Сталь: классификация, производство и маркировка
Сталь − деформируемый (ковкий) сплав железа с углеродом (и другими элементами). Содержание углерода в стали, не превышает 2,14%, но не менее 0,022%. Сталь классифицируют по следующим признакам:
- по химическому составу (углеродистая, легированная);
- по назначению (конструкционная, инструментальная, специального назначения);
- по качеству (обыкновенного и высокого качества);
- по способу производства (конвертерная, мартеновская, электросталь);
- по степени раскисления (кипящая, полуспокойная, спокойная);
- по способу изготовления изделий (литая, кованная, катанная, штампованная).
Основой товарной классификации стали является ее химический состав, что отражается и в маркировке стали – в большинстве случаев наименование марки составляется таким образом, чтобы по ней можно было бы судить об основном химическом составе стали. Кроме того, учитывается ряд других признаков. По химическому составу стали делятся на углеродистые и легированные.
Углеродистой сталью называется сталь, не содержащая никаких специально введенных добавок, кроме углерода. При этом следует иметь в виду, что сталь всегда содержит примеси, наиболее вредными из которых являются сера и фосфор. Сера вызывает красноломкость стали – хрупкость при горячей обработке, фосфор – хладноломкость – хрупкость при нормальной и пониженной температуре. Кислород, азот, водород снижают пластичность стали.
|
|
Углерод в различных марках стали содержится от 0,1 до 1,35%. Содержание углерода определяет ее свойства и применение. Поэтому стали подразделяются на конструкционную – с содержанием углерода до 0,85% и инструментальную – с содержанием углерода от 0,65 до 1,35%. Чем больше углерода, тем тверже и прочнее сталь. Низкоуглеродистые стали отличаются большей пластичностью.
Конструкционной называют сталь, пригодную для изготовления различных деталей машин и конструкций. Она должна обладать комплексом высоких механических свойств, то есть быть достаточно прочной и пластичной в условиях самых разнообразных внешних нагрузок – статических, динамических, циклических, растягивающих, скручивающих. Кроме того, конструкционная сталь должна иметь высокие технологические свойства, то есть хорошо отливаться, обрабатываться давлением, резанием, хорошо свариваться, так как из нее изготавливают изделия сложной формы. Конструкционная сталь употребляется в очень больших количествах, поэтому желательно, чтобы она была дешевой как по составу (не содержала дорогих и дефицитных элементов), так и по затратам на производство.
По степени раскисления сталь изготавливается как кипящая, полуспокойная и спокойная, что отражается в конце наименования марки стали дополнительными индексами: кп (кипящая – раскисленная марганцем), пс (полуспокойная – раскисленная марганцем и алюминием) и сп (спокойная – раскисленная марганцем, кремнием и алюминием). Кипящую сталь сразу разливают из ковша в изложницы, она содержит значительное количество растворенных газов. Спокойная сталь − это сталь, выдержанная некоторое время в ковшах вместе с раскислителями (кремний, марганец, алюминий), которые соединяясь с растворенным кислородом, превращаются в оксиды и выплывают на поверхность массы стали. Такая сталь имеет лучший состав и более однородную структуру, но дороже кипящей на 10-15 %. Полуспокойная сталь занимает промежуточное положение между спокойной и кипящей. Каждый из этих видов металла имеет достоинства и недостатки. Выбор технологии раскисления и разливки стали определяется ее назначением и технико-экономическими показателями производства.
|
|
В зависимости от качества углеродистую конструкционную сталь делят на два вида: сталь обыкновенного качества и качественную.
В зависимости от назначения и гарантируемых характеристик металла при его поставке углеродистую сталь обыкновенного качества делят на три группы: А, Б и В.
|
|
Сталь группы А определяется ее механическими свойствами. Она используется для изготовления изделий, не подвергающихся горячей обработке (ковке, сварке и термической обработке). Хотя химический состав стали и указывается в сертификате, но отклонение в нем от норм браковочным признаком не является. Гарантируемыми характеристиками механических свойств стали группы А являются: временное сопротивление – максимальная нагрузка, которую выдерживает сталь на 1 мм2 сечения и относительное удлинение – отношение удлинения образца при его растяжении до разрыва к первоначальной длине, определяемые при испытании на растяжение (в %).
Сталь группы Б предназначена для горячей обработки, поэтому для нее гарантируемой характеристикой является химический состав. В стандарте нормируется минимальное и максимальное содержание углерода (используется при установлении режимов термической обработки – закалки, отпуска и т.д.), марганца и кремния, а также максимально допустимое содержание вредных примесей серы и фосфора. Номер стали отражает содержание в ней углерода: чем больше углерода, тем выше номер.
В стали группы В гарантируются как механические свойства, так и химический со-став (содержание углерода, серы и фосфора).
|
|
В обозначение марки сталей обыкновенного качества по ГОСТу 380–94 входит: вид группы (Б или В, А опускается), затем слово «Ст.», номер группы и степень раскисления – кп, пс и сп. Например, сталь БСт.3кп, БСт.3пс, Ст.3сп.
Сталь обыкновенного качества предназначается для изготовления строительных конструкций, арматуры, крепежа, деталей машин, не несущих повышенных нагрузок.
Качественная сталь превосходит сталь обыкновенного качества по однородности, является более чистой по сере и фосфору, неметаллическим включениям и имеет более узкие пределы содержания углерода. Из этой стали делают ответственные детали машин и механизмов, поковки, штамповки, калиброванные прутки, серебрянку – светлые круглые прутки точных размеров со специальной отделкой поверхности.
Кипящие стали имеют небольшую прочность и высокую пластичность. Их, в основном, прокатывают в тонкий лист, из которого методом холодной штамповки получают детали глубокой вытяжки, например, сталь 08кп применяют для штамповки кузовов автомобилей.
В обозначение марки качественных сталей входит слово сталь, затем – содержание углерода в сотых долях процента и степень раскисления. Например, сталь 45сп содержит 0,45% углерода, спокойная. Углеродистая качественная сталь выпускается горячекатаной и кованой (ГОСТ 1050–88).
Инструментальная углеродистая сталь предназначена для изготовления всякого рода инструментов: режущих – резцов, фрез, сверл, метчиков и т. д.; измерительных – микрометров, шаблонов, штангенциркулей и т.д. Инструментальная сталь должна обладать высокой твердостью (значительно более высокой, чем обрабатываемая сталь), высокой износоустойчивостью для сохранения при резании размеров и формы режущей кромки, а также достаточной прочностью и пластичностью, чтобы избежать поломки инструмента в процессе работы.
Инструментальная углеродистая сталь маркируется буквой У (углеродистая) и цифрой, указывающей содержание углерода в десятых долях процента, например, сталь У8 содержит углерода 0,8%. Если после цифры никаких букв нет, то это сталь качественная, если стоит буква А, то высококачественная, и если Г – то с повышенным содержанием марганца. Высококачественная сталь отличается меньшим содержанием вредных примесей.
Промышленность выпускает семь марок качественной инструментальной стали – от У7 до У13, столько же и с таким же содержанием углерода высококачественных (от У7А до У13А) и две марки с повышенным содержанием марганца (У8Г и У8ГА).
Легированной сталью называют сталь, в состав которой кроме углерода введены одна или несколько специальных добавок (легирующих элементов) в количестве, заметно изменяющем структуру стали, ее свойства и условия термической обработки. Легирующие добавки повышают прочность, коррозийную стойкость стали, снижают опасность хрупкого разрушения.
Кроме железа, углерода и легирующих элементов всякая легированная сталь содержит обыкновенные примеси (кремний, марганец, серу и фосфор), скрытые примеси (кислород, азот, водород) и различные случайные примеси. Наиболее часто применяемыми легирующими элементами являются марганец – повышает твердость, износостойкость, обозначается в марке буквой Г, хром – повышает коррозионные свойства, при свыше 10% хрома сталь становится нержавеющей, обозначается буквой Х, никель – придает коррозионную стойкость, жаростойкость жаропрочность обозначается буквой Н, а также кремний (С), вольфрам (В), молибден (М), кобальт (К), ванадий (Ф), титан (Т), алюминий (Ю) и ряд других металлов. В наименовании обычно указываются только основные входящие в состав стали легирующие элементы без указания их количества. Например, марганцовистая, хромоникелевая, хромомолибденовая и т. д.
Конструкционную легированную сталь применяют в строительстве и машиностроении. В качестве легирующих добавок она может содержать кремний, марганец, небольшие количества хрома и никеля. Она подразделяется на низколегированную с суммарным содержанием легирующих элементов в пределах 3–4% (наиболее часто применяют в строительстве) и высоколегированную сталь с содержанием добавок 6–8%.
В марке конструкционной легированной стали первая однозначная или двузначная цифра указывает содержание углерода в стали в десятых (однозначная цифра) или сотых (двузначная цифра) долях процента. Буквы, следующие за первой цифрой, указывают наименование легирующих элементов, входящих в состав стали данной марки. Цифры, стоящие после каждой из букв, указывают содержание соответствующего легирующего элемента в целых процентах. Отсутствие цифры говорит о том, что содержание соответствующего элемента в стали менее 1,5%. Пример: легированная сталь 15Н2М содержит 0,15% углерода, менее 2% никеля, менее 1,5% молибдена.
В процессе резания металлов, особенно – скоростного, инструмент сильно нагревается, твердость резко снижается, и он теряют режущие свойства. Поэтому для изготовления режущих инструментов применяются инструментальные легированные стали, легированные вольфрамом, хромом, молибденом и ванадием, которые придают стали красностойкость, то есть способность сохранять твердость и прочность при температуре красного каления.
Для инструментальной легированной стали порядок маркировки по легирующим компонентам тот же, что и для конструкционных сталей, но содержание углерода указывается первой цифрой в десятых долях процента. Если цифра отсутствует, то сталь содержит около 1% углерода. Например, хромо-молибденовая сталь 1Х12М содержит 1% углерода, 12% хрома, 0,4-0,6% молибдена.
Легированная сталь с особыми свойствами - эта группа легированной стали специального назначения, которая отличается по составу и по свойствам. Как правило, это высоколегированные стали, содержащие более 8–10% специальных добавок. К ним, в частности, относятся:
- жаропрочные стали – стали, которые сохраняют прочность при работе в условиях высоких температур в течение длительного времени. К ним относятся стали для изготовления лопаток турбин, корпусов котлов и др. деталей энергетических установок;
- коррозионностойкие (нержавеющие) стали – стали этой группы обладают высокой коррозионной стойкостью не только на воздухе, но и в различных более агрессивных средах, например, в пресной и морской воде, в различных кислотах и щелочах. Наиболее часто встречаются нержавеющие стали марок 3Х13 и 4Х13, из которых изготавливают измерительный и хирургический инструменты, предметы домашнего обихода.
Некоторые группы сталей специального назначения имеют особую маркировку из букв, которые ставятся впереди цифр: А – автоматная (применяется для последующей обработки на станках-автоматах), Ш – шарикоподшипниковая (для изготовления шариковых и роликовых подшипников1), Р – быстрорежущая (для изготовления резцов, выдерживающих высокие температуры и применяемых при скоростном резании металлов), Е – магнитотвердая (для изготовления магнитов), Э – электротехническая (для изготовления сердечников трансформаторов), Св– сварочная (для изготовления сварочных электродов) и др. В этом случае в буквенной части марки не указываются или указываются не все легирующие элементы, например, сталь Р18, используемая для изготовления режущих инструментов, содержит вольфрам, хром и ванадий, но в марке стали это не отражено. Химический состав таких сталей можно определить только по ГОСТу или по Техническим условиям.
По способу производства (кислородный конвертер, мартеновская печь, электрическая дуговая печь) сталь называется кислородно-конвертерной, мартеновской или электросталью.
Исходными материалами для производства стали служат: передельный чугун, металлолом, отходы металлургического производства, при этом в промышленно развитых странах использование металлолома носит более приоритетный характер, чем чугуна, так как это приносит меньше экологических убытков, дает более дешевую продукцию и возможность получения сразу легированных сталей.
Задача плавки состоит в удалении углерода и примесей – фосфора, серы, кремния и др. Процесс плавки состоит из трех этапов:
1. В расплавленной шихте под воздействием вдуваемого кислорода или кислорода добавляемой руды окисляются и всплывают в виде шлака примеси.
2. Углерод окисляется кислородом и удаляется с поверхности, при этом сталь как бы кипит.
3. Так как при продувании часть кислорода соединилась с железом, производится ее раскисление путем ввода ферромарганца, ферросилиция и ферроалюминия. Раскисленная сталь при разливке не кипит и обозначается при маркировке как сп, нераскисленная сталь после застывания содержит пузырьки газа и называется кипящей (кп), промежуточная – полуспокойная (пс).
Основными способами получения стали являются мартеновский, кислородно-конвертерный и электротермический с постепенным уменьшением доли мартена. Также существует схема прямого восстановления железа из руд, при которой сталь производится из руды, минуя стадию получения чугуна.
В кислородных конвертерах выплавляется большая часть стали. Сущность кислородно-конвертерного способа плавки стали состоит в том, что через расплавленный и залитый в конвертер чугун продувается технически чистый кислород, который вступает в реакцию с углеродом чугуна и примесями, переводит их в шлак и отходящие газы.
Мартеновская печь представляет собой пламенную печь, в которой над плавильным пространством достигается необходимая температура за счет сгорания газа, предварительно нагретого в регенераторах-теплообменниках. Газ и обогащенный кислородом воздух проходят через регенераторы – массивные конструкции из огнеупорного кирпича и по каналам поступают в плавильное пространство печи. Здесь газ и воздух смешиваются и сгорают, образуя пламя высокой температуры. Продукты сгорания поступают во вторую пару регенераторов нагревают их и выходят в дымовую трубу. Затем клапаны переключаются, кислород и газ направляются через нагретые регенераторы, нагреваются и поступают в плавильное пространство. По мере охлаждения регенераторов направление газа и воздуха снова меняют на обратное, и процесс повторяется.
Недостаток мартеновского способа получения стали состоит в том, что, во-первых, он требует затрат на энергоресурсы, во-вторых, их сжигание загрязняет атмосферу, в-третьих, производительность его ниже, чем в конвертерах. Поэтому в Японии, Англии, Германии мартены заменены конвертерами, в России проведены работы по их модернизации, однако проблема их замены еще остается
Еще одним способом получения стали является плавка стали в электропечах. Плавка стали происходит в печах, нагреваемых под воздействием электрического тока. Печи подразделяются на электродуговые, где плавка происходит за счет электрической дуги, возникающей между шихтой и графитовыми электродами, и индукционные, где плавка осуществляется нагревом шихты за счет индукции вихревых токов. Преимущества этого способа: быстрый нагрев, контролируемость процесса, возможность создания вакуума или установленной определенной газовой среды. Получают сталь высокого качества и заданного состава, так как исключаются примеси. В настоящее время этот способ широко применяют для выплавки высококачественных углеродистых и легированных сталей, а также ферросплавов.
2.6. Металлообработка. Производство стальных труб
и металлоизделий
Металлообработка − процесс работы с металлами по созданию отдельных частей, сборочных узлов или больших структур (металлоконструкций), который охватывает широкий диапазон различных действий: от построения больших кораблей и мостов, до изготовления мельчайших деталей и ювелирных изделий. Поэтому термин включает в себя широкий диапазон процессов, используемых инструментов и оборудования.
Металлообработка − технологический процесс, при котором изменяется форма и размеры металла, деталям придается желаемая форма при помощи одного из нескольких методов обработки металла. Технологическую основу машиностроительного производства составляют различные виды обработки металлов и других конструкционных материалов:
- литье;
- обработка металла давлением (прокатка, прессование, волочение);
- ковка, штамповка;
- обработка резанием;
- сварка.
Литейным производством называется процесс получения фасонных отливок путем заполнения жидким металлом изготовленных для этой цели форм, где залитый металл затвердевает. Методом литья в зависимости от применяемой технологии можно получить законченные изделия или заготовки, которые затем подвергают механической обработке. Отливки можно изготавливать из чугуна и стали, меди и алюминия, медных, алюминиевых и других сплавов цветных и черных металлов. Литьем можно получить детали массой от нескольких граммов (например, детали приборов) до сотен тонн (например, станины крупных станков) с толщиной стенки от 0,5 до 500 мм и более самой сложной конфигурации.
В общем машиностроении литье (по массе) занимает более 60% производства всех деталей машин. Литьем получают как многие металлоемкие, сложные по форме, но малоответственные изделия вроде батарей отопления, так и весьма ответственные детали, какими являются автомобильные блоки цилиндров, поршни, турбинные лопатки, колеса, всевозможные станины, лопасти гидротурбин и другие изделия.
Литейное производство широко используется в авиастроении, судостроении, приборостроении, радиоэлектронике, ракетостроении и атомной энергетике - при изготовлении отливок из тугоплавких сплавов. Большой спрос на литье наблюдается в химическом машиностроении, где широко используются трудно обрабатываемые жаропрочные и коррозионностойкие сплавы. Наибольшее количество литья - около 70 % от массы всех отливок - производят из серого чугуна, далее идет стальное литье (около 20 %), литье из ковкого чугуна (около 8 %), из медных, алюминиевых, титановых и цинковых сплавов.
Современное литейное производство использует около 50 различных технологий, при этом наиболее часто применяемыми являются следующие виды литья: в песчано-глинистые формы, в металлические формы (кокиль), под давлением, по выплавляемым моделям, в оболочковые формы, центробежное литье, электрошлаковое литье, а также литье под низким давлением, вакуумным всасыванием, выжиманием, жидкой штамповкой. Формы для заливки металлом применяются разовые (для одной заливки с последующим разрушением) и многоразовые.
Продукцией сталеплавильного производства являются слитки массой от 0,05 до 400 т. Многогранные слитки поступают на машиностроительные заводы, где служат заготовками для ковки крупных поковок (валы турбин, крупные кольца), квадратные слитки – для прокатки и ковки, прямоугольные – для прокатки листов, круглые – для прокатки бесшовных труб. Слитки сечением 80х80 мм и более служат заготовками при ковке, штамповке и прокатке.
Прокатке подвергается около 75% выплавленной стали. Прокаткой называется обработка металлов давлением путем обжатия слитка или заготовки между вращающимися валками прокатного стана для уменьшения их сечения и придания им заданной формы. Прокаткой получают изделия с постоянным по длине сечением (прутки, арматуру, трубы, балки, фасонный профиль, листы и т.д.) или с периодически изменяющейся по длине формой. Прокатка – завершающая часть полного металлургического производства.
Прокатка осуществляется на прокатных станах. Прокатываемый слиток увлекается силой трения, возникающей между валками и слитком, при этом валки обжимают слиток и при прокручивании придают его поперечному сечению соответствующую форму – профиль. Прокатка подразделяется на горячую – с предварительным нагревом металла – и холодную. Валки подразделяются на листовые – для получения листов, и сортовые – для получения фасонного металлопроката – рельсов, балок и т. д.
Первичную прокатку делают на мощных станах – блюмингах для последующего проката заготовок в сортовой прокат и слябингах – для последующего получения листа. Соответственно, заготовки называются блюмы (сечением от 150 ×150 до 450 ×450) и слябы (толстые плиты толщиной до 350 мм). Станы для прокатки готовых изделий подразделяются на сортовые (для получения сортового проката), листопрокатные, рельсобалочные, трубопрокатные и специального назначения.
Форма поперечного сечения проката называется профилем. Совокупность форм и размеров профилей называется сортаментом. Сортамент разделяется на 4 группы: сортовой, листовой, трубы и специальные виды проката. Сортовой прокат делят на профили простой геометрической формы – квадрат, шестигранник, круг, прямоугольник и фасонные – швеллер, тавр, двутавр, угловой прокат и др., а также профили специального назначения для различных отраслей промышленности. Внешний вид некоторых профилей представлен на рисунке 5.
Рис.5. Виды сортового проката
Трубы подразделяются на сварные и бесшовные (цельнотянутые).
Бесшовные трубы значительно дороже сварных, отличаются большей точностью, лучшей поверхностью и могут обтачиваться. Высокая стоимость бесшовных труб обусловлено сложностью их изготовления, использованию дорогостоящего оборудования и большой его энергоемкостью. Благодаря уникальным техническим характеристикам и эксплуатационным свойствам наиболее популярна труба цельнотянутая бесшовная. Отсутствие каких бы то ни было швов в них гарантирует стойкость к химическим, механическим воздействиям и исключает протечку таких труб. В результате получается монолитное изделие, которое отличается однородной структурой, а значит имеет значительные преимущества перед другими видами труб.
Цельность изделия обеспечивает его надежность, высокие антикоррозионные свойства, устойчивость к высокому давлению. Цельнотянутые трубы чаще всего покрывают цинком, что дает возможность не применять дополнительные меры антикоррозионной защиты. Оцинкованные трубы не требуют нанесения грунтовки или краски, за исключением мест резьбовых соединений, где поврежден верхний оцинкованный слой. Во избежание аварий на стыках труб цельнотянутые трубы подлежат соединению с помощью фитингов или муфт, которые также должны быть выполнены из одинакового с трубами металла.
Длина цельнотянутых труб может составлять от 1,5 м до 10 м. Поскольку подобные трубы имеют широкое распространение и применяются в различных отраслях промышленности, то часто производятся не только из стали, но и из различных сплавов, а также из цветных металлов. Высокие прочностные характеристики, отличающие бесшовные трубы, сделали их незаменимыми в трубопроводах, где жидкие среды отличаются агрессивностью, подаются под высоким давлением или имеют высокие температуры (например, пар). Это позволяет использовать цельнотянутые трубы в любых магистральных трубопроводах, начиная от коммунальной сферы. Абсолютно ровная внутренняя поверхность таких труб является идеальной для подачи питьевой воды. Поскольку трубопровод из бесшовных труб прекрасно переносит высокие температуры и скачки давления, а также химически устойчив, то он оптимален для использования в системах отопления и горячего водоснабжения. Прочность и надежность муфтовых соединений гарантирует безопасность использования таких труб для монтажа потенциально взрывоопасных трубопроводов, по которым транспортируется газ, нефть, другие углеводороды. Например, на нефтеперерабатывающих предприятиях все внутренние трубопроводы сделаны из бесшовных труб.
Еще одна ниша для использования бесшовных труб – энергетика и атомная промышленность, тракторостроение и авиационная промышленность, угольные шахты и буровые вышки. Благодаря отсутствию швов этот вид проката используется в оборонной промышленности, судостроении, вагоностроении и тяжелой промышленности. Высокая степень износостойкости обеспечила применение бесшовных труб в тех сферах, где присутствуют наиболее сложные условия эксплуатации металла.
Труба цельнотянутая бесшовная является разновидностью труб бесшовных, в производстве которых применяют одну из особых технологий работы с горячим металлом, позволяющую достичь максимальных показателей прочности. Методом вытягивания из массы горячего металла формируют заготовку для трубы, после чего она становится пригодной к процессу калибровки. Также бесшовный прокат возможно получить на специальных прокатных станах (получение отверстия методом прошивки). Существует принципиально иной способ – высверливание отверстия в цилиндрических заготовках.
Сварные трубы, диаметр которых достигает 2500 мм, значительно дешевле бесшовных, но менее прочны, имеют худшую поверхность и не могут обтачиваться. Заготовкой для сварных труб служат лента или листы шириной, равной длине окружности трубы. Технологический процесс изготовления сварных труб состоит из следующих операций: формовка плоской заготовки в трубу, сварка трубы, отделка и правка.
2.7. Особенности организации и управления производством
на предприятиях цветной металлургии
Цветная металлургия включает добычу, обогащение руд цветных металлов и выплавку цветных металлов и их сплавов.
Цветные металлы и их сплавы применяются в значительно меньших объемах и реже, чем черные металлы. По физическим и химическим свойствам применяемые в промышленности металлы можно подразделить на следующие группы:
- легкие – алюминий, магний, титан и другие;
- тяжелые – медь, никель, кобальт, свинец, олово, цинк, ртуть и другие;
- тугоплавкие – вольфрам, молибден и другие;
- легкоплавкие - цинк, олово, свинец и другие;
- благородные (драгоценные) – золото, серебро, платина и платиноиды (рутений, родий, палладий осмий, иридий).
Основная масса цветных металлов используется в виде сплавов, так как они обладают более широким спектром физических, механических и химических свойств. Название сплавов цветных металлов в большинстве случаев соответствует их основе. Так, сплавы на основе меди называют медными, на основе алюминия – алюминиевыми и т. д.
Иногда в название сплава входит основной и главный легирующий элемент: медно-никелевые, оловянно-свинцовые и др. При маркировке цветных металлов и их сплавов обозначение отдельных элементов отличается от принятых в марках легированных сталей. В большинстве случаев – это первая буква русского названия элемента, а для элементов, названия которых имеют одинаковую начальную букву, добавляется еще одна буква: алюминий (А), железо (Ж), кремний (К), медь (М), магний (Мг), марганец (Мц), никель (Н), олово (О), свинец (С), титан (Т), фосфор (Ф), хром (X), цинк (Ц). Буквы, соответствующие элементам, входящим в состав марки сплава, располагаются в убывающем порядке, и после каждой из них ставится цифра, указывающая количество этого элемента в целых процентах. Если цифра отсутствует, то это значит, что содержание этого элемента находится в пределах одного процента.
Из всех цветных металлов медь нашла наиболее раннее применение. Ее сплавы, называемые бронзами, были известны человечеству с доисторических времен, когда они были единственным металлом, из которого изготовлялись оружие и орудия труда (бронзовый век). Медь имеет красновато-розовый цвет, химически мало активна, обладает высокой коррозионной стойкостью в атмосферных условиях и в парах воды. Характерными физическими свойствами меди являются ее высокие тепло- и электропроводность. По электропроводности медь занимает первое место среди других технических металлов. Медь – очень пластичный металл, но имеет невысокую механическую прочность. Основная часть меди идет на приготовление сплавов и легирование других металлов. Значительная часть меди идет на изготовление электропроводов и используется в электроэнергетике, в радиоэлектронике и приборостроении, однако, большая часть меди в настоящее время поступает на экспорт в виде рафинированной, т.е. чистой меди.
Обладая замечательными свойствами, медь, в то же время, как конструкционный материал не удовлетворяет требованиям машиностроения, поэтому ее легируют, т.е. вводят в ее состав такие металлы, как цинк, олово, алюминий, никель и др., за счет чего улучшаются ее механические и технологические свойства. Наиболее широко используются латуни, бронзы и медно-никелевые сплавы.
Латунями называются сплавы меди с цинком. Различают двухкомпонентные латуни и специальные, в которые дополнительно введены другие легирующие элементы. Цинк повышает прочность и пластичность меди, но в определенных пределах содержания цинка. Максимальной пластичностью обладает латунь, содержащая 40% цинка. По сравнению с медью латуни обладают большей прочностью, коррозионной стойкостью и упругостью. Они обрабатываются литьем, давлением и резанием. По технологическому назначению их подразделяют на обрабатываемые давлением и литейные.
Основная масса латуни идет на изготовление катанного полуфабриката: полос, труб, проволоки и различных профилей. Латунь обрабатывается в холодном состоянии. Она дешевле меди. В обозначении марок латуней принята буквенно-цифровая система: первая буква «Л» – означает «латунь», затем – перечень символов, входящих в сплав компонентов, затем – их процентное содержание. Первая цифра указывает на содержание меди, остальные – на содержание других легирующих элементов. Содержание цинка в обозначении марки не указывается – для того чтобы его определить, необходимо от 100% вычесть процентное содержание меди и других химических элементов, входящих в данную латунь. Например, томпак Л90 – это латунь, содержащая 90% меди, остальное – цинк; латунь алюминиевая ЛА77-2 содержит 77% меди, 2% алюминия, остальное – цинк; латунь ЛАНКМц75-2-2,5-0,5-0,5 содержит 75% меди, 2% алюминия, 2,5% никеля, 0,5% кремния, 0,5% марганца, остальное – цинк.
Бронзы (название произошло от королевства Бурунди, откуда в древности поставлялась медь в Европу) – сплав меди с оловом, алюминием, бериллием, кремнием, свинцом, хромом и с другими элементами. Как и латуни, бронзы подразделяются на литейные и деформируемые. Марка бронзы состоит из букв «Бр.», после них – символы компонентов, затем их процентное содержание. Например, Бр. А7 – бронза с содержанием алюминия 7% (старые монеты), Бр.ОЦС4–4–2 содержит 4, 4 и 2% олова, цинка и свинца.
Бронзы подразделяются на оловянистые – на основе олова и безоловянистые – сплавы с другими металлами. Некоторые типы бронз хорошо обрабатываются давлением и резанием. Бронзы применяются при изготовлении антифрикционных деталей (вкладышей подшипников скольжения), арматуры, работающей в пресной воде, жидком топливе и паре при температурах до 250°С; используются в химической и пищевой промышленности. Оловянистые бронзы хорошо льются и применяются в художественном литье.
Медно-никелевые сплавы маркируются буквой М, затем – по легирующим элементам аналогично бронзам. Например, мельхиор МНЖМц 30–08–1 содержит 30% никеля, 0,8% железа, 1% марганца. Он имеет высокую коррозионную стойкость, применяется для теплообменных аппаратов, работающих в морской воде, и для украшений. Константан МНМц40–1,5 – имеет большое электрическое сопротивление и применяется в виде проволоки и лент в реостатах, электроизмерительных приборах. Монель-металл НМЖМц29–2,5–1,5 – сплав на основе меди с высоким содержанием никеля, отличается высокой коррозионной стойкостью в агрессивных средах, широко применяется в судостроении, электротехнике и других отраслях промышленности.
Медные руды представляют собой различные сернистые соединения. Наряду с медью они содержат никель, цинк, свинец, золото, серебро и другие металлы. Медь из руды получают преимущественно пирометаллургическим (с применением высоких температур) способом. Технологическая система получения меди состоит из следующих процессов:
- обогащение руды методом флотации, основанном на различной смачиваемости соединений меди и пустой породы. Размельченная руда помещается в суспензию с флотационным агентом, например, пихтовым маслом, который создает пленку на поверхности рудных частичек. При продувке воздухом образуемые пленкой пузырьки собираются на поверхности руды и увлекают ее наверх в виде пены. Пустая порода, которая не смачивается маслом, опускается на дно. Собранная и высушенная пена – концентрат содержит до 30% меди;
- концентрат обжигается, в результате получается сернистый газ, который идет на получение серной кислоты, и обожженный медный концентрат. Обожженный концентрат переплавляется в отражательных печах с получением медного штейна – продукта, состоящего из меди и сульфидов железа;
- штейн продувается в конвертерах кислородом с получением черновой меди, содержащей 1,5% примесей. При продувке в присутствии кварцевого песка сульфиды железа переходят в окись железа и уходят в шлак, а получающийся сернистый газ также идет на приготовление серной кислоты;
- очистка (рафинирование) черновой меди осуществляется огневым или электролитическим методом. При огневом методе в расплав меди кладутся деревянные (осиновые) жерди и пропускается воздух. Кислород воздуха в присутствии жердей окисляет и выводит примеси. При электролитическом методе черновая медь устанавливается в качестве анода, катодом служат медные листы. При пропускании тока анод растворяется, и медь оседает на катоде – на дне. За 10 дней получается лист меди весом 60-90 кг. При этом примеси осаждаются на дно ванны в виде шлама. Иногда в шламе содержится до 35% серебра, 6% селена, 1% золота. Поэтому шламы обычно перерабатывают для получения этих элементов.
Производство меди сопряжено с высокими затратами энергии и экологически вредно.
Процесс производства меди представлен на рисунке 6.
Алюминий сравнительно молодой металл. Название его происходит от латинского слова alumen – так 500 лет до н.э. называли алюминиевые квасцы, которые использовались для протравливания при крашении тканей и дубления кож. Алюминий как элемент был открыт в 1825 г., когда были получены первые небольшие комочки этого металла. Начало его промышленного освоения относится к концу XIX столетия – после открытия технологии его получения путем электролиза глинозема, растворенного в расплавленном криолите. Этот принцип лежит и в основе современного промышленного извлечения алюминия из глинозема во всех странах мира.
Рис.6. Технологический процесс производства меди
Алюминий представляет собой серебристо-белый пластичный металл. В воздушной среде он быстро покрывается окисной пленкой, которая защищает его от коррозии. Алюминий химически стоек против азотной и органических кислот, но разрушается щелочами, а также соляной и серной кислотами.
Важнейшее свойство алюминия – небольшая плотность, он в три раза легче железа. Механические свойства алюминия невысоки: сопротивление на разрыв – 5–9 кгс/мм2, относительное удлинение – 25–45%. Высокая пластичность (достигается отжигом при температурах 350–410°С) этого металла позволяет прокатывать его в очень тонкие листы, например, фольга может иметь толщину до 0,005 мм. Алюминий хорошо сваривается, однако трудно обрабатывается резанием. Для повышения прочности в алюминий вводят кремний, марганец, медь и другие компоненты.
Значительные природные запасы алюминия, его небольшая плотность, высокие антикоррозионные свойства и хорошая электропроводность способствовали широкому распространению этого металла в различных отраслях техники. Алюминий и его сплавы применяются в самолето- и машиностроении, при строительстве зданий и линий электропередач, во многих отраслях промышленности. Из него изготовляют различные емкости и арматуру для химической промышленности, в пищевой промышленности применяется упаковочная фольга из алюминия и его сплавов (для обертки кондитерских и молочных изделий). Широкое признание получила алюминиевая посуда. Алюминий хорошо подвергается различным тонким покрытиям и окраске, поэтому его используют и как декоративный материал. Алюминий всех марок содержит более 99% чистого алюминия.
В зависимости от химического состава он подразделяется на алюминий особой, высокой и технической чистоты, обозначается буквой А и цифрой, показывающей десятые и сотые доли процента после 99%, например, А85 – содержит 99,85% алюминия.
Так как прочность алюминия очень незначительна, то в качестве конструкционных материалов применяют алюминиевые сплавы. Сплавы подразделяются на деформируемые – в основном, дюралюминий и литейные – главным образом силумин. Дюралюминий, дюраль (от нем. Düren – город, где впервые было начато промышленное производство сплава) – сплав алюминия с медью (2,2–5,2%), магнием (2–2,7%) и марганцем (0,2–1,0%). Его подвергают закалке в воде после нагрева до температуры около 500 °С и упрочняющему старению. По своим механическим свойствам он приближается к среднеуглеродистым сталям. Применяется, главным образом, в виде различного проката – листы, уголок, трубы и т.д. Как конструкционный материал он используется для транспортного и авиационного машиностроения.
Силумин – сплав алюминия и кремния, обладает хорошими литейными свойствами, мягкий, применяется для изготовления неответственных деталей методом литья и давления. Кроме алюминия (основа) и кремния (10–13%) в этот сплав входят: железо – 0,2–0,7%, марганец – 0,05–0,5%, кальций – 0,07– 0,2%, титан – 0,05–0,2%, медь – 0,03% и цинк – 0,08%. Могут использоваться также сплавы алюминия с цинком, магнием и т.д.
Производство алюминия – сложный технологический процесс. В свободном виде алюминий, вследствие своей активности, не встречается. Его получают из минералов – бокситов, нефелинов и алунитов, при этом сначала производят глинозем, а затем из глинозема путем электролиза получают алюминий. Технологическая схема производства алюминия состоит из процессов:
- получение глинозема Al2O3 путем выщелачивания концентрированным раствором щелочи измельченного боксита и его последующего прокаливания;
- растворение глинозема в расплаве криолита (Na3AlF6) и его электролиз в ванне с угольным анодом и покрытым угольными блоками катодом. Катионы алюминия нейтрализуются на катоде и выпадают в расплав. На производство 1 т алюминия уходит 17–18 тыс. кВт электроэнергии;
- электролитическое рафинирование, аналогичное рафинированию меди, где анодом являются алюминиевые блоки.
Сдерживающим фактором увеличения выпуска алюминия можно считать недостаток освоенных месторождений алюминиевых руд и получения высококачественных концентра-тов. Успешное развитие отрасли можно объяснить двумя факторами – своевременной переориентацией отрасли на внешний рынок и сложившимся дешевым относительно мировых цен уровнем стоимости электроэнергии. На экспорт поступает, в основном, первичный, не прошедший обработку алюминий.
Титан – серебристо-белый металл. Его коррозийная стойкость выше нержавеющей стали за счет оксидной пленки (аналогично алюминию). Абсолютно стоек в морской воде и атмосферных условиях, во многих кислотах, но реагирует с плавиковой кислотой. Легкий металл, тугоплавкий, высоко пластичен, хорошо обрабатывается давлением, плохо резанием, обладает высокой прочностью.
Сочетание высокой механической прочности, немагнитности и коррозионной стойкости при достаточной технологичности делают титан и его сплавы весьма ценными для применения в ряде областей техники и медицины. Например, в авиационной промышленности из них изготовляют обшивки самолетов и многие детали компрессоров; в судостроении – обшивку судна, теплообменники, гребные винты; в химическом и нефтяном машиностроении – резервуары, фильтры, теплообменники, трубопроводы. Большое значение титановые сплавы приобретают в космическом аппаратостроении, судо- и кораблестроении, в энергетическом машиностроении. Из них изготовляют лопатки турбин низкого давления, лопатки компрессоров, бандажные кольца, крепежные и другие изделия.
Нашли они также применение и в медицине для изготовления скрепляющих пластин и гвоздей при переломах костей, изготовления хирургических инструментов и аппаратуры современной медицины. В последние годы титан широко стал применяться для изготовления бытовой техники и инструмента, однако широкое применение титана в ряде областей ограничивается его высокой стоимостью. Титан впервые был открыт в 1791 г., в чистом виде выделен в 1925 г., а первый промышленный металл получен только в 1948 г.
По распространенности в земной коре титан среди металлов занимает четвертое место после алюминия, железа и магния, т. е. в природе его больше, чем таких давно и широко применяемых металлов, как медь, свинец, олово, цинк, никель, серебро, золото и платина, вместе взятых. Широкая распространенность в земной коре и прекрасное сочетание физических и химических свойств делают титан одним из лучших металлов настоящего и будущего.
Основными промышленными рудами, из которых получают титан, являются рутил (TiO2) и ильменит (FeTiO2), содержащий 53% TiO2 и 47% FeO. Технология получения титана очень сложная и экологически вредная.
К титану и его сплавам применимы все виды механической обработки: точение, сверление, фрезерование, шлифование, полирование. Однако, для этого требуются специальный инструмент и разработка наиболее рациональных режимов резания.
Никель – серебристо-белый металл с голубоватым оттенком, легко поддается полировке до зеркального блеска, коррозийно-стойкий, обладает высокими механическими свойствами, относительно дорогой металл. В чистом виде никель применяют главным образом для антикоррозионных и декоративных покрытий, основная масса используется для производства сплавов. Является одним из главных продуктов цветной металлургии, составляющих экспорт.
К легкоплавким металлам относятся металлы, температура плавления которых ниже температуры плавления цинка – 419º С. К промышленно используемым легкоплавким металлам относятся: цинк, свинец, олово, сурьма, кадмий и ртуть.
Цинк – металл светло-серо-голубоватого цвета, хрупкий при комнатной температуре, при нагревании до 100–150°С становится пластичным. Больше половины цинка идет на покрытие сталей с получением кровельного (оцинкованного) железа, так как цинк, аналогично алюминию, благодаря оксидной пленке, обладает антикоррозионными свойствами и способностью покрывать сталь плотным, хорошо прилегающим слоем. Значительная часть цинка идет на производство латуни.
Свинец отличается высокой плотностью, пластичен, температура плавления 327ºС, обладает аналогичными алюминию оксидными свойствами, поэтому широко используется для защиты от коррозии в виде пластин, труб и т.д., так как нанести его тонким слоем очень трудно. Свинец используется также при приготовлении припоев для пайки металлов, для защиты от рентгеновского излучения, для изготовления типографских шрифтов, в аккумуляторах, в подшипниках скольжения, как этилсвинец добавляется в бензин для повышения детонационных свойств или октанового числа и т.д. Свинец токсичен и биологически вреден для организма человека, накапливается и не вымывается из организма, приводит к тяжелым отравлениям.
Олово – наиболее легкоплавкий из применяемых металлов, температура плавления 232ºС. По коррозийной стойкости приближается к благородным металлам, легко покрывает металлы тонким слоем, нетоксичен, широко применяется в пищевой промышленности для изготовления белой жести (консервные банки), для производства бронзы, входит в состав припоев.
Ртуть – жидкий при комнатной температуре металл, температура плавления -38,9ºС), пары очень токсичны, растворяет другие металлы, включая золото, с получением ртутной амальгамы, используется в медицине, приборостроении, электронике и электротехнике.
Продукция порошковой металлургии нашла применение во всех отраслях промышленности, особенно, в автомобилестроении, энергомашиностроении, в радиотехнической промышленности и т. д. Технология порошковой металлургии позволяет получать изделия как из одного металла, например, железа (такие изделия называют однокомпонентными), так и из смеси порошков металлов или металлов с неметаллами (многокомпонентные изделия), причем в самых различных сочетаниях.
По этой технологии можно получить сплавы (точнее, псевдосплавы) из металлов, которые не образуют растворов, не смешиваются в жидком состоянии (железо – свинец, вольфрам – медь и др.), а также из металлов с неметаллами (медь – графит, алюминий – оксид алюминия, карбид и др.), из некоторых оксидов металлов (Fe2O3 и MnO, Fe2O3). Из порошковых материалов изготовляют и такие изделия, которые технологически могут быть получены и с помощью других методов – отливкой, штамповкой или обработкой резанием, однако порошковая металлургия дает большую экономию металла (коэффициент использования металла достигает 0,9) и значительное снижение себестоимости деталей. Например, при изготовлении некоторых деталей методами литья с последующей механической обработкой отходы металла составляют до 40%, а при получении такой детали методами порошковой металлургии отходы металла могут составлять 2–5%. Однако изготовление деталей методами порошковой металлургии экономически оправданно только при массовом производстве вследствие высокой стоимости пресс-форм.
Технология изготовления порошковых материалов и изделий состоит из операций, таких как: получение металлических порошков восстановлением из окислов и других со-единений или измельчение исходного материала в мельницах; составление смеси заданного состава (приготовление шихты), очистка порошков от примесей, классификация по размеру частиц, смешивание; холодное прессование смеси порошков в стальных пресс-формах на механических или гидравлических прессах при давлении 0,1–1 гПа; спекание полученных спрессованных заготовок или изделий в защитной атмосфере или в вакууме при температуре несколько ниже температуры плавления материала или его наиболее легкоплавкого компонента для придания им необходимых физико-механических свойств.
Материалы, получаемые порошковой металлургией, подразделяются на конструкционные порошковые материалы общего назначения, заменяющие обычные углеродистые и легированные стали, чугуны и цветные металлы, и материалы, обладающие специальными свойствами: высокой износостойкостью, жаропрочностью, твердостью, коррозионной стойкостью, особыми магнитными и электрическими характеристиками.
Конструкционные детали, изготовленные по технологии порошковой металлургии, являются наиболее распространенным видом ее продукции. Так как при их получении практически полностью отсутствуют отходы, то они имеют минимальную стоимость и трудоемкость. Изделия, полученные порошковой металлургией, отличаются от литых или обработанных давлением металлов и сплавов того же состава отсутствием усадочных раковин, трещин, полосчатой структуры и др. дефектов. Порошковые конструкционные материалы применяют для изготовления деталей машин и приборов, в том числе из них изготавливают шестерни, кулачки, поршневые кольца, диски, втулки и др. детали. При этом сокращается объем механической обработки, снижается трудоемкость, повышается коэффициент использования металла.
Методом порошковой металлургии получают детали из железоуглеродистых сплавов, в том числе коррозионностойких, из порошков алюминия, магния, бериллия, меди, никеля, бронз, латуней, титана, хрома и др. металлов и сплавов. Порошковые металлокерамические твердые сплавы применяют в виде пластинок к режущему инструменту и инструменту для буров при бурении горных пород. Некоторые мелкие режущие инструменты (сверла, развертки, фрезы) изготовляют целиком из твердых сплавов.
Металлокерамические твердые сплавы отличаются высокой твердостью (82–92 HRA) и способны сохранять режущую способность до температур 1000–1100°С. Основной составляющей таких сплавов являются карбиды вольфрама, титана, тантала. В качестве связующего применяют кобальт. Порошковые антифрикционные материалы применяют для изготовления подшипников скольжения наряду с литыми сплавами типа баббитов, бронз и т.д. Их получают из порошков как черных, так и цветных металлов.
К благородным металлам относят золото, серебро, платину и металлы платиновой группы – палладий, рутений, осмий, родий, иридий. Металлы имеют красивый внешний вид, стойки против окисления и воздействия кислот, обладают высокой температурой плавления, хорошо обрабатываются давлением, являются редкими. За все существование человечества добыто около 100 тыс. т золота. В отличие от других металлов, благородные металлы, в основном, находятся в самородном, т.е. металлическом состоянии. Под самородком не следует понимать чистый металл – как правило, это сплавы. Например, самородное золото может содержать до 40% серебра.
Область применения благородных металлов специфична. Раньше их использовали исключительно для изготовления украшений и как валюту, в настоящее время все большую часть потребляет техника, особенно – микроэлектроника. В США и Японии среднее потребление золота на технические нужды составляет 80–90 т в год. В ювелирных сплавах содержание золота, платины, серебра характеризуется пробой, в технических сплавах – маркой сплава. В мире существует 4 системы проб: тысячная, золотниковая, каратная и унциевая. Они отличаются тем, что принято за 100%. В России стандартной принята тысячная проба, которая характеризует содержание золота в сплаве с точностью до десятых долей процента. Тысячная проба показывает количество грамм благородного металла, содержащееся в 1000 г. сплава. Например, 583 проба содержит 58,3% золота, остальная часть сплава называется лигатурой, состав элементов которой не регламентируется. Для ювелирных изделий в России установлены: для золота – 375, 500, 583, 750, 958 пробы, для серебра – 750, 800, 916, 925, 960 пробы. В каратной пробе за 100% принято 24 карата, 1 карат равен 0,2 г. Каратная проба применяется для измерения массы камней.
Золото – металл ярко желтого цвета, с ярким металлическим блеском, в 3,5 раза тяжелее железа, не растворимо в кислотах и щелочах, растворимо в царской водке (смесь соляной и азотной кислоты), растворимо в ртути и цианистых солях. Очень пластично – раскатывается в прозрачную фольгу толщиной 10-4 мм зеленоватого цвета. По электропроводности занимает третье место. Широко используется в технических целях, особенно – для золочения контактов, работающих в микроэлектронике. Это объясняется тем, что поверхность медных контактов окисляется и межконтактное соединение может нарушиться.
Серебро – блестящий белый металл, прекрасно поддается полировке, занимает первое место среди металлов по тепло- и электропроводности, растворяется серной и азотной кислотой, реагирует с сероводородом, пластичен и малопрочен, раскатывается в прозрачную с голубоватым оттенком фольгу до 25*10-5 мм.
Примерно 25% серебра добывается из руд, 75% – как сопутствующий металл при добыче меди, свинца и т.д. Значительное количество серебра (до 60%) идет на экспорт. Из сплавов серебра находят применение серебряные припои, используемые для пайки цветных металлов и обозначаемые «ПСр.» и цифрой, показывающей содержание серебра в %, например, ПСр. 28 содержит 28% серебра. Серебро широко применяется в радиопромышленности, при изготовлении зеркал и т.д.
К металлам платиновой группы (МПГ), или платиноидам, относятся: платина, палладий, родий, иридий, рутений и осмий. Их использование говорит о высоком уровне развития промышленности. Эти металлы нашли применение именно в современных производствах, так как они обладают исключительно полезными свойствами, которых нет у других металлов и материалов. К таким свойствам относятся: высокая электропроводность, пластичность, отражательная способность, теплопроводность, малая химическая активность, стойкость к коррозии, нетоксичность, уникальные каталитические свойства, а также способность сохранять все это в широком диапазоне температур, давления и состава агрессивных сред.
Родий и иридий нерастворимы в царской водке. В ювелирной промышленности платину применяют для ограновки бриллиантов, так как она имеет одинаковое с бриллиантами тепловое расширение и придает им лучший блеск. Широко применяется в химической промышленности, в медицине, радиопромышленности, из платины и иридия изготовлены эталоны веса и длины. В электротехнике и электронике они используются для производства изделий исключительно высокой надежности. Для изготовления надежных коммутационных соединений (разъемов, штекеров) применяется сплав палладия и серебра. В составе сопротивлений высокой надежности (резисторов) используют платину и рутений, в конденсаторах на керамической основе – платину и палладий, в конденсаторах на танталовой основе – платину. В виде покрытий жестких дисков компьютеров применяют сплав платины и кобальта – для увеличения плотности записей. В качестве катализаторов платиноиды используются в химической и нефтехимической промышленности. В нефтехимии наибольшее распространение получили платино-рениевые катализаторы, с помощью которых из нефти производится более 5 тыс. видов синтетических продуктов.
Палладий используют в катализе для получения мономеров синтетического каучука, полупродуктов для производства синтетических волокон, моющих средств. Платиноиды применяются также в качестве катализаторов неорганических соединений, особенно аммиака и азотной кислоты. Металлы платиновой группы широко применяются и в других отраслях – в приборостроении, атомной промышленности, медицине (в основном, в стоматологии). Основная область применения палладия – производство каталитических фильтров-нейтрализаторов для автомобильной промышленности. Достаточно большие объемы палладия используются в электронике и медицине. Доля остальных отраслей в использовании палладия невелика. Родий почти полностью потребляется автомобильной промышленностью в производстве каталитических фильтров-нейтрализаторов выхлопных газов. В частности, родий добавляют в некоторые палладиевые каталитические системы для нейтрализации оксидов азота в выхлопных газах. Основная область применения рутения и иридия – электроника.
Металлы платиновой группы относятся к числу редких, содержание их в земной коре очень невелико. Добыча обходится дорого, и на мировом рынке цена их выше цены золота. Поэтому длительное время потребление МПГ было незначительным. Стимулом для быстрого роста потребления платиноидов в промышленности стало внедрение в индустриально развитых странах в 80–90-е годы XX столетия пятого технологического уклада. Широкое развитие в этот период электронной промышленности, производства телекоммуникационного и лазерного оборудования, роботостроения потребовало применения новых металлов и сплавов, и платиноиды оказались практически незаменимыми. Введение в 70-х годах в Японии, а в 80-х годах – в США, строгих норм содержания вредных веществ в выхлопных газах автомобилей привело к оснащению продаваемых в этих странах автомобилей платиновыми и палладиевыми каталитическими фильтрами-нейтрализаторами.
2.8. Особенности производственной деятельности
в машиностроении. Сборочное производство
Машиностроение занимает ведущее положение среди других отраслей экономики. Это обусловлено тем, что основные производственные процессы во всех отраслях промышленности, строительства и сельском хозяйстве выполняют разнообразные машины механизмы. Поэтому первостепенная роль в техническом перевооружении производства, повышения технического уровня, улучшения качественных показателей всех сфер экономики принадлежит машиностроению. Машиностроение повышает производительность труда и расширяет ассортимент выпускаемой продукции. От степени совершенства деталей машин зависит качество машины в целом, что, в свою очередь, определяет конкурентоспособность продукции.
Производственный процесс изготовления машин представляет собой совокупность технологических и экономических процессов, в результате которых исходные материалы и полуфабрикаты преобразуются в заготовки с последующей обработкой с целью получения готовых изделий – деталей машин. Из сборочных единиц и деталей машин путем сборки получают конечную продукцию машиностроения – средства производства.
Производственный процесс на предприятиях машиностроения осуществляется в специализированных цехах:
- литейных;
- кузнечно-прессовых;
- сварочных;
- обрабатывающих;
- сборочных и др.
Структура машиностроительного предприятия представлена на рисунке 7.
Рис.7. Структура машиностроительного предприятия
Процесс изготовления машин на машиностроительном предприятии подразделяются на основное, вспомогательное и обслуживающее производство.
Основное производство включает технологические процессы преобразования исходных материалов, полуфабрикатов и комплектующих в готовую продукцию – средства производства. Данные процессы основаны, как правило, на механических, тепловых и химических воздействиях на предмет труда. Это процессы получения заготовок методами литья, обработки металлов давлением, сварки резки, механической и термической обработки деталей машин, сборки машин, их отделки, окраски, нанесения покрытия и т.д.
Вспомогательное производство обеспечивает нормальное функционирование основного производства. Это изготовление различных видов технологической оснастки, приспособлений, режущего, штампового и измерительного инструментов, ремонт оборудования, энергетическая и другие службы машиностроительного предприятия.
Обслуживающее производство включает в себя внутризаводское транспортирование материалов, полуфабрикатов, деталей, складские операции, технический контроль.
В свою очередь, основное производство в машиностроении состоит из трех основных этапов:
- заготовительного;
- обрабатывающего;
- сборочного.
Заготовительное производство в машиностроении включает технологические процессы преобразования исходных материалов в заготовки деталей машин. Основными технологическими процессами заготовительного производства в машиностроении являются обработка металлов давлением, литье, сварка. В результате осуществления технологических процессов заготовительного производства из исходного сырья получают заготовки деталей машин.
Обрабатывающее производство главным образом включает в себя технологические процессы обработки металлов резанием, термическую и химико-термическую обработку деталей машин, а также специальную обработку и нанесение защитных покрытий (гальваническое производство). В результате осуществления технологических процессов обрабатывающего производства из заготовок получают готовые детали машин с требуемой формой, точностью размеров и другими характеристиками.
Сборочное производство является заключительным этапом изготовления машин. Технологический процесс сборки связан с образованием разъемных и неразъемных соединений составных частей машин. Из готовых деталей собираются узлы, из которых по заранее определенной схеме получают готовое изделие – машину.
В сборочном производстве различают две организационные формы сборки: стационарную, при которой готовое изделие полностью собирают на одном месте, к которому последовательно подаются все детали, узлы и сборочные единицы, и подвижную, когда собираемое изделие последовательно перемещается по рабочим местам, на каждом из которых выполняется определенная сборочная операция. Подвижную сборку осуществляют с помощью конвейера и используют преимущественно в массовом производстве.
Базовыми элементами сборочного производства являются детали, узлы, сборочные единицы, комплексы, комплекты.
Деталь – часть машины, изготовленная из однородного по наименованию и марке материала без применения сборочных операций. Детали могут быть простыми (гайка, пружина) или сложными (коленчатый вал, станина станка). Детали объединяются в узлы.
Узел представляет собой законченную сборочную единицу, состоящую из ряда деталей, соединенных между собой сборочными операциями и имеющих общее функциональное назначение (подшипник качения, редуктор). Признаком узла является обособленность его сборки от сборки других элементов машины.
Сборочная единица представляет собой сложный узел, который может включать несколько простых узлов. Например, редуктор состоит из подшипников, валов с насаженными на них зубчатыми колесами.
Комплекс – два и более изделия, не соединенных сборочными операциями, но представляющих собой единую техническую систему, предназначенную для выполнения взаимосвязанных эксплуатационных функций (например, компьютер с периферийными устройствами).
Комплект – набор изделий, имеющих общее эксплуатационное назначение вспомогательного характера (набор инструментов).
Особенности сборочного производства связаны с большим объемом вспомогательных работ, удельный вес которых в массовом производстве может достигать 20%.
При сборке основным видом работ является осуществление различных соединений и сопряжений деталей. Использование данных операций позволяет получать разъемные и неразъемные, подвижные и неподвижные соединения и сопряжения двух или нескольких деталей иди узлов.
К разъемным соединениям относят такие, которые могут быть полностью разобраны без повреждения составляющих их частей и крепежных деталей. К разъемным соединениям относят резьбовые (могут осуществляться с применением крепежных деталей: винтов, гаек, либо выполнением резьбы на соединяемых деталях), штифтовые, шпоночные и шлицевые. Остальные соединения относят к неразъемным.
В первую группу неразъемных соединений входят соединения с гарантированным натягом, получаемым без дополнительных средств крепления (например, прессованием). Такие соединения используются, как правило, при сборке готовых деталей. Ко второй группе относят соединения, осуществляемые с помощью сварки, пайки, клепки и склеивания.
Сварка – технологический процесс образования неразъемного соединения деталей машин, конструкций и сооружений путем их местного сплавления или совместного деформирования, в результате чего возникают прочные связи между атомами соединяемых тел. Наиболее часто получают методом сварки заготовки сложной конфигурации и крупногабаритные, состоящие из нескольких частей. Применение сварных заготовок обеспечивает значительную экономию металла, уменьшение массы заготовок (например, по сравнению с литьем), а также снижение трудоемкости изготовления. Сварные соединения обеспечивают большую прочность и надежность по сравнению с другими видами соединений.
Выделяют следующие виды сварки: термическая (электродуговая и газовая), механическая (сварка давлением) и термомеханическая (комбинированная). Электродуговая и газовая сварка являются одними из наиболее распространенных технологических процессов в машиностроении.
Пайка – процесс соединения заготовок, выполненных из металлов и неметаллических материалов, находящихся в твердом состоянии, посредством расплавленного присадочного материала, называемого припоем. Температура плавления припоя должна быть ниже температуры плавления основного материала. Пайка не вызывает значительного коробления и окисления поверхностей соединяемых заготовок. Пайку применяют для сборки изделий и сборочных единиц. Паять можно заготовки из углеродистой или легированной стали всех марок, твердых сплавов, чугунов, редких металлов и их сплавов. Преимуществами пайки являются достаточная прочность и чистота соединения, отсутствие оплавления металла, сохранение форма и размеров изделия, возможность механизации и автоматизации процесса.
Клепка – процесс создания неразъемного соединения с помощью заклепок – стержней круглого сечения, устанавливаемых в совмещенные отверстия соединяемых деталей. В настоящее время клепка применяется ограниченно, только в авиа- и судостроении, а также в крупных металлоконструкциях. Это связано с тем, что несмотря на прочность соединения, недостатком клепки являются низкая технологичность и производительность процесса. В настоящее время при сборке чаще применяют сварку или склеивание.
Машиностроительный комплекс − это совокупность отраслей промышленности, производящих разнообразные машины. Он ведущий среди межотраслевых комплексов. Это обусловлено несколькими причинами. Во-первых, машиностроительный комплекс − крупнейший из промышленных комплексов, на его долю приходится почти 20 % производимой продукции и всех работающих в хозяйстве России. Во-вторых, машиностроение и металлообработка характеризуются более крупными размерами предприятий, чем промышленность в целом (средний размер предприятия в отрасли составляет по численности рабочих около 1700 человек, по сравнению с менее чем 850 по промышленности в целом), большей фондоемкостью, капиталоемкостью и трудоемкостью продукции; конструктивно-технологическая сложность продукции машиностроения требует разнообразной по профессиям и квалифицированной рабочей силы. Отрасли машиностроения представлены на рисунке 8.
Рис.8. Отрасли машиностроения
Заводы тяжелого машиностроения отличаются большим потреблением металла и обеспечивают машинами и оборудованием предприятия металлургического, топливно-энергетического, горнодобывающего и горно-химического комплексов. Для него характерны как предприятия, выпускающие детали и узлы или предприятия, специализированные на выпуске отдельных видов оборудования (паровые котлы или турбины для электростанций, горно-шахтное оборудование, экскаваторы), так и универсальные, выпускающие в серийном или индивидуальном исполнении разные виды оборудования.
В состав отрасли входят следующие 10 подотраслей: металлургическое машиностроение, горное, подъемно-транспортное машиностроение, тепловозостроение и путевое машиностроение, вагоностроение, дизелестроение, котлостроение, турбостроение, атомное машиностроение, полиграфическое машиностроение. Около 90 % производства отрасли сосредоточено в европейской части, остальное − в Западной Сибири и на Дальнем Востоке.
Производство металлургического оборудования, занимающее первое место в отрасли по стоимости продукции, расположено, как правило, в районах крупного производства стали и проката. На предприятиях Урала выпускается оборудование для агломерационных фабрик, доменные и электроплавильные печи, а также оборудование для прокатного и дробильно-размольного производства.
Профиль заводов горного машиностроения − машины для разведки, а также открытого и закрытого способов добычи, дробления и обогащения твердых полезных ископаемых на предприятиях черной и цветной металлургии, химической, угольной, промышленности и промышленности строительных материалов, транспортного строительства. Они, как правило, расположены в районах потребления − на Урале и в Сибири и др.
Тепловозостроение, вагоностроение и путевое машиностроение обеспечивает железнодорожный транспорт магистральными грузовыми, пассажирскими и маневровыми тепловозами, грузовыми и пассажирскими вагонами и т.д.
Турбостроительные заводы выпускают оборудование для тепловых, атомных, гидравлических и газотурбинных электростанций, газоперекачивающее оборудование для магистральных газопроводов, компрессорное, нагнетательное и утилизационное оборудование для химической и нефтеперерабатывающей промышленности, черной и цветной металлургии.
Электротехническая промышленность выпускает изделия более 100 тысяч наименований продукции, потребителем которой является практически вся экономика. По объему производства она значительно превосходит в совокупности все подотрасли тяжелого машиностроения. Для производства электротехнической продукции требуется широкий набор технических средств и материалов, производимых различными промышленными комплексами. В настоящее время основными регионами электротехнического машиностроения являются Центральный, Северо-западный и Западно-Сибирский районы.
Станкоинструментальная промышленность включает производство металлорежущих станков, кузнечнопрессового оборудования, деревообрабатывающего оборудования, металлообрабатывающего инструмента, централизованный ремонт металлообрабатывающего оборудования. Заводы станкоинструментальной промышленности размещены в основных машиностроительных районах. Средний размер предприятий сравнительно невелик.
Продукция приборостроения отличается небольшой материало- и энергоемкостью, но для ее производства требуются высококвалифицированная рабочая сила и научно-исследовательские кадры. Поэтому основная часть производственного потенциала сосредоточена в крупных городах. Например, в Москве и Московской области размещены десятки научно-производственных и производственных объединений, специализирующихся на выпуске, монтаже и наладке средств автоматизации, разработке программного обеспечения, конструировании и производстве часов, медицинских приборов, измерительной аппаратуры, оргтехники.
В машиностроение для легкой и пищевой промышленности входят следующие подотрасли: производство оборудования для текстильной, трикотажной, швейной, обувной, кожевенной, меховой промышленности, а также для производства химических волокон и оборудование для пищевой промышленности.
В авиационной и ракетно-космической промышленности кооперируются предприятия практически всех отраслей промышленного производства, поставляющие разнообразные материалы и оборудование. Предприятия отличаются высоким уровнем квалификации инженерно-технического и рабочего персонала, что обусловило возникновение и развитие данных отраслей промышленности в крупных промышленных центрах.
Автомобильная промышленность по объему производства, а также по стоимости основных фондов является крупнейшей отраслью машиностроения. Продукция автомобилестроения широко используется во всех отраслях экономики и является одним из самых ходовых товаров в розничной торговле. Свыше 80 % перевозимых грузов приходится на автомобильный транспорт.
2.9. Особенности организации и управления производством
на предприятиях химической промышленности. Производство серной кислоты
Химическая промышленность производит продукцию, используя химические методы переработки сырья и материалов В ее отраслевой структуре выделяют две большие группы отраслей: основная (неорганическая) химия и промышленность органического синтеза.
Химическая промышленность характеризуется чрезвычайно широкой сырьевой базой. Она использует нерудное минеральное сырье из земных недр (фосфориты, апатиты, сера), топливные минеральные ресурсы (нефть, природный газ, уголь, сланцы), отходы черной и цветной металлургии, лесной, пищевой и легкой промышленности. Используя сырье из других отраслей, химическая промышленность комбинируется и кооперируется с ними. Для нее характерна и концентрация производства, осуществляемая путем объединения предприятий или увеличения мощностей технологических линий.
Отрасли химической промышленности в целом относятся к материалоемким. Поэтому основными факторами размещения предприятий химической промышленности является сырьевой, топливно-энергетический, потребительский, водный, экологический.
Группу основной химии образует:
- горно-химическая промышленность, занимающаяся добычей химического сырья;
- собственно, основная химия, которая производит минеральные удобрения (азотные, калийные, фосфатные), серную кислоту, соду.
В группе отраслей промышленности органического синтеза входят:
- химия органического синтеза (производство органических полуфабрикатов - этилена, ацетилена, бензола, этилового спирта, уксусной кислоты и др.);
- производство полимеров (синтетических смол, каучука, пластмасс, химических волокон);
- переработка полимеров (производство изделий из пластмасс, шин, резинотехнических изделий).
Кроме основных крупных групп, выделяют группу других отраслей химической промышленности:
- лакокрасочная;
- фотохимическая промышленность;
- производство химреактивов и др.
Основная химия специализируется на производстве кальцинированной и каустической соды, минеральных удобрений, серной кислоты.
Серная кислота применяется:
- в разнообразных производствах химической промышленности: минеральных удобрений, пластмасс, красителей, искусственных волокон, минеральных кислот, моющих средств;
- в нефтяной и нефтехимической промышленности: для очистки нефти, получения парафинов;
- в цветной металлургии: для получения цветных металлов - цинка, меди, никеля и др.
- в черной металлургии: для травления металлов;
- в целлюлозно-бумажной, пищевой и легкой промышленности (для получения крахмала, патоки, отбеливания тканей) и т.д.
Серную кислоту в промышленности производят двумя способами: контактным и нитрозным. Серную кислоту контактным способом производят в больших количествах на сернокислотных заводах. В настоящее время основным методом производства серной кислоты является контактный, т.к. этот метод имеет преимущества перед другими:
- получение продукта в виде чистой концентрированной кислоты, приемлемой для всех потребителей;
- уменьшение выбросов вредных веществ в атмосферу с выхлопными газами.
Сырьем для производства серной кислоты является сера (S), серный колчедан (пирит FeS2), сульфиды цветных металлов (Cu2S, ZnS, PbS), сероводород (H2S).
Для получения серной кислоты используют, в основном, флотационный колчедан - отход производства при обогащении медных руд, содержащих смеси сернистых соединений меди и железа. Возможно использование серы, которая также образуется при обогащении руд цветных металлов, добываемых на рудниках.
Измельчённый очищенный влажный (после флотации) пирит сверху засыпают в печь для обжига в «кипящем слое». Снизу пропускают воздух, обогащённый кислородом, для более полного обжига пирита. Температура в печи для обжига достигает 800°С. Пирит раскаляется до красна и находится в «подвешенном состоянии» из-за продуваемого снизу воздуха. Поэтому процесс обжига происходит очень быстро, за несколько секунд. За счёт выделяющейся теплоты в результате реакции поддерживается температура в печи. Избыточное количество теплоты отводят: по периметру печи проходят трубы с водой, которая нагревается. Горячую воду используют дальше для центрального отопления рядом стоящих помещений.
Из печи выходит печной газ, состав которого: SO2, O2, пары воды и мельчайшие частицы огарка (оксида железа). Такой печной газ необходимо очистить от примесей твёрдых частиц огарка и паров воды. Для удаления мелких частиц смесь направляется в электрофильтры, для удаления паров воды в печном газе (осушка печного газа) используют серную концентрированную кислоту, которая является очень хорошим осушителем, поскольку поглощает воду. Осушку печного газа проводят в сушильной башне. На выходе из сушильной башни печной газ уже не содержит ни частичек огарка, ни паров воды. Печной газ теперь представляет собой смесь оксида серы SO2 и кислорода О2.
Затем происходит каталитическое окисление SO2 в SO3 кислородом в контактном аппарате. И третьей, заключительной стадией, является поглощение SO3 серной кислотой в поглотительной башне. Оксид серы очень хорошо растворяется в такой кислоте, образуя олеум: H2SO4·nSO3. Образовавшийся олеум сливают в металлические резервуары и отправляют на склад. Затем олеумом заполняют цистерны, формируют железнодорожные составы и отправляют потребителю.
Дата добавления: 2018-02-28; просмотров: 892; Мы поможем в написании вашей работы! |
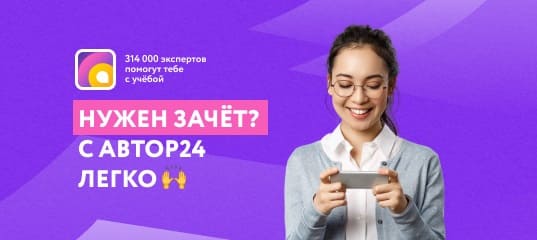
Мы поможем в написании ваших работ!