Отклонения на угловые размеры поковок
Длина угловых элементов L, мм | Допуск для классов точности | |
I | II | |
До 25 25-60 60-100 100-160 Св. 160 | ±1°30¢ ±0°45¢ ±0°30¢ ±0°15¢ ±0°10¢ | ±3°00¢ ±1°30¢ ±0°45¢ ±0°30¢ ±0°15¢ |
Таблица 3.11
Отклонения на радиусы скруглений в поковках, мм (см. эскиз к табл. 3.10)
Радиусы скруглений поковки R | Допуск для классов точности | |
I | II | |
До 3 3-6 6-10 10-16 16-25 25-40 40-60 |
Порядок расчета технико-экономических показателей следующий.
Определяем массу заготовки
Gз = r×Vз, (3.8)
где r – плотность материала, кг/см3; Vз – объем заготовки, см3.
Объем заготовки определяется по плюсовым допускам.
Обычно сложную фигуру заготовки условно разбивают на элементарные части (цилиндры, конусы, пирамиды и т.д.) и определяют объемы этих элементарных частей. Сумма элементарных объемов составит общий объем заготовки. Принимая во внимание все потери материала (угар, облой, некратность, на отрезку и т.д.), в зависимости от метода получения заготовки определяют норму расхода материала на проектируемую деталь.
Потери материала на деталь, изготавливаемую из проката, состоят из некратности длины проката, торцовой обрезки, прорезки и удаляемых опорных концов.
Длина торцового обрезка зависит от размеров сечения проката и при резке ножницами обычно составляет Lо.т. = (0,3…0,5)×а, где а - сторона квадрата (диаметр круга).
Прорезка определяется в зависимости от толщины дисковой пилы или ширины резца. Ширина прореза сегментной дисковой пилы диаметром 660 мм – 6 мм, а диаметром 710 мм – 6,5 мм.
|
|
Ширина режущей части резца при разрезке проката на станках токарного типа зависит от диаметра заготовки:
Диаметр заготовки, мм … 40-60 60-80 80-100 100-150
Ширина режущей части
резца, мм ………………… 3-5 4-5; 5-6; 6-7
Некратность длины проката определяется исходя из выбранной длины проката и заготовки с учетом потерь от выбранного метода заготовительного раскроя.
При расчете некратности длины проката необходимо стремиться к нулю или минимальным величинам. Средне вероятная расчетная длина некратности при раскрое немерного проката составляет примерно половину длины заготовки.
Некратность в зависимости от принятой длины проката
Lнк = Lпр – х (L3+lр), (3.9)
где Lпр – длина выбранного проката, мм; х-число заготовок, изготавливаемых из принятой длины проката, шт; Lз – длина заготовки, мм; lp-ширина реза, мм.
Число заготовок, изготавливаемых из принятой длины проката,
, (3.10)
где lо.т – длина торцового обрезка проката, мм; lзаж – минимальная длина опорного (зажимного) конца, мм.
Минимальная длина опорного конца зависит от конструкции технологического оборудования и зажимных элементов приспособления для данного станка. Она должна быть достаточной для создания надежного контакта при уравновешивании опрокидывающего момента (обычно не менее 10…20 мм); её выбирают в каждом отдельном конкретном случае.
|
|
Общие потери материала (%) при изготовлении деталей из проката
Пп.о = Пнк + По.т + Пзаж + Потр, (3.11)
где Пнк – потери материала на некратность, %;
Пнк = (Lнк ×100) / Lпр; (3.12)
По.т – потери на торцовую обрезку проката, %
По.т = (lо.т ×100)/Lпр; (3.13)
Пзаж – потери при выбранной длине зажима,%
Пзаж = (lзаж×100)/Lпр; (3.14)
Потр – потери на отрезку заготовки,%
Потр = (lр×100)/Lпр. (3.15)
Отходы при механической обработке металлов по разным видам заготовок от чистой массы деталей в среднем составляют для отливок чугунных, стальных, бронзовых 15-20%; свободной ковки 15-40%, объемной горячей штамповки 10%; проката (стали) 15%.
Основным показателем, характеризующим экономичность выбранного метода изготовления заготовок, является коэффициент использования материала, выражающий отношение массы детали к массе заготовки.
Коэффициент использования материала с учетом технологических потерь
Ки.м = Gд/Gз.п, (3.16)
где Gд – масса детали по рабочему чертежу, кг; Gз.п – расход материала на одну деталь с учетом технологических потерь, кг.
|
|
Для рационального расходования материала необходимо повышать коэффициент его использования, он должен быть не ниже 0,75.
Расход материала на заготовку с учетом технологических потерь
Gз.п = Gз(100+Пп.о)/100. (3.17)
Годовая экономия материала от выбранного метода получения заготовки с учетом технологических потерь
Эм.п = (G`з.п - G``з.п) N, (3.18)
где G`з.п – расход материала на одну деталь при первом методе получения заготовки, G``з.п – расход материала на одну деталь при втором методе получения заготовки, кг.
Технико-экономический расчет себестоимости производится в зависимости от выбираемых методов получения заготовок.
Стоимость заготовки из проката, штамповки и литья определяют по расходу материалу, массе стружки на деталь, стоимость материала и его технологическим отходам.
Стоимость заготовки можно найти по формуле:
Сз.п = СмGз.п – (Gз.п-Gд) , (3.19)
где См – цена 1 кг материала заготовки, руб; Сотх – цена 1 т отходов материала, руб.
Экономический эффект по использованию материала на годовую производственную программу выпуска деталей без учета технологических потерь:
Эм = (G`з-G``з) См N, (3.20)
где Gз – расход материала на деталь при первом методе получения заготовки, кг; Gз – расход материала на деталь при втором методе получения заготовки, кг; N – годовой объем выпуска деталей, шт.
|
|
Экономический эффект выбранного вида изготовления заготовки в денежном выражении на годовую производственную программу выпуска изделия составит:
Э = (С`з.п – С``з.п)×N, (3.21)
где Сз.п – стоимость заготовки, полученная при первом методе, руб; Сз.п – стоимость заготовки, полученная при втором методе, руб.
Пример. Произвести технико-экономический расчет двух вариантов изготовления заготовки: методом горячей объемной штамповки и из проката. Годовой объем выпуска деталей – 180 000 шт. Рабочий чертеж детали – вал (см. рис. 3.1). Материал детали – сталь 45 ГОСТ 1050-88. Масса детали – 10,8кг.
Устанавливаем тип производства по годовому объему выпуска изделий и массе детали по рабочему чертежу согласно табличным данным (см. табл. 3.1). Тип производства – массовый.
Вариант I. Заготовка из проката. Согласно точности и шероховатости поверхностей обрабатываемой детали определяем промежуточные припуски по таблицам. За основу расчета промежуточных припусков принимаем наружный диаметр 80f 7 мм.
Обработку поверхности диаметром 80 мм производят в жестких центрах, на многорезцовом токарном полуавтомате; окончательную обработку поверхности детали выполняют на кругошливовальном станке.
Технологический маршрут обработки данной поверхности:
Операция 005. Токарная.
Операция 010. Токарная.
Операция 015. Термическая обработка НRCэ 41…45.
Операция 020. Шлифовальная однократная.
1. HRCЭ 41... 45. '
2. Неуказанная шероховатость поверхностей Ra = 12,5 мкм.
3. * Размер для cправки
Рис. 3.1. Чертеж детали
Припуски на подрезание торцовых поверхностей определяют в табл.3.12,а припуски на обработка наружных поверхностей (точение и шлифование) - по табл. 3.13.
При черновом точении припуск на обработку составляет 4,5мм, a при чистовом 2 мм и на шлифовальную однократную обработке 0,5 мм.
Определяем промежуточные размеры обрабатываемых поверхности согласно маршрутному технологическому процессу:
на токарную операцию 010
Dр.010 = Dн = 2zш = 80 +0,5 + 80,5 мм;
на токарную операцию 005
Dр.005 = Dр.010 + 2z010 = 80,5 + 2,0 = 82,5 мм;
Расчетный размер заготовки
Dр.з = Dр.005 + 2z005=82,5 +4,5=87 мм.
По расчетным данным заготовки выбираем необходимый размер горячекатаного проката обычной точности по ГОСТ 2590-71 (табл. 3.14). Например, диаметр проката 90 мм записывается следующим образом:
Круг
Нормальная длина проката стали обыкновенного качества при диаметре 53-110мм 4-7 м. Отклонения для диаметра 90мм равны 0,5 мм 90,5 (см. табл. 3.14).
Припуски на подрезку торцовых поверхностей заготовки выбираются по табл. 3.12. Припуск на обработку двух торцовых поверхностей заготовки равен 2,4 мм.
300+2,4=302,4=303
Таблица 3.12
Дата добавления: 2015-12-20; просмотров: 12; Мы поможем в написании вашей работы! |
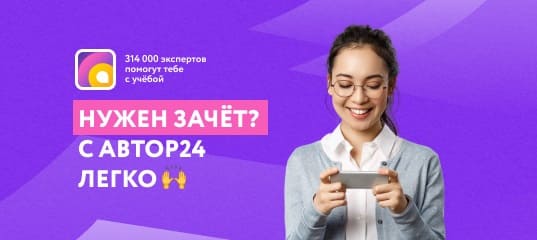
Мы поможем в написании ваших работ!