Читайте также: Инструкция для ремонта рено премиум
Рис. 1. Схема технологического процесса ремонта трактора АСХГЗ-НАГИ в мастерской МТС при узловом методе
Наибольшее количество ремонта по тракторам за всё время их эксплуатации проводится мастерскими МТС (см. Ремонтные мастерские). Ремонт тракторов в мастерских выполняется по определённому технологическому процессу. Этот процесс состоит из ряда последовательно (а на нек-рых этапах и параллельно) выполняемых подготовительных, разборочных, ремонтных, сборочных, контрольных, испытательных и заключительных операций. В мастерских МТС наибольшее распространение имеет орг-ция технологического процесса ремонта тракторов узловым методом. На рис. 1 приведена схема технологического процесса ремонта узловым методом трактора АСХТЗ-НАТИ в мастерской МТС. На каждый трактор (или на отдельный его агрегат или узел), поступивший в ремонт, оформляют заказ, составляют дефектовочную ведомость и затем на определённых рабочих местах мастерской выполняют отдельные операции или процессы этого ремонта. Первая операции — это наружная очистка и мойка трактора, удаление накипи в системе охлаждения (последнее часто выполняется в предремонтный период эксплуатации тракторов). Затем идут операции разборки трактора на узлы и детали, мойка деталей, осмотр и выбраковка, ремонт деталей, комплектование узлов, сборка узлов и механизмов, их испытание и сборка всего трактора. При узловом методе ремонта тракторов заранее организуют весь комплекс работ, составляющий полный технологический процесс ремонта трактора по узлам. Соответственно специфическим особенностям операций, входящих в ремонт того или др. узла, в ремонтной мастерской организуют отдельные специализированные рабочие места, посты или цехи, оборудование к-рых приспосабливают к наилучшему выполнению ремонтных работ по этим узлам.
|
|
Все ремонтные работы на каждом рабочем месте (посту, в цехе) мастерской проводятся рабочими, подчинёнными руноводству и контрольному аппарату мастерской. За определёнными рабочими местами закрзпляются постоянные рабочие на весь период ремонта. Мастерская МТС при узловом методе ремонта представляет собой организованное предприятие, выполняющее запланированную программу ремонтных работ. Работы выполняют рабочие на специализированных рабочих местах посредством приспособлений и инструментов (см. Ремонтное оборудование). При узловом методе ремонта операции технологического процесса ремонта разделяются по рабочим местам на основании расчёта загрузки каждого рабочего, занятого на том или другом рабочем месте мастерской. Так. обр., напр., рабочий, выполняя работы по ремонту карбюратора, догружается работами по ремонту деталей регулятора. Рабочий, занятый ремонтом вентилятора и муфты сцепления, догружается работами по ремонту масляного насоса, фильтра и т. д. Создаются условия, способствующие повышению квалификации ремонтных рабочих.
|
|
При узловом методе ремонта не все узлы трактора разбирают на детали. Ряд узлов и агрегатов трактора без детальной разборки их, после наружной мойки, направляют непосредственно на рабочие места. К таким узлам, напр., по трактору АСХТЗ-НАТИ относятся: электрооборудование, карбюратор, регулятор и мостик магнето, вентилятор, масляный насос и фильтры, сливной клапан, головка цилиндра с клапанным механизмом, шатуны с крышками и вкладышами, коленчатый и распределительный валы, главное сцепление, радиатор, баки, воздухоочиститель, коробка передач, крышка с рычагом переключения, коробка рулевого управления, бортовые фрикционы с валом, пусковая рукоятка, гусеницы. Осуществление узлового метода ремонта требует: 1) общего улучшения работы мастерской (обеспечения чистоты рабочих мест, приведения в исправность оборудования, правильной планировки цехов); 2) орг-ции и оборудования специализированных рабочих мест (постов, цехов) мастерских, согласно технологической схеме ремонта; 3) расстановки рабочей силы по рабочим местам и точного ознакомления каждого рабочего с объёмом выполняемых им работ; 4) обеспечения каждого рабочего места необходимой технической документацией для ремонта. Кроме того, при узловом методе мастерская обеспечивает быстрое и своевременное восстановление имеющегося в МТС оборотного фонда запасных узлов и агрегатов к тракторам.
|
|
На рис. 2 представлена схема орг-ции ремонта тракторов в мастерской МТС узловым методом. В мастерской МТС организуют и оборудуют указанные на этой схеме рабочие места, напр. рабочее место № 1 устраивают для наружной мойки и промывки системы охлаждения (см. Моечные машины). Далее организуют рабочие места № 2 по разборке трактора и № 3 — по разборке двигателя. Непосредственно за рабочим местом разборки трактора и рабочим местом разборки двигателя располагается рабочее место № 4 по мойке деталей и узлов. Следующее рабочее место № 5 предназначено для осмотра и выбраковки деталей. При узловом методе ремонта большая часть объёма работ по осмотру и выбраковке выполняется непосредственно около мойки (рабочее место № 4), но нек-рая часть этих работ производится на рабочих местах ремонта узлов и агрегатов, т. к. нек-рые узлы разбираются только на рабочих местах их ремонта. После осмотра невыбракованные детали и узлы доставляют на соответствующие рабочие места для ремонта, выбракованные детали — в утиль. Детали, допустимые к постановке на трактор без ремонта, доставляют на рабочее место № 6 — по комплектовке. От налаженной работы комплектовочной во многом зависит качество работы всех рабочих мест по ремонту узлов трактора. Новые запасные части из склада, восстановленные или отремонтированные части из цехов поступают на соответствующие рабочие места для постановки в узлы только через комплектовочную. Комплектовочную располагают в центре мастерской, чтобы бесперебойно обслуживать все рабочие места. Все остальные рабочие места по ремонту тракторов располагают в мастерской примерно в том порядке, в каком они расположены на схеме.
|
|
Нек-рые рабочие места, организуемые в мастерских по ремонту тракторов, сходны с соответствующими рабочими местами в пром. предприятиях (рабочие места токаря, слесаря, кузнеца, инструментальщика и т. п.). Но большая часть рабочих мест, необходимых для ремонта тракторов, имеет много специфических, отличительных черт как в орг-ции, так и в оборудовании (см. Ремонтное оборудование). Заливка подшипников, т. е. покрытие антифрикционным сплавом (см.), в ремонте тракторов представляет собой одну из наиболее сложных и часто повторяемых ремонтных операций. Заливка производится на рабочем месте, к-рое имеет спец. верстак, разделённый на 3 части: 1) для подготовки подшипников к заливке (выплавка старого сплава, правка вкладышей и т.п.); 2) для плавки антифрикционного металла и заливки подшипников; 3) для первичной обработки залитых подшипников (удаление литников, зачистка тыльной стороны подшипника и т. п.). На верстаке располагают требуемые приспособления и инструменты. Подобная специфическая особенность оборудования рабочих мест по ремонту характерна для рабочих мест по ремонту головок цилиндров и клапанного механизма, по ремонту шатунно-поршневой группы, по ремонту муфты сцепления и др.
При ремонте тракторов производятся разные виды холодной и горячей обработки металлов, гидравлические испытания, различные виды измерений, контроля и т. п. Из видов холодной обработки металлов наиболее часто применяют след.: опиливание напильником или припиливание — для подгонки шпонок, стыков поршневых колец, для заправки помятых граней гаек и головок болтов, для подгонки торцов подшипников скольжения, для выравнивания плоскостей разъёма деталей, имеющих коробление, и т. п.; шабрение торцовым, трёхгранным или лапчатым шабером для выравнивания поверхностей особо ответственных деталей с целью устранения неровностей износа или коробления, для окончательной подгонки скользящих подшипников и т. п.; обточку или растачивание резцами на токарных или спец. станках для обработки различных деталейтракторов с целью удаления неровностей износа и восстановления форм деталей, напр.: растачивание гильз, цилиндров, обточка корпусов подшипников под добавочное кольцо или втулку, обточка деталей после обварки или наварки для устранения неровностей, изготовление втулок, болтов, шпилек и др. деталей спец. ремонтных размеров и т. п.; сверление — свёрлами на сверлильных станках, дрелью или приспособлением с трещёткой; сверлением удаляют из резьбовых гнёзд отломанные шпильки и болты, а также восстанавливают формы отверстий под детали креплений ремонтными размерами или постановкой проходных втулок и т. и.; строжку — резцами на строгальных станках или спец. приспособлениях для обработки поверхностей (рамы, корпуса коробки передач и др.), требующих восстановления плоскостности после износа или после заварки неровностей износа или для подготовки детали под добавочные пластинчатые накладки и т. п.; фрезерование — фрезами на фрезерных станках или спец. приспособлениях для обработки новых шпоночных канавок и шлицевых пазов в валах, шестернях, шкивах и т. п. вместо разрушенных старых канавок и пазов, а также для обработки плоских поверхностей поверхностей гнёзд клапанов и т. п.; шлифование — шлифовальными камнями на шлифовальных станках или спец. приспособлениях и приборах для устранения неровностей износа фасок клапанов, для устранения эллипсности шеек коленчатых и др. валов, для устранения эллипсности и конусности гильз цилиндров и т. п.; полирование — тонкими абразивно действующими пастами или полирующими мастиками, наносимыми на быстро вращающийся предмет (полирующий фетровый круг, притирочный стержень или втулку и т. п.); полировкой улучшают поверхность детали для лучшей теплоотдачи и смазки (шейки коленчатых валов, гильзы цилиндров), точной подгонки деталей по размеру (плунжер-гильза насосных элементов дизельной топливной аппаратуры) или для придания блеска и внешней отделки деталей (отражатели фар); притирку одной детали по другой с применением абразивных паст для окончательной обработки сопрягающихся деталей, требующих герметичности в соединениях без уплотнительных деталей (клапан — гнездо клапана, пробка крана — корпус и т. п.); развёртывание ручными или машинными развёртками (раздвижными или с постоянным размером) для подгонки расточенных отверстий, гл. обр. небольшого диам. (до 50 мм), под размер сопрягаемых шлифованных валов (подгонка втулок масляного насоса под размер валика, подгонка втулок шатунов или отверстий в поршнях под поршневой палец и т. д.).
Рис. 2. Схема организации ремонта тракторов в мастерской МТС узловым методом: 1 — наружная мойка трактора; 2, 3- разборка трактора и двигателя; 4 — мойка узлов и деталей; 5 — дефектовка деталей; в — комплектовка деталей для сборки узлов; 7, 8, 18, 34, 35 — работы выполняются в ММКР и РЗ; 9, 20, 21 — заливка подшипников, ремонт радиаторов, термостата, баков и воздухоочистителей; 10 — расточка подшипников и укладка коленчатого вала; 11 — ремонт и подгонка деталей шатунно-поршневой группы; 12 — ремонт блока; 13 — сборка двигателя; 14 — ремонт деталей и сборка головки цилиндров и клапанного механизма; 15 — ремонт и сборка масляного насоса, водяного насоса, испытание масляного насоса и сервомеханизма (С-80); 16 — ремонт деталей, сборка, испытание и регулировка карбюратора и дизельной топливной аппаратуры; 17 — ремонт электрооборудования; 19 — ремонт вентилятора, муфты сцепления и тормозных лент; 22 — обкатка и испытание двигателя; 23 — ремонт коробки передач, механизма переключения, кардана, механизма выключения пускового двигателя; 24 — ремонт корпуса заднего моста, рамы и поперечных брусьев; 25 — ремонт рулевого управления поддерживающих роликов, подвески трактора и гусеницы; 26 — ремонт диференциала, малых шестерён бортовых фрикционов, вала заднего моста; 27 — переклёпка рамы, прицепного устройства, крыльев, капота, кабины, сиденья; 28 — сборка заднего моста и ходовой части; 29 — окончательная сборка трактора, обкатка его; 30, 31 — слесарно-механические работы; 32 — сварочные работы; 33 — кузнечные работы; 36 — склад запасных частей; 37 — склад инструмента (инструментальная); 38 — склад материалов; 39 — склад топлива и смазочных материалов
Дата добавления: 2022-06-11; просмотров: 25; Мы поможем в написании вашей работы! |
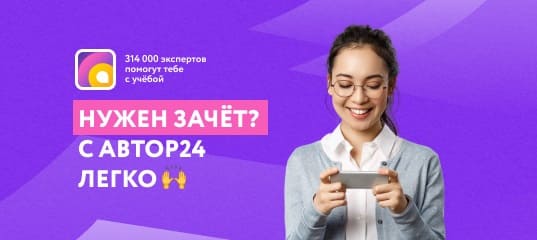
Мы поможем в написании ваших работ!