Производство полимерных материалов
Химия органического синтеза дает большую долю продукции химической промышленности. Синтетические материалы создают новую сырьевую базу для промышленности, строительства. В основном они дешевле и лучшего качества чем натуральные, но имеют особые гигиенические свойства.
Химия органического синтеза включает заводы, производящие полуфабрикаты для получения полимеров. Отрасль использует в основном нефтяное сырье.
Полимерными материалами называют вещества природного или искусственного происхождения, макромолекулы которых состоят из одинаковых многократно повторяющихся групп атомов, называемых мономерными (элементарными) звеньями. Число моно-мерных звеньев, входящих в состав макромолекулы, – от 100 до 1000. Величина молекулярной массы оказывает влияние на свойства полимеров. Так, с увеличением молекулярной массы уменьшается растворимость полимера, повышается температура его плавления, возрастают прочность и твердость. Кроме того, свойства полимеров зависят от химического состава мономеров, формы цепей молекул и их строения (структуры полимера).
Полимеры классифицируют по ряду признаков. По происхождению полимеры подразделяются на:
- природные, или натуральные (например, биополимеры – белки, нуклеиновые кислоты, полисахариды);
- искусственные (получаемые химической переработкой природных полимеров, например, ацетилцеллюлоза);
- синтетические (получаемые путем синтеза низкомолекулярных веществ – мономеров).
|
|
В зависимости от строения макромолекул различают полимеры линейной, разветвленной и сетчатой структуры. Макромолекулы полимеров линейной структуры представляют собой открытую линейную цепь (например, натуральный каучук) или вытянутые в линию последовательные циклы (например, целлюлоза). Полимеры такого вида имеют невысокую прочность, легко плавятся, растворяются в органических растворителях. Макромолекулы полимеров разветвленной структуры имеют форму линейной цепи с ответвлениями в виде коротких ветвей. Такие полимеры, как правило, менее эластичны, при нагревании размягчаются, но трудно плавятся, в растворителях лишь набухают. Макромолекулы полимеров сетчатой структуры – результат связывания (сшивания) линейных и разветвленных цепей поперечными связями (мостиками). Эти полимеры чаще всего имеют кристаллическое строение, при повышенной температуре не плавятся, не разлагаются, не растворяются ни в каких растворителях и лишь иногда способны набухать (резина, поликонденсационные смолы).
По назначению полимерные материалы делятся на следующие группы:
- пластические массы (пластмассы, пластики) и композиты;
|
|
- эластомеры (каучуки и резины);
- химические волокна;
- лакокрасочные материалы, полимерные покрытия и пленки;
- клеи и герметики.
Полимерные материалы отличаются от традиционных материалов, издавна используемых человечеством, комплексом особых свойств, высокой экономичностью методов переработки в изделия, практически неограниченной сырьевой базой. Для полимерных материалов характерны следующие положительные свойства:
- малая плотность и, как следствие, – высокий условный показатель прочности (отношение временного сопротивления на разрыв к плотности), превышающий аналогичный показатель лучших сортов стали;
- устойчивость к воздействию агрессивных сред, атмосферному и радиационному;
- ярко выраженные радио- и электротехнические свойства, в том числе диэлектрические, мало зависящие от температуры и частоты электрического поля;
- широкий регулируемый диапазон фрикционных свойств;
- специфические оптические свойства, способность пропускать лучи света в широком диапазоне волн, в том числе ультрафиолетовые (70 % для полиметилметакрилата против 1–3 % для силикатного стекла);
- возможность целенаправленного изменения физико-механических и химических свойств полимеров, сочетания в одном материале противоположных качеств, например, твердости и гибкости.
|
|
К недостаткам полимерных материалов относятся:
- низкая теплостойкость (как правило, она не превышает 120 ° С, за исключением фторопластов и кремнийорганических полимеров);
- недостаточные по сравнению с металлическими сплавами твердость и прочность;
- ползучесть, т.е. изменение формы и прочности под механическими воздействиями, особенно при повышении температуры;
- большое тепловое расширение;
- низкая теплопроводность, затрудняющая отвод тепла;
- склонность к старению, т.е. деструктивному разрушению с течением времени и ухудшению показателей физико-механических свойств.
Тем не менее, использование современных полимеров позволяет снизить материалоемкость продукции за счет замены традиционных конструкционных материалов. Технически возможное и экономически целесообразное применение полимеров вместо металлических сплавов позволяет достичь значительной экономии капитальных затрат, так как для производства пластмасс требуются значительно меньшие капиталовложения, чем для производства эквивалентного объема металлов, особенно тяжелых цветных. Особенно эффективна замена полимерами тяжелых цветных металлов, коррозионностойкой стали, ценных сортов древесины.
|
|
Все синтетические полимеры производят двумя способами: полимеризацией и поликонденсацией.
Полимеризация – процесс соединения многих молекул мономера в макромолекулу полимера, имеющего тот же элементарный состав, что и исходный мономер. При реакциях полимеризации происходит разрыв двойных связей мономеров с образованием мономерных группировок, которые, соединяясь между собой, образуют молекулы полимера. Побочные продукты при этой реакции не выделяются. Процесс полимеризации может быть цепным и ступенчатым.
Поликонденсация – образование высокомолекулярного соединения в результате взаимодействия большого числа молекул двух или больше разных мономеров с одновременным выделением побочных низкомолекулярных продуктов реакции (Н20, NH3, СO2 и др.). Образующиеся при поликонденсации полимеры имеют как линейную (полиамиды, полиэфиры, поликарбонаты), так и пространственную структуру (аминокислоты, фенолоальдегидные смолы).
Пластические массы (пластмассы, пластики) – конструкционные материалы на основе полимеров, способные приобретать требуемую форму при нагревании под давлением и устойчиво сохранять ее после охлаждения. По составу пластмассы бывают простые (ненаполненные) и сложные (наполненные). Простые пластмассы состоят только из полимеров (иногда с добавкой пластификатора или красителя).
Сложные пластмассы содержат, кроме того, ряд других компонентов в зависимости от требуемых свойств материала. Основными компонентами сложных пластмасс являются связующие вещества, наполнители, пластификаторы, отверждающие вещества и катализаторы, стабилизаторы, красители, газообразователи.
Связующие вещества – это полимерная основа пластмасс (различные смолы, соединяющие в монолитный материал другие компоненты пластмассы). Они обусловливают основные свойства пластмасс.
Наполнители вводятся в состав пластмасс с целью направленного изменения их свойств, а также снижения расхода связующего вещества и удешевления пластмассы. В качестве наполнителей применяются порошкообразные, волокнистые и другие вещества как органического, так и неорганического происхождения.
Пластификаторы придают материалу повышенную пластичность, в результате чего облегчается формование изделий, уменьшается их хрупкость, особенно при низких температурах, увеличиваются гибкость и эластичность. В качестве пластификаторов используются вещества, химически инертные по отношению к другим компонентам смеси.
Отверждающие вещества и катализаторы вводятся в состав пластмасс для ускорения их перехода в твердое состояние. Стабилизаторы замедляют процесс старения пластмасс, но не влияют на их первоначальные свойства. Красители – вещества, которые придают пластмассе тот или иной цвет или оттенок, улучшая ее внешний вид. Газообразователи вводятся в состав пластмасс с целью образования в них пор, обеспечивающих уменьшение плотности и повышение теплоизолирующих свойств (например, в производстве пенопластов, поропластов).
Классифицируют пластмассы по тем же признакам, что и полимерные материалы. Главное преимущество использования пластмасс по сравнению с другими материалами – это простота переработки их в изделия.
Из полимеризационных пластмасс наиболее широко используются: полиэтилен, полипропилен, полистирол, винипласт, фторопласт и полиакрилат.
Полиэтилен является продуктом полимеризации этилена. Его получают при крекинге нефти, из коксового газа, из этилового спирта. Полиэтилен выпускается в виде пленок толщиной 0,03–0,3 мм, шириной 1400 мм и длиной до 300 м, а также в виде листов толщиной 1–6 мм и шириной до 1400 мм. Полиэтилен обладает исключительно высокими диэлектрическими свойствами, поэтому находит широкое применение при изготовлении кабельной изоляции, деталей для радиоаппаратуры, телевизионных и телеграфных установок. Вследствие водонепроницаемости и химической стойкости (при температурах до 60°С он стоек против соляной, серной, азотной кислот, растворов щелочей и многих органических растворителей) полиэтилен применяют для изготовления деталей химической аппаратуры, нефте- и газопроводов, цистерн, им выстилают каналы оросительных сетей. Полиэтилен нетоксичен, поэтому из него изготавливают пленку для хранения пищевых продуктов, применяют для изготовления предметов домашнего обихода. Так как полиэтилен прозрачен, то его применяют в качестве заменителя стекла, в сельском хозяйстве полиэтиленовой пленкой покрывают парники. Из полиэтилена изготавливают крышки подшипников, детали вентиляторов и насосов, гайки, шайбы, полые изделия вместимостью до 200 л, тару для хранения и транспортировки кислот и щелочей.
Полипропилен является производным этилена. По сравнению с полиэтиленом полипропилен имеет более высокую механическую прочность и жесткость, большую теплостойкость и меньшую склонность к старению. Недостатком полипропилена является его невысокая морозостойкость. Полипропилен применяют для изготовления антикоррозионного покрытия резервуаров, труб и арматуры трубопроводов, изоляторов, а также для изготовления деталей, применяемых при работе в агрессивных средах. Из полипропилена изготавливают корпуса автомобилей и аккумуляторов, прокладки, трубы, фланцы, водонапорную арматуру, пленки, пленочные покрытия бумаги и картона, корпуса воздушных фильтров, конденсаторы, зубчатые и червячные колеса, ролики, подшипники скольжения, фильтры масляных и воздушных систем, уплотнения, детали приборов и автоматов точной механики, кулачковые механизмы, детали телевизоров, холодильников, стиральных машин, изоляцию проводов и кабелей и т.д.
Полипропилен обладает хорошими технологическими свойствами – способностью к литью, экструзии, прессованию, сварке и обработке резанием. Отходы при производстве полипропилена и отработавшие изделия из него используют для повторной переработки.
Полистирол – продукт полимеризации стирола. Твердый, жесткий, бесцветный, прозрачный полимер, водостоек, обладает прекрасными диэлектрическими свойствами, химически инертен, легко окрашивается в различные цвета. Недостатками полистирола являются его повышенная хрупкость при ударных нагрузках, склонность к старению, невысокая тепло- и морозостойкость. Полистирол перерабатывается в изделия литьем под давлением, экструзией. Его применяют для изготовления деталей радио- и электроаппаратуры, предметов домашнего обихода, детских игрушек, трубок для изоляции проводов, пленок для изоляции в электрических кабелях и конденсаторах, открытых емкостей (лотков, тарелок, подносов), прокладок, втулок, светофильтров, крупногабаритных изделий радиотехники (корпусов транзисторных приемников), деталей электропылесосов, мебельной фурнитуры, конструкционных изделий с антистатическими свойствами. Ударопрочным полистиролом облицовывают пассажирские вагоны, салоны автобусов и самолетов. Из него изготавливают крупногабаритные детали холодильников, корпуса радиоприемников, телефонных аппаратов и т. д.
Поливинилхлоридные пластмассы (пластмассы на основе поливинилхлорида, полихлорвинил или сокращенно ПХВ) имеют хорошие электроизоляционные свойства, химически стойки, не поддерживают горения, атмосферо-, водо-, масло- и бензостойки. Обработкой порошкового ПХВ получают винипласт в виде пленок, листов, труб, стержней. Винипластовые детали хорошо механически обрабатываются и хорошо свариваются. Из винипласта изготавливают трубы для транспортировки воды, агрессивных жидкостей и газов, коррозионностойкие емкости, защитные покрытия для электропроводки, детали вентиляционных установок, теплообменников, шланги вакуум-проводов, защитные покрытия для металлических емкостей, изоляцию проводов и кабелей. Поливинилхлорид используют для получения пенопластов, линолеума, искусственной кожи, объемной тары, товаров бытовой химии, вибропоглощающих материалов в машиностроении и на всех видах транспорта, водо-, бензо- и антифризостойких трубок, прокладок и т.д.
Фторопласты – производные этилена, где все атомы водорода заменены галогенами. Наиболее широкое распространение получил фторопласт-4 (тефлон), или политетрафторэтилен. Фторопласт-4 в изделиях представляет собой белое вещество со скользкой, не смачивающейся водой поверхностью. Он имеет исключительно высокие диэлектрические свойства, по химической стойкости превосходит все известные материалы, включая благородные металлы, может длительно выдерживать температуры до 250ºС. Пленка из него не становится хрупкой даже в среде жидкого гелия. Он стоек к воздействию минеральных и органических щелочей, кислот, органических растворителей, не набухает в воде, не смачивается жидкостями и вязкотекучими средами пищевых производств (тестом, патокой, вареньем и т.д.). При непосредственном контакте не оказывает влияния на организм человека, разрушается только под действием расплавленных щелочных металлов. Фторопласт-4 имеет низкий коэффициент трения и применяется для изготовления подшипников скольжения без смазки. Фторопласты широко применяются в электро- и радиотехнической промышленности, а также для изготовления химически стойких труб, кранов, мембран, насосов, подшипников, деталей медицинской техники, коррозионностойких конструкций, тепло- и морозостойких деталей (втулок, пластин, дисков, прокладок, сальников, клапанов), для облицовки внутренних поверхностей различных криогенных емкостей.
Полиакрилаты. Наиболее известным представителем этой группы является органическое стекло (оргстекло). Оно термопластично, достаточно прочно, легче стекла, обладает высокой прозрачностью и пропускает ультрафиолетовые лучи, имеет высокий коэффициент преломления. Его применяют для изготовления оптических стекол, из него делают окна самолетов и кораблей, предметы домашнего обихода. Недостаток – низкая поверхностная твердость.
Полиамиды включают в себя такие известные пластмассы, как нейлон, капрон и др. Их применяют для изготовления зубчатых колес и др. деталей машин – получают методом литья под давлением, для электроизоляции проводов – путем нанесения на них расплавленной смолы, для изготовления волокна – при продавливании смолы через фильеры, для изготовления пленки и клея. Волокна из полиамидов используют для корда автопокрышек, изготовления буксировочных канатов, для производства чулочно-носочных изделий и т.д. Полиамиды имеют низкий коэффициент трения и могут использоваться в качестве подшипников.
Полиуретаны характеризуются высокой упругостью, износостойкостью, низким коэффициентом трения. Их используют для изготовления изоляции, фильтровальных и парашютных тканей, применяют для получения пенопластов, каучуков, пленок антикоррозионных покрытий.
Основу термореактивных пластмасс (реактопластов) составляет связующее вещество – химически затвердевающая термореактивная смола. Кроме того, в состав реактопластов входят наполнители, пластификаторы, отвердители, ускорители или замедлители, растворители. Наполнителями, определяющими структурную основу пластмасс, могут быть порошковые, волокнистые и гибкие листовые материалы. Наиболее известными являются слоистые пластики, представляющие собой композиции из чередующихся слоев связующей смолы и листового наполнителя. В зависимости от вида наполнителя слоистые пластики получают свое наименование: гетинакс (наполнитель – бумага), текстолит (наполнитель – хлопчатобумажная ткань), асботекстолит (наполнитель – асбестовая ткань), стеклотекстолит (наполнитель – стеклянная ткань), древеснослоистые пластики – ДСП (наполнитель – древесный шпон).
Слоистые наполнители пропитывают смолой, сушат и режут по размеру. Из готовых листов в этажных прессах горячим способом прессуют плиты, а в пресс-формах – иные заготовки или детали.
Из полимерных материалов делают зерна, нити, пленки, трубы и самые разнообразные изделия сложной формы. Выбор метода изготовления изделия определяется видом полимера, его исходным состоянием, а также формой и размерами изделия.
Основными методами переработки пластмасс являются: литье, прессование, экструзия, горячее напыление, вакуумное и пневматическое формирование, вальцевание, обработка на станках со снятием стружки и др. Большинство пластмасс перерабатывают в вязкотекучем состоянии способами прессования, литья и выдавливания.
Переработка пластмасс – комплекс процессов, обеспечивающий получение готовых изделий или полуфабрикатов из пластмасс с заданными свойствами на специальном оборудовании. Переработке пластмасс предшествуют проектирование рациональной конструкции изделия, выбор оптимального метода переработки и условий его осуществления, разработка состава материала, наиболее пригодного для выбранного метода производства, оборудования и последующих условий эксплуатации.
Технология переработки пластмасс включает следующие основные стадии:
- приготовление материала на основе исходного полимера и подготовка его к формованию (например, таблетирование);
- формование полученного материала и изготовление из него изделий или полуфабрикатов;
- последующая обработка с целью улучшения свойств поли мера или изделия (термическая обработка, механическая обработка, сварка и др.).
Способы формования изделий из пластмасс зависят от их отношения к нагреву, т.е. от того, являются они термопластами или реактопластами. Прямое (компрессионное) прессование – самый распространенный способ переработки пластмасс (преимущественно – термореактивных). Прессование включает следующие операции: дозировку прессовочного материала, загрузку его в пресс-форму, закрытие пресс-формы, выдержку изделия в пресс-форме при повышенной температуре (130–190 °С) и под давлением (20–60 МПа) для осуществления реакции поликонденсации, разъем пресс-формы, извлечение изделия, очистку и подготовку пресс-формы для следующей запрессовки, очистку изделия от заусенцев. Увеличению производительности прессования способствуют предварительные нагревание прессовочных материалов и их таблетирование. Для переработки термопластичных материалов метод прессования используется значительно реже, так как в этом случае после каждой запрессовки прессуемое изделие нужно охлаждать в пресс-форме до полного затвердевания, что резко снижает производительность установки.
Экструзия (шприцевание или выдавливание) – процесс получения профилированных изделий большой длины (трубы, стержни, ленты, нити) непрерывным или периодическим выдавливанием. Шприцевание выполняется на экструдерах, основной рабочей деталью которых является винт (червяк, шнек), или на гидравлических прессах, имеющих поршень (плунжер), совершающий возвратно-поступательное движение. Методом экструзии можно перерабатывать большинство термопластичных материалов. В промышленности наиболее широкое применение получили одночервячные экструдеры.
После выхода из экструдера некоторые виды профилированных материалов подвергаются таким операциям, как охлаждение, вытяжка, намотка, обрезка. Для их осуществления экструдеры дооборудуют соответствующими механизмами (тянущими, охлаждающими, устройствами для намотки и обрезки). В отдельных случаях вытяжку совмещают с намоткой, например, при производстве нитей или листового материала.
Методом выдавливания перерабатывается в полимерные пленки большинство синтетических полимеров, для чего используют экструдеры с кольцевой или плоскощелевой головкой. В первом случае расплав полимера экструдируется в виде рукава, который растягивается сжатым воздухом. Рукавный способ – наиболее производительный и экономичный метод изготовления полимерных пленок. Плоскощелевой способ позволяет формовать полимерные пленки, которые в некоторых случаях дополнительно подвергаются разглаживанию на гладильных валках. Он предпочтительнее в тех случаях, когда требуется получить пленку равной толщины с высоким качеством поверхности.
Экструзией можно получать объемные, многослойные и вспененные изделия с поверхностью, имитирующей различные декоративные материалы; непрерывные изделия – пленки, профили самого разнообразного типа, листы, трубы и шланги, наносить покрытия из пластмассы на проволоку. Масса погонного метра изделий, изготовленных методом экструзии, может составлять от нескольких граммов до 100 кг и более. Им получают пленки шириной до 25 м и трубы диаметром до 1,2 м. Производительность крупных экструдеров достигает 3–3,5 т/ч, степень автоматизации производства также достаточно высока.
Недостатки экструзии – сложность управления процессом и высокая стоимость оборудования.
Листовое формование предназначено для получения из листов термопластичных материалов изделий коробчатой формы или профилированных листов. Формование этим способом (рис. 9.14) осуществляется путем штампования, сжатым воздухом (пневмоформование), вакуумом (вакуум-формование). Формование из листов является единственным методом изготовления изделий с большой поверхностью и малой толщиной стенки.
2.12. Особенности организации и управления производством
на предприятиях нефтеперерабатывающей промышленности
В зависимости от получаемых из нефти продуктов существует три варианта ее переработки:
- топливный, применяемый для получения моторного и котельного топлива;
- топливно-масляный, которым вырабатывают топливо и смазочные масла;
- нефтехимический (комплексный), продуктами которого являются не только топливо и масла, но и сырье для химической промышленности (олефины, ароматические и предельные углеводороды и др.).
Жидкое топливо, полученное из нефти, в зависимости от его использования делят на:
- карбюраторное (автомобильный бензин) – для двигателей внутреннего сгорания;
- реактивное (керосин) – для реактивных и газотурбинных двигателей;
- дизельное (газойль, соляровый дистиллят) – для дизельных двигателей;
- котельное (мазут) – для топок паровых котлов, генераторных установок, металлургических печей.
Продукты переработки нефти представлены на рисунке 9.
В общем случае переработка нефти на нефтепродукты включает ее добычу, подготовку и процессы первичной и вторичной переработки.
Первичная переработка нефти, осуществляемая физическими методами (главным образом прямой перегонкой), состоит в разделении ее на отдельные фракции (дистилляты), каждая из которых является смесью углеводородов.
Вторичная нефтепереработка представляет собой разнообразные процессы переработки нефтепродуктов, полученных в результате первичной переработки. Эти процессы сопровождаются деструктивными превращениями содержащихся в нефтепродуктах углеводородов и являются по своей сути химическими процессами.
Процесс прямой перегонки основан на явлениях испарения и конденсации смеси веществ с различными температурами кипения. Кипение смеси начинается при температуре, равной средней температуре кипения составных частей. При этом в парообразную фазу переходят преимущественно легкие низкокипящие компоненты (имеющие меньшую плотность и кипящие при более низких температурах), а в жидкой фазе остаются высококипящие (имеющие большую плотность и кипящие при более высоких температурах). Если образовавшуюся парообразную фазу отвести и охладить, из нее конденсируется жидкая. В нее перейдут главным образом высококипящие (тяжелые) компоненты, а в парообразной фазе останутся легкие. Схема переработки нефти представлена на рисунке 10.
Рис.9. Продукты переработки нефти
Рис.10. Схема переработки нефти
Таким образом, из исходной смеси получают три фракции. Одна из них, оставшаяся жидкой при кипении, содержит преимущественно высококипящие компоненты; вторая, сконденсировавшаяся, имеет состав, близкий к составу исходной смеси; третья, парообразная, содержит в основном низкокипящие компоненты.
За счет однократных (перегонка) либо многократных (ректификация) процессов кипения и конденсации полученных фракций можно добиться достаточно полного разделения низко- и высококипящих компонентов.
Технологический процесс прямой перегонки нефти состоит из четырех основных операций: нагрева смеси, испарения, конденсации и охлаждения полученных фракций.
При двухступенчатой перегонке нефть предварительно обессоливают и обезвоживают, затем нагревают в трубчатой печи первой ступени до температуры 300–350 ° С (на 25–30 °С выше температуры кипения). Разделение нефти на фракции производят в ректификационной колонне, которая представляет собой цилиндрический аппарат высотой 25–55 м и диаметром 5–7 м. Предварительно нагретую нефть подают в нижнюю часть колонны. Здесь нефть закипает и разделяется на две фазы: парообразную и жидкую. Жидкие продукты стекают вниз, а пары поднимаются вверх по колонне. В верхнюю часть колонны подается орошающая жидкость (флегма). Поднимающиеся снизу пары многократно контактируют по высоте колонны со стекающей жидкой фазой. Встречаясь с поднимающимися горячими парами, орошающая колонну жидкость нагревается и частично испаряется. Пары, отдавая ей теплоту, конденсируются, и конденсат стекает в нижнюю часть колонны. По мере подъема паров их температура уменьшается, при этом стекающая вниз флегма все более обогащается тяжелыми фракциями, поднимающиеся пары – легкими. Внизу колонны собирается жидкость, содержащая наиболее тяжелые фракции (мазут). Мазут сливается из нижней части колонны и охлаждается в теплообменниках, нагревая при этом подаваемую в колонну нефть.
Для поддержания процесса кипения в ректификационную колонну подается перегретый пар, который уносит с собой остатки легких фракций, не испарившихся ранее. Самая легкая бензиновая фракция при температуре 180–200 ° С отводится из колонны в виде паров в конденсатор и отделяется от воды в сепараторе. Часть бензиновой фракции возвращается в колонну для орошения. С промежуточных зон колонны отводятся так называемые средние фракции: керосиновая, кипящая при температуре 200–300 °С, и газойлевая (температура кипения 300–350 °С).
Полученный после первоначальной перегонки мазут (его выход – около 55 % исходной нефти) из первой ректификационной колонны перекачивается в трубчатую печь второй ступени, где нагревается до 400–420 °С. Из печи мазут поступает во вторую ректификационную колонну, работающую при давлении ниже атмосферного (остаточное давление – 5–8 кПа). Из нижней части этой колонны выводится гудрон, а по высоте отбираются масляные дистилляты. Производительность двухступенчатых установок составляет 8–9 тыс. т нефти в сутки. Выход бензина при прямой перегонке зависит от фракционного состава нефти и колеблется от 3 до 15 %. Сравнительно малый выход бензина (до 15 %) при прямой перегонке вызывает необходимость переработки других, менее ценных фракций, получаемых при прямой перегонке нефти и содержащих тяжелые молекулы углеводородов. Такая переработка называется крекингом.
Крекинг (англ. to crack – раскалывать, расщеплять) – расщепление длинных молекул тяжелых углеводородов, входящих в состав, например, мазута, на более короткие молекулы легких низкокипящих продуктов. Главными факторами, влияющими на протекание процесса крекинга, являются температура и продолжительность выдержки: чем выше температура и больше продолжительность выдержки, тем полнее идет процесс и больше выход продуктов крекинга. Большое влияние на ход и направление процесса крекинга оказывают катализаторы. При соответствующем подборе катализатора можно проводить реакцию при меньших температурах, обеспечивая получение необходимых продуктов и увеличение их выхода.
Исходя из вышеизложенного, различают две разновидности крекинга: термический и каталитический. Термический крекинг ведут при повышенных температурах под высоким давлением (температура 450–500 °С и давление 2–7 МПа). Основной целью термического крекинга является получение светлого топлива из мазута или гудрона. Термический крекинг осуществляется в трубчатых печах, в которых происходит расщепление тяжелых углеводородов. Далее смесь продуктов крекинга и непрореагировавшего сырья проходит через испаритель, в котором отделяется крекинг-остаток, т.е. вещества, не поддающиеся крекингу. Легкие продукты поступают в ректификационную колонну для разделения и получения легких товарных фракций.
Каталитический крекинг – переработка нефтепродуктов в присутствии катализатора. В последнее время этот метод находит все большее применение для получения светлых нефтепродуктов, в том числе бензинов. К его достоинствам относят:
- высокую скорость процесса, в 500–4000 раз превышающую скорость термического крекинга, и как следствие, – более мягкие условия процесса и меньшие энергозатраты;
- увеличение выхода товарных продуктов, в том числе бензинов, характеризующихся высоким октановым числом и большей стабильностью при хранении;
- большой выход газообразных углеводородов, являющихся сырьем для органического синтеза;
- использование сырья с высоким содержанием серы вследствие гидрирования сернистых соединений и выделения их в газовую фазу с последующей утилизацией.
В качестве катализаторов на установках каталитического крекинга используются синтетические алюмосиликаты. Бензин каталитического крекинга характеризуется хорошими эксплуатационными свойствами. Газы каталитического крекинга выгодно отличаются высоким содержанием изобутана и бутилена, используемых в производстве синтетических каучуков.
2.13. Особенности организации и управления производством
на предприятиях деревообработки
Деревообрабатывающая промышленность — отрасль лесной промышленности. Используя как сырье различные лесоматериалы, деревообрабатывающая промышленность осуществляет механическую и химико-механическую обработку и переработку древесины.
Основная задача деревообрабатывающего производства — глубокая переработка древесины, включая максимальное использование отходов от лесозаготовок и деревообработки, изыскание дополнительных резервов древесины и ее экономии во всех отраслях народного хозяйства.
Деревообрабатывающая промышленность производит такие материалы, как шпалы, фанера, древесные плиты, брусья, а также готовые детали для вагоностроения, автостроения, авиастроения, судостроения, спички, мебель, деревянную тару и др.
Производство фанеры отличается высокой нормой расхода сырья и ориентацией на березовые древостои.
Фанера, которую также называют древесно-слоистой плитой (ДСП), представляет собой многослойный строительный материал, который производится путем склеивания предварительно подготовленного (лущеного) шпона, иногда в композиции с другими материалами. Количество слоев шпона, как правило, нечетное (свыше трех). Для увеличения прочности листа ДСП слои шпона накладываются таким образом, чтобы волокна древесины каждого нового слоя были перпендикулярны нижнему листу. Если же количество слоев шпона в фанере четное, то два средних слоя обязательно должны иметь одинаковое направление волокон. Лист фанеры имеет наружные (лицевой и оборотный) и внутренние слои шпона, которые отличаются качеством и иногда породой древесины. Виды фанеры классифицируются по конструктивным и технологическим признакам, определяющим ее эксплуатационные качества.
В зависимости от сферы применения различают фанеру общего назначения, которая изготавливается из трех и более слоев шпона и используется в производстве мебели, тары, в строительстве. Фанера такого вида в зависимости от применяемого клея бывает следующих марок: фанера повышенной водостойкости с применением фенолоформальдегидных клеев; фанера средней водостойкости с применением карбамидоформальдегидных клеев; фанера средней водостойкости с применением альбуминоказеиновых клеев.
Шпон наружных и внутренних слоев фанеры производится из древесины различных пород. Причем вид фанеры по материалу определяется по виду древесины, из которой изготовлены ее наружные слои. При этом слои шпона, которые расположены симметрично относительно продольной оси сечения фанеры, должны быть одинаковой толщины и из одной породы древесины.
В зависимости от качества шпона наружных слоев фанера делится на пять различных сортов – А/АВ, АВ/В, В/ВВ, ВВ/С, С/С. Также по стандартам разрешается следующее сочетание лицевых слоев: А/В, А/ВВ, АВ/ВВ, В/С. Фанера может быть шлифованной или нешлифованной с одной или обеих сторон. При этом шероховатость нешлифованной фанеры из древесины лиственных пород не должна превышать 200 мкм, шлифованной – 80 мкм, а из древесины хвойных пород – не более 300 и 200 мкм соответственно.
Фанера производится в листах длиной от 1220 до 2440 мм, шириной от 725 до 1525 мм и толщиной 1,5-18 мм. Фанера длиной по одной стороне более 1800 мм называется большеформатной. Фанера, у которой больший размер совпадает с продольным направлением волокон шпона наружных слоев, называется продольной. Другие виды фанеры носят название поперечных. Влажность фанеры марок ФСФ и ФК должна составлять 5-10 %, а ДСП марки ФБА – 6-15 %. Влажность фанеры, которая используется в мебельном производстве, не должна по стандарту превышать 10 %.
Облицовочная фанера состоит, как правило, из трех и более слоев лущеного шпона. При этом один или оба наружных слоя такой фанеры изготавливается из облицовочного материала.
Облицовывание может быть самостоятельной процедурой или же осуществляться при склеивании паркета. Фанера, которая облицовывается строганым шпоном, делится на разные марки, в зависимости от используемого клея: с применением фенолоформальдегидного клея (ФОФ) и с применением карбамидоформальдегидного клея (ФОК). Для облицовывания используется строганый шпон толщиной до 1 мм. Шпон может быть различных сортов и текстуры: первого и второго сортов, радиальный, полурадиальный, тангентальный и тангентально-торцовой.
Фанера марки ФОФ используется в условиях повышенных атмосферных воздействий (например, в строительстве, судостроении и т. д.). Для того чтобы придать поверхности фанеры большую стойкость, шпон в некоторых случаях пропитывают меламиновой смолой. Фанеру, которая облицовывается бумагой, изготавливают из лущеного шпона с облицовочным покрытием, который выполняет защитно-декоративные функции.
Бывает и декоративная фанера, которая, в зависимости от вида облицовочного покрытия и используемых смол, производится нескольких марок: ДФ-й, ДФ-3 с прозрачным бесцветным и окрашенным покрытием на основе сульфатной бумаги, ДФ-2 и ДФ-4 с непрозрачным бумажным покрытием с нанесенным на него рисунком (обычно с имитацией древесной текстуры).
В армированной фанере один или несколько внутренних слоев шпона заменяется листами резины, металла, металлическими сетками и другими, более прочными, нежели шпон, материалами. Это способствует повышению прочности материала без значительного увеличения массы. Для увеличения эластичности фанеры и снижения ее водопроницаемости она армируется листовой резиной.
Профилированная фанера представляет собой слоистый материал, поперечному сечению листа которого при склейке придается сложная форма (например, трапецеидальная или волнистая). Это позволяет добиться высокой жесткости листа фанеры вдоль профиля.
Строительную фанеру изготавливают из шпона хвойных пород (лиственницы и сосны) толщиной 2-4,5 мм или из комбинированных материалов. Фанера комбинированного вида изготавливается с чередующими слоями шпона из древесины хвойных пород толщиной от 2 мм и березового шпона толщиной от 1,5 мм или же только из чередующихся слоев березового шпона разной толщины. Наружные слои фанеры изготавливают из березового шпона толщиной 1 мм.
По качеству наружных слоев фанера из древесины хвойных слоев делится на шесть различных видов, в зависимости от того, предназначена ли она под прозрачную или непрозрачную отделку или для применения в скрытых от обрезания конструкциях. Комбинированная фанера производится семи различных сортов. Строительную фанеру производят с использованием клеев высокой водостойкости марок ФСФ и ФК. Она может быть как шлифованной, так и нешлифованной. Фанера, используемая для строительства, выпускается, в основном, больших форматов размером 2440 на 1220 мм толщиной от 8 до 19 мм. В зависимости от используемых материалов различаются различные сферы применения ДСП. Так, фанера из древесины хвойных пород предназначается для строительства сооружений сборно-щитового, каркасного и передвижного типа, применяется в вагоностроении и для возведения деревянных домов. Комбинированная фанера используется как обшивной материал. А ДСП из березового, ольхового шпона и из древесины хвойных пород производится на экспорт.
Березовая авиационная фанера производится из тонкого березового шпона высокого качества и используется для изготовления легких летательных аппаратов, музыкальных инструментов. Бакелизированная фанера изготавливается склеиванием листов березового лущеного шпона при взаимно перпендикулярном направлении волокон в смежных слоях фенолоформальдегидных смол. Такая фанера бывает различных марок, в зависимости от применяемого клея и способа его нанесения: ФСБ, ФБС1 (наружные слои пропитываются спирторастворимой смолой), ФБВ и ФБВ1 (наружные слои пропитаны водорастворимой смолой, а на внутренние слои нанесена спирторастворимая смола). Для изготовления такой фанеры используется шпон сорта В для наружных и сорта ВВ для внутренних слоев. Производится такая фанера при высоком давлении с применением большого количества клея, поэтому она отличается высокой прочностью.
Для изготовления фанеры используется шпон из древесины березы и реже других лиственных пород, а для внутренних слоев часто применяется шпон из древесины хвойных пород. Выбор сырья обусловлен ценами на него и технологическими свойствами материалов. В этом плане соотношение цены и качества древесины березы и хвойных пород наиболее оптимальное. Иногда применяются иные виды древесины (например, граб, бук, тополь, клен, ольха), но ДСП из них стоит дороже. Технология производства фанеры включает в себя несколько основных этапов. Вначале производится подготовка древесины для лущения. Для этого сырье сначала вымачивается с целью выравнивания общей влажности. Все это осуществляется практически вручную. После вымачивания бревна транспортируются на линию лущения. На втором этапе из предварительно вымоченных бревен изготавливают листы шпона. Размер готовых листов зависит от размера будущего фанерного листа. Листы шпона нарезаются при помощи роторных ножниц. Для оптимизации процесса производства все отходы, которые не используются для дальнейшего производства фанеры, поступают в рубительную машину, а потом используется для теплогенерирующей установки. На третьем этапе шпон высушивается в сушилке – многоэтажной роликовой системе, которая обеспечивает поэтажное прохождение шпона от входа к выходу за определенное время.
Время задается при помощи специальной программы, а сам же процесс сушки проходит при участии теплогенерирующей установки, которая работает на отходах лущения. Слои сначала сортируются, дефектные участки вырезаются, после чего все слои склеиваются. При прохождении через систему поверхностного контроля листы сортируются по влажности, потом пропитываются клеем и складываются послойно в так называемый «бутерброд». Для склейки шпона используется смола, бакелитовая пленка, клеи на основе фенолформальдегидных смол и т. д. Листы с большим количеством брака или низкого качества проходят сортировку отдельно. Все дефектные участки также вырезаются из полотнища, а на их место приклеиваются заплатки. Потом такие листы используются в середине фанерного листа. На предпоследнем этапе заранее подготовленные и проклеенные слои шпона отправляются под термопресс. Под воздействием веса и температуры формируется окончательная форма фанеры. На завершающем этапе фанере, в зависимости от ее применения, придается требуемая форма. Листы ламинируются и упаковываются.
Производство фанеры определенных видов и назначений может несколько отличаться от этой схемы. Так, например, для изготовления лущеного шпона с тангельной структурой используются специальные станки. При обработке с полена-чурака, которое предварительно проходит термообработку, аккуратно снимается верхний тонкий слой древесины по спирали. Такой шпон укладывается слоями особым образом. Направление волокон каждого слоя в фанерном листе направлено под одним углом от слоя, который находится в центре. Количество слоев шпона в такой фанере, как правило, тоже нечетное – от трех до двадцати трех.
Декоративная фанера обладает красивой текстурой, так как лущеный лист обычно включает в себя части нескольких годовых колец исходного древесного материала. Иногда для изготовления такой фанеры применяется способ лущения вполдерева, при котором срезы делаются параллельно оси бревна диаметрально к ней (в других случаях – по окружности). Коническое лущение позволяет добиться необычных срезов, как у стружки в машинке для механической заточки карандашей. Также слои для декоративной фанеры могут строгаться (так называемая волновая нарезка). В этом случае лущильные ножи затачивают волнообразно.
Декоративная фанера, которая используется преимущественно при изготовлении мебели, упаковывается в пачки из листов, полученных из одного ствола дерева одним и тем же способом резания или лущения. Клееная фанера изготавливается в больших листах различной толщины. Самые дорогие сорта фанеры облицовываются с одной или обеих сторон шпоном более ценных пород дерева.
Дата добавления: 2018-02-28; просмотров: 2468; Мы поможем в написании вашей работы! |
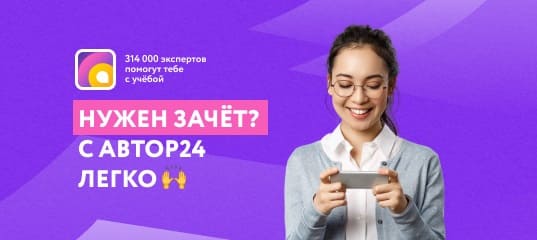
Мы поможем в написании ваших работ!