Силовая схема двигателя АЛ-31Ф
1-наружный корпус;
2-ротор низкого давления;
3-внутренний корпус;
4-ротор высокого давления;
5-промежуточный корпус;
6-узлы крепления к самолету.
Крепление двигателя к самолету.
Крепление двигателя на самолете, а также подвеска узлов при транспортировке производится по средствам специальных креплений, Устанавливаемых на силовом корпусе двигателя. В общем случае узлы крепления к двигателю передает нагрузки:
- Реактивную тягу
- Силы инерции масс двигателя, возникающие при маневрах самолета
- Гироскопический момент от ротора двигателя
- Силы инерции и момент, возникающий от неуравновешенности двигателя отбалансированного с определенной степенью точности.
Кроме этого в ТВД действует реактивный момент от винта, направленный в сторону, противоположную вращению. При наличие на двигателе двух винтов, вращающихся в разные стороны, реактивный момент равен разности моментов винтов. Конструкция и расположение на двигателе узлов крепления предъявляются следующие основные требования:
- Точки подвески должны быть расположены так, чтобы обеспечивать крепление двигателя в шести направлениях: осевом, вертикальном, боковом направлениях и продольной, вертикальной и горизонтальной оси. При этом система подвески не должна допускать двойного крепления в направлении и вокруг названных осей. Благодаря этому изолируется корпусная система двигателя от деформации самолетной конструкции и предупреждается возникновение в узлах подвески больших нерасчетных нагрузок.
- Точки крепления двигателя при всех условиях полета и режимах работы не должны препятствовать термическим деформациям корпуса двигателя.
- Основные точки подвески должны быть расположены на силовых корпусах компрессоров в полости близкой к центру массы двигателя. Обычно такими плоскостями являются плоскости внутренних силовых связей опор ротора компрессора.
- Дополнительные точки подвески должны быть расположены на корпусе турбины, а также в плоскости внутренних связей опор турбины.
- Форсажная камера должна иметь дополнительную точку подвески в плоскости корпуса управляемого реактивного сопла и также форсажная камера должна быть присоединена к корпусу турбины с помощью шарнирного соединения.
- В случае тонкостенных конструкций корпусов для избежания больших и местных радиальных деформаций и задевания лопаток за корпус не допускается в точках подвески большие радиальные усилия.
- Для проведения такелажных, монтажных и транспортных работ на двигателе должны быть дополнительные точки подвески и поддержки, удовлетворяющие требованиям для основных точек подвески. При выполнении монтажных работ на самолете, подвеска и поддержка двигателя в произвольных точках не допускается во избежание деформаций.
|
|
Конструкция осевых компрессоров.
|
|
Классификация осевых компрессоров.
Все компрессора можно разделить на сверхзвуковые и дозвуковые. Кроме этого компрессора разделяются по числу роторов на однороторные однокаскадные, двухроторные двухкаскадные и трехроторные.
Двухроторные компрессоры располагаются последовательно. Трехроторные компрессоры применяются в двухконтурных ТРД. Они приводятся от трех газовых турбин.
Компрессора подразделяются по конструкции ротора на дисковые, барабанные и барабанно-дискового типа.
По конструкции проточной части компрессоры бывают: с постоянным средним диаметром, с постоянным наружном диаметром и изменяющимся диаметром втулки, с постоянным диаметром втулки и изменяющимся наружном диаметром.
Компрессор состоит из ротора и статора. На статоре располагаются лопатки спрямляющих и направляющих аппаратов, которые изменяют направление потока. На роторе расположены рабочие лопатки, которые вращаясь сжимают поток воздуха.
Ротор компрессора.
|
|
По конструктивному исполнению ротор осевого компрессора может быть барабанного, дискового и смешанного типа. На роторе этого типа несколько рядов рабочих лопаток закреплены на цилиндрическом или коническом барабане, представляющим собой канавку из алюминиевого сплава или стали, механически обработанную со всех сторон. Две стальные крышки закрывают барабан с торцев и имеют цапфы, которыми ротор опирается на подшипники. Крутящий момент каждой из турбины передается через стенку барабана. Достоинством ротора барабанного типа является простота конструкции, определяющую сравнительную простоту его изготовления и большая поперечная жесткость, благодаря которой критическая частота вращения очень высока. Критической частотой вращения называется частота вращения, при которой вращающийся ротор имеет большие прогибы, вызывающие вибрацию двигателя и его разрушение. К недостаткам такого ротора можно отнести невозможность его использования в быстроходных компрессорах, из-за того, что на его поверхности из условий прочности допускается окружная скорость не более 200 м/с, а также из-за того, что у него большая масса и габариты. Роторы такого типа применялись на первых двигателях, в настоящее время они не применяются.
|
|
Ротор дискового типа имеет соединенные с валом специально спроектированные диски, на периферии которых прикреплены рабочие лопатки. Диски обладают большой точностью и допускают на своей наружной поверхности окружные скорости 250-360 м/с, поэтому ступени компрессора с дисковыми роторами являются высоконапорными и применяются в двигателях с большими степенями повышения давления. Крутящий момент каждой ступени передается через вал. Недостатком ротора этого типа является небольшая поперечная жесткость по сравнению с ротором барабанного типа. Критическая частота вращения не велика и близка к рабочей. Ротор дискового типа, по сравнению с ротором барабанного типа имеет небольшую конструктивную и технологическую сложность.
1-вал;
2-диск;
3-напрессованная втулка;
4-штифт;
5-конические пояски.
Роторы барабанно-дискового типа сочетают достоинства роторов барабанного и дискового типов. Они состоят из секций, которые представляют собой диск с барабанной проставкой. Роторы барабанно-дисковой конструкции обладают высокой изгибной жесткостью, допускающая высокие окружные скорости вращения, поэтому они получили широкое распространение в современных осевых компрессорах. Роторы барабанно-дисковой конструкции выполняются неразборными и разборными. Каждая из конструкции имеет свои достоинства и недостатки, например, ротор компрессора, в котором соединение дисков осуществляется при помощи штифтов.
|
1- диск I ступени;
2- рабочая лопатка;
3- диски промежуточных ступеней;
4- штифты;
5- полотно задней цапфы.
В данном случае секция ротора представляет собой диск с барабанным участком, которая соединяется с аналогичным диском радиальными штифтами и посадкой с натягом по цилиндрическим поясам. Такое соединение имеет следующие особенности: стальные штифты запрессовываются в отверстия, находящиеся в пазах лопаток. Это обеспечивает фиксацию штифтов от выпадения под действием центробежных сил. При помощи этих же штифтов передаются крутящие моменты, барабанные части дисков центрируются в расточках смежных дисков. Описанная конструкция отличается большой жесткостью и надежным центрированием соединяемых элементов. Это объясняется тем, что соединение дисков и центрирование выполнено на максимальновозможных диаметрах с относительно большими натягами. В этой конструкции даже в случае потери натяга или превращение его в зазор, центрирование надежно обеспечивается штифтами. Однако, выполнение дисков с барабанными участками усложняет технологию их изготовления, хотя данная конструкция имеет сравнительно мало соединительных стыков. Это повышает жесткость ротора, делает его более легким. Основным недостатком роторов такой конструкции является трудность монтажа и демонтажа, т.к. по существу это неразъемная конструкция.
Другим типом соединения, очень часто применяемого в двигателях является соединение дисков при помощи торцевых щлицев и стяжного болта.
|
1-диски;
2-задняя цапфа;
3-торцевые шлицы;
4-стяжной болт.
Торцевые шлицы, выполненные на торцах барабанных участков треугольного профиля. Шлицы передают крутящий момент и центрируют диски относительно друг друга. Для улучшения прилегания треугольных шлицев при сборке стыкуемые детали предварительно обжимаются под прессом со значительным усилием, чтобы снять микронеровности на поверхности контакта. Затяжка болта производится также под прессом и контролируется по вытяжке болта. Данная конструкция отличается надежным центрированием на относительно больших диаметральных размерах. Конструкция эта разборная и позволяет легко заменять диски. Недостатками такого ротора является технологическая сложность выполнения торцевых треугольных шлицев и дисков с барабанными участками, а также сложность монтажа из-за необходимости производить затяжку ротора под прессом. Из опыта эксплуатации установлено, что на роторе данной конструкции на переходных режимах работы двигателя ( запуск, разгон, торможение ) появляется разность температур между дисками и стяжным болтом, т.к., например, при запуске двигателя пакет дисков нагревается быстрее, чем стяжной болт. Это увеличивает затяжку болта, и наоборот, при выключении двигателя пакет дисков охлаждается быстрее, чем стяжной болт, поэтому затяжка болтов ослабевает. Из этого следует, что стяжной болт испытывает большие напряжения, потому что его начальная затяжка должна компенсировать всевозможные температурные деформации, а усталостные напряжения стяжного болта вызывают тяжелые последствия, поэтому в современных двигателях используются соединения дисков при помощи призонных болтов. Диски таких роторов имеют тонкостенные барабанные участки с фланцами. Фланцы соединяются между собой при помощи промежуточного диска, на полотнах этих дисков имеются кольцевые площадки, по которым фланцы барабанных участков стягиваются при помощи призонных болтов, которые передают крутящий момент и обеспечивают центровку. Задняя цапфа ротора соединяется с последним диском аналогично, т.е. с помощью призонных болтов, передняя цапфа выполняется заодно с диском. Распространение такой конструкции объясняется следующими достоинствами ротора данной конструкции: большой жесткостью, надежным центрированием, на всех режимах работы двигателя, простотой замены дисков. Разрушение одного или нескольких болтов не приводит к серьезным неисправностям. К недостаткам этих роторов можно отнести зависимость стабильности соединения от изгибной жесткости фланцев барабанных устройств. Нагружение болтов напряжениями среза при возможности относительного перемещения соединяемых дисков. Кроме этого существует технологическая сложность: постановка призоных болтов не возможна, если отверстия не развернуты совместно. Кроме этого наличие барабанных устройств, выполняемых совместно с дисками усложняет технологию изготовления, т.к. сложное выполнение канавок дисков затрудняет обеспечение надлежащих физико-механических свойств поверхности в радиальных и осевых направлениях. Роторы компрессоров низкого и высокого давления двигателя АЛ-31Ф барабанно-дисковой конструкции с применением новейших технологий сборки. Каждый ротор состоит из неразборной части, секции, которые соединяются между собой при помощи сварки, и разборной, секции, которые соединяются при помощи призонных болтов и стяжек. Это обеспечивает при соответствующей модульной конструкции компрессора ремонтопригодность роторов в полевых условиях.
Рабочие лопатки.
Рабочая лопатка- это наиболее ответственная деталь ротора от совершенства и долговечности которой зависит надежная работа компрессора. Лопатка работает в сложных условиях, на нее действуют инерционные и аэродинамические силы. Эти силы вызывают напряжения растяжения, изгиба и кручения. Кроме этого на рабочие лопатки последних ступеней действует высокая температура порядка 1000 К. Поэтому рабочая лопатка ротора компрессора должна обеспечивать:
- Высокую прочность и жесткость.
- Высокую степень чистоты обработки. Это необходимо для уменьшения потери на трение при течении воздуха по межлопаточному каналу.
- Высокую точность исполнения размеров при изготовлении лопаток, т.к. от этого зависят параметры воздушного потока в проточной части компрессора.
- Возможные меньшие концентраторы напряжений, особенно в местах перехода профильной части к хвостовику.
- Минимальная масса хвостовика. Например, снижение массы на 1% снижает массу ротора, приходящуюся на одну лопатку на 4-5%.
- Конструкция хвостовика должна позволять удобную сборку ротора и замену лопатки в случае ее повреждения.
- Минимальное остаточное напряжение. Необходимая долговечность лопатки определяется назначением летательного аппарата, для которого предназначен компрессор.
Рабочая лопатка состоит из профильной части (перо лопатки) и хвостовика. Формы и размеры профильной части лопатки определяются аэродинамическим расчетом. Окончательная конструкция уточняется с учетом требований обеспечения статической и динамической прочности. Рабочая лопатка должна быть легкой и достаточно технологичной, допускающей массовое производство. Рабочая лопатка компрессора выполняется с тонкой входной кромкой и малыми углами поворота потока. Хвостовики лопаток выполняются трех типов:
- Ласточкин хвост
- Елочный
- Шарнирный.
Такими же делаются профили пазов под лопатки в дисках ротора. При соединении хвостовика лопатки с пазом, образуется замок для крепления лопаток. Соединение лопатки с диском должно удовлетворять следующим требованиям:
- Высокая прочность
- возможность размещения необходимого числа лопаток на диске;
- легкость сборки и замены лопаток;
- малая масса.
Самое широкое распространение получило соединение типа ласточкин хвост. Сечение лопатки выполнено в форме трапеции с плоскими рабочими поверхностями. Паз в диске также представляет собой трапецию, которая размещается под некоторым углом к оси ротора.
|
Соединение типа ласточкин хвост имеет следующие преимущества:
- Отличается не большой высотой, это позволяет применять легкие диски;
- имеет относительно не большую толщину, это обеспечивает возможность размещения нужного количества лопаток на диске с целью получения решетки нужной густоты;
- технологичность конструкции.
Существенным недостатком является низкая способность гасить колебания лопаток, в следствие колебания лопаток появляются переменные контактные напряжения, которые служат причиной разрушения хвостовика или выступа диска.
Елочное соединение практически не применяется в компрессорах из-за сложности производства.
Шарнирное крепление лопаток выглядит следующим образом:
|
1-диск;
2-шайба;
3-палец;
4-заклепка;
5-лопатка.
В приведенной схеме лопатка 5 проушинами замков вставлена в пазы диска 1 и соединяется с диском помощью пальцев 3. От осевого перемещения пальцы ограничены с одной стороны радиальными выступами, а с другой стороны при помощи шайбы 2 закрепленной заклепкой 4.
Шарнирное соединение позволяет лопатке самоустанавливаться при действии на нее газодинамических и инерционных сил. Такую лопатку можно применять при умеренных окружных скоростях на периферию лопаток примерно меньше 320 м/с. Для уменьшения износа и устранения заедания в шарнире применяется твердая смазка. В проушины лопатки изнутри, с торцев и наружную поверхность ось натирают порошком двухсернистого молибдена.
Корпус компрессора.
Корпус компрессора представляет собой полый цилиндр или усеченный конус в зависимости от способа профилирования проточной части компрессора. С торцев к корпусу компрессора крепятся корпуса переднего и заднего подшипников.
Корпус компрессора может быть цельным и разъемным, с продольным разъемом или поперечным разъемом. Корпус с продольным разъемом позволяет выполнить сборку компрессора с окончательно собранным и отбалансированным ротором. Если корпус не разъемный, то ротор вместе с направляющими лопатками вводится с торца. В некоторых случаях изготавливаются технологические разъемы, например, поперечные технологические разъемы, применяются при изготовлении корпусов из разных материалов. Например, для первых ступеней используется алюминиевый сплав, для последних – стальные сплавы. Фланцы, служащие для соединения частей корпуса между собой увеличивает жесткость и уменьшает работу корпуса на изгиб. Однако, неравномерная жесткость разъемного корпуса по окружности приводит к неравномерному тепловому расширению и короблению при нагревании, поэтому, обычно с наружной стороны корпуса устанавливаются ребра, при помощи которых добиваются одинаковой жесткости по окружности. Корпуса компрессоров отливаются из алюминиевых сплавов или свариваются из листовой стали и титановых сплавов. Корпус компрессора обычно состоит из переднего корпуса, нескольких промежуточных корпусов и заднего корпуса. В переднем корпусе устанавливается входной направляющий аппарат, который изменяет направление на входе.
|
1-резьбовая цапфа;
2-полка;
3, 5-полукольца;
4-внутренняя цапфа.
На промежуточных корпусах и заднем корпусе устанавливаются лопатки направляющего аппарата. Кроме этого задний корпус служит для силовой связи с корпусом камеры сгорания, поэтому его изготавливают из более жаропрочного материала. Направляющий аппарат компрессора устанавливается на промежуточных корпусах и представляет собой кольцевой набор профилированных лопаток, которые устанавливаются за соответствующими ступенями рабочих лопаток. Они могут крепиться консольно – с одной стороны или по обоим сторонам. К конструкции направляющего аппарата предъявляется ряд специальных требований, например, направляющий аппарат должен обеспечить свободу температурного расширения лопаток. Кроме этого требуется, чтобы сохранялась концентричность внутренних и наружных креплений относительно оси ротора. В большинстве случаев встречаются направляющие аппараты с двухсторонним креплением лопаток. Двухстороннее крепление лопаток может быть жестким, когда лопатка жестко прикреплена к наружному корпусу и внутреннему кольцу. Такие лопатки обычно устанавливаются на первых ступенях компрессоров, где температура воздуха изменяется незначительно. На последних ступенях компрессора устанавливаются лопатки направляющего аппарата, допускающие радиальное перемещение лопатки по радиусу при нагреве. Это необходимо для компенсации температур деформации на последних ступенях. Кроме этого на корпусе компрессора крепится устройство перепуска воздуха.
Клапан перепуска воздуха:
1-клапан;
2-корпус клапана;
3-поршень;
4-штуцер подвода масла;
5-штуцер слива масла;
6-пружина;
7-защитная сетка.
Перепуск воздуха из компрессора с помощью ленты:
1-окна в корпусе компрессора;
2-силовой цилиндр механизма перепуска;
3-поршень;
4-пружина;
5-шток поршня;
6-зубчатые секторы;
7-лента перепуска;
8-корпус компрессора.
Перепуск воздуха может осуществляться при помощи ленты и клапанов. На корпусе компрессора расположены окна, которые закрываются лентами перепуска. Если необходимо окна открыть, то натяжение ленты ослабляют при помощи зубчатой передачи и осуществляется перепуск воздуха. Кроме этого существует клапан перепуска воздуха, который осуществляет перепуск воздуха по исполнительной команде, подаваемый по системе управления.
Дата добавления: 2018-04-05; просмотров: 2714; Мы поможем в написании вашей работы! |
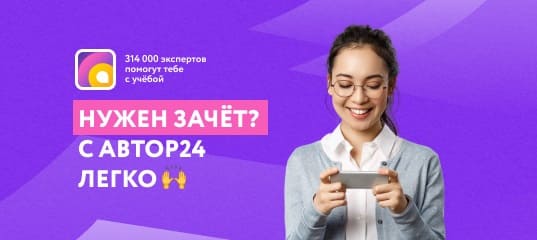
Мы поможем в написании ваших работ!