Января И дня 172? года Поввлевдю хозяина Тульской
ФЛБрИКН КорНКАу БСЛОГЛАЗОВД
Енть. кнутом н сослать на рАвоту в монастыря, понеже он, подлец, осмелился войску Государства продлвдть негодные пнщдли к фузен.
СтАршнну Дльдер.ндлА фрфла Фукса вить кнутом н сослать в Азов, пусть не ставит клсйла на плоуие ружья.
Приказано оружейной клнцелярнн из ПетереуугА переехлть в Тулу н денно н нощно блюсти нспрдвность ружей. Пусть дьякн н подьячие смотрят,
КАК АЛЬДбрМАЛЫ КЛ6К.НА СТАВЯТ, БуДС
солтвмне возьмет, сдлш,н прове|жть н ос.иотро-и м стрелькою. А двл ружья каждый .иееяц стрелять пока не испортятся.
Буде ЗАМИнка в войске приключиться при сражения по недогляду дьяков н подьячих вить оных кнутьялш нбщддно по оголбнио.ну месту.
Хозяину — 25 кнутов м пени по червонцу за ружь.
Отлршкку Дльдбрмллд — вить до
БбСНуСТВМЯ.
СтАршего дьякл отдать, в унтер-офицеры.
Дьяка — ОТДАТЬ Б ПКСАрН.
Подьячего амшнть воскресной чдркн срок&н н« одингод.
Новому хозяину ружейной флврнки Демидову повелевдю построить дьяк&н н подьячим нзеы, дабы не ууже хозяйской выли, вуде хуже, пусть Демидов не обижастся, поведевлю
ЖИВОТА ЛИШИТЬ.
Петр I
67 |
/лавя1. ОТЕЧЕСТВЕННЫЙ ОПЫТ УПРАВЛЕНИЯ КАЧЕСТВОМ ПРОДУКЦИИ
Особое внимание уделил Петр I стандартизации оружейного снаряжения. Так, в указе № 2436 от 15 февраля 1712 г. сказано: «А ружье драгунское, так и солдатское, также и пистолеты, когда будет поведено, делать одним калибером».
|
|
В контексте рассматриваемого вопроса об управлении качеством несомненный интерес представляет Указ Петра I о качестве от 11 января 1723 года. Из текста Указа ясны не только требования Государя к качеству продукции (в данном случае — ружья для армии), но и к системе контроля качества, государственного надзора за ним и меры наказания за выпуск дефектной продукции (текст Указа прилагается).
Стремясь к расширению внешней торговли, Петр I не только ввел технические условия, учитывающие высокие требования иностранных рынков к качеству отечественных товаров, но и организовал в Петербурге и Архангельске правительственные бракеражные комиссии, которым вменялось в обязанность следить за качеством экспортируемого Россией сырья (льна, пеньки, древесины и т. д.).
Развитие промышленности и транспорта в России привело к расширению работ по стандартизации. В 1860 году был установлен единый размер железнодорожной колеи (1524 мм) и утверждены габаритные нормы приближения строений и подвижного состава. В 1889 году приняты первые технические условия на проектирование и сооружение железных дорог, а в 1898 году — единые технические требования к поставке основных материалов и изделий для нужд железнодорожного транспорта. В 1899 году был выпущен единый сортамент профилей прокатной стали.
|
|
В 1900 году был принят ряд правил и норм проектирования и эксплуатации электротехнических устройств.
Внедрение российских национальных стандартов и единых требований к качеству продукции в дореволюционной России затруднялось из-за большого числа иностранных концессий, владельцы которых применяли, как правило, свои стандарты. Такое положение привело, в частности, к распространению в России трех систем мер (аршинной, дюймовой, метрической), которые затрудняли производство продукции и контроль ее качества.
Одним из первых после революции был принят декрет «О введении международной метрической системы мер и весов» (14 сентября 1918 г.), имевший важное значение для развития стандартизации. В 1925 г. создается Комитет по стандартизации, на который возлагается руководство работами по стандартизации в стране и утверждение стандартов, обязательных для всех отраслей народного хозяйства. В 1926 г. был утвержден первый общесоюзный стандарт ОСТ 1 «Пшеница. Селекционные сорта зерна. Номенклатура». В том же году были приняты стандарты на новый сортамент стального проката, что позволило сократить число типоразмеров профилей в 6 раз, а также стандарты на метрическую и дюймовую резьбу, на допуски и посадки, что позволило наладить серийное и массовое производство стандартных общемашиностроительных деталей. Эти стандарты стали основой для овладения методами передовых зарубежных фирм, таких, как Форд, Тейлор, по контролю качества продукции на основе системы допусков и посадок.
|
|
Таким образом, одной из первых форм управления качеством стала проверка изделий методом сортировки и разбраковки на годные и негодные.
б»_________Часть 2. ОТЕЧЕСТВЕННЫЙ И ЗАРУБЕЖНЫЙ ОПЫТ УПРАВЛЕНИЯ КА ЧЕСТВОМ
1.2. Развитие контроля качества
Первостепенная необходимость контроля качества с целью получения данных об объекте управления отражена в ГОСТ 15467-79: «Управление качеством продукции — установление, обеспечение и поддержание необходимого уровня качества продукции при ее разработке, производстве и эксплуатации или потреблении, осуществляемое путем систематического контроля качества и целенаправленного воздействия на условия и факторы, влияющие на качество продукции».
Рассмотрим взаимосвязанные вопросы, составляющие историческую последовательность развития управления качеством продукции в нашей стране:
|
|
• контроль качества продукции;
• оценка качества продукции;
• управление качеством продукции (УКП); этапы системного подхода в УКП;
• взаимосвязь непосредственного УКП с обеспечивающими его факторами (роль государства, государственная система стандартизации, гармонизация с международными стандартами и др.).
Технический контроль качества лежит в основе любого способа управления качеством как у нас, так и за рубежом.
Организация контроля качества — это система технических и административных мероприятий, направленных на обеспечение производства продукции, полностью соответствующей требованиям НД — нормативных документов.Технический контроль — это проверка соответствия объекта контроля установленным техническим требованиям.
Под контролем качества (КК) понимается проверка соответствия количественных или качественных характеристик продукции или процесса, от которого зависит качество продукции, установленным техническим требованиям.
Суть контроля заключается в получении информации о состоянии объекта контроля и сопоставлении полученных результатов с установленными требованиями, зафиксированными в чертежах, стандартах, ТУ, договорах на поставку и т. п. документах.
Основные термины и определения контроля установлены ГОСТ 16-504-81.
Это объект контроля, метод контроля, исполнители контроля и документация на проведение контроля. Метод контроля допускает применение определенных средств измерений и контрольных образцов (утвержденных единиц продукции, как образцовых).
Классификация видов контроля дана на рис. 2.1.
КК на предприятии осуществляют изготовители продукции и производственные мастера; работники ОТК — отдела технического контроля (рис. 2.2), рабочие, переведенные на самоконтроль, представители заказчика на предприятии (если это оговорено в контракте на поставку).
Сложность проблемы качества требует комплексного подхода к организации службы качества предприятия, в которой целесообразно объединить не только подразделение, осуществляющее контроль
»——.^...——..м——•—««——|•»•^^»^^»»^^...——...............^——.^^ _, Ручной
ПгУ^^ЖЗЩ'!** ••!''• ^'•^^^Щ ^^^и1ВХОДНОЙ 1Е)^^^^^^^*у^^,^^^:
1 — Механизированный
— Йрацейса !Ц-^^Операционный РЙЙ^ЙВИВ
Й^_„_Й | • ЙИВявсквИ138""—~ Автоматизированные системы^К''3^!0'^^— Приемочный — Автоматические системы ~~ Активный контроль |— Сплошной _________ Н' ^л^^^»1т^1^1^11 ^™ самоконтроль I- ^ Непрерывный • 8|гааизации а—1 Одноступенчатый (к. исполнителя —Периодический Й^' Э | + приемка ОТК) «— Летучий ^~————— Многоступенчатый (к. исполнителя + операционный контроль + специальный + приемочный) |— Контроль качества продукции — Контроль товарной и сопроводительной документации [Во-вдиянию^нЯ В^ Контроль технологического процесса |§аэмвэкйЙе№Д8 _ -—Контроль средств технологического I Д
ЩД|^ Разрушающий оснащения Ц|Й||Ь»^^№|: |1_ Не разрушающий — Контроль технологической дисциплины — Контроль квалификации исполнителен —— Контроль прохождения рекламаций __ Контроль соблюдения условий эксплуатации
Рис. 2.1. Классификация видов технического контроля
тва.'^-^'-1^ | '^:д^я1 | т | ^^Я4 | * я1 | „Йа»,й,я-й^ | |||||||||
.'/^^Й^й^^ИЯвЙ^!» | ^^^ | | | ||||||||||||
| | | | | | ... | .„„.„ | Ч | |||||||||
/• \ Планирование качества и планирование | [ Управ | качес] | эление гвом | Информация | о качестве | Лаборатория контро-^ ля качества | Пров качес | ерка | тва ] | (Измер ная те) | итель- [ хника | ^ | Обучение повышен квалифик | ей ие кации | |||
контроля | с \ | ^ | ||||||||||||
\- у | \ | |||||||||||||
-» ^ | ———— | —————. | Методы | и | ||||||||||
качества | | | Испытания ] | - | КВход | ной | | [ Прещ | изион- ) | средства | моти- | ||||||
1 ные ^ | редства | вации в с | эбла- | |||||||||||
качества и | качест | вом | ||||||||||||
надежности | постав | ЭДИКОВ | Обработка и | ^ ность ] | ении 1 | ния качес | ства | |||||||
г л | \. | |||||||||||||
\ Контроль | звод- ) | |||||||||||||
сферы произ- | | материалов | ствен | нын | Эдект | ронная | |||||||||
\^ ^/ | ||||||||||||||
контроля | • } | |||||||||||||
качества | собств | енном | эксплуатации \. ^ | ная те V | -/ | Специал | ьные | |||||||
\^ -/ | /' \ | \- | "\ | задачи в | рам- | |||||||||
Контроль | 4Финн | 1ШНЫИ | БМЫ | |||||||||||
Документация | моделей и | конт | >оль ] | |||||||||||
данных о | опытных | - • | \. | ^ | ||||||||||
применения | качестве | образцов ^ ^ | 1 средст измер | гв ений | ||||||||||
средств | ^ | |||||||||||||
контроля |
Рис. 2.3. Функции службы качества
72 |
Часть 2. ОТЕЧЕСТВЕННЫЙ И ЗАРУБЕЖНЫЙ ОПЫТ УПРАВЛЕНИЯ КАЧЕСТВОМ
качества, но и подразделения по организации всей работы в области обеспечения и анализа качества, а также стимулирования качества.
На рис. 2.3 представлены функции службы качества для крупного предприятия.
Планирование качества сводится к планированию качественных характеристик, планированию надежности изделий на стадии их разработки. Кроме того, надо заниматься подготовкой контроля и применения контрольных средств. При этом должны разрабатываться методы управления качеством как в собственном производстве, так и у поставщиков — смежников. Необходимо вести аналитическую работу — обработку и анализ данных по качеству и затратам на его обеспечение.
В систему контроля качества на крупных фирмах входят подразделения испытаний на надежность, контроля материалов, стендовой отработки и проверки макетов, опытных образцов продукции. Неотъемлемой частью работы по контролю качества является контроль покупных изделий, входной контроль на всех участках и технологических переходах в производстве, операционный и окончательный (финишный) контроль готовой продукции. К функции контроля непосредственно примыкает метрологическое обеспечение производства, которое позволяет осуществлять разработку, поверку и правильную эксплуатацию средств измерений, электронных, компьютерных устройств и контроль их состояния.
И, наконец, необходимо подготавливать программы и организовывать обучение и повышение квалификации кадров, обеспечивать мотивацию и стимулирование персонала для успешного решения задач качества.
Разумеется, не каждое предприятие способно содержать полностью развитую службу качества. Малые и средние предприятия, как правило, прибегают к услугам специализированных консультационных, инжиниринговых фирм, ограничиваясь, в лучшем случае, наличием одного инженера по качеству.
Научной основой современного технического контроля стали мате-матико-статистические методы. Управление качеством продукции может обеспечиваться двумя методами: посредством разбраковки изделий и путем повышения технологической точности. Издавна методы контроля сводились, как правило, к анализу брака путем сплошной проверки изделий на выходе. При массовом производстве такой контроль очень дорог: контрольный аппарат должен в 5—6 раз превышать количество производственных рабочих, и даже при этом нет полной гарантии от брака.
Поэтому от сплошного контроля переходят к выборочному с применением статистических методов обработки результатов. Однако такой контроль эффективен только тогда, когда технологические процессы, будучи в налаженном состоянии, обладают точностью и стабильностью, достаточной для «автоматической» гарантии изготовления бездефектной продукции. Отсюда встает необходимость стабилизировать производство. Самым надежным способом стабилизации производства является создание системы качества, а затем ее сертификация. Подробно об этом рассказывается в главе 3 части 5 учебника.
73 |
Глава 1. ОТЕЧЕСТВЕННЫЙ ОПЫТ УПРАВЛЕНИЯ КА ЧЕСТВОМ ПРОДУКЦИИ
СТАТИСТИЧЕСКИЕ МЕТОДЫ
Статистический анализ точности и стабильности технологи | Статистический приемочный | ||
ческих процессов и качества продукции | контроль качества продукции | ||
Статистическое регулирование | Статистические методы оценки | ||
технологических процессов | качества продукции |
Рис. 2.4. Области применения статистических методов управления качеством продукции
Основные области применения статистических методов УКП показаны на рис. 2.4.
Основные этапы, требующие применения статистических методов, приведены на рис. 2.5.
Причины изменений качества носят различный характер:
1. Случайныеизменения — это сумма многочисленных «случайных причин», влияние каждой из которых незначительно, причем отдельную причину для любой крупной составляющей совокупных изменений установить невозможно (например, множество сил, заставляющих монету падать «орлом» или «решкой» вверх при беспорядочном подбрасывании).
Производству и контролю всегда присуща стабильная «система случайных причин». Колебания вследствие такой стабильности модели неизбежны, но оказываются в состоянии статистического регулирования.
2. Неслучайные изменения — это изменения (колебания) вследствие «неслучайных причин» (причин систематических погрешностей), обычно характеризующих различия между рабочим, машинами, материалами, методами, в каждом факторе во времени.
При наличии «неслучайных причин» изменение в данных не следует ожидаемым схемам, и считается, что процесс «неуправляемый».
На рис. 2.6. показано различие в подходах к контролю производства. Если раньше традиционным способом считалось оценивание (контроль) изделий, то теперь есть стремление контролировать технологический процесс, характеристики которого позволяют оценивать и качество выпускаемой продукции.
Статистическое регулирование процессов обеспечивает систематический подход к оптимизации процессов. Оно (5РС) помогает:
Часть 2. ОТЕЧЕСТВЕННЫЙ И ЗАРУБЕЖНЫЙ ОПЫТ УПРАВЛЕНИЯ КАЧЕСТВОМ
Рис. 2.5. Основные этапы управления качеством продукции, требующие применения статистических методов
75 |
Глава!. ОТЕЧЕСТВЕННЫЙ ОПЫТУПРАВЛЕНИЯ КАЧЕСТВОМ ПРОДУКЦИИ
г |
традиционное регулирование ;
процессов \
человек машина материал метод условия (среда) |
не в порядке
брак,
дополнительная обработка
-процесс ——»> осмотр изделие
в порядке
новое регулирование процесса
человек машина материал метод условия (среда) |
•процесс изделие |
не в порядке |
анализ мероприятия |
оценка процесса |
в порядке
выбранные параметры измерения изделия и процесса
Рис. 2.6. Различные подходы к контролю производства
76 |
Часть 2. ОТЕЧЕСТВЕННЫЙ И ЗАРУБЕЖНЫЙ ОПЫТ УПРАВЛЕНИЯ КА ЧЕСТВОМ
• избавиться от отходов (потерь);
• выявить проблемные области (участки);
• избавиться от субъективности при принятии решений;
• снизить изменчивость (непостоянство, неустойчивость) процесса;
• достичь намеченной цели;
• определить момент достижения совершенства. Вместе с тем регулирование процессов с применением статистических методов не заменяет:
• решения проблем (принятия решений);
• вынесения надежных технических оценок;
• инженерного проектирования и научных разработок;
• оптимизации операций;
• методов проектирования, анализа и управления.
1.3. Разработка методов оценки качества продукции
Возникновение необходимостиоценок качества продукции исторически обусловлено разделением труда и появлением массового производства. Здесь можно выделить 3 этапа.Первый — этап непосредственного соединения человека со средствами производства, когда КП зависело от мастерства работника, его физического совершенства, органов его чувств. Изготовление и потребление продукции не было разделено ни в пространстве, ни во времени, поэтому необходимость в оценке отсутствовала.
На втором этапе — этапе машинного производства, с усилением разделения труда, развитием товарных отношений, когда продукция производится на неизвестного потребителя и в массовом количестве, возникает необходимость в получении объективной оценки КП; эта оценка должна нести информацию о потребности в той или иной продукции. Оценка качества здесь уже важна, но особая необходимость в ней приобретаетсяна третьем этапе — этапе автоматизированного производства в силу того, что продукция все более усложняется, одновременно предлагается до нескольких десятков разновидностей товаров одного и того же назначения, резко сокращается период между сменами моделей, возрастает серьезность последствий, к которым может привести неточная или ошибочная оценка.
До недавнего времени существовало много видов оценок для определения КП:
• соответствие КП действующей НД (стандартам, ТУ, договорам);
• оценка на предпроизводственной стадии при принятии решения о постановке продукции на производство или еще раньше, когда принимается решение о разработке продукции и ее параметры заносятся в карту технического уровня и качества; продукция на этой стадии сравнивается с аналогом, который уже до этого удовлетворял конкретную потребность;
• аттестация продукции по категориям качества;
• разбивка продукции по сортам;
• сертификация продукции;
77 |
/лева 1. ОТЕЧЕСТВЕННЫЙ ОПЫТ УПРАВЛЕНИЯ КАЧЕСТВОМ ПРОДУКЦИИ
• по результатам-испытаний опытных образцов;
• оценка экономичности продукции с точки зрения расходования ресурсов по себестоимости, ценам (оптовой и розничной), суммарным затратам (изготовления и эксплуатации);
• оценки КП торговыми органами для экспорта и внутренних нужд;
• оценка госприемкой.
Наличие большого количества видов оценок свидетельствовало о двух моментах: во-первых, проблема оценки считалась сложной задачей, во-вторых, признавалось, что в то время отсутствовали достаточно объективные методы по количественной оценке качества, которые принимались бы всеми потребителями. Именно такое положение дел с оценкой КП привело к усилению научных исследований в нашей стране по поиску объективных количественных оценок КП (также потребительной стоимости, полезности), а затем и к появлению научного направления, связанного с количественной оценкой качества, квалиметрией. Квалиметрия оперирует не с определением некоего абсолютного качества, а с относительными оценками и определяет качество по отношению к изделию, принятому за базу сравнения — уровень качества (ГОСТ 15467-79). Были введены понятия показателей качества продукции: единичный, комплексный, групповой, обобщенный, относительный, интегральный. Предлагалось учитывать только важнейшие свойства продукции при оценках КП. Среди оценок КП были дифференциальная, а также — надежности, технического и технико-экономичес-кого уровня качества. Первым этапом оценки КП являлся выбор номенклатуры показателей качества. В 1979 году ВНИИ Стандартизации Госстандарта предложил для оценки КП номенклатуру из 10 видов показателей; каждый из видов содержал множество более конкретных показателей. В зависимости от используемых средств методы измерения показателей качества подразделялись на измерительные, регистрационные, расчетные, органолептические, экспертные и др.
За базовую модель изделия выбиралась не только существующая, но и гипотетическая, отражающая самые различные уровни качества:
• средний достигнутый мировой;
• средний достигнутый народнохозяйственный;
• высший достигнутый народнохозяйственный;
• экономически оптимальный;
• перспективный народнохозяйственный;
• перспективный мировой.
Для получения относительных показателей качества в сопоставление оцениваемого и базового образца брались как единичные показатели (дифференциальная оценка), так и обобщенные (комплексная оценка). Следует еще раз отметить, что такой подход к оценке КП существует иногда и сейчас (например, при оценке уровня конкурентоспособности продукции), но за рубежом наши способы оценок КП не были приняты.
78 Часть 2. ОТЕЧЕСТВЕННЫЙ И ЗАРУБЕЖНЫЙ ОПЫТ УПРАВЛЕНИЯ КА ЧЕСТВОМ
1.4. Разработка системного подхода к управлению качеством продукции на отечественных предприятиях
Движение за улучшение качества продукции в России существовало с периода проведения индустриализации. С течением времени становилось ясно, что устойчивого совершенствования качества продукции нельзя добиться путем проведения отдельных и даже крупных, но разрозненных мероприятий. Только путем системного и комплексного, взаимосвязанного осуществления технических, организационных, экономических и социальных мероприятий на научной основе можно быстро и устойчиво совершенствовать КП (табл.2.1).
Факторы, влияющие на качество продукции, укрупненно могут быть представлены тремя блоками: качество производимой продукции зависит от внутренних (внутрифирменных) обстоятельств, человеческого фактора и внешних условий (рис. 2.7).
Проследим шаг за шагом последовательность воплощения системного подхода к организации работ по улучшению КП в отечественной практике.
1. В 1950-е годы получила распространениесаратовская система организации бездефектного изготовления продукции и сдачи ее с первого предъявления (БИП) (табл. 2.2).
Цель системы — создание условий производства, обеспечивающих изготовление рабочими продукции без отступлений от технической документации.
Основным критерием, применяемым для количественной оценки качества труда рабочего, явился процент сдачи продукции с первого предъявления, который исчисляется как процентное отношение количества партий, принятых с первого предъявления, к общему количеству партий, изготовленных рабочим и предъявленных ОТК.
От процента сдачи продукции с первого предъявления зависело по определенной шкале материальное и моральное стимулирование исполнителя.
Внедрение системы БИП позволило:
• обеспечить строгое выполнение технологических операций;
• повысить персональную ответственность рабочих за качественные результаты своего труда;
• более эффективно использовать моральное и материальное поощрение рабочих за качество их труда;
• создать предпосылки для широкого развертывания движения за повышение качества продукции.
Моральное стимулирование привело к появлению званий «Мастер золотые руки», «Отличник качества» и др. Со временем изменились функции ОТК — контроль велся выборочно, а в основе стал самоконтроль. Именно последний выявил дефекты, не зависящие от рабочего, что привело к проведению среди руководства «Дней качества» и созданию постоянно действующих комиссий по качеству. На ряде предприятии процент сдачи с первого предъявления партий продукции был заменен на процент числа рабочих дней без брака от общего числа рабочих дней.
Таблица 2.1 Классификация факторов, оказывающих влияние на качество продукции (по данным конца 80-х годов)
ТЕХНИЧЕСКИЕ | ОРГАНИЗАЦИОННЫЕ | ЭКОНОМИЧЕСКИЕ | СОЦИАЛЬНЫЕ |
• вид изготавливае | • обеспеченность ма | • форма оплаты труда | • состояние воспита |
мой продукции и серий | териалами, сырьем и т. д.; | и величина зарплаты; | тельной работы; |
ность ее производства; | • техническое обслу | • премирование за вы | • подбор, расстановка |
• состояние техничес | живание оборудования, | сококачественную работу | кадров и перемещение |
кой документации; • качество технологического оборудования, | оснастки и т.п.; • планомерность и ритмичность работы; | и продукцию; • удержание за брак; • соотношение между | кадров; • организация учебы и повышения квалификации; |
оснастки, инструмента; | • организация работ с | КП, себестоимостью и це | • организация и про |
• состояние испыта | поставщиками; | ной; | ведение соц. соревнова |
тельного оборудования; | • организация инфор | • организация и про | ния; |
• качество средств из | мационного обеспечения; | ведение хоз. расчета | • взаимоотношения в |
мерения и контроля; | • научная организа | коллективе; | |
• качество исходных | ция труда, культура про | • жилищно-бытовые | |
материалов, сырья, ком | изводства; | условия; | |
плектующих изделий | • организация питания и отдыха | • организация отдыха в нерабочее время |
Глава 1. ОТЕЧЕС1 | ГВЕННЫЙОП | ЫТУПРАВЛЕН1 | ИЯ КАЧЕСТВОМ Г | 1РОДУКЦИИ | 8/ |
Таблица 2.2 | |||||
Название | Дата | Основная | Критерии | Объект | Область |
системы | и место | суть | управления | управления | применения |
создания | системы | ||||
1 | 2 | 3 | 4 | 5 | 6 |
1. | 1955 г. | Строгое | Единичный: | Качество тру | Производ |
БИП | Саратов | выполне | соответствие | да индивиду | ство |
ние техно | качества ре | ального ис | |||
логичес | зультата тру | полнителя. | |||
ких | да требовани | Качество тру | |||
операций | ям НТД | да коллектива | |||
Обобщенный: | через качест | ||||
процент сдачи | во труда от | ||||
продукции с | дельных ис | ||||
первого пре | полнителей | ||||
дъявления | |||||
2. | 1961г. | Высокий | Единичный: | Качество ин | Любая стадия |
СБТ | Львов | уровень | соответствие | дивидуально | жизненного |
выполне | качества ре | го исполните | цикла продук | ||
ния опера | зультата тру | ля. Качество | ции | ||
ций всеми | да установ | труда коллек | |||
работника | ленным | тива через | |||
ми | требованиям | качество тру | |||
Обобщенный: | да отдельных | ||||
коэффициент | исполнителей | ||||
качества тру | |||||
да | |||||
3. | 1958 г. | Высокий | Соответствие | Качество из | Проектирова |
КАНАРСПИ | Горький | уровень | качества пер | делия и качес | ние + техноло |
конструк | вых промы | тво труда | гическая под | ||
ции и тех | шленных из | коллектива | готовка | ||
нологичес | делий | производства, | |||
кой подго | установлен | производство | |||
товки про | ным требова | ||||
изводства | ниям | ||||
4. | 1964г. | Повыше | Соответствие | Качество из | Весь жизнен |
НОРМ | Ярославль | ние тех | достигнутого | делия и качес | ный цикл про |
нического | уровня мото | тво труда | дукции | ||
уровняй | ресурса за | коллектива | |||
качества | планирован | ||||
изделий | ному | ||||
значению при | |||||
ступенчатом | |||||
планирова | |||||
нии |
82 |
Часть 2. ОТЕЧЕСТВЕННЫЙ И ЗАРУБЕЖНЫЙ ОПЫТ УПРАВЛЕНИЯ КА ЧЕСТВОМ
1 | 2 | 3 | 4 | 5 | 6 |
5. | 1975 г. | Управление | Соответствие | Качество из | Весь жизнен |
КСУКП | Львов | качеством на | качества | делия и | ный цикл |
базе | продукции | качество тру | продукции | ||
стандарти | высшим дос | да коллекти | |||
зации | тижениям | ва | |||
науки и тех | |||||
ники | |||||
6. | 1980г. | Управление | Эффектив | Качество | Весь жизнен |
КСУКП и | Днепро | качеством | ность произ | продукции, | ный цикл |
ЭИР | петровск | продукции | водства, дос | экономичес | продукции |
КСПЭП | Красно | и эффектив | тигаемая за | кие показа | |
дар | ностью про | счет повыше | тели пред | ||
изводства | ния качества | приятия | |||
Условт | ые обозначе | ния систем. | |||
БИП— СБТ- сь | - бездефект лстема безд | гное изготов дефектного | иение продук труда; | щии; | |
КАНА1 | "СПИ—ка | гчество, над | ежность, ре | суре с первых | изделий; |
НОРМ двигателей | — научна) | я организац | ия работ по | повышению | моторесурса |
КСУКГ | 7 — компле> | ксная систе | ма у правлены | ся качеством | продукции; |
КСУКГ | 7 и ЭИР — | комплексно | ^я система у | правления ка | чеством про- |
дукциииэ( | 'ирективньи | м использовй | тием ресурсе | 9в; | |
КСПЭ1 | 7 — компле | 'ксная сист | ема повышен | ия эффектив | ности произ- |
водства. |
Вместе с тем система БИП имела ограниченную сферу действия, она распространялась только на рабочих цехов основного производства.
Система работала но принципу «есть дефект — нет дефекта», не учитывая многообразие недостатков и различную степень их влияния на качество выпускаемой предприятием продукции.
В принципе БИП воплотилась в зарубежных программах «ноль дефектов» и сохранилась во всех отечественных. Более того, когда отмечалось десятилетие КСУКП, то она была зарегистрирована только на 30 тыс. предприятиях, а БИП к этому времени — на 60 тыс.
Принцип БИП, распространенный затем на функциональные подразделения завода и цеха, на НИИ и КБ, лег в основу системы бездефектного труда — СБТ.
2. Львовский вариант саратовской системы —система бездефектного труда (СБТ) впервые разработана и внедрена на Львовском заводе телеграфной аппаратуры и некоторых других предприятиях г. Львова в начале 60-х годов.
Цель системы — обеспечить выпуск продукции отличного качества, ' высокой надежности и долговечности путем повышения ответственно-
|
Гмва I. ОТЕЧЕСТВЕННЫЙ ОПЫТ УПРАВЛЕНИЯ КА ЧЕСТВОМ ПРОЦУКЦИИ___________83
сти и стимулирования каждого работника предприятия и производственных коллективов за результаты их труда.
Основным критерием, характеризующим качество труда и определяющим размер материального поощрения, является коэффициент качества труда, который вычисляется для каждого работника предприятия, каждого коллектива за установленный промежуток времени (неделя, месяц, квартал) путем учета количества и значимости допущенных производственных нарушений. В системе устанавливается классификатор основных видов производственных нарушений: каждому дефекту соответствует определенный коэффициент снижения. Максимальная оценка качества труда и максимальный размер премии устанавливаются тем работникам и коллективам, которые за отчетный период не имели ни одного нарушения.
Внедрение СБТ позволило:
• количественно оценить качество труда каждого работника, каждого коллектива;
• повысить заинтересованность и ответственность каждого работника, каждого коллектива за качество своего труда;
• повысить трудовую и производственную дисциплину всех работников предприятия;
• вовлекать в соревнование за повышение качества продукции всех работников предприятия;
• сократить потери от брака и рекламации, повысить производительность труда.
Львовская СБТ, так же как и саратовская система БИП, заключалась в том, что она распространялась главным образом на стадию изготовления продукции. Известны попытки применения принципов бездефектного труда в научно-исследовательских и проектно-конструкторских организациях, однако широкое применение СБТ получила на промышленных предприятиях для оценки и стимулирования качества исполнительского (не творческого) труда.
БИП и СБТ устраняли отрицательные субъективные причины; устранение объективных причин началось со следующих модификаций систем.
3. Система КАНАРСПИ (качество, надежность, ресурс с первых изделий) впервые разработана и внедрена на машиностроительных предприятиях г. Горького (Нижнего Новгорода) в 1957 — 1958 гг. В этой системе был сделан упор на повышение надежности изделий за счет укрепления технической подготовки работы КБ и технологов производства, на долю которых приходилось 60 — 85% дефектов, обнаруживаемых в эксплуатации. Создавались опытные образцы узлов, деталей, систем и изделия в целом и проводились их исследовательские испытания. Значительное развитие получило опытное производство, стандартизация и унификация, общетехнические системы стандартов, такие, как Единая система конструкторской документации (ЕСКД), Единая система технологической подготовки производства (ЕСТПП).
Характерным для системы КАНАРСПИ является то, что она выходит за рамки стадии изготовления продукции и охватывает многие виды работ на стадии исследования и проектирования и на стадии эксплуатации. На стадии исследования и проектирования при изготовлении опытного образца большое внимание уделяется выявлению причин отказов и их устранению в допроизводственный период.
Часть 2. ОТЕЧЕСТВЕННЫЙ И ЗАРУБЕЖНЫЙ ОПЫТ УПРАВЛЕНИЯ КА ЧЕСТВОМ
Решение этой задачи осуществляется за счет развития исследовательской и экспериментальной базы, повышения коэффициента унификации, широкого применения методов макетирования и моделирования, ускоренных испытаний, а также конструкторско-технологической отработки изделий в процессе технологической подготовки производства. Результаты эксплуатации изделий рассматриваются в системе как обратная связь и используются для совершенствования конструкции изделия и технологии его изготовления.
В КАНАРСПИ широко используются принципы бездефектного труда и бездефектного изготовления продукции.
Внедрение системы КАНАРСПИ на ряде предприятий Горьковской области позволило:
• сократить сроки доводки новых изделий до заданного уровня качества в 2 — 3 раза;
• повысить надежность выпускаемых изделий в 1,5 — 2 раза, увеличить ресурс в 2 раза;
• снизить трудоемкость и цикл монтажно-сборочных работ в 1,3 — 2 раза.
Планирование улучшения качества продукции и управления КП по этому критерию, а также распространение внимания к качеству по всему жизненному циклу продукции получили развитие в системе НОРМ.
4. СистемаНОРМ (научная организация труда по увеличению моторесурса) впервые разработана и внедрена на Ярославском моторном заводе в 1963 — 1964 гг. Цель системы — увеличение надежности и долговечности выпускаемых двигателей.
В основу системы НОРМ положен принцип последовательного и систематического контроля уровня моторесурса и периодического его увеличения на базе повышения надежности и долговечности деталей и узлов, лимитирующих моторесурс, основным показателем в системе является ресурс двигателя до первого капитального ремонта, выраженный в моточасах. Рост этого показателя в системе планируется.
Организация работ в системе построена по принципу цикличности. Каждый новый цикл по повышению моторесурса начинается после достижения в производстве ранее запланированного уровня моторесурса и предусматривает определение его фактического уровня, выявление деталей и узлов, лимитирующих моторесурс; планирование оптимального уровня увеличения моторесурса; разработку и проверку инженерных рекомендаций по обеспечению планируемого уровня моторесурса; разработку комплексного плана конст-рукторско-технологических мероприятий по освоению двигателя с новым ресурсом в производстве; проведение комплекса конструк-торско-технологических мероприятий и опытно-исследовательских работ; закрепление достигнутого ресурса в производстве; поддержание достигнутого уровня в эксплуатации.
На стадии производства система НОРМ включает в себя положения системы БИП и СБТ, на стадии проектирования — основные положения системы КАНАРСПИ.
Внедрение системы НОРМ позволило увеличить ресурс ярославских двигателей до первого капитального ремонта с 4 тыс. до 10 тыс. часов, увеличить гарантийный срок на двигателе на 70%, снизить потребность в запасных частях более чем на 20%.
85 |
Глава I. ОТЕЧЕСТВЕННЫЙ ОПЫТ УПРАВЛЕНИЯ КА ЧЕСТВОМ ПРОДУКЦИИ
Достижение запланированного уровня качества стало возможным за счет комплексного подхода к УКП путем обобщения опыта предшествующих систем по всем стадиям жизненного цикла продукции.
5. В 1975 году па передовых предприятиях Львовской области появилиськомплексные системы управления качеством продукции (КСУКП).
Целью КСУКП было создание продукции, соответствующей лучшим мировым аналогам и достижениям науки и техники. С 1978 года Госстандартом была разработана и утверждена система основных функций УКП. В связи с внедрением на предприятиях КСУКП получили развитие метрологическое обеспечение производства (МОП), многоступенчатый анализ дефектов и статистический контроль качества, были созданы группы качества, на предприятиях и в объединениях стали разрабатываться программы качества, вводилась аттестация продукции, получила широкое развитие сеть головных и базовых организаций, а также — сеть учреждений по повышению квалификации специалистов в области УКП, в вузах были введены в программы обучения курсы по стандартизации и УКП. В 1985 г. отмечалось, что за десятилетие с помощью КСУКП удалось создать и успешно реализовать конкурентоспособную продукцию, повысить удельный вес продукции высшей категории качества в 2 — 3 раза, значительно сократить потери от брака и рекламаций, уменьшить в 1,5 — 2 раза сроки разработки и освоения новой продукции. Вместе с тем указывалось, что на многих предприятиях при создании систем управления качеством (СУК) нарушались основные принципы комплексного системного подхода, что привело к формализму в этой работе и, по существу, к отсутствию системы. Основные причины этого — экономическая незаинтересованность предприятий в улучшении КП, а следовательно, и в системе, внедрение СУК на предприятиях излишне административными методами. Это породило у многих мнение, что СУК себя не оправдали и ими не следует заниматься. Вместе с тем уже при перестройке экономики и переходе на хозяйственный расчет стало ясно, что КП становится основным условием жизнеспособности предприятий, особенно на внешнем рынке.
Дальнейшее развитие СУК шло в составе систем управления более высокого уровня: отраслевых и территориальных вплоть до государственной на базе разработки программ «качество» и включения их в народнохозяйственные планы. Таким образом, организовывалась внешняя среда систем управления КП. В 1978 году были разработаны и утверждены Госстандартом Основные принципы Единой системы государственного управления качеством продукции (ЕСГУКП).
6. Внутри предприятий управление качеством продукции также шло по линии охвата более широкого круга проблем. Решение задач по улучшению качества выпускаемой продукции на многих предприятиях увязывалось с эффективным использованием ресурсов. Примером такой системы сталаднепропетровская КСУКП и ЭИР.
Создавалиськомплексные системы повышения эффективности производства (КСПЭП) и, наконец, система управления предприятием и объединением (ГОСТ 24525). Вопросы управления качеством в этих экономических системах занимали от одной пятой до одной пятнадцатой доли (по числу целевых подсистем управления). Разумеется, Гос-
86 Часть 2. ОТЕЧЕСТВЕННЫЙ И ЗАРУБЕЖНЫЙ ОПЫТ УПРАВЛЕНИЯ КА ЧЕСТВОМ
стандарт в одиночку уже не мог руководить упомянутыми системами в целом, а другие ведомства (Госплан, ГКНТ, Госкомтруд и др.) не видели в этом необходимости.
При переходе к рыночным условиям исчезли директивные методы управления, появилась конкуренция товаропроизводителей, которые напрямую ощутили требования мирового сообщества к качеству продукции.
Большой заслугой Госстандарта в переходный период к рынку явилась работа по гармонизации отечественных стандартов на системы качества с международными, в которых нашел отражение и отечественный опыт по УКП. Несмотря на отрицательные последствия экономического кризиса в России, определенно делается ставка на улучшение качества продукции уже в период выхода из кризиса.
Проблема качества — комплексная, т. е. ее можно решить только при проведении одновременно соответствующей политики в сферах законодательства, экономики, техники, образования и воспитания, а также на основе скоординированной работы производителей, эксплуатационников и потребителей, научных и инженерных структур, законодательных и исполнительных органов управления. Координирующим федеральным органом исполнительной власти в трех важнейших для обеспечения решения проблемы качества сферах деятельности — стандартизации, сертификации и метрологии — является Госстандарт России.
Техническая политика Госстандарта в области управления качеством предусматривает содействие отечественным товаропроизводителям во внедрении систем качества на предприятиях в соответствии с требованиями международных стандартов ИСО семейства 9000.
Отечественный опыт комплексного управления качеством является хорошим фундаментом освоения стандартов ИСО 9000, которые представляют более высокий уровень развития науки управления качеством. Основными отличиями систем качества (по ИСО 9000) от КСУКП являются следующие:
• ориентация на удовлетворение требований потребителя;
• возложение ответственности за качество продукции на^онкрет-ных исполнителей;
• проверка потребителем производства поставщика;
• выбор поставщика комплектующих изделий и материалов;
• сквозной контроль качества продукции, начиная от материалов и кончая утилизацией продукции;
• маркетинг;
• организация учета и анализа затрат на качество;
• прослеживаем ость материалов и комплектующих изделий по всему циклу производства;
• решение вопросов утилизации продукции после эксплуатации. Для освоения прогрессивного мирового опыта по управлению качеством необходимо реализовать комплекс обеспечивающих мероприятий, включающий разработку и реализацию системы мер и преимуществ, стимулирующих работу. На это должна быть нацелена создаваемая в стране организационная структура, проводящая оценку и признание систем качества, а также обучение специалистов, способных выполнять все виды работ в области обеспечения, контроля и улучшения качества.
Глава 2 ЗАРУБЕЖНЫЙ ОПЫТ УПРАВЛЕНИЯ КАЧЕСТВОМ
Международное сообщество выработало единый подход к нормированию технических требований к качеству продукции. Пирамида уровней директивных документов показана на рис. 2.8. Важная роль в этом деле отводится законодательству как форме государственного регулирования качества и методов его обеспечения. Законодательные основы стандартизации, сертификации и метрологии в различных регионах мира приведены в табл. 2.3.
Последовательное развитие методов и подходов к управлению качеством в мире показано на рис. 2.9. Представленная картина эволюции мышления в области качества подтверждает непрерывное совершенствование и усложнение той деятельности, которую принято называть управлением качества. Содержание каждого последующего этапа управления качеством впитывало в себя новые разработки теории качества и отвечало запросам потребителей, обеспечивало удовлетворение их возрастающих требований.
На современном этапе развития научно-технического прогресса качество продукции выдвигается в число ключевых проблем развития национальных экономик. Во всех промышленно развитых странах мира ведется активный поиск путей решения проблемы повышения качества продукции, ее конкурентоспособности на мировом рынке.
Рассмотрим историю развития управления качеством на примере трех ведущих регионов мира: США, Японии и Западной Европы.
Таблица 2. 3 | |||
^!;ЩЩ^^»:^3£& Й. ••• ;:.&".-.1д;:..д: •м^-;йЭ^-В:а'.::'''... •"'•••'. .'й'':^.:.' ЗДй:; | Д||^ИЬЙ^а|№|вБЕ^Н Д11ЙЙ1!Й|ййёй1ЙЙН ^^й^^:111?^1:IУ1:1^^•1^1:^:::^I^И|11^:^^11:^^11^^:^?::^^:^:^:::^:^^ :::':;:::а:;Ф::?^ | |Д|)сйюгий1;'^- '^"""^Ш жОмх^тран^э^а^^:', '," | |
Регион (страна) | Закон по стандартизации | Закон по сертификации | Закон по метрологии |
Америка (на примере США) | о каталогизации и стандартизации (1954г.) | о безопасности потребительских товаров (1972г.) | о метрологической системе (1986 г.) |
Азия (на примере Японии) | о промышленной стандартизации (1949 г., поправки — 1980 г.) | о безопасности потребительских товаров (1973 г.) | — об измерениях (1985г.) |
Европа (на примере Германии) | соглашение между ДИН и федеральным правительством (1979г.) | — об обеспечении безопасности технических средств (1968г.) — об охране окружающей среды (1974г.) • — о продуктах питания и товарах массового потребления (1974г.) | — об измерительном деле (1985 г.) — о единицах измерений и о поверке (1985 г.) |
90 |
Часть 2. ОТЕЧЕСТВЕННЫЙ И ЗАРУБЕЖНЫЙ ОПЫТ УПРАВЛЕНИЯ КА ЧЕСТВОМ
2.1. Опыт управления качеством в США
Промышленная революция в Америке положила конец ремесленничеству. Ремесленник контролировал процесс производства с начала до конца. Он был и инспектором по качеству, сам закупал сырье, торговал и выполнял функции управляющего. Работа для него стала предметом гордости, и, кроме того, он мог осуществлять контроль за конечной продукцией.
В XIX в. в результате перехода к серийному производству потребовался новый тип рабочего. Для фабрик были необходимы рабочие, согласные выполнять в известной последовательности простые повторяющиеся операции. От таких рабочих не требовалось высокого уровня подготовки и профессиональных навыков. Стиль управленческой работы базировался на том, что рабочий не имел оборудования, рабочих навыков, не стремился к общению и не был заинтересован в труде. Отсюда и враждебные отношения между рабочими и руководящим составом. Рабочий делал то, что ему говорили. Если он был плохим работником, его увольняли.
В Америке эта система работала хорошо, ибо позволяла производить больше товаров при меньших расходах. После второй мировой войны, когда большая часть глобального промышленного потенциала была уничтожена, во всех странах переживали острый недостаток в товарах широкого потребления. Территория США не подвергалась бомбардировке и не была ареной сухопутных сражений. Промышленность США начала быстро и, как казалось, в неограниченном количестве производить холодильники, телевизоры, автомобили и радиоприемники, чтобы удовлетворить потребности, возросшие во всем мире в результате возвращения бывших солдат домой. В 40-е и 50-е годы качество товаров, производимых в Америке, было низкое. Единственный вопрос, над которым задумывались, касался лишь объемов возможного производства.
Серьезной проблемой для промышленности США являлись огромные затраты вследствие низкого уровня качества. 20 — 25 про-| центов всех текущих затрат типичного американского предприятия! шло на обнаружение и устранение дефектов продукции. Иными| словами, до одной четверти всех работников предприятия ничего| не производили — они лишь переделывали то, что было непра-| вильно сделано с первого раза. Если прибавить к этому затраты! на ремонт или замену дефектных изделий, которые вышли за пределы предприятия и попали на рынок, то суммарные расходы вследствие низкого уровня качества составляли 30 и более процентов от издержек производства.
Многие специалисты США считали низкое качество главным тормозом роста производительности труда и конкурентоспособности американской продукции.
^Повысить уровень качества или оказаться в проигрыше — другой альтернативы для американской промышленности не существовало.
Решение проблемы качества в США чаще всего пытались найти в различных протекционистских мерах: тарифах, квотах, пошлинах, за-
91 |
Гмва2. ЗАРУБЕЖНЫЙ ОПЫТ УПРАВЛЕНИЯ КАЧЕСТВОМ
щищающих американскую продукцию от конкурентов. А вопросы повышения качества отодвигались на второй план.
Администрация США по требованию американских предпринимателей приняла ряд протекционистских мер по защите американских производителей автомобилей, стали, бытовой электроники, мотоциклов и т. д. Даже ведущие американские компании, в которых качество продукции считалось основной целью, рассматривали качество как средство уменьшения издержек производства, а не способ удовлетворения нужд потребителей.
Вместе с тем наиболее трезвомыслящие управляющие фирм США поняли, что надо повышать качество американских товаров. Какие же меры предлагались для этого? Было решено уделить внимание развитию таких проблем, как:
1) мотивация рабочих;
2) кружки качества;
3) статистические методы контроля;
4) повышение сознательности служащих и управляющих;
5) учет расходов на качество;
6) программы повышения качества;
7) материальное стимулирование.
В США в начале 80-х годов управление качеством сводилось к планированию качества — и это было прерогативой службы качества. При этом недостаточно внимания уделялось внутрипроизводственным потребителям — планы повышения качества делались без учета потребностей внутри фирмы. Процесс такого управления качеством создавал не планы, а проблемы.
Для 80-х годов характерна массированная кампания по обучению прямо на рабочих местах как способ повышения качества и обнаружения дефектов. Поставщики тоже предприняли попытки обучить качеству свой персонал.
В этот же период в США были изданы две книги Э. Деминга:
«Качество, производительность и конкурентоспособность» и «Выход из кризиса». В этих монографиях изложена философия Деминга, знаменитые «14 пунктов», которые легли в основу всеобщего (тотального) качества (То1а1 ОиаШу).
В США стали четче представлять проблему качества. У американской промышленности есть ресурсы, потенциал, амбиции и хорошо оплачиваемое руководство высшего звена. Огромные капиталовложения в новую технологию и разработку новых видов продукции, а также новые отношения между рабочими и управляющими, строящиеся на общей заинтересованности в повышении качества продукции и работы, создают предпосылки для новой технической революции в США.
Специалисты США возлагают большие надежды на совершенствование управления качеством, которое должно означать, по их мнению, радикальную перестройку сознания руководства, полный пересмотр корпоративной культуры и постоянную мобилизацию сил на всех уровнях организации на поиск путей к непрерывному повышению качества американской продукции.
По выражению видного американского специалиста А. Фейгенбау-ма, «качество — это не евангелизм, не рацпредложение и не лозунг; это образ жизни».
92 |
Часть 2. ОТЕЧЕСТВЕННЫЙ И ЗАРУБЕЖНЫЙ ОПЫТ УПРАВЛЕНИЯ КА ЧЕСТВОМ
Новым тенденциям в США наибольшее сопротивление оказывают руководители среднего звена. Для многих из них управленческая политика, основанная на качественном подходе, представляется угрозой их авторитету и даже их должностному положению. Производственные же рабочие, как правило, готовы взять на себя ответственность за качество своей работы.
Сердцевиной революции в области качества является удовлетворение требований заказчиков (потребителей). Каждый рабочий на конвейере является потребителем продукции предыдущего, поэтому задача каждого рабочего состоит в том, чтобы качество его работы удовлетворяло последующего рабочего.
Внимание со стороны законодательной и исполнительной власти к вопросам повышения качества национальной продукции — новое явление в экономическом развитии страны. Одна из главных задач общенациональной кампании за повышение качества — добиться реализации на деле лозунга «Качество — прежде всего!». Под этим лозунгом ежегодно проводятся месячники качества, инициатором которых стало Американское общество по контролю качества (АОКК) — ведущее в стране научно-техническое общество, основанное в 1946 г. и насчитывающее в настоящее время 53 тыс. коллективных и индивидуальных членов.
Конгресс США учредил национальные премии имени Малькольма Болдриджа за выдающиеся достижения в области повышения качества продукции, которые с 1987 г. ежегодно присуждаются трем лучшим фирмам. Премии вручает Президент США во второй четверг ноября, отмечаемый как Всемирный День Качества.
Анализируя американский опыт в области качества, можно отметить следующие характерные его особенности:
• жесткий контроль качества изготовления продукции с использованием методов математической статистики;
• внимание к процессу планирования производства по объемным и качественным показателям, административный контроль за исполнением планов:
• совершенствование управления фирмой в целом. Принимаемые в США меры, направленные на постоянное повышение качества продукции, не замедлили сказаться на ликвидации разрыва в уровне качества между Японией и США, что усилило конкурентную борьбу на мировом рынке, превращающемся в единый, глобальный рынок. ,
2.2. Опыт управления качеством в Японии ••
Опыт Японии убедительно показывает, что повышение качества — работа, которая никогда не кончается.
В 1945 году Япония лежала в руинах; ее промышленность была полностью разрушена. Об отсталости японской техники в тот период дает представление следующее сопоставление.
Имеющий большое значение в современной радиотехнике трансформатор низкой частоты для усилителей, изготовляемый в Японии, весил 250 г., в то время как вес этого аппарата конструкции США — всего 30 г.
93 |
Глею 2 ЗАРУБЕЖНЫЙ ОПЫТ УПРАВЛЕНИЯ КАЧЕСТВОМ
Будучи погружен в воду, японский трансформатор выходил из строя в течение 15 минут, американский же — полностью герметичен и непроницаем.
Однако в конце 40-х — начале 50-х годов японские специалисты, пройдя обучение у авторитетных американских ученых по управлению качеством Э. Деминга и Дж. Джурана, стали успешно применять эти знания в промышленности Японии.
Был внедрен так называемый цикл Деминга, связанный с проектированием, производством, сбытом продукции, анализом и вытекающими из его результатов изменениями для повышения уровня качества — цикл РВСА «планирование — выполнение — проверка — корректирующее воздействие» («р1ап-с1о-сЬеск-асиоп»).
Активно использовались контрольные карты для управления технологическим процессом. Авторский гонорар от книги лекций Деминга был использован для учреждения премий его имени. Золотые медали Деминга присуждаются с 1951 г. для отдельного лица и для предприятия. Все это создало атмосферу, в которой управление качеством рассматривается как орудие руководства. На передовых фирмах Японии с наибольшей полнотой и последовательностью внедрены комплексный подход и принципы системного управления качеством. Опыт подобных фирм тщательно изучается, анализируется, и делаются попытки его заимствования в США и в странах Западной Европы.
Считается, что японский подход к управлению качеством имеет ряд отличительных черт, однако сравнительный анализ показывает, что теоретические положения имеют универсальный характер и в этом смысле они интернациональны. Системы управления качеством тех прогрессивных зарубежных фирм, где эти концепции нашли наиболее полную и правильную практическую реализацию, сходны по своему характеру, сам механизм внедрения и развития систем также универсален по своей сути.
Отличительными элементами японского подхода к управлению качеством являются: 1) ориентация на постоянное совершенствование процессов и результатов труда во всех подразделениях; 2) ориентация на контроль качества процессов, а не качества продукции;
3) ориентация на предотвращение возможности допущения дефектов; 4) тщательное исследование и анализ возникающих проблем по принципу восходящего потока, т. е. от последующей операции к предыдущей; 5) культивирование принципа: «Твой потребитель — исполнитель следующей производственной операции»; 6) полное закрепление ответственности за качество результатов труда за непосредственным исполнителем; 7) активное использование человеческого фактора, развитие творческого потенциала рабочих и служащих, культивирование морали: «Нормальному человеку стыдно плохо работать».
Основная концепция «японского чуда» — совершенная технология, будь то технология производства, управления или обслуживания. На фирмах широко внедряются вычислительная и микропроцессорная техника, новейшие материалы, автоматизированные системы проектирования, широко применяются статистические методы, которые полностью компьютеризированы.
94 |
Честя, 2. ОТЕЧЕСТВЕННЫЙ И ЗАРУБЕЖНЫЙ ОПЫТ УПРАВЛЕНИЯ КАЧЕСТВОМ
Характерной особенностью разработки системы управления качеством в последние годы является то, что в ее состав включают систему связи с потребителем и систему связи с поставщиками.
Пути решения проблемы дальнейшего повышения качества руководители фирм видят только в сотрудничестве, взаимном доверии поставщиков, производителей и потребителей. Главное они видят в обязательном установлении причин ненадлежащего качества, независимо от того, где они будут обнаружены — у поставщика или потребителя, и реализации совместных мероприятий по устранению выявленных причин в максимально короткие сроки.
Заслуживает внимания практика целенаправленного создания собственной субподрядной сети, которая работает с заказчиком на долгосрочной основе. Японским фирмам удалось доказать, что даже в условиях свободной конкуренции подобный принцип оказывается более эффективным, чем практикуемый на Западе ежегодный конкурс субподрядчиков.
Создание собственной сети поставщиков накладывает на заказчика и, серьезные обязательства. Они связаны с организацией на субподрядных | предприятиях действенных подсистем обеспечения качества, оказанием) финансового, технического и организационного содействия им в налаживании контроля качества продукции, в модернизации производствен-1 ных мощностей и т. д. С этой целью разрабатываются специальные про-| граммы, предусматривающие изучение состояния дел у поставщиков в| области качества продукции, изучение их производственных возможно-} стей, подготовку и обучение кадров, разработку и реализацию других) мероприятий, от которых зависит качество поставляемой продукции. |
При наличии доверительных отношений с поставщиками, Основы-1 вающихся на совместном поиске путей повышения качества продукции,! обеспечивается переход на распространенную в Японии систему дове-1 рия, дающую значительную экономию времени и средств, необходимых на проведение входного контроля материалов и деталей, поступающих с фирмы-поставщика.
Японские специалисты считают, что нужно начинать с фактов и с их анализа, а не с защиты логики обязанностей и ответственности. Нужны совместные усилия, коллективные решения.
Важнейшей предпосылкой успешной работы по качеству является подготовка и обучение персонала.
Неоднократно подчеркивалось, что начинать процесс обучения следует с высшего руководящего звена. Целесообразнее это делать силами привлекаемых специалистов-консультантов по качеству. Общие сведе-д ния о деятельности по качеству, даваемые в процессе обучения, должны] сочетаться с конкретными приемами и рекомендациями. Считается, чта каждой фирме лучше составить собственную программу обучения, за-1 дав при этом необходимые цели (повышение производительности, сни-1 жение уровня дефектности).
Лидерство во внедрении и распространении концепции комплексно' го управления качеством должно принадлежать высшему руководств) компании. Это правило становится единой и универсальной основой успеха.
В последние годы обучение ведется самыми современными метода! ми. Разработаны программы деловых игр по качеству с использовани-|
95 |
Гмча! ЗАРУБЕЖНЫЙ ОПЫТ УПРАВЛЕНИЯ КАЧЕСТВОМ
ем персональных ЭВМ. Обучающийся сам принимает решения и старается создать воображаемому предприятию наилучшие условия для достижения высокой конкурентоспособности продукции.
Обучение рабочих осуществляется, как правило, их непосредственными руководителями — мастерами, начальниками участков. Обучение мастеров, начальников участков и цехов состоит из 6-дневного теоретического курса и 4-месячной практической деятельности.
В компании «Ниссан Мотор» в течение первых 10 лет работы учебе с отрывом от производства отводится не менее 500 дней. В дальнейшем учеба продолжается непосредственно на рабочих местах по вечерам и в выходные дни. Процесс обучения обязательно заканчивается аттестацией, которая проводится периодически для всех категорий работающих, включая и управляющих. Аттестация проводится руководителями соответствующего подразделения с привлечением специалистов. Периодичность аттестации в зависимости от категории рабочих — один раз в 3 месяца, 6 месяцев, один раз в год.
Ряд специалистов кроме фирменного экзамена сдают государственный экзамен. Например, на фирме «Табай Эспек» 75% работников прошли государственную аттестацию Министерства труда. Обучение перед государственной аттестацией платное. За обучение платит фирма. Работник, прошедший государственную аттестацию, получает надбавку к зарплате.
Результаты аттестации вывешиваются на рабочих местах. Допускается аттестация до трех раз. Работник, не прошедший аттестацию в третий раз, считается профессионально непригодным для работы на данном рабочем месте.
У обучения есть очень важный побочный полезный эффект: изменение в лучшую сторону личного отношения людей к работе по качеству. Считают, что качество на 90% определяется воспитанием, сознательностью и только на 10% знаниями. Учебные программы могут дать лишь эти 10 процентов, но зато они сообщают импульс изменению отношения работников к качеству, которое в дальнейшем надо поддерживать постоянными усилиями.
Большое внимание уделяется кружкам качества (подробно о них говорится дальше). Формирование кружков — добровольное. Исследования показали, что имеется .прямая зависимость посещаемости кружков и активности на заседаниях от степени добровольности, самостоятельности в выборе тем, автономии в решении внутренних вопросов кружка. Заседание кружков — единственный вид непроизводственной деятельности, разрешенной в рабочее время. Заседания еженедельные. Если кружки собираются после работы, то компания выплачивает компенсацию, как за сверхурочное время. Лозунги кружков качества: «Качество определяет судьбу предприятия»; «Что сегодня кажется прекрасным, завтра — устареет»; «Думай о качестве ежеминутно».
Регулярно проводятся цеховые и заводские конференции кружков качества. Дважды в год конференции кружков качества проводятся на Уровне всей компании. Проводятся и всеяпонские съезды представители кружков качества. Кружок считается признанным официально, если он зарегистрирован Японским союзом ученых и инженеров (.Ш5Е) и °б этом было оповещение в журнале «Мастер и контроль качества».
96 |
Часть 2. ОТЕЧЕСТВЕННЫЙ И ЗАРУБЕЖНЫЙ ОПЫТ УПРАВЛЕНИЯ КА ЧЕСТВОМ
На японских предприятиях для персонала разработана программа участия в обеспечении качества, получившая название «пять нулей». Она сформулирована в виде коротких правил — заповедей:
не создавать (условия для появления дефектов);
не передавать (дефектную продукцию на следующую стадию);
не принимать (дефектную продукцию с предыдущей стадии);
не изменять (технологические режимы);
не повторять (ошибок).
Эти правила детализированы для этапов подготовки производства и собственно производства и доведены до каждого работника.
Таким образом, можно выделить главное в отношении к качеству в Японии:
• широкое внедрение научных разработок в области управления и технологии;
• высокая степень компьютеризации всех операций управления, анализа и контроля за производством;
• максимальное использование возможностей человека, для чего принимаются меры по стимулированию творческой активности (кружки качества), воспитанию патриотизма к своей фирме, систематическому и повсеместному обучению персонала.
2.3. Европейский опыт управления качеством
Если в Японии и США на протяжении многих лет реализуются программы повышения качества, проводится активная политика в вопросах качества, осуществляется долгосрочное планирование качества, то в Европе за редкими исключениями управление качеством продолжало оставаться, по существу, контролем качества.
В течение 1980-х годов повсюду в Европе наблюдалось движение к высокому качеству продукции и услуг, а также к усовершенствованию самого обеспечения качества. Широко внедрялись системы качества на основе стандартов ИСО серии 9000.
Это привело к более последовательной позиции по вопросам качества, более надежным поставкам и более стабильному уровню качества в целом.
Необходимо отметить большую и целенаправленную деятельность стран Западной Европы по подготовке к созданию единого европейского рынка, выработке единых требований и процедур, способных обеспечить эффективный обмен товарами и рабочей силой между странами.
Важное место в этой деятельности занимают специальные ассоциации или организации, осуществляющие координацию в масштабах региона. В процессе подготовки к открытому общеевропейскому рынку, провозглашенному с 1 января 1993 г., были выработаны единые стандарты, единые подходы к технологическим регламентам, гармонизированы национальные стандарты на системы качества, созданные на основе стандартов ИСО серии 9000, введены в действие их европейские аналоги — ЕМ серии 29000. Большое значение придается сертификации систем качества на соответствие этим стандартам, созданию авторитетного европейского органа по сертификации в соответствии с требованиями стандартов ЕМ серии 45000. Указанные стандарты должны стать
97 |
^ва2. ЗАРУБЕЖНЫЙ ОПЫТ УПРАВЛЕНИЯ КА ЧЕСТВОМ
гарантами высокого качества, защитить миллионы потребителей от низкосортной продукции, стимулировать производителей к новым достижениям в области качества.
Для нормального функционирования европейского рынка поставляемая продукция должна быть сертифицирована независимой организацией. Кроме сертификации продукции проводится аккредитация испытательных лабораторий и работников, осуществляющих контроль и оценку качества продукции. Важнейший аспект их деятельности — контроль за удовлетворением требований потребителя и разрешение конфликтов, которые имеют место между производителем и поставщиком продукции.
фирмы проводят еще более интенсивную политику в области повышения качества продукции, а процессы подвергаются более жесткому контролю.
Качество стало фактором обеспечения конкурентоспособности европейских стран. Для реализации такой стратегии потребовались:
1. Единые законодательные требования (директивы).
2. Единые стандарты.
3. Единые процессы проверки, чтобы убедиться, что фирма соответствует требованиям рынка.
В 1985 г. принята новая концепция гармонизации стандартов, введены требования по обеспечению безопасности и надежности, но эти требования являются рекомендательными. В то же время обеспечение единых требований имеет большое значение. Поэтому и ориентируется Европа на основополагающие стандарты ИСО 9000 и ЕМ 29000. Введена маркировка продукции знаком СЕ.
Образованы Европейский координационный совет по испытаниям и сертификации и Европейский комитет по оценке и сертификации систем качества. В состав комитета входят организации по сертификации Великобритании, Швейцарии, ФРГ, Австрии, Дании, Швеции, Франции, Испании, Португалии, Греции, Голландии, Бельгии, Финляндии, Норвегии, Ирландии и Италии.
Главная задача проводимой работы — полностью удовлетворить запросы миллионов потребителей единого европейского рынка с наименьшими затратами.
Европейский рынок ставит серьезные задачи перед фирмами других стран, намеревающимися попасть на него.
Для того чтобы выстоять в конкурентной борьбе, крупнейшие фирмы Европы объединяют усилия для выбора прогрессивных форм и методов управления качеством продукции, связывают с их внедрением гарантию стабильного качества продукции. А она, как известно, включает стабильную технологию, надлежащую систему поддержания технологической точности оборудования и оснастки, метрологические средства контроля и испытаний продукции, эффективную систему подготовки кадров.
В сентябре 1988 г. президенты 14 крупнейших фирм Западной Европы подписали соглашение о создании Европейского фонда управления качеством (ЕФУК).
Область деятельности Европейского Фонда управления качеством:
1. Поддерживать руководство западноевропейских компаний в ускорении процесса создания качества для достижения преимуществ во всеобщей конкуренции.
Часть!. ОТЕЧЕСТВЕННЫЙ И ЗАРУБЕЖНЫЙ ОПЫТ УПРАВЛЕНИЯ КАЧЕСТВОМ 1
2. Стимулировать и, где это необходимо, помогать всем сегментам} западно-европейского сообщества принимать участие в деятельности, по улучшению качества и укреплению культуры европейского качества.
ЕФУК совместно с Европейской организацией по качеству (ЕОК) ' учредил Европейскую премию по качеству, которая начиная с 1992 года присуждается лучшим фирмам. Подробно о критериях Европейской и других премий по качеству говорится в разделе 3.2. (пункт 3).
Отличительными особенностями европейского подхода к решению проблем качества являются:
• законодательная основа для проведения всех работ, связанных оценкой и подтверждением качества;
• гармонизация требований национальных стандартов, правил процедур сертификации;
• создание региональной инфраструктуры и сети национальных ор' ганизаций, уполномоченных проводить работы по сертификации про| дукции и систем качества, аккредитации лабораторий, регистраци специалистов по качеству и т. д.
Сопоставление западного (США и Европа) и восточного (Япония подходов к качеству приведено в табл. 2.4.
Десять лет назад в докладах на конференциях и в журнальных стат! ях приводился график динамики уровня качества в Японии и на Запад (в Европе и США) (рис.2.10).
Таблица 2.
Дата добавления: 2018-02-15; просмотров: 930; Мы поможем в написании вашей работы! |
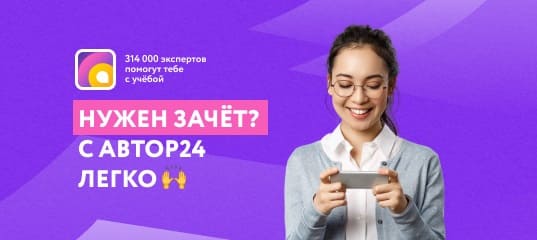
Мы поможем в написании ваших работ!