Производство аммиака при среднем давлении
Условия процесса: температура 450-550 оС, давление 300-320 атм, состав азотоводородной смеси стехиометрический.
N2 + 3 H2 ® 2 NH3
Свежая азотоводородная смесь компрессором 1 сжимается до 300-320 атм, пропускается через маслянный фильтр 2, аммиачный холодильник 3 и сепаратор 4. Затем поступает в колонну синтеза 5, которая выполнена из отдельных секций (рис. 6.2).
![]() |
Рис. 6.2. Технологическая схема производства аммиака при среднем давлении
Общая высота колонны синтеза 10-12 м, диаметр до 1 м, толщина стенок 12-15 см. Внутри колонны находятся теплообменники (2) типа «труба в трубе». Трубчатая часть внутреннего
теплообменника заполнена гранулированным катализатором, а по межтрубному пространству циркулируют газы.
За один проход через слой катализатора при температуре 450-550 оС и давлении 320 атм образуется 20-25 % аммиака. Остальные 75-80 % составляют не прореагировавшие азот и водород.
Горячие контактные газы проходят по нижнему теплообменнику, отдают своё тепло на нагрев исходной смеси азота и водорода, при этом сами охлаждаются до 200 оС. Затем газовая смесь проходит систему водяных холодильников 6, где давление уменьшается до атмосферного. За счет резкого понижения давления происходит уменьшение температуры до 20 оС и аммиак, содержащийся в газах, конденсируется. 94 % аммиака (от общего его содержания) переходит в жидкое состояние. Жидкий аммиак отделяют в сепараторе 7.
|
|
Непрореагировавшие азот, водород и 6 % аммиака компрессором 1 возвращают в процесс, смешав со свежими порциями азота и водорода. Эта смесь проходит масляный фильтр 2, который необходим для удаления смазочного масла, которое попадает в цикл вместе с газом, выходящим из насоса. В сепараторе 4 при температуре – 40 оС отделяют оставшиеся 6 % аммиака, а смесь азота с водородом возвращают в цикл.
Колонна синтеза работает в автотермичном режиме 5-7 лет. Периодически процесс останавливают и проверяют активность катализатора.
Синтез аммиака при высоком давлении
В зарубежной практике имеются производства синтеза аммиака, работающие под давлением 700-1500 атм. В данном случае степень конверсии смеси азота и водорода за один проход через катализатор составляет 50-60 %. Общая степень конверсии с учетом циркуляции – 99.8 %.
Процессы под давлением 1500 атм не нуждаются в катализаторе, так как его роль играют стенки колонны синтеза.
![]() |
Колонна синтеза аммиака представляет собой цельнотянутый кованный цилиндр, изготовленный из пушечной стали. Высота колонны 10-12 м, диаметр 80 см, толщина стенок – 20 см (рис. 6.3).
Рис. 6.3. Схема колонны синтеза аммиака при высоком давлении
В центре колонны проходит труба, внутри которой находятся вольфрамовые нити, служащие для её запуска. Также внутри имеется каталитическая коробка, заполненная гранулированным катализатором. Пространство между стенками каталитической коробки и колонны синтеза разделено гофрированной металлической перегородкой.
|
|
Входящая в колонну снизу, холодная исходная азотоводородная смесь проходит в пространстве между внутренней стороной и гофрированной перегородкой и поступает в центральную трубу с температурой 480 оС. Затем при температуре 480-530 оС поступает в каталитическую коробку, где идет синтез аммиака с образованием 50 % его. Контактные газы выходят из каталитической коробки, проходят пространство между стенками коробки и внутренней стороной гофрированной перегородки, которая при этом нагревается и отдает тепло исходной смеси азота и водорода, движущейся в противоток. После запуска колонны вольфрамовые нити отключают, а подогрев исходной газовой смеси осуществляется за счет тепла реакции. В автотермичном режиме колонна работает несколько лет.
![]() |
На рис. 6.4. приведена схема производства аммиака при высоком давлении. Свежая порция азота и водорода компрессором 1 сжимается до 1500 атм, проходит масляный фильтр 2 и поступает в колонну синтеза 3. Здесь образуется 60 % аммиака. Контактные газы, содержащие аммиак, азот и водород, поступают в аммиачный холодильник 4, где при температуре – 40 оС конденсируется до 96 % аммиака от его общего количества. Жидкий аммиак отделяют в сепараторе 5, а не прореагировавшие азот и водород, а также 4 % аммиака возвращают в компрессор 1.
|
|
Рис. 6.4.Технологическая схема производства аммиака при высоком давлении
Данная схема производительна, но требует высоких материальных затрат, оснащенности автоматическими средствами управления процесса, высокой культуры обслуживания.
КОНТРОЛЬНЫЕ ВОПРОСЫ К ГЛАВЕ 6
6-1. В чем заключается проблема «связанного азота»?
6-2. Укажите промышленные методы «связывания» атмосферного азота и сравните их энергоемкость и эффективность.
6-3. Почему в производстве аммиака используется циклическая схема?
6-4. Как в производстве аммиака получают контактную массу? Для чего в нее вводят оксиды алюминия, калия и кальция?
6-5. Почему в производстве аммиака наиболее распространены системы «среднего» давления?
ЗАДАЧИ К ГЛАВЕ 6
6-1. В процессе синтеза аммиака из простых веществ в замкнутом сосуде давление в реакционной смеси упало на 10 % (при постоянной температуре). Определите состав полученной после реакции газовой смеси (в % по объему), если в исходной смеси содержание компонентов отвечало стехиометрическому соотношению.
|
|
6-2. При температуре 400 оС и давлении 30 МПа в равновесии с азотоводородной смесью находится 47 % аммиака (по объему). Исходя из уравнения реакции: N2 + 3H2 ↔ 2 NH3, определите количество аммиака, азота и водорода (в литрах), находящихся при указанных условиях в 1 м3 газовой смеси.
6-3. Константа равновесия реакции 3 H2 + N2 ↔ 2 NH3 при некоторой температуре равна 2. Сколько моль азота следует ввести на 1 л газовой смеси, чтобы 75 % водорода превратить в аммиак, если исходная концентрация водорода была равна 10 моль/л?
6-4. Для реакции синтеза аммиака: N2 + 3H2 ↔ 2NH3 найдены равновесные концентрации веществ: [N2] = 0.4 моль/л; [Н2] = 2 моль/л; [NH3] = 0.8 моль/л. Вычислите константу равновесия и исходные концентрации азота и водорода.
6-5. Имеется смесь азота и водорода, которая в 1.9 раза тяжелее водорода. После пропускания смеси через колонну синтеза аммиака образовалась смесь, которая после приведения к начальным условиям стала на 25 % тяжелее гелия. Рассчитайте выход аммиака.
6-6. Определите концентрацию аммиака на входе в контактный аппарат, если уменьшение о6ъема в результате реакции составляет 0.9. Концентрация аммиака на выходе составляет 16 об. %.
6-7.Рассчитайте состав синтез-газа на выходе из колонны синтеза аммиака, если концентрация аммиака на входе в колонну 2 об. %. Расчет вести на 100 кмоль газа. Уменьшение объема вследствие реакции 0.89.
6-8. Выразите состав эквимолекулярной смеси азота и водорода: а) моль/л; б) в процентах по массе; в) в процентах по объему.
6-9. Синтез аммиака осуществляется в колонне под давлением 3.03· 107 Па и температуре 673 К. Газ, выходящий из колонны, имеет следующий состав (об. %): NН3 – 17; N2 – 11,0; Н2 – 72,0. Рассчитайте соотношение N2 и Н2 в исходной смеси газов.
6-10. В колонну синтеза поступает азотоводородная смесь со скоростью 30 000 мЗ/с. Определите, сколько аммиака (в кг) образуется за один цикл, если концентрация аммиака на входе в колонну 4 % (по объему), на выходе – 16 % (по объему).
6-11.Энтальпия образования аммиака из азота и водорода при температуре 773 К и давлении 3·107 Па равна ΔН = -55,8 кДж/моль. Определите, сколько теплоты выделится при синтезе 15 т аммиака в этих условиях.
6-12. Определите энтальпию образования аммиака (в кДж/кмоль) при температуре 773 К и давлении 1·108 Па, если при образовании 1 кг аммиака в этих условиях выделяется 4047.05 кДж теплоты.
6-13. Определите степень окисления аммиака, если для получения 1000 т/сут 100 %-ной азотной кислоты на окисление ежечасно подается 135 000 м3 аммиачно-воздушной смеси, содержащей 11.5 % NH3.
6-14. Определите массу аммиака и воздуха, необходимую для получения 4 т 50 %-ной азотной кислоты при следующих условиях: степень окисления аммиака 0.97, степень абсорбции оксидов азота 0.92, содержание аммиака и аммиачно-воздушной смеси 11.5 об. %.
6-15. Сколько азотной кислоты (кг) можно получить из 21 кмоль оксида азота(IV)? Сколько кислоты получается при абсорбции этой массы NO2 водой и сколько воздуха (состава 21 % О2, 79% N2) необходимо добавлять для доокисления образующегося оксида азота NO до оксида азота NO2.
6-16. Составьте материальный баланс производства 1 т азотной кислоты. Производственными потерями пренебречь. Состав воздуха: 21 об. % О2 и 79 об. % N2.
6-17. Определите теоретически возможную концентрацию азотной кислоты при полном окислении аммиака.
6-18. Определите часовой расход воды на абсорбцию оксидов азота из нитрозного газа, содержащего 9.5 % NО2 поступающего в абсорбционную колонну со скоростью 48 000 м3/ч. Степень абсорбции 0.98.
6-19. Определите напряженность катализатора контактного аппарата окисления аммиака производительностью 3.0 т/ч азотной кислоты. Степень превращения NO и NO2 0.96, степень абсорбции 0.99. Общая активная поверхность всех сеток катализатора 3.94 м2.
6-20. Аммиак окисляется на платинородиевом катализаторе в течение 0.0002 с. Объем промежутков между нитями в слое катализатора равен 0.00095 м3. Определите объемную скорость, с которой аммиачно-воздушная смесь проходит через слой катализатора (м3/м3 · ч).
Дата добавления: 2018-02-18; просмотров: 4653; Мы поможем в написании вашей работы! |
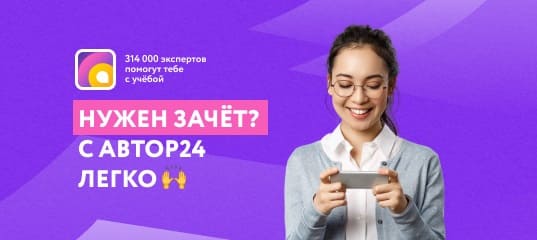
Мы поможем в написании ваших работ!