Колебания лопаток и дисков осевых компрессоров и турбин
Колебания лопаток.
На лопатки осевых компрессоров и газовых турбин действуют в процессе работы периодически изменяющиеся силы. Если частота этих сил совпадает с частотой собственных колебаний лопаток, возникает явление резонанса. При появлении на каком либо режиме работы двигателя резонанса колебания, напряжение в рабочих лопатках резко увеличивается, в результате может произойти разрушение лопаток. Если поломка лопаток происходит от колебаний, то место излома имеет характерный ритм, которое в свойстве поломки деталей из-за недостаточной усталостной прочности. поломка лопатки обычно приводит к повреждению и разрушению всех остальных лопаток. Периодичность действия сил, вызывающих вынужденные колебания лопаток объясняется несколькими причинами в качестве первой из этих причин можно назвать порциальность подвода газов к рабочим лопаткам. Эта порциальность связана с наличием в проточной части двигателя направляющих лопаток в компрессоре и сопловых в турбине, тюк. Число таких лопаток конечно по окружности, следовательно на каждую лопатку действует переменное усилие. Переменные усилия могут появиться также при отклонении размеров спрямляющих и сопловых лопаток от средних значений. При этом расходы воздуха и газа через отдельные межлопаточные канала получаются разные. Кроме этого разными также будут скорости и давление газа на выходе из канала. Теоретически шаг лопатки во всей окружности должен оставаться одинаковым, однако, при изготовлении делаются технологические разъемы корпусов компрессоров и турбин, т.е. в месте соединения корпусов шаг лопаток будет изменяться. Это также приведет к появлению вынужденных колебаний каждой рабочей лопатки с определенной частотой. Известно, что число форсунок для подачи топлива по окружности имеет определенное количество. Это тоже приводит к появлению колебаний, кроме этого на двигателе для усиления конструкции применяются ребра и стойки, которые также вызывают вынужденные колебания с определенными частотами. Т.е. в общем случае частота вынужденных колебаний рабочих лопаток пропорционально числу оборотов ротора двигателя. Рассмотрим существующие формы колебаний лопаток. Колебания лопаток могут быть изгибными, крутильными и изгибно – крутильными. Рассмотрим изгибные колебания лопаток. При изучении изгибных колебаний рабочих лопаток рассматривается как консольная балка, имеющая большое число форм собственных колебаний. Обычно изучаются несколько низших форм. Рассмотрим их:
|
|
Понятие колебаний дисков.
Под действием периодически изменяющихся сил на дисках компрессоров и турбин могут возникать резонансные колебания. Силы могут действовать на диск или на рабочие лопатки. Непосредственно на диск действуют переменные силы, вызванные колебаниями вала и силы, возникающие при пульсирующем подсасывании воздуха или газа. Подсасывание воздуха или газа происходит когда в пространстве между стенкой корпуса и диском давление уменьшается, при этом с противоположной стороны на диск действуют силы, стремящиеся увеличить давление, возникает прогиб диска, давление увеличивается, подсос уменьшается. Однако диск возвращается в обратное направление, тем самым уменьшается давление. При этом подсос увеличивается и диск снова прогибается в ту же сторону, так возникает колебание диска. Формы колебаний дисков разнообразны, однако в основном все колебания разделяют на три вида:
|
|
- зонтичное колебание. Колебания дисков происходят относительно ступицы;
|
- колебание с одной или несколькими узловыми окружностями;
- колебания с одним или несколькими узловыми диаметрами.
Два первых вида колебаний вызываются осевыми силами. Осевые силы возникают при пульсирующем подсасывании газа, а также при механическом воздействии на вал сил, вызванных неисправностью упорных подшипников или соединительных муфт. Чаще всего встречаются колебания с одним или несколькими узловыми диаметрами. Эти колебания вызываются силами, действующими непосредственно на рабочие лопатки, а через рабочие лопатки на диск. Колебания с одним или несколькими узловыми диаметрами можно классифицировать следующим образом: самый простой вид колебания – с одним узловым диаметром, более сложной формы является сочетание колебаний с одним узловым диаметром и одной или несколькими узловыми окружностями. Эти колебания возникают при совместных колебаниях диска и вала. Они являются динамически неуравновешенными. Существуют колебания диска, являющиеся также сочетанием колебаний с двумя или более узловыми диаметрами с одной или несколькими узловыми окружностями. Эти колебания являются динамически уравновешенными и называются циклически симметричными. При этих колебаниях диск не передает на вал поперечных или продольных усилий. Для всех форм колебаний диска число узловых диаметров и окружностей связано с частотой колебания, т.е. чем выше число узловых линий, тем выше частота колебаний. Диски с рабочими лопатками осевых компрессоров и турбин имеют те же формы колебаний, что диски без лопаток. Однако в этом случае узловые окружности могут располагаться как на диске, так и на лопатках. Однако при этом те лопатки, которые расположены на узловых диаметрах будут иметь только крутильные колебания, а лопатки, расположенные на выпуклостях – только изгибные колебания, а остальные лопатки – смешанные изгибно-крутильные колебания. Из этого следует, что диск с рабочими лопатками представляет собой единую систему, в которой колебания отдельных элементов диска и рабочих лопаток отличается от колебаний, не соединенных между собой рабочих лопаток и диска. Помимо форм колебаний, колебания дисков могут отличаться еще и видом колебаний. Колебания диска, когда все точки колеблются с одинаковой фазой и одновременно достигают крайних положений, или положения равновесия называются синфазными колебаниями. В этом случае узловые диаметры все время остаются неподвижными относительно диска. Колебания диска могут быть фазовыми, при которых различные точки диска расположенные по окружности, имеют различные формы колебаний. Если фазовые углы отдельных точек применяются равномерно по окружности, то на диске образуется волна, бегущая по неподвижному диску с угловой скоростью ω. Когда волна пробежит полную окружность, частота колебаний каждой точке диска будет равна числу узловых диаметров, тогда круговая частота будет равна:
|
|
|
|
f=ωz
ω – угловая скорость бегущей волны
z – узловых диаметров.
Вид колебаний диска зависит от вида возбуждений. Внешнее воздействие, которое перемещается относительно диска, вызывает колебания типа бегущей волны. Обычно на вращающихся дисках компрессоров и турбин возникают колебания типа бегущей волны, т.к. внешнее воздействие на диске перемещается относительно него. Причинами, вызывающими появление бегущей волны следующие:
- в зависимости от сочетаний числа рабочих и направляющих лопаток может возникнуть внешнее воздействие, которое перемещается по направлению или на встречу движения рабочего колеса;
- появление вращающегося срыва, создающего импульс, вызывающее волну колебаний, движущуюся относительно диска со скоростью, равной половине вращения;
- при взаимодействии роторов двухвальных двигателей.
Наибольшую опасность представляют радиальные колебания, при которых скорость бегущей волны равна и противоположна скорости вращения диска. В этом случае на диске образуется стоячая волна колебаний, которая неподвижна относительно наблюдателя и определяет форму изгиба, которую принимают все участки вращающегося диска.
Камера сгорания.
Камера сгорания является ответственным узлом двигателя, в котором происходит преобразование химической энергии топлива в тепловую энергию. Поэтому к камерам сгорания предъявляются следующие требования:
- высокая полнота сгорания топлива на всех режимах работы двигателя. Коэффициент полноты сгорания должен быть не менее 0,98 – 0,99;
- минимальные потери полного давления в камере сгорания. В двухконтурных двигателях коэффициент восстановления полного давления – 0,94 – 0,96, в одноконтурных двигателях – 0,9 – 094;
- минимальные габаритные размеры камеры сгорания. Размеры камеры сгорания влияют на продольные и поперечные размеры двигателя и его массу;
- устойчивая работа без погасания и вибрационного горения во всем эксплуатационном диапазоне;
- надежный розжиг топлива в земных и высотных условиях;
- минимальный уровень содержания твердых частиц дымности, токсичных выбросов продуктов сгорания;
- высокая надежность конструкции и стабильность характеристик камеры сгорания при данном ресурсе двигателя;
- хорошая технологичность, малая металлоемкость, удобство эксплуатационного обслуживания и ремонтопригодность.
Рассмотрим особенности технологичной схемы камеры сгорания. Из курса Теории АД известно, что в авиационном двигателе используются трубчатые, трубчато – кольцевые и кольцевые камеры сгорания. Любая камера сгорания состоит из корпуса и жаровой трубы. В жаровой трубе осуществляется подача топлива через топливную форсунку и воздуха через стабилизатор, организация перемешивания и горения. Сжигание топлива происходит в отдельной зоне сгорания, а в дальнейшем – смешение продуктов сгорания с воздухом, т.е. решается задача полного сжигания топлива при средней температуре в зоне горения 2000 0С и получения рабочего тела с температурой, при которой сохраняется работоспособность деталей турбин. Для этого поток воздуха, подводимый в камеру сгорания разделяется на первичный, поступающий через лопаточный стабилизатор и отверстия в зону горения, и вторичный, протекающий по отверстиям в жаровой трубе в зону смешения в жаровой трубе. Благодаря зоне смешения температура продуктов сгорания на выходе из камеры сгорания снижается до необходимой величины для поступления в сопловой аппарат турбины. Такое разделение потока воздуха обеспечивает устойчивую работу авиационного двигателя. Высокие температуры в зоне горения и смешения, при которых не работоспособны современные материалы, требуют эффективного охлаждения жаровой трубы и других деталей камеры. С этой целью используется первичный воздух, поступающий непосредственно в зону горения и вторичный, протекающий в пространстве между корпусом и жаровой трубой, при этом происходит конвективное охлаждение. Т.е. отвод тепла от стенок жаровой трубы при обтекании их воздухом снаружи. Но это оказывается недостаточным, поэтому воздух, проникающий в зону смешения частично направляется вдоль внутренней поверхности жаровой трубы, образуя заградительный, непрерывно обновляющийся пристеночный слой. Который защищает внутренние стенки жаровой трубы от контакта с горячими газами. Вторая особенность работы камеры сгорания – это относительно большая скорость воздушного потока, т.к. уменьшение скорости приводит к увеличению габаритов двигателя. В связи с этим, устойчивость при высокой скорости воздушного потока достигается образованием токов горячих газов, которые продвигаются против потока воздуха. В этом случае фронт пламени, т.е. поверхность, разделяющая подготовленную для воспламенения смесь и факел горения движется в зоне горения со скоростью, превышающей скорость течения воздуха, что предотвращает срыв пламени. Скорость воздуха, которая на выходе из компрессора порядка 110 м/с, а количество первичного воздуха, поступающего в зону горения – примерно 30 % от общего расхода воздуха через двигатель. Воздух протекает через каналы стабилизатора, которые образованы лопатками, расположенными под углом к оси камеры закручивается и движется одновременно в осевом, окружном и радиальном направлении и его траектория имеет форму спирали. Благодаря этому в центральной части зоны горения устанавливается пониженное давление и в нее поступает горячий газ. Т.о. в результате закрутки потока центральной части жаровой трубы образуется зона обратных потоков, поэтому важнейшим устройством, расположенным в начале жаровой трубы является стабилизатор горения, который имеет следующие конструктивные особенности:
|
а- лопаточный стабилизатор;
б, в – конические стабилизаторы;
1 – кольцо;
2 – лопатка;
3, 4, 8 – втулки форсунки;
5, 9 – ребра;
6, 7 – кромки;
10, 13, 15 – отверстия подвода воздуха для охлаждения и сдува нагара;
11 – дефлектор;
12 - конус;
14 – зазор.
Элементы жаровых труб.
а – ореберная поверхность;
б - щели;
в, г - отверстия;
д, з – отверстия и направляющие козырьки;
1, 2, 3 – секции жаровой трубы;
е – отверстия для двойного расширения;
ж - прорези;
и – образование защитного слоя;
к – соединение секций заклепками;
1 - шайба;
2 – заклепка;
л – сотовый материал;
1, 3 - стенки;
2 – гофрированный заполнитель.
Элементы подвода воздуха.
|
а, б, в – подводящие отверстия;
г – патрубок;
д – патрубок с охлаждением;
1 – наружный патрубок;
2 – внутренний патрубок.
В жаровых трубах для уменьшения температуры стенки жаровой трубы и продуктов сгорания применяется подвод воздуха при помощи отверстий и щелей, направляющих воздух вдоль внутренней поверхности. Щелевые устройства обеспечивают высокую степень турбулизации потока воздуха и устойчивой работы камеры сгорания. Очень эффективна конструкция, состоящая из двух стенок и гофрированной прослойки. Воздух протекает по каналам, образованные гофрами, эффективно охлаждает стенки жаровой трубы. В этом случае расход охлаждающего воздуха уменьшается на 50 %. Показанные элементы подвода воздуха в элементы жаровой трубы разнообразны по конструкции. Простейший подвод воздуха – через круглые отверстия, имеет большой недостаток, т.к. температура кромок отверстия ниже температуры стенки, поэтому возникают большие термические напряжения, приводящие к поломкам стенок трубы, для уменьшения термических напряжений, кромки стенок окантовываются. Наиболее эффективна конструкция патрубка с охлаждением. В этом случае глубина проникновения воздуха позволяет интенсивно охладить продукты сгорания, а воздух, поступающий по каналу между патрубками охлаждает переднюю кромку внутреннего патрубка. Трубчато – кольцевые камеры сгорания представляют собой трубчатые жаровые трубы, соединенные между собой устройствами, позволяющими равномерно разместить жаровые трубы по окружности камеры сгорания. Соединительные устройства позволяют обеспечить равномерное воспламенение топливо – воздушной смеси в жаровых трубах. Соединительное устройство выглядит следующим образом:
|
1, 8 – внутренние патрубки;
2 - кожух;
3, 6 - полумуфты;
4 - замок;
5 - прокладка;
7 – внешний патрубок;
9 – уплотнительная обойма;
10 – уплотнительное кольцо;
11 – втулка.
В соединительном устройстве к кожуху 2 приварен фланец обоймы 9 для крепления внешнего патрубка 7, фиксирующего жаровые трубы. К жаровым трубам приварены втулки 11 под соединительные внутренние патрубки 1 и 8 , служащие для поджигания смесей в трубах, не имеющих воспламенителей и для выравнивания между ними давления. Патрубки 1 и 8 обеспечивают поджигание смесей в случае самопроизвольного прекращения горения в отдельных камерах. Соединительное устройство состоит из внутренних 1 и 8 патрубков и внешних 7, которые входят во втулки 11 и 9 соответственно. Наружные патрубки 7 смежных камер стягиваются полумуфтами 3 и 6. Между фланцами наружных патрубков расположена медно – асбестовая прокладка, а между фланцами 9 и наружными патрубками расположены уплотнительные кольца 10 из асбестового шнура. Данное соединение допускает перемещение жаровых труб при наличии температурной деформации.
Дата добавления: 2018-04-05; просмотров: 1902; Мы поможем в написании вашей работы! |
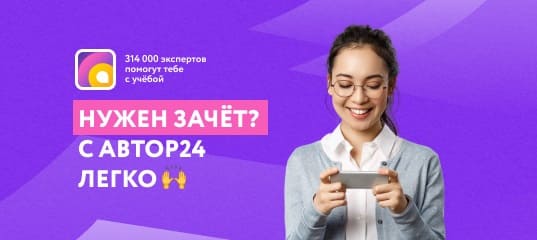
Мы поможем в написании ваших работ!