Гранулометрический анализ и флотация твердого сырья».
Перед химической переработкой сырье подвергают предварительной подготовке с целью придания ему состава и свойств, необходимых для осуществления химико-технологического процесса, повышения концентрации полезного компонента, понижения содержания влаги и вредных примесей, достижения определенной дисперсности. Важнейшими операциями подготовки твердого сырья являются измельчение, классификация и обогащение. Для оценки степени измельчения сырья определяют содержание в нем частиц различных размеров – гранулометрический состав.
Наиболее распространенным методом обогащения твердого сырья является флотация. Флотационное обогащение представляет физико-химический процесс разделения компонентов сырья (полезного материала и пустой породы), основанное на различной смачиваемости их.
Смачиваемость минералов характеризуется величиной краевого угла смачивания Q вдоль границы раздела фаз «твердое тело – жидкость – воздух». В соответствии с величиной угла смачивания минералы подразделяются на несмачиваемые (гидрофобные), для которых Q> 900 и смачиваемые (гидрофильные), для которых Q<900.
Так как силы поверхностного натяжения стремятся выровнять уровень жидкости, то вследствие различия углов смачивания частицы гидрофобных материалов всплывают с пузырьками воздуха в виде пены и могут быть собраны, а частицы гидрофильных материалов погружаются в жидкость. Таким образом, в результате флотации получают один или несколько флотационных концентратов, содержащих полезные компоненты, извлеченные из сырья, и флотационные хвосты, состоящие, главным образом, из пустой породы.
|
|
Эффективность флотации, полнота выделения полезного компонента из сырья зависит от ряда факторов. К ним относятся:
1. Природа и состав флотируемого сырья, в том числе различие в смачиваемости полезного минерала и пустой породы;
2. Дисперсность сырья; достаточная скорость и избирательность процесса достигается только при некоторой средней крупности частиц, обычно, размер частиц сырья составляет 0,1-0,3 мм;
3. Концентрация пульпы, т.е. соотношение твердой и жидкой фаз в ней; обычно колеблется в пределах от 1:5 до 1:3;
4. Состав воды, в том числе рН и природа содержащихся в ней примесей; эффективность флотации максимальна при рН=7;
5. Ассортимент, применяемых в процессе флотореагентов.
Флотореагентами называется вещества, способствующие более полному разделению полезного минерала и пустой породы, т.е. повышению эффективности флотации. Так как природные минералы, входящие в состав сырья, обычно не сильно различаются по смачиваемости, то для повышения гидрофобности полезного компонента в пульпу вводят коллекторы (собиратели) – поверхностноактивные вещества, адсорбирующиеся на его частицах и покрывающие их мономолекулярной гидрофобной пленкой. Коллекторы обладают избирательной способностью, поэтому выбор их зависит от типа флотируемого сырья.
|
|
Для создания устойчивой пены в пульпу добавляют пенообразователи (вспениватели) – ПАВ, образующие на пузырьках воздуха адсорбционную пленку, препятствующую их слипанию. В качестве вспенивателей применяют терпеновые спирты (сосновое масло), каменноугольную смолу, высокомолекулярные алифатические спирты, крезолы, алкиларилсульфонаты и другие вещества.
При флотации полиметаллических руд для выделения в виде отдельных концентратов всех полезных компонентов в пульпу вводят регуляторы, повышающие гидрофобное действие собирателей (активаторы) или способствующие повышению гидрофильности (подавители), и предотвращающие адсорбцию собирателя на поверхности минерала.
В некоторых случаях один и тот же флотореагент может играть различную роль – собиратель может быть и пенообразователем, пенообразователь проявлять собирательные свойства и т.п.
Так как флотореагенты обладают весьма высокой активностью, количество их, вводимое в пульпу, не превышает 100-200 г на тонну флотируемого сырья. Только в отдельных случаях, например при флотации углей, оно повышается до 400-3000 г на тонну.
|
|
В качестве материала для изучения флотации в работе используют сульфидные руды различных металлов (галенит, сфалерит, халькопирит, известняки (кальцит), флюорит, каменный уголь. При общей методике проведения процесса флотации, флотация этих материалов отличается природой применяемых флотореагентов и рН среды.
Флотация сульфидных руд. Цель флотации – повышение содержания сульфидов соответствующих металлов и отделение в виде флотационных хвостов железного колчедана и пустой породы. Флотореагенты – ксантогенат натия (10 г/т), а при флотации сфалерита дополнительно пенообразователь Т-66, рН= 8-9
Флотация известняков и флюорита. Цель флотации – отделение пустой породы, флотореагент – олеат натрия (100 г/т). рН = 9-9,5.
Флотация каменного угля. Цель флотации – отделение примесей сульфида железа, оксида кремния и глины. Флотореагенты – керосин (1500 г/т) и Т-66 (15 г/м3 пульпы).
1. Принцип метода:
Определение гранулометрического состава
Гранулометрический (зерновой) состав, характеризующийся распределением частиц твердого материала по их дисперсности, определяют методом ситового анализа. Для этого навеску сырья просеивают через набор сит, отличающихся величиной отверстий. При этом часть материала проходит через сито (проход), а часть остается на сите (остаток). Сита при просеивании встряхиваются вручную или с помощью механических вибраторов с частотой колебаний в вертикальной и горизонтальной плоскостях 50 Гц. Последний способ предпочтительнее, так как обеспечивает более однообразные объективные результаты.
|
|
При ситовом анализе сырье разделяется на классы (фракции). Число фракций, получаемых при просеивании через набор сит, равно
N= n +1 (3)
где n – число сит.
Точность ситового анализа зависит от допуска в изготовлении сит и степени отклонения просеиваемых частиц от шарообразной формы.
Сита изготавливают из сеток с квадратными отверстиями с размерами от 2,5 до 0,04 мм.
Крупность просеиваемых частиц характеризуется так называемым эквивалентным диаметром, принимая, что частица условно имеет форму шара с объемом, равным объему реальной частицы. Эквивалентный диаметр определяется по формуле.
Dэ = 1,24 V = 1,24 G/ (2)
где: Dэ – эквивалентный диаметр частицы, см.
G – масса частицы, г
ρ - плотность материала частицы, г/см3.
Флотационное обогащение сырья.
Минеральное или органическое сырье (сульфидная руда, каменный уголь) подвергают флотационному обогащению в лабораторной флотационной машине с механическим перемешиванием пульпы. Так как флотореагенты обладают весьма высокой активностью, количество их, вводимое в пульпу, не превышает 100-200 г на тонну флотируемого сырья. Только в отдельных случаях, например при флотации углей, оно повышается до 400-3000 г на тонну. Количество флотореагентов, вводимых в пульпу, рассчитывают по формуле
gф = | Gф 10в | (3) |
или, если реагент вводится в виде разбавленного раствора,
gф= | Gф в 10в С | (4) |
где: gф – масса вводимого флотореагента, г
Vф – объем раствора флотореагента, мл
Gф –навеска флотируемого сырья, г,
в– заданный расход флотореагента, г/т,
С – концентрация раствора флотореагента, г/мл.
Цель работы:
моделирование процесса флотационного обогащения твердого минерального и органического сырья и определение его гранулометрического состава.
Посуда и оборудование.
Прибор для ситового анализа,
сушильный шкаф,
металлическая ступка,
чашки фарфоровые,
лабораторная флотационная машина,
ступка металлическая,
ступка фарфоровая,
сито с размерами отверстий 0,05-0,1 мм,
воронка Бюхнера,
секундомер,
промывалка,
стакан стеклянный.
Реактивы
образцы анализируемого сырья: сульфидные руды (галенит, сфалерит, халькопирит),
фосфориты,
сильвинит,
каменный уголь,
ксантогенат натрия,
керосин,
олеат натрия,
сода
Ход работы:
Анализируемое сырье растирают в ступке и сушат в сушильном шкафу при 105-1100С до постоянного веса. Из полученной пробы отбирают на технических весах в фарфоровой чашке навеску 50 г с точностью 0,01 г. Прибор для просеивания собирают, следя за тем, чтобы сита были чистыми и сухими. Навеску анализируемого сырья высыпают на верхнее сито, закрывают прибор крышкой и стягивают сита скобой.
Если просеивание ведется вручную, то прибор встряхивают в наклонном положении с частотой колебаний около 150 в минуту, постепенно поворачивая его на полный оборот вокруг вертикальной оси. При механическом встряхивании прибор закрепляют на машине для встряхивания или вибраторе и включают их.
Просеивание ведут в течение 2 минут, после чего проводят контрольный опыт, подставляя под последнее сито лист глянцевой бумаги. Просеивание считают законченным, если в течение 1 минуты через сито проходит не более 0,05 г анализируемого материала.
1. Флотационное обогащение сырья.
Флотируемый материал измельчают в металлической ступке, растирают до мелкого порошка в фарфоровой ступке и просеивают через сито. Из полученной пробы отбирают навеску 2 г с точностью до 0,01 г. При флотации известняков и флюорита их предварительно отмучивают в дистиллированной воде и сушат в сушильном шкафу при 105-1100 С.
Вместо природной медной судьфидной руды для изучения процесса флотации может быть использована искусственно приготовленная смесь сульфида меди и пустой породы. Для получения сульфида меди смешивают 63 г порошкообразной меди и 32 г растертой серы, помещают смесь в тугоплавкую пробирку и нагревают до расплавления серы. После того, как бурно протекающая реакция закончится, пробирку снова нагревают при 200-3000С в течение 3-4 минут, охлаждают и обернув бумагой разбивают. Осколки стекла отделяют и полученный продукт растирают в ступке с 15 г серы. Смесь помещают в пробирку и вновь нагревают при 200-3000С в течение 5-10 минут. После охлаждения пробирки ее разбивают, отделяют стекло и растирают полученный сульфид меди (11) в ступке. Для флотации готовят смесь полученного сульфида меди (5-10г) с тонко измельченным кварцевым песком (90-95% от массы смеси). Полученную пробу обрабатывают как указано.
Дистиллированную воду доводят до заданного значения рН, растворяя в ней карбонат натрия, рН измеряют с помощью универсальной индикаторной бумаги.
Флотореагенты – ксантогенат натрия, олеат натрия и Т-66 растворяют в дистиллированной воде и готовят 1%-ный раствор их.
Во флотокамеру флотационной машины со снятой перегородкой 6 помещают 2 г флотируемого сырья, заливают 18 мл воды и рассчитанный по формуле (5) объем раствора флотореагента. Включают мешалку и перемешивают содержимое флотокамеры в течение 2 минут. Затем вставляют в камеру перегородку, включают секундомер и начинают процесс флотации. При флотации образующаяся пена с концентратом переливается в разделительное отделение камеры Б, а порода в виде хвостов оседает на дне камеры.
Через каждые 15 секунд с помощью пеносборника снимают пену, стараясь не захватывать при этом пульпу, и собирают ее в фарфоровую чашку. Процесс флотации ведут до прекращения образования пены, на что требуется, в зависимости от природы флотируемого сырья, от 3 до 5 минут. По окончании флотации чашку с концентратом переносят в сушильный шкаф, сушат при 105-1100С до постоянного веса и взвешивают с точностью до 0,01 г.
Образовавшуюся во флотокамере пульпу, содержащую хвосты, выливают в стеклянный стакан, флотокамеру обмывают из промывалки дистиллированной водой и промывные воды присоединяют к пульпе. Содержимое стакана фильтруют через предварительно взвешенный бумажный фильтр. Осадок вместе с фильтром сушат в сушильном шкафу при 105-1100С и взвешивают на технических весах с точностью до 0,01г.
Расчеты и оформление результатов:
1. Гранулометрический состав анализируемого сырья выражают в процентном содержании в нем отдельных фракций. Это содержание рассчитывается как отношение массы каждой фракции к массе навески. При этом каждая фракция обозначается верхним и нижним пределами размеров частиц: прошедших через данное сито со знаком минус, оставшихся на данном сите со знаком плюс:
Хф(-n+(n+1)) = | Gф(-n(n+1)) 100% G | (5) |
где: Хф – доля (содержание) фракции в %,
Gф – масса фракции, г
G – навеска сырья, г
N – номер сита.
Например, фракция, прошедшая через сито № 2 и оставшаяся на сите №3, обозначается как
Хф(-2+3) = | Gф(-2+3) 100% G |
Полученные данные сводят в таблицу № 1:
Таблица № 1.
№ фракции | Gф, г | Хф,% |
100% |
Результаты анализа представляют также в виде графика. Откладывая на оси абсцисс № фракции и по оси ординат долю фракции Хф.
2. Количественными показателями процесса флотации являются выход концентрата, степень обогащения сырья и степень извлечения полезного компонента из сырья.
Выход концентрата рассчитывается по формуле:
ή= | G к 100% G с | (6) |
где, Gк – масса полученного концентрата, г
G с – масса флотируемого сырья (навеска), г
Степень обогащения сырья рассчитывается по формуле
Хо = | Акк Ако | (7) |
где: Акк – содержание полезного компонента в концентрате, %
Акс – содержание полезного компонента в сырье, в %
При расчете принимают, что концентрат состоит из чистого компонента, т.е. что Акк =100%. Содержание полезного компонента в сырье, т.е. Акс задается преподавателем в начале работы.
Степень извлечения полезного компонента из сырья рассчитывается по формуле
Хи = | G кк 100% Gкс | (8) |
где: G кк – масса полезного компонента в концентрате, г
G кс – масса полезного компонента в сырье, г
Так как G кк =G к Акк и G кс= Gс Акс.
Что, подставив эти значения и значение G к из формулы (6) в формулу (8), получим
Хи = | Gк Акк 100% Gс А кс | = | Акк (G2 – G1) 100% Акс g | (8а) |
Массу флотационных хвостов рассчитывают по формуле
Gk = g2 – g1
где: g1 – масса фильтрата, г
g2 – масса фильтрата с осадком,г
Полученные данные сводят в таблицу № 2
Таблица № 2
До флотации | После флотации | Показатели процесса |
Масса сырья, г Gс | Масса Масса хвостов Потери, г концентрата | Хо Хи % % |
Контрольные вопросы:
1. Приведите классификацию ресурсов химического сырья.
2. Чем измеряется скорость исчерпывания запасов сырья?
3. Что такое рециркуляция сырья и как она влияет на время исчерпывания его ресурсов?
4. Что является целью обогащения сырья и от чего зависит выбор метода обогащения?
5. Перечислите количественные показатели процесса обогащения и дайте им определение.
Литература:
1. В.И. Игнатенков, В.С. Бесков. Примеры и задачи по общей технологии. М.: Академкнига, 2005, 198 с.
2. Э.Е. Нифантьев, Н.Г. Парамонова. Основы прикладной химии. М.: Владос, 2002. 375 с.
3. Р.С. Соколов, Химическая технология, в 2-х томах, 2000, Т. 1. 368 с.
РАБОТА №4.
Дата добавления: 2016-01-06; просмотров: 23; Мы поможем в написании вашей работы! |
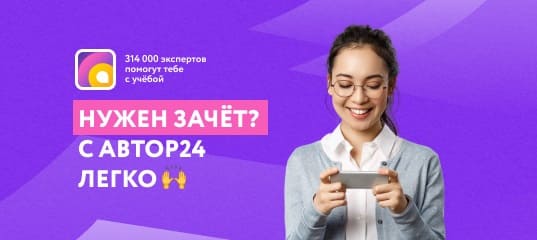
Мы поможем в написании ваших работ!