Билет 18. 2.Магнезитовые (периклазовые) огнеупоры, особенности технологии, свойства и применение
Магнезиальными (периклазовыми) называют огнеупоры, содержащие не менее 85% MgO. Их используют для кладки различных печей, футеровка которых контактирует с расплавами металлов и основных шлаков. Магнезитовые порошки применяют для набивки пода металлургических печей, торкретирования их футеровки, в качестве заполнителей бетонов; они являются также сырьем для производства периклазсодержащих изделий.
Сырьем для производства периклазовых огнеупоров является магнезит, состоящий в основном из карбоната магния. Природный магнезит содержит около 9% примесей, в том числе 2-2,5% СаО, 2-2,5% Si02, ~3% Fe203 и 1 % А1203, которые существенно влияют на фазовый состав и свойства огнеупоров.
Технологический процесс производства периклазовых изделий включает операции: измельчение спекшегося магнезита, его рассев на две фракции, их дозировку в необходимом соотношении, увлажнение с введением небольших(0,5— 1 %) количеств органических клеящих добавок, прессование, сушку и обжиг изделий. В качестве тонкой фракции в периклазовых изделиях применяют получаемый в трубных мельницах тонкомолотый обожженный магнезит, который вводят в состав массы в количестве до 40%. Влажность приготовленной шихты обычно составляет около 3—5%.
На способ приготовления массы в производстве периклазовых изделий влияет наличие в обожженном магнезите свободного оксида кальция, который образуется при прокаливании примеси СаС03. Гидратация оксида кальция в изделиях может приводить к их растрескиванию, поэтому свободный оксид кальция предварительно гидратируют, а массу затем перемешивают для равномерного распределения порошка гидроксида кальция по объему шихты.Этот процесс осуществляют в бункерах, куда порошок поступает предварительно увлажненным в двухвальных смесителях. При вылеживании температура порошка не должна превышать 40—45°С. После вылеживания в течение 2—3 сут порошки перемешивают и увлажняют раствором JICT. Для ускорения гидратации массу подогревают паром в сушильных барабанах, при этом температуру подогрева подбирают так, чтобы не было кристаллизации гидроксида магния.Для получения достаточно плотных изделий шихта должна иметь следующий зерновой состав фракций: 1—0,5 мм — 20-30%, 0,5-0,088 мм - 30-50%, <0,06 мм - 30-50%.Изделия формуют на гидравлических прессах при давлении 80—120 МПа для получения высокой плотности заготовок. Высушивают изделия во избежание гидратации периклаза при невысоких (50—60°С) температурах сухим воздухом при большом коэффициенте обмена.Обжигают периклазовые изделия в туннельных печах. Особенность обжига заключается в сравнительно небольшой (примерно 1 м) высоте садки изделий, причем изделия укладывают на их большую плоскость (плашку). Необходимость такой садки обусловлена тем, что температура обжига изделий превышает температуру начала деформации. Температура обжига обычно составляет 1600— 1750°С.Обожженные обычные изделия имеют пористость около 25%, температуру начала деформации — 1550°С, прочность на сжатие — около 50 МПа. Применение для изделий плотного, хорошо спеченного магнезита при уменьшенном максимальном размере частиц позволяет снизить пористость до 12—15%.Для повышения качества изделий на основе природного магнезита применяют его обогащение и введение добавок оксида алюминия и хромита. Обогащение сырья до содержания MgO более 98% позволяет изготавливать изделия с очень малым количеством расплава, преимущественно с прямой связью между кристаллами периклаза, что резко повышает температуру начала деформации, химическую и термическую стойкость.
|
|
|
|
1.Приведите классификацию глазурей по плавкости и рассмотрите способы их приготовления.По температуре плавления глазури делятся на легкоплавкие и тугоплавкие. Глазури для гончарных изделий и майолики имеют температуру плавления 850-1100°С (легкоплавкие), для фаянсовых изделий 1100-1200°С, для фарфора и каменного товара 1200-1400°С (тугоплавкие). Плавкость регулируют составом. Тугоплавкие содержат больше Al2O3, SiO2 и меньше щелочных оксидов, легкоплавкие наоборот - поэтому их обычно фририттуют. Способ приготовления легкоплавких глазурей: Фриттованные глазури. При наличии в шихте глазури растворимых в воде компонентов она, как правило, сплавляется (фриттуется) или спекается при температуре на 300-400°С выше температуры плавления глазури. Фриттуют и глазури содержащие токсичные вещества (РbО). Не обязательно все компоненты глазури сплавлять, некоторые (например каолин и глину) лучше добавить при помоле. При сплавлении глазури растворимые компоненты шихты взаимодействуют с другими ее составляющими и образуют нерастворимые силикаты. Фриттованные глазури более легкоплавки, чем сырые того же состава, качество поверхности после обжига у них выше. Это объясняется тем, что сырая глазурь образует стекловидную плёнку в процессе обжига на поверхности изделия, для чего необходимо затратить больше энергии и времени, чем для того, чтобы только расплавить готовое стекло в случае фриттованной глазури. Тонкий помол способствует их скорейшему созреванию. Легкоплавкие глазури по способу приготовления делятся на фриттованные и нефриттованные (сырые).
Фриттованные глазури получают сплавлением смеси сырьевых материалов при температуре 1300-1450°С. Главное назначение фриттования - сплавление растворимых в воде компонентов фритты и перевод их в нерастворимое состояние. Следует иметь в виду, что температура плавления у фриттованных глазурей на 100-150 °С ниже по сравнению с сырой глазурью аналогичного состава, так как необходимые химические процессы образования силикатов и других соединений у фриттованных глазурей происходят уже во время их плавления. При приготовлении сырых глазурей, в отличие от фриттованных, шихтовую смесь загружают непосредственно в шаровую мельницу мокрого помола и после достижения необходимой тонины помола (остаток на сите №0063 К 0,1-0,2%) сливают в емкости-мешалки для хранения.
Нефриттованныеглазури нашли наиболее широкое применение в производстве санитарно-технических изделий. Наиболее широко применяются матовые глазури. Поскольку покрытие на керамике, полученное на основе нефриттованных глазурей, также представляет собой стекловидный слой, то в отношении его можно применять известные положения стеклообразного состояния. Необходимо учитывать, что при термообработке покрытия на основе фритты в условиях обжига происходят преимущественно процессы плавления глазури и взаимодействия ее с керамической основой, в то время как при обжиге сырой глазури непосредственно на поверхности керамического черепка протекают процессы разложения сырья, полиморфные превращения, стеклообразование и кристаллизация расплава, а также происходит взаимодействие с керамической основой. Нефриттованные глазури применяются в основном для декорирования фарфоровых, реже фаянсовых изделий, изделий технической керамики и характеризуются высокой температурой формирования покрытий. Сырые глазури - самые простые в изготовлении. Сырьевые материалы взвешиваются согласно рецепту, перемешиваются и полученная шихта загружается в шаровую мельницу с водой. Соотношение мелющихся тел, шихты и воды примерно1:1. Помол глазури осуществляется в течение 48-72 часов в зависимости от прочности сырьевых материалов и правильно подобранной скорости вращения мельницы. Затем глазурная суспензия процеживается через сито 4900-64000 отв/см2 и доводится до нужной консистенции добавлением воды или, при ее избытке, отстаиванием и сливанием. В составе сырых глазурей не должно быть компонентов, растворимых в воде, в противном случае эти компоненты (сода, борная кислота, кристаллическая бура, поташ и др.) при нанесении глазурной суспензии на изделие вместе с водой уйдут в пористый черепок, изменив состав глазури.
|
|
|
|
Билет 16 1. Выбор температурно-временного режима обжига керамических изделий с учетом происходящих физико-химических процессов. Причины возникновения механических напряжений при обжиге керамических изделий и пути их снижения. Не менее сложно подбирать состав керамической массы и температуру ее обжига. На практике поступают следующим образом. В том случая, если сетка трещин глазури крупная (несоответствие КТР невелико), повышают температуру обжига изделий на 30-50°С, или увеличивают время обжига. В обоих случаях создаются условия для лучшего развития промежуточного слоя, который является как бы буфером выравнивающим напряжения, возникающие между стеклом и черепком. КТР промежуточного слоя имеет среднее значение между КТР глазури и КТР черепка. Нанесение глазури более тонким слоем также способствует лучшему согласованию глазури с черепком. Часто цек образуется не сразу после обжига, а с течением времени. Это объясняется тем, что пористый силикатный черепок способен при поглощении несколько увеличиваться в объеме. Появлению цека способствует и разница температур между внутренней и наружной сторонами черепка.Цикл обжига керамических изделий состоит из периодов нагревания, выдержки в области максимальных температур и охлаждения.
Целью обжига является завершение химических реакций и фазовых превращений, уплотнение керамики, достижение заданных свойств и микроструктуры. Например, при обжиге динасовых огнеупоров процесс оценивают по степени превращения исходного кварца в тридимит и кристобаллит, что требует определенной температуры выдержки, которую можно варьировать. Для завершения спекания температура обжига является более существенным фактором, чем время выдержки. Снижение температуры требует поэтому резкого увеличения выдержки. С технико-экономической точки зрения рационален относительно короткий обжиг при высоких температурах. Именно так и поступают при получении изделий из AI2O3 с добавками 0,5— 1 мае. % MgO, частично стабилизированного Zr02 и т. п.
Значительные вариации температуры и времени выдержки возможны для материалов с широким интервалом спекшегося состояния, когда изменение параметров обжига влияет преимущественно на кинетику спекания и рекристаллизацию, например при обжиге высокоогнеупорной оксидной керамики Существенные изменения температуры допустимы и при жидкофазном спекании, если содержание расплава и его вязкость мало меняются с температурой, например при обжиге изделий из огнеупорных глин. Однако для стеатитовой, форстеритовой, кордиеритовой керамики интервал допустимых температур обжига не должен превышать 20—40°С. По этому предпочитают увеличивать продолжительность выдержки, задавая температуру у нижней границы допустимого предела, строго соблюдая однородность температурного поля в печном пространстве. Время выдержки зависит также от формы и размеров изделий, поскольку продолжительность выравнивания температуры в объеме изделия пропорциональна квадрату его толщины. Для получения лучших результатов режим обжига должен быть оптимизирован по наиболее важным свойствам обжигаемых изделий с учетом процессов, протекающих в обжигаемой заготовке. Период нагревания - важная стадия обжига, на которой необходимо по возможности быстро достичь максимальной температуры, избежав при этом разрушения или повреждения, которые обусловлены объемными изменениями изделий либо интенсивны ми процессами массообмена. Удаление остатков воды, сохранившихся в заготовке после сушки, не связано с объемными изменениями, но при больших скоростях нагревания происходит увеличение давления пара в порах, которое может вызвать мгновенное разрушение изделия. Поэтому примерно до 200-300°С скорость нагревания, особенно крупных, должна строго лимитироваться. При обжиге тонкостенных и хорошо высушенных массивных изделий скорость нагревания может быть большой. Выделение химически связанной воды и других продуктов разложения сырьевых компонентов (глины, талька, карбонатов идр.) протекает в широком температурном интервале и обычно не вызывает напряжений и разрушения изделий. Эти процессы необходимо завершить до начала интенсивного спекания, так как выделение газообразных веществ может вызвать вспучивание, повреждение глазури ит. п. Опасными являются механические напряжения, возникающие в нагреваемом изделии вследствие его неравномерного термического расширения при повышении температуры. Перепад темпера тур обусловливает сжатое состояние наружных и растянутое внутренних слоев изделия. Максимальный перепад температур и напряжения, при превышении которых в изделии появляются трещины, зависит от коэффициента расширения, теплопроводности, прочности, модуля упругости, геометрии тела и механизма спекания. На режим обжига оказывают влияние и механические напряжения, возникающие из-за неравномерной усадки при спекании, которые имеют обратный знак по отношению к напряжениям, связанным с термическим расширением. Поэтому перед началом усадки или на начальных ее стадиях необходимо снижать скорость нагревания или даже приостанавливать повышение температуры, чтобы уравнять температуру по объему изделий и предотвратить неравномерную усадку. Чтобы избежать образование трещин и деформаций в процессе усадки, заготовки помещают на подставки из той же массы (бомзы), что предотвращает задержку усадки силами трения между изделием и подом печи. На допустимую скорость нагревания некоторых видов керамики могут влиять химические или фазовые превращения, которые должны быть завершены в определенном температурном интервале. Если они связаны с окислительно-восстановительными процессами, то необходимо согласованное регулирование температуры и газовой среды. Охлаждение керамики, полученной твердофазным спеканием, не сопровождается существенными физико-химическими процессами, что позволяет достаточно точно рассчитать допустимую скорость охлаждения. В изделиях, содержащих жидкую фазу, при охлаждении происходит ее затвердевание с переходом из пластичного в упругое состояние, что связано с возникновением напряжений. Возможна также частичная или полная кристаллизация расплава с выделением одной или нескольких твердых фаз.До завершения затвердевания или кристаллизации расплава материал способен к пластической деформации, что ведет к релаксации напряжений и позволяет увеличить скорость снижения температуры. Наибольшая опасность образования трещин при охлаждении наблюдается при переходе изделия в хрупкое состояние. Именно в этот период следует замедлять скорость снижения температуры.Если в изделиях образуется несколько фаз с разным температурным коэффициентом расширения, то при охлаждении могут возникать напряжения на границах этих фаз, которые, как правило, приводят к образованию микротрещин, снижающих прочность, но обычно не приводящих к полному разрушению. Для таких материалов также требуется снижение скорости охлаждения, чтобы нарастание напряжений происходило медленно.Фактическая длительность обжига керамических изделий в промышленных печах почти всегда намного превышает минимальную продолжительность, необходимую для получения бездефектной продукции. Это связано с недостаточной изученностью отдельных процессов обжига, что обусловливает выбор скоростей повышения и снижения температуры с заведомо большим резервом; неравно мерностью распределения температуры в промышленных печах и необходимостью ее выравнивания; с инерционностью периодических печей; с трудностью регулирования температуры. В пламенных туннельных печах на отдельных ее участках часто равномерный и быстрый прогрев изделий затруднен также в связи с принятыми способами их садки в печь. Многорядная садка изделий друг на друга неизбежно снижает обогреваемую поверхность. Использование огнеупорных контейнеров (капселей) и других видов огнеприпаса также требует дополнительного времени на их прогрев.Совершенствование конструкции печей и оптимизация режима обжига позволяют в значительной степени смягчить влияние перечисленных факторов. Использование высокоэффективных пористых теплоизоляционных материалов, в том числе волокнистых, позволяет существенно уменьшить их размеры, резко сократить расход топлива и электроэнергии при обжиге за счет уменьшения тепловых потерь, осуществить заданный режим обжига. Все это способствует получению изделий с заданными свойствами и резкому уменьшению брака.
Дата добавления: 2018-04-04; просмотров: 306; Мы поможем в написании вашей работы! |
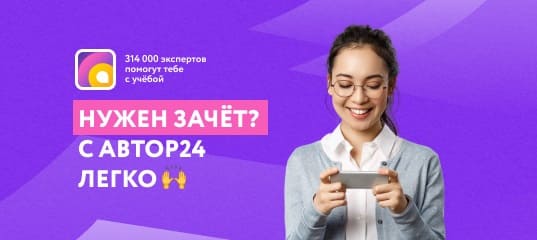
Мы поможем в написании ваших работ!