Физико-химические основы процесса
Нейтрализация азотной кислоты аммиаком
Процесс нейтрализации азотной кислоты аммиаком описывается простой реакцией:
NН3 + НNО3 = NН4NО3 +Q (3)
Эта реакция является практически необратимой и протекает с большой скоростью без образования побочных продуктов. В процессе нейтрализации выделяется большое количество тепла, определяемое тепловым эффектом реакции, концентрацией исходной азотной кислоты и температурой реагентов.
Так как конечной целью производства является получение твердого нитрата аммония, то на стадии нейтрализации стремятся получить, возможно, более концентрированные растворы аммиачной селитры, чтобы в дальнейшем упростить и удешевить стадию выпаривания раствора до состояния безводного плава.
Оптимальные условия для проведения процесса нейтрализации выбираются в результате анализа совместного влияния на этот процесс таких параметров, как концентрация азотной кислоты, температура и давление в реакторе.
Для получения высококонцентрированных растворов необходимо применять азотную кислоту высокой концентрации, подогревать реагенты.
Тепло процесса отводится, теряется в окружающую среду и расходуется на испарение воды из раствора. Получение безводного плава возможно при концентрации азотной кислоты – 63% и температура азотной кислоты –1000С. Однако целесообразность такого процесса ограничивается высокой температурой, которая развивается в нейтрализаторе. С повышением температуры нейтрализации увеличиваются потери азота из-за некоторого разложения азотной кислоты и аммиачной селитры. Кроме того, при высоких температурах вследствие заметного увеличения давления паров аммиачной селитры создаются условия для ее уноса с соковым паром в виде аэрозоля.
|
|
Температура в зоне нейтрализации зависит от давления. Промышленные установки для получения раствора аммиачной селитры с использованием тепла реакции нейтрализации подразделяются на 4 типа:
1) установки, работающие с использованием вакуум-испарителя – менее экономичен, используют танковые и продувочные газы производства аммиака или газы дистилляции производства карбамида.
2) установки, работающие под повышенным давлением - получению сокового пара с более высокими параметрами; но возникает необходимость в применении жидкого аммиака и усложнении технологической схемы.
3) комбинированные установки, работающие под давлением в зоне нейтрализации и при разрежении в зоне отделения соковых паров от раствора аммиачной селитры.
4) установки, работающие при атмосферном давлении (изб. Р = 0.3 ат) - широко распространена, плюсы: простота схемы, возможность использования газообразного аммиака, стабильность режима работы.Процесс нейтрализации ведут при 110 –1350С в слабокислой среде, т.к. при этом потери аммиака, азотной кислоты и аммиачной селитры с соковыми парами меньше, чем в щелочной среде.
|
|
Выпаривание растворов аммиачной селитры
Непременным условием улучшения качества аммиачной селитры является обеспечения высокой степени упаривания ее растворов в выпарных аппаратах с достижением остаточного содержания воды в готовом продукте не более 0.3%. В зависимости от метода кристаллизации продукта, конструкции выпарных аппаратов растворы аммиачной селитры упаривают до состояния плава различной концентрации. Так, при кристаллизации в гранбашнях растворы в доупарочных аппаратах упариваются до концентрации 99.7% - 99.9% NН4NО3. С увеличением концентрации растворов NН4NО3 при их упаривании температура раствора повышается, и возрастают потери аммиачной селитры с соковым паром. Поэтому применяют выпарные аппараты, работающие при разрежении 550 –600 мм рт ст. Это позволяет упаривать растворы при пониженных температурах их кипения, что способствует уменьшению потерь продуктов на этой стадии производства.
Для упаривания растворов аммиачной селитры часто применяют двухступенчатую схему выпарки, реже трехступенчатую. Двухступенчатое упаривание проводят с таким расчетом, чтобы в первой ступени концентрация повышалась до 84%, во второй – до 99.5%. Для выпарки применяют пленочные выпарные аппараты, представляющие собой кожухотрубные теплообменники с сепараторами специальной конструкции. Отличительной особенностью этих аппаратов является упаривание растворов в тонкой пленке (слое), движущейся со скоростью 25 м/сек вдоль внутренней поверхности трубок.
|
|
Кристаллизация плава аммиачной селитры (гранулирование)
В зависимости от методов кристаллизации плава аммиачная селитра может быть получена в виде мелких частично раздробленных кристаллов, в форме плотных чешуек и в виде сферической гранулы (d = 2 мм). При получении соли из плава селитры выделяется значительное количество тепла за счет охлаждения плава, кристаллизации и рекристаллизации соли. С повышением концентрации аммиачной селитры количество тепла, выделяющегося при кристаллизации соли, значительно уменьшается.
Кристаллизация аммиачной селитры из ее плавов осуществляется в аппарате с полным использованием тепла процесса (кристаллизаторы чашечного типа, шнеки),с частичным использованием тепла (охлаждающие барабаны - вальцы) и без использования тепла (грануляционные башни). Кристаллизаторы чашечного типа и шнеки сравнительно редко применяются в промышленности из-за их громоздкости и малой производительности. Охлаждающие барабаны–вальцы являются аппаратами непрерывного действия и большой производительности. Доля не гранулированной аммиачной селитры, получаемой в этих кристаллизаторах и барабанах, незначительна по сравнению с общим ее выпуском.
|
|
В н.в. существует три технологических способа гранулирования твердых веществ из расплавов:
1) Разбрызгивание капель расплавов с помощью различных грануляционных устройств в объеме гранбашни, где далее происходит затвердевание капель и охлаждение образовавшихся гранул при их свободном падении.
2) Напыление плава, затвердевание его и дальнейшее охлаждение образовавшихся гранул в условиях кипящего слоя.
3) Проведение тех же, что и по способу 2 операций в условиях вращающихся барабанов с внутренними лопастями - сферодайзеров.
Основным промышленным способом является гранулирование расплавов в грануляционных башнях.
Сущность процесса гранулирования в аппарате с кипящим слоем заключается в следующем: раствор, упаренный до содержания NН4NО3 в нем 80-86%, с помощью форсунок распыляется в псевдоожиженный слой твердых частичек нитрата аммония. Охлаждающим агентом является горячий воздух. Происходит испарение влаги из диспергированной жидкости и образование твердых мелких частичек, которые периодически попадают в зону факела, увлажняются и снова подсыхают за счет теплоты горячего воздуха, и таким образом их размеры увеличиваются. Аппарат работает непрерывно. Преимущество данного способа заключается в совмещении стадий глубокого упаривания раствора, грануляции и сушки в одном аппарате.
Конечной стадией процесса является кондиционирование удобрения –обработка поверхности гранул различными добавками (чаще всего ПАВ) с целью предотвращения слеживания и обеспечения хорошей сыпучести. Обработка гранул ПАВ приводит к гидрофобизации поверхности гранул, что защищает продукт от
быстрого увлажнения при соприкосновении с воздухом, относительная влажность которого выше гигроскопической точки аммиачной селитры. В качестве ПАВ используют алкилсульфаты, алкилсульфонаты,
алкиларилсульфонаты, соли алифатических и ароматических аминов и др. В качестве опудривающих добавок применяют диатомит, талькомагнезит, вермкулит, известняк, мел, доломит и др.
Кондиционирование гранул нитата аммониия осуществляется во вращающемся барабане перед отправкой его на склад, причем обрабатывается только товарная фракция продукта.
Товарный нитрат аммония хранят в одноэтажных огнестойких складах израсчета до 20000т насыпью или 2500 т в мешках в каждом помещении. Помещения склада должны быть сухими, оборудованными вентиляцией и воздушным отоплением. Полы настилают из кислотоупорных материалов.
В процессе хранения соблюдают меры, исключающие возможность загрязнения нитрата аммония различными предметами, смазывающими и обтирочными материалами и др. Предусматривают контроль за температурой не только поступающего нитрата аммония, но и внутри бурта, а также соответствующую сигнализацию. Нитрат аммония не должен находится в контакте с веществами, дающими щелочную или кислую реакцию.
Технологическая схема производства аммиачной селитры.
Рассмотрим технологическую схему современного крупнотоннажного агрегата по производству аммиачной селитры АС –72 мощностью 1360 т/сутки. Исходная 58–60% азотная кислота подогревается в подогревателе 2 до температуры 70–800Ссоковым паром из аппарата ИТН 1 и подается на нейтрализацию. Перед аппаратом 1 азотной кислоте добавляют фосфорную и серную кислоты в таких количествах, чтобы в готовом продукте содержалось 0.3–0.5% Р2О5 и 0.05–0.2% сульфата аммония.
В агрегате АС-72 установлены два аппарата ИТН, работающие параллельно. Кроме азотной кислоты в них подают газообразный аммиак, предварительно нагретый в подогревателе 3 паровым конденсатом до Т =120–1300С. Количества подаваемых азотной кислоты и аммиака регулируют таким образом, чтобы на выходе из аппарата ИТН раствор имел небольшой избыток кислоты (2 –5 г/л), обеспечивающий полнотупоглощения аммиака.
В нижней части аппарата происходит реакция нейтрализации при температуре155 –1700С; при этом получается концентрированный раствор, содержащий 91–92%NН4NО3. В верхней части аппарата водяные пары (так называемый соковый пар)отмываются от брызг аммиачной селитры и паров азотной кислоты. Часть теплоты сокового пара используется на подогрев азотной кислоты. Затем соковый пар направляют на очистку и выбрасывают в атмосферу.
СХЕМА С ДВОЙНОЙ УПАРКОЙ
Кислый раствор аммиачной селитры направляют в донейтрализатор 4, куда поступает аммиак, необходимый для взаимодействия с оставшейся азотной кислотой. Затем раствор подают в выпарной аппарат 5. Выпарной аппарат 5снабжен промывателем воздуха, что дополнительно снижает поступление загрязнений в промывной скруббер 20. Так, соковый пар из аппарата ИТН содержит1–3 г/л аммиачной селитры и менее 1 г/л азотной кислоты, а воздух после выпарного аппарата – 2-3г/м3 селитры и 0.5–1г/м3 аммиака. Полученный плав, содержащий 99.7 –99.8% селитры, на выходе из выпарного аппарата 5 проходит донейтрализацию в гидрозатворе 10, при 1750С проходит фильтр 11, поступает в бак12, на котором установлен центробежный погружной насос 13, перекачивающий плав на верх башни в напорный бак 16.
Процесс гранулирования плава осуществляется в прямоугольной башне с размерами в плане 8 *11 м. Высота полета гранул 50 –55 м. Такая большая высота выбрана из условий полной кристаллизации капель и остывания гранул средним диаметром 2.2 –2.6 мм в полете до температуры 90–1100С при экономном расходе
воздуха через башню с целью снижения расхода электроэнергии и скорости воздуха в башне.
Высококонцентрированный плав из напорного бака 16 поступает в три гранулятора 17 производительностью 20 т/ч каждый. В нижнюю часть грануляторов подается воздух, охлаждающий падающие сверху капли селитры. Во время падения капель с высоты 50–55 м при обтекании их потоком воздуха образуются гранулы
удобрения. Температура гранул на выходе из башни равна 90–1100С; горячие гранулы охлаждают в аппарате кипящего слоя 24. Это прямоугольный аппарат, имеющий три секции и снабженный решеткой с отверстиями. Под решетку вентиляторами подается воздух; при этом создается псевдоожиженный слой гранул селитры, поступающих по транспортеру из грануляционной башни. Воздух после охлаждения попадает в грануляционную башню.
Гранулы аммиачной селитры транспортером 25 подают на обработку поверхностно-активными веществами во вращающий барабан 27. Затем готовое удобрение транспортером 25 направляют на упаковку.
Таким образом, в башне агрегата АС–72 в результате применения монодисперсных грануляторов обеспечен выравненный гранулометрический состав, снижено содержание мелких гранул, уменьшена скорость воздуха по сечению башни, т.е. созданы более благоприятные условия для уменьшения уноса пыли из башни и снижения нагрузки на промывной скруббер.
Воздух, выходящий из грануляционной башни, загрязнен частицами аммиачной селитры, а соковый пар из нейтрализатора и паро-воздушная смесь из выпарного аппарата содержат непрореагировавшие аммиак и азотную кислоту, а также частицы унесенной аммиачной селитры. Для очистки этих потоков в верхней части грануляционной башни расположены шесть параллельно работающих промывных скрубберов тарельчатого типа 20, орошаемых 20–30%-ным раствором аммиачной селитры, которая подается насосом 14 из сборника 15. Часть этого раствора отводится в нейтрализатор ИТН для промывки сокового пара, а затем подмешивается к раствору селитры, и, следовательно, используется для выработки продукции.
Очищенный воздух отсасывается из грануляционной башни вентилятором 19 и выбрасывается в атмосферу.
Раздел 3. Калийные удобрения
Общая характеристика
Больше 90% добываемых из недр земли и вырабатываемых заводскими методами калийных солей используют в качестве удобрений. Калийные минеральные удобрения представляют собой природные или синтетические соли и содержат питательный элемент в форме иона К+. Калийные удобрения подразделяются на:
1) сырые калийные соли – размолотые природные водорастворимые калийные минералы;
2) концентрированные калийные удобрения – продукты заводской переработки сырых солей;
3) калийные соли – продукты, получаемые смешением сырых солей, содержащих калий и натрий и концентрированных солей калия.
В зависимости от природы аниона калийные удобрения подразделяются на хлоридные и бесхлорные.
Качество калийной продукции и сырья принято характеризовать содержанием основного компонента (например, КСl) или содержание калия в пересчете на К2О.Обычно в калийных удобрениях содержится 40-60% К2О, а в используемых в качестве удобрений сырых солях –20%.
К калийным удобрениям хлоридного типа относят природные минералы (каинит, сильвинит), продукты промышленной переработки минералов (хлорид калия),смешанные калийные соли, полученные смешением природных минералов схлоридом калия, электролитные растворы (побочный продукт электролиза карналлита). К бесхлорным калийным удобрениям относятся сульфат калия и калимагнезия (двойная соль сульфата калия и сульфата магния).
Все калийные удобрения растворимы в воде. Их выпускают в кристаллическом игранулированном виде. Содержание питательного элемента в них (в пересчете на К2О)колеблется от 10% в природных минералах до 60% в концентрированном удобрении – хлориде калия. Основные калийсодержащие минералы и их составы приведены в таблице 1.
Таблица 1 – Состав и свойства наиболее распространенных калийных минералов
Минерал | Состав | Содержание К2О, % |
Сильвин | KCl | 63 |
Сильвинит | KCl∙NaCl | 22-25 |
Карналлит | KCl∙MgCl2∙6H2O | 17 |
Каинит | KCl∙MgSO4∙3H2O | 19 |
Шенит | K2SO4∙MgSO4∙6H2O | 23 |
Лангбейнит | K2SO4∙2MgSO4 | 23 |
Полигалит | K2SO4∙MgSO4∙2CaSO4∙2H2O | 16 |
Алунит | (K, Na)2SO4∙Al2(SO4)3∙4Al(OH)3∙ | 23 |
Калушит | K2SO4∙CaSO4∙H2O | - |
Глазерит | 3K2SO4∙Na2SO4 | - |
Нефелин | (K, Na)2O∙Al2O3∙2SiO2∙ | 6-7 |
Из приведенных данных видно, что в н.в. основным калийным удобрением, обеспечивающим свыше 95% потребностей сельского хозяйства, является хлорид калия. Природные низкоконцентрированные минералы без предварительной переработки в н.в. не используются.
Сырьем для получения калийных солей служат растворимые в воде природные минералы, содержащие хлористый калий или сульфат калия. Хлористый калий получают главным образом из сильвинита, руды состоящей из смеси сильвинита КСl и галита NаСl; другим видом сырья, используемым редко, является карналлит с примесью хлористого натрия. Сульфат калия получают из ангбейнита, каинита.
Месторождения калийных солей находятся на Урале – Верхнекамское месторождение, представленное сильвинито-карналлитовыми рудами. Данное месторождение имеет большое содержание газов (азот, метан, водород, диоксид углерода) в порах и пустотах породы. Содержание КСl в сильвините –23-30%, NаСl–65-75%, нерастворимых глинистых веществ–0,5–3%. Второе по величине месторождение калийных руд имеется в Белоруссии. Оно представлено сильвинитами с небольшой примесью карналлита (0,1-0,3%). В руде содержится 26-29%КСl и 4-12% нерастворимых глинистых веществ. В воде океанов запасы калия практически неисчерпаемы. Сгущенная путем испарения в бассейнах морская вода может явиться источником для промышленного получения солей калия.
Хлорид калия
Хлорид калия представляет собой твердое кристаллическое вещество с Т
плавл.=776°С. Это безбалластное удобрение содержит 63,1% калия в пересчете на К2О, плохо растворим в воде и метаноле.
Хлорид калия является основным продуктом калийном промышленности. Около 95 % хлорида калия применяется в качестве удобрения, а остальное количество перерабатывают в соединения калия, применяемые в различных отраслях народного хозяйства.
Согласно требований действующего ГОСТ 4568-83, предусматривается производство хлорида калия марок К (кристаллизацией из растворов), Ф (флотационным обогащением калийных руд) для технических целей и гранулированного или крупнокристаллического продукта для сельского хозяйства. Хлорид калия, выпускаемый для с/х,с целью исключения слеживаемости, обрабатывается алифатическими аминами или другими кондиционирующими добавками.
Таблица 2 – Требования к качеству KCl (содержание в пересчете на сухое вещество, %)
Показатель | Технический | Для сельского хозяйства | ||||
К | Ф | |||||
1 сорт | 2 сорт | 1 сорт | 2 сорт | 1 сорт | 2 сорт | |
KCl, не менее | 98 | 95±1 | 95±1 | 91±1 | 95±1 | 91±1 |
NaCl, не более | 1,4 | 4,5±1 | 4,5±1 | 7±1 | Не нормируется | |
Влаги, не более | 1,0 | 1,0 | 1,0 | 1,0 | 1,0 | 1,0 |
не раствор.в воде остатка, не более | 0,2 | Не нормируется |
Хлорид калия производят в основном двумя способами:
1) галургическим
2) флотационным
Дата добавления: 2018-02-28; просмотров: 579; Мы поможем в написании вашей работы! |
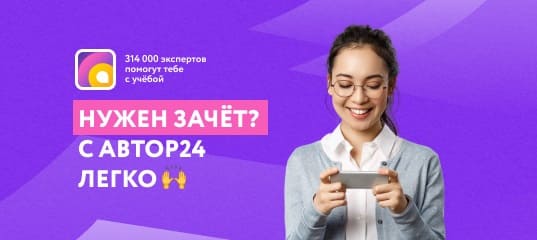
Мы поможем в написании ваших работ!