Химические методы нанесения покрытий
В основе химических методов обработки лежит воздействие на обрабатываемую поверхность заготовки химически активных веществ. В результате протекающих химических обменных реакций происходит либо растворение поверхностного слоя в окружающей среде, либо осаждение вещества из среды на поверхность заготовки. Это обусловило возможность использования химических методов, во-первых, для поверхностного и глубинного травления заготовок и, во-вторых, для осаждения на обрабатываемую поверхность покрытий (плёнок).
Химические методы получения покрытий реализуются без наложения на среду, в которой ведётся обработка, электрического тока путём осаждения металла из водных растворов или из газовой среды (фазы).Покрытия такого типа известны в литературе как химические покрытия.
Непосредственному нанесению химического покрытия на поверхность заготовки должна предшествовать подготовка поверхности к выполнению этой операции.
Химические методы нанесения покрытий осаждением из водных растворов
Существуют несколько способов химического осаждения металлов из водных растворов: контактный; контактно-химический; метод химического восстановления (химическая металлизация).
Контактный способоснован на вытеснении ионов осаждаемого металла из раствора более активным металлом. Примером реализации данного способа может быть реакция меднения железного гвоздя, помещённого в раствор сульфата меди.
|
|
Fe + CuSO4 = FeSO4 + Cu↓.
Контактно-химический способ осаждения металлов заключается в создании гальванической пары между металлом основы и более активным металлом. Так, при осаждении серебра на медную основу создают гальваническую пару с помощью более активного металла алюминия или магния. В этом случае более активный металл отдаёт свои электроны меди, и на отрицательно заряженной медной поверхности ионы Ag+ восстанавливаются до металла.
Метод химического восстановления (химическая металлизация) заключается в том, что металлические покрытия получают в результате восстановления ионов металла из водных растворов, содержащих восстановитель.
Химические методы нанесения металлических покрытий при своей сравнительной простоте обеспечивают высокую прочность сцепления металлического слоя с основой (до 2 МПа), равномерную толщину слоя и его высокую электропроводность. Эти методы позволяют получать равномерные покрытия на деталях сложной конфигурации, причём не только на внешних, но и на внутренних поверхностях.
Рассмотрим далее особенности проведения процесса химической металлизации и получения наиболее распространенных процессов химического осаждения покрытий: оксидирования, воронения, фосфатирования и хроматирования.
|
|
Химическая металлизация — нанесение покрытия из металла на поверхность заготовки методом его химического осаждения. Химическую металлизацию можно осуществлять как на металлах, так и на неметаллических материалах, например, пластмассах.
Химический метод получения металлических покрытийна металлах основан на восстановлении ионов осаждаемого металла из раствора в результате взаимодействия его с восстанавливающим веществом (восстановителем), находящимся в растворе.Восстановитель, окисляясь, отдаёт свои электроны имеющимся в растворе ионам металла, которые превращаются в атомы и осаждаются на обрабатываемой поверхности в виде металлической плёнки. Реакция восстановления интенсивно протекает на металлической поверхности покрываемой заготовки, являющейся каталитической для данного процесса.
В настоящее время разработаны способы получения покрытий химическим восстановлением более 20 различных металлов. Этим же методом получают покрытия бинарными и тройными сплавами, например, сплавами Ni- P, Ni- B, Ni-Mo- B, Ni-Co- P. В промышленности широкое распространение получили химическое никелирование и химическое омеднение поверхностей заготовок.
|
|
Основу химического никелирования составляет восстановление ионов никеля из водных растворов и осаждение их в виде атомов на поверхности заготовки. Этим методом можно покрывать наружные поверхности заготовок сложной формы и внутренние поверхности, недоступные для нанесения покрытия другими методами. Никелевое покрытие с успехом применяют для защиты от коррозии энергетического оборудования, работающего при температуре 600…650 0С в газовой среде, для покрытия магниевых и титановых деталей вертолетных роторов, а также алюминиевых зеркал, используемых на спутниках в условиях космоса. Оно применяется также для защиты от коррозии хирургических инструментов и деталей часов.
Химическое меднение. Восстановление ионов Сu2+ из раствора, содержащего соли меди, формальдегидом (в виде гидрата метиленгликоля НСНО + Н2О СН2(ОН)2) с целью получения медных зеркал на стекле известно с конца XIX века. Широкое распространение этот процесс получил для изготовления простых и многослойных печатных схем, при металлизации пластмасс, изготовлении медных зеркал и для других целей.
Металлические покрытия на пластмассах как бы облагораживают изделия, упрочняют, делают их более стойкими к тепловым, световым, радиационным, механическим и другим воздействиям. Свойства металлизированных пластмассовых изделий, на которых основано столь широкое их применение, в значительной степени зависят от способа нанесения металлического покрытия.
|
|
Широко известен, например, метод химического омеднения пластмасс при изготовлении печатных плат. Восстановление меди на поверхности пластмассовой печатной платы производят из раствора, содержащего соли меди, никеля, а также формалин, соду и другие химикаты. Длительность осаждения слоя меди толщиной 0,25…0,5 мкм составляет 15…20 мин. Для удаления водорода, выделяющегося в процессе омеднения, и для лучшего смачивания обрабатываемых поверхностей раствором, процесс проводят с плавным покачиванием плат или с наложением на технологическую систему ультразвуковых колебаний.
Химическое оксидирование. Оксидированием называют нанесение оксидных покрытий на металлы химическим и электрохимическим методами. Химические оксидные плёнки образуются при обработке металлов в растворах, содержащих окислители, которые способны генерировать на поверхности кислород, вступающий во взаимодействие с металлом.
Воронение.Широко известны в промышленности технологии оксидирования углеродистых и низколегированных сталей и чугунов, получившие название «воронение». На поверхностях изделий, изготовленных из этих материалов, методом воронения создают пористые плёнки окислов железа (Fe3O4 и других) толщиной 1…10 мкм. Воронение применяют преимущественно для декоративной отделки поверхности путём придания ей определённого цвета. Цветформирующейся плёнки определяется толщиной покрытия и последовательно меняется с увеличением толщины от жёлтого к бурому, вишнёвому, фиолетовому, синему и серому.
Существуют следующие виды воронения:
— щелочное — воронение в щелочныхрастворах с окислителями при температуре 135…150 °C;
— кислотное— воронение в кислых растворах химическим или электрохимическим способами;
— термическое — окисление стали при высоких температурах: в атмосфере перегретого водяного пара при 200…480 °C или в парах аммиачно-спиртовой смеси при 520…880 °C, в расплавленных солях при 400…600 °C, а также в воздушной атмосфере при 310…450 °C с предварительным покрытием поверхности деталей тонким слоем асфальтового или масляного лака.
Структура покрытия мелкокристаллическая, микропористая. Для придания блеска, а также улучшения защитных свойств окисной плёнки её также пропитывают маслом (минеральным или растительным).
Сейчас воронение применяется преимущественно в качестве декоративной отделки, а раньше для уменьшения коррозии металла.
Прочные оксидные плёнки получают также на меди и её сплавах. Подвергаются химическому оксидированию и магниевые сплавы. Толщина оксидных плёнок на них колеблется от 2 до 5 мкм, предельная эксплуатационная температура таких плёнок находится в пределах 200…250 оС.
Фосфатирование.Фосфатированием называют метод нанесения на аноде (заготовке) покрытия, состоящего из мелкокристаллического слоя смешанных фосфатов железа, цинка или марганца.
Фосфатированиев основном используют для образования на чёрных металлах (низкоуглеродистые и углеродистые стали, чугун) трудно растворимой фосфатной плёнки типа Ме3(РО4)n, где обозначение «Ме» соответствует металлу основы, на которую наносится покрытие. Цветные металлы подвергают фосфатированию реже, чем чёрные.
Фосфатирование может быть реализовано химическим и электрохимическим методами. Осуществляется этот процесс в водных растворов препаратов, известных под названием МАЖЕФ (марганец, железо, фосфор), основу которых составляют однозамещённые соли ортофосфорной кислоты (H3PO4) марганца, железа (MnHPO4, Fe(H2PO4)2, Mn(H2PO4)2).
С целью получения фосфатной пленки водный раствор солей подвергается гидролизу
Me (Η2ΡΟ4)2«Me(HРО4) + Η3ΡΟ4.
При нагревании до температуры кипения гидролиз идет дальше
5Ме(Н2РО4)2« 2Ме(НРО4) + Ме3(РО4)2 + 6Η3ΡΟ4.
Как известно, при взаимодействии железа с фосфорной кислотой образуются одно-, двух- и трёхзамещённые фосфаты и выделяется водород:
Fe + 2H3PO4 = Fe(H2PO4)2 + Η2,
Fe + Fe(H2PO4)2 = 2Fe(HPO4) +Η2,
Fe + 2Fe(HPO4) = Fe3(PO4)2 + H2.
Параллельно может идти диссоциация однозамещенных фосфатов
3Fe(H2PO4)2«Fe3(PO4)2 + 4Η3ΡΟ4.
Однозамещённые фосфаты хорошо растворимы в воде, двухзамещённые трудно растворяются, а трёхзамещённые практически не растворяются. Последние два соединения и являются основой фосфатной пленки, формирующейся на поверхности обрабатываемых изделий.
Толщина фосфатного покрытия обычно составляет 10…12 мкм, но в некоторых случаях создают покрытия толщиной в несколько десятков микрометров. Фосфатная плёнка не боится органических масел, смазочных, горячих материалов, толуола, бензола, всех газов, кроме сероводорода. Она имеет более высокую коррозионную стойкость, чем оксидная плёнка. Поэтому фосфатные покрытия применяют для защиты поверхностей от атмосферной коррозии. Этот вид покрытия используется также для грунтования поверхности перед нанесением лакокрасочных материалов, уменьшения трения при выполнении операций волочения и накатки резьбы, изоляции участков стальных поверхностей перед лужением, свинцеванием, цинкованием; для электроизоляции пластин трансформаторов, роторов и статоров.
Хроматирование — метод химического нанесения тонкоплёночного покрытия из хроматов (солей хромовой кислоты H2CrO4) на поверхностях заготовок из сталей, цинка, кадмия, магния, алюминия и их сплавов. В процессе хроматирования на поверхности данных металлов образуются пассивные плёнки толщиной менее 1 мкм, состоящие из солей трудно растворимых хроматов (Fe2(CrO4)3, ZnCrO4, CdCrO4, MgCrO4, Al2(CrO4)3) зелёного, жёлтого, чёрного или бледно-голубого цветов, которые заметно улучшают коррозионную стойкость детали. Хроматирование широко применяют для покрытия оцинкованной стали с целью защитить её от образования белой ржавчины во время транспортировки и хранения.
Химическое хроматирование проводят, используя водный раствор хромовой кислоты или хромата, часто содержащий другие добавки, например, фосфорную и соляную кислоты.
Дата добавления: 2018-04-04; просмотров: 3555; Мы поможем в написании вашей работы! |
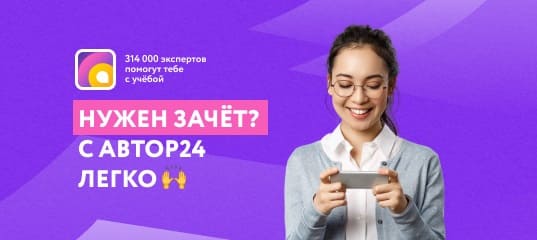
Мы поможем в написании ваших работ!