Прокатка в чистовой клети
1-й проход. Исходные данные: Н 1 = 48 мм, L 1= 5,257 м.
Принимаем = 9 мм (см. табл.4).
Далее расчет ведем аналогично, его результаты приведены в табл.5. Общее количество проходов в чистовой клети - семь. Суммарное машинное время прокатки — 41,1 с.
В результате прокатки имеем лист с размерами 12х1840х20934 мм. После обрезки его переднего и заднего концов, а также боковых кромок получаем лист 12х1700х20000 мм.
3.3.2. Расчет температурного режима прокатки
Температурный режим прокатки зависит от температуры нагрева сляба, снижения температуры вследствие контакта прокатываемого металла с окружающей средой — воздухом, водой, валками и различными деталями стана, повышения температуры в результате тепла пластической деформации. Доля перечисленных составляющих в суммарном тепловомбалансе различна, поэтому для определенных условий можно отбрасывать некоторые составляющие теплового баланса,считая их влияние незначительным или предполагая, что неучтенные статьи компенсируются. Так для расчета температурного режима прокатки толстых листов можно ограничиться учетом потерь тепла только излучением и конвекцией. Тогда расчет температуры прокатки следует выполнять, используя уравнение В. А. Тягунова [4]:
(34)
где — снижение температуры раската вследствие теплоизлучения, оС;
t — температура раската перед проходом, оС;
— время охлаждения, с.
В клетях толстолистовых станов после каждого прохода происходит изменение зазора перед рабочими валками и направления их вращения, а раскат после выброса из валков останавливается и рольгангом подается обратно. Время, необходимое для выполнения этих операций, называется временем паузы между проходами t п.
|
|
Время охлаждения раската в каждом проходе будет равно сумме машинного времени прохода и времени паузы между проходами:
. (35)
Пример 3. Расчет температурного режима прокатки в чистовой клети стана 2800 листа 12х1700х20000 мм из раската 48х1840х5257 мм (исходные данные берутся из примера 2).
1-й проход. Исходные данные: = 1050о C,
= 39 мм, t м1=2,8 с,
= 2 с.
2,8 + 2 = 4,8 c.
= 1050 – 6 = 1044° С.
2-й проход. Исходные данные: t 2 = 1044° С, = 31,5 мм, t м2 = 3,5 с,
= 2 с.
3,5 + 2 = 5,5 c.
=1044 – 9 = 1035° С.
Аналогично для других проходов:
= 13° С;
= 25° С;
= 1022° С;
= 978° С;
= 19° С;
= 33° С;
= 1003° С;
= 945° С.
В последнем седьмом проходе раскат после выброса из валков не останавливается и не подается обратно, а отводится рольгангом от клети к роликовой правильной машине. Поэтому ,
= 28° С, а температура конца прокатки
составляет:
= 945 – 28 = 917° С.
3.3. Расчет сопротивления металла
пластической деформации
Сопротивление металла деформации в точке деформируемого тела равно интенсивности напряжений в этой точке, доста-
|
|
точной для осуществления пластической деформации при заданных условиях взаимодействия тела и валков. Значение может быть определено по формуле Л. В. Андреюка [6]:
(36)
где S,а,b,с – постоянные коэффициенты для стали данной марки (табл. 6);
— базисное значение сопротивления деформации (см. табл. 6), МПа;
U — скорость деформации, .
Таблица 6
Коэффициенты уравнения (36)
Сталь | S | ![]() | A | b | С |
Ст 3 кп | 0,885 | 77,9 | 0,135 | 0,164 | - 2,8 |
Ст 3 сп | 0,96 | 90,7 | 0,124 | 0,167 | - 2,54 |
Ст 5 сп | 0,917 | 89,5 | 0,144 | 0,208 | - 3,35 |
0,934 | 87,6 | 0,125 | 0,266 | - 2,46 | |
15Г | 0,842 | 0,126 | 0,188 | - 2,74 | |
35Г2 | 0,94 | 83,5 | 0,151 | 0,122 | - 3,66 |
330ХГСА | 0,996 | 92,4 | 0,134 | 0,25 | - 3,34 |
20ХГ2С | 1,011 | 95,8 | 0,125 | 0,213 | - 3,65 |
87,4 | 0,143 | 0,173 | - 3,05 | ||
40Х | 0,979 | 87,5 | 0,13 | 0,17 | - 3,62 |
65Г | 1,007 | 72,7 | 0,166 | 0,222 | - 3,02 |
20Х13 | 0,9 | 0,132 | 0,21 | - 3,26 | |
12Х18Н10Т | 0,825 | 0,112 | 0,088 | - 4,35 |
Скорость деформации определяем по формуле
, (37)
где — окружная скорость валков, м/с;
— длина дуги захвата, м (
);
R — радиус рабочих валков, м (для чистовой клети стана 3600 R = 0,5 м, для стана 2800 R = 0,4 м);
Н — толщина полосы перед проходом, м.
3.3.4. Расчет усилия и момента прокатки
Силу, с которой металл давит на валки, обычно определяют по формуле
(38)
|
|
где — среднее контактное давление металла на валки, Па;
Fк — проекция контактной площадки металла с валками, м2.
Для листовой прокатки величину Fк находят из выражения
(39)
где В — ширина раската при прокатке в клети, м.
Среднее контактное давление зависит от напряженного состояния металла в очаге деформации
, (40)
где — коэффициент напряженного состояния.
В зависимости от геометрического параметра очага деформации М. Я. Бровман рекомендует принимать [4]:
при 0,5
2;
при
2;
при
0,5,
где
Средняя толщина полосы в очаге деформации
.
Момент прокатки — составляющая момента на валу двигателя главного привода, обусловленная сопротивлением прокатываемого металла деформированию и трением на контактных поверхностях очага деформации. Момент прокатки в клети стана следует определять по формуле:
(41)
где — коэффициент плеча приложения усилия прокатки (для чистовой клети толстолистового стана
= 0,39).
3.4. Расчет производительности стана,
площади складов металла,
расхода энергоносителей, материалов
и инструмента
Часовую производительность толстолистового стана можно определить по формуле (1), среднюю — по (6), годовую — по (7).
Коэффициент использования реверсивного стана составляет 0,85-0,87 [7].
|
|
Коэффициент расхода металла при прокатке толстолистовой стали из слябов следующие [7]:
— кипящая углеродистая сталь 1,18 - 1,23
— спокойная углеродистая сталь 1,20 - 1,25
— низколегированная сталь 1,20 - 1,27.
Темп прокатки в черновой и чистовой клетях толстолистового стана, как правило, различен. Темп прокатки на двухклетьевом стане в целом будет определяться наибольшим темпом прокатки в одной из клетей. Поэтому необходимо рассчитать темп прокатки в черновой и чистовой клетях стана и в формулу (1) подставить наибольший:
(42)
где — суммарное машинное время прокатки в клети, с;
— число проходов в клети;
— время паузы между проходами, с;
— время паузы между концом прокатки в клети одного раската и началом прокатки следующего, с.
Число часов работы в году реверсивных толстолистовых станов горячей прокатки составляет 7200 [2].
Емкость и площадь складов слябов и готовой продукции определяют по формулам (20), (21). Слябы укладывают пачками в стопы высотой до 3 м или крест-накрест в штабеля высотой до 4 м. Удельная нагрузка q на данном складе составляет 120 кН/м2. На складе готовой продукции пачки горячекатаных толстых листов хранятся в штабелях высотой до 3 м (q =70 кН/м2).
Расходные коэффициенты для определения годовой потребности цеха в различных ресурсах по формуле (22) [1, 2]:
электроэнергия, кВт ч/т 80-90
вода, мз/т 35-50
сжатый воздух, мз/т 30
пар, кг/т 40
топливо, кДж/т 2,51×106
смазочные материалы, кг/т:
густые 0,1
жидкие 0,3
огнеупоры, кг/т:
для нагревательных колодцев 2,5
для нагревательных печей 0,6
валки, кг/т 1,2-1,8
4. ПРОЕКТИРОВАНИЕ ЛИНИИ ПРОИЗВОДСТВА
ГОРЯЧЕКАТАНОЙ ЛИСТОВОЙ СТАЛИ
НА НЕПРЕРЫВНОМ СТАНЕ
4.1. Схема производства и характеристика
технологических операций
В настоящее время основное количество листовой стали толщиной от 1,2 до 16 мм получают на непрерывных станах горячей прокатки.
В Российской Федерации установлены три таких современных стана 2000: на Новолипецком, Череповецком и Магнитогорском металлургических комбинатах. Технические параметры этих станов представлены в табл.7.
Технологический процесс производства на участках горячей прокатки с непрерывными широкополосными станами осуществляется по следующей принципиальной схеме:
- нагрев слябов в методических печах до заданной температуры в зависимости от марки стали;
- прокатка в черновой группе до толщины подката 25 – 50 мм;
- прокатка в чистовой группе до заданной толщины полосы;
- охлаждение полосы на отводящем рольганге до требуемой температуры смотки;
- смотка полосы в рулон на моталках;
- передача рулонов на склад готовой продукции цеха, либо в отделение отделки горячекатаных рулонов, либо в цех холодной прокатки.
Все технологические операции от посада слябов в нагревательные печи до выдачи рулонов на склад готовой продукции проводятся в едином технологическом потоке стана.
Компоновка оборудования непрерывных широкополосных станов характеризуется высокой степенью поточности технологического процесса (рис.3) и определяется сортаментом, объемом производства, принятой технологической схемой и перспективой развития.
Стан 2000 Новолипецкого металлургического комбината введен в эксплуатацию в 1969 году. Он предназначен для производства листа толщиной 1,2-16 мм и шириной 900-1850 мм из слябов толщиной 200-250 мм, длиной до 10,5 м и массой до 36 т.
Таблица 7
Технические параметры современных непрерывных
широкополосных станов горячей прокатки
Параметры | Стан 1700 НЛМК | Стан 2000 ЧерМК | Стан 2000 ММК |
Размеры полосы, мм: толщина ширина | 1,2 – 16 900 – 1850 | 1,2 – 16 900 – 1930 | 1,2 – 16 750 – 1850 |
Диаметр рулона, мм: внутренний наружный |
![]() |
![]() |
![]() |
Размеры исходного сляба, мм: толщина ширина длина Масса сляба, т | 200 – 250 900 – 1850 4000-10500 10 – 36 | 150 – 250 950 – 1850 4500-10500 4 – 36 | 750 – 1850 480-12000 до 45 |
Число и тип рабочих клетей: черновой группы чистовой группы | 1 вертикальная, 1 дуо горизонтальная, 4 кварто универсальные 7 кварто | 1 вертикальная, 1 дуо горизонтальная, 4 кварто универсальные 7 кварто | 1 вертикальная, 1 дуо горизонтальная, 5 кварто универсальные 7 кварто |
Мощность главных приводов, кВт: черновой группы чистовой группы суммарная стана Максимальная скорость прокатки, м/с | |||
Противоизгиб валков | - | Рабочих в клетях 5, 6, 7 чистовой группы | Рабочих в клетях чистовой группы |
Количество моталок: конечных промежуточных | |||
Удельная масса рулона максимальная, т/м | 20,5 | 20,5 | 20,5 |
Годовая производительность, млн. т | 6,1 | 6,3 | 5,5 |
![]() ![]() |
![]() |
![]() |
![]() |
Нагрев слябов до 1180-1280о С производится пятью методическими нагревающими печами производительностью 250-320 т/ч каждая при холодном посаде. Первые три печи толкательного типа, а четвертая и пятая — с шагающими балками.
Черновая группа стана состоит из вертикального окалиноломателя, двухвалковой клети и четырех универсальных четырехвалковых клетей. Чистовая группа — из двухвалкового окалиноломателя с горизонтальными валками и семи четырехвалковых клетей, объединенных в непрерывную группу.
Во время нагрева сляб в печи интенсивно окисляется раскаленными газами и покрывается толстым слоем окалины. Чтобы окалина не вдавливалась в металл при прокатке, ее удаляют в вертикальном окалиноломателе. Сляб обжимается с боков на 15-80 мм, хрупкая окалина отслаивается с его поверхности и сбивается водой, подаваемой под давлением до 15 МПа.
Клети черновой группы находятся на значительном удалении друг от друга и раскат, прежде чем войти в последующую клеть, полностью выходит из предыдущей. Обжатие в вертикальных валках черновых универсальных клетей принимают таким, чтобы компенсировать естественное уширение металла при прокатке в горизонтальных валках. На выходе раската за каждой клетью установлен гидросбив для удаления окалины.
После прокатки в черновой группе подкат толщиной 25-50 мм с температурой 1000-1120о С (меньшее значение температуры соответствует меньшей толщине подката) по промежуточному рольгангу поступает в чистовую группу клетей.
Перед чистовой группой установлены ножницы для обрези переднего и заднего концов раската. В чистовом окалиноломателе валки прижимаются к металлу с помощью пружинных стаканов. При обжатии полосы на 0,2-0,4 мм разрушается слой окалины, образовавшийся при прохождении промежуточного рольганга. Раздробленная окалина удаляется гидросбивом. Клети чистовой группы расположены на близком расстоянии друг от друга и полоса при прокатке может одновременно находиться во всех клетях.
Для получения стали с мелким и равномерным зерном прокатку в последней клети необходимо проводить при температуре 850-950о С, а смотку полосы в рулон — 500-650о С. Для ускоренного охлаждения раскатов над отводящим рольгангом и под ним установлены устройства для интенсивной подачи воды (до 12000 мз/ч).
Передний конец полосы заправляют в моталку при скорости прокатки не выше 10 м/с, а затем ее повышают домаксимальной (20 м/с). При этом ускорение составляет 0,05-0,1 м/с2, что способствует выравниванию температуры по длине полосы (при ускорении происходит разогрев металла по длине из-за увеличивающейся скорости деформации).
Смотка полос осуществляется в одной из двух групп моталок. Ближайшая к клетям группа моталок предназначена для быстро остывающих полос толщиной 1,2-5 мм, а дальняя — для более толстых. После смотки рулоны поступают по подземному конвейеру в цех холодной прокатки или в отделение отделки горячекатаных рулонов.
Стан 2000 Череповецкого металлургического комбината (1975 г.) аналогичен стану 2000 Новолипецкого металлургического комбината. Основные отличия состоят в следующем:
— установлено четыре нагревательных печи с шагающими балками;
— три последние черновые клети объединены в непрерывную подгруппу, что позволило сократить длину черновой группы на 83 м;
— в чистовой группе предусмотрена возможность установки восьмой клети.
Непрерывный стан 2000 ОАО "ММК" является последним из серии таких станов, спроектированных и изготовленных производственным объединением "Ново-Краматорский машиностроительный завод". Стан предназначен для производства горячекатаных полос из непрерывно-литых слябов массой до 45 т, толщиной 250 мм, шириной 750-1850 мм и длиной 4,8-12 м. Нагрев слябов до температуры прокатки производится в трех методических печах с шагающими балками. Производительность каждой печи 460 т/ч. В дальнейшем предусмотрена установка четвертой печи. Стан имеет черновую группу, включающую вертикальный окалиноломатель, двухвалковую клеть и пять универсальных клетей кварто, из которых три последних объединены в непрерывную подгруппу, а также чистовую группу в составе горизонтального окалиноломателя и семи клетей кварто (предусмотрена возможность установки восьмой клети).
4.2. Расчет режимов обжатий
Расчет режима обжатий в клетях черновой группы аналогичен расчету для толстолистового стана. Допустимые относительные обжатия в клетях черновой группы стана 2000 приведены в табл. 8 [4].
Таблица 8
Допустимые обжатия в черновой группе клетей стана 2000
Допустимые обжатия, % | ||
Клеть | полосы шириной до 1450 мм | полосы шириной более 1450 мм |
Клеть дуо | ||
Первая универсальная клеть | ||
Вторая универсальная клеть | ||
Последние универсальные клети |
Толщина раскатов, выдаваемых из черновой группы клетей в чистовую, определяется толщиной готового листа [4].
Толщина раската перед непрерывной группой, мм | Толщина готового листа, мм |
25-32 25-36 28-36 35-40 | 1,2-1,5 1,8-2,0 2,5-3,0 3,5-12 |
Обжатия по клетям чистовой группы целесообразно рассчитывать из условия обеспечения заданной загрузкиэлектродвигателей в соответствии с рекомендациями И. Имаи [6]:
(43)
где Н — толщина раската перед чистовой группой, мм;
h — толщина готового листа, мм;
m — коэффициент, зависящий от конечной толщины,
m = 0,3 + 0,21/ h;
— коэффициент загрузки электродвигателей клети, определенный как отношение суммы потребляемой на прокатку мощности в клетях от первой до i -й к общей мощности прокатки во всех клетях чистовой группы,
где n — число клетей чистовой группы.
При определении следует использовать данные табл.9.
Таблица 9
Мощности двигателей клетей чистовых групп, кВт [8.9]
Клети чистовой группы | НЛМК | ЧерМК | ММК |
Основным условием непрерывного процесса прокатки является постоянство секундного объема металла, проходящего через любую клеть стана. Это условие выражается уравнением
(44)
где F1, F2, F3, Fi — площади поперечных сечений прокатываемой полосы на выходе из клетей;
V1, V2, V3 ..., Vi — скорости прокатки в клетях.
Площадь поперечного сечения полосы на выходе из клети определяется по формуле
где — ширина полосы после i -й клети.
Для широкополосной листовой прокатки характерно смещение частиц металла преимущественно по направлению прокатки. Поэтому ширина полосы в чистовой группе изменяется незначительно и ее допустимо считать постоянной:
Тогда скорость прокатки в любой клети можно определить по формуле
(45)
где — скорость прокатки в последней клети чистовой группы, м/с.
При прокатке без ускорения непрерывной группы клетей составляет 10 м/с для полосы толщиной 1,2 мм; 9,8 м/с — для 1,5 мм; 9,3 м/с — для 2 мм; 8,5 м/с — для 3 мм; 6,8 м/с — для 4 мм; 6 м/с — для 6 мм; 3,8 м/с — для 8 мм.
Пример 4. Расчет режима обжатий и скорости прокатки на стане 2000 ОАО "ММК".
Расчет будем вести для полосы сечением 2х1600 мм. Размеры исходного сляба принимаем 250х1600х10000 мм. Для полосы толщиной 2мм раскат перед непрерывной группой должен иметь толщину 25 – 36 мм (выбираем 30 мм).
Суммарное обжатие в черновой группе клетей
.
Принимаем абсолютное обжатие в клети дуо h 1 = 30 мм, в универсальных клетях соответственно
h 2 = 50 мм;
h 3 = 45 мм;
h 4 = 40 мм;
h 5 = 35 мм;
h 6 = 20 мм.
Определяем относительные обжатия и сравниваем их с допустимыми из табл.8:
;
Во всех клетях черновой группы выбранные обжатия не превышают допустимых.
По формулам (31) и (32) определяем коэффициент вытяжки и длину раската
.
Длина раската после черновой группы = 83,49 м, и он может свободно разместиться на промежуточном рольганге длиной 146,2 м (см.рис.3).
Обжатия в чистовой группе рассчитываем по формуле (43).
Общая мощность двигателей во всех клетях чистовой группы
93200 кВт.
Определяем коэффициенты вытяжки и длину раската
Рассчитываем скорость прокатки в клетях стана при =9,3 м/с (прокатка без ускорения)
Машинное время прокатки в любой клети чистовой группы одинаково и составляет
Расчет температурного режима прокатки тонких полос (в непрерывной группе клетей) можно выполнять, используя упрощенное уравнение В. А. Тягунова [4]:
, (46)
где — снижение температуры полосы из-за теплоизлучения, оС;
t - начальная температура полосы, оС;
— время охлаждения, с;
h — толщина полосы, мм.
Пример 5. Расчет температурного режима прокатки в чистовой группе клетей стана 2000 полосы сечением 2х1600 мм из промежуточного раската толщиной 30 мм (исходные данные берутся из примера 4). Температура перед непрерывной группой 1015о С.
Расстояние между всеми клетями чистовой группы по 6 м (см. рис. 3). Промежуток между 1 и 2 клетями полоса пройдет за время
Следующие межклетьевые промежутки будут пройдены:
За время прохождения расстояния между 1 и 2 клетями передний конец полосы, имевший в первой клети температуру , остынет на величину
Температура переднего конца полосы во второй клети
.
Аналогично для следующих клетей:
Задний конец раската подойдет по промежуточному рольгангу к первой клети после того, как будет прокатана вся полоса в этой клети, то есть через . За это время задний конец остынет на величину
Температура заднего конца раската в первой клети
Далее считаем потери тепла излучением и температуру в клетях заднего конца полосы:
Таким образом, после прокатки в чистовой группе без ускорения, разница в температурах переднего и заднего концов полосы составит
Расчет сопротивления металла пластической деформации, усилия и момента прокатки выполняется по формулам (36)-(41).
Радиус рабочих валков чистовых клетей стана 2000 ОАО "ММК" R = 0,425 м, для других станов 2000 — R = 0,4 м. Для первых клетей непрерывной группы коэффициент приложения равнодействующей y можно принять равным 0,48, в последних — y = 0,34 [9].
4.3. Определение производительности стана,
площади складов металла,
расхода энергоносителей, материалов
и инструмента
Часовую, среднюю часовую и годовую производительность стана определяем по формулам (1), (6) и (7).
Коэффициент использования полунепрерывных и непрерывных широкополосных станов горячей прокатки равен 0,9 (при прокатке полос толщиной менее 2 мм kи = 0,75) [9].
Коэффициент расхода металла при производстве стали в рулонах без обрезки кромок:
— кипящей углеродистой — 1,02-1,05;
— спокойной углеродистой и низколегированной — 1,03-1,075;
— легированной — 1,04-1,1.
Число часов работы в году непрерывного стана горячей прокатки составляет 7000.
Емкость и площадь складов слябов и готовой продукции определяем по формулам (20), (21).
Слябыукладывают пачками в стопы высотой до 3 м или в штабель крест-накрест высотой до 4м. Удельная нагрузка q на данном складе составляет 120 кН/м2.
Около 40% горячекатаных рулонов по межцеховому конвейеру сразу передаются в цех холодной прокатки. Оставшиеся 60% укладываются в штабель-пирамиду в вертикальном положении оси рулона, в несколько рядов высотой до 4,5м и хранятся до отгрузки потребителю. Удельная нагрузка q на складе готовой продукции составляет 80 – 110 кН/м2. Нагрузка зависит от удельной массы рулона на 1 м ширины рулона.
Расходные коэффициенты для определения годовой потреб-
ности цеха в различных ресурсах по формуле (22) [1,2]:
электроэнергия, кВт×ч/т 60-70
вода, мз/т 40
сжатый воздух, мз/т 15
пар, кг/т 30
топливо, кДж/т 2,28×106
смазочные материалы, кг/т:
густые 0,15
жидкие 0,35
огнеупоры для печей, кг/т 0,6
валки, кг/т 1-1,1
Дата добавления: 2016-01-05; просмотров: 59; Мы поможем в написании вашей работы! |
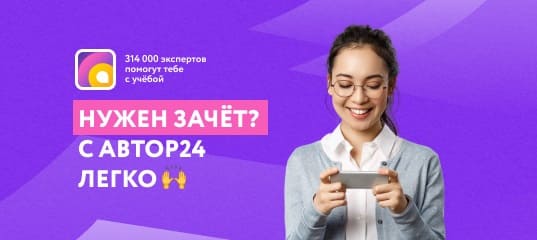
Мы поможем в написании ваших работ!