Методы стандартизации
В зависимости от поставленных целей и решаемых задач используют различные методы стандартизации.
Смысл стандартизации состоит в упорядочивании решений правил, методов и т. д. в целях их многократного использования. Любая работа в сфере стандартизации начинается с анализа имеющегося массива информации и выделения основных, наиболее характерных признаков, в соответствии с которыми этот массив может быть систематизирован.
К методам стандартизации относятся систематизация, классификация, кодирование, типизация, унификация (основной метод стандартизации) и агрегатирование.
Систематизация - распределение предметов исследования в определенном порядке или последовательности, образующее систему, удобную для использования.
В технике систематизация широко используется при делении машины на сборочные единицы, а последних – на детали с определенными принципами их обозначения, например, каталоги запасных частей автомобилей.
Систематизация является предпосылкой перехода к следующему методу стандартизации – классификации.
Классификация – распределение множества объектов стандартизации на классификационные группы по определенным, как правило, наиболее характерным для группы изделий одного назначения, признакам.
На этом принципе в технике построены типоразмерные ряды главных параметров, производится классификация однотипных машин по основным параметрам и т. д., например, типоразмерные ряды грузоподъемности строительных кранов или пределы измерения микрометров: 0-25 мм; 25-50 мм; 50-75 мм и т. д.
|
|
Классификация и систематизация предполагает кодирование информации.
Кодирование – образование по определенным правилам объектов или групп объектов и присвоение им кодов, позволяющее заменить несколькими знаками (или символами) наименования этих объектов.
Коды позволяют идентифицировать объекты наиболее коротким способом (минимальным количеством знаков), способствуя повышению эффективности сбора, учета, хранения и обработки информации. Число знаков в коде определяется его структурой и зависит от количества кодируемых признаков. Наиболее часто применяются десятизначные системы кодирования.
Классификация и кодирование широко применяется в стандартизации для обозначения стандартов, входящих в межотраслевые системы стандартов, например:
|
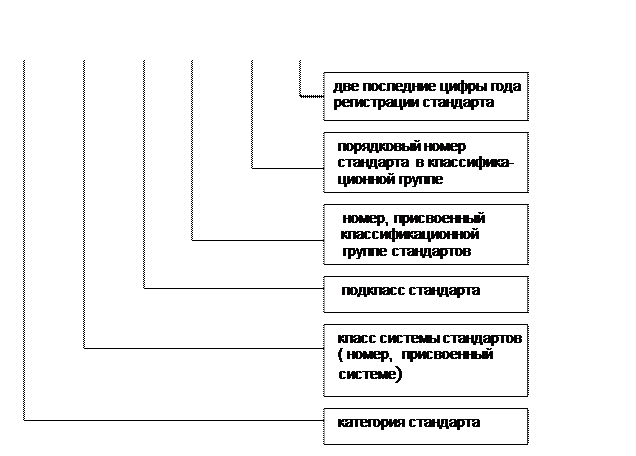
Порядок проведения работ по классификации и кодированию информации регламентирован комплексом государственных стандартов «Единая система классификации и кодирования технико-экономической и социальной информации (ЕСКК ТЭСИ)», на основе которой разработаны такие, широко используемые в нашей стране классификаторы, как общероссийский классификатор отраслей народного хозяйства (ОКОНХ), Общероссийский классификатор предприятий и организаций (ОКПО), Общероссийский классификатор единиц измерений (ОКЕИ) и др. В ряде случае классификаторы могут иметь и более длинное кодовое обозначение объектов, например по технологическому классификатору машиностроительной продукции технологический код включает 14 индексов, из которых 6 индексов – на постоянную часть кода, а 8 – переменную.
|
|
Постоянная часть предназначена для классификации групп основных признаков детали: размерных характеристик (диаметр, длина и т.п.); группы материалов (стали, чугуны, цветные сплавы и др.); способа технологических процессов получения детали (резанье, литье, обработка давлением и т.д.).
Переменную часть кода используют для конкретизации признаков определенного вида детали, описанной постоянным кодом. В переменную часть кода входит вид заготовки (пруток, поковка, отливка и др.); точность (квалитет) элементов детали, шероховатость ее поверхностей, наличие термообработки и масса детали.
Структура технологического кода позволяет с использованием электронно-вычислительной техники обрабатывать информацию на различных уровнях конструкторско-технологической подготовки производства, существенно влияя на выбор оборудования, подъемно-транспортных и складских средств, технологических режимов обработки деталей и режущего инструмента а также и средств измерений для их контроля.
|
|
После того, как собранный массив информации систематизирован и классифицирован по определенным признакам, переходят к следующему методу стандартизации – типизации.
Типизация конструкций изделий и технологических процессов позволяет существенно снизить издержки за счет повышения серийности производства и качества продукции, что, в свою очередь, повышает конкурентоспособность как выпускаемой продукции, так и самой фирмы.
Типизацияконструкций изделий – разработка и установление типовых конструкций, содержащих конструктивные параметры, общие для изделий сборочных единиц и деталей.
При типизации анализируют уже существующие типоразмеры изделий, их составные части, агрегаты и детали, а также оценивают перспективы развития науки, техники и промышленности, возникающие при этом возможные потребности рынков сбыта. В результате такого анализа может оказаться, что внесение сравнительно небольших изменений в конструкцию детали или сборочной единицы может удовлетворить потребности большого количества новых потребителей. Это
|
|
Итогом такой работы часто может стать установление соответствующих типоразмерных рядов изделий, их составных частей, деталей или даже их элементов.
Типизация технологических процессов – разработка и установление технологического процесса для производства однотипных деталей или сборка однотипных составных частей или изделий в целом. В этом случае типовой технологический процесс разрабатывается для типовой детали, обладающей наибольшим количеством признаков, характерных для деталей данной классификационной группы, имея в виду, что некоторые операции или переходы технологического процесса будут опущены при обработке деталей, не обладающих данным технологическим или конструктивным признаком.
Наиболее распространенным и эффективным методом стандартизации является унификация.
Унификация –это выбор оптимального числа разновидностей
продукции, процессов и услуг, значений их параметров и размеров.
Унификация позволяет установить минимально необходимое, но достаточное количество видов, типов, типоразмеров, обладающих высокими показателями качества и полной взаимозаменяемостью.
Результаты унификации не обязательно оформляются в виде стандарта, но стандартизация изделий и их элементов обязательно основывается на унификации.
Принципиальное отличие унификации от других методов стандартизации состоит в том, что в процессе унификации предполагается внесение изменений в конструкцию изделия или иного объекта унификации с целью увеличения его применяемости и снижения его себестоимости с одновременным повышением качества.
Объектами унификации могут быть изделия массового, серийного и/или индивидуального производства, а также отдельные размеры или элементы деталей, агрегаты, сборочные единицы, модули (например, гибкие производственные модули), машины, если они состоят из сравнительно небольшого количества сборочных единиц одинакового назначения и выполняют близкие по характеру операции или процессы.
Унификация подразделяется на:
• внутриразмерную, когда унификация охватывает все модификации определенной машины как в отношении ее базовой модели, так и в отношении модификации этой модели;
• межразмерную, когда унифицируют не только модификации одной базовой модели, но и базовые модели машин разных размеров данного параметрического ряда; • межтиповую, когда унификация распространяется на машины разных типов, входящих в различные параметрические ряды.
Внутриразмерная и межразмерная унификация наиболее часто проводится на заводском уровне. Так, например, в коробке передач автомобиля ВАЗ 2110 используется 131 наименование деталей из ранее созданных автомашин – от ВАЗ 111 – «Ока» до ВАЗ 2109 «Самара» и лишь 60 новых, а в двигателе - 195 ранее используемых и 75 новых (оригинальных). И это несмотря на то, что в ВАЗ 2110 новый инжекторный двигатель.
Межтиповая унификация широко используется в автомобильной промышленности крупнейших мировых производителей. Например, такие разные марки автомобилей, как Opel Signum V6, Audi A3 и Nissan Micra используют систему управления двигателем фирмы Bosch.
Агрегатирование – принцип создания машин, оборудования и приборов из унифицированных стандартных агрегатов (автономных узлов), устанавливаемых в изделии в различном количестве и комбинациях.
Эти агрегаты должны обладать полной взаимозаменяемостью по всем эксплуатационным параметрам и присоединительным размерам.
Внедрение унификации и агрегатирования привело к тому, что до 80% деталей и сборочных единиц переходят из изделия в изделие без изменений, обеспечивая при этом оптимальные эксплуатационные показатели и сокращая сроки проектирования и освоения новой техники в 2-2,5 раза при снижении в 1,5...2 раза соответствующих затрат.
Дата добавления: 2016-01-05; просмотров: 55; Мы поможем в написании вашей работы! |
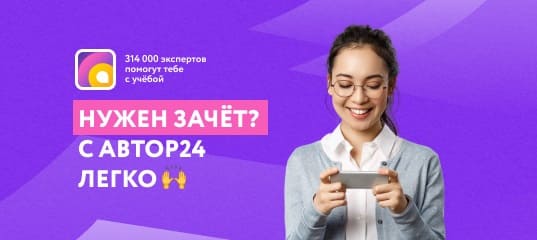
Мы поможем в написании ваших работ!