Проектирование линии производства холоднокатаной листовой стали
5.1. Схема производства и характеристика
технологических операций
В настоящее время имеется устойчивая тенденция к увеличению доли холоднокатаной листовой стали в общем выпуске листового проката. Это связано с увеличением производства автомобилей и других видов пассажирского транспорта, сельскохозяйственных машин, бытовых металлических изделий (холодильников, кондиционеров и других электроприборов), изделий пищевой и консервной промышленности с применением металлической тары, изделий электротехнической, радиотехнической, полиграфической промышленности. Особенно увеличилась потребность и соответственно производство холоднокатаного металла с антикоррозионными покрытиями в связи с применением гладких и профилированных листов в строительстве для ограждающих конструкций промышленных зданий и сооружений. Доля холоднокатаного листа в общем объеме производства проката промышленно развитых стран за 10 – 15 лет составляет 18 – 39 %.
Холоднокатаные листы и полосы (ленты) толщиной от 5 до 0,001 мм широко применяют в разных отраслях промышленности благодаря широкому сортаменту и высокому качеству. Эта продукция характеризуется высокой степенью точности размеров, плоскостностью, чистотой поверхности, повышенными механическими и технологическими свойствами металла.
На современных участках для производства холоднокатаной листовой стали применяется прогрессивный рулонный способ, который обеспечивает:
|
|
- высокую производительность как собственно прокатных станов, так и многочисленных технологических агрегатов (травления, отжига, дрессировки, нанесения покрытия, резки и т.д.), устанавливаемых на этих участках;
- непрерывность технологического потока в составе каждого агрегата и возможность автоматизации производства;
- высокое качество продукции по геометрии и механическим свойствам;
- высокие технико-экономические показатели производства.
Характеристика некоторых отечественных современных станов холодной прокатки приведена в табл.10.
Таблица 10
Технические параметры современных станов
холодной прокатки
Параметры | Стан 2500 ММК | Стан 2000 НЛМК | Стан 1700 КарМК | Стан 1400 КарМК |
Размеры исходной полосы, мм: толщина ширина | 1,5–5,0 1250-2350 | 1,8-6,0 900-1850 | 1,8-6,0 700-1550 | 1,8-3,0 700-1250 |
Диаметр рулона: внутренний наружный |
730-830
![]() | 1200-2250 | 1550-2700 | 1550-2200 |
Размеры полосы после прокатки, мм: толщина ширина | 0,6-2,5 1250-2350 | 0,35-3,5 900-1850 | 0,4-3,5 700-1550 | 0,1-0,6 700-1250 |
Диаметр рулона: внутренний наружный Максимальная масса рулона, т Число клетей |
![]() | 1200-2200 | 1550-2700 | 1100-2200 |
Диаметр валков, мм: рабочих опорных | 500-470 1500-1410 | 615-550 1610-1490 | 600-570 1400-1320 | |
Длина бочки валков, мм: рабочих опорных | ||||
Мощность двигателей, кВт: разматывателя рабочих клетей моталки | 2х2800 2х2800 | 2х590 4х2050 2х1065 | 2х200 2х29001 2(2х2400)1-5 3х1250 | 2х6401 2х1002 30001 2х30002-6 2(4х630) |
Максимальная скорость прокатки, м/с | 31,7 | |||
Максимальная емкость петлевого устройства, м | - | - | Нет свед. | |
Масса оборудования, т | ||||
Общая длина агрегата, м | 30,4 |
Примечание. 1, 2, 1 – 5, 2 – 6 - номер разматывателя или клети.
|
|
Исходным продуктом для холодной прокатки листовой стали являются горячекатаные полосы толщиной 2-6мм, поступающие с широкополосных станов горячей прокатки.
Готовой продукцией цехов холодной прокатки являются:
— горячекатаная полосовая и листовая сталь, с поверхности которой удалена окалина;
— горячекатаная термически обработанная полосовая и листовая сталь, с поверхности которой удалена окалина;
|
|
— холоднокатаная конструкционная углеродистая и низколегированная сталь толщиной 0,4-3 мм в рулонах и листах;
— жесть (тонкая листовая сталь толщиной 0,08-0,35 мм, предназначенная, главным образом, для изготовления штампованных изделий, например, консервных банок, крышек к стеклянной таре);
— оцинкованная холоднокатаная сталь;
— холоднокатаная электротехническая (трансформаторная и динамная) сталь;
— холоднокатаная нержавеющая сталь.
Схемы технологического процесса производства холоднокатаной стали (рис.4) включают следующие операции.
1. Удаление окалины с поверхности горячекатаных полос, чтобы она не вдавливалась при холодной прокатке в металл и валки. Наибольшее распространение для очистки металлопроката получил химический способ (травление в растворе соляной или серной кислоты). Для обеспечения непрерывности движения полосы через кислотные ванны задний конец предыдущего рулона сваривают стыкосварочной машиной с передним концом последующего. При этом увеличивается масса рулона, что значительно повышает производительность станов холодной прокатки.
2. Холодная прокатка осуществляется при температуре металла не более, чем 150-200° С. В современных цехах процесс осуществляется, как правило, рулонным способом, при котором металл прокатывают в виде длинных полос, сматываемых в рулоны. Около 90% холоднокатаной листовой стали прокатывают на непрерывных станах, у которых все клети расположены последовательно, в каждой клети осуществляется один проход, и раскат одновременно находится в нескольких клетях.
|
|
Для получения конструкционной листовой стали толщиной 0,4-2,5 мм, шириной 1500-2350 мм, в рулонах массой 20-60 т применяют четырех- или пятиклетьевые непрерывные станы производительностью 1-1,7 млн.т/год.
![]() | |||||||
| |||||||
| |||||||
| |||||||
Рис.4. Схемы технологического процесса производства
холоднокатаной листовой стали:
а — конструкционной стали; б — жести; в — оцинкованной стали
Для получения жести применяют пяти- или шестиклетьевые станы. Производительность таких станов достигает 750 тыс. т в год.
Холодная прокатка ведется с применением технологических смазок, которые подаются на поверхность валков и полосы. Смазка снижает коэффициент трения, благодаря чему уменьшаются сопротивление деформации и давление металла на валки. В качестве смазочных материалов применяют эмульсии, состоящие из подогретой воды (95-97%), кальцинированной соды и масла. При прокатке конструкционного листа используют эмульсии на основе минеральных масел, а при получении жести — дорогие, но более эффективные эмульсии с растительными маслами (например, пальмовым маслом).
3. Электролитическое обезжиривание и очистка предназначены для удаления с поверхности стальной холоднокатаной полосы остатков технологической смазки, применяемой на станах холодной прокатки. Сгорая и разлагаясь в очаге деформации, технологическая смазка оставляет на поверхности проката жировую пленку с наличием вкатанного сажистого углерода. Нанесение покрытий невозможно без предварительной механической очистки полосы щетками и химического обезжиривания.
4. Термическая обработка (рекристаллизационный отжиг при 720-750° С) производится для достижения требуемых механических свойств холоднокатаной углеродистой листовой стали. Отжиг осуществляется в колпаковых печах или на непрерывных агрегатах с протяжными печами.
5. Дрессировка представляет собой холодную прокатку отожженного металла с обжатием 0,5-3% (в отдельных случаях до 5%). Дрессированные листы приобретают блестящую полированную поверхность. Кроме того, происходит поверхностное упрочнение (наклеп) металла. Это необходимо для стали, применяемой для изготовления штампованных изделий, так как при холодной штамповке листов, имеющих недостаточно жесткий поверхностный слой, могут появиться дефекты поверхности (следы от пересечения плоскостей сдвигов с внешней поверхностью листа).
Дрессировку осуществляют на одно- или двухклетьевых станах.
6. Резка полосы, смотанной в рулоны, производится на агрегатах следующих видов:
— агрегаты поперечной резки, предназначенные для разрезки полос на листы мерной длины и выдающие продукцию в виде листов, уложенных в пакеты;
— агрегаты продольной резки, предназначенные для разрезки полос на более узкие ленты и выдающие продукцию в рулонах;
— комбинированные агрегаты резки, выполняющие в зависимости от потребности функции агрегатов поперечной или продольной резки.
Масса исходных рулонов, подаваемых на агрегаты резки, достигает 40 т и более; скорость перемещения полосы в процессе резки 1-7 м/с.
7. Нанесение покрытия на поверхность листового проката является эффективным методом защиты металла от коррозии. Большую долю в производстве проката с покрытиями занимает белая (луженая) жесть, широко применяющаяся для изготовления консервной тары и в ряде других отраслей промышленности для упаковки красок, масел и другой продукции, а также в радиоэлектронике и приборостроении.
Оловянные покрытия на жесть могут быть нанесены двумя способами:
— горячим лужением, при котором металл пропускается через ванны с расплавленным оловом;
— электролитическим лужением, когда слой олова осаждается на поверхность жести в сернокислой, щелочной или галогенной ванне.
Скорость движения металла при электролитическом лужении достигает 8-10 м/с, а при горячем — 0,5 м/с. Высокая производительность агрегатов и малый расход олова при электролитическом нанесении покрытий обусловили широкое распространение этого способа.
Новым материалом, успешно заменяющим белую жесть, является хромированная лакированная жесть. Хромирование производится электролитическим способом, лакирование — в электролитическом поле высокого напряжения, сушка лакового покрытия — индукционным нагревом. Новая жесть обладает высокой коррозионной стойкостью и не требует больших затрат на изготовление.
Конструкционную листовую сталь покрывают цинком или алюминием, что повышает срок службы листов в десятки раз. Горячим цинкованием (опусканием листов в расплавленный цинк, имеющий температуру 450-500° С) получают толщину покрытия 10-40 мкм.
В последнее время расширяется производство листов с неметаллическими покрытиями (пластмассы и лаки), которые наносятся на поверхность проката в виде пленок или порошков с помощью вращающихся валков и электрических полей высокого напряжения.
Схемы производства нержавеющей и электротехнической сталей имеют более сложный вид и могут включать многократную термообработку различных видов (закалка, обезуглероживающий отжиг, высокотемпературный отжиг и т.п.), полировку, шлифование и т.д.
Основной агрегат на участках производства холоднокатаного листа, определяющий его сортамент и производительность,- стан холодной прокатки. В современных цехах холодной прокатки устанавливаются непрерывные четырех-, пяти- и шестиклетьевые четырехвалковые и реверсивные, чаще всего одноклетьевые, четырех-, шести- или двадцативалковые станы. Реверсивные станы используются в основном для производства листов широкого сортамента из малоуглеродистых, легированных и электротехнических сталей, а также тонкой и тончайшей полосы из труднодеформируемых сталей и сплавов. Непрерывные станы устанавливаются в цехах с высокой производительностью. Для прокатки тонких листов и жести начали применять непрерывные станы бесконечной прокатки, оборудованные стыкосварочными машинами и петленакопителями (рис.5), обеспечивающими прокатку сваренных встык горячекатаных полос без заправки в стан передних концов каждого рулона и пауз между рулонами. На обычных непрерывных станах потери времени по этим причинам достигает 16 – 21 %. Преимущества стана бесконечной прокатки перед обычными непрерывными станами заключаются в повышении производительности из-за снижения простоев, тихого хода и значительного повышения машинного времени работы стана (в среднем на 50%); увеличении выхода годного в результате сокращения обрези переднего и заднего концов полосы (18 – 30 м на каждом рулоне); сокращении в 1,5 раза расхода валков и улучшении поверхности полос за счет снижения надавов на бочке валков от концов полос; улучшении условий труда и сокращении обслуживающего персонала благодаря полной автоматизации процесса прокатки.
5.2. Расчет основных параметров
холодной листовой прокатки
5.2.1. Расчет режима обжатий и скорости прокатки
в клетях стана
Распределение обжатий по клетям оказывает влияние на устойчивость процесса прокатки, качество готового листа и энергетические затраты при холодной прокатке. Существует несколько вариантов распределения обжатий (рис.6).
Рис.6. Варианты распределения обжатий по клетям:
1 — убывающий; 2 — с максимальными обжатиями
в средних проходах; 3 — возрастающий;
— частные обжатия в клетях; i — номера клетей по ходу прокатки
При выборе убывающего варианта исходят из следующих соображений. По мере холодной прокатки сопротивление деформации стали и ее твердость возрастают. Поэтому наибольшие обжатия обеспечивают в первых проходах, когда металл еще достаточно мягок. Убывающий вариант обеспечивает наименьший разогрев полосы, что позволяет вести прокатку с большой скоростью. Однако он может быть применен в случае, если подкат имеет незначительную разнотолщинность и высокую плоскостность.
В варианте с максимальными обжатиями в средних проходах, незначительная деформация металла в первых клетях способствует некоторому уменьшению исходной разнотолщинности.
Возрастающий вариант обеспечивает эффективное выравнивание продольной разнотолщинности полосы, но приводит к значительному разогреву полосы на выходе из стана.
Суммарные и частные обжатия, применяемые при холодной прокатке листовой стали на непрерывных станах с различным количеством клетей, приведены в табл.11.
Таблица 11
Суммарные и частные обжатия при холодной прокатке
Число клетей | Общее суммарное | Частные обжатия в клетях eI, % | ||||||||||||||
Стана | Обжатие e,% | 1 клеть | 2 клеть | 3 клеть | 4 клеть | 5 клеть | 6 клеть | |||||||||
50 – 80 | 10-35 | 25-45 | 25-45 | 20-25 | — | — | ||||||||||
60 – 90 | 10-35 | 35-45 | 35-45 | 25-40 | 25-35 | — | ||||||||||
80 – 95 | 25-35 | 25-35 | 25-35 | 25-35 | 25-35 | 25-35 | ||||||||||
При расчете режимов обжатий сначала выбираем один из вариантов распределения обжатий. Затем выбираем частные обжатия из интервалов, указанных в табл.11. По формуле (47) рассчитываем толщины полос перед клетями
(47)
где — толщина полосы перед i -й клетью;
— толщина полосы после i -й клети.
Толщина исходной горячекатаной полосы, входящей в первую клеть, должна составлять 2-6 мм. Значение общего суммарного обжатия e должно находиться в интервале, указанном в табл. 11.
Максимальная скорость прокатки в последней клети четырехклетьевого стана достигает 18-25, пятиклетьевого — 25-30, шестиклетьевого — 35-45 м/с. В других клетях непрерывного стана скорость прокатки рассчитывается по уравнению (45).
Пример 6. Расчет режима обжатий и скорости прокатки на пятиклетьевом непрерывном стане 1200.
Расчет будем производить для полосы сечением 0,22х730 из стали 08кп.
Выбираем режим с максимальными обжатиями в средних проходах. Частные обжатия в клетях подбираем из табл.11.
По формуле (47) рассчитываем толщину полосы перед клетями.
Толщина полосы перед 5-й клетью
Перед 4-й клетью
Перед 3-й клетью
Перед 2-й клетью
Толщина исходной горячекатаной травленой полосы перед 1-ой клетью
Определяем общее суммарное относительное обжатие
Определяем суммарное и частные абсолютные обжатия:
Принимаем скорость в последней клети V = 25 м/c.
Тогда по уравнению (45):
5.2.2. Расчет сопротивления металла
полосы деформации
Холодная прокатка характеризуется значительным деформационным упрочнением металла. Поэтому значение предела текучести материала полосы sТ возрастает от в сечении входа в очаг деформации до
в сечении выхода. При расчете сопротивления металла деформации используют усредненное значение предела текучести
(48)
где n - коэффициент, учитывающий влияние среднего главного нормального напряжения (при прокатке широких и тонких полос n = 1,15).
Для расчета наиболее часто используют формулу А. В. Третьякова [10]
(49)
где — предел текучести металла в исходном (недеформированном) состоянии, МПа;
a, в — коэффициенты, зависящие от марки стали;
— суммарное относительное обжатие, которое накопила полоса к моменту выхода из i -й клети.
Значения предела текучести металла в исходном состоянии и коэффициентов а и в, необходимые для расчета предела текучести с учетом обжатия полосы, представлены в табл.12.
Таблица 12
Исходные данные для расчета предела текучести с учетом
обжатия полосы [10]
Марка | Предел текучести металла в | Коэффициенты формулы (49) | |
Стали | исходном состоянии ![]() | А | в |
08пс | 294,3 | 75,5 | 0,48 |
08кп | 225,6 | 33,9 | 0,6 |
294,3 | 28,9 | 0,64 | |
367,9 | 31,0а | 0,64 | |
343,4 | 82,0 | 0,48 | |
343,4 | 85,0 | 0,48 | |
Cт1 | 255,1 | 13,1 | 0,73 |
Cт2 | 294,3 | 30,0 | 0,62 |
Пример 7. Расчет сопротивления металла полосы деформации (исходные данные взяты из примера 6).
Суммарное относительное обжатие, которое имеет полоса к моменту выхода из 1-й клети ,а на выходе из 5-й клети -
(см. пример 6).
Из табл. 12 для стали 08кп , a = 33,9; b = 0,6.
Пределы текучести металла на выходе из клетей:
Усредненные значения предела текучести:
Сопротивление металла пластической деформации:
5.2.3. Расчет усилия и момента прокатки
Усилие прокатки определяем по формуле (38). Радиус бочки рабочего валка R составляет для станов 1200 и 2500 — 0,25 м, для станов 2000, 1700 и 1400 – 0,3 м.
Наиболее простым выражением для определения величины среднего контактного давления p при холодной прокатке является [4]
(50)
где ;
— коэффициент трения при установившемся процессе прокатки (
).
Момент прокатки определяем по формуле (41). Для расчетов холодной прокатки .
5.3. Определение производительности стана
Часовую, среднюю часовую и годовую производительность стана определяем по формулам (1), (6) и (7).
Расход металла при холодной прокатке на непрерывных станах определяется, главным образом, обрезью концов рулонов из-за отклонений по толщине. При производстве жести kр =1,09, при холодной прокатке конструкционной листовой стали kр =1,07.
Коэффициент использования непрерывного стана равен 0,9.
Прокатка полосы на станах холодной прокатки идет на различных скоростях (рабочей, заправочной, замедленной для прокатки швов), что затрудняет определение ритма прокатки. Для приближенных расчетов необходимо определить время, необходимое для прокатки всего рулона на рабочей скорости, и полученное значение умножить на поправочный коэффициент.
Таким образом, ритм прокатки будет равен
(51)
где L — длина рулона после прокатки на стане, м;
Vк — скорость прокатки в последней клети стана, м/с;
с — поправочный коэффициент, учитывающий время прокатки с пониженной скоростью и время пауз (для непрерывных станов холодной прокатки с = 1,3).
, (52)
где h — толщина готового холоднокатаного листа, м;
b — ширина листа, м;
r — плотность стали.
Масса рулона G для стана 2500 составляет 30 т, для стана 2000 — 50 т, для стана 1700 — 45 т, для стана 1400 — 30 т, для стана 1200 — 15 т.
Число часов работы в году непрерывного стана холодной прокатки составляет 7500 ч.
5.4. Выбор вспомогательного оборудования
Для обеспечения выпуска заданного объёма прокатной продукции необходимо определить требуемое число машин и агрегатов, обеспечивающих технологический поток производства. Расчёт проводится с учетом максимальной производительности стана.
При выборе вспомогательного оборудования следует учитывать последние достижения мировой практики и принимать к установке самое совершенное современное оборудование.
Производительность непрерывного травильного агрегата
, (53)
где — ритм работы участка травильных ванн, с.
,
где — скорость движения полосы в ваннах, зависящая от их числа и длины, м/с.
Число ванн, шт | Длина каждой ванны, м | Скорость движения полосы, м/с |
1,2 – 1,8 | ||
1,7 – 2,5 | ||
2,1 – 3,1 |
Необходимое количество травильных агрегатов
.
Дата добавления: 2016-01-05; просмотров: 50; Мы поможем в написании вашей работы! |
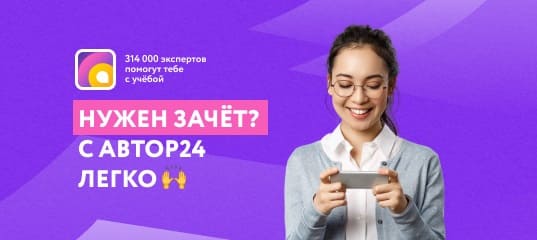
Мы поможем в написании ваших работ!