Технологии огнеупоров на основе диоксида циркония
Билет 19. 1. Требования, предъявляемые к свойствам глазурей: выбор оптимальных значений температуры разлива и ТКЛР. На качество глазури и ее разлив оказывают существенное влияние свойства глазурных расплавов. Разлив глазури, определяемый в первую очередь ее исходным составом, должен проходить на заключительной стадии обжига, при этом температура должна быть заметно ниже температуры размягчения керамических изделий. Плавкость глазури обычно определяют экспериментально. Ориентировочно ее можно рассчитать по числам плавкости К = (а,п, + а2п2 + ... + ann„) / (b,m, + b2m2 + ... +bmrn J, (3.85) где а и b — справочные константы плавкости легкоплавких и тугоплавких оксидов; пит — содержание оксидов в глазури. Качество растекания глазури, ее кристаллизационная способность, залечивание некоторых дефектов (шагрень, пузырь, нако-лы) в большей мере зависят от ее вязкости, которая определяется составом и температурой и может количественно быть рассчитана по уравнениям lgr|=lgA-l-B/T или lgri=lgA-t-b/T2, гдеТ — абсолют ная температура; А, В и Ь — константы, зависящие от природы расплава. Считается, что нормальный разлив глазури обеспечивается при вязкости (2-2,5)-102 Па-с. Известное влияние на разлив глазури, смачиваемость ею керамики оказывает поверхностное на тяжение глазурного расплава .Существенное влияние на свойства глазурей оказывают напряжения, возникающие в них при охлаждении, по мере которого, как показано на диаграмме (рис. 3.45) глазурь из жидкого состояния последовательно переходит в вязкопластичное (точка Т,), а затем в твердоупругое (точка Т,;). При дальнейшем охлаждении возникают напряжения вследствие разности коэффициентов термического сжатия затвердевшей глазури (а,) и собственно керамики (ак), величина которых зависит от размера этой разности. При ar>ak, в глазури возникают наиболее опасные растягивающие напряжения. Если они превышают прочность глазури, то в ней могут возникнуть разрывы (брак, именуемый цеком). При ar>ak возникающие сжимающие напряжения могут вызвать отслаивание глазури. Известное влияние на поведение глазури оказывает промежуточный слой, образующийся на границе глазурь — керамика за счет некоторого взаимодействия их составляющих и процессов диффузии и растворения. Этот слой создает естественный переход от глазури к керами ке и содействует выравниванию напряжений, пред отвращая образование указанных дефектов. Напряжения от разности ТКЛР глазури и керамики в отличие от иных известных напряжений, снимаемых режимом охлаждения и отжигом, можноснизитьлишь при изменении состава керамики и глазури, однако при этом следует учитывать что это может вызвать нежелательные изменения других свойств глазури, таких как плавкость, вязкость и т. п. Щелочные оксиды в наибольшей мере еннжают температуру разлива глазури, химическую стойкость, механические свойства, они же резко повышают ее ТКЛР, т. е. склонность к цеку. Щелочно-земельные оксиды повышают температуру разлива, однако сокращают интервал разлива, повышают склонность глазури к помутнению. Они же повышают прочность и упругость глазури, уменьшают склонность к цеку. Весьма ценными составляющими гла зури являются оксиды стронция, бария, бериллия, свинца, однако последние три токсичны. Наиболее легкоплавкие глазури (разлив при 400-500°С) получают при использовании оксидов свинца и бора. Повышают тугоплавкость, упругость, прочность, химическую стойкость оксиды алюминия и кремния, при этом последний явля ется главным стеклообразователем в глазурях .Диоксиды титана, циркония, олова вводят в глазури в качестве глушителей для придания им непрозрачности за счет содействия кристаллизации стекла, слабой их растворимости в глазурном расплаве и высокого коэффициента светопреломления по сравнению с таковым для стекла. В застывшем состоянии у глазурей определяют различные свойства — твердость, прочность, термостойкость, блеск, волнистость, толщину и др. Однако важнейшей величиной является термический коэффициент линейного расширения (сжатия), который определяют экспериментально с помощью дилатометров и ориентировочно расчетом, основанным иа принципе аддитивности а-107 = Да,/ 100, (3 86) где А; — молярная доля оксидов, а( - справочные парциальные коэффициенты этих оксидов.Кислотность глазурей, которая оказывает существенное влияние на образование промежуточного слоя, определяют расчетом по соотношению содержания кислых и основных оксидов в глазури. Регулируют кислотность изменением состава. Типичные ее значения, например, у полевошпатовых глазурей для фарфора 1,8—2,5, фритованных глазурей для фаянса — 1,5—2,5. Дефекты глазури — это наиболее типичные и часто встречающиеся виды брака изделий, их причины — некачественное приготовление глазурной суспензии, несогласованность глазури и керамики, ошибки при нанесении глазури, неудовлетворительная под готовка поверхности изделий, повреждения покрытия при его нанесении и огнеприпасом при обжиге. Образованию тонких трещин в глазури или ее отслаиванию также способствует неправильный режим охлаждения, нанесение покрытий чрезмерной толщины, недостаточное развитие переходного слоя, малая эластичность глазури. Плохая обдувка изделий сжатым воздухом, чрезмерная пористость глазуруемых изделий, попадание на поверхность жирных веществ, удары струи шликера о гипсовую форму обусловливают образование капель и складок, мелких впадин, наплывов, натеков, пониженного блеска, не покрытых глазурью мест, литейных пятен. Нарушения режима обжига, изменяющие плавкость и вязкость глазури, несвоевременное выделение газов из керамики, нарушение газовой среды, некачественный огнеприпас, попадание железа из оборудования вызывают образование наколов, науглероживание, желтоватое окрашивание, вскипание глазури, возникновение рябизны и других дефектов.
|
|
|
|
|
|
|
|
Технологии огнеупоров на основе диоксида циркония.
К этой группе материалов относят бадцелеитовые (Zr02 более 90%), бадцелеито-корундовые (20%< Zr02<90%) и цирконовые (Zr02>50%, Si02>25%).
Для изготовления огнеупоров применяют стабилизированный диоксцд циркония, содержащий (молярные%) 12 СаО, либо 10 У20з, либо 15 MgO, а также комбинацию этих оксидов. Для стабилизации диоксида циркония исходный порошок Zr02 смешивают со стабилизирующей добавкой, прессуют брикеты, обжигают их при 1750°С, затем дробят, рассевают на фракции и применяют в качестве заполнителя для изготовления изделий. Обычно используют две фракции заполнителя для получения плотной упаковки частиц. В качестве дисперсной связки применяют тонкомолотый стабилизированный диоксид циркония, который вводят в шихту в количестве 15—25%. Изделия прессуют при давлении —100 МПа и обжигают при 1750°С.Для изготовления огнеупоров из Zr02 широко применяют элек- троплавленный стабилизированный диоксид циркония, который получают плавкой смеси Zr02 и стабилизирующей добавки в дуговых электрических печах или индукционной плавкой в холодных тиглях. Пористость изделий из электроплавленного диоксида циркония составляет 20—30%, прочность при сжатии 50—100 МПа. Изделия из полностью стабилизированного диоксида циркония характеризуются сравнительно низкой термостойкостью. Для повышения термостойкости в шихту добавляют 25—30% моноклинной модификации электроплавленного Zr02, что придает изделиям микротрещиноватое строение.Изделия из диоксида циркония зернистого строения применяют в сталеплавильном производстве для разливочных и стопорных систем в качестве вставок-дозаторов и скользящих затворов, для футеровки стекловаренных и других печей, в виде тиглей для плавки металлов и огнеприпаса для обжига некоторых изделий технической керамики.Длительный нагрев стабилизированного диоксида циркония при температуре 2000°С и выше приводит к интенсивной рекристаллизации, что существенно снижает прочность и приводит к разрушению изделий. Для уменьшения роста кристаллов, стабилизации структуры и свойств изделий из ZrO% при температурах до 220СРС заранее при спекании таких изделий формируют двухфазную структуру, состоящую из кубического и тетрагонального твердого раствора. При этом тетрагональный твердый раствор должен выделяться по границам кристаллов кубического твердого раствора, препятствуя их росту. Такая структура может быть создана различными приемами, например обжигом изделий При 2100—2200°С с пониженным, но определенным количеством стабилизатора с последующим медленным охлаждением изделий или их длительной выдержкой при 1000—1200°С.Цирконовые изделия изготовляют из циркона (Z1O2 • SiC^), который не имеет при нагревании полиморфных превращений, но разлагается в твердой фазе при 1676°С на диоксид циркония и кри-стобалит; характеризуется высокой химической стойкостью к кислым средам и расплавам сталей.Для промышленных целей циркон извлекают из цирконовых песков обогащением при помощи отсадочных машин, флотацией, а также обработкой кислотами для удаления примесей, содержащих оксида железа. В цирконовом концентрате содержание Zr02+Hf02 должно быть не менее 60%, а оксидов железа не более 0,15%.Для изготовления огнеупоров циркон измельчают до зерен размером 1 —2 мм. Зерновой состав шихт выбирают с учетом максимальной упаковки частиц, в качестве связки вводят тонкомолотый циркон или 5—10% огнеупорной глины. Давление прессования изделий составляет 80—120 МПа, температура обжига 1550—1600°С. Обожженные изделия имеют пористость 12—16%, прочность на сжатие —100 МПа, температуру начала деформации 1520— 1570°С, термостойкость более 20 воздушных теплосмен. Цирконовые огнеупоры применяют в условиях воздействия расплавленных хлоридов, кислых шлаков и расплавов золы углей. Из циркона изготавливают вставки-дозаторы, стаканы и втулки для установок непрерывной разливки стали.Циркон применяют также в шихте бадделеитокорундовых плавленолитых огнеупоров «бакор».
.
Дата добавления: 2018-04-04; просмотров: 215; Мы поможем в написании вашей работы! |
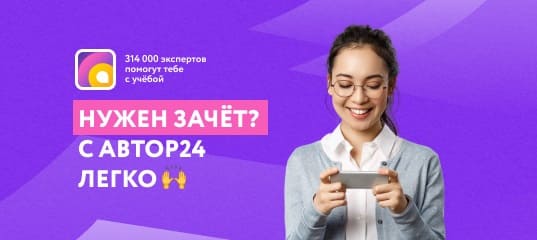
Мы поможем в написании ваших работ!