Стадиальность и схемы дробления и измельчения
На обогатительных фабриках дробление и измельчение полезных ископаемых производится с высокой степенью измельчения конечного продукта. Например, для получения доломитовой муки следует куски крупностью до 1300 мм вначале раздробить, а затем измельчить до крупности 0,1 мм, т.е. общая степень дробления (измельчения)
Получение высоких степеней дробления (измельчения) в одной машине невозможно. Вследствие конструктивных особенностей существующих дробилок и мельниц их эффективная работа возможна при ограниченных степенях дробления и измельчения. Поэтому наиболее рационально дробить и измельчать материал от исходной крупности до требуемого размера конечного продукта в нескольких последовательно работающих дробилках и измельчающих машинах. В каждой из них будет осуществлена лишь часть общего процесса дробления или измельчения, которая называется стадией дробления или измельчения.
Общая степень дробления и измельчения равна произведению всех стадий дробления и измельчения
i общ = . (2.7)
В зависимости от крупности дробимого материала и дробленого продукта различают:
- крупное дробление (от 1500–500 до 350–100 мм), или первая стадия дробления (i обычно не более 5);
- среднее дробление (от 350–100 до 100–40 мм), или вторая стадия дробления (i обычно не более 8–10);
- мелкое дробление (от 100–40 до 30–5 мм), или третья стадия дробления (i обычно не более 10).
|
|
Измельчение также осуществляется обычно в несколько стадий. Степень измельчения при этом оценивают или соотношением размеров максимальных зерен в исходном и измельченном продукте, или процентным содержанием определенного класса крупности (+0,100 мм; –0,074 мм или –0,044 мм) в измельченном продукте. Различают:
- грубое измельчение (от 30–5 до 5–0,1 мм при содержании класса –0,074 мм 20–40 %);
- тонкое измельчение (от 5–0,1 до 0,1–0,05 мм при содержании класса –0,074 мм 40–75 %);
- сверхтонкое измельчение (от 0,1–0,05 мм до содержания класса –0,074 мм более 75 %).
Дробление и особенно измельчение являются весьма энергоемкими процессами. Поэтому при осуществлении их на практике следует руководствоваться принципом: «Не дробить ничего лишнего». Поэтому, если в исходном продукте содержится достаточное количество готового класса, то его выделяют перед дроблением или измельчением путем грохочения или классификации по одной из ниже приведенных схем (рис. 2.2).
Рис. 2.2. Схемы открытого и замкнутого циклов дробления и измельчения:
а – открытый цикл; б – открытый цикл с предварительным грохочением или
классификацией; в – замкнутый цикл с совмещенными предварительным
и поверочным грохочением или классификацией; г – замкнутый цикл
|
|
с поверочным грохочением или классификацией
Совокупность операций дробления и грохочения или измельчения и классификации составляет цикл дробления или измельчения, который может быть открытым или замкнутым. В открытом цикле (рис. 2.2, а) каждый кусок проходит через дробилку или мельницу только один раз. В замкнутом цикле выделяемые при грохочении или классификации крупные куски возвращаются в виде циркулирующей нагрузки еще раз на дробление или доизмельчение в тот же самый аппарат (рис. 2.2, в, г).
Процессы дробления осуществляются в щековых, конусных, валковых, молотковых, роторных дробилках, а также в других аппаратах для дробления. Выбор типа дробимого аппарата зависит от
физико-механических свойств (прочности, хрупкости, вязкости, трещиноватости и др.) и крупности исходного материала, требуемой степени дробления и гранулометрического состава дробимого продукта, заданной производительности.
Щековые дробилки
В щековых дробилках материал дробится в рабочем пространстве, образованном подвижной и неподвижной щеками в результате раздавливания, раскалывания, излома и истирания кусков материала, загружаемых в приемную часть дробилки. При приближении подвижной щеки к неподвижной осуществляется рабочий ход, при обратном движении – холостой. Куски материала в рабочем пространстве располагаются в зависимости от крупности: вверху – более крупные, ниже – менее крупные. По мере их дробления под действием силы тяжести при каждом отходе подвижной щеки материал продвигается вниз. Одновременно дробленый материал из нижней части периодически разгружается вниз через выпускную щель при каждом холостом ходе подвижной щеки.
|
|
Щековые дробилки (ЩД) применяются в основном для крупного и среднего, а также мелкого дробления.
По характеру движения подвижной щеки различают щековые дробилки двух кинематических групп (рис. 2.3):
- с простым качанием щеки (ЩДП);
- со сложным движением щеки (ЩДС).
Чтобы предотвратить выброс материала из приемного отверстия дробилки при рабочем ходе подвижной щеки, максимальное значение угла между щеками, называемого углом захвата , не должно превышать двойного угла трения дробимого материала, т.е.
, (2.9)
где - угол трения дробимого материала.
Рис. 2.3. Принцип действия и кинематические схемы щековых дробилок:
а – с простым движением щеки; б – со сложным движением щеки;
|
|
1 – неподвижная щека; 2 – подвижная щека; 3 – дробящая футеровочная
плита; 4 – маховик; 5 – передняя распорная плита; 6 – задняя распорная плита;
7 – шарнирно-эксцентриковый механизм; 8 – распорная плита;
9 – приводной эксцентриковый механизм
На практике угол захвата лежит в пределах =15–24о для различных материалов.
Типоразмеры щековых дробилок, характеризуемые шириной В и длиной L – их приемного отверстия, зависят от крупности кусков перерабатываемой горной породы. Максимальная крупность кусков исходного материала не должна превышать 85 % ширины приемного отверстия.
Крупность дробленого продукта зависит от величины разгрузочной щели в, которая может иметь минимальный размер S 1 при
сомкнутом положении щек (конец рабочего хода) и максимальный размер S 2 при разомкнутом положении (конец холостого хода). Разница между ними представляет собой ход подвижной щеки, т.е.
S 2 – S 1 = e. (2.10)
Ширина выходной щели в связана с максимальной крупностью кусков в готовом продукте и определяется
d max = 1,2 в.
Размер выходной щели в – параметр переменный. В щековых дробилках его можно регулировать, тем самым изменяя крупность продукта. Диапазон изменений в для щековых дробилок крупного дробления 45, среднего
30, мелкого
15 %.
Наибольшую производительность щековые дробилки развивают при оптимальной частоте качаний подвижной щеки, связанную с частотой вращения приводного вала. При данной частоте максимально используется время отхода подвижной щеки, что дает возможность разгрузиться вниз призме выпадения с наибольшей высоты и, соответственно, обеспечить максимальную производительность. Оптимальная частота качаний подвижной щеки (мин-1)
или
, (2.11)
где g – ускорение свободного падения; g = 9,81 м/с2.
Объемная производительность щековой дробилки (м3/ч)
V = 30 n (S 1 + S 2) (S 2 – S 1) L / tgα. (2.12)
Массовая производительность (т/ч)
, (2.13)
где – плотность материала, т/м3;
k – коэффициент разрыхления материала при выходе из дробилки в зависимости от его прочности, k = 0,25–0,70.
Дробящие футеровочные плиты являются основными рабочими органами щековых дробилок и представляют собой сменные быстроизнашивающиеся детали. Их стоимость составляет 30–40 % общих затрат на дробление. Дробящие футеровочные плиты, крепящиеся к неподвижной и подвижной щекам, делают из прочных износостойких материалов. Для того, чтобы заменить раздавливание менее энергоемкими видами деформации (изгиб, сдвиг), футеровочные плиты или их часть делают с рифлениями. Для этого выступы на плите неподвижной щеки располагают против впадин на плите подвижной щеки. Боковые стенки рабочего пространства дробилки футеруются гладкими плитами.
С целью снижения затрат энергии на дробление в последнее время находят применение различные конструкции и профили дробящих плит (сочетание прямолинейного и криволинейного профилей, выполнение обоих профилей криволинейными и т.п.).
Дробилки с простым качанием щеки применяются для крупного дробления. Дробилки со сложным качанием рекомендуется применять для мелкого и среднего дробления, а также для дробления вязких материалов. Благодаря принудительному выталкиванию дробленого материала из разгрузочной щели щековые дробилки со сложным качанием щеки имеют более высокую производительность.
На обогатительных фабриках щековые дробилки применяются для крупного дробления. Эти дробилки не могут работать под завалом и поэтому для кусков горной породы сооружают приемные бункера небольшой емкости. Из приемного бункера в дробилку горная порода равномерно подается пластинчатым питателем. Иногда перед дробилкой устанавливают колосниковый грохот. Пластинчатый питатель подает материал на грохот и в дробилку поступает только надрешетный продукт. Дробленый продукт обычно разгружается из дробилки на ленточный конвейер, который транспортирует его в следующую стадию дробления. Щековые дробилки устанавливают на фундаментах, не связанных с фундаментами здания.
Максимальная степень дробления, которую можно достичь в щековых дробилках, составляет 8. Обычно же дробилки работают при степенях дробления от 3 до 5.
Типоразмер щековых дробилок характеризуется шириной приемного отверстия В и длиной камеры дробления L и обозначается В х L (мм). Типоразмеры щековых дробилок с простым качанием подвижной щеки (ЩДП): 900 х 1200; 1200 х 1500; 1500 х 2100; типоразмеры щековых дробилок со сложным движением щеки: 160 х 250; 250 х 400; 250 х 900; 400 х 900; 600 х 900. Соответственно дробилки обозначаются, например: ЩДП-9 х 12; ЩДС-1,6 х2,5; где цифры обозначают ширину В и длину L приемной камеры в дециметрах.
Преимуществами ЩДП являются возможность осуществления дробления материалов любой прочности, т.к. конструкция с верхним подвесом подвижной щеки создает максимальное усилие в верхней части рабочего пространства при малом ходе сжатия; в несколько раз больший срок службы дробящих плит по сравнению с ЩДС. Характерной особенностью современных ЩДП является использование дробящих поверхностей с криволинейным продольным профилем. Это позволяет, при наличии в материале большого количества мелких кусков, сразу проваливающихся в нижние зоны камеры дробления, существенно уменьшить забивание дробилки, снизить износ футеровочных плит и повысить производительность дробилки при том же расходе энергии.
Дробилки ЩДС позволяют получать более равномерный по крупности конечный дробленый продукт и работают с большей степенью дробления, чем дробилки ЩДП. Недостатком дробилок ЩДС является то, что усилия дробления передаются непосредственно эксцентрику приводного вала, а это затрудняет создание дробилок больших размеров и применение их для крупного дробления, Кроме того, при сложном движении подвижной щеки материал подвергается не только раздавливанию, но и истиранию и резанию, что приводит к образованию большого количества мелочи и вызывает повышенный износ дробящих плит.
Конусные дробилки
Конусные дробилки получили широкое распространение в горной промышленности для крупного, среднего и мелкого дробления руд, горно-химического сырья, строительных горных пород. Они являются высокопроизводительными машинами непрерывного действия. Дробление (рис. 2.4) осуществляется в кольцевом пространстве между неподвижным 1 и подвижным 2 дробящими конусами.
Рис. 2.4. Принцип действия и кинематические схемы конусных дробилок:
а – крупного дробления; б – среднего и мелкого дробления;
1 – неподвижный конус; 2 – подвижный конус; 3 – вал; 4 – эксцентриковый
стакан; 5 – подпятник; 6 - подшипник; 7 – коническая зубчатая передача;
8 – привод; 9 – подвеска на траверсе; 10 – предохранительные пружины
Подвижный конус, как бы обкатывая внутреннюю поверхность неподвижного конуса, производит дробление крупных кусков в результате их раздавливания, а также частично истирания и разламывания вследствие криволинейной формы дробящих поверхностей. Исходный материал загружается сверху в пространство между подвижным и неподвижным конусами, а разгрузка дробленого продукта производится вниз под дробилку через щель во время отхода подвижного конуса от неподвижного.
Конусные дробилки в зависимости от назначения подразделяются на дробилки крупного (ККД) (см. рис. 2.4, а), среднего (КСД) и мелкого (КМД) дробления (см. рис. 2.4, б).
Подвижный дробящий конус 2 у дробилки крупного дробления жестко закреплен на валу 3. Верхний конец вала шарнирно подвешен к верхней траверсе 9, а нижний вставлен в эксцентриковый стакан 4. При вращении эксцентрикового стакана через коническую зубчатую передачу 7 ось вала описывает коническую поверхность с вершиной в точке О. Ось вала образует с геометрической осью
дробилки некоторый небольшой угол, называемый углом гирации (процессии).
Подвижный конус дробилок КСД и КМД опирается на сферический подпятник 5. Вал 3 подвижного конуса не имеет верхнего крепления и поэтому эти дробилки называются дробилками с консольным валом. Эксцентриковый стакан получает вращение от приводного устройства 8 через зубчатую коническую передачу, при этом подвижный конус получает качательное (гирационное) движение.
Подвижный конус как бы перекатывается по неподвижному (через слой материала), вследствие чего происходит непрерывное дробление материала. Поэтому в любой момент времени происходит сближение какого-либо участка поверхности подвижного конуса с неподвижным и осуществляется дробление материала в этом месте, в то время как на диаметрально противоположной стороне подвижный конус отходит от неподвижного, тем самым побуждая разгрузку дробленого продукта под действием силы тяжести.
Основными технологическими характеристиками щековых дробилок являются: угол захвата , оптимальная частота вращения эксцентрикового стакана n опт, объемная и массовая производительность.
Угол захвата конусных дробилок, представляющий собой угол между внутренней поверхностью неподвижного и наружной поверхностью подвижного дробящего конуса, как и у щековых дробилок должен быть меньше двойного угла трения, т.е.
2
.
При оптимальной частоте n опт вращения эксцентрикового стакана достигается максимальная производительность дробилки. Такую частоту имеем, если время половины оборота эксцентрикового стакана равно времени свободного падения куска дробленого продукта с максимально возможной высоты h до уровня разгрузочного отверстия
. (2.14)
Т.к. ход подвижного конуса
е = S 2 – S 1, (2.15)
где S 2 – максимальное раскрытие выходного отверстия (процесс разгрузки) «параллельной зоны»;
S 1 – минимальное раскрытие выходного отверстия (процесс дробления), то
, (2.16)
где 1 – угол наклона образующей внутреннего подвижного конуса к вертикали;
2 – угол наклона образующей неподвижного конуса к вертикали.
С учетом (2.15) и (2.16) из уравнения (2.14) получим
(2.17)
или
. (2.18)
За один оборот дробящего конуса из дробилки разгрузится объем материала V 1, равный произведению площади кольца F с трапецеидальным поперечным сечением на среднюю длину этого кольца 2 , где R – расстояние от оси вращения до центра тяжести трапеции
, (2.19)
где .
Тогда
. (2.20)
Объемная производительность конусной дробилки (м3/ч)
(2.21)
где n – частота вращения эксцентрикового стакана, мин-1.
Массовая производительность конусной дробилки (т/ч)
(2.22)
где – насыпная плотность дробимого материала, т/м3;
k – коэффициент разрыхления материала при выходе из дробилки, k = 0,25–0,70.
Камеры дробления конусных дробилок крупного, среднего и мелкого дробления различаются конфигурацией. У дробилок для крупного дробления усеченный конус чаши обращен большим основанием вверх, а у дробилок для среднего и мелкого дробления – вниз. Дробящие конусы у дробилок всех типов обращены большими основаниями вниз, но у дробилок для крупного дробления конус крутой, а у дробилок для среднего и мелкого дробления – пологий. Камера дробилок крупного дробления приспособлена к приему крупных кусков, поэтому кольцевое пространство между подвижным и неподвижным конусами расширяется в верхней части. Максимальный диаметр дробящего куска примерно в 1,5 раза превышает ширину приемного отверстия дробилки, а ширина разгрузочной щели составляет 0,1–0,2 от его размера.
Профиль рабочего пространства конусных дробилок для среднего и мелкого дробления предусматривает прием более мелкого материала и позволяет выдавать относительно равномерный по крупности дробленый продукт. Дробилки мелкого дробления по сравнению с дробилками среднего дробления имеют большую длину «параллельной зоны» между конусами и меньшую высоту дробящего конуса, поэтому их иногда называют короткоконусными. Производительность дробилок среднего и мелкого дробления пропорциональна площади разгрузочной щели. Учитывая небольшую ее ширину, стремятся увеличивать ее длину за счет применения пологих дробящих конусов.
Конусные дробилки крупного дробления отличаются от дробилок среднего и мелкого дробления величиной эксцентриситета стакана, определяющего амплитуду качаний дробящего конуса. У дробилок крупного дробления эксцентриситет стакана меньше 25 мм, а у дробилок среднего и мелкого дробления – больше 100 мм. Степень дробления у конусных дробилок крупного дробления составляет 3–5, у дробилок среднего и мелкого дробления – от 4 до 7.
Дробилки крупного дробления характеризуются шириной приемного отверстия (500; 900; 1200 и 1500 мм). Типоразмеры обозначаются ККД-500; ККД-900; ККД-1200; ККД-1500. Ширина разгрузочной щели составляет от 75 до 300 мм. В зависимости от типоразмера дробилок, физических свойств горной породы (крупности, крепости, влажности) производительность ККД колеблется от 150 до 2600 м3/ч. Типоразмеры дробилок среднего и мелкого дробления характеризуются диаметром основания подвижного конуса (Д = 600; 900; 1200; 1750; 2200; 2500 и 3000 мм) и обозначаются, например, КСД-900; КСД-2200; КМД-1750; КМД-2200. Производительность дробилок среднего дробления колеблется от 20 до 1500 м3/ч, производительность дробилок мелкого дробления – от 20 до 1000 м3/ч при крупности загружаемых кусков материала 40–300 и 40–110 мм соответственно.
Конусные дробилки характеризуются высокой производительностью, сравнительно низким удельным расходом энергии и достаточно равномерным по крупности дробленым продуктом.
К недостаткам конусных дробилок относится сложность конструкции, затрудняющая их ремонт и обслуживание, а также неудовлетворительная их работа при дроблении глинистых и вязких материалов, которые быстро забивают (запрессовывают) рабочую зону и разгрузочную щель дробилки.
Валковые дробилки
В валковых дробилках материал дробится между двумя валками 1 вращающимися навстречу друг другу (рис. 2.5). Один из них обычно вращается в неподвижно закрепленных подшипниках 5, другой – в подвижных 3, удерживаемых в направляющих спиральными амортизирующими пружинами 4, предохраняющими дробилку от поломки при попадании в нее недробимых предметов. Дробимый материал, поступающий в пространство между валками сверху, затягивается ими и дробится. Дробленый продукт под действием силы тяжести выпадает вниз.
Рис. 2.5. Схема двухвалковой дробилки:
1 – валок; 2 – корпус; 3 – подвижный подшипник;
4 – предохранительная пружина; 5 – неподвижный подшипник
Положение перемещающихся подшипников 4 фиксируется с помощью тяг, гаек и прокладок. Предварительно сжатые пружины компенсируют нормальные усилия, возникающие при дроблении материала. При попадании недробимых материалов в зазор между валками пружины 4 сжимаются и подвижные подшипники отодвигаются, что предотвращает остановку дробилки. Ширина щели S между валками изменяется регулировочными болтами или специальными прокладками.
Валковые дробилки бывают одно -, двух -, трех - и четырехвалковые. В четырехвалковых дробилках одна пара валков расположена над другой, т.е. эта дробилка может рассматриваться как две двухвалковые дробилки (две стадии дробления), смонтированные в один корпус. У одновалковых дробилок другая рабочая поверхность является неподвижной.
Валковые дробилки разделяются на дробилки с гладкими, рифлеными, ребристыми и зубчатыми валками. Часто применяют сочетание различных поверхностей.
Дробилки с гладкими валками работают по принципу раздавливания и ограниченного истирания при затягивании исходного материала в щель между валками. Однократность сжатия кусков материала при попадании между валками обуславливает малый выход мелочи в дробленом продукте. Эти дробилки не переизмельчают материал, поэтому широко применяются для среднего и мелкого дробления материалов в основном средней прочности ( 150 МПа).
Дробящее действие валковых дробилок с зубчатыми валками – раскалывание, разламывание, раздавливание. Характер дробящего действия дробилок с зубчатыми валками соответствует дроблению хрупких и мягких пород (уголь, соль, кокс и т.д.) с пределом прочности = 80 МПа.
Важной характеристикой для работы валковых дробилок является угол захвата . Углом захвата
валковых дробилок с гладкими валками является угол, образованный двумя касательными, проведенными к поверхностям валков в точках соприкосновения с дробимым куском. Его значение должно быть не более двойного угла трения
, т.е.
. (2.23)
При одинаковом диаметре Д рифленые и зубчатые валки могут захватывать более крупные куски материала, чем гладкие. Так, если Д – диаметр валка, d – диаметр куска материала, то при дроблении пород средней прочности соотношение Д /d для гладких валков составляет 17–20, для рифленых – 10, для зубчатых – 2–6.
Валковые дробилки имеют диаметр валка 400–1500 мм и длину, равную 0,4–1,0 диаметра (длина зубчатых валков может быть больше, чем диаметр). Средняя степень дробления для всех видов валковых дробилок составляет 3–6.
Производительность валковых дробилок пропорциональна диаметру Д, длине L, скорости вращения валков n и ширине разгрузочной щели S между ними. Можно представить, что при непрерывной подаче в валковую дробилку материала из нее будет выходить как бы непрерывная лента дробленого продукта. Объем материала, выходящего из дробилки за один оборот валков V 1, соответствует объему прямоугольного параллелепипеда с основанием, равным площади щели между валками, и высотой, равной длине окружности валка
м3/об, (2.24)
где Д – диаметр валка, м;
L – длина валка, м;
S – ширина щели, м.
Объемная производительность
м3/ч, (2.25)
где n – частота вращения валков, мин-1.
Массовая производительность
т/ч, (2.26)
где – насыпная плотность дробимого материала, т/м3;
k – коэффициент разрыхления дробленого материала при выходе из дробилки. Для прочных материалов k = 0,2–0,3; для хрупких k = 0,4; для рыхлых, влажных и вязких k = 0,5–0,6.
Частоту вращения валков (с-1) можно определить по формуле
(2.27)
где d – диаметр куска исходного материала, м;
Д – диаметр валка, м;
f – коэффициент трения материала о валок; f = 0,3–0,45.
Валковые дробилки предназначены для мелкого и среднего дробления материалов малой и средней прочности. Они отличаются малыми затратами энергии, так как в процессе работы осуществляют только однократное воздействие. Они не переизмельчают дробленый продукт. Применение скребков дает возможность производить дробление вязких и влажных материалов в дробилках с гладкими валками. К другим достоинствам валковых дробилок относятся простота и компактность конструкции, надежность в эксплуатации; к недостаткам – малая производительность и непригодность для дробления очень твердых горных пород.
Дата добавления: 2015-12-19; просмотров: 54; Мы поможем в написании вашей работы! |
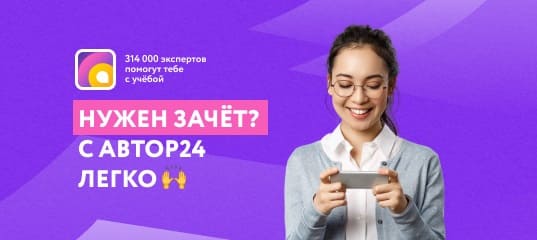
Мы поможем в написании ваших работ!