Способы защиты металлов от коррозии
Существует много способов защиты металлов от коррозии, которые применяют в зависимости от условий эксплуатации изделий или конструкций, от вида коррозионных сред и других факторов. Основными способами предотвращения коррозионных процессов являются следующие:
выбор материалов, устойчивых против коррозии в данной среде;
тщательная обработка поверхностей, соприкасающихся с коррозионной средой;
нанесение металлических покрытий;
нанесение неметаллических покрытий;
обработка коррозионной среды;
электрохимическая защита.
При выборе материалов для изготовления изделий и конструкций необходимо стремиться к тому, чтобы эти материалы при прочих равных условиях обладали наибольшей коррозионной стойкостью в данной среде.
Так, материалы электродов или присадочной проволоки, используемые при сварке, не должны отличаться по составу от материала свариваемых изделий или конструкций. В противном случае, например при сварке нержавеющей стали электродами из углеродистой стали, сварной шов будет корродировать аналогично обыкновенной углеродистой стали.
Тщательная обработка поверхностей повышает сопротивляемость изделий и конструкций к коррозии, особенно если они работают в активных коррозионных средах. В судостроении такими конструкциями являются обшивка корпуса судна, гребные винты, трубы судовых систем, крыльевые устройства судов на подводных крыльях и т. д.
|
|
Нанесение покрытий (металлических и неметаллических) представляет собой пассивную защиту, цель которой — не допустить соприкосновения коррозионной среды с основным металлом.
Все металлические покрытия делятся на две группы: анодные и катодные.
Анодными покрытиями называются такие, электродный потенциал которых ниже электродного потенциала основного металла.
Катодными покрытиями называются такие, электродный потенциал которых выше электродного потенциала основного металла.
В качестве анодных покрытий для железа будут, например, цинк и кадмий, а катодных — олово, медь и никель.
Катодные покрытия защищают основной металл механически до тех пор, пока сохраняется их сплошность. При нарушении покрытия (царапины, трещины и т. п.) создается гальваническая пара и происходит коррозия основного металла как более активного.
Анодные покрытия защищают основной металл механическим и электрохимическим путем. При нарушении покрытия также создается гальваническая пара и происходит коррозия металла покрытия как более активного.
Металлические покрытия могут быть нанесены следующими способами: гальваническим, плакированием, металлизацией (набрызгиванием), диффузионным, горячим.
|
|
Гальванический способ заключается в нанесении на поверхность изделия покрытия путем электролиза. Изделие погружают в ванну с электролитом, содержащим соли защитного металла, присоединяют к катоду, а пластину покрывающего металла — к аноду источника тока. При пропускании электрического тока через электролит металл с пластины осаждается на изделии в виде плотного сплошного слоя одинаковой толщины.
Плакирование заключается в покрытии одного металла другим путем их механического соединения в нагретом состоянии. Для защиты от коррозии покрывающий слой металла должен быть антикоррозионным. Например, сталь чаще всего плакируют медью, алюминием, никелем и латунью. С целью экономии металла и одновременно повышения его антикоррозионных свойств, один металл плакируют металлом того же рода, но с более высокой степенью сопротивляемости к коррозии. Например, углеродистую сталь плакируют нержавеющей сталью, дуралюмин — чистым алюминием.
Металлизация (набрызгивание) заключается в нанесении на поверхность изделий или конструкций слоя расплавленного металла, обладающего более высокой антикоррозионной стойкостью, чем защищаемый. Антикоррозионный слой наносят при помощи специального устройства (металлизатора). В металлизатор металл подается в виде проволоки, затем расплавляется газовым пламенем или электрической дугой и распыляется сжатым воздухом. Диффузионный способ заключается в насыщении поверхностных слоев изделий элементами, стойкими к коррозии. Он осуществляется при высоких температурах и обеспечивает получение стойких к коррозии поверхностей изделий не только при обычной температуре, но и при нагреве до 1200 К.
|
|
Широко распространены следующие виды диффузионной защиты: алитирование — насыщение алюминием, азотирование — насыщение азотом, хромирование — насыщение хромом, силици-рование — насыщение кремнием и др.
Горячий способ заключается в нанесении покрытий путем погружения изделий в ванну с расплавленным металлом или нанесения его на нагретую поверхность изделий. Подобным
образом могут быть нанесены покрытия только из низкоплавких металлов: олова, цинка, свинца и их сплавов. Покрытие изделий оловом и его сплавами называется лужением, цинком — цинкованием, свинцом — свинцеванием.
Цель нанесения неметаллических покрытий на поверхность изделий, так же как и металлических,— не допустить соприкосновения коррозионной среды с основным металлом.
|
|
К неметаллическим покрытиям относятся: лаки, краски, эмали, смазки, цементные покрытия, резина, эбонит, окисные защитные пленки.
Нанесение лакокрасочных покрытий — основной метод защиты изделий от коррозии, особенно в судостроении.
Смазки применяют обычно для защиты от атмосферной коррозии различных изделий при их хранении на складах или транспортировке. Смазки представляют собой смеси незатвер-девающих и неокисляющих веществ (вазелина, парафина, масла) с добавками загустителей. Срок действия зависит от их состава.
Покрытие изделий антикоррозионными смазками называется консервацией.
Цементные покрытия применяют в судостроении для защиты от коррозии, например, внутренних поверхностей цистерн питьевой воды. В этом случае они помогают сохранить вкус питьевой воды.
Покрытие изделий резиной или эбонитом — гуммирование — производят таким образом: сперва их обезжиривают, обрабатывают металлическими щетками для придания им шероховатости, затем покрывают резиновым клеем, приклеивают листы резины и производят вулканизацию. Гуммирование предназначено для защиты изделий от воздействия кислот, щелочей, растворов солей.
Защита окисными пленками заключается в создании на поверхности изделий антикоррозионных пленок путем окисления их поверхностных слоев. Защитные пленки получают оксидированием и фосфатированием.
Оксидирование — это создание окисных пленок в сильных окислителях. Для этого изделия из стали погружают в растворы азотнокислых солей и выдерживают в течение 1—2 ч при температуре примерно 400 К. Оксидирование изделий из алюминиевых и магниевых сплавов производят химическим или электрохимическим способами. Оксидирование стали обычно называют воронением.
Фосфатирование — это создание на поверхности изделия защитной пленки фосфорнокислых соединений железа и марганца. Для фосфатирования изделие погружают в раствор фосфорнокислых соединений железа и марганца и выдерживают в течение 1 —1,5 ч при температуре около 373 К. После фосфатирования на поверхности изделия образуется пленка светло- или темно-серого цвета. Фосфатирование является одним из самых экономичных и надежных способов защиты стальных изделий от коррозии.
Защита изделий от коррозии путем обработки коррозионной среды заключается или в удалении из нее веществ, вызывающих коррозию, или во введении особых веществ, понижающих коррозионную активность среды. Например, из воды, питающей судовые паровые котлы, удаляют кислород с помощью специальных устройств, называемых деаэраторами. Отсутствие кислорода резко снижает коррозионную активность воды.
Для понижения активности коррозионной среды вводят вещества, называемые замедлителями коррозии или ингибиторами.
Электрохимический способ является эффективным средством защиты изделий от коррозии. С помощью этого способа можно значительно снизить, а в некоторых случаях и полностью исключить коррозию судовых конструкций. Существуют два метода электрохимической защиты: катодный и протекторный.
Катодный метод основан на предотвращении коррозии при помощи постоянного тока. Конструкция присоединяется к источнику постоянного тока и служит катодом. Анодом служат специально устанавливаемые на конструкции электроды, которые изготовляют из мягкой стали, кремнистого чугуна, графита или магниевого сплава. В результате при прохождении электрического тока коррозионному разрушению подвергается не поверхность конструкции, а специальные электроды.
Протекторный метод защиты заключается в том, что к защищаемой конструкции присоединяют пластину металла с более низким электродным-потенциалом, чем защищаемый. При этом протектор — металл с более низким потенциалом— разрушается и таким образом защищает металл конструкции. Протекторы с основным металлом образуют гальваническую пару, в которой протектор является анодом, а основной металл катодом.
Так, для защиты стального корпуса судов применяют протекторы из цинка, магния, алюминия и их сплавов. Их изготовляют в виде цилиндров, дисков, планок, шаров, листов и т. п. Протекторы присоединяют к конструкции при помощи сварки или на шпильках. После разрушения их заменяют новыми. Протектор может защищать поверхность конструкции, которая примерно в 200 раз больше его собственной. Протекторная защита является надежной, но увеличивает массу конструкции, а в движущейся воде увеличивает силу сопротивления.
ЖЕЛЕЗОУГЛЕРОДИСТЫЕ СПЛАВЫ
К железоуглеродистым сплавам относят чугун и сталь.
Чугунпредставляет собой сплав железа с углеродом, в котором углерода находится свыше 2 % Чаще всего в технике применяют чугуны, имеющие от 2,4 до 3,8 % углерода. Содержание примесей в чугунах достигает следующих пределов: кремния — до 3,6%, марганца—; до 1,5 %, серы — до 0,06 %, фосфора — до 1,2 %',
Чугун — самый дешевый машиностроительный материал. Он служит для изготовления отливок и является исходным продуктом для выплавки стали.
Для получения чугуна необходимо приготовить шихту— смесь сырых материалов, подлежащую переработке в доменных печах. Шихта для производства чугуна состоит из железных руд, топлива и флюсов.
Железными рудами называют природные ископаемые, в состав которых входят окислы железа и пустая порода (глинозем; кремнезем и др.). Железные руды являются источниками железа в процессе получения чугуна. Для выплавки чугуна применяют в основном железную руду двух видов: красный железняк и магнитный железняк .
Для удаления пустой породы из руды применяют (флюсы — вещества, образующие с пустой породой легко плавкие соединения. В качестве флюсов используют известняк.
Топливо (кокс) обеспечивает необходимую температуру для расплавления шихты. Углерод кокса входит также в состав железоуглеродистых сплавов.
Углерод в чугуне может находиться либо в химическом соединении с железом — в виде карбида железа Fe3C (цементита), либо в свободном состоянии — в виде частиц графита. В зависимости от формы и состояния углерода различают белый, серый, высокопрочный и ковкий чугун.
Если углерод в чугуне находится в виде цементита, то такой чугун имеет в изломе белый цвет и поэтому называется белым. Белый чугун очень твердый и хрупкий. Он плохо обрабатывается резанием и имеет низкие литейные свойства. Получению белого чугуна способствует марганец, который препятствует процессу графитизации. Основная масса белого чугуна используется на переделку в сталь, поэтому белый чугун называют также передольным. Часть белого чугуна идет на получение ковкого чугуна.
Если углерод в чугуне находится в свободном состоянии в виде графита, то такой чугун имеет в изломе серый цвет и называется серым. Получению серого чугуна способствует кремний.
Серый чугун отличается от передельного чугуна меньшей твердостью и хрупкостью, а также хорошей обрабатываемостью резанием. Он имеет отличные литейные свойства и применяется для получения отливок, поэтому серый чугун называют литейным чугуном.
В сером чугуне графит имеет форму пластинок. Они нарушают целостность металлической основы чугуна и играют роль надрезов и мелких трещин. Поэтому серый чугун плохо сопротивляется растяжению и имеет низкую пластичность и вязкость. Чем меньше графитовых включений в чугуне и чем они мельче, тем выше механические свойства чугуна.
Дата добавления: 2018-04-05; просмотров: 1649; Мы поможем в написании вашей работы! |
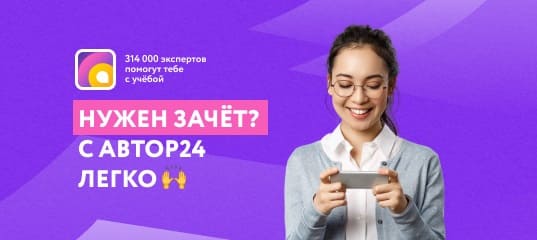
Мы поможем в написании ваших работ!