Особенности температурно-временного режима обжига и процессы, происходящие при обжиге динасовых огнеупоров
Динасом называют огнеупор, содержащий не менее 93% Si02, изготовляемый из кварцевых пород с известково-железистым или иным минерализатором, обеспечивающим полиморфное превращение кварца в тридимит и кристобалит.
Обжиг динаса является одной из важнейших и ответственных стадий технологического процесса. При обжиге динаса происходит взаимодействие Si02 и СаО с образованием метакальциевого силиката, дающего с метасиликатом монооксида железа твердый раствор. При температуре около 900°С образуется богатый Si02 расплав, который растворяет кварц и метакристобалит, а из насыщенного расплава выкристаллизовывается тридимит; при охлаждении расплав застывает в стекловидное вещество.При высокой температуре зерна кварца растрескиваются и растворяются в расплаве.Роль расплава заключается в снижении напряжений, возникающих при различных превращениях кварца, связывании кристаллических частиц и заполнении образующихся трещин, частичном растворении кварца.В отсутствие жидкой фазы увеличивающиеся зерна кварца, лишенные подвижности, не в состоянии разместиться в объеме изделия за счет его пор; трещины не заполняются жидким стеклом и изделие не в состоянии сохранить свои размеры.Чтобы предохранить динас при обжиге от разбухания и трещиноватости, в печи необходимо поддерживать слабо восстановительную среду, которая при наличии минерализаторов обеспечивает образование жидкой фазы при достаточно низкой температуре в связи с переходом Fe^O^ в FeO и плавления эвтектической жидкости в системе СаО—FeO—Si02.Максимальная температура обжига динасовых изделий составляет 1430— 1450"С. На конечных стадиях обжига скорость нагревания изделий должна быть небольшой, чтобы преимущественно образовался тридимит, а не кристобалит, что уменьшает вероятность возникновения трещин. При кристаллизации тридимита из расплава его кристаллы срастаются между собой, образуя прочный каркас, в порах которого располагается стекловидная фаза. Такое строение огнеупора обеспечивает высокую температуру деформации под нагрузкой. Научно обоснованный режим обжига, учитывающий физикохимические процессы на различных стадиях, обусловил продолжительность обжига в туннельных печах в течение 5—8 сут, а в периодических печах для сложных фасонных изделий — 15—18 сут. Контроль качества динаса, т. е. степени перерождения кварца в тридимит и кристобалит в обжиге, может быть осуществлен различными методами: определением истинной плотности; рентгепофазо- вым количественным, микроскопическим и дилатометрическим анализами. Требования к динасу регламентируются ГОСТом
|
|
Важнейшими свойствами динаса являются высокая температура начала деформации, составляющая под нагрузкой 0,2 МПа в среднем 1650°С, отсутствие заметного расширения динаса при температурах выше ~600°С, что позволяет использовать этот материал в диапазоне 600— 1600°С в условиях резких термоударов.
|
|
Билет 14.
Шамотные огнеупоры: сырьевые материалы, технология изготовления, свойства, применение.
Шамотными называют изделия, изготавливаемые из огнеупорных глин и каолинов с отощением их шамотом или непластичной не размокающей в воде глинистой породой. Шамотом называют обожженную глину.
Сырьевые материалы. Сырьем для производства шамотных изделий служат глинистые материалы, содержащие не менее 28% AI2O3 и имеющие огнеупорность не ниже 1580°С. Максимальное содержание Л12О3 в шамотных изделиях может достигать 45% при использовании чистых каолинов.
Технологический процесс производства. В производстве шамотных изделий огнеупорную глину применяют в качестве дисперсной связки и для получения отощающего материала — шамота.
Подготовка связующей глины. Карьерную глину с влажностью примерно 20% перед измельчением высушивают до влажности 8—11%. Для более эффективной работы сушильного аппарата глину предварительно дробят на мелкие куски при помощи глинорезательной машины (етругача).
|
|
Глину сушат в сушильных барабанах, работающих по принципу прямоточного движения глины и горячих газов, что позволяет использовать газы с температурой до 600—800°С без опасения перегрева глины до ее частичной дегидратации. Продолжительность пребывания глины в барабане зависит от длины барабана, его наклона и скорости вращения. Температура отходящих из барабана газов должна быть не ниже 110—120°С. При более низких температурах возможна конденсация паров воды на выходящей из барабана глине.
При уменьшении остаточной влажности в глине до 3—5% увеличивается количество уносимой дымовыми газами глинистой пыли и при последующем измельчении глины возрастает пылеобразование. Повышение влажности сверх указанной нормы увеличивает крупность помола и вызывает налипание глины па пальцы корзин дезинтегратора.
Нормальная работа дезинтегратора требует равномерной подачи глины кусками размером 15—35 мм, что достигается установкой питателя. Для предотвращения попадания в дезинтегратор металлических предметов перед дезинтегратором устанавливают магнитный сепаратор.
|
|
Помол глины в дезинтеграторе при нормальной ее влажности позволяет получить до 80% частиц менее 0,5 мм. Более крупные зерна отделяют на ситах.
Установка воздушного сепаратора после дезинтегратора позволяет отделять меньшие по размеру частицы, однако при этом увеличивается расход электроэнергии.
После магнитной сепарации измельченная отсеянная глина поступает в бункер
Подготовка шамота. При производстве шамотных изделий в качестве отощающего материала применяют шамот, т. е. предварительно обожженную глину с определенной величиной зерна.
Стину для получения шамота иногда обжигают в шахтных печах с газовым отоплением. Для равномерного питания печей однородной кусковой глиной с предельной величиной —200 мм ее необходимо брикетировать. Для этого ее дробят, увлажняют и перерабатывают на ленточном прессе. Выходящий из пресса брус разрезают на брикеты, которые без допрессовки поступают на сушку и обжиг. Значительное улучшение качества брикета и увеличение его прочности достигается с помощью пресс-вальцов
Наиболее эффективным агрегатом для обжига глины на шамот является вращающаяся печь, в которой можно обжигать глину в виде шлама, например после мокрого обогащения. Подача и выгрузка сырья просты и полностью механизированы, достигается высокая температура обжига и большая степень спекания шамота, устраняется неравномерность обжига, присущая шахтным печам. Небольшой размер кусков выходящего из печи шамота исключает необходимость его дробления. Однако при использовании шлама имеет место значительный пылеунос, достигающий 10—15%. Поэтому для обжига применяют глину в виде кусков, полученных после стругача, или в виде брикетов небольшого размера, получаемых с помощью пресс-вальцов. Обожженный шамот подвергают дроблению до зерен заданного размера.
Критерием качества является его водопоглощение: оно должно быть менее 5%, у особо качественного — менее 2%. Качество шамота зависит от свойств глины и способа ее подготовки, плотности брикета, температуры обжига.
Дельный расход условного топлива при обжиге глины на шамот во вращающихся печах примерно в 1,5 раза выше, чем в шахтных печах.
Вращающиеся печи используют прежде всего на крупных заводах, а также при производстве различных высокоогнеупорных материалов, требующих весьма высоких температур обжига. Преимуществом обжига глины на шамот во вращающихся печах является устранение рада подготовительных операций, что видно из приведенных схем.
Дробление и измельчение шамота. Шамот дробят и затем измельчают до предельной величины зерна 3-4 мм при содержании мелкой фракции (мельче 0,5 мм) около 40—45%. Для этого шамот дробят в щековых, реже в конусных дробилках до кусков размером 20—30 мм, а затем измельчают в шаровых мельницах непрерывного действия с периферийной разгрузкой либо в трубных мельницах.
При многошамотной технологии изделий используют плотноспекший- ся шамот с водопоглоще- нием менее 3—5% и определенным соотношением крупных (3-1 мм) и мелких (менее 0.1—0,2 мм) фракций, производя рассев измельченного шамота на фракции и их последующее смешивание для приготовления шихты. Более дешевым и простым считают двухступенчатый помол с целью получения фракций разного размера: крупной фракции — на вальцах или короткоконусной дробилке и мелкой фракции — в трубной мельнице. При этом требуется просев шамота лишь крупной фракции для ограничения предельной величины зерна (3—4 мм); количество мелкой фракции при измельчении на вальцах и дробилке получается в допустимых пределах. Измельченный шамот обязательно отмагничивают и затем подают в бункера.Подбор зернового состава шамота. Наиболее существенным фактором в производстве шамотных изделий является зерновой состав шамота, регулируя который можно изменять их свойства, например получить плотный и прочный огнеупор повышенной шла неустойчивости или менее плотный зернистого строения, но более термостойкий.В обычных шамотных массах, содержащих 40—50% связующей глины и шамот с непрерывным зерновым составом, плотность укладки зерен шамота не обеспечивает получения изделий высокой плотности Изменяя содержание в шамоте наиболее мелкозернистой фракции, можно лишь в некоторой ограниченной мере регулировать свойства изделий. Так, увеличение количества этой фракции, даже независимо от повышения предельной крупности зерна до 4—5 мм, увеличивает прочность, плотность и непроницаемость изделий, однако термическая стойкость при этом несколько снижается, а усадка повышается на 2—3%. Наоборот, уменьшение количества мелкозернистой фракции, даже при снижении предельной крупности зерна до 1 —2 мм, вызывает разрыхление изделий и уменьшение их прочности. При этом повышаются пористость и термическая стойкость. Это обусловлено образованием внутренних разрывов и микротрещин между связкой и зерном и в самой связке из-за снижения общей усадки изделий ввиду образования каркаса из крупных зерен шамота. Ря довой шамот для изделий общего назначения с 40-50% связующей глины содержит около 40—45% зерен размером менее 0,5 мм и около 25—30% зерен меньше 0,2—0,1 мм.Большинство огнеупоров, в том числе и из огнеупорной глины, изготавливают по так называемой многошамотной технологии, где имеется возможность существенного регулирования пористости, газопроницаемости, усадки, термостойкости, т. е. свойств, от которых зависит стойкость изделий в службе. Количество шамота доводят до 80—85%, при этом незначительное количество глины, присутствующей в массе и тонким слоем покрывающей зерна шамота, мало влияет на плотность их укладки. В связи с этим возможно осуществить максимально плотную укладку зерен путем создания разрывного зернового состава при использовании двух фракций шамота — крупной с размером зерен 3—0,5 мм и мелкой — менее 0,1 мм. При этом мелкая фракция заполняет свободное пространство между плотно уложенными крупными зернами, что позволяет существенно снизить пористость изделий. Для повышения плотности изделий мелкую фракцию шамота смешивают с глиной в трубных мельницах. При получении высококачественных изделий по многошамотной технологии необходимо выдерживать определенные требования, предъявляемые к зерновому составу шамота, обеспечивающего плотнейшую упаковку частиц и низкую пористость изделий. Эти требования сводятся к следующим: шамот должен иметь низкое (<2%) водопоглощение; фракции шамота должны быть узкими; разрыв между размером фракций должен быть в 8—10 раз; количество мелкого шамота должно быть таким, чтобы он заполнял промежутки между крупными зернами; при использовании двух фракций их отношение должно быть примерно 3:7 (30% мелкой и 70% крупной). Дальнейшее увеличение количества фракций дает лишь небольшое повышение плотности; к тому же, исходя из технологических соображений, нельзя применять зерна очень крупного размера, а использовать фракции шамота менее 10—20 мкм нецелесообразно, так как их трудно получить, а кроме того, роль третьей мельчайшей фракции играет вводимая в массу глина. Поэтому на практике ограничиваются двумя фракциями шамота. Максимальную плотность обожженного изделия при содержании 15—20% глины получают при содержании крупной фракции (3—0,5 мм) —50—40%, мелкой (менее 0,1 мм) — 35—40%. Указанное количество глины оказывается достаточным, чтобы обеспечить в условиях хорошего контакта вместе с мелкой фракцией шамота интенсивное спекание и упрочнение изделий при температуре ~ 1400°С. Подготовка массы и формование изделий. Наиболее широко для формования огнеупоров используют полусухое прессование по представленной выше схеме. Обработка массы перед прессованием оказывает решающее влияние на качество изделий. Для обработки шамотной и многошамотной массы применяют тяжелые смесительные бегуны. При этом необходимо равномерно распределить глину и шамот, уплотнить массу, обеспечить контакт зерен шамота с глиной, что повышает плотность изделий при прессовании. При подготовке обычных шамотных масс с большим количеством глины в бегуны сначала загружают шамот. Для лучшего сцепления шамотных зерен с глиной их замачивают глиняным шликером с влажностью -70%, который готовят из части вводимой глины и разжижителей-электролитов. Количество шликера должно быть таким, чтобы вместе с остальной глиной в целом влажность массы составляла 8—9%. При перемешивании шамота, смоченного шликером, происходит впитывание влаги шликера зернами шамота и на их поверхности образуется тонкая глинистая пленка, облегчающая в дальнейшем связь с остальной связующей глиной. Затем к замоченному шликером шамоту добавляют остальную глину в виде тонкого порошка. Перемешивание и перетирание массы под тяжестью катка обеспечивает образование хорошей связи между зернами и глиной, которая плотно налипает на влажные зерна. При подготовке многошамотных масс необходимо применять тонкодисперсную высокопластичную глину, при этом часть глины следует использовать в виде шликера. Для равномерного распределения глины по поверхности шамотных зерен необходима особо тщательная обработка массы в смесителе. Для увеличения связности массы и прочности отпрессованных изделий в глиняный шликер обязательно добавляют 0,5— 1 % J1CT (считая на сухую массу). При обработке массы в бегунах может иметь место нежелательное изменение зернового состава шамота в результате домола крупной фракции. Поэтому многошамотную массу рекомендуется перемешивать в следующей последовательности: мелкозернистый шамот подают в смесительные бегуны и замачивают шликером, затем туда же вводят остальную глину; полученную массу смешивают с крупнозернистым шамотом. Последняя стадия перемешивания массы в достаточно толстом слое и особенно при возможности регулирования давления катка уменьшает домол крупной фракции. Для обеспечения более тесного контакта глины с тонкой фракцией шамота и домола крупных комков глины их предварительно перемешивают в трубной мельнице. Полученная таким образом тонкая смесь совместного помола поступает в смесительные бегуны, в нее вводят шликер и затем крупную фракцию шамота. Следует отметить, что при запуске в смеситель первоначально тонкой фракции шамота из-за негерметичности оборудования возможно сильное пыление. Поэтому обычно уменьшают давление катка на чашу и первоначально загружают крупную фракцию шамота, которая в этих условиях при последующем смешивании со шликером домалывается очень незначительно, затем добавляют глину, перемешивают с крупной фракцией шамота, потом добавляют тонкую фракцию или смесь совместного помола. Когда материалы полностью загружены, давление катка на массу возрастает, что приводит к ее уплотнению, но крупная фракция сохраняется, так как нет непосредственного дробящего действия от катка в связи с тем, что зерна окружает мягкая масса в виде глины. Такая последовательность смешивания обеспечивает беспылевую работу агрегата, хорошую обработку массы и небольшой домол крупной фракции . Иногда используют упрощенный способ изготовления многошамотных масс. Заполнителем служит нефракционированный шамот с предельной величиной зерна 3—4 мм и содержанием мелкой фракции (<0,5 мм) 40—60%. Количество глины в массе составляет 20—25%, перемешивание шамота и глины осуществляют по схеме, принятой для обычных шамотных масс.Прессование обычных шамотных масс осуществляют на коленно- рычажных прессах при давлении около 40 МПа. Многошамотные массы прессуют при повышенных давлениях — 80—100 МПа. Для этих целей используют коленно-рычажные прессы и мощные гидравлические 1000- и 1500-тонные прессы, одновременно прессующие три кирпича нормальных размеров при давлении около 125 МПа. Изделия снимают со стола пресса механическими захватами, приводимыми в действие сжатым воздухом. При многошамотном производстве повышается себестоимость изделий из-за большего содержания шамота, большего износа оборудования и пресс-форм, более тщательной переработки массы, более мощного прессового оборудования и более высокой температуры обжига. Поэтому такую технологию используют при изготовлении ответственных изделий (ковшевого и доменного припаса, подвесного свода нагревательных печей и др.). Стоимость многошамотных изделий на 20—25% выше, чем обычных огнеупоров.Сушка и обжиг. Исходные заготовки в зависимости от способа формования содержат от 5 до 20% воды. Перед обжигом их необходимо высушивать до минимальной влажности. Введение шамота в массы значительно облегчает сушку благодаря пористости и увеличению размера пор, по которым влага свободно выходит из объема изделий.Шамотные изделия сушат главным образом в туннельных сушилках, оборудованных приборами для автоматического регулирования температуры и влажности теплоносителя, что обеспечивает равномерность высушивания изделий при минимальном браке.Полусухое прессование огнеупоров допускает форсированный режим сушки. Теплоносителем служит воздух, взятый из зоны охлаждения печи, его температура при входе 180—250с,С, при выходе — 60—80°С. Изцелия из сушилки поступают в туннельную печь нагретыми до температуры примерно 50"С. Продолжительность сушки составляет обычно 10—12 ч и зависит от габаритов изделий. Во избежание повреждений углов и ребер изделий при перекладке с вагонетки на вагонетку их после прессования сразу устанавливают на печные вагонетки, которые после сушилки поступают непосредственно в туннельную печь. Обжиг является завершающим этапом производства. В отличие от многих других огнеупоров обжиг шамотных изделий относительно прост. Процессы перекристаллизации и образования муллита, достижение равновесия в фазовом составе не являются решающими. Обжиг должен обеспечить спекание в такой степени, чтобы изделия имели постоянство объема в последующей службе при высокой температуре, необходимую прочность и заданную пористость. При обжиге шамотных изделий процессы спекания и формирования фазового состава связаны с физико-химическими превращениями, проходящими в глинистой со ставляющей, так как в зернах шамота они завершены при его получении. Значительные объемные изменения глины при спекании могли бы быть причиной возникновения трещин на изделиях. Однако при введении в массу шамота, уменьшающего усадку до 1 —3%. а в многошамотных — до 0,2—0,5%, и умеренных скоростях обжига трещин обычно не возникает. Этому также способствуют пластические свойства шамотного огнеупора, приобретаемые им при температурах интенсивного спекания (1100— 1250°С) вследствие образования жидкой фазы.Обжиг шамотных изделий обычно завершается при температуре, превышающей на 100— 150°С температуру спекания связующей глины. Это необходимо для равномерного интенсивного прогревания изделий по всему сечению и завершения всех процессов, связанных с формированием фазового состава огнеупора. Выдержка (5—6 ч)при максимальных (1350— 1400°С) температурах необходима, так как завершение всех процессов проходит во времени.Процесс охлаждения шамотных изделий сопровождается лишь нормальным термическим сокращением их объема; скорость охлаждения изделий обычно составляет 60—80°С в 1 ч. Обожженные огнеупоры содержат около 50% кристаллической фазы, в основном муллита, -50% стекловидной фазы, образующейся из дисперсного кремнезема, выделяющегося из каолинита, и 5—7% примесей, содержащихся в исходном сырье. Игольчатые кристаллы муллита равномерно распределены в стекловидной фазе. Шамотные изделия обжигают главным образом в туннельных печах. В периодических печах обжигают лишь большемерные и фасонные изделия, требующие индивидуальных режимов обжига и разнооб разной конфигурации садки Современная типичная туннельная печей для обжига шамотных изделий имеет длину 120, ширину — 3, высоту — 2,1 м. В нее помещают 40 вагонеток длиной по 3 м. На каждую из них грузят 12—14 т изделий. Печи отапливают мазутом или природным газом Продолжительность обжига составляет 32—36 ч.
Дата добавления: 2018-04-04; просмотров: 189; Мы поможем в написании вашей работы! |
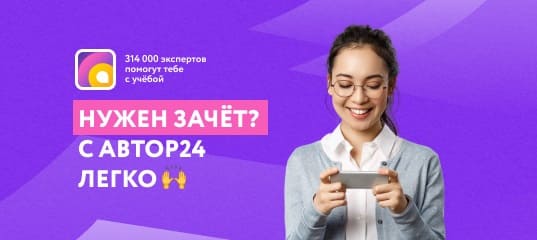
Мы поможем в написании ваших работ!