Технологические схемы производства
Проката
Технологический процесс представляет собой последовательность технологических операций, дающих возможность получить готовую продукцию, удовлетворяющую требованиям потребителя. Основной технологической операцией является пластическая деформация металла в приводных прокатных валках. К вспомогательным операциям относятся: транспортировка, резка, смотка и размотка рулонов, правка, травление, нагрев, охлаждение, нанесение покрытий, сортировка, упаковка и т.д. Сочетания технологических операций в определенной последовательности и с определенными режимами дают возможность получить все многообразие прокатной продукции.
Исходным материалом для прокатного производства могут быть слитки, полученные разливкой стали в изложницы, и литые блюмы и слябы, поступающие с машин непрерывного литья заготовок (МНЛЗ). Слитки сначала поступают на обжимные станы, где из них изготавливают катаные блюмы, слябы и заготовки (полупродукт). В настоящее время самым прогрессивным способом получения полупродукта является разливка стали на МНЛЗ. Обжимные и заготовочные станы, предназначенные для переработки слитков, выводятся из эксплуатации, ипродукция сталеплавильных цехов непосредственно поступает на сортовые и листовые станы горячей прокатки в виде литых блюмов, слябов и заготовок.
Схемы производства и характеристики технологических операций применительно к различным видам металлопроката приведены в соответствующих главах данного учебного пособия.
|
|
1.3. Типы прокатных станов
Прокатным станом называется совокупность оборудования, предназначенного для формоизменения металла в приводных валках, транспортировки, отделки и упаковки проката. Оборудование станов делится на основное и вспомогательное. Первое непосредственно осуществляет прокатку металла и включает рабочие клети с приводом.
К вспомогательному оборудованию относятся:
— транспортирующие механизмы, обеспечивающие перемещение исходных материалов, полупродукта и готового металлопроката (мостовые краны, рольганги, транспортеры, подъемные столы, опрокидыватели, толкатели и т.д.);
— обрабатывающие механизмы, работа которых связана с проведением операций, не относящихся непосредственно к деформации металла, но технологически необходимых для последующей его обработки (ножницы, моталки, разматыватели, правильные машины, травильные агрегаты, машины для обвязки и упаковки проката и т.д.).
По виду выпускаемой продукции прокатные станы делятся на:
— обжимные станы (блюминги и слябинги), на которых из слитков получают полупродукт — катаные блюмы и слябы;
|
|
— заготовочные станы, производящие из блюмов заготовки для сортовых, проволочных и трубных станов;
— рельсобалочные станы для прокатки железнодорожных рельсов, балок, швеллеров и других крупных профилей;
— крупносортные станы для прокатки двутавровых балок и швеллеров, угловой стали, фасонных профилей отраслевого назначения и простых профилей (круглая сталь);
— среднесортные станы для прокатки простых и фасонных профилей общего и отраслевого назначения;
— мелкосортные станы для прокатки простых и фасонных профилей общего назначения;
— проволочные станы, служащие для прокатки катанки (круглой заготовки для проволоки) диаметром 5—13 мм в бунтах;
— станы горячей прокатки листов и полос, включающие одно – трехклетьевые толстолистовые станы для прокатки листов толщиной 4 – 200 мм (возможно до 400 мм), шириной 1000 – 5300 мм, а также многоклетьевые полунепрерывные и непрерывные широкополосные станы для производства полос и листов толщиной 1,2 – 16 мм, шириной 500 – 2300 мм рулонным способом;
— станы холодной прокатки листовой стали и жести толщиной от 5 до 0,1 мм и менее, шириной 500 – 2300 мм, включающие непрерывные четырех- и пятиклетьевые станы холодной прокатки, непрерывные шестиклетьевые жестепрокатные станы, многовалковые (12 – 20-валковые) реверсивные станы для прокатки тонкой и тончайшей ленты рулонным способом.
|
|
— трубные станы для производства бесшовных и сварных труб;
— станы специального назначения для прокатки шаров, колесо- и кольцепрокатные, периодической продольной или поперечно-винтовой прокатки.
За основной параметр сортовых станов принимают диаметр валков. Если в стане несколько клетей, параметром всего стана в целом является размер валков последней чистовой клети.
Например, "стан 500" означает, что диаметр валков чистовой клети равен 500 мм.
Сортовой прокат – наиболее массовый вид продукции - характеризуется широким сортаментом по форме и размерам профилей. В зависимости от формы поперечного сечения сортовой прокат подразделяется на простые и фасонные профили. К простым профилям относятся круг, квадрат, шестигранник, арматурная сталь периодического профиля, полоса. Фасонные профили подразделяются на профили общего и специального (отраслевого) назначения. К фасонным профилям общего назначения – рельсы, трехгранная, овальная и другие стали, применяемые в транспортном и сельскохозяйственном машиностроении, судостроении, строительстве, угольной, нефтяной и других отраслях промышленности. По размерам поперечного сечения весь сортовой прокат условно подразделяется на сталь крупносортную, среднесортную и мелкосортную. Например, на рельсобалочных станах диаметр круглой или сторона квадратной стали составляет 90 – 250 мм, на крупносортном – 50 – 120 мм, среднесортном – 20 – 75 мм, мелкосортном – 10 – 40 мм.
|
|
Основным параметром листовых станов является длина бочки валка, которая определяет наибольшую ширину прокатываемых на стане полос.
Например, "стан 2000" означает, что длина бочки валков равна 2000 мм.
Толстолистовой прокат получают горячей прокаткой на непрерывных широкополосных станах (например, станы 2500 и 2000 ОАО "ММК") и специализированных реверсивных станах (например, стан 2800 Орско-Халиловского металлургического комбината, станы 4500 и 2350 ОАО "ММК"). На широкополосных станах производят листовую продукцию толщиной до 16 мм в рулонах. Реверсивные станы выдают листы мерной длины толщиной до 50 мм и плиты толщиной 50—380 мм.
Тонколистовую сталь получают на широкополосных станах горячей прокатки и на станах холодной прокатки.
Стан для производства гнутых профилей (профилегибочный агрегат) обозначается двумя размерными интервалами: первый характеризует толщину исходной заготовки для стана, второй — ширину.
Например, "стан 1-4х50-300" означает, что гнутые профили могут быть получены на данном стане из полос толщиной 1—4 мм и шириной 50—300 мм.
2. ПРОЕКТИРОВАНИЕ ЛИНИИ ПРОИЗВОДСТВА
СОРТОВОЙ СТАЛИ
2.1. Схема производства и характеристика
технологических операций
Технологическая схема на участках производства сортового проката в общем виде представляет комплекс основных операций, определяющих состав и компоновку оборудования:
- нагрев исходной заготовки;
- горячая прокатка необходимого профилеразмера сечения
металла;
- горячая резка раскатов;
- охлаждение и отделка проката для придания ему необходи-
мых товарных свойств (механических, технологических) и
формы (длины, кривизны, упаковки и т.п.).
Схема расположения оборудования современного сортового стана представлена на рис.1. Стан является непрерывным, т.е. все его клети расположены последовательно, в каждой клети осуществляется один проход, и раскат одновременно находится в нескольких клетях.
Заготовки перед прокаткой на сортовых станах нагреваются в методических пламенных печах. Плавный и экономичный нагрев металла обеспечивается переменным температурным режимом по длине печи и противоточным движением продуктов сгорания и нагреваемых заготовок. Температура нагрева заготовок из углеродистых и низколегированных сталей с содержанием углерода до 0,45% составляет 1200—1220о С.
Прокатные клети, как правило, разделяются на две группы: черновую и чистовую. Перед черновой группой находятся ножницы для обрезки переднего конца заготовки. Между группами клетей расположен промежуточный рольганг с летучими аварийными ножницами. В случае каких-либоотказов в чистовой группе аварийные ножницы должны порезать раскат на мелкие куски, которые можно легко убрать со стана.
После выхода из последней клети стана раскат разрезается на части, соответствующие длине холодильника (100-120 м). Сортовые профили простой формы (круг, квадрат, полоса) режут на ножницах. Чтобы предотвратить искажение формы фасонных профилей (уголок, швеллер, рельс) применяют пилы.
В настоящее время для охлаждения сортовых профилей в основном применяют холодильники реечного типа. Охлаждаемые полосы лежат на неподвижных рейках. При поступлении очередного раската подвижные рейки совершают ход, перемещая весь металл, находящийся на холодильнике на 100—200 мм. Так, постепенно, полосы перемещаются от одного края холодильника к другому, остывая до 50—100о С.
После прокатки и охлаждения раскат, как правило, искривлен по длине. Для устранения этого дефекта металл подвергают знакопеременному изгибу на роликовых правильных машинах. Полоса, требующая правки, пропускается между двумя рядами роликов, установленных в шахматном порядке. При движении полоса изгибается роликами и выпрямляется.
2.2. Определение производительности стана
и количества рабочих клетей
Практически возможная часовая производительность прокатного стана по каждому виду профиля определяется по формуле [1]
, (1)
где G — масса исходной заготовки, т;
Ки — коэффициент использования стана;
t — темп (ритм) прокатки, с;
Кр — коэффициент расхода металла.
Коэффициент использования стана учитывает неизбежные потери времени из-за небольших и случайных задержек, нарушающих нормальный ритм прокатки (стан при этом не останавливается). Значение коэффициента Ки =0,85 – 0,9, причем более высокое значение относится к непрерывным станам.
Расход металла при горячей прокатке вызван его потерями в виде окалины, обрези, брака. Для крупносортных станов Кр = 1,1, для среднесортных — Кр = 1,075—1,078, для мелкосортных — Кр =1,075.
Темп прокатки — это время от начала прокатки одной заготовки до начала прокатки последующей.
(2)
где t м — машинное время прокатки, с;
t п — время паузы между прокаткой заготовок, с.
, (3)
где — конечная длина раската после прокатки в последней клети стана, м;
V к — линейная скорость раската на выходе из последней клети стана, м/с.
Скорость прокатки в последней клети непрерывного крупносортного стана 10—12 м/с, среднесортного — 12 -15 м/с, мелкосортного — до 20 м/с.
, (4)
где — длина исходной заготовки (
= 6—12 м);
— общая вытяжка (относительное удлинение металла после прокатки на стане).
, (5)
где Fо - площадь поперечного сечения исходной заготовки, м2;
Fк - площадь поперечного сечения готового профиля, м2.
Исходным материалом для крупносортных станов могут являться блюмы сечением 300х300 мм, 350х350 мм и длиной до 6 м; для среднесортных — катаная или литая заготовка квадратного или прямоугольного сечения от 100х100 мм до 250х250 мм длиной до 12 м; для мелкосортных — 80х80 мм до 130х130 мм длиной до 12 м; для проволочных – катаная или литая заготовка сечением от 100х100 мм до 130х130 мм и длиной 12 – 15 м.
Зная долю каждого профиля в общем выпуске и часовую производительность по каждому профилю, можно определить среднюю производительность по формуле
(6)
где а1, а2,..., ап — доля каждого профиля в общем выпуске, %;
А1, А2,..., Ап — производительность по каждому профилю, т/ч.
Годовая производительность прокатного стана
(7)
где N — число часов работы стана в году.
Для крупносортных станов N = 7100 ч, для среднесортных — N = 7300 ч, для мелкосортных — N = 7400 ч, для проволочных — N = 7500 ч.
Определяем количество рабочих клетей стана, необходимое для прокатки профиля с наибольшей .
Если известны вытяжки при прокатке в каждой клети стана, то общая вытяжка может быть определена как произведение частных вытяжек:
или
,
где — среднее значение вытяжки при деформации металла в клетях стана (
= 1,3).
Отсюда количество клетей, необходимых для прокатки сортового профиля из исходной заготовки, можно определить по формуле
(8)
2.3. Выбор нагревательных устройств
и вспомогательного оборудования
Расчет числа нагревательных печей производится следующим образом.
Вычисляем активную площадь пода одной печи (площадь днища печи, на которой лежит нагреваемый металл)
(9)
где Lп — длина активного пода печи.
Суммарная активная площадь пода печей, необходимых для обеспечения нагретым металлом прокатного стана:
, (10)
где А мах — наибольшая из часовых производительностей стана, т/ч;
Кс — средняя величина съема с единицы активной площади пода, т/м2ч.
При горячем всаде (когда в печь подается металл, еще не остывший после прокатки на заготовочном стане) Кс = 0,8-0,9 т/м2ч, при холодном — Кс = 0,6 т/м2ч.
Необходимое количество печей
(11)
Холодильник в общем случае состоит из подводящего рольганга, собственно холодильника и отводящего рольганга. Расстояние между ножницами и холодильником определяет тормозной путь прокатанного металла. При малой длине этого пути раскат не успевает затормозиться, ударяется об упор в конце рольганга, сворачивается и запутывается.
Минимальная длина тормозного пути
(12)
где f — коэффициент трения (f = 0,3—0,5);
g — ускорение свободного падения (g = 9,81 м/с2).
Ширина холодильника Вx определяется по формуле
, (13)
где m — число раскатов, поступающих на холодильник со стана, шт/ч;
— время, необходимое для охлаждения металлопроката, ч;
а — расстояние между лежащими рядом на холодильнике раскатами (шаг гребенок на рейках); для крупносортных станов величина а составляет около 0,5 м, среднесортных — 0,3 м, мелкосортных — 0,15 м;
К — коэффициент неплотности укладки раскатов на холодильнике (К = 0,9).
(14)
где G1 — масса 1 м длины раската, кг;
lр — длина раската, м.
Если lк 120 м, то lр = lк. Если lк > 120 м, то lр = lк/ni
120. Здесь ni — наименьшее целое число.
(15)
где — коэффициент теплоотдачи между охлаждающимся раскатом и окружающей средой;
Fохл — теплоотдающая поверхность 1 м длины охлаждаемого раската, м2;
Tср — средняя температура раската в процессе его охлаждения, оС,
;
T1 — температура, с которой прокатанный металл поступает на холодильник (800 – 950о С);
T2 — температура, при которой металл убирается с холодильника (50 – 100° С);
— количество тепла, отдаваемое 1 м длины раската при его охлаждении на холодильнике;
(16)
с1 и с2 — теплоемкость стали при соответствующей температуре, кДж/(кг×град). Теплоемкостьсталипри 800оС с1 = 0,678 кДж/(кг×град), при 50о С — с2 = 0,469 кДж/(кг×град).
Необходимое количество роликовых правильных машин
. (17)
Производительность одной правильной машины
(18)
где Кпр — коэффициент, учитывающий паузы и задержки при правке (0,85 - 0,95);
— темп правки, с.
Машинное время правки одного раската
(19)
где Vпр — скорость правки (0,5 - 2 м/с).
2.4. Склады металла и определение их площади
В цехе горячей прокатки должны быть предусмотрены склады: исходных заготовок, готовой продукции, запасных частей, масел, валков.
Выбор типа, емкости и компоновки оборудования складов зависит от сортамента продукции, способа производства и производительности цеха. Емкость складов заготовки и готовой продукции зависит также от наличия общезаводских складов и цехов для производства исходной заготовки и дальнейшего передела проката и труб, а промежуточных складов – от соотношения производительности участков, выдающих полупродукт на промежуточное складирование, и участков, принимающих его на дальнейшую обработку.
Склады заготовок, полупродукта и готовой продукции размещают, как правило, в пролетах производственного здания цеха шириной 24,0 – 36,0 м, а в отдельных случаях – шириной 42,0 м, оборудованных соответствующими грузоподъемными устройствами. Применяют продольное и поперечное расположение металла относительно пролета склада. При наличии электромостовых кранов с вращающейся траверсой металл укладывается в штабели слоями крест-накрест.
Хранение слитков и прокатной продукции на складах осуществляется следующим способом.
Слитки укладываются в штабель высотой до 2,5 м, блюмы и заготовки – в штабель крест-накрест высотой до 2,5 м, слябы - пачками в стопы высотой до 3 м или в штабель крест-накрест, сортовая заготовка – в штабель крест-накрест высотой до 4 м или в карманы-стойки.
Рельсы укладываются в штабель с прокладками высотой до 4 м или в карманы-стойки, балки и швеллеры – в штабель с прокладками или крест-накрест высотой до 4 м, крупносортная, среднесортная и мелкосортная сталь – обвязанными пачками в штабель крест-накрест высотой до 4 м, на многоярусные стеллажи на стойках или на высотных складах, круглая заготовка – рядами или обвязанными пачками в штабель крест-накрест высотой до 4 м или в карманы-стойки с прокладками, сортовая сталь и катанка в бунтах – в корзинах в несколько горизонтальных рядов высотой до 5 м или в переносных контейнерах.
Основной характеристикой складов металла является их емкость Мс, определяемая количеством металла, которое может быть на них размещено [2]:
, (20)
где Тхр — норма продолжительности хранения, сут (для склада заготовок Тхр =3-4 сут, для склада готовой продукции Тхр=2-3 сут);
Q 2 - максимальная интенсивность удаления металла со склада, т/ч.
Для склада заготовок Q 2 принять равной наибольшей из часовых производительностей стана, а для склада готовой продукции Q 2 принять равной средней часовой производительности.
Полезная площадь склада определяется по емкости Мс, т, и удельной нагрузке q, кН/м2, по формуле [2]
. (21)
Удельные нагрузки q на площади складов в прокатных цехах можно принять следующими:
блюмы и заготовки до 5 м – 70, слябы длиной до 12 м – 120, заготовка квадратная до 12 м – 120, рельсы длиной до 25 м – 50, балки и швеллеры – 30, сталь крупносортная, среднесортная и мелкосортная – 80, катанка – 20.
2.5. Расход энергоносителей, материалов
и инструмента
Потребителями электроэнергии являются приводы рабочих клетей прокатных станов и других машин, а также системы искусственного освещения. Другие виды энергоносителей используются в нагревательных печах (горючие газы, воздух), системах охлаждения оборудования и металла, мокрых газоочистках, системах гидросбива и гидроудаления окалины (вода), отопительных устройствах (пар, горячая вода) и т.п.
Для определения годовой потребности проектируемой технологической линии в различных видах ресурсов необходимо годовую производительность умножить на соответствующий расходный коэффициент:
Пi = ki AГ, (22)
где Пi — расход какого-либо энергоносителя, материала или инструмента;
ki — расходный коэффициент (табл.1).
Таблица 1
Расход энергоносителей, материалов и инструмента
при сортовой прокатке [1, 2]
Вид энергоносителя, | Тип стана | ||
материала или инструмента | крупно–сортный | средне–сортный | мелко–сортный |
Электроэнергия, кВт×ч/т, При прокатке углеродистых сталей | 70–80 | ||
При прокатке легированных сталей | 120–180 | ||
Вода, м3/т | 20–40 | 20–40 | 20–40 |
Сжатый воздух, м3/т | |||
Пар, кг/т | |||
Топливо для нагревательных печей, кДж/т (при холодном посаде) | 2,28×106 | 2,28×106 | 1,56×106 |
Смазочные материалы, кг / т, | |||
густые | 0,1 | 0,05 | 0,05 |
Жидкие | 0,4 | 0,25 | 0,45 |
Огнеупорный кирпич для нагревательных печей, кг/т | 0,6 | 0,6 | 0,6 |
Валки, кг/т | 2,5 | 0,4 | 0,3 |
В цехах хранят запасные и сменные детали, масса которых составляет примерно 3% от массы всего механического оборудования прокатного стана.
Дата добавления: 2016-01-05; просмотров: 17; Мы поможем в написании вашей работы! |
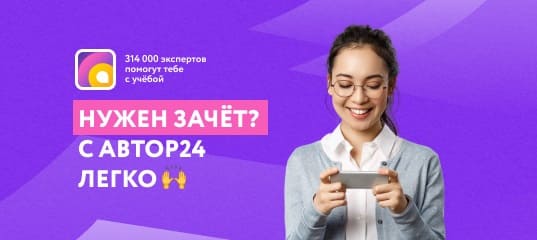
Мы поможем в написании ваших работ!