Номенклатура выпускаемой продукции
Стеновые мелкие блоки из ячеистого бетона должны удовлетворять требованиям настоящего стандарта ГОСТ 25485-89 «Бетоны ячеистые. Технические условия» и изготовляться по технологическим регламентам, утверждённым в установленном порядке.
Блоки предназначены для кладки наружных, внутренних стен и перегородок зданий с относительной влажностью воздуха помещений не более 75% и при неагрессивной среде.
В помещениях с влажностью воздуха более 60 % внутренняя поверхность блоков наружных стен должна иметь пароизоляционное покрытие.
Характеристики
1. Прочность автоклавного и неавтоклавного бетонов характеризуют классами по прочности на сжатие в соответствии со СТ СЭВ 1406.
Для бетонов установлены следующие классы: В0,5; В0,75; В1; В1,5; В2; В2,5; В3,5; В5; В7,5; В10; В12 .5; В15.
Для конструкций, запроектированных без учета требований СТ СЭВ 1406, показатели прочности бетона на сжатие характеризуются марками: М7,5; М10; М15; М25; М35; М50; М75; М100; М150; М200;
2. По показателям средней плотности назначают следующие марки бетонов в сухом состоянии: D300; D350; D400; D500; D600; D700; D800; D900; D1000; D1100; D1200;
3. Для бетонов конструкций, подвергающихся попеременному замораживанию и оттаиванию, назначают и контролируют следующие марки бетона по морозостойкости: F15; F25; F35; F50; F75; F100.
Назначение марки бетона по морозостойкости проводят в зависимости от режима эксплуатации конструкции и расчетных зимних температур наружного воздуха в районах строительства.
|
|
Таблица 3
Допускаемые предельные отклонения для блоков
№ п/п | Наименование отклонения геометрического параметра | Предельные отклонения, мм | ||
блоков для кладки на клею | блоков для кладки на растворе | |||
категория 1 | категория 2 | категория 3 | ||
Отклонения от линейных размеров | ||||
1 | Отклонение по: Высоте Длине, толщине | ±1 ±2 | ±3 ±4 | ±5 ±6 |
2 | Отклонение от прямоугольной формы (разность длин диагоналей) | 2 | 4 | 6 |
3 | Искривление граней и ребер | 1 | 3 | 5 |
Повреждения углов и ребер | ||||
1 | Повреждения углов не более двух на одном блоке глубиной | 5 | 10 | 15 |
2 | Повреждения ребер на одном блоке общей длиной не более двукратной длины продольного ребра и глубиной | 5 | 10 | 15 |
Таблица 4
Номенклатура продукции
№ п/п | Наименование | Класс по прочности на сжатие | Теплопроводность λ, Вт/м0С | Размеры, мм | ||
длина | ширина | толщина | ||||
1 | Блоки | В1,5 | 0,191 | 400 | 200 | 200 |
Технологическая часть
Консультант: ___________________________________К.Е.Филиппова
Общая характеристика технологии
На текущий момент существует две основные методики производства пенобетона и изделий из него: первый - это баротехнология, а второй - это классический способ производства. И если сырьевой состав пенобетона в обеих методиках почти одинаков, то способ затворения и очередность введения основных компонентов значительно отличаются.
|
|
Благодаря этим отличиям, производители получают на выходе продукцию совершенно разного качества и прочности. Разнятся и эксплуатационные характеристики полученных пенобетонных блоков.
Баротехнология - более простой, и как следствие - менее затратный способ производства пенобетонных блоков, так как не требует дорогостоящего технологического оборудования и дополнительного времени на получение условной единицы продукции.
Стоит заметить, что из экономических соображений большинство производителей пенобетонных блоков используют именно этот способ получения пенобетона.
При производстве пенобетона по баротехнологии, основной процесс происходит следующим образом. В герметичный смеситель вводятся основные компоненты пенобетона: цемент М400, песок, иногда используется зола-унос, вода, пенообразователь, ускорители твердения и воздухововлекающие добавки. Далее, в смеситель под давлением нагнетается воздух, и все это активно размешивается. При размешивании, раствор активно насыщается воздухом (воздухововлечение).
|
|
Затем полученный раствор, под давлением, по трубопроводу поступает непосредственно в литьевые формы. Наступает освобождение атмосферного давления (нагнетенного компрессором в камеру смесителя) и пенобетонная смесь увеличивается в объеме.
Достоинства:
1. Более низкая себестоимость производства пенобетонных блоков. Основной плюс баротехнологии пенобетона - это экономическая выгода для производителя. Используется более дешевое технологическое оборудование. Такой процесс производства пенобетонных блоков прост и не требует больших вложений. При желании, подобное производство можно организовать в любом приспособленном для этого помещении.
Недостатки:
1. Более низкая прочность пенобетонных блоков.
2. Так как лучше и эффективней взбиваются более жидкие субстанции, производители пенобетонных блоков вынуждены вводить в состав затворения большее количество воды, чем это требуется для полноценного процесса гидратации цемента, что негативно сказывается на окончательной прочности пенобетонных плит, изготовленных из такого пенобетона.
3. Структура пенобетона, изготовленного по баротехнологии, отличается довольно большой крупностью пор и зачастую напоминает срез ракушечника или мелкой пемзы. Размер воздушных пустот в структуре пенобетонных блоков, изготовленных по баротехнологии, редко бывает меньше 1-2 мм. Благодаря таким крупным порам, пенобетонные блоки имеет меньшую прочность и несущую способность в стенах будущего дома.
|
|
4. Применение неэкологичных синтетических пенообразователей. Для набора нужной подвижности смеси, без существенного увеличения пропорции воды, производители пенобетонных блоков зачастую применяют пластифицирующие добавки, например - суперпластификаторы.
Классический способ производства пенобетонных блоков. В отличие от баротехнологии, где процесс пенообразования происходит непосредственно в смесителе затворения пенобетонной смеси, применение пеногенератора позволяет производителям пенобетонных блоков замешивать основные компоненты в правильной дозировке, без поиска компромиссов с изменением водоцементного отношения и т.п. Благодаря этому, на выходе получаются более технологичные изделия из пенобетона.
Производство пенобетона с применением пеногенератора выглядит следующим образом: при помощи дозаторов, в смеситель подаются сыпучие сырьевые компоненты: песок, цемент, иногда в качестве заполнителя добавляется зола-унос. Затем в смеситель подаются жидкие компоненты: вода, растворенные в воде химические добавки. Начинается смешивание компонентов. Процесс получения раствора для изготовления пенобетона практически не отличается от способа баросмешивания. Те же требования по гомогенности (однородности) состава, пропорциям и качественным характеристикам сырья.
Далее в смеситель начинает подаваться уже готовая техническая пена из пеногенератора. Количество необходимой пены регламентируется требуемой плотностью пенобетонных блоков и регулируется временем работы пеногенератора.
В смесителе происходит активное смешивание пены с цементно-песчаным раствором. Это полностью контролируемый процесс, как по пропорциям, так и по времени насыщения. Благодаря этому, производство пенобетонных блоков выходит на совершенно иной качественный уровень.
Достоинства:
1. Более качественная структура массива пенобетонных блоков. Благодаря применению заранее приготовленной качественной пены, производители пенобетона получают на выходе изделия с правильной структурой. В массиве пенобетона отсутствуют крупные воздушные поры, благодаря чему, пенобетонные блоки имеют более высокую и равномерную прочность.
2. Экологичность пенобетонных блоков. В "пеногенераторной технологии" производства используются экологически чистые белковые пенообразователи, что благотворно влияет на экологичность вашего будущего жилья.
Недостатки:
1. Высокая себестоимость получения пенобетона. Наверное, это самый большой и единственный минус. При производстве используется более дорогостоящее оборудование. Сам процесс требует больше времени на получение единицы готовой продукции.
2. Более высокая стоимость пенобетонных блоков. Этот минус вытекает из предыдущего. Выше себестоимость - более высокая цена продукции при её реализации.
Сырье и материалы
2.2.1.Характеристика сырья и полуфабрикатов, технология их подготовки и складирования
1. Гипсовое вяжущее (ГОСТ 23789 – 79) – поставщик ООО « Ангарский гипсовый завод» г. Иркутск, в 3128 км от г. Якутска.
Таблица 5
Химический состав, %
SiО2 | Аl2О3 | Fe2О3 | СаО | МgО | SO3 | Н2О | CaSO4·2H2O |
0,25-8,52 | 0,19 | 0,01-0,22 | 27,75-32,53 | 0,24-9,6 | 27,88-46,58 | 12,65-19,83 | 59,89-99,99 |
Тонкость помола
Характеризуется массой гипсового вяжущего, оставшегося при просеивании через сито №02. Остаток на сите составил 8,76 %. Это означает, что гипсовое вяжущее относится к вяжущим среднего помола (остаток на сите не более 14 %).
Нормальная густота
Нормальная густота гипсового теста определяется на приборе Суттарда. Характеризуется количеством воды, в процентах от массы вяжущего, необходимого для получения диаметра расплыва 180±5 мм. Нормальная густота составила 55%.
Сроки схватывания
Сроки схватывания гипсового теста нормальной густоты определяют при помощи прибора Вика (игла). По срокам схватывания гипсовое вяжущее относятся к нормальнотвердеющим, так как начало схватывания составило 12 мин 30 сек и конец схватывания 15 мин.
Прочностные характеристики
Прочностные характеристики гипсового вяжущего определяют, подвергая испытанию образцы – балочки размером 40х40х160 мм их гипсового теста нормальной густоты через 2 часа после изготовления.
Таблица 6
Rсжср, МПа | Rизг, кгс/см2 |
4,61 | 24,9 |
Из полученных результатов гипсовое вяжущее имеет параметры Г4 – Б II.
2. Модифицированная добавка состоит из двух компонентов: Активной минеральной добавки – цеолита (ГОСТ 25094 - 82. Добавки активные минеральные. Методы испытаний) и пластификатора – ультра (ГОСТ 8728 – 88. Пластификаторы. Технические условия).
Цеолит. При приготовлении пенобетонов было использовано композиционное гипсовое вяжущее (КГВ) на основе цеолитового порошка с пластификатором (далее «Цеолком»). Для этого природные цеолиты подвергали механохимической активации в планетарной мельнице-активаторе Retsch PM 400 со скоростью вращения 150 оборотов в минуту, массой мелющих шаров до 60 г в течение 15 минут, что позволило диспергировать материал до ультрадисперсного состояния. При активации размеры частиц цеолитов достигают в среднем 1,3 мкм, причем до 11 % от общего количества частиц имеют размеры 3-30 нм. «Цеолком» снижает плотность материалов, при этом увеличивает их прочность.
Таблица 7
Химический состав природного цеолита, %
SiО2 | Аl2О3 | Fe2О3 | СаО | МgО | К2О +Na2О | ТiО2 | Н2О+ | Н2О- |
65,11 | 12,16 | 1,08 | 2,62 | 1,88 | 3,30 | 0,13 | 8,89 | 4,26 |
Суперпласт Феррокрит Ультра – поставщик ООО «Компонент» г. Владимир, в 7780 км от г. Якутска.
Продукт «Феррокрит Ультра» целесообразно применять в производстве сборного железобетона для получения высокоподвижных бетонных смесей и высокопрочных бетонов В 40 и выше, в том числе на рядовых материалах, изготавливаемых по конвейерной, кассетной, стендовой или агрегатно-поточной технологии с целью получения бетонов с улучшенными физико-механическими свойствами и долговечностью. Также рекомендуется к применению в производстве легкого и мелкозернистого бетона с высокими прочностными показателями и заданными параметрами.
Возможности и преимущества
Применение продукта «Феррокрит Ультра» в технологии производства железобетонных конструкций обеспечивает:
1. По реологическим свойствам:
- увеличение подвижности бетонной смеси от П1 до П5;
- увеличение прочности бетона в первые сутки нормального твердения на 30% и более в равноподвижных смесях;
- снижение водопотребности бетонной смеси на 10-20%;
- придание смеси высокой удобоукладываемости без расслоения и водоотделения.
2. По физико-механическим показателям:
- достижение более высоких прочностных показателей бетона в условиях нормального твердения за счет водоредуцирующего эффекта;
- увеличение показателей по долговечности бетона;
- в 1,5-1,6 раза увеличение сцепления бетона с закладной арматурой и металлоизделиями;
- улучшение качества поверхности изделий;
3. По технико-экономическим показателям:
- снижение расхода вяжущего на 15-20% без снижения прочностных показателей бетона;
- при тепло-влажностной обработке изделий сокращение цикла изотермии (на 1,5-2 часа), а также снижение температуры изотермии на 15-250 °С;
- увеличение оборачиваемости форм в 1,5-2 раза;
- увеличение производительности труда на 20-30%.
Рекомендации по применению
Для приготовления бетонов с добавкой «Феррокрит Ультра» должны применяться материалы, соответствующие НТД. Подбор состава бетона с добавкой заключается в корректировке рабочего состава бетона без добавки. Добавка «Феррокрит Ультра» вводится в бетонную смесь вместе с водой затворения в виде водного раствора рабочей концентрации. Рабочая концентрацияприменяемого раствора выбирается потребителем исходя из требований технологии, условий применения и удобства в использовании. Эффективность действия добавки зависит от минерального состава цемента и заполнителей.
Дозировка
Дозировка добавки зависит от назначения бетонной смеси, содержания в цементе трехкальциевого алюмината, активных минеральных добавок и дисперсности цемента и находится в пределах 0,35-0,9% от массы цемента в пересчете на сухое вещество. Оптимальная дозировка определяется экспериментально на применяемых материалах.
Таблица 8
Наименование показателя | Значение показателя для добавки | |
В форме порошка | ||
С ненормируемым воздухововлече нием | С пониженным воздухововлечением | |
Внешний вид | Однородный порошок светло- коричневого цвета | |
Плотность при 20°С, не менее, г/см3 | 0,5 | |
Массовая доля воды, % не более | 10,00 | |
Показатель активности водородных ионов (рН), 2,5% водного раствора | 8,5 ± 1,5 | |
Массовая доля ионов хлора в сухом веществе %, не более | 0,1 | |
Повышение марки бетонной смеси по удобоукладываемости без снижения прочности во все сроки твердения | от П1 до П5 | |
Содержание воздуха в бетонной смеси по объему, % | не нормируется | 3 |
3. Вода для бетонов и растворов (ГОСТ 23732-79)
При изготовлении пенобетонных блоков рекомендуется применять питьевую воду, без какой-либо проверки. Содержание воды в пористом бетоне складывается из расчетного количества, необходимого для затворения раствора, и воды, содержащейся в пене. Перед добавлением пены водоцементное отношение раствора должно составлять минимум 0,38. Слишком низкое значение водоцементного отношения может явиться причиной получения изделия с более высокой, чем заданная, объемной плотностью. Это обусловлено тем, что бетон будет забирать из пены необходимую для химических и физических взаимодействий воду, вызывая частичное разрушение пены, т.е. снижение ее объема в пенобетонной смеси. Оптимальное соотношение - в интервале от 0,4 до 0,45. Температура воды не допускается выше +25°С.
4. Пенообразователь ПБ-Люкс (ТУ 2481-004-59586231-2005).
Пенообразователь ПБ-Люкс представляет оптимальную смесь анионактивных ПАВ со стабилизирующими и функциональными добавками. Продукт обладает высокими технологическими, экономическими и экологическими характеристиками, позволяя при минимальных издержках получать максимальную прибыль. Пенообразователь ПБ-Люкс используется во всех известных технологиях получения пенобетона - с использованием пеногенераторов, «миксерной» технологии, баротехнологии.
Эксплуатационные преимущества пенообразователя "ПБ-Люкс"
1) Используется во всех известных технологиях производства пенобетона;
2) Совместим со всеми органическими и неорганическими добавками, используемые для модификации бетона;
3) Содержит все необходимые компоненты для достижения высокой кратности и устойчивости пены. Легко дозируется и смешивается с водой;
4) Коэффициент устойчивости пены в цементном тесте превышает 0,95.
Кратность пены варьируется от 5 до 50 изменением настроек оборудования. Позволяет получать пенобетона с плотностью 350-1200 кг/м³;
5) Легко дозируется и смешивается с водой;
6) Расход пенообразователя ПБ-Люкс на 1 м³ пенобетона составляет 0,6-0,7 кг (для плотности 350 кг/м³) и менее при большей плотности пенобетона (при работе с пеногенератором).
Таблица 9
Физико-химические показатели пенообразователя "ПБ-Люкс"
п/п | Наименование показателей | Норма по ТУ 2481-004-59586231-2005 |
1 | Внешний вид | Однородная жидкость от светло-желтого до коричневого цвета |
2 | Запах | Специфический, присущий продукту. |
3 | Плотность при 20º С, кг/м³ | 1040 - 1100 |
4 | Водородный показатель (рH) продукта | 8,0 - 10,5 |
5 | Кратность пены рабочего раствора с объемной долей продукта 4%, не менее | 7,0 |
6 | Устойчивость пены в технологической среде | Выдерживает испытание |
5. Смазка для форм ОЭ-2.
Обратная эмульсия (тип "вода в масле") применяется для смазки форм при изготовлении пенобетонных изделий. Она состоит из: эмульсии ОЭ-2 (20%) и насыщенного раствора извести (80%). Смазка должна быть постоянной по составу и хорошо удерживаться на вертикальной поверхности форм.
2.2.2.Обоснование расходов материалов и полуфабрикатов
Завод по производству модифицированных пеногипсовых блоков располагается в северной части г. Якутска. Сырье для производства модифицированных пенобетонных блоков получают с завода, ООО «Ангарский гипсовый завод» (стоимость 1 тонны ГВВ – 2200 р.), ООО «Сунтарцеолит» (стоимость 1 тонны Цеолита – 6000 р.), пенообразователь ПБ-Люкс «АТК Строй» г. Барнаул (стоимость 1 кг пенообразователя – 80 р.).
2.2.3.Сбыть сырья
В последние десятилетия происходит интенсивная разработка новых строительных технологий и материалов с повышенными качественными и эксплуатационными характеристиками. Северные регионы РФ, в том числе и Республика Саха (Якутия), характеризуются экстремальными климатическими условиями, богатыми минеральными ресурсами, отдаленностью от крупных промышленных центров и сложной транспортной схемой. Этим обусловлены особые требования к материалам, применяемым в условиях Севера, их эксплуатации и обслуживании.
В состав базы строительной индустрии Республики Саха (Якутия) входят около 40 предприятий (в том числе 10 крупных и средних), производящих: цемент, смеси бетонные, сборные железобетонные изделия; материалы, изделия и конструкции из древесины; щебень, гравий, песчано-гравийные смеси, строительный песок; керамзит; теплоизоляционные материалы с общей численностью работающих около 2,5 тыс. человек.
Строительный комплекс Республики Саха (Якутия) из-за ограниченности номенклатуры выпускаемой продукции более половины из общего объема потребляемых строительных материалов и изделий ввозит из других регионов РФ и зарубежа. В республику ввозятся значительные объемы теплоизоляционных минераловатных материалов, сухих строительных смесей, керамических и огнеупорных материалов, гипсокартона, гипсоволокнистых плит, изделий подвесных потолков, акустических плит, кровельных, сантехнических, отделочных материалов, предметов домоустройства, материалов для полов, химических добавок для бетонов и растворов. Все это ведет к удорожанию конечной строительной продукции – как новых, так и реконструируемых зданий и сооружений, так как транспортные затраты повышают стоимость строительных материалов до двух раз.
Новые требования по теплозащите зданий привели стройиндустрию к применению новых конструктивных решений зданий и их ограждающих конструкций. Нашли применение зарубежные и отечественные системы утепления фасадов с применение энергоэффективных теплоизоляционных материалов.
В последние годы строительная индустрия Республики стала производить строительные материалы и изделия, которые ранее не производились:
- сульфатостойкий и тампонажный цемент;
- экструдированный пенополистирол;
- сухие строительные смеси;
- полистиролбетон и стеновые блоки из полистиролбетона
- и другие.
2.2.3.Технико-экономическая характеристика складов сырья
Склад занимает одно из важных мест в цепочке любого производства. Надежная сохранность сырья, оптимальное использование складских площадей, эффективная работа оборудования при максимальной загрузке и легкая модернизация при необходимости — эти задачи выполнимы, если заранее учесть особенности используемого сырья и подобрать наиболее подходящее оборудование для оснащения склада с учетом всех современных технических требований.
Наиболее значимыми факторами, влияющими на сохранность свойств сырья, являются: относительная влажность, температура, освещенность, газовый состав воздуха, воздухообмен, физико-химические и биологические процессы, протекающие в самом сырье, и воздействие амбарных вредителей.
Хранение сыпучих материалов должно производиться в закрытых, защищенных от ветра складах.
Для хранения сыпучих материалов должны быть устроены лари, оборудованные местной вытяжной вентиляцией из верхней части ларя, обеспечивающей скорость движения воздуха при открытых загрузочных отверстиях 0,7 м/с.
Чтобы работа силосов была эффективной и безопасной, необходимы различные вспомогательные механизмы, такие как фильтры для сбора пыли, датчики уровня и т.д. Фильтр для сбора пыли нужен для улавливания мелких частиц из потока избыточного воздуха при загрузке в емкости сырья, материала. Датчик уровня сыпучих материалов — это незаменимое устройство для обеспечения безопасной эксплуатации силосов и бункеров, а также для контроля над минимальным и максимальным уровнем материалов, находящихся в емкости. Предохранительный клапан предназначен для сброса избыточного давления внутри силоса. Затвор используется для контролируемой разгрузки сыпучих материалов из бункеров и силосов.
Заслонки и задвижки используются для преграждения потока материалов, движимых силой тяжести при выгрузке из силосов спиральными транспортерами, вакуумными конвейерами или пневмотранспортерами.
Виброаэраторы (вибровентиляторы) используются для более полной выгрузки сыпучего сырья из силоса при помощи аэрации и легкой вибрации.
2.4. Режим работы и производственные программы предприятия
Режим работы цеха
Режим работы цеха характеризуется числом рабочих дней в году, количеством рабочих смен в сутки и количеством часов работы в смену.
Режим работы устанавливается по нормам технологического проектирования предприятий отрасли, а при отсутствии их – исходя из требований технологии.
При назначении режимов нужно стремиться во всех случаях, когда это не обусловлено технологической необходимостью, избегать трехсменной организации труда, так как работа в ночной смене вызывает много трудностей.
В цехах и отделениях, не являющихся ведущими для проектируемого предприятия или имеющих сравнительно небольшую производительность, возможна односменная работа.
Принимаются следующие режимы работы: для предприятий с непрерывно работающими печами – непрерывная рабочая неделя при трехсменной работе, обычно, печное отделение заводов вспученного перлита работает 330 дней в году, а минераловатного производства – 365 дней.
Для остальных предприятий может быть принята работа по прерывной недели 260 дней (365 календарных дней – 104 выходных, 8 праздничных + 7 дней компенсации неполного рабочего дня по субботам) в две или в три смены в зависимости от производительности предприятия.
Для предприятий с автоклавной обработкой изделий принимают режим работы по 6-дневной рабочей неделе – 305 дней (365 календарных дней – 52 выходных и 8 праздничных), учитывая низкой коэффициент загрузки автоклавов. Для отделений тепловой обработки предусматривается трехсменная работа, для остальных отделений – двухсменная.
Если в одном и том же отделении некоторые операции выполняются в одну или две смены, а остальные круглосуточно, то режим работы должен члениться пооперационно. Так, например, автоклавное отделение газобетонного цеха может по загрузке работать в две 8-часовые смены, а тепловая работа автоклавов длиться 24 часа в сутки.
Номинальное число рабочих дней в году для складов и отделений по приему сырья и материалов и отгрузке готовой продукции железнодорожным транспортом 365 дней при трехсменной работе. Продолжительность рабочей смены 8 часов. Итоговые данные по запроектированным режимам рекомендуется сводить в табл. 6.
Номинальный годовой фонд рабочего времени определяется по формуле:
Фн=Дн·См·Тсм=260*2*8=4160
Годовой фонд чистого рабочего времени составляет:
Фч=Фн·Кти·Ксм=4160*0,95*0,85=3359,2
Коэффициент технического использования оборудования определяется с учетом времени простоя оборудования в год. Ориентировочно Кти=0,95.
Коэффициент использования рабочего времени вычисляют по формуле
где Тсм – продолжительность рабочей смены, ч;
Тпэ – время на подготовительно-заключительные операции, ч;
Тдн – время на личные надобности, ч;
Тотд – время на отдых, ч.
Ориентировочные значения коэффициента Ксм:
1. для помольного оборудования – 0,95;
2. для формовочного и резательного оборудования – 0,85;
3. для автоклавов – 1;
4. для отделочного оборудования в производстве ячеистого бетона – 0,85;
5. для оборудования по изготовлению арматуры – 0,9;
6. для плавильного оборудования – 0,75;
7. для конвейерных линий минераловатных производств – 0,75.
Таблица 11
№ п/п | Наименование цехов, отделений, операций | Кол-во рабочих дней в году Дн | Кол-во смен в сутки См | Продолжительность рабочей смены Тсм, ч | Номинальный годовой фонд рабочего времени, Фн, ч | Коэффициент технического использования оборудования Кти | Коэффициент использования рабочего времени Ксм | Годовой фонд рабочего времени Фч, ч |
1 | Цех по производству модифицированных пеногипсовых блоков | 260 | 2 | 8 | 4160 | 0,95 | 0,85 | 3359,2 |
Расходы сырья и полуфабрикатов
Таблица 12
№ п/п | Наименование сырья и полуфабрикатов | Ед. измерения | Расходы в | |||
час | смену | сутки | год | |||
1. | Гипс | т | 1,7 | 13,46 | 26,9 | 7001,28 |
2. | Вода | т | 0,92 | 7,35 | 14,7 | 3825,12 |
3. | Модифицированная добавка | т | 0,1 | 0,82 | 1,64 | 426,82 |
4. | Пенообразователь | т | 0,06 | 0,48 | 0,96 | 249,6 |
Определение мощности цеха
В этом разделе технологической части расчет производства по полуфабрикатам и готовой продукции, исходя из принятого режима работы.
При расчете производительности следует учитывать возможный брак в производстве и производственные потери, размеры которых принимаются по соответствующим нормативам.
Средние величины возможных производственных потерь, %:
Для заводов ячеистых бетонов:
1. При формовке – 5;
2. При резке «горбушки» и резке массива:
- в индивидуальных формах – 10;
- при резательной технологии – 15;
3. При тепловой обработке – 2,5.
Расчет производительности для каждого технологического передела производится по формуле
П=(П0)/((1-Б)/100)),
где Пр – производительность рассчитываемого передела;
П0 – производительность передела. Следующего (по технологическому потоку) за рассчитываемым;
Б – производственные отходы и потери от брака, %.
Расчеты по производительности цеха приведены в табл.7.
Таблица 13
№ п/п | Наименование передела | Ед. изм. | Величина производственных отходов и потерь, % | Производительность в | |||
год | сутки | смену | час | ||||
1 | СГП | м3 | 0 | 12480 | 48 | 24 | 3 |
2 | Распалубка | м3 | 10 | 13728 | 52,8 | 26,4 | 3,3 |
3 | Формовка | м3 | 5 | 14414,4 | 55,44 | 27,72 | 3,5 |
4 | Приготовление пенобетонной смеси | м3 | 3 | 14846,8 | 57,11 | 28,55 | 3,6 |
Организация складского помещения
Склады производственных предприятий организуются для хранения необходимого сырья и выпускаемой готовой продукции.
Склад готовой продукции
1. Определение вместимости склада готовой продукции, м3
В=В1ˑТ, где
В1 - суточный объем готовых изделий, м3;
Т - продолжительность хранения, равная 10-14 суткам.
В= В1ˑТ =24 ˑ10=240 м3
2. Определение площади склада готовой продукции, м2
Па=(ВК1)/В2, где
К1 – коэффициент, учитывающий площадь склада на проходы и проезды, принимается равным 1,5;
В2 – нормативный объем изделий, допускаемый на 1 м2 площади, принимается равным 1,8 м3.
Па=(ВК1)/В2=(240ˑ1,5)/1,8=200 м2
2.5. Расчет площади и объемов узлов цеха
Бункера – саморазгружающиеся емкости для приемки и хранения сыпучих материалов – устанавливают над технологическим оборудованием для обеспечения его непрерывной работы. Обычно бункера рассчитывают на 1,5-2-часовой запас материала. Форма и размеры бункеров не стандартизированы.
Наибольшее применение нашли бункера прямоугольного поперечного сечения. Обычно верхняя часть бункера имеет вертикальные стенки, высота которых не должна превышать более чем в 1,5 раза размеры бункера в плане, нижнюю часть его выполняют в виде усеченной пирамиды с симметричными или лучше с несимметричными наклонными стенками. Для полного опорожнения бункера угол наклона стенок пирамидальной части должен на 10-15° превышать угол естественного откоса загружаемого материала в покое и угол трения о его стенки. Требуемый геометрический объем бункера определяют по формуле,
(6)
где ПЧ - расход материала, м3/ч;
n=2 - запас материала
η - коэффициент заполнения, принимается равным 0,85 - 0,9.
Определим требуемый геометрический объем бункера:
Vгеом = (2,8×2) / 0,9= 6,23 м³ для гипса
Vгеом = (0,171×2) / 0,9= 0,38 м³ для цеолита
2.6. Ведомость оборудования
Подбор оборудования для цеха по производству модифицированных пенобетонных блоков.
Установка Фомм – Проф. 1000
В установках Фомм – Проф. пенобетон производится по классической технологии (которая используется во всем мире), в качестве добавки применяется белковый пенообразователь GreenFroth. Сначала в установку загружается вода, цемент и песок и производится цементно песчаный раствор. Потом из пеногенератора в раствор добавляется пена и производится пенобетон. Произведенный пенобетон под действием избыточного воздушного давления подается в место заливки или в формы для производства пеноблоков.
Таблица 14
Техническая характеристика
№ п/п | Наименование | Показатель |
1 | Обслуживающий персонал, чел | 3 |
2 | Объем рабочей емкости смесителя, л | 1000 |
3 | Производительность, м3/ч | 6 |
4 | Мощность электродвигателя, кВт | 12 |
5 | Рабочее давление воздуха пеногенератора, атм | 6 |
6 | Масса, кг | 900 |
7 | Габариты в мм: - длина - ширина - высота | 2800 1200 1700 |
\
Компрессор ременной REMEZA СБ4-270.F37 - это воздушный компрессор для получения безмасляного сжатого воздуха. На компрессоре СБ4-F37 основан на поршневом блоке ANEST IWATA (Япония). , который гарантирует длительный срок эксплуатации компрессора и его надежную работу. Входной воздушный фильтр задерживает крупные частицы пыли и грязи. Ременной привод предусмотрительно защищен металлическим кожухом. Компрессор Remeza СБ4-F37 практически не нуждается в техническом обслуживании и может работать даже в тяжелых промышленных условиях.
Таблица 15
Техническая характеристика
№ п/п | Наименование | Показатель |
1 | Напряжение питания, В | 380 |
2 | Номинальная мощность, кВт | 4 |
3 | Производительность, л/мин | 675 |
4 | Тип компрессора | Поршневой, безмасляный |
5 | Объем ресивера, л | 270 |
6 | Масса, кг | 180 |
7 | Габариты в мм: - длина - ширина - высота | 1670 600 1200 |
Транспортер шнековый. Состоит из трубы в которую вмонтирован шнек, моторредуктора придающего вращение шнеку, загрузочной горловины и выходного отверстия.
Транспортер шнековый предназначен для транспортировки мелкодисперсных сыпучих материалов и смесей. Возможна эксплуатация на любых площадях с удобным подходом для эксплуатации при температуре не ниже 0ºС.
Транспортер шнековый подключается к трехфазной сети переменного тока напряжение питания 380 В, частотой 50 Гц, с глухо-заземленной нейтралью. Шнековый транспортер предназначен как для стационарной работы, так и на строительных объектах.
Рис. 6 Шнековый транспортер
Таблица 16
Технические характеристики
№ п/п | Наименование | Показатель |
1 | Длина транспортера, м | 5 |
2 | Диаметр шнека, мм | 210 |
3 | Производительность, т/час | 12 |
4 | Мощность приводного электродвигателя, кВт | 5 |
5 | Масса, кг | 350 |
Высокоточная форма на 60 блоков 400х200х200мм.Данные формы наиболее качественны и долговечны. Каждая форма весит около 1 тонны и без труда собирается и разбирается 2 работниками.
Формы пенобетона предназначены для получения пенобетонных блоков определенных типоразмеров. Выходящий из установки пенобетон заливается в форму, выстаивается в ней от 2 до 3 часов (время зависит от температуры, количества добавленного ускорителя и т.п.). После этого форма пенобетона разбирается, и из нее достаются готовые пенобетонные блоки.
Преимущества:
1. Гарантирована точность на блок в пределах 1 мм;
2. У формы максимально удобная конструкция, формы легко разбираются и обслуживаются 1 человеком, без помощников и техники;
3. Гарантировано отсутствие протечек без использования прокладок;
4. Формы устойчивы к внешним воздействиям и очень долговечны.
Таблица 17
Технические характеристики
№ п/п | Наименование | Показатель |
1 | Вес формы, кг | 500 |
2 | Материал формы | металл |
3 | Количество блоков | 60 |
4 | Объем формы, м³ | 0,96 |
Силос гипса. Несущий каркас и все части складов гипса изготавливаются из качественной стали и покрываются защитным составом от коррозии. Это позволяет работать в любых климатических условиях и гарантирует их долговечность. Детали силосов изготавливаются из стали толщиной 6 - 10 мм.
Для зимнего использования возможна обшивка многослойным утеплителем снаружи силосов. Внизу каждого силоса устанавливается электрический вибратор.
В комплект каждого склада цемента входит: силос цемента, опорные конструкции, площадка обслуживания, лестница, загрузочная труба, ограждения.
Выгрузка гипса из силоса осуществляется шнеком или пневмонасосом. Подача гипса в силос осуществляется по наклонному ленточному транспортеру, или пневматическим раздатчиком.
Таблица 18
Технические характеристики
№ п/п | Объем, м3 | Вес хранимого гипса, т | Диаметр, м | Высота, м | Масса, т |
1 | 40 | 52 | 2,4 | 13 | 5,5 |
Транспортеры ленточные.Транспортеры предназначены для подачи сыпучих компонентов из мест хранения в установки, где из них производится конечный продукт. Транспортер состоит из рамы, на которой на специальных поперечинах установлены ролики. На транспортерах с прямой лентой на каждой поперечине установлено по 1 валику, на транспортерах с лентой в форме желоба по 3 ролика. Установка 3 роликов позволяет получить ленту в форме желоба и наиболее эффективную передачу песка. Привод состоит из надежного моторедуктора напрямую подсоединенного к валу, через который приводится в движение лента.
Рис. 8 Ленточный транспортер
1 – рама; 2 – ведущий барабан; 3 – электродвигатель; 4 – червячный редуктор; 5 – натяжной барабан; 6 – ползун; 7 – натяжной винт; 8 – лента; 9 – опора роликовая верхняя; 10 – опора роликовая нижняя; 11 – стойка; 12 – раскос; 13 – винтовая опора; 14 – воронка (опцион.); 15 - скребок наружный; 16 – скребок внутренний.
Длина транспортера может быть любой. В зависимости от длины, нагрузки и скорости передачи по всей длине устанавливается разное количество роликов, а также подбирается моторедуктор необходимой мощности.
Погрузчик вилочный SF20Tгрузоподъемностью 2 тонны, высота подъема груза 3 м, предназначен для захвата, подъема и опускания изделия (груза), транспортировки его и укладки, а также для других работ в условиях промышленности, строительства, транспорта и складского хозяйства.
В конструкции применена безмостовая схема привода хода погрузчика с раздельным приводом каждого колеса, применены гидравлические дисковые тормоза с металлокерамическими дисками, отличающиеся высокой надежностью, установлен нейтрализатор выхлопных газов для работы в закрытых помещениях.
Таблица 19
Технические характеристики
№ п/п | Наименование | Показатель |
1 | Номинальная грузоподъемность, т | 2 |
2 | Масса снаряженного автопогрузчика не более, т | 4,8 |
3 | Номинальная мощность двигателя, кВт (л.с.) | 37 (2650) |
4 | Максимальное давление в гидросистеме, не менее, МПа (кг/см2) | 18 (180) |
5 | Максимальное давление в приводе хода, МПа (кг/см2) | 32 (320) |
6 | Высота подъема груза, м | 3,3 |
7 | Радиус поворота по наружному габариту, мм | 2350 |
8 | База, мм | 3445 |
9 | Угол наклона грузоподъемника (вперед/назад), не менее, ºС | 6 / 12 |
10 | Скорость подъема груза, м/с | 0,3 |
11 | Скорость передвижения, (с грузом / без груза) не менее, км/ч | 20 / 20 |
12 | Расстояние центра массы груза от спинки вил, мм | 500 |
Щековая дробилка ДЩ-150.Поставщик – Научно-технологическая компания «Активатор» г. Новосибирск. Подготовка сырья для шаровых мельниц проводится в щековых дробилках. Щековые дробилки перерабатывают кусковый материал крупностью от 2-3 мм до 300 мм и измельчают его до 0,5-1 мм с производительностью 100-1000 кг/ч.
Материал загружается в бункер через загрузочное окно, попадает в камеру дробления. Дробление производится двумя плитами (щеками) которые приводятся в движение электродвигателем через ременную передачу. Размер фракции и производительность регулируется путем перемещения щек и выставления ширины разгрузочной щели.
Специальные исполнения дробилок позволяют измельчать материал не только раскалыванием, но и сдвигом. В иллюстрациях на примере волластонита и мрамора показано как щековая дробилка может эффективно измельчать кусковой материал до крупки.
Таблица 20
Технические характеристики
№ п/п | Наименование | Показатель |
1 | Размер входящего материала, мм | 100-300 |
2 | Размер измельченного материала, мм | 0,5-5 |
3 | Производительность, кг/ч | 400 |
4 | Мощность электродвигателя, кВт | 3 |
5 | Обороты электродвигателя, об/мин. | 1500 |
6 | Масса, кг | 300 |
7 | Габариты в мм: - длина - ширина - высота | 1000 800 1000 |
Центробежно-эллиптическая шаровая мельница «Активатор-С500»: Максимальная производительность (500 кг/час) для сверхтонкого помола (1-3 микрона).
«Активатор-С500» (500 кг/час) идеально подходит для комплектации линий приготовления пенобетона, газобетона, пеносиликатов, сухих строительных смесей, ВНВ бетонов. Помол различных наполнителей для строительства и лакокрасочного производства: мрамор, мел, тальк, волластонит, кальциты, доломит, бентонит, каолин, кварц, песок и т.д.
Таблица 21
Технические характеристики
№ п/п | Наименование | Показатель |
1 | Количество помольных камер, шт. | 2 |
2 | Внутренний диаметр помольной камеры, мм | 105 |
3 | Производительность, кг/ч | 500 |
4 | Мощность электродвигателя, кВт | 11 |
5 | Обороты электродвигателя, об/мин. | 1000 |
6 | Длина (без помольных барабанов), мм. | 1100 |
7 | Длина помольного барабана, мм. | 1500 |
8 | Масса, кг | 650 |
9 | Габариты в мм: - длина - ширина - высота | 1000 800 1000 |
Дезинтегратор мокрого помола - «ДМПК-ГОРИЗОНТ» производства машиностроительного предприятия «ТЕХПРИБОР» г. Щекино Тульской области относится к типу измельчительного оборудования ударного действия и предназначен для измельчения широкого перечня материалов, а также приготовления высокосвязных паст, растворов, суспензий.
Это быстроходный четырехрядный дезинтегратор с функцией принудительной очистки камеры помола, реализующий один из наиболее эффективных способов разрушения твердых тел - «свободный удар». Помимо самого дезинтегратора мокрого помола, агрегат включает в себя: конвейер-питатель, магнитный сепаратор, насос выдачи раствора, дозатор жидких компонентов, пульт управления.
Краткий перечень технологических возможностей дезинтегратора «ДМПК-ГОРИЗОНТ»®:
1) Коллоидный помол в присутствии диспергирующей среды (жидкости, ПАВов). Агрегирование (слипание) частиц в процессе их измельчения, как правило, является негативным фактором, снижающим технологическую ценность продукта. При тонком помоле материала отдельные частицы должны быть удалены друг от друга на такое расстояние, чтобы силы взаимного притяжения не смогли преодолеть расклинивающего действия жидкости. Ударное измельчение в диспергирующей среде устраняет проблему агрегирования тонких частиц позволяя создавать устойчивые коллоидные системы с отношением твердой и жидкой фазы от 1:2 до 1:6;
2) Высокая степень измельчения, механоактивация - низкие энергозатраты. Быстроходные дезинтеграторы - это высокоэнергонагруженные измельчительные агрегаты. Большая интенсивность ударных воздействий обеспечивает не просто быстрое разрушение частиц материала, но и глубокие изменения их внутренней структуры. Часть затраченной на измельчение энергии аккумулируется в виде дефектов и искажений кристаллической решетки, в результате чего продукт «ударного» помола приобретает большую реакционную способность. Избыточная энергия дефектов структуры позволяет в полной мере использовать адсорбционный эффект уменьшения прочности частиц, увеличения их хрупкости, снижения удельного расхода энергии на разрушение твердого тела (эффект Ребиндера);
3)
Приготовление растворов, паст, суспензий с заданным соотношением твердых и жидких компонентов. Одна из традиционных областей применения дезинтеграторов - смешивание. Ни один другой агрегат не способен обеспечить такой высокий уровень усреднения компонентов смеси как дезинтегратор. Помимо возможности «сухого» перемешивания материалов естественной влажности, дезинтегратор мокрого помола «ДМК-ГОРИЗОНТ»® также позволяет получать многокомпонентные растворы высокой связности, консистенция (подвижность, вязкость) которых определяется требованиями последующих технологических процессов.
Измельчительный агрегат - «ДМПК - ГОРИЗОНТ»® (Рис.2) состоит из дезинтегратора мокрого помола (1), магнитного сепаратора (2), винтового питателя с расходным бункером на раме (3), растворонасоса выдачи продукта помола (4), расходомера - дозатора жидких компонентов (5), шкафа управления работой агрегата.
Материал, подлежащий измельчению, загружается в расходный бункер винтового питателя. Регулирование производительности питателя, а значит и объема материала, поступающего в дезинтегратор, производится за счет изменения частоты вращения подающего винта. Для повышения точности дозирования сыпучих материалов и предотвращения сводообразования в расходном бункере питателя смонтирован шнек-ворошитель.
Из разгрузочного патрубка винтового питателя материал поступает в магнитный сепаратор, где происходит отделение ферромагнитных включений.
Далее материал через загрузочную горловину поступает в помольную камеру дезинтегратора, а именно в центр роторов-корзин. На своем пути от центра роторов к их периферии частицы материала сталкиваются с помольными органами и быстро разрушаются, при этом интенсивность ударного воздействия постоянно возрастает по мере удаления частиц от центра и увеличения линейной скорости пальцев-бил. При измельчении материала в водной среде (высокое водотвердое отношение) размольная мощность дезинтегратора еще более увеличивается благодаря высокочастотным колебаниям и кавитационному эффекту.
Жидкие компоненты подаются в камеру помола от расходомера-дозатора через полый вал привода в центр ротора-корзины на специальный рассекатель. Подобная схема подачи, когда жидкость в камере помола пребывает в аэрозольном состоянии, характеризуется высоким качеством распределения, смачивания поверхности частиц обрабатываемого материала.
По выходу из камеры помола полученный раствор, паста или суспензия попадает в цилиндрический корпус растворонасоса, установленного в нижней части корпуса дезинтегратора. Выдача продукта производится по гибкому рукаву Ду-50 под избыточным давлением 18 кгс/см2.
Таблица 22
Технические характеристики
№ п/п | Наименование | Показатель |
1 | Количество роторов | 2 |
2 | Расположение роторов | горизонтально-соосное |
3 | Производительность, м3/ч | 1-4,6 |
4 | Мощность электродвигателя, кВт | 40 |
5 | Максимальный размер частиц перерабатываемого материала, мм | не более 12 |
6 | Масса, кг | 1682 |
7 | Габариты в мм: - длина - ширина - высота | 3300 2900 2500 |
8 | Твердость перерабатываемого материала по шкале Мооса | не более 4 |
Области применения:
1. Химическое производство: как измельчитель, коллоидная мельница, разрыхлитель, смеситель, гомогенизатор, аппарат для проведения ряда химических и массообменных процессов;
2. Топливо и энергетика: механокрекинг и гидрогенизация каменного угля. Синтез жидкого топлива на основе гидрирования экстрактов из угля, торфа, лигнина и другого твердого сырья. Механоактивация угля в процессах подготовки облагороженного топлива. Усовершенствование способов переработки угля посредством пиролиза, гидрогенизации, экстракции. Дезинтеграторный помол угля позволяет повысить его теплоту сгорания, снизить давление некоторых технологических процессов, увеличить выход полезных компонентов, устранить выброс от дымовых отходов вредных веществ;
3. Производство удобрений: измельчение, повышение реакционной способности апатитов и фосфоритов. Изготовление комбинированных удобрений на основе твердофазных реакций;
4. Производство строительных материалов и минеральных красителей: активация минеральных вяжущих веществ, получение коллоидных растворов. Приготовление многокомпонентных композиционных смесей, паст и суспензий.
В ведомости оборудования перечисляется все основное технологическое и транспортное оборудование, принятое в проекте к установке. В ведомости указываются название, тип и краткая техническая характеристика оборудования (паспортная производительность и мощность электродвигателя); для грузоподъемного оборудования дополнительно – грузоподъемность, для ленточных конвейеров – длина (между осями барабанов), для элеваторов – высота в габарите. Для бункеров достаточно привести в ведомости их емкость и указать материал бункеров.
Таблица 23
№ п/п | Наименование и краткая характеристика оборудования | Кол-во | Примечание |
Основное оборудование | |||
1 | Пенобетоносмеситель Фомм – Проф. 1000 | 1 | |
2 | Высокоточная форма на 60 блоков 400х200х200 | 6 | |
3 | Компрессор | 1 | |
4 | Цифровая дозация воды | 1 | |
5 | Транспортер ленточный | 2 | |
6 | Щековая дробилка | 1 | |
7 | Измельчительный агрегат «ДМПК-ГОРИЗОНТ» | 1 | |
8 | Весовой дозатор добавок | 3 | |
11 | Расходные баки с нагревателями | 2 | |
13 | Погрузчик вилочный | 1 | |
14 | Упаковщик поддонов пенобетона | 1 | |
15 | Силос для гипса | 2 | |
16 | Расходный бункер для цеолита | 3 | |
17 | Расходный бункер для модифицированной добавки | 1 | |
18 | Цифровой программируемый пульт управления производством | 1 | |
19 | Шаровая мельница «Активатор С-500» | 1 | |
20 | Автомат для фасовки в формируемый пакет (doy-pack) паст | 1 | |
Дополнительное оборудование | |||
1 | Фильтр силоса | 1 | |
2 | Предохранительный клапан силоса | 1 | |
3 | Пластина аэрации | 6 | |
4 | Осушитель воздуха Camozzi MC202 | 1 | |
5 | Весы электронные для взвешивания пены (от 1 до 5000г, точность 1г) | 1 | |
6 | Прибор контроля прочности Черноусенко | 1 | |
7 | Мойка Karcher для очистки установок | 1 | |
8 | Грузовик для перевозки продукции | 1 |
2.7. Расчет потребностей в энергетических ресурсов
Расчет потребности в энергетических ресурсах
Таблица 24
Расход электроэнергии
| Основное оборудование и его наименование с электродвиг. | Кол-во единиц оборудова-ния | Мощность электродвигателей, кВт | Коэфф-нт исп. во времени | Коэф. загружения по мощности | Часовой расход электроэнер. с учетом коэф. исп. и загрузки по мощности, кВтЧч | |
Единицы | Общая | ||||||
1 | Установка Фомм – Проф | 1 | 12 | 12 | 0,9 | 0,9 | 9,72 |
2 | Компрессор ременной REMEZA СБ4 – 270 | 1 | 4 | 4 | 0,9 | 0,9 | 3,24 |
3 | Цифровая дозация воды | 1 | 2 | 2 | 0,3 | 0,39 | 0,234 |
4 | Транспортер ленточный | 4 | 5,5 | 22 | 0,85 | 0,85 | 15,89 |
5 | Щековая дробилка | 1 | 3 | 3 | 0,85 | 0,85 | 2,16 |
6 | Шаровая мельница | 1 | 11 | 11 | 0,3 | 0,8 | 2,64 |
7 | Измельчительный агрегат | 1 | 40 | 40 | 0,85 | 0,85 | 28,9 |
8 | Весовой дозатор добавок | 3 | 0,3 | 0,9 | 0,6 | 0,72 | 0,38 |
9 | Погрузчик вилочный | 1 | 33 | 33 | 0,3 | 1,3 | 12,87 |
10 | Упаковщик поддонов пенобетона | 1 | 0,6 | 0,6 | 0,3 | 1,3 | 0,234 |
11 | Цифровой программируемый пульт управления производством | 1 | 1 | 1 | 0,8 | 0,8 | 0,64 |
Итого: | 77 |
Потребность завода в энергетических ресурсах
Таблица 25
Потребность завода
Наименование энергетического ресурса | Единица измерения | Расходы | |||
в час | в смену | в сутки | в год | ||
Электроэнергия | кВт | 77 | 616 | 1232 | 320320 |
2.8. Штатная ведомость завода или цеха
Таблица 26
№ п/п | Должность | Количество рабочих в сутки |
АУП | ||
1 | Директор | 1 |
2 | Бухгалтер | 1 |
Основные рабочие | ||
3 | Начальник цеха | 2 |
4 | Заместитель начальника цеха | 2 |
5 | Лаборант | 2 |
6 | Наладчик оборудования | 2 |
7 | Водитель погрузчика | 2 |
8 | Сменный мастер | 2 |
9 | Рабочие | 4 |
10 | Механик цеха | 2 |
11 | Уборщик | 3 |
12 | Начальник цеха | 2 |
13 | Заместитель начальника цеха | 2 |
ИТОГО: | 21 |
Технический контроль
Консультант: ____________________________________Т.С.Антипкина
3.1. Входной контроль сырьевых материалов
При входном контроле проверяется наличие сопроводительных документов (паспортов и сертификатов), по которым устанавливается возможность применения материалов, полуфабрикатов. Кроме того, проводят необходимые испытания материалов, применяемых для приготовления пенобетона. В лаборатории входного контроля проверяют качество материалов, поступающих на предприятие. Организуют и контролируют проведение технологического опробования материалов в цехе, оформляют акты на забракованные материалы, контролируют соблюдение правил хранения материалов на складе, информируют отделение о качестве поступающих материалов, извещают поставщиков о некачественных материалах, выявленных при входном контроле и в процессе производства.
3.2. Пооперационный контроль производства
Для технологической линии производства пенобетонных блоков с применением цеолитовой пасты разрабатывают технологическую карту производственного процесса (технологические правила, регламентирующие содержание, последовательность и способы выполнения операций на всех стадиях изготовления изделий). При операционном контроле во время выполнения или после завершения определенной технологической операции определяют соответствие технологических параметров производства к требованиям проектной и технологической документации. Приемка законченных стеновых блоков включает:
1) освидетельствование конструкций, включая необходимые контрольные замеры, а в необходимых случаях – контрольные испытания;
2) проверку документации, связанной с приемкой и испытанием материалов, полуфабрикатов и изделий, которые применяются при изготовлении стен;
При приемке законченных стеновых блоков должно проверяться:
1) соответствие стен рабочим чертежам и правильность их расположения в плане и по высоте;
2) качество пенобетона по прочности, плотности, влажности, а в необходимых случаях и другие показатели, предусмотренные проектом.
3.3. Приемо-сдаточный контроль
Приемку изделий проводят в соответствии с ГОСТ 13015, настоящего стандарта, а также договора на изготовление (поставку) продукции.
Изделия принимаются партиями. Партией считают число изделий, изготовленных из одного сырья, по одной технологии, одной марки по средней плотности, одного класса по прочности на сжатие, в объеме не менее сменной, но не более суточной выработки или заказа. В договоре на поставку может быть установлен иной объем партии.
Циклограмма производства
Консультант: ______________________________________К.Е. Филиппова
4.1. Общие положения
Предприятие по производству модифицированных пенобетонных блоков мощностью 7200 м3 в год расположено в г. Якутске.
Гипс будет храниться в силосах. Склад цеолита и добавок будет размещаться непосредственно в складе.
Снабжение цеха сырьем производится следующим образом: большой транспортный расход уделяется гипсу, из-за расстояния перевозки г. Иркутск, в 3128 км от г. Якутска – поставщик ООО ТД «Ангарский гипсовый завод» и пластификатору г. Владимир, в 7780 км от г. Якутска – поставщик ООО «Компонент». Цеолит доставляется автосамосвалом с месторождения Хонгуруу которое расположено в 22 км к востоку от поселка Кемпендяй Сунтарского района, на правом склоне долины ручья Курун-Юрях в отгорах хребта Хонгуруу. Вода поступает с центрального трубопровода.
В производстве строительных материалов, как правило, участвуют не одиночки, а целые коллективы, вступая при этом в определенные производственные отношения.
В условиях рыночной экономики предприятия должны удовлетворять определенные требования:
1. область большей гибкостью в организациях и управлении производством;
2. точно выполнять договорный срок;
3. систематически анализировать объем выручки, полученной от реализации продукции и затраты на ее производство;
4. контролировать и добиваться повышения качества;
5. следить за конкурентным уровнем производства, внедрить передовые достижения в науке, технике и технологии.
Для выполнения любых строительных процессов требуются материально-технические и трудовые ресурсы. К первым относятся строительные материалы, конструкции и детали, строительные машины, механизмы, инвентарь, приспособления и инструменты, а ко вторым – строительные рабочие различных профессий и квалификаций, а также машинисты строительных машин и механизмов. Кроме них в строительном производстве принимают участие звеньевые и бригадиры, назначаемые из числа наиболее квалифицированных рабочих, а также инженерно-технические работники (ИТР) – мастера, производители работ, начальники участков, инженерно-технический персонал подготовки и управления строительным производством.
Организационная структура управления цехом
Дата добавления: 2018-02-18; просмотров: 720; Мы поможем в написании вашей работы! |
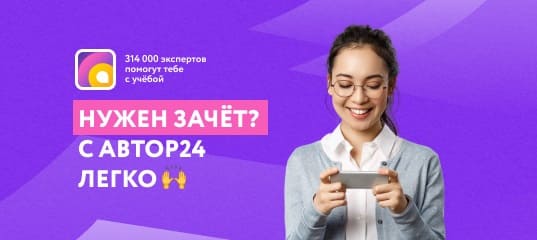
Мы поможем в написании ваших работ!