Выбор материалов зубчатой передачи
Кинематический расчет привода
Выбрать двигатель привода вращающегося стола контрольно-измерительного прибора; определить общее передаточное число привода и произвести его распределение по ступеням .
Исходные данные: момент сопротивления вращению стола Т =
= V = 10 Н∙м, частота вращения стола прибора nст = 60 об/мин.
Решение
Определяем КПД привода.
Значения КПД:
зубчатой цилиндрической пары ηзц = 0,98;
зубчатой конической пары ηзк = 0,97;
пары подшипников качения ηп = 0,99;
. (1)
Требуемая мощность электродвигателя
Вт; (2)
где P – мощность электродвигателя, Вт;
Tc – момент сил сопротивления на выходном валу редуктора, Н∙м;
ωс – номинальная угловая скорость выходного вала, с–1;
Kдин – коэффициент запаса, учитывающий необходимость преодоления динамических нагрузок в момент разгона. Если в задании не оговорено время переходного процесса, обычно принимают Kдин = 1,05…1,10;
η – коэффициент полезного действия привода, равный произведению частных КПД передач, входящих в кинематическую схему.
ω= =
=6,28 с-1. (3)
где ω – угловая скорость, с–1;
nст – частота вращения стола, об/мин.
По таблице [2] выбираем двигатель серии 4А с номинальной мощностью
Pном = 90 Вт и n = 1390 мин–1, тогда угловая скорость двигателя
с–1. (4),
где ─ частота вращения двигателя, мин–1.
Передаточное отношение зубчатой передачи
|
|
. (5)
где ωдв ─ угловая скорость двигателя, с–1;
ωст ─ угловая скорость вращения стола, с–1.
Округленное значение передаточного отношения 23, необходимо использовать двухступенчатую зубчатую передачу. Производим приближенное распределение передаточного отношения по ступеням в соответствии с [3].
Для конической передачи Uпк = 4.
Для цилиндрической передачи Uпц = 5,6.
Расчетное передаточное отношение
. (6)
Относительная погрешность передаточного отношения или заданной скорости не должна превышать 5 %:
или
. (7)
Проверим правильность наших расчетов:
. (8)
Проектирование и расчёт зубчатых передач
Разработка конструкции передачи и необходимые расчеты
Определение основных размеров передачи
Из условия прочности [4, 5] можно вычислить приблизительное значение диаметра меньшего колеса (шестерни):
, (9)
где d1 – делительный диаметра меньшего колеса (шестерни), мм;
С – коэффициент, учитывающий геометрию передачи и свойства материалов: С = 2,8 – для стальных незакаленных колес; С = 2,0 – для стальных закаленных;
Т1 – крутящий момент на валу меньшего колеса, Н∙мм;
U12 – передаточное отношение пары зубчатых колес.
|
|
d1≥2,8∙ =61,2 мм. (10)
Число зубьев меньшего колеса (шестерни) z1 = 20.
Модуль m в миллиметрах определяется из следующей зависимости:
, (11)
где z1 – число зубьев шестерни (определяется по рекомендации справочной литературы [3, 4] в зависимости от необходимой плавности работы, скорости вращения или заданного межосевого расстояния).
m1= =61,2/20=3. (12)
Модули эвольвентного зацепления цилиндрических колес регламентированы ГОСТ 9563-60. Стандартизован нормальный модуль mn. Стандарт предусматривает два ряда предпочтения. В первом ряду предусмотрены модули от 0,05 до 100 мм [2]. Второй ряд предусматривает промежуточные значения, в единичном производстве их применение нежелательно.
Изготовление колес c модулем менее 1,0 мм затруднительно.
Определение числа зубьев колеса z2 осуществляется по формуле
=5,6∙20=112 (цилиндрическая передача);
для третьего и четвёртого колёс конической передачи
z3=20, z4=4∙20=80.
Для цилиндрической передачи:
межосевое расстояние аw
, мм, (13)
где d1 – делительный диаметр шестерни, мм;
d2 – делительный диаметр колеса ( =3∙112=336), мм.
=
(14)
Диаметры вершин зубьев:
=61,2+6=67,2 мм; (15)
=336+6=342 мм. (16)
|
|
Ширина шестерни
=0,5∙61,2=30,6 мм, (17)
где ybd– коэффициент ширины зубчатого венца (ybd = 0,4…0,6).
Ширина колеса
мм. (18)
b2=30,6-2,5=28,1 мм. (19)
Для конической передачи:
межосевое расстояние аw
, мм, (20)
где d2 – делительный диаметр колеса, мм;
d3 – делительный диаметр шестерни ( =3∙20=60), мм;
d4=3∙80=240 мм (делительный диаметр колеса).
=
(21)
Диаметры вершин зубьев:
=60+6=66 мм; (22)
=240+6=246 мм. (23)
Ширина шестерни
=0,5∙60=30 мм, (24)
где ybd– коэффициент ширины зубчатого венца (ybd = 0,4…0,6).
Ширина колеса
мм.
b4=30-2,5=27,5 мм (25)
Силовой расчёт передачи
Целью силового расчета является определение сил и моментов, действующих на звенья передачи.
Таблица 1
Исходные данные для расчета силовых параметров передачи
Наименование параметра | Обозначение, ед. изм. | Значение параметра |
Подводимая (потребляемая) мощность | Р, Вт | 90 |
Угловая скорость колеса | ω, с–1 | 145,5 |
Число зубьев колеса | z2 z4 | 112 80 |
Диаметр колеса (сектора) | dw, мм | 60 |
Угол наклона зуба | βw, градус | 0 |
Угол зацепления в торцовой плоскости | αwt, градус | 0 |
Передаточное отношение | U12 | 23 |
Коэффициент внешней динамической нагрузки | Kдин | 1,05 |
Коэффициент перегрузки | Kпер | 1,2 |
Коэффициент трения в зацеплении зубьев | m | 0,1 |
|
|
Таблица 2
Расчет силовых параметров передачи
Определяемая величина | Расчетная формула | Значение величины |
Момент на колесе | ![]() | 649,5 |
То же, при перегрузке | ![]() | 779,4 |
Окружная сила в зубчатой передаче | ![]() | 21,65 |
Радиальная сила на колесе | ![]() | 0 |
Осевая сила на колесе | ![]() | 0 |
Нормальная сила на рабочей поверхности зубьев | ![]() | 21,65 |
Коэффициент нагруженности контакта | ![]() ![]() ![]() | 9,7 |
Коэффициент полезного действия цилиндрической передачи | ![]() | 0,82 |
Момент на ведомом валу | ![]() | 12249,57 |
Выбор материалов зубчатой передачи
Материал деталей передачи может быть назначен еще при разработке технического предложения – сталь, цветной металл, чугун, пластмасса. Однако такие данные пригодны только для ориентировочных расчетов на этапе эскизного проектирования. Для окончательных расчетов требуется указание марки материала и, при необходимости, его свойств с учетом термообработки.
Для колес, получаемых резанием, чаще всего применяют стали марок 45 и 40Х в нормализованном или улучшенном состоянии.
Для литых колес обычно применяют чугуны типа СЧ30, ВЧ65 и др., чаще всего с дополнительной обработкой резанием. Применение литейных сталей, например, типа сталь 40Л, позволяет уменьшить габариты передачи. Для повышения работоспособности колес применяется термообработка, например, улучшение или закалка.
Из цветных металлов сравнительно часто применяются бронзы типа БрАЖ 9-4 или высокопрочные алюминиевые сплавы, например, типа В95. Литые колеса рационально изготавливать из бронз типа БрА9Мц2, алюминиевых сплавов типа АЛ8 или магниевых типа МЛ6. Повышенная стоимость материалов может окупиться их более высокой технологичностью и эффективностью работы.
Следует заметить, что цветные металлы и пластмассы, как правило, применяют в качестве материала колеса, сопряженного со стальным или чугунным колесом.
Марка материала и термообработка | Модуль упругости E, МПа | Коэффициент Пуассона ν | Допустимое напряжение σt, МПа | Предел текучести σт, МПа | Твердость |
Сталь 45 ГОСТ 1050-74 Нормализованная | 210∙103 | 0,26 | 600 | 340 | 210 НВ |
Длина ступицы
(26)
где Dy = 30– диаметр вала, мм.
Рабочая длина шпонки
=0,8∙30=24 мм, где Ссм – коэффициент, учитывающий прочность материала ступицы при работе на смятие, для стальных втулок Ссм = 0,8.
Рис.1 ─ Крепление колёс на валах.
Дата добавления: 2018-04-05; просмотров: 80; Мы поможем в написании вашей работы! |
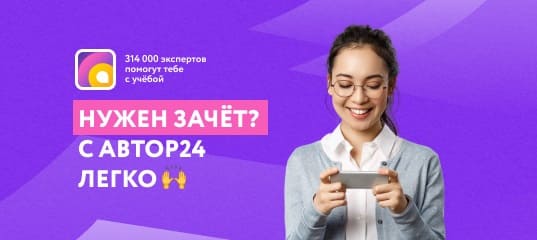
Мы поможем в написании ваших работ!