Технико-экономическое обоснование выбора заготовки
Технико-экономическое обоснование выбора заготовки для обрабатываемой детали производят по нескольким направлениям: металлоемкости, трудоемкости и себестоимости, учитывая при этом конкретные производительные условия. Технико-экономическое обоснование ведется по двум или нескольким выбранным вариантам. При экономической оценке определяются металлоемкость, себестоимость или трудоемкость каждого выбранного варианта изготовления заготовки, а затем их сопоставляют.
Технико-экономический расчет изготовления заготовки производят в следующем порядке:
устанавливают метод получения заготовки согласно типу производства, конструкции детали, материалу и другим техническим требованиям на изготовление детали;
назначают припуски на обрабатываемые поверхности детали согласно выбранному методу получения заготовки по нормативным таблицам или производят расчет аналитическим методом;
определяют расчетные размеры на каждую поверхность заготовки;
назначают предельные отклонения на размеры заготовки по нормативным таблицам в зависимости от метода получения заготовки;
производят расчет массы заготовки на сопоставляемые варианты;
определяют норму расхода материала с учетом неизбежных технологических потерь для каждого вида заготовки (некратность, на отрезание, угар, облой и т.д.);
определяют коэффициент использования материала по каждому из вариантов изготовления заготовок с технологическими потерями и без потерь;
|
|
определяют себестоимость изготовления заготовки, выбранных вариантов для сопоставления и определения экономического эффекта получения заготовки;
определяют годовую экономию материала от сопоставляемых вариантов получения заготовки;
определяют годовую экономию от выбранного варианта заготовки в денежном выражении.
Величину припуска на механическую обработку стальных поковок общего назначения, изготовляемых горячей объемной штамповкой на разных видах кузнечно-прессового оборудования, отливок, получаемых разными методами литья (стали, чугуна и цветных металлов), определяют по табличным нормативам согласно массе заготовки, точности ее изготовления, группе стали, степени сложности габаритным размерам, шероховатости обрабатываемых поверхностей и другим конструктивным элементам детали и техническим требованиям на её изготовление.
Расчетные размеры для заготовки определяют по следующие формулам:
при обработке наружных и внутренних поверхностей тел вращения (для внутренних поверхностей принимают с обратным знаком) принимают
Dp = Dном + 2Zo; (3.6)
при односторонней обработке плоских поверхностей
|
|
Нр = Нном + Zo, (3.7)
где Dр – расчетный диаметр заготовки, мм; Dном – номинальный диаметр обрабатываемой поверхности детали, мм; Zо – общий припуск на обработку на одну сторону, мм; Нр – расчетный размер плоской поверхности, мм; Нном – номинальный размер обрабатываемой плоской поверхности, мм.
Расчетные размеры на заготовку округляют до технологической возможности оборудования и экономической целесообразности принятой точности. Рекомендуемые расчетные размеры заготовок следует округлять в сторону увеличения припусков в зависимости от степени точности и типа производства.
Отклонения (допуски) на размеры заготовок назначают по таблицам в зависимости от метода получения заготовок (прокат, литье, штамповка и др.).
Схема определения допусков на штампованные поковки повышенной и нормальной точности (табл. 3.2) содержит четыре основных параметра – масса поковки, группа стали, степень сложности, размер.
Пример. Поковка класса I массой 1,4 кг на размер250 мм. Группа стали М1 и степень сложности поковки С2. Определить по таблице допуск на размер заготовки. Допуск на размер равен мм (см. табл. 3.2).
Поковка класса I массой 0,35 кг на размер 160 мм. Группа стали М1 и степень сложности С1. Определить по таблице допуск на размер заготовки. Допуск на размер заготовки равен мм (см. табл. 3.2).
|
|
Поковка класса I массой 2,8 кг на размер 280 мм. Группа стали М2 и степень сложности С3. Определить по таблице допуск на размер заготовки. Допуск на размер заготовки равен мм (см. табл. 3.2).
Допуск на внутренние размеры поковок должны устанавливаться с обратными знаками, например, если для наружной поверхности диаметром 80 мм установлен допуск , то для внутреннего диаметра 80 мм допуск будет равен
.
Допускаемые отклонения на размеры назначают по ГОСТ 1855-55 для отливок из серого чугуна и по ГОСТ 2009-55 для стальных фасонных отливок (табл. 3.3).
Таблица 3.3
Допускаемые отклонения (±) на размеры чугунных и стальных отливок
Дата добавления: 2015-12-20; просмотров: 8; Мы поможем в написании вашей работы! |
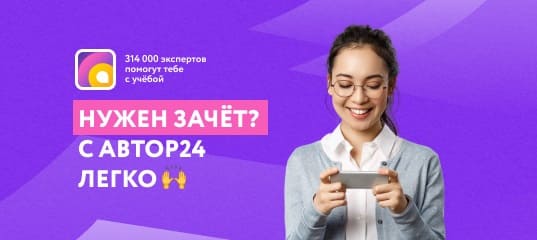
Мы поможем в написании ваших работ!