Технологичсекая схема производства азотной кислоты из аммиака
В производстве азотной кислоты при атмосферном давлении (рис. 7.2) атмосферный воздух насосом 1 подается в башню 2, орошаемую холодной водой, где он очищается от различных механических примесей. Затем воздух промывают хромовой смесью для удаления примесей мышьяка, фосфина, сероводорода. Очищенный воздух проходит осушитель 3 заполненный молекулярными ситами и поступает в теплообменник 4, обогреваемый газами из аппарата 6. Воздух нагревается до 250 оС и поступает в смеситель 5, куда также подается чистый аммиак. Приготавливается аммиачно-воздушная смесь с содержанием аммиака до 10 % (по объему).
Рис. 7.2. Технологическая схема производства азотной кислоты при атмосферном давлении
Эта смесь идет в контактный аппарат 6, где вначале проходит слой битого кварца и поролитовую керамику, для удаления мелких частиц. Чистая смесь поступает к поверхности каталитической сетки, где при температуре 800-820 оС и атмосферном давлении осуществляется контактное окисление аммиака до оксида азота(II). Нитрозные газы, содержащие до 10 % оксида азота(II), 5.5 % кислорода, остальное азот и пары воды сначала проходят теплообменник 4, где нагревают атмосферный воздух, а сами охлаждаются до 350 оС, а затем поступают в котел-утилизатор 7. Здесь газы охлаждаются. Затем они поступают в сепаратор 8, совмещенный с водяным холодильником, для понижения температуры до 20 оС. Здесь оксид азота(II) окисляется в оксид азота(IV). Оксид азота(IV), частично реагируя с водой, образует 30 % НNO3, которая используется для орошения башен 9-10. В башню 9 снизу дополнительно подают оксид азота(IV). В башнях 9-10 образуется 50 % азотная кислота, которую охлаждают и сливают в приемник 11. Даже при подаче атмосферного воздуха остается небольшое количество оксида азота(II), который пропускают через колонну 12, продуваемую атмосферным воздухом. Здесь образуется оксид азота(IV), который либо возвращают в башни 9-10, либо пропускают через башню 13, орошаемую 20 % раствором гидроксидом кальция. При этом протекает реакция:
|
|
4 NO2 + 2 Ca(OH)2 = Ca(NO3)2 + Ca(NO2)2 + 2 H2O
Образуется нитрат-нитритная смесь. Так как, нитриты обладают канцерогенным действием и, попадая в организм человека, вызывают раковые опухоли, полученную смесь загружают в аппарат 14, для обработки 50 % раствором азотной кислоты:
Ca(NO2)2 + 4 HNO3 = Ca(NO3)2 + 4 NO2 + 2 H2O
Полученный раствор нитрата кальция упаривают досуха и используют как азотное удобрение. Выделяющийся оксид азота(IV) из аппарата 14 возвращают в башню 12.
Все выходящие из аппарата газы перед сбросом в атмосферу пропускают через мокрый электрофильтр 15.
Синтез азотной кислоты при атмосферном давлении позволяет получить кислоту с концентрацией не больше 50 %. Однако в производстве красителей, взрывчатых веществ и других нитросоединений необходима кислота высокой концентрации. Для этих целей используют синтезы аммиака при повышенном давлении: 6-8 или 50 атм.
|
|
Производство азотной кислоты под давлением 6-8 атм
При производстве используется контактный аппарат с водяной рубашкой для поддержания температуры 800-820 оС, так как при более высокой температуре аммиак окисляется до азота (рис. 7.3).
900 oC
4 NH3 + 3 O2 = 2 N2 + 6 H2O
Кроме того, при высоком давлении газов повышается унос катализатора, поэтому после котла-утилизатора ставят «мокрый» электрофильтр для улавливания платины.
Одновременно с 60 % азотной кислотой, получают 75 % серную кислоту и нитрозу, которая идет на производство серной кислоты.
![]() |
Рис. 7.3. Технологическая схема производства азотной кислоты под давлением 6-8 атм
Атмосферный воздух насосом 1 нагнетается в башню 2, орошаемую холодной водой. Затем воздух проходит фильтр 3, заполненный водоотнимающим средством. В результате этих операций воздух очищается от механических примесей и осушается. Чистый воздух поступает в компрессор 4, где сжимается до 6-8 атм, проходит масляный фильтр 5 и теплообменник 6, для повышения температуры до 250 оС. С этой температурой воздух поступает в смеситель 7, куда также подается аммиак. Здесь получают аммиачно-воздушную смесь с содержанием аммиака до 10 % (по объему). Эта смесь идет в контактный аппарат 8, в котором при температуре 800-820 оС на поверхности платиновой сетки протекает реакция окисления аммиака до оксида азота(II) и воды. Так как, используется высокое давление, скорость реакции окисления повышается и температура может подняться до 900 оС, что нежелательно. Учитывая это, контактный аппарат имеет водяную рубашку. После контактного аппарата нитрозные газы проходят теплообменник 6, где отдают тепло на нагрев исходного воздуха, а сами охлаждаются. Дополнительно газы охлаждаются в котле-утилизаторе 9 и поступают в газовый сепаратор 10, совмещенный с водяным холодильником. Здесь же имеется «мокрый» электрофильтр, служащий для улавливания платины. При давлении 6-8 атм на 1 тонну образующейся азотной кислоты уносится до 0.15 г платины.
|
|
В сепараторе 10 оксид азота(II) окисляется до оксида азота(IV). Здесь образуется также 50 % азотная кислота, которая идет на орошение башни 11, в которую снизу подается оксид азота(II). В башне 11 образуется 60 % азотная кислота, которая бурая на цвет, так как содержит большое количество оксида азота(IV). Учитывая это, азотная кислота из колонны 11 поступает в башню 12, где обрабатывается «острым» паром. При этом оксиды азота отдуваются и получается светлая азотная кислота, которая является товарным продуктом. Эта стадия называется осветлением кислоты.
|
|
Оксиды азота из башни 12, после охлаждения до 20 оС, направляют в башню 14, орошаемую 80 % серной кислотой. В этой башне получают нитрозу, которая затем идет на получение серной кислоты. Раствор нитрозы сливают в приемник 15. Все газы перед сбросом в атмосферу пропускают через санитарный электрофильтр 16.
Дата добавления: 2018-02-18; просмотров: 1832; Мы поможем в написании вашей работы! |
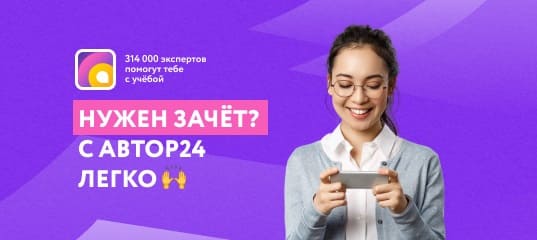
Мы поможем в написании ваших работ!