Методы нанесения металлических и неметаллических неорганических покрытий
Лекция 4
Покрытия и технологии их нанесения
Покрытие — это слой или несколько слоев материала, искусственно полученных на покрываемой поверхности (ГОСТ 9008-82. Покрытия металлические и неметаллические неорганические. Термины и определения).Нанесение покрытий является одной из основных технологий, направленных на защиту детали от коррозии и получения новых функциональных свойств, таких как повышенная поверхностная твёрдость, износостойкость, антифрикционная способность. Поверхность, на которую наносится покрытие, принято называть основой.
Классификации покрытий
В литературных источниках встречаются различные классификации методов нанесения покрытий, строящиеся на различных классификационных признаках.
По физической сущности процессов в зоне соединения наносимого материала и основы покрытия можно классифицировать на покрытия, создаваемые:
— адгезионными силами сцепления наносимого материала и основы без проникновения наносимого материала в основу;
—расплавлением поверхностного слоя и созданием переходного сложного по составу и структуре промежуточного слоя между наносимым материалом и основой (методы наплавки);
— модифицированием поверхностного слоя без изменения его размеров. Сюда можно отнести цементацию, азотирование, ионную модификацию поверхностного слоя и другие способы.
|
|
По реализуемой функциипокрытия подразделяютназащитные(коррозионностойкие и износостойкие покрытия), декоративные (цвет, форма, рисунок, рельеф), защитно-декоративные, специальные, в том числе и для формирования переходных слоев.
Основное назначение защитных покрытий связано с их разнообразными защитными функциями. Большое распространение получили коррозионностойкие, жаростойкие и износостойкие покрытия. Широко применяются также теплозащитные, электроизоляционные и отражающие покрытия.
По способу защитного действия металлические покрытия можно разделить на катодные и анодные в зависимости от того, какую функцию выполняет покрытие в той или иной эксплуатационной среде. Если слой покрытия является беспористым и сплошным, то любое покрытие защищает изделие от коррозии. Однако покрытие практически всегда повреждается при эксплуатации и его защитные свойства определяются процессами, которые происходят на поврежденных местах. При наличии влаги на оголенных местах начинает работать локальный микрогальванический элемент «металл основы — металл покрытия». Если электродный равновесный потенциал металла покрытия по отношению к металлу основы является положительным, покрытия являются катодными, в противоположном случае — анодными.
|
|
Применение катодных покрытий обеспечивает лишь механическую защиту основного металла. При наличии в покрытии пор, трещин и других дефектов эти участки в образовавшейся гальванопаре будут выполнять роль катода. Основной металл, являясь анодом, начнет растворяться, причем тем интенсивнее, чем больше будет разность равновесных электродных потенциалов.
В отличие от катодных анодные покрытия обеспечивают не только механическую, но и электрохимическую защиту.При этом покрытие, являющееся анодом, растворяется. Например, при нанесении цинка на сталь работа локального элемента вызывает коррозию цинка, а железо в большей или меньшей степени оказывается защищенным от разрушения. Степень защищенности зависит от активности металла покрытия: чем меньше он подвергается коррозии, тем лучше защищает основной металл даже там, где уже не покрывает его поверхность.
К катодным покрытиям следует отнести медные и никелевые — по стали, золотые и серебряные — по меди и ее сплавам; к анодным — цинковые покрытия по стали, никелевые — на меди.Оксидные и фосфатные покрытия являются нейтральными, так как относятся к диэлектрикам.
|
|
Декоративные покрытия – исключительно широко применяются при производстве бытовых изделий, украшений, повышении эстетичности промышленных установок и приборов, протезировании в медицинской технике и др.
ГОСТ 9008-82. «Покрытия металлические и неметаллические неорганические. Термины и определения» подразделяет все покрытия на две группы: группу металлических и неметаллических неорганических покрытий и группу органических покрытий. Примеры отдельных видов покрытий, входящих в эти группы представлены в таблице 4.1.
Таблица 4.1
Виды покрытий
Металлические и неметаллические неорганические покрытия | Органические покрытия | |
Металлические покрытия | Неметаллические неорганические покрытия | |
Алюминирование | Анодно-окисные | Лакокрасочные |
Никелирование | Оксидные | Полимерные |
Меднение | Фосфатные | Смолы |
Кадмирование | Пассивирование | Растительные |
Золочение | Воронение | Живые ткани |
и другие | Неорганические эмали | Другие |
Классификация покрытий по толщине. Покрытиями или толстыми пленками называют слои конденсированного вещества свыше 1 мкм. Слои менее 1 мкм называют пленками.Пленки свыше 10 нм считаются просто тонкими. По толщине тонкие пленки обычно делят на нанометровые (0,1…100 нм) и субмикронные (0,1…1 мкм). Пленки толщиной до нескольких атомных монослоев (0,1…10 нм) называют ультратонкими.
|
|
По количеству наносимых слоевпокрытия подразделяют на однослойные и многослойные (два и более слоев).Многослойные покрытия, создаваемые последовательно наносимыми слоями, нашли широкое распространение в настоящее время, поскольку обеспечивают лучшие функциональные свойства, чем однослойные, в том числе,лучшее сцепление покрытия с основой.
Методы нанесения металлических и неметаллических неорганических покрытий
На рисунке 4.1 представлена общая классификация методов нанесения металлических покрытий. Далее приведена краткая характеристика некоторых их них. Отдельными разделами в пособии рассмотрены методы нанесения покрытий химическими, электрохимическими и вакуумными методами.
|








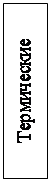
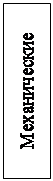

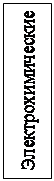

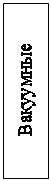
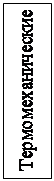


Механические методы нанесения покрытийиспользуют для получения цинковых, кадмиевых и оловокадмиевых покрытий.В основе этих методов лежит размещение покрываемых заготовок в сосудах с соответствующими тонкими металлическими порошками, активаторами и стеклянными шариками и их перемешивания в результате чего порошки вдавливаются в поверхность заготовок.
Термические методы нанесения покрытий реализуются погружением заготовок в расплав с последующим охлаждением; напайкой и наплавкой покрытия.
Погружением в горячий расплав наносят покрытия из низкоплавких материалов: цинка, олова, алюминия. Они предохраняют основной материал от коррозии.
Наплавка покрытия — это нанесение слоя металла или сплава на поверхность изделия посредством сварки плавлением. Выделяют следующие способы наплавки:
— ручная дуговая наплавка покрытыми электродами;
— дуговая наплавка под флюсом проволоками и лентами;
— дуговая наплавка в защитных газах вольфрамовыми (неплавящимися) и проволочными металлическими (плавящимися) электродами;
— дуговая наплавка самозащитными порошковыми проволоками;
— плазменная наплавка;
— лазерная наплавка;
— электронно-лучевая наплавка;
— индукционная наплавка;
— газопламенная наплавка.
К термомеханическим методам нанесения покрытий относят плакирование, обкатка.
Плакирование (фр. plaquer — накладывать, покрывать), те́рмомехани́ческоепокры́тие — нанесение на поверхность металлических листов, плит, проволоки, труб тонкого слоя другого металла или сплава термомеханическим способом. С этой целью используют методы холодной и горячей прокатки, плакирование взрывом и наплавку плакирующего слоя.
К плакированию часто относят нанесение покрытия сусальным золотом на поверхность заготовки. Однако этот способ золочения поверхности все же следует отнести к методу склеивания основы и наносимого слоя сусального золота. Остановимся на этом подробнее.
Покрытие сусальным золотом— главный метод золочения куполов на сегодня. Сусальное золото — это тончайшие пленки золота всегда одного размера, 91,5 ×91,5 мм, и разной толщины.От нее зависит так называемый лигатурный вес сусального золота. Для золочения куполов используется золото с лигатурным весом 3…5 г. В России делают сусальное золото, которое обычно выпускают в виде «книг», состоящих из 60 листов.
Производится сусальное золото нескольких цветов, зависящих от того, какие добавки делаются к чистому золоту. Чем чище золото, то есть чем больше количество каратов драгоценного металла, тем менее чувствительна позолота к влиянию погодных и климатических условий. Для наружного золочения могут быть использованы лишь сорта более 23,75 карата.Это значит, что в сплаве содержится 23,75 части золота и 0,25 части добавок.
Технология золочения металлических поверхностей сусальным золотом состоит из трех этапов:
— подготовка поверхности под золочение;
— подготовка материалов и нанесение грунтовочных слоев;
— золочение.
Для приготовления грунтов используются такие материалы, как: свинцовый сурик, тонкотертый свинцовый крон, лак ЯН-54, лак ЯН-153 или ГФ-166. Грунт наносится три раза. Перед нанесением последующего слоя грунта просушенную поверхность шлифуют водостойкой шкуркой среднего зерна, затем промывают водой и обезжиривают спиртом. Высушенный слой грунта тщательно протирают суконкой для выравнивания полировки. Если есть недостатки на поверхности, проводят повторную грунтовку и полировку.
Подготовленную поверхность золотят масляным способом на лак МА-594 (мордан) и оставляют на просушку, которая длится 6, 12 или 24 часа, в зависимости от сорта мордана. Окончательно понять, готова ли поверхность для золочения, можно проверив ее «на отлип» от пальца: легко притронуться к покрытию. Если палец чувствует отлип, а на нем не остается лака — он готов к восприятию позолоты. Очень важно поймать нужное время для нанесения сусального золота: в жидком покрытии золото может «утонуть», к сухому — прикрепится слабо или вообще не прикрепится.
Процесс золочения выглядит так: позолотчик специальной кистью за счет естественного электрического заряда подцепляет предварительно раскроенный кусок золота, кисть с висящим в воздухе листиком золота подносится к липкой поверхности и от легкого касания одним краем он приклеивается к поверхности. После накладки золото прижимают, затем располировывают тампоном из ваты. Золото наносят обязательно внахлест, места разрывов и трещины «фликуют». По окончании золочения лак МА594 должен окрепнуть в течение 20…25 суток. Затем поверхность консервируется, то есть покрывается защитным лаком.
Купола золотят в шатрах, то есть лесах, обтянутых полиэтиленом, которые защищают от пыли, основного врага позолотчика. После того как выполнено золочение, купол должен хотя бы пару месяцев постоять под шатром, чтобы сродниться с климатом. Конструкция лесов должна обеспечивать доступ к каждому участку поверхности двух специалистовпозолотчиков. Высота яруса не менее 100 и не более 150 см, расстояние от поверхности купола до пола лесов — от 20 до 35 см. Важна максимальная прозрачность полиэтилена, так как сусальное золото можно наносить только при естественном освещении.
В отличие от нитрида титана, золото является пластичным материалом. Оно исключает появление микротрещин при перепаде температур и морозах. Химическая нейтральность золота не допускает адсорбции веществ из окружающей среды. В совокупности с антистатическими свойствами любые осадки не оставляют загрязнений, а делают поверхность более чистой и блестящей.
Натуральная позолота в связи с высокой стоимостью и недолговечностью материала в наши дни используется все реже. Зато все более популярными становятся кровельные материалы из нержавеющей стали с покрытием из нитрида титана. Такой материал в точности имитирует цвет золота и вплоть до 100 лет сохраняет свою первоначальную красоту.
Основой купола является листовая медь. Известно, что медь — это цветной металл, а у цветных металлов адгезионные свойства ниже, чем у черных. Следующим этапом являлась грунтовка, выравнивающая поверхность, но главная задача грунта — повышение адгезии, то есть сцепления позолоты с поверхностью. После грунтовки проводится окраска, с ее помощью создается фон, а потом краска закрывается лаком. Он призван защитить грунт от проникновения влаги и создать гладкую поверхность. После этого применяется лак мордан, а уже затем — сусальное золото.
Химические методы нанесений покрытий являются одной из наиболее распространенной групп методов нанесения покрытий. Реализуется этот метод путем осаждения покрытия в жидкости или из парогазовой среды (метод CVD) в результате прохождения химических реакций без пропускания через раствор электрического тока.
К электрохимическим методам нанесения покрытий относят методы получения металлических и неметаллических неорганических покрытий на электродах, опущенных в электролит при прохождении через электролит электрического тока. Осаждение металла из электролита на катоде относят к гальваническим методам покрытия. Создание неорганических неметаллических покрытий на катоде в соответствии с ГОСТ 9008-82 относят к анодно-окисным покрытиям, как разновидности электрохимических покрытий.
Газотермические методы нанесения покрытийосуществляются распылением газовой струей нагретого до жидкого или вязкотекучего состояния диспергированного материала. К этой группе методов относятгазопламенные, газоплазменные, светолучевые методы, метод электродуговой металлизации, детонационное напыление.
В качестве примера реализации газотермического метода напыления далее приведено описание плазменного метода нанесения покрытия.
Плазменное напылениехарактеризуется тем, что нагрев вещества до температур плавления осуществляется в дуговом разряде, а расплавленный материал в капельной форме направляется на изделие потоком высокотемпературной плазмы. В этом отношении плазменное напыление имеет по своим физическим и технологическим основам много общего с плазменной наплавкой с присадочной проволокой. Отличие этого технологического метода по области применения от плазменной наплавки заключается в первую очередь тем, что на поверхность заготовки, называемой при напылении подложкой, наносится покрытие — слой материала малой толщины (10-6…10-3 м). Напыляемый материал нагревается в плазмотроне и затем с потоком плазмы осаждается на подложку. Температура подложки может меняться в широких пределах.
Для реализации процесса плазменного напыления существуют несколько схем, которые сводят к двум схемам, отличающимся по виду используемого для напыления исходного материала: порошок (рис. 4.2,а) и проволока (рис. 4.2,б).
В первом случае электрическая дуга 1 (рис. 4.2, а) горит между неплавящимися охлаждаемыми катодом 3 и соплом 2, между которыми прокачивается плазмообразующий газ 4. Для подачи в плазменную струю порошка, находящегося в загрузочном бункере 5, применяется специальный дозатор 6, который позволяет смешивать порошок с транспортирующим газом 7 и точно регулировать расход порошка. Для защиты напыленного слоя от окисления может применяться специальное сопло, через которое прокачивается инертный газ 8. Изменяя расстояние от торца сопла до напыляемой заготовки L, можно регулировать температуру плазменной струи с жидкой фазой напыляемого материала в момент достижения ими поверхности изделия.
Процесс формирования покрытия на подложке не требует ее поверхностного расплавления. Температура подложки не превышает 300 0С, а для расплавления напыляемых частиц материала достаточно иметь температуру плазмы ниже 7000 0С. При этих условиях, несмотря на малое время пребывания частиц в потоке плазмы, происходит их нагрев с полным или поверхностным расплавлением. Одновременно частицы разгоняются до скорости 300…800 м/с.
При попадании напыляемого материала в виде жидких капель на подложку происходит их растекание, деформация, охлаждение и кристаллизация. При этом на поверхности материала подложки первые частицы закрепляются чисто механически, за счет адгезии, но если возможно химическое взаимодействие между материалами подложки и напыления, то образуются их соединения, увеличивающие прочность сцепления покрытия с основным материалом.
В связи с этим при плазменном напылении используют плазмотроны косвенного действия, когда электрическая дуга зажигается между катодом и анодом, расположенными внутри плазмотрона. Из этих же соображений в стационарных условиях для реализации плазменного напыления может быть рациональным применение высокочастотных плазмотронов.
При плазменном напылении покрытия могут быть получены из многих как металлических, так и неметаллических материалов, которые используются в виде порошкового материала с размером частиц 5…150 мкм. При этом свойства материала подложки (заготовки) после нанесения покрытия практически не изменяются.
Весь процесс — от нагрева частицы в струе плазмы до ее охлаждения на поверхности подложки — происходит за время 10-3…10-4 с. Время кристаллизации при этом составляет 10-5…10-7 с.
Исходя из физических особенностей процесса, видно, что для покрытий, наносимых плазменным напылением, нельзя применять материалы, разлагающиеся или возгоняющиеся при нагреве до высоких температур.
Покрытия, полученные методом плазменного напыления, обладают высокой плотностью и хорошим сцеплением с основой. Прочность сцепления покрытия с поверхностью изделия в среднем равна 10…55 МПа на отрыв, а некоторых случаях она достигает 120 МПа. Методом плазменного напыления создаются покрытия с плотной, малопористой структурой. Пористость покрытия находится в пределах 8...15 %. Толщина покрытия обычно не более 1 мм,так как при ее увеличении в напыляемом слое возникают напряжения, стремящиеся отделить этот слой от поверхности изделия.
При проведении процессов металлизации, т. е. при создании металлического слоя на поверхности изделия, чаще всего используют схему плазменного напыления, представленную на рисунке 4.2, б. Металлизации могут подвергаться как металлические, так и неметаллические изделия. В этом случае, также как и при порошковом напылении, применяют плазмотроны косвенного действия, но одним из электродов становится проволока из напыляемого материала2, непрерывно поступающая внутрь плазмотрона. Электрическая дуга 3 горит между проволокой и соплом 4, являющимся катодом. Плазмообразующий газ 5 выдувает расплавленные частицы металла проволоки, поток которых 6 напыляется на поверхность заготовки 1. Этот процесс применяется при создании на металлических изделиях (особенно крупногабаритных) защитного покрытия. При металлизации неметаллических изделий на их поверхности может создаваться электропроводный слой, имеющий самостоятельное значение или используемый для дальнейшей гальванической обработки.
Для получения покрытия требуемого качества при максимальной производительности требуется согласование параметров режима плазменного напыления, в том числе: мощности и температуры плазменного потока (струи), его скорости, видов плазмообразующего, транспортирующего и защитного газов (их расхода, скорости и сечения потоков), расстояния до подложки (заготовки) и т. д. Поэтому общие рекомендации по реализации процессов плазменного напыления не позволяют определить режимы проведения процесса в конкретных условиях применения, что требует проведения технологических исследований для определения оптимальных управляющих параметров процесса при выполнении конкретных технологических процессов.
Ряд проблем по достижению высокого качества плазменного напыления связан с разностью коэффициентов теплового расширения основного и напыляемого материалов. Это различие приводит к появлению внутренних напряжений как в напыленном слое, так и в поверхностном слое изделия. Эти напряжения могут привести непосредственно при охлаждении или в процессе работы изделия к отрыву напыленного слоя от основного материала. Возможность отрыва покрытия от подложки является одной из причин того, что подложку не нагревают до высоких температур (обычно ниже 300 °С).
По этой же причине при напылении на поверхность металлических изделий керамических слоев применяют напыление с переходными слоями между основой и покрытием из материалов, имеющих средние значения коэффициента термического расширения между значениями коэффициентов линейного расширения материала подложки и напыляемого материала. Указанные сложные физические особенности процессов напыления, а также то, что специального оборудования для плазменного напыления не выпускается, снижает их конкурентоспособность по отношению к другим методам нанесения покрытий на изделия.
Детонационное напыление — одна из разновидностей газотермического напыленияпромышленных покрытий, в основе которого лежит принцип нагрева напыляемого материала (обычно порошка) с последующим его ускорением и переносом на напыляемую деталь с помощью продуктов детонации. При детонационном напылении для нагрева и ускорения напыляемого материала используется энергия продуктов детонации газокислородного топлива. В качестве горючего газа обычно применяется пропан-бутановая смесь.
Детонационное напыление (рис.4.3) производится несколькими циклами в секунду, за каждый цикл толщина напыленного слоя составляет около 6 мкм.
Рис. 4.3. Детонационное напыление:
1 — подача ацетилена, 2 — кислород, 3 — азот, 4 — напыляемый порошок, 5 — детонатор, 6 — водоохлаждающая труба, 7 — заготовка (основа)
Диспергированные частицы имеют высокую температуру (более 4000 оС) и скорость (более 800 м/с). При этом температура основного металла невелика, что исключает его тепловое деформирование. Однако деформация может произойти от действия детонационной волны, это и является ограничением применения данного метода. Стоимость детонационного оборудования также велика, требуется наличие специальной камеры.
Благодаря высокой скорости напыляемых частиц (600…1000 м/сек.), детонационные покрытия обладают плотностью, близкой к плотности спеченного материала и высокой адгезией. Детонационное напыление позволяет напылять широкий круг материалов: металлы и их сплавы, оксиды, твердые сплавы на основе карбидов. При этом нагрев напыляемого изделия незначителен.
Детонационное напыление из-за своего дискретного характера является очень экономичным, но не слишком производительным методом (по сравнению, например, с высокоскоростным газопламенным напылением). Как правило, оно экономично для напыления поверхностей площадью не более нескольких квадратных сантиметров. Благодаря высокой плотности и адгезии получаемых детонационным способом покрытия широко применяются в авиации, автомобильной и других областях машиностроения.
Вакуумные покрытия.В основе процессов, протекающих в зоне формирования покрытий в вакууме, лежит физическая конденсация потока частиц материала покрытия, находящегося в атомарном, молекулярном или ионизированном состоянии, на поверхность заготовки. Для получения потока (пара) частиц используют различные источники энергетического воздействия на материал. В связи с этим различают формирование осаждаемого потока частиц посредством термического испарения материала, ионным распылением и взрывным испарением-распылением. По этому признаку вакуумные покрытия подразделяют на термические вакуумные, ионно-плазменные и плазменно-дуговые (ионно-лучевые) покрытия. Основы технологий нанесения вакуумных покрытий, их характеристики и области применения будут рассмотрены в разделе 5.4.
Дата добавления: 2018-04-04; просмотров: 3092; Мы поможем в написании вашей работы! |
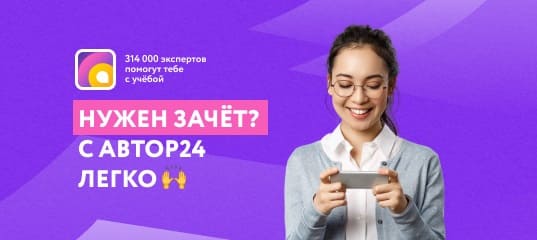
Мы поможем в написании ваших работ!