Материалы для деталей компрессора
Материалами для изготовления дисков являются алюминиевые сплавы АК4-1, АК6-1 – до температуры 520 0К, стали 30ХГСА – до температуры 725 0К, при более высоких температурах применяются титановые сплавы ВТ3-1, ВТ9. Заготовки для изготовления дисков или барабанов выполняются штамповкой. В дальнейшем заготовки с минимальными допусками подвергаются механической обработке. Изготавливают заготовки механическим или электрохимическим способом, а также точной штамповкой, вальцовкой и чеканкой. Позволяет получить профиль пера с окончательными размерами и требуемой формой. Рабочие лопатки для сравнительно низких рабочих температур изготавливают из алюминиевых сплавов АК4 или из композитных материалов на эпоксидной основе. При более высоких температурах материалом для лопаток являются, стали Х17Н2 или титановые сплавы ВТ8, ВТ10. Корпус компрессора изготавливается из алюминиевых сплавов АЛ4, АЛ5 – для первых ступеней, последние ступени выполняются сварные из титановых сплавов или из листовой стали. Выбор материала корпуса определяется главным образом температурой воздуха проточной части компрессора.
Уплотнение концевых зазоров.
Для предупреждения соприкосновения подвижных и неподвижных поверхностей компрессора между ними должны быть обеспечены зазоры – радиальные и осевые. Радиальный зазор между концом лопатки и корпусом должен быть как можно меньше, т.к. через него может перетекать воздух из полости с большим давлением в полость с меньшим давлением. Это влечет за собой уменьшение КПД компрессора и увеличение расхода топлива. Величина радиального зазора зависит от множества факторов, наиболее важными из них являются деформации деталей ротора под действием центробежных сил и нагрева, деформация корпуса под действием давления воздуха и нагрева и производственные допуски на изготовление детали. Точно учесть все факторы невозможно, поэтому величина зазора в холодном состоянии ( монтажный зазор ) устанавливается экспериментально. Радиальный зазор можно уменьшить путем покрытия внутренней поверхности корпуса мягким материалом в местах, где располагаются рабочие лопатки. При касании рабочих лопаток слой покрытия срабатывается и обеспечивается получение минимального зазора. Осевой зазор между рабочими лопатками и направляющим аппаратом желательно иметь минимальный для уменьшения длины компрессора. При расчетах зазор выбирается в пределах 15 – 20 % от хорды профиля рабочей лопатки.
|
|
Лабиринтные уплотнения.
Наличие разности давлений по обе стороны каждой ступени способствует перетеканию воздуха из полости большего давления в полость меньшего давления, а следовательно к снижению КПД компрессора и экономичности двигателя. Для разделения полостей с различными давлениями и для уменьшения утечки воздуха применяются лабиринтные уплотнения, которые состоят из гребешков и камер.
|
|
|
Гребешки лабиринтных уплотнений располагаются на подвижных деталях. При перетекании воздуха через щели скорость растет, давление падает, а при попадании его в камеры – наоборот, но из-за наличия потерь на вихреобразование, давление не восстанавливается до начального. Т.о. действие лабиринтного уплотнения заключается в многократном дросселировании воздуха при протекании его через каналы, резко меняющимися сечениями. Уменьшить утечку воздуха через лабиринт можно, уменьшив зазор, увеличив число гребешков и камер. Уменьшению зазора между подвижной и неподвижной деталями препятствует опасность задевания гребешков по неподвижной детали при деформации ротора или корпуса. Это может привести к разрушению лабиринтного уплотнения. Разрушение можно избежать, если нанести на не подвижную деталь мягкое покрытие, в котором гребешки лабиринта могут прорезать канавки, оставаясь не поврежденными.
|
|
Газовые турбины.
Турбина расположена между камерой сгорания и реактивным соплом или форсажной камерой. Турбины разделяются на одноступенчатые и многоступенчатые. Многоступенчатые турбины различаются по числу валов. В ТРД двухвальная турбина применяется при двухроторных осевых компрессорах. В ТВД двухвальная турбина приводит отдельно компрессор и винт. В авиационном двигателе в основном используются осевые турбины. Радиальные турбины применяются в основном на вспомогательных силовых установках. По конструкционным признакам газовые турбины можно разделить:
- По способу охлаждения сопловых и рабочих лопаток:
турбины с неохлаждаемыми сопловыми и рабочими лопатками. Детали этих турбин изготавливаются из высококачественного материала, механические свойства которых сохраняются при рабочих температурах нагрева лопаток. Эти лопатки охлаждаются вследствие теплопроводности материала;
турбины с воздушным охлаждением сопловых и рабочих лопаток. Для охлаждения в лопатках выполняются каналы, по которым движется воздух. Пройдя лопатки нагретый воздух выходит газовый тракт и смешивается с газами;
турбины с водяным или топливным охлаждением. Недостатком такой системы является ее сложность, а также надежная работа уплотнительных устройств и при такой системе охлаждения увеличивается масса двигателя;
|
|
- По конструкции ротора:
турбины с неразъемным ротором;
турбины с разъемным ротором.
- По расположению дисков:
турбина с консольным расположением дисков;
турбина с расположением дисков между опорами.
Газовая турбина состоит из неподвижной части – статора и подвижной – ротора турбины. Ротор турбины состоит из вала и дисков с рабочими лопатками. Опорами вала турбины обычно являются цапфы компрессора и роликовый подшипник, расположенный вблизи дисков. Для уменьшения массы турбин применяется консольное расположение дисков с подшипником перед турбиной. Для уменьшения изгибных напряжений на валу диски могут располагаться между опорами. При соединении диска турбины с валом, необходимо иметь ввиду ряд особенностей, относящихся к валу и всему узлу газовой турбины:
- большой передаваемый крутящий момент;
- повышенная температура места соединения вследствие передачи тепла от диска;
- возможность появления вибрационных нагрузок из-за неуравновешенности ротора, пульсации газа на лопатках турбины;
- возможность появления дополнительных напряжений из-за недостаточной жесткости опор;
- появление значительных изгибных нагрузок при маневрах самолета;
- необходимость сохранения центровки деталей во всем интервале рабочих температур во избежание нагружения балансировки.
Ротора турбины, в зависимости от конструкции двигателя могут выполняться неразъемными и разъемными. Неразъемный ротор не допускает разъединения и соединения рабочих колес при монтаже на двигателя. Рабочие колеса разъемных роторов можно последовательно монтировать в двигателе, чередуя их соответствующими сопловыми аппаратами. При этом должны быть обеспечены соосность опорных поверхностей роторов , центрирование элементов ротора относительно статера, а также должно быть предотвращено увеличение остаточного дисбаланса, достигнытого после балансировки. Неразъемные роторы соединяются при помощи сварки, радиальных штифтов, напрессовки дисков на шлицевой вал и сопряжения фланцев диска и вала на эвольвентных шлицах с затяжкой болтами. К разъемным роторам относятся ротора с различными соединениями, посредством болтов, в том числе при иомощи призонных болтов, торцевых шлицев с центральным стяжным болтом или несколькими болтами, расположенными по окружности фланца. Широкое распространение имеют неразъемные роторы, соенинение при помощи радиальных штифтов и разъемные роторы, соединенные призонными болтами.
Неразъемный ротор турбины:
1-хвостовик вала;
2-шлицевая втулка;
3-вал;
4-внутреннее кольцо шарикоподшипника;
5-втулка вала;
6-втулка масляного лабиринта;
7, 8, 14-штифт;
9,16-диски I и II ступеней;
15-силовое кольцо;
17-балансировочный винт;
18-дистанционное кольцо;
19-кольцо замка;
20-контровочное кольцо;
21-гайка;
22-центрирующий буртик.
|
Разъемное соединение ротора турбины:
1-вал;
2-болт;
3-стопорное кольцо;
4, 5-диски II и III ступеней;
6-контровочная шайба;
7-гайка;
8-лыска;
9-конус.
Диск первой ступени с натягом напрессовываются на фланец вала 3 и на бурт кольца 15. диск второй ступени напрессовывается с натягом на силовое кольцо 15. при напрессовке диски нагреваются до температуры 425 К. отверстия для штифтов развертываются после напрессовки и в них с натягом запрессовываются радиальные фтифты, которые фиксируются в осевом направлении обжимом наружных кромок отвнрстий. Для предотвращения задиров при запрессовке штифты азотируются. Все элементы соединений расиолпженны на относительно малых радиусах. Это обеспечивает их устойчивую работу в условиях более низких температур. Соединительные элементы дисков являются охватывающими по отношению к валу и силовому кольцу. Это предотвращает нагружение вала и кольца растягивающими напряжениями. В случае высокой температуры дисков с другой стороны силовое кольцо под действием центробежной силы растягивается больше дисков, что обеспечивает стабильность посадки. Тем не менее в роторе предусмотрено дополнительное центрирование буртиками 22, в котором вал является охватывающим элементом диска. Центрирующие элементы расположены с гарантированным зазором в холодном состоянии, но могут находиться в контакте при быстром выходе двигателя на режим, однако, опыт эксплуатации показывает, что штифты также является надежными центрирующими элементами.
Изобразим вильчатое штифтовое соединение:
|
- элементы вилки одного из дисков
- соединительный элемент сопряженного диска или вала
- штифт
- упорный торец
5, 6 центрирующая поверхность.
На вильчатом штифтовом соединении имеются двухопорные штифты. Это делает соединение более прочным и жестким, т.к. в штифте на срез работают два сечения. В зависимости от принятого способа центрирования элементы 1 и 2 могут сопрягаться по поверхностям 5 или 6. способ центрирования выбирается в зависимости от напряжений под действем центробежных сил, материалов сопрягаемых деталей и их температурного состояния. Число и диаметр штифтов выбирается в зависимости от действующих нагрузок. В применяемых соединениях диаметры штифтов выбираются в пределах 4-10 мм, длина штифтов 7,5-18 мм, расстояние от торца 4 до оси штифтов от 5 до 12 мм.
При разъемных соединениях ротора турбины, рабочие колеса 4 и 5 вторых и третьих ступеней центрируются и крепятся при помощи призонных болтов по обоим сторонам фланца вала ротора. Конические пояски болтов с натягом входят в аналогичные отверстия дисков. Посадка на конические пояски обеспечивает надежное центрирование дисков относительно вала, а мыски на болтах допускают не значительное перемещение дисков в радиальном направлении в результате теплового расширения и сжатия. Имеющиеся стопорные кольца предотвращают выпадение болтов при постановке рабочего колеса третьей ступени. Призонные болты воспринимают все нагрузки на диски и валы.
Соединение лопатки с диском.
Соединение рабочей лопатки с диском - елочного типа. Это напряженное и ответственное место в конструкции газовой турбины. Соединение передает на диск все нагрузки, действующие на рабочие лопатки. Достоинства соединения:
- клиновидная форма замковой части обеспечивает близкое к равномерному распределение напряжений в расчетных сечениях;
- относительно малые размеры паза позволяют разместить большое число лопаток;
- свободная, с зазором установка лопаток в диск устраняет возникновение температурных напряжений в соединении;
- наличие зазоров между зубьями лопаток и диска допускает продувку соединений воздухом, обеспечивая некоторое охлаждение;
- возможна легкая замена лопаток в процессе сборки и ремонта.
Недостатки:
- затрудненный теплоотвод от лопатки в диск из-за малой суммарной поверхности контакта зубьев;
- значительная концентрация напряжений вблизи малых радиусов впадин;
- необходимость изготовления с высокой точностью пазов в диске и в хвостовике рабочих лопаток.
Дата добавления: 2018-04-05; просмотров: 918; Мы поможем в написании вашей работы! |
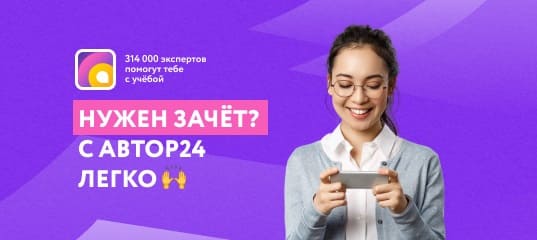
Мы поможем в написании ваших работ!