Эффективность (точность) грохочения
В производственных условиях при грохочении достичь идеально точного разделения по крупности невозможно, так как на процесс грохочения влияют различные факторы. Поэтому при грохочении часть зерен размером менее отверстий сита не может пройти сквозь просеивающую поверхность и оказывается в надрешетном продукте, тем самым «засоряя» его и одновременно уменьшая количество подрешетного продукта.
Основным показателем грохочения является его эффективность Е (%), характеризующая точность разделения материала по крупности. Численно она определяется отношением количества подрешетного продукта к общему количеству его в исходном материале, т.е. представляет собой извлечение нижнего класса в подрешетный продукт.
Эффективность грохочения можно рассчитать по следующей формуле
, (1.1)
где С – масса подрешетного продукта;
Q – масса исходного материала;
α – содержание нижнего класса в исходном материале, %.
Для определения эффективности грохочения по указанной формуле необходимо знать массу исходного материала Q и подрешетного продукта С, непосредственное определение которых при непрерывном процессе в производственных условиях представляет известные трудности. Поэтому отношение масс С / Q определяют по содержанию нижнего класса в исходном материале α и надрешетном продукте v.
Формула для определения эффективности грохочения по нижнему классу имеет вид
|
|
, (1.2)
где v – содержание нижнего класса в надрешетном продукте, %.
Содержание нижнего класса α и v определяют тщательным рассевом проб как исходного материала Q, так и надрешетного продукта Т на ситах с отверстиями той же величины и формы, что и в сите грохота, эффективность грохочения которого определяют.
Подобным образом можно определить эффективность грохочения по любому заданному суммарному или узкому классу крупности, который мельче размера отверстий сита грохота, считая эффективностью грохочения по заданному классу отношение массы этого класса в подрешетном продукте к массе того же класса в исходном материале, т.е.
(1.3)
где α 1, 1, v 1 – соответственно содержание заданного класса крупности в исходном материале, подрешетном и надрешетном продуктах в процентах.
Формула (1.2) позволяет определить эффективность грохочения Е упрощенно по содержанию v нижнего класса в надрешетном продукте, по так называемому «замельчению»: этим способом пользуются для целей текущего контроля операции грохочения при относительно постоянном или мало изменяющемся содержании нижнего класса α в исходном материале, так как каждому «замельчению» надрешетного продукта будет соответствовать определенное извлечение данного класса в подрешетный продукт.
|
|
При грохочении сыпучего материала эффективность грохочения зависит от продолжительности рассева. Поэтому увеличение производительности грохота, приводящее к уменьшению продолжительности рассева материала, сопровождается понижением эффективности грохочения.
На эффективность грохочения значительное влияние оказывают также гранулометрический состав и влажность исходного материала, размер и форма отверстий сит на грохоте, частота и амплитуда колебаний просеивающей поверхности, угол наклона сита, способ грохочения.
Эффективность грохочения возрастает с увеличением содержания подрешетного продукта в исходном материале и при его значениях 60–80 % становится максимальной. Наличие в исходном материале так называемых «трудных» зерен, имеющих размер, близкий к размеру отверстий сита, вызывает их забивку и понижает эффективность грохочения.
Влажность исходного материала (содержание внешней влаги) значительно ухудшает эффективность грохочения, особенно мелких классов. При повышенном содержании влаги мелкие зерна слипаются в крупные агрегаты и разделить их при сухом грохочении с достаточной эффективностью не удается. В таких случаях предусматривается мокрое грохочение, при котором вода подается на грохот вместе с исходным материалом. В необходимых случаях мокрое грохочение повышает качество продукции, например, песка, щебня, гравия.
|
|
Производительность грохотов в общем случае зависит от удельной нагрузки (т/м2 ч), площади сита, насыпной плотности материала, коэффициентов, учитывающих различные факторы процесса грохочения, а также конструкцию просеивающей поверхности.
Дата добавления: 2015-12-19; просмотров: 28; Мы поможем в написании вашей работы! |
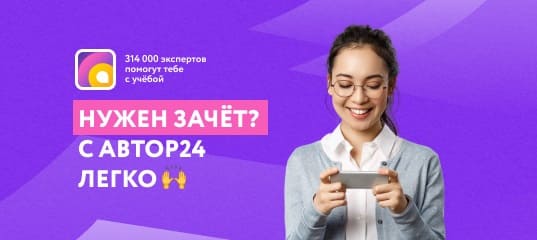
Мы поможем в написании ваших работ!