Влияние обработки давлением на структуру и свойства металла
В зависимости от температурно-скоростных условий деформирования различают холодную и горячую деформацию.
Холодная деформация характеризуется изменением формы зерен, которые вытягиваются в направлении наиболее интенсивного течения металла (рис. 3, а). При холодной деформации формоизменение сопровождается изменением механических и физико-химических свойств металла. Это явление называют упрочнением (наклепом). Изменение механических свойств состоит в том, что при холодной пластической деформации по мере ее увеличения возрастают характеристики прочности, в то время как характеристики пластичности снижаются. Металл становится более твердым, но менее пластичным. Упрочнение возникает вследствие поворота плоскостей скольжения, увеличения искажений кристаллической решетки в процессе холодного деформирования (накопления дислокаций у границ зерен).
Изменения, внесенные холодной деформацией в структуру и свойства металла, не необратимы. Они могут быть устранены, например, с помощью термической обработки (отжигом). В этом случае происходит внутренняя перестройка, при которой за счет дополнительной тепловой энергии, увеличивающей подвижность атомов, в твердом металле без фазовых превращений из множества центров растут новые зерна, заменяющие собой вытянутые, деформированные зерна. Так как в равномерном температурном поле скорость роста зерен по всем направлениям одинакова, то новые зерна, появившиеся взамен деформированных, имеют примерно одинаковые размеры по всем направлениям.
|
|
![]() | Рис. 3. Схемы изменения микроструктуры металла при деформации: а — холодной; б — горячей |
Явление зарождения и роста новых равноосных зерен взамен деформированных, вытянутых, происходящее при определенных температурах, называется рекристаллизацией. Для чистых металлов рекристаллизация начинается при абсолютной температуре, равной 0,4 абсолютной температуры плавления металла. Рекристаллизация протекает с определенной скоростью, причем время, требуемое для рекристаллизации, тем меньше, чем выше температура нагрева деформированной заготовки.
При температурах ниже температуры начала рекристаллизации, наблюдается явление, называемое возвратом. При возврате (отдыхе) форма и размеры деформированных, вытянутых зерен не изменяются, но частично снимаются остаточные напряжения. Эти напряжения возникают из-за неоднородного нагрева или охлаждения (при литье и обработке давлением), неоднородности распределения деформаций при пластическом деформировании и т. д. Остаточные напряжения создают системы взаимно уравновешивающихся сил и находятся в заготовке, не нагруженной внешними силами. Снятие остаточных напряжений при возврате почти не изменяет механических свойств металла, влияет на некоторые его физико-химические свойства. Так, например, в результате возврата значительно повышается электрическая проводимость, сопротивление коррозии холоднодеформированного металла.
|
|
Формоизменение заготовки при температуре выше температуры рекристаллизации сопровождается одновременным протеканием упрочнения и рекристаллизации.
Горячей деформацией называют деформацию, характеризуются таким соотношением скоростей деформирования и рекристаллизации, при котором рекристаллизация успевает произойти во всем объеме заготовки и микроструктура после обработки давлением оказывается равноосной, без следов упрочнения (рис. 3, б).
Чтобы обеспечить условия протекания горячей деформации, приходится с увеличением ее скорости повышать температуру нагрева заготовки (для увеличения скорости рекристаллизации). Если металл по окончании деформации имеет структуру, не полностью рекристаллизованную, со следами упрочнения, то такая реформация называется неполной горячей деформацией. Неполная горячая деформация приводит к получению неоднородной структуры, снижению механических свойств и пластичности, поэтому обычно нежелательна.
|
|
При горячей деформации сопротивление деформированию примерно в 10 раз меньше, чем при холодной деформации, а отсутствие упрочнения приводит к тому, что сопротивление деформированию (предел текучести) незначительно изменяется в процессе обработки давлением. Этим обстоятельством объясняется в основном то, что горячую обработку применяют для изготовления крупных деталей, так как при этом требуются меньшие усилия деформирования (менее мощное оборудование).
Следует учитывать, что при обработке давлением заготовок малых размеров (малой толщины) трудно выдержать необходимые температурные условия ввиду быстрого их охлаждения на воздухе и от контакта с более холодным инструментом.
При горячей деформации пластичность металла выше, чем при холодной деформации. Поэтому горячую деформацию целесообразно применять при обработке труднодеформируемых, малопластичных металлов и сплавов, а также заготовок из литого металла (слитков). В то же время при горячей деформации окисление заготовки более интенсивно (на поверхности образуется слой окалины), что ухудшает качество поверхности и точность получаемых размеров.
|
|
![]() | ![]() | ||
Рис. 4. Макроструктура металла после обработки давлением | |||
Холодная деформация без нагрева заготовки позволяет получать большую точность размеров и лучшее качество поверхности по сравнению с обработкой давлением при достаточно высоких температурах. Отметим, что обработка давлением без специального нагрева заготовки позволяет сократить продолжительность технологического цикла, облегчает использование средств механизации и автоматизации и повышает производительность труда.
Влияние холодной деформации на свойства металла можно использовать для получения наилучших эксплуатационных свойств деталей, а управление изменением свойств в требуемом направлении и на желаемую величину может быть достигнуто выбором рационального сочетания холодной и горячей деформации, а также числа и режимов термических обработок в процессе изготовления детали.
Исходной заготовкой для начальных процессов обработки металлов давлением (прокатки, прессования) является слиток. Кристаллическое строение слитка неоднородно (кристаллиты различных размеров и форм). Кроме того, в нем имеется пористость, тазовые пузыри и т. п. Обработка давлением слитка при нагреве его до достаточно высоких температур приводит к деформации кристаллитов и частичной заварке пор и раковин. Таким образом, при обработке давлением слитка может увеличиться и плотность металла.
В результате деформации кристаллитов и последующей рекристаллизации металл получает мелкозернистое строение, т. е. размеры зерен после рекристаллизации исчисляются в сотых или десятых долях миллиметра, причем эти размеры примерно одинаковы по всем направлениям (равноосная структура).
Если слиток загрязнен неметаллическими включениями, обычно располагающимися по границам кристаллитов, то в результате обработки давлением неметаллические включения вытягиваются в виде волокон по направлению наиболее интенсивного течения металла. Эти волокна выявляются травлением и видны невооруженным глазом в форме так называемой волокнистой макроструктуры (рис. 4, а). Полученная в результате обработки давлением литого металла волокнистая макроструктура не может быть разрушена ни термической обработкой, ни последующей обработкой давлением. Последняя зависимости от характера деформирования может изменить лишь направление и форму волокон макроструктуры.
Металл с явно выраженной волокнистой макроструктурой характеризуется анизотропией (векториальностью) механических свойств. При этом характеристики прочности (предел текучести, временное сопротивление и др.) в разных направлениях отличаются незначительно, а характеристики пластичности (относительное удлинение, ударная вязкость и др.) вдоль волокон выше, чем поперек их.
Так как направление волокон зависит от характера деформирования заготовки, то в готовой детали желательно получить такое расположение волокон, при котором она имела бы наилучшие свойства. При этом общие рекомендации следующие: необходимо, чтобы наибольшие растягивающие напряжения, возникающие в деталях в процессе работы, были направлены вдоль волокон, а если какой-либо элемент этой детали работает на срез, то желательно, чтобы перерезывающие силы действовали поперек волокон; необходимо чтобы волокна подходили к наружным поверхностям детали по касательной и не перерезались наружными поверхностями детали. Выполнение этих требований не только повышает надежность детали (в том числе и при динамическом нагружении), но и улучшает другие эксплуатационные характеристики, например сопротивление истиранию.
Возможность воздействия обработкой давлением на расположение волокон, а следовательно, и на свойства деталей можно иллюстрировать следующим примером. В зубчатом колесе, изготовленном резанием из прутка (рис. 4, б), растягивающие напряжения, возникающие при изгибе зуба 1действием сопряженного колеса, направлены поперек волокон, что понижает их надежность. При горячей штамповке зубчатого колеса из полосы (рис. 4, в) волокна по-разному ориентированы в различных зубьях относительно наибольших растягивающих напряжений: в зубе 1 — вдоль волокон, а в зубе 2 — поперек. Следовательно, зубья оказываются неравнопрочными. При изготовлении зубчатого колеса осадкой (рис; 4, г) из отрезка прутка круглого сечения волокна получают почти радиальное направление. В этом случае все зубья равнопрочны, а наибольшие растягивающие напряжения, возникающие при изгибе, направлены почти вдоль волокон.
Дата добавления: 2015-12-17; просмотров: 21; Мы поможем в написании вашей работы! |
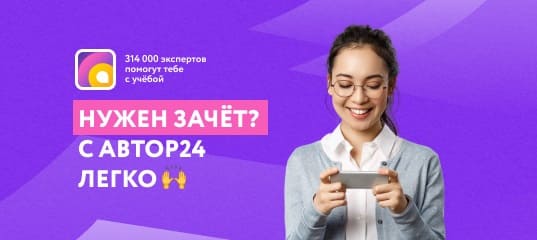
Мы поможем в написании ваших работ!