Очистка бум. Массы. Побготовка бум. Массы к отливу.
Нередко перед отливом бумаги на бумагоделательной машине исходную бумажную массу отрегулированной концентрации из машинного бассейна через переливной бачок постоянного напора направляют для окончательного размола на коническую или дисковую мельницы, устанавливаемые не в размольно подготовительном отделе, а в начале зала бумагоделательных машин.
Большей частью назначение такого размола — рафинирование массы, т. е. разбивка отдельных сохранившихся пучков волокон и выравнивание степени помола всей массы с незначительным повышением общей степени помола массы (на 1 — 3 °ШР).
В отдельных, сравнительно редких, случаях при выработке некоторых технических видов бумаги размалывающие мельницы устанавливаются перед бумагоделательной машиной для осуществления основного непрерывного размола массы при частичной или полной ликвидации размольно-подготовительного отдела. В этих случаях устанавливаются последовательно или параллельно несколько мельниц.
Для осуществления последующей операции очистки бумажной массы от сора минерального и растительного происхождения необходимо прежде всего сильно разбавить водой бумажную массу, имеющую концентрацию в машинном бассейне 2,5—3,5 % и при этой же концентрации пропущенную через рафинирующую мельницу. Разбавление массы осуществляется оборотной водой от бумагоделательной машины и необходимо потому, что из относительно густой массы трудно удалить загрязнения. Кроме того, разбавление массы необходимо и для последующего отлива бумаги и получения ее с однородной структурой (с безоблачным просветом). В случаях относительно небольших производственных потоков массы ее разбавление оборотной водой производят в дозировочном бачке. На современных предприятиях обычно разбавление массы осуществляют с использованием смесительного насоса. В настоящее время эта схема разбавления массы из-за ее эксплуатационных преимуществ (легкая регулировка при интенсивном перемешивании массы с водой и равномерном разбавлении) получила распространение не только на предприятиях большой производственной мощности, но и на предприятиях с небольшими производственными потоками массы.
|
|
Смесительный насос устанавливают на первом этаже с таким расчетом, чтобы вода из сборника оборотной воды поступала во всасывающий трубопровод насоса самотеком под постоянным напором. В этот же трубопровод поступает масса из бака постоянного уровня. Количество поступающей массы регулируется задвижкой. Эта схема имеет и некоторые модификации с регулированием степени разбавления массы задвижкой на нагнетательном трубопроводе или же с регулированием подачи оборотной воды на обводном трубопроводе между нагнетательным и всасывающим трубопроводами.
|
|
При выработке различных видов бумаги концентрация массы в каждом случае различна и может отличаться между собой в очень больших пределах (от 0,1 % при выработке тончайших видов бумаги до 1,8% при выработке картона). 7. Очистка бумажной массы от сора необходима прежде всего для повышения качества изготовляемой бумаги. Кроме того, посторонние включения в бумажной массе служат одной из причин обрывов бумажного полотна при его изготовлении па бумагоделательной машине.
Виды сора в бумажной массе различны, как и различны причины его появления. Сор минерального происхождения попадает в бумажную массу в виде песка от дефибрерных камней и каменной гарнитуры размалывающих аппаратов. Металлические включения могут попасть от ножей размалывающих аппаратов, а также из недостаточно очищенной макулатуры или тряпичной массы (скрепки, кнопки и пр.). Загрязнения растительного происхождения (крупная костра, щепочки, кусочки коры, сгустки массы и пр.) могут появиться из полуфабрикатов при их плохой очистке. Кроме того, различного рода загрязнения могут попасть в бумажную массу с наполнителями и сернокислым алюминием, производственной водой, оборотным браком и из недостаточно чисто промытого оборудования и коммуникаций. Moгут попасть в бумажную массу и случайные посторонние включения (кусочки штукатурки или резины от конвейерных лент и пр.).
|
|
Особый вид загрязнений представляет собой слизь — скопление микроорганизмов (бактерий, грибов, водорослей) и продуктов их жизнедеятельности. Микроорганизмы поступают в производственные потоки со свежей водой и в условиях подходящей питательной среды быстро развиваются. В виде обрастаний они покрывают внутренние поверхности оборудования и трубопроводов, загрязняя потоки бумажной массы и оборотной воды. Бороться со слизеобразованнем методами сортирования массы нельзя, так как слизь проходит через ячейки сита или отверстия любой аппаратуры для сортирования бумажной массы. Действенные методы борьбы со слизеобразованием заключаются в тщательной и регулярной промывке оборудования и трубопроводов с периодическим использованием этом соответствующих антисептических средств.
Ранее применявшейся простейшей аппаратурой для отделения из бумажной массы посторонних включений большей плотности, чем плотность растительных волокон, была песочница— открытый деревянный или железобетонный желоб с наклонно установленными по ходу движения массы перегородками. При медленном движении массы над перегородками песочницы тяжелые включения осаждались на дне, на котором иногда были смонтированы электромагниты, облегчающие выделение из потока массы некоторых металлических включений. Ввиду малой производительности, громоздкости и необходимости периодических очисток это оборудование в настоящее время не применяется.
|
|
Для очистки бумажной массы от включений большей плотности, чем плотность растительных волокон, в настоящее время применяется аппаратура, в которой очистка осуществляется под действием центробежной силы.
Одним из аппаратов, основанных на этом принципе, является центробежный очиститель, применяемый перед бумагоделательными машинами сравнительно небольшой производительности и при выработке ограниченного ассортимента видов бумаги (конденсаторная и некоторые другие). Бумажную массу, содержащую минеральный наполнитель, через центробежный очиститель не пропускают.
Масса, поступающая сверху аппарата, крыльчаткой отбрасывается к стенкам внутреннего барабана. Отходы, отделяющиеся под действием центробежной силы, удаляются через патрубок, а предварительно очищенная масса через отверстие поступает из внутреннего барабана в наружный, где она дополнительно очищается и удаляется через желоб Производительность центробежного очистителя 60 м3/ч.
Большое распространение для очистки бумажной массы приобрели так называемые вихревые очистители, в которых очистка массы производится также под действием центробежной силы. Эти аппараты, занимающие мало места, устанавливают обычно батареями в одну, две и три ступени. Известны два основных типа вихревых очистителей: фортрапы и центриклинеры. Первые имеют цилиндрическую форму и две последовательно установленные на некотором расстоянии друг от друга резиновые диафрагмы, через отверстия которых вниз проходят отходы, а вверх по центральной оси аппарата поднимается очищенная масса. Центриклинеры имеют коническую форму, облегчающую процесс очистки массы, и в них отсутствуют диафрагмы. Благодаря простоте своего устройства и эффективной очистке бумажной массы центриклинеры вытеснили фортрапы и применяются повсеместно не только для очистки бумажной массы, но и для очистки полуфабрикатов (целлюлозы и древесной массы). Центриклинер представляет собой трубу конической формы При этом масса приобретает завихрения и движется вниз по спирали. Тяжелые частицы под влиянием центробежной силы отбрасываются к стенкам аппарата. Коническая форма трубы способствует развитию в ее нижней части большей центробежной силы, благодаря чему увеличивается эффект очистки массы Отходы удаляются по внутренней стенке трубы из нижней части аппарата. В центральной ее части создается зона разрежения, благодаря которой очищенная масса поднимается вверх и удаляется из аппарата через патрубок.
НАПОРНЫЕ ЯЩИКИ.
Напускные устройства бумагоделательных машин по своей конструкции существенно различаются между собой в зависимости от скорости машины. Дело в том, что качество изготовляемой бумаги в значительной степени зависит от относительной скорости поступления массы на сетку бумагоделательной машины по сравнению со скоростью движения сетки. Если скорость массы значительно меньше скорости сетки, волокна нижней части массного потока, касаясь каким-либо своим концом сетки, увлекаются последней и вытягиваются в машинном направлении, т. е. в направлении хода сетки. Вследствие этого изготовляемая бумага имеет ярко выраженную ориентацию волокон в машинном направлении преимущественно на своей нижней (сеточной) стороне. Последующие слои волокон касаются уже не сетки, а волокон нижнего слоя, не успевших еще полностью приобрес!и скорость сетки. Поэтому ориентация волокон в машинном направлении в этих слоях хотя и имеет место, но менее выражена. Еще менее выражена она на верхней поверхности бумажного полотна. Чем толще изготовляемая бумага, тем большее различие в ориентации волокон на ее верхней и сеточной сторонах.
Повышенная ориентация волокон в машинном направлении приводит к анизотропии в прочностных свойствах бумаги: существенно более высокой прочности бумаги в ее машинном направлении по сравнению с прочностью в поперечном направлении. Для большинства видов бумаги желательно небольшое различие в ориентации волокон и соответственно в прочности по машинному и поперечному направлениям. Поэтому в большинстве случаев необходимо, чтобы скорость поступления массы на сетку была бы примерно равна скорости сетки при допустимом отставании скорости массы от скорости сетки на 5—10%. Только в сравнительно редких случаях (при выработке шпагатной бумаги, бумаги для телеграфной ленты и пр.), когда нужна повышенная прочность бумаги именно в машинном направлении, скорость поступления массы на сетку существенно меньше скорости сетки. Превышение скорости массы над скоростью сетки ведет к наплывам массы на сетку с образованием на ней поперечных волн и к ухудшению равномерности просвета бумаги. При выработке отдельных видов бумаги, например тонкой конденсаторной, изготовляемой при низкой скорости бумагоделательной машины с длинным сеточным столом, практически невозможно создать столь малый напор массы перед выходом ее на сетку, который соответствовал бы скорости выхода массы примерно равной скорости сетки. В этом случае скорость массы несколько превышает скорость сетки. Скорость потока на самой сетке уменьшают подъемом сеточного стола в направлении от грудного вала к гауч-валу.
Скорость поступления на сетку бумагоделательной машины
ТЕХНИЧЕСКАЯ ХАРАКТЕРИСТИКА, ОСНОВНЫЕ ЧАСТИ БДМ…
Для изготовления бумаги используются различные типы бумагоделательных машин, различающиеся между собой по принципу образования бумажного полотна: столовые (плоскосеточные), цилиндровые (круглосуточные), комбинированные, двухсеточные и их модификации, машины сухого способа изготовления бумаги. Тем не менее основным типом применяемых бумагоделательных машин до сих пор остается столовая машина.
По сравнению с первой бумагоделательной машиной Робера увеличилась ширина, скорость и, следовательно, производительность современных столовых машин, усовершенствовались конструктивные особенности сеточного стола, добавились прессовая, сушильная и отделочная части машины, привод машины теперь осуществляется от электродвигателей. Однако не изменился основной принцип изготовления бумаги из водной суспензии соответствующим образом обработанных растительных волокон, осаждаемых на непрерывно движущейся плоской сетке.
Если машина Робера имела ширину 0,64 м, скорость 10— 12 м/мин и производительность не более 0,5 i бумаги в сутки, то современные столовые бумагоделательные машины при ширине до 8—10 м могут достичь скорости до 1000—1500 м/мин и производительности до 500 т и более бумаги в сутки. Бумагоделательная машина Робера имела длину 2,5 м, современные столовые машины 120—-130 м. ин. Если принять: В —необрезная ширина бумаги на бумагоделательной машине, м; v— средняя (рабочая) скорость машины, м/мин, то очевидно, что каждую минуту бумагоделательная машина может изготовить Вv квадратных метров бумаги или 0,001Bvq кг бумаги, где q — масса 1 м2 бумаги, г. Cooт ветственно за 1 ч машина может изготовить 0,06Вvq кг бумаги. Однако 1 выбранный час непрерывной работы машины дает недостаточную информацию о ее практической работе, в процессе которой есть обязательные остановки машины для проведения необходимых ремонтных работ, а также смены одежды машины (сетки и сукон). Поэтому обычно интерес представляет хотя бы суточная работа машин с К1 — фактическим числом часов работы машины в сутки Здесь следует иметь в виду, что K1 является фактическим числом часов работы машины в сугки, средним за длительный период времени работы машины, а не за отдельно выбранные сутки, в течение которых могут и не производиться ремонтные или другие работы, требующие остановки машины. При проектировании обычно принимается К\ равным 22,5—23 ч в сутки.
Таким образом, суточная производительность бумагоделательных машин составит 0,06 BvqK1, кг, при условии, что в процессе выработки не будет брака и обрывов бумажного полотна на машине, вызывающих холостой ход машины, т. е, времени работы машины без продукции на накате (времени, необходимого для ликвидации обрывов бумажного полотна). Указанная производительность называется суточной производительностью машины брутто. Обозначим коэффициент производительности машины, учитывающий ее холостой ход,— К2 и коэффициент производительности машины, учитывающий брак на машине,— К3,- Обычно в зависимости от вида вырабатываемой бумаги, технического состояния бумагоделательной машины и квалификации обслуживающего персонала холостой ход машины составляет 2—5 % от времени всей работы машины и, следовательно, K2 соответственно равняется 0,98—0,95.
Брак в производстве бумаги в зависимости от тех же причин, включая потери бумаги при обрезании кромок на перемотно-резательном станке, при суперкаландрировании и пр. составляет от 2 до 12 % и соответственно /G, равняется 0,98—0,88.
Очевидно, что суточная производительность бумаги нетто Р, кг/сут, определится по формуле:
Эта суточная производительность нетто соответствует количеству товарной продукции. Выработка бумаги брутто на накате определяется по той же формуле, но соответствующие коэффициенты учитывают холостой ход и брак на машине (без учета соответствующих потерь при различных операциях в отделочном цехе).
Дата добавления: 2015-12-17; просмотров: 19; Мы поможем в написании вашей работы! |
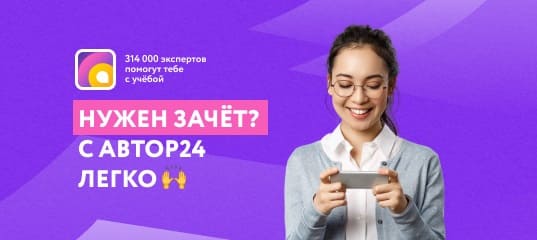
Мы поможем в написании ваших работ!