не менее 45 HRC и иметь шероховатость не более
Ra = 0,16…0,32 мкм.
На рис. 9, а–в показаны три случая установки манжет. Случаях б и в необходимо предупредить возможность просачивания масла по зазору между валом и втулкой (или ступицей насадной детали). Это достигается обработкой торцов а до шероховатости Ra = 0,63…1,25 мкм и соблюдением строгой перпендикулярности торцов относительно оси отверстия. Для обеспечения полной герметичности рекомендуется покрывать торцы герметизирующими мазями или устанавливать на торцах уплотнительные прокладки.
а б в
Рис. 9 ─ Примеры установки манжетных уплотнений:
а – на вал; б – на промежуточную втулку; в – на ступицу насадной детали
На валах, на которые надевают манжету при сборке, должны быть предусмотрены пологие фаски. Это избавляет от необходимости применять специальные монтажные приспособления, например монтажную втулку.
Более подробно конструкции уплотнений, их сравнительный анализ, методика выбора и расчета подробно изложены в литературе [3, 8, 12, 13].
5.3.Требуемая долговечность работы подшипника LN
Номинальная долговечность (ресурс) подшипника в миллионах оборотов
, (43)
где С – динамическая грузоподъемность по каталогу;
Р – эквивалентная нагрузка;
ρ – показатель степени:
для шарикоподшипников ρ= 3.
Номинальная долговечность в часах
, (44)
где С – динамическая грузоподъемность по каталогу;
n – скорость вращения, об/мин.
LN= )3=6764603 млн об.
Lh= =81∙106ч.
Запас долговечности ч. (45)
Можно сделать следующий вывод: срок службы подшипников достаточен.
Материал подшипника ШХ4. Шероховатость Ra0,32 мкм.
Размеры:
d=17 мм, D=30 мм, da=19 мм, Da=21 мм, Ра=27 мм, а=2 мм, b=7 мм по ГОСТ 100058-75.
Передача винт-гайка
Передача винт–гайка представляет собой кинематическую винтовую пару, которую используют для преобразования с большой плавностью и точностью хода вращательного движения в поступательное. Ведущим звеном, совершающим вращательное движение, может быть как винт (рис. 7.1), так и гайка. В силовых механизмах большее распространение получила трапецеидальная резьба
(ГОСТ 9484-81). В механизмах приборов для получения точных перемещений используют метрическую резьбу.
Рис. 10 ─ Передача винт–гайка
Поскольку основным видом разрушения в передачах винт–гайка является изнашивание сопряженных винтовых поверхностей, средний диаметр резьбы обычно выбирают, исходя из критерия работоспособности для совпадающих поверхностей, зависящего от межвиткового давления и допускаемого давления: p£ [р].
Допускаемые давления выбирают исходя из условий работы и материалов винта и гайки, которые должны составлять износостойкую антифрикционную пару.
Кинематика и КПД передачи
Скорость поступательного перемещения V гайки или винта, м/с:
, (46)
где P – шаг резьбы, мм;
n – частота вращения гайки или винта, мин–1;
z – число заходов винта.
V= =0,000002 м/с, n=
=
=60,4 мин–1.
При определении КПД пренебрегают потерями в опорах, и его определяют приближенно как отношение работ на завинчивание винта без учета сил трения (µ = 0 и ρ= 0) и с учетом сил трения (µ ≠ 0 и ρ≠ 0). Тогда, используя зависимость между моментом сопротивления в резьбе и осевой силой, получим
, (47)
где β – угол подъема резьбы, градус; β=7,
ρ – приведенный угол трения в резьбе, градус; ρ=11.
η= =-0,76.
Из этой формулы видно, что КПД передачи возрастает с увеличением угла подъемаβ и уменьшением коэффициента трения µ в резьбе (уменьшением ρ).
Для увеличения угла подъема в механизмах применяют многозаходные винты. Ход резьбы в этом случае S = z · P (P и z – шаг и число заходов резьбы). Однако винты с углом β > 25° на практике не применяют, так как дальнейшее увеличение β не дает существенного повышения КПД, а передаточное отношение при этом снижается. Обычно η ≤ 0,7.
Для повышения КПД механизмов стремятся уменьшить коэффициент трения в резьбе путем изготовления гаек из антифрикционных материалов (бронзы, латуни и др.), смазки и тщательной обработки контактирующих поверхностей.
Средний диаметр винта по условию износостойкости
, (48)
где Fa – осевая нагрузка, Н;
yr – коэффициент высоты гайки; yr=0,9
(Н1 – высота гайки);
x – отношение высоты рабочего профиля резьбы к ее шагу, для трапецеидальной резьбы x = 0,50;
[p] – допустимое давление в резьбе, для материала винтовой пары сталь–бронза [р] = 8…10 МПа.
Fa= =
=51,3 Н;
d2= =2,13 мм.
Берем винт наружным диаметром 16 мм, внутренним 12 мм, шаг резьбы р=2 мм по ГОСТ 24737-81.
Потребное число рабочих витков, определяющих высоту гайки, находят по формуле
, (49)
где Fa – осевая нагрузка, Н;
d2 – средний диаметр резьбы, мм;
h – рабочая высота профиля, мм; d-d2=16-2.13=13.87 мм.
[р]=8 – допустимое давление в резьбе, МПа.
ZB= =0,069.
Высота гайки определяется по следующей формуле:
, (50)
где р – шаг резьбы, мм.
Н1=0,069∙2=0,138 мм.
Ходовые винты изготовляют из высокоуглеродистых сталей 40, 45, 50, 40ХН, 50ХГ, 65Г и др. с закалкой до твердости 40…50 HRC. Гайки изготовляют из оловянистых бронз БрО10Ф1, БрО6Ц6С3 и др. для высоких окружных скоростей (0,1–0,25 м/с), а для малых окружных скоростей используют антифрикционные чугуны марок АВЧ-1, АВЧ-2, АКЧ-1, АКЧ-2 или серые чугуны марок СЧ 15, СЧ 20. Материал ─ сталь 45.
Дата добавления: 2018-04-05; просмотров: 82; Мы поможем в написании вашей работы! |
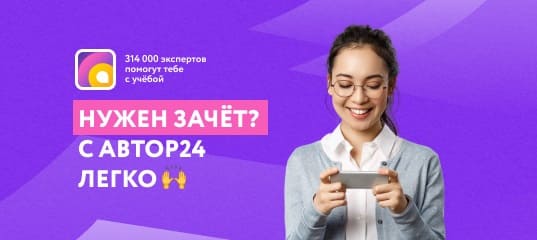
Мы поможем в написании ваших работ!