Строительная известь
Сырьём для производства строительной извести служат карбонатные породы: известняк, мел, доломитизированный известняк, доломит, мергелистый известняк. По механической прочности сырьё характеризуется пределом прочности при сжатии, МПа:
- твёрдые породы – более 60;
- породы средней твёрдости – 30…60;
- мягкие породы – 10…30;
- очень мягкие – менее 10.
Твёрдые породы используются во фракционированном виде.
По химическому составу и сортности получаемой извести карбонатные породы делятся на классы (см. табл. 3.1).
Таблица 3.1
Состав и сортность извести, получаемой из карбонатных пород
Состав | Классы карбонатных пород (ОСТ 21-27-76) | ||||||
А | Б | В | Г | Д | Е | Ж | |
Углекислый кальций СаСО3, %, не менее | |||||||
Углекислый магний MgCO3, %, не более | |||||||
Глинистые примеси SiO2 + Al2O3 + Fe2O3, %, не более | |||||||
Сорт получаемой извести (ГОСТ 9179) | Воздушная кальциевая | Воздушная магнезиальная | Воздушная доломитовая | Гидравлическая | |||
Первый, второй | Второй, третий | Первый, второй | Второй, третий | Первый, второй | Второй, третий | - |
Воздушную известь получают путем обжига сырья до полного удаления диоксида углерода, в результате чего получают продукт, состоящий преимущественно из СаО и MgO. Обжиг производят в шахтных печах, реже во вращающихся или в установках для обжига во взвешенном состоянии (кипящем слое). Обжиг твёрдых пород ведут в шахтных или вращающихся печах, мягкие породы обжигают преимущественно во вращающихся печах.
|
|
Основные реакции, происходящие при обжиге, состоят в термическом разложении карбонатов кальция и магния:
CaCO3 = CaO + CO2; MgCO3 = MgO + CO2.
Температура обжига составляет обычно 1000 … 1200оС. В результате получают комовую негашёную известь.
При более высоких температурах обжига образуются крупные кристаллы оксидов кальция и магния, происходит уплотнение продуктов обжига. Такая известь в обычных условиях медленно или совсем не реагирует с водой ("пережог"). Наличие пережога вредно влияет на качество извести.
При недостаточно высоких температурах обжига или в тех случаях, когда часть кусков сырья имела крупные размеры, возможно сохранение в извести неразложившегося углекислого кальция, который является балластом и ухудшает её свойства (т.н. "недожог").
Комовая негашёная известь, выходящая из печи – полупродукт, который для превращения в вяжущее измельчают: механически – размолом в мельницах (молотая известь), или химическим путём – гашением водой (гашёная известь). Для регулирования сроков схватывания и улучшения качества извести в нее в процессе измельчения или после помола могут вводиться тонкомолотые минеральные добавки: шлаки, золы, трепелы, туфы и др.
|
|
Гашение извести заключается в том, что вода поглощается порами извести и химически взаимодействует с оксидами кальция и магния:
CaO + H2O = Ca(OH)2; MgO + H2O = Mg(OH)2.
При этом выделяется большое количество тепла и часть воды испаряется, а известь вследствие изменения объёма распадается а тонкий порошок.
В зависимости от количества воды, взятой для гашения, можно получить гидратную известь-пушонку, известковое тесто и известковое молоко.
Для получения извести-пушонки теоретически достаточно 32,13% от массы негашёной извести. Практически воды берут в 2 … 3 раза больше (60 … 80%), т.к. при гашении часть её испаряется.
При гашении извести в тесто расход воды увеличивается до 2…3 ч (по массе) на ч извести; при ещё большем количестве воды получают известковое молоко.
Механизм твердения воздушной извести при обычной температуре и давлении обусловлен двумя процессами:
- кристаллизацией Са(ОН)2 за счёт испарения излишней воды;
- карбонизацией – взаимодействием с углекислым газом воздуха:
Са(ОН)2 + СО2 = СаСО3 + Н2О
При тепловлажностной обработке в автоклаве (в среде насыщенного пара при температуре 170…200 оС, давлении 0,8…1,6 МПа) в смеси с измельчённым кремнезёмистым компонентом (кварцевым песком, шлаком и т.д.) происходит гидросиликатное твердение воздушной извести за счёт взаимодействия её с кремнезёмом (SiO2) с образованием гидросиликатов кальция (пуццолановая реакция):
|
|
n Ca(OH)2 + SiO2 + m H2O = n CaO×SiO2×(m -1)H2O
Таким образом получают силикатные материалы и изделия – силикатный кирпич, силикатные бетоны.
Гидравлическую известь получают обжигом мергелистых известняков при температуре 900…1100 оС. При производстве гидравлической извести во время обжига часть образующегося СаО соединяется с оксидами SiO2, Al2O3 и Fe2O3, входящими в состав глинистых веществ, присутствующих в сырье. Это может быть представлено в виде следующих реакций:
2CaO + SiO2 = 2CaO×SiO2
2CaO + Fe2O3 = 2CaO× Fe2O3
CaO + Al2O3 = CaO× Al2O3
Образующиеся силикаты, ферриты и алюминаты кальция, обладают гидравлической активностью и образуют при взаимодействии с водой труднорастворимые соединения что обусловливают способность гидравлической извести твердеть не только на воздухе, но и в воде. Поскольку в гидравлической извести содержится также значительное количество свободного оксида кальция СаО, то она как и воздушная известь гасится при действии на неё воды.
|
|
3.2.3 Магнезиальные вяжущие вещества, растворимое (жидкое) стекло и кислотоупорный цемент
Каустический магнезит получают при умеренном обжиге магнезита при температуре 700...800 °С. Он состоит в основном из оксида магния.
Каустический доломит изготовляют обжигом природного доломита при 650...750 °С, т. е. ниже температуры диссоциации углекислого кальция. В каустическом доломите присутствуют как оксид магния, являющийся активной частью вяжущего, так и карбонат кальция, который, не обладая вяжущими свойствами, снижает активность по сравнению с каустическим магнезитом.
При затворении магнезиальных вяжущих водой процесс гидратации оксида магния идет очень медленно, а затвердевший камень имеет небольшую прочность. Поэтому каустический магнезит и доломит затворяют не водой, а водными растворами хлористых и сернокислых солей. В указанных растворах повышается растворимость оксида магния и резко ускоряется процесс твердения.
Наиболее распространённым затворителем для магнезиальных вяжущих является раствор хлористого магния MgCl2×6Н2О, причём среднее отношение его массы (по сухому веществу) к массе активной магнезии MgO, содержащейся в каустическом магнезите в количестве около 85%, составляет приблизительно 1: 2.
При затворении магнезиальных вяжущих раствором хлористого магния наряду с гидратацией оксида магния с образованием Mg(OH)2 происходит также образование гидрооксихлорида магния (MgCl2×3Mg(OН)2×7H2O). Затвердевший камень при этом набирает высокую прочность (при сжатии 40... 60 МПа — на каустическом магнезите и 10...30 МПа — на каустическом доломите).
Недостатком изделий на магнезиальных вяжущих, получаемых с применением в качестве затворителя раствора хлористого магния, является их повышенная гигроскопичность. Для уменьшения гигроскопичности и увеличения водостойкости используют другие виды затворителей, например сернокислый магний (MgSO4×7Н2O), сернокислое железо в сочетании с хлористым магнием и др.
Магнезиальные вяжущие можно применять только при твердении на воздухе при его относительной влажности не более 60%.
Растворимое стекло представляет собой натриевый или калиевый силикат (Na2O× n SiO2 или K2O× n SiO2), где n = 2,5...4 — модуль стекла. Чем больше модуль стекла, тем выше его клеящие свойства и кислотостойкость. Более высоким модулем и соответственно лучшими свойствами обладает калиевое растворимое стекло.
Растворимое стекло получают из смеси кварцевого песка с содой (Na2CO3), сульфатом натрия (Na2SO4) или поташом (K2CO3) в стекловаренных печах при температуре 1300...1400°С. Образовавшийся расплав при быстром охлаждении распадается на стекловатые полупрозрачные куски, называемые силикат-глыбой.
В строительстве растворимое стекло применяют в жидком виде и часто называют жидким стеклом. Растворение силикат-глыбы производят водяным паром в автоклаве. Раствор жидкого стекла, поступающего на строительство, содержит 50...70 % воды и имеет плотность 1,3...1,5 т/м3.
Твердение жидкого стекла происходит на воздухе за счёт высыхания, а также под влиянием углекислоты воздуха.
Силикаты натрия или калия в воде подвергаются гидролизу. По мере испарения жидкой фазы концентрация коллоидного кремнезема повышается, он коагулирует и уплотняется.
Углекислота воздуха нейтрализует едкую натриевую или калиевую щелочь, образующуюся в растворе при гидролизе и препятствующую выпадению из раствора кремниевой кислоты. В результате действия углекислоты воздуха усиливается коагуляция кремнекислоты жидкого стекла, благодаря чему ускоряется твердение.
Однако глубина проникания углекислоты сравнительно невелика и положительное ее действие наблюдается только на поверхности, внутренние же слои жидкого стекла твердеют очень медленно. В связи с этим для ускорения твердения применяют различные катализаторы, в первую очередь кремнефтористый натрий (Na2SiF6).
При взаимодействии кремнефтористого натрия с растворимым стеклом образуется малорастворимый фтористый натрий и нерастворимый гель кремнекислоты, являющийся клеящим веществом. Реакция идёт примерно следующим образом:
Na2SiF6 + 2Na2O×SiO2 + 6H2O = 6 NaF + 3 Si(OH)4.
В водном растворе кремнефтористого натрия вследствие его гидролитической диссоциации присутствует кислота (HF), которая нейтрализует свободную щёлочь в растворе растворимого стекла и ускоряет твердение системы.
На основе жидкого стекла изготовляют кислотоупорный цемент. Он состоит из тонкоизмельченного кислотоупорного наполнителя (кварца, кварцита, диабаза, андезита и т. п.) и ускорителя твердения — кремнефтористого натрия, смешанного с наполнителем в сухом виде. Затворяется кислотоупорный цемент раствором жидкого стекла.
Чаще всего применяют кислотоупорный кварцевый кремнефтористый цемент, в котором наполнителем является чистый тонкомолотый кварцевый песок.
Основное достоинство и принципиальное отличие кислотоупорного цемента от других неорганических вяжущих веществ — его способность сопротивляться действию большинства минеральных и органических кислот (кроме фтористоводородной, кремнефтористоводородной и фосфорной).
Схватываются кислотоупорные цементы в пределах 0,3...8 ч. Предел прочности при растяжении через 28 сут, как без последующего кипячения в серной кислоте, так и с ним, должен быть не менее 2,0 МПа, а кислотостойкость — не менее 93 % (потери при растворении цементного порошка в кислоте – не более 7%). На кислотоупорном цементе можно получить бетоны с прочностью при сжатии 30...40 МПа и более.
Кислотоупорный цемент применяют для приготовления кислотоупорных замазок, растворов и бетонов. Кислотоупорный цемент непригоден для конструкций, подверженных длительному воздействию воды, пара и щелочей, а также в условиях низких температур (ниже -20 °С).
Портландцемент
Технология портландцемента в основном сводится к приготовлению сырьевой смеси надлежащего состава, ее обжигу до спекания (получение клинкера) и помолу клинкера в тонкий порошок с добавлением небольшого количества двуводного гипса – регулятора схватывания.
Для производства портландцемента применяются сырьевые материалы, содержащие карбонат кальция и алюмосиликаты (известняки, глины, мергели). Чаще используют искусственные сырьевые смеси из известняка или мела и глинистых пород при соотношении между ними в сырьевой шихте примерно 3:1 (% по массе): СаСО3 — 75...78 и глинистого вещества — 22...25. Вместо глины или для частичной ее замены используют также отходы различных производств (доменные шлаки, нефелиновый шлам и т. п.).
Химический состав клинкера, выраженный через содержание основных оксидов, находится в следующих пределах (% по массе): СаО — 63...66; SiO2 — 21...24; Аl2О3 — 4...8; Fe2O3 — 2...4, их суммарное количество составляет 95......97%. В относительно небольших количествах в клинкере содержатся MgO, SO3, TiO2, Mn2O3, Na2O, K2O, P2O5 и др.; их влияние на свойства цемента весьма значительно.
Указанные элементы присутствуют в клинкере в виде различных соединений (минералов). На 70…80 % портландцементный клинкер состоит из силикатов кальция.
Портландцемент по составу отличается от клинкера, так как при его помоле к нему добавляют гипс, чтобы замедлить сроки схватывания. Содержание гипса ограничивается допустимым общим содержанием в портландцементе ангидрида серной кислоты (SO3).
Состав сырьевой смеси подбирают таким образом, чтобы обеспечить требуемый химико-минералогический состав цемента.
Для обеспечения нужного химического состава сырьевой смеси применяют корректирующие добавки, содержащие недостающие оксиды. Например, количество SiO2 повышают, добавляя в сырьевую смесь трепел, опоку. Добавление колчеданных огарков увеличивает содержание Fe2O3.
Сырьевую смесь приготовляют сухим или мокрым способом. В соответствии с этим различают и способы производства цемента — сухой и мокрый. При мокром способе сырьевую смесь приготавливают в виде водной суспензии (шлама), при сухом смешение измельчённых исходных компонентов ведут в сухом виде. Преимуществом сухого способа производства является снижение расхода теплоты на обжиг в 1,5...2 раза и более высокая производительность.
Промежуточное положение занимает комбинированный способ производства, при которых используют для обжига печи, работающие на гранулах (шахтные, с конвейерными кальцинаторами, спекательные решётки).
Обжиг сырьевой смеси обычно осуществляется во вращающихся печах. Вращающаяся печь представляет собой стальной цилиндр длиной до 200 м и более, диаметром до 5...7 м, футерованную изнутри огнеупорными материалами. Печь располагается горизонтально на роликах под углом 3...4о к горизонту и медленно вращается вокруг своей оси. Благодаря этому сырьевая смесь, загруженная в верхнюю часть печи, постепенно перемещается к нижнему концу, где происходит горение топлива (природного газа, мазута, угольной пыли). Поток раскалённых газов, образующийся при горении топлива, движется навстречу сырьевой смеси и обжигает ее.
Сырьевая смесь, перемещающаяся внутри печи, постепенно нагревается и проходит последовательно несколько характерных участков, отличающихся преобладающими в них процессами.
В зоне сушки сырьевая смесь встречается с горячими газами и подсушивается при повышении температуры до 150…250 °С.
В зоне подогрева при увеличении температуры до 500…600 °С сгорают находящиеся в сырье органические примеси и удаляется химически связанная вода из глинистых минералов.
Подготовительные зоны (сушки и подогрева) при мокром способе производства занимают 50...60 % длины печи.
При сухом способе производства широко применяют вращающиеся печи с циклонными теплообменниками (так называемый декарбонизатор), при котором сухая смесь проходит перед печью через систему циклонов, нагреваясь там за счёт тепла отходящих газов, и попадает затем в печь уже нагретой до температуры 800…900оС и частично декарбонизированной. Длина печи при этом соответственно уменьшается за счёт отсутствия в ней зон сушки и подогрева.
В зоне декарбонизации (кальцинирования) при температуре 900......1200°С происходит процесс диссоциации карбонатов кальция СаСО3 (известняка) на CaO и СО2.
Реакции в твёрдом состоянии между известью (СаО) и глинистыми составляющими начинаются уже при температуре 750…800оС, но значительно ускоряются они в так называемой зоне экзотермических реакций при температуре 1200…1300оС. К концу зоны экзотермических реакций полностью образуются двухкальциевый силикат – белит - 2CaO×SiO2 (C2S), трехкальциевый алюминат ЗСаО×Аl2О3 (С3А) и четырехкальциевый алюмоферрит 4СаО×А12О3×Fе2О3 (C4AF), но часть оксида кальция еще остается в свободном виде. Обжигаемый материал агрегируется в гранулы.
В зоне спекания при 1300...1450 °С обжигаемая смесь частично расплавляется. В расплав переходят С3А, C4AF и все легкоплавкие примеси сырьевой смеси. По мере появления расплава в нем растворяются частично растворяется C2S и вступает во взаимодействие с находящимся в расплаве свободным СаО, в результате чего образуется основной минерал портландцементного клинкера: алит - трехкальциевый силикат 3CaO×SiO2 (C3S). Некоторая часть трёхкальциевого силиката образуется за счёт реакции между C2S и СаО в твёрдом состоянии.
С3S плохо растворяется в расплаве и вследствие этого выделяется из расплава в виде мелких кристаллов, способных к росту.
В зоне охлаждения (заключительная стадия обжига) температура клинкера понижается до 1000 °С, происходит окончательная фиксация его структуры и состава, включающего C3S, C2S, C3A, C4AF, стекловидную фазу и второстепенные составляющие. От того, какую структуру приобретают составляющие портландцементного клинкера в процессе обжига и охлаждения, зависят свойства цемента.
По выходе из печи клинкер быстро охлаждается в специальных холодильниках, чтобы предотвратить образование в нем крупных кристаллов и сохранить в незакристаллизованном виде стекловидную фазу. Без быстрого охлаждения клинкера цемент обладает пониженной реакционной способностью.
После выдержки на складе (1...2 недели) или без неё клинкер превращают в цемент путем помола его в тонкий порошок, добавляя небольшое количество двуводного гипса. Готовый портландцемент направляют для хранения в силосы и далее на строительные объекты.
Ориентировочное содержание основных четырех минералов в портландцементном клинкере составляет (% по массе): алит[1] 3CaO×SiO2 (C3S) — 40...65, белит 2CaO×SiO2 (C2S) — 15...40, трёхкальциевый алюминат ЗСаО×А12О3 (С3А) — 3...15, четырёхкальциевый алюмоферрит 4СаО×А12О3×Fе2О3 (C4AF) — 10...20.
Трехкальциевый силикат (алит) — основной минерал цементного клинкера — обладает большой активностью в реакции с водой, особенно в начальные сроки, значительным тепловыделением при твердении, быстро твердеет и набирает высокую прочность.
Двухкальциевый силикат (белит) значительно менее активен, чем алит. Обладает низким тепловыделением при гидратации, медленно твердеет, но в течении длительного срока набирает значительную прочность, в ряде случаев превосходящую прочность алита.
Трехкальциевый алюминат отличается самым быстрым взаимодействием с водой, наибольшим тепловыделением, однако продукты его твердения имеет повышенную пористость, низкие прочность, морозостойкость и коррозионную стойкость. Быстрое твердение С3А при отсутствии в цементе добавки двуводного гипса вызывает ускоренное схватывание цементного теста.
Четырехкальциевый алюмоферрит характеризуется умеренным тепловыделением, медленно твердеет и набирает невысокую прочность.
Нежелательными составными частями клинкера являются свободные оксиды кальция и магния. Их вредное влияние проявляется в том, что они гидратируются очень медленно с увеличением объёма в уже затвердевшем цементе. Содержание свободных СаО и MgO в клинкере допускается соответственно не более 1 и 5 %.
В клинкере присутствуют также щелочные оксиды Na2O и К2О, переходящие в него из сырьевых материалов и золы твердого топлива. Их вредное влияние может проявиться в тех случаях, когда бетон изготовлен на реакционноспособных заполнителях, содержащих аморфный кремнезем (диоксид кремния). Щелочи, реагируя с диоксидом кремния, образуют в водной среде водорастворимые силикаты калия и натрия с увеличением объема, что вызывает растрескивание бетона. Кроме этого, щелочные оксиды снижают морозостойкость бетона, уменьшают эффективность применения химических добавок. В связи с этим нежелательно, чтобы содержание щелочных оксидов в пересчёте на Na2O в цементе превышало 0,6 %.
Твердение портландцемента после затворения водой (гидратация) обусловлено рядом химических и физико-химических процессов, в результате которых образуются новые гидратные соединения.
Процесс гидратации трехкальциевого силиката выражается уравнением:
2 (3СаО× SiO2) + 6Н2О = ЗСаО × 2SiO2 × 3Н2О + 3Са(ОН)2.
В результате образуется практически нерастворимый в воде гидросиликат кальция и гидроксид кальция, который частично растворим в воде.
Двухкальциевый силикат гидратируется медленнее C3S и при его взаимодействии с водой выделяется меньше Са(ОН)2, что видно из уравнения реакции:
2 (2СаО × SiO2) + 4Н2О = 3СаО × 2SiO2 × ЗН2О + Са(ОН)2.
Приведённые уравнения являются ориентировочными, поскольку молярное соотношение СаО: SiО2 в гидросиликатах, образующихся при гидратации цемента, может изменяться в зависимости от состава материала, условий твердения и других обстоятельств. Для всех полукристаллических и аморфных гидратов кальциевых силикатов применяется термин C-S-H. Гидросиликаты кальция низкой основности, имеющие состав (0,8...1,5)CaO×SiO2× (1...2,5)Н2О обозначаются (по Тейлору) формулой C-S-H(I), гидросиликаты высокой основности (1,5...2)CaO×Si02× n H2O — формулой C-S-H(II). Образование низкоосновных гидросиликатов кальция повышает прочность и долговечность цементного камня; при возникновении высокоосновных гидросиликатов его прочность и коррозионная стойкость меньше.
Взаимодействие трехкальциевого алюмината с водой приводит к образованию гидроалюминатов кальция, например:
3СаО × Аl2О3 + 6Н2О = 3СаО × Аl2О3 × 6Н2О.
Реакция протекает с большой скоростью. Образующиеся гидроалюминаты кальция создают непрочную рыхлую коагуляционную структуру, что вызывает быстрое загустевание цементного теста.
Для замедления сроков схватывания портландцемента в него вводится при помоле небольшая добавка двуводного гипса. В результате химического взаимодействия трехкальциевого гидроалюмината с введенным гипсом и водой образуется гидросульфоалюминат кальция (эттрингит) по схеме:
ЗСаО × Аl2О3 × 6Н2О + 3 (CaSO4 ×2H2O) + (19...20) Н2О =
= 3СаО× Аl2О3 ×3CaSO4 × (31...32) Н2О
В цементном тесте, жидкая фаза которого представляет собой насыщенный раствор Са(ОН)2, эттрингит сначала выделяется в коллоидном тонкодисперсном состоянии, осаждаясь на поверхности минерала С3А в виде полупроницаемых оболочек, что замедляет его гидратацию и отодвигает сроки схватывания цемента.
Появление свободного гидроалюмината кальция и преждевременное загустевание цементного теста предотвращается, пока не израсходуется находящийся в растворе гипс (обычно 1...3 ч).
Двуводный гипс при правильной дозировке является не только регулятором сроков схватывания портландцемента, но и улучшает свойства цементного камня. Это связано с последующей кристаллизацией эттрингита в виде длинных иглоподобных кристаллов – после того, как концентрация гидроксида кальция в жидкой фазе твердеющего цементного теста понижается за счёт кристаллизации Са(ОН)2 из пересыщенного раствора. Кристаллы эттрингита вносят значительный вклад в раннюю прочность цементного камня (до 1…2 суток) и уплотняют его структуру.
Четырехкалъциевый алюмоферрит и другие алюмоферриты кальция взаимодействует с водой по сложным схемам с образованием различных кристаллогидратов – гидроалюминатов, гидроферритов кальция и их твёрдых растворов, например: 4CaO×Al2O3×13H2O; 3CaO×Al2O3×6H2O; 4CaO×Fe2O3×13H2O; 3CaO×Fe2O3×6H2O; 4CaO×Al2O3×Fe2O3×13H2O; 4CaO×(Al, Fe)2O3 ×19H2O; 3CaO×(Al, Fe)2O3×6H2O и др.
Образующиеся гидроалюминаты и гидроферриты могут связываться добавкой гипса, как и продукты гидратации трёхкальциевого алюмината, в результате чего образуются гидросульфоалюминаты и гидросульфоферриты кальция.
Стекловидная фаза цемента гидратируется с образованием твёрдых растворов алюмоферритов кальция состава 3CaO×Al2O3×Fe2O3×6H2O и гидрогранатов, имеющих общую формулу 3CaO×(Al, Fe)2O3× x SiO2×(2-6)H2O.
При твердении цемента на воздухе также происходит карбонизация гидроксида кальция при его взаимодействии с углекислотой воздуха на поверхности цементного камня.
Указанные химические превращения протекают одновременно с физико-химическими процессами микроструктурообразования, такими как молекулярное и коллоидное растворение, коллоидация и кристаллизация. Cуществует различное теоретическое толкование об их характере и последовательности.
Часть исследователей (А. Ле Шателье, П.А. Ребиндер, В.Б. Ратинов, Ю.М. Бутт и др.) объясняют твердение портладцемента процессами растворения кристаллов в воде с образованием насыщенных и перенасыщенных растворов с последующей кристаллизацией из них. В то же время многие исследователи (А.А. Байков, Д. Джефри, Х. Функ, О.П. Мчедлов-Петросян, В.В. Тимашев, И.П. Выродов, Р. Кондо и др.) трактуют стадию взаимодействия кристаллов с водой как топохимическую, т.е сопровождающуюся присоединением поверхностью кристаллов молекул воды или ионов Н+, ОН- с образованием на цементных зёрнах гидратированного слоя небольшой толщины и последующим переходом частично или полностью гидратированных ионов в водный раствор.
Процесс гидратации портладцемента может быть условно разделён на несколько стадий.
В начальный период при соприкосновении частиц цемента с водой на их поверхности сразу начинается растворение клинкерных минералов и гипса, в результате чего жидкая фаза цементного теста насыщается ионами Ca2+, SO42-, OH-, K+, Na+ и др. В раствор переходят также небольшие количества ионов алюминия, железа и кремния. Быстрое насыщение водного раствора ионами Ca2+ объясняется гидролизом C3S в выделением Са(ОН)2.
После достижение пересыщения из раствора кристаллизуются Са(ОН)2 (портландит) и эттрингит, которые образуют малопроницаемые оболочки в первую очередь на участках C3A и C4AF на поверхности цементных зёрен, благодаря чему затрудняется диффузия воды к негидратированной части зёрен и замедляется процесс гидратации.
Спустя приблизительно 1 ч после затворения в растворе появляются микрокристаллы гидросиликатов кальция, которые также участвуют в образовании экранирующих оболочек на зёрнах цемента.
Период заторможенных реакций (индукционный период) продолжается 1…3 ч и более, затем в результате разрушения экранирующих оболочек растущими из-под них кристаллами эттрингита и портландита процессы гидратации вновь ускоряются.
Гидросиликаты кальция образуются на данной стадии преимущественно в виде длинных волокон, одновременно образуется значительное количество гидросиликатного гидросиликатного геля и формируется каркас твердеющего цементного камня.
В дальнейшем происходит постепенное заполнение порового пространства всё новыми продуктами гидратации и их срастание между собой, что приводит к упрочнению системы.
На ранних стадиях твердения, пока не сформировался каркас твердеющей системы (до схватывания теста), цементные зёрна контактируют друг с другом через оболочки геля, и цементное тесто обладает коагуляционной структурой. Характерной особенностью коагуляционной структуры является ее тиксотропность, т. е. способность обратимо разрушаться (разжижаться) при механических воздействиях (перемешивание, вибрирование и т. д.).
Образовавшийся цементный камень представляет собой микроскопически неоднородную дисперсную систему, названную В. Н. Юнгом «микробетоном». Заполняющая часть в нем состоит из внутренних частей цементных зерен, еще не вступившими в реакции, а вяжущая - гелеобразными и кристаллическими новоообразованиями. Количество, дисперсность, строение, физико-химическая природа, характер и число контактов гелеобразных и кристаллических фаз цементного камня наравне с поровой структурой определяет свойства цементного камня.
Для твердеющего цементного теста характерно явление контракции (стяжение) - уменьшения абсолютного объема системы (цемент-вода), вызванное тем, что объём продуктов гидратации несколько меньше суммарного объёма воды и твёрдых веществ, вступающих в реакцию.
Количество воды, необходимое для полной гидратации цемента, составляет теоретически около 20 % от массы портландцемента, а для получения пластичного цементного теста цемент затворяется значительно большим количеством воды (35...60 %). Испаряемая вода на разных этапах твердения постепенно уходит из цементного камня, оставляя поры. Учитывая также, что цемент гидратируется не полностью, а существенная его часть остаётся в виде непрореагировавших ядер цементных зёрен в "микробетоне Юнга", затвердевший цементный камень имеет значительную пористость – до 35%, что отрицательно сказывается на прочности и морозостойкости камня. В связи с этим для увеличения прочности и долговечности цементного камня важную роль играет уменьшение водоцементного отношения.
Скорость химических реакций, протекающих при твердении цемента, а также полнота использования цемента и его прочность увеличиваются при повышении тонкости помола.
При увеличении степени гидратации цемента при длительном твердении цемента в благоприятных условиях возрастает объем новообразований и уменьшается пористость цементного камня, при этом повышаются прочность и долговечность бетона.
Для непрерывного повышения прочности цементного камня необходима влажная теплая среда. Твердение практически прекращается в сухой среде или при отрицательной температуре. При замораживании твердеющего цементного камня, если оно произошло уже после существенного формирования структуры и достижения критической прочности, способен после оттаивания к дальнейшему твердению, но в этом случае не может быть достигнута такая же прочность, как при твердении в нормальных условиях.
Помимо выбора цемента надлежащего химико-минералогического состава и тонкости помола ускорение твердения бетона достигают тепловлажностной обработкой (пропариванием, автоклавной обработкой), введением специальных добавок и их сочетанием.
Дата добавления: 2016-01-05; просмотров: 99; Мы поможем в написании вашей работы! |
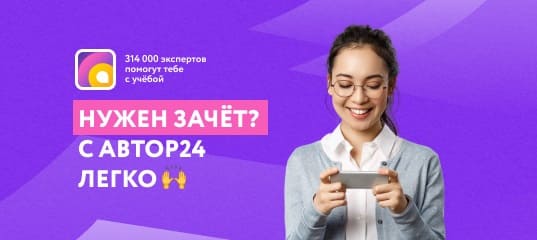
Мы поможем в написании ваших работ!