Раздел Режимы резания при точении
Раздел Инструментальные материалы
Вопрос 1
Условие работы режущих инструментов и требования к инструментальным материалам.
Ответ:
Режущие инструменты работают при очень напряженных термомеханических нагрузках, их поверхности находятся в контакте с чистыми, только что образовавшимися поверхностями стружки и детали. Зачастую контакт инструмента со стружкой и обрабатываемой деталью осуществляется в течение достаточно длительного периода, поэтому режущее лезвие инструмента в окрестности режущей кромки и участков контакта инструмента со стружкой и обрабатываемой деталью прогревается достаточно равномерно до высоких температур.
Из-за очень больших скоростей деформации в процессе резания прочностные характеристики и твердость стружки существенно возрастают в сравнении с исходными свойствами обрабатываемого материала, измеренными в статических условиях нагружения. Прочность и твердость инструментального материала под влиянием температуры резко уменьшаются. При резании, например, чистое железо, мягкое в условиях статического нагружения, способно вызвать напряжения, достаточные для деформации и срезания быстрорежущей стали, имеющей в аналогичных условиях нагружения значительно более высокие механические характеристики. В связи с этим к режущим инструментальным материалам предъявляется целый ряд повышенных требований.
|
|
Для того, чтобы иметь возможность резать обрабатываемый материал и противостоять абразивному изнашиванию, режущий инструментальный материал должен иметь высокую твердость. Чтобы противостоять пластическим деформациям и разрушению, режущий инструментальный материал должен обладать высокими пределами прочности на сжатие и на изгиб.
Режущий инструментальный материал должен сопротивляться разрушению при знакопеременном нагружении, то есть иметь высокий предел выносливости. Он должен выдерживать ударные нагрузки, то есть иметь высокую ударную вязкость, а также сопротивляться возникновению и росту трещин, удалению собственных частиц при контактном взаимодействии с обрабатываемым материалом, то есть быть износостойким. Опыт показывает, что для повышения износостойкости кристаллохимические свойства инструментального материала должны отличаться от соответствующих свойств обрабатываемого материала.
Твердость и прочностные характеристики режущих инструментальных материалов должны сохраняться при повышенных температурах. Это свойство инструментального материала обычно называют теплостойкостью. Кроме того, в условиях прерывистого или нестационарного резания режущий инструментальный материал должен быть малочувствительным к циклическим температурным изменениям.
|
|
Желательно, чтобы режущий инструментальный материал обладал достаточно высокой теплопроводностью, так как это препятствует возникновению локальных термических напряжений на контактных площадках инструмента и способствует снижению температуры.
Вопрос 2
Характеристика инструментальных углеродистых сталей, легированных сталей.
Ответ:
Инструментальные углеродистые стали по содержанию углерода и твердости подразделяются на низкоуглеродистые, содержащие углерод до 0,25%; среднеуглеродистые - от 0,25% до 0,6% и высокоуглеродистые - от 0,6 до 2%.
Углеродистые инструментальные стали в соответствии с ГОСТ 1435-99 обозначаются следующими марками: У7; У8; У8Г; У9; У10; У11; У12; У13. Буква У указывает, что сталь углеродистая, а следующая за ней цифра - среднее содержание углерода в десятых долях процента. Буква Г в марке показывает повышенное содержание марганца. Углеродистые инструментальные стали бывают качественные и высококачественные.
Высококачественные углеродистые инструментальные стали, выплавляемые в электропечах, маркируются таким же образом, но с добавлением в конце буквы А, то есть У7А, У8А и так далее. Буква А обозначает, что сталь является высококачественной (улучшенной), по составу более чистой, с пониженным содержанием серы (до 0,03%), фосфора (также до 0,03%), остаточных примесей и неметаллических включений. Содержание марганца в этих сталях колеблется в пределах от 0,15 до 0,40%; кремния от 0,15 до 0,35%.
|
|
Достоинством инструментальных углеродистых сталей является их хорошая обрабатываемость, невысокая твердость (160-180 НВ). Однако они имеют и крупные недостатки: небольшой интервал закалочных температур, необходимость быстрого охлаждения в воде при закалке, что приводит к короблению, деформации инструментов и даже образованию трещин.
Инструментальная углеродистая сталь применяется для изготовления различных инструментов (режущих, мерительных и других), которые должны обладать высокой износоустойчивостью и красностойкостью.
Легирующие элементы, вводимые в инструментальные стали, увеличивают теплостойкость (вольфрам, молибден, кобальт, хром), закаливаемость (марганец), вязкость (никель), износостойкость (вольфрам).
В сравнении с углеродистыми легированные инструментальные стали имеют следующие преимущества: хорошую прокаливаемость; большую пластичность в отожженном состоянии, значительную прочность в закаленном состоянии (см. гл. V), более высокие режущие свойства.
|
|
Низколегированные инструментальные стали содержат д о 2,5% легирующих элементов, имеют высокую твердость (HRC 62-69), значительную износостойкость, но малую теплостойкость (200-260°С). В отличие от углеродистых сталей их используют для изготовления инструмента более сложной формы.
В низколегированных сталях X, 9ХС, ХВГ, ХВСГ основной легирующий элемент - хром. Сталь X легирована только хромом. Повышенное содержание хрома значительно увеличивает ее прокаливаемость. Сталь X прокаливается в масле полностью в сечении до 25 мм, а сталь У10 - только в сечении до 5 мм. Применяют сталь X для изготовления токарных, строгальных и долбежных резцов. Сталь 9ХС кроме хрома легирована кремнием. По сравнению со сталью X она имеет большую прокаливаемость – до 35 мм; повышенную теплостойкость - до 250-260°С (сталь X до 200-210°С) и лучшие режущие свойства. Из стали 9ХС изготовляют сверла, развертки, фрезы, метчики, плашки.
Сталь ХВГ легирована хромом, вольфрамом и марганцем; имеет прокаливаемость на глубину до 45 мм. Сталь ХВГ используют для производства крупных и длинных протяжек, длинных метчиков, длинных разверток и тому подобное.
Сталь ХВСГ - сложнолегированная сталь и по сравнению со сталями 9ХС и ХВГ лучше закаливается и прокаливается. При охлаждении в масле она прокаливается полностью в сечении до 80 мм. Она меньше чувствительна к перегреву. Теплостойкость ее такая же, как у стали 9ХС. Сталь ХВСГ применяют для изготовления круглых плашек, разверток, крупных протяжек и другого режущего инструмента.
Высоколегированные инструментальные стали содержат вольфрам, хром и ванадий в большом количестве (до 18% основного легирующего элемента); имеют высокую теплостойкость (600-640°С). Их используют для изготовления высокопроизводительного режущего инструмента, предназначенного для обработки высокопрочных сталей и других труднообрабатываемых материалов. Такие стали называют инструментальными быстрорежущими (ГОСТ 19265-73). Быстрорежущие стали обозначают буквой Р, цифра после которой указывает содержание вольфрама. Содержание хрома (4%) и ванадия (2%) в марках быстрорежущих сталей не указывают. В некоторые быстрорежущие стали дополнительно вводят молибден, кобальт и большое количество ванадия. Марки таких сталей содержат соответственно буквы М, К, Ф и цифры, указывающие их количество. Наиболее распространены Р18, Р9. Р10К5Ф5 и другие быстрорежущие стали.
Вопрос 3
Характеристика быстрорежущих сталей.
Ответ:
Быстрорежущую сталь относят к группе инструментальных сталей, т. е. сталей, используемых для изготовления разнообразного инструмента. Эти стали должны отличаться высокой твердостью, прочностью и износостойкостью, а в некоторых случаях должны удовлетворять и ряду дополнительных требований, в частности быть стойкими против коррозии, сохранять неизменными размеры и форму инструмента в течение длительного времени, обладать способностью противостоять значительным динамическим нагрузкам.
В готовых изделиях быстрорежущая сталь должна обладать высокой твердостью (HRC 63—66, а для резания труднообрабатываемых изделий — до HRC 66—69), высокой прочностью и сопротивлением пластической деформации, теплостойкостью (красностойкостью), а для ряда инструмента — возможно лучшей вязкостью. Твердость быстрорежущей стали определяет сопротивление пластической деформации и контактным напряжениям, возникающим в рабочей кромке инструмента. С увеличением твердости возрастает износостойкость, увеличивается возможность получения более чистой и ровной поверхности обрабатываемого металла и самого инструмента, уменьшается налипание обрабатываемого металла на поверхность режущего инструмента. Инструменты, для которых характерна недостаточная твердость, не могут быть использованы для резания или деформирования обрабатываемых ими деталей: они быстро теряют форму и размеры под действием возникающих напряжений. Твердость определяется химическим составом и структурой быстрорежущей стали и зависит от содержания углерода в мартенсите (альфа-растворе), количества и дисперсности выделившихся карбидов или интерметаллидов и от количества остаточного аустенита. Быстрорежущие стали относят к ледебуритному классу. Они содержат более 0,6% С и приобретают высокую твердость и износостойкость в результате мартенситного превращения при закалке и дисперсионного твердения при высоком отпуске (560—620° С), вызываемого выделением упрочняющей фазы — в основном карбидов вольфрама, молибдена, ванадия. Твердость быстрорежущй стали является важнейшим, но не единственным свойством, определяющим эксплуатационные характеристики инструмента. До 70% мелких режущих инструментов ломаются преждевременно до наступления нормального износа, что свидетельствует об очень важном значении прочности и вязкости инструментальной стали. Прочность быстрорежущей стали характеризует сопротивление изгибающему или крутящему моменту, а вязкость — сопротивление образованию трещин и разрушению под действием ударных нагрузок. При использовании сталей высокой прочности повышается стойкость инструмента и производительность обработки, становится возможным резание с большей подачей и резание материалов большей прочности. Достаточно высокая вязкость в сочетании с высокой прочностью предупреждает выкрашивание, образование трещин и поломку инструмента.
Часто применяютсябыстрорежущие стали марок Р18,Р6М3. Наиболее массовое употребление получила марка Р6М5.Это высоколегированная инструментальная сталь, обладающая красностойкостью, то есть не теряющая режущих свойств при нагреве до 600-700 °С. Она способна резать металл со скоростями в 3-4 раза выше допустимых для углеродистых и низколегированных инструментальных сталей.
Вопрос 4
Характеристика твердых сплавов.
Ответ:
Твёрдые сплавы – твёрдые и износостойкие металлические материалы, способные сохранять эти свойства при 900-1150°С. В основном изготовляются на основе карбидов вольфрама, титана, тантала, хрома при различном содержании кобальта или никеля.
Различают спечённые и литые твёрдые сплавы. Главной особенностью спеченных твердых сплавов является то, что изделия из них получают методами порошковой металлургии и они поддаются только обработке шлифованием или физико-химическим методам обработки (лазер, ультразвук, травление в кислотах и другими), а литые твердые сплавы предназначены для наплавки на оснащаемый инструмент и проходят не только механическую, но часто и термическую обработку (закалка, отжиг, старение и другие). Порошковые твердые сплавы закрепляются на оснащаемом инструменте методами пайки или механическим закреплением.
Характерной особенностью твердых сплавов является очень высокая твердость 87…92 HRC при достаточно высокой прочности. Твердость и прочность зависят от количества связующей фазы (кобальта) и величины зерен карбидов. Чем крупнее зерна карбидов, тем выше прочность. Твердые сплавы отличаются большой износостойкостью и теплостойкостью. Основными твердыми сплавами являются группы ВК (WC + Co), TK (WC + TiC + Co), TTK (WC + TiC + TaC + Co). Наиболее распространенными сплавами группы ВК являются сплавы марок ВК3, ВК6, ВК8, ВК20, где число показывает содержание кобальта в процентах, остальное – карбиды вольфрама WC. Сплавы группы ТК марок Т30К6, Т14К8 – первое число показывает содержание карбидов титана в процентах, второе – содержание кобальта в процентах. Сплавы этой группы лучше противостоят изнашиванию, обладают большей твердостью, тепло- и жаростойкостью, стойкостью к коррозии, но меньшей теплопроводностью и большей хрупкостью. Используются на средних и высоких скоростях резания.
Износостойкость инструментов из твердых сплавов превышает износостойкость инструментов из быстрорежущих сталей в 10…20 раз и сохраняется до температур 800…1000 °С.
Вопрос 5
Характеристика минералокерамических материалов.
Ответ:
Минералокерамическим называют материал, полученный путем обработки порошкообразных минералов или их смесей с другими веществами и последующего обжига отформованного полуфабриката. Минералокерамические режущие пластины изготавливаются методами порошковой металлургии из исходного сырья дисперсностью 1...2 мкм.
Инструментальная промышленность выпускает минералокерамический инструмент, оснащенный многогранными (трех -, четырех -, пяти -, и шести-гранными) неперетачиваемыми пластинами.
Современная минералокерамика подразделяется на четыре группы:
- оксидная;
- оксидно-карбидная;
- оксидно-нитридная;
- нитридно-кремниевая.
Физико-механические свойства минералокерамики зависят от ее структуры, которая характеризуется формой, размером, плотностью и взаимным расположением зерен. Основной ее недостаток — низкая теплопроводность, что необходимо учитывать при выборе типа крепления пластинок к державкам инструмента и способа обработки.
Минералокерамика имеет ряд положительных качеств. Так, предел прочности на сжатие у нее такой же, как у твердых сплавов, а теплостойкость — на 200…300° С выше, чем у них, и почти вдвое выше, чем у быстрорежущих сталей. Главное же достоинство ее заключается в том, что она сохраняет твердость при высоких температурах, возникающих в зоне резания. Например, при температуре 1000°С твердость минералокерамики составляет HRC 61, а твердого сплава ВК8 — HRC 26. При обработке минералокерамическим инструментом сталей достигается меньшая шероховатость поверхности, так как на нем не образуется нароста.
Рационально используя свойства минералокерамики, можно разработать высокопроизводительный технологический процесс получистовой и чистовой обработки стали, чугуна, цветных металлов-, жаропрочных сплавов.
Инструмент, оснащенный минералокерамикой, позволяет заменить операции шлифования токарной обработкой, причем качество обработанной поверхности не снижается и в большинстве случаев повышает эксплуатационные свойства деталей. Применение минералокерамики позволяет, наряду со значительным снижением трудоемкости, технологическим методом повысить долговечность работы деталей.
Минералокерамическим режущий инструмент получил значительное применение в машиностроительных отраслях промышленности. Данный инструмент также можно широко использовать в практике лезвийной обработки восстановленных напеканием автоматической наплавкой поверхностей деталей машин при выполнении чистовых операций взамен операции шлифования.
Вопрос 6
Характеристика алмазов и сверхтвердых материалов.
Ответ:
Алмазы и алмазные инструменты широко используются при обработке деталей из различных материалов. Для алмазов характерны исключительно высокая твердость и износостойкость. По абсолютной твердости алмаз в 4 - 5 раз тверже твердых сплавов и в десятки и сотни раз превышает износостойкость других инструментальных материалов при обработке цветных сплавов и пластмасс. Кроме того, вследствие высокой теплопроводности алмазы лучше отводят теплоту из зоны резания, что способствует гарантированному получению деталей с бесприжоговой поверхностью. Однако алмазы весьма хрупки, что сильно сужает область их применения.
Для изготовления режущих инструментов основное применение получили искусственные алмазы, которые по своим свойствам близки к естественным. При больших давлениях и температурах в искусственных алмазах удается получить такое же расположение атомов углерода, как и в естественных. Масса одного искусственного алмаза обычно составляет карата (1 карат - 0,2 г). Вследствие малости размеров искусственных кристаллов они непригодны для изготовления таких инструментов, как сверла, резцы и другие, а поэтому применяются при изготовлении порошков для алмазных шлифовальных кругов и притирочных паст.
Лезвийные алмазные инструменты выпускаются на основе поликристаллических материалов типа «карбонадо» или «баллас». Эти инструменты имеют длительные размерные периоды стойкости и обеспечивают высокое качество обработанной поверхности. Применяются они при обработке титановых, высококремнистых алюминиевых сплавов, стеклопластиков и пластмасс, твердых сплавов и других материалов.
Алмаз как инструментальный материал имеет существенный недостаток — при повышенной температуре он вступает в химическую реакцию с железом и теряет работоспособность.
Для того чтобы обрабатывать стали, чугуны и другие материалы на основе железа, были созданы сверхтвердые материалы, химически инертные к нему. Такие материалы получены по технологии, близкой к технологии получения алмазов, но в качестве исходного вещества используется не графит, а нитрид бора.
В сверхтвердых материалах поликристаллы плотных модификаций нитрида бора превосходят по теплостойкости все материалы, применяемые для лезвийного инструмента: алмаз в 1,9 раза, быстрорежущую сталь в 2,3 раза, твердый сплав в 1,7 раза, минералокерамику в 1,2 раза.
Эти материалы изотропны (одинаковая прочность в различных направлениях), обладают микротвердостью меньшей, но близкой к твердости алмаза, повышенной теплостойкостью, высокой теплопроводностью и химической инертностью по отношению к углероду и железу.
Эффективность применения лезвийных инструментов из различных марок сверхтвердых материалов связана с совершенствованием конструкции инструментов и технологии их изготовления и с определением рациональной области их использования.
Наиболее распространенными сверхтвердыми материалами являются:
- композиты 01(эльбор-Р) и 02 (белбор) используют для тонкого и чистового точения и фрезерования без ударов деталей из закаленных сталей твердостью 55...70 НRС, чугунов и твердых сплавов ВК15, ВК20 и ВК25 с подачами до и глубиной резания до 0,8
- композит 05 применяют для чистового и получистового точения без ударов деталей из закаленных сталей твердостью 40...58 HRC, чугунов твердостью до 300 НВ с подачами до и глубиной до 2,5 мм
- композит 10 (гексанит-Р) используют для тонкого, чистового и получистового точения и фрезерования с ударами деталей из закаленных сталей твердостью не выше 58 HRC, чугунов любой твердости, сплавов ВК15, ВК20, ВК25 с подачей до и глубиной резания до 0,6 мм
При этом период стойкости инструментов возрастает в десятки раз по сравнению с другими инструментальными материалами.
Область применения сверхтвердых материалов до недавнего времени ограничивалась из-за сравнительно небольших размеров поликристаллов. В настоящее время освоен выпуск двухслойных неперетачиваемых пластин, состоящих из твердого сплава (основа) и слоя из поликристаллов алмаза или нитрида бора толщиной до 0,5 мм, что повышает общую эффективность использования инструментов из сверхтвердых материалов.
Раздел Токарные резцы
Вопрос 7
Основные части токарного резца.
Ответ:
Резец состоит из двух основных частей: головки и тела (стержня). Головка является рабочей (режущей) частью резца; тело служит для закрепления резца в резцедержателе.
Головка состоит из следующих элементов: передней поверхности, по которой сходит стружка, и задних поверхностей, обращенных к обрабатываемой детали. Одна из задних поверхностей, обращенная к поверхности резания, называется главной; другая, обращенная к обработанной поверхности, — вспомогательной.
Режущие кромки получаются от пересечения передней и задних поверхностей. Различают главную и вспомогательную режущие кромки. Основную работу резания выполняет главная режущая кромка.
Пересечение главной и вспомогательной режущих кромок называется вершиной резца.
Основные части токарного резца показаны на рисунке 1.
Рисунок 1 Основные части токарного резца
Вопрос 8
Характеристика метода точения.
Ответ:
Технологический метод формообразования поверхностей заготовок точением. Характеризуется наличием двух движений: вращательным главным движением заготовки (определяет скорость peзания и поступательным движением режущего инструмента - резца (движение подачи
).
Схема точения приведена на рисунке 2.
Рисунок 2 Схема точения
На вертикальных полуавтоматах и автоматах и токарно-карусельных станках заготовки имеют вертикальную ось вращения, на всех прочих - горизонтальную. Движение подачи осуществляется параллельно, перпендикулярно или под углом к оси вращения заготовки.
На станках токарной группы обрабатывают в основном наружные и внутренние поверхности, имеющие форму тел вращения, а также плоские торцовые поверхности. На специальных и специализированных станках можно обрабатывать и более сложные поверхности, например поверхности, описываемые уравнением спирали Архимеда, циклоиды и так далее, а также плоские многогранники (четырех-, шестигранные плоские поверхности и так далее).
Под термином точение (обтачивание), как правило, понимают обработку наружных поверхностей. Разновидности точения - это растачивание - обработка внутренних поверхностей; подрезание - обработка плоских (торцовых) поверхностей и разрезание - разделение заготовки на части или отрезание готовой детали от ее заготовки - пруткового проката. Точение осуществляется резцами
Вопрос 9
Главные углы резца.
Ответ:
Главными углами резца являются главный задний угол, передний угол, угол заострения, угол резания. Эти углы измеряются в главной секущей плоскости.
Углы резца показаны на рисунке 3.
Рисунок 3 Углы резца
Главная секущая плоскость - это плоскость, перпендикулярная к главной режущей кромке и основной плоскости.
Главным задним углом называется угол между главной задней поверхностью резца и плоскостью резания.
Этот угол обозначается греческой буквой α (альфа).
Углом заострения называется угол между передней и главной задней поверхностями резца.
Этот угол обозначается греческой буквой β (бэта).
Передним углом называется угол между передней поверхностью резца и плоскостью, проведенной через главную режущую кромку перпендикулярно к плоскости резания.
Этот угол обозначается греческой буквой γ (гамма).
Углом резания называется угол между передней поверхностью резца и плоскостью резания.
Этот угол обозначается греческой буквой δ (дельта).
Вопрос 10
Углы резца в плане.
Ответ:
Главным углом в планеφ называется угол между проекцией главной режущей кромки на основную плоскость и направлением подачи; определяется конструктивными особенностями детали, жесткостью системы станок -приспособление - инструмент - деталь (СПИД) и выбирается в пределах от 30 до 90°. С уменьшением угла улучшается качество обрабатываемой поверхности, повышается стойкость резца, однако при недостаточной жесткости системы СПИД уменьшение угла
вызывает вибрацию заготовки и резца, что приводит к ухудшению шероховатости поверхности. В этом случае применяют резцы с главным углом в плане, равным 60, 75 или 90°.
Вспомогательный угол в плане - угол между проекцией вспомогательной режущей кромки и направлением подачи - для резцов различных типов выбирается от 5 до 45°.
Угол при вершине резца в плане - угол между проекциями главной и вспомогательной режущих кромок на основную плоскость.
Углы резца в плане показаны на рисунке 4.
Рисунок 4 Углы резца в плане
Вопрос 11
Угол наклона главной режущей кромки.
Ответ:
Углом наклона главной режущей кромки λ называется угол, заключенный между режущей кромкой и линией, проведенной через вершину резца параллельно основной плоскости.
Угол наклона главной режущей кромки показан на рисунке 5.
Рисунок 5 Угол наклона главной режущей кромки
Этот угол измеряется в плоскости, проходящей через главную режущую кромку перпендикулярно к основной плоскости. Угол наклона главной режущей кромки считается отрицательным, когда вершина резца является наивысшей точкой режущей кромки; равным нулю — при главной режущей кромке, параллельной основной плоскости, и положительным, когда вершина резца является наинизшей точкой режущей кромки. Угол λ делается для изменения направления стружки; он влияет па прочность головки резца и режущей кромки.
Вопрос 12
Классификация токарных резцов.
Ответ:
Резцы классифицируются:
- по направлению подачи – на правые и левые (правые резцы на токарном станке работают при подаче справа налево, т. е. перемещаются к передней бабке станка);
- по конструкции головки – на прямые, отогнутые и оттянутые
- по роду инструментального материала – из быстрорежущей стали, твердого сплава и так далее;
- по способу изготовления – на цельные и составные (при использовании дорогостоящих режущих материалов резцы изготовляют составными: головка – из инструментального материала, а державка – из конструкционной углеродистой стали; наибольшее распространение получили составные резцы с пластинами из твердого сплава, которые припаиваются или крепятся механически);
- по сечению державки – на прямоугольные, круглые и квадратные; по виду обработки - на проходные, подрезные, отрезные, прорезные, расточные, фасонные, резьбонарезные и другие.
Раздел Режимы резания при точении
Вопрос 13
Элементы режимов резания при токарной обработке.
Ответ:
Элементами, характеризующими процесс резания являются: скорость резания, подача и глубина резания.
Скоростью резания при токарной обработке называется величина перемещения в главном движении режущей кромки инструмента относительно обрабатываемой поверхности в единицу времени.
Подачей называется величина перемещения режущей кромки резца за один оборот обрабатываемой детали. Подача обозначается буквой s и измеряется в миллиметрах за один оборот детали.
В зависимости от направления, по которому перемещается резец при точении относительно оси центров станка, различают:
- продольную подачу - вдоль оси центров;
- поперечную подачу - перпендикулярно к оси центров;
- наклонную подачу - под углом к оси центров (при обтачивании конической поверхности).
Глубиной резания называют слой металла, снимаемый за один проход резца. Измеряется глубина резания в миллиметрах.
При токарной обработке глубина резания определяется как полуразность между диаметром заготовки и диаметром обработанной поверхности, полученной после одного прохода резца.
Вопрос 14
Основное (технологическое) время.
Ответ:
Основное (технологическое) время — это время, в течение которого призводится снятие стружки.
Если этот процесс совершается только станком без непосредственного участия рабочего, то это время будет машинно-автоматическим;
Если же процесс снятия стружки совершается станком при непосредственном управлении инструментом или перемещением заготовки рукой рабочего, то это время будет машинно-ручным.
Основное технологическое время для токарной операции определяется отношением пути, пройденного обрабатывающим инструментом, к его минутной подаче:
где – длина пути, пройденного инструментом в направлении подачи
– длина обрабатываемой поверхности, мм;
–длина врезания
– длина перебега инструмента
–дополнительная длина для снятия пробной стружки
– число рабочих ходов;
– частота вращения заготовки
– подача.
Дата добавления: 2018-02-28; просмотров: 647; Мы поможем в написании вашей работы! |
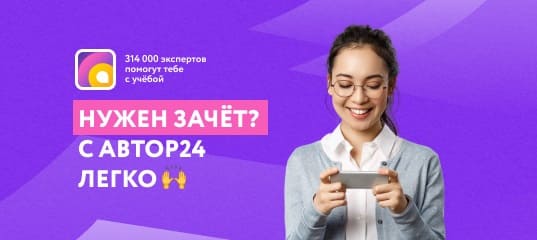
Мы поможем в написании ваших работ!