Жёсткость машиностроительных конструкций.
Способность деталей сопротивляться изменению формы под действием нагрузки и сохранять деформацию в пределах нормы является одним из важных критериев работоспособности. Для некоторых конструкций расчеты на жесткость являются основными; их производят, исходя из заранее заданных перемещений. К таким деталям относятся, например, упругие чувствительные элементы приборов. Расчеты на жесткость обязательны при проектировании статически неопределимых конструкций, когда одних уравнений равновесия (механики) от изгибающих и крутящих моментов, нормальных и поперечных сил недостаточно. В этом случае дополнительными являются уравнения деформаций (сопромат). Оценка жесткости важна при расчетах устойчивости деталей, нагруженных сжимающими силами (пружины и т. д.), при проектировании деталей в условиях действия динамических нагрузок. В расчетах на жесткость должны учитываться иногда как собственная жесткость детали (деформация основного объема материала детали), так и ее поверхностная прочность (деформация поверхностных слоев).
Критерии жёсткости.
Таковыми считаются:
– критерий точности и стабильности работы , т.е недопущение возникновения статических или динамических перемещений элементов проектируемой конструкции, снижающих точность выполнения рабочих операций;
– критерий выносливости , т.е. недопущение повторных колебаний, неблагоприятно отражающихся на усталостной прочности проектируемой конструкции;
|
|
– критерий устойчивости перемещения — недопущение возникновения фрикционных автоколебаний тех или иных деталей в проектируемой конструкции..
Факторы, определяющие жёсткость конструкции.
Жесткость детали характеризуется:
-коэффициентом жесткости k, представляющим собой отношение нагрузки (сила, момент силы, давление) к деформации (угловой или линейной),
-обратной ему величиной — чувствительностью s = 1/k; k = F/δ = ЕА/l для стержня длиной l, площадью сечения А, с модулем упругости Е и удлинением δ; k = М/φ = GJ/l для вала диаметром d, углом закручивания φ, модулем сдвига G, моментом инерции J — пd4/32.
Конструктивные способы повышения жёсткости конструкции.
К основным конструктивным способам повышения жесткости относятся следующие:
• замена изгиба растяжением или сжатием;
• целесообразная расстановка опор, исключение невыгодных по жесткости видов нагружения (для деталей, работающих на изгиб);
• рациональное, не сопровождающееся возрастанием массы, увеличение моментов инерции сечений;
• рациональное усиление ребрами, работающими предпочтительно на сжатие;
|
|
• усиление заделочных участков и участков перехода от одного сечения к другому;
• предупреждение деформаций за счет введения поперечных и диагональных связей;
• увеличение жесткости смежных деталей;
• применение скорлупчатых, сводчатых, сферических, яйцевидных и тому подобных форм (для деталей коробчатого типа);
• применение конических, чашечных, сферических форм; рациональное оребрение, гофрирование (для деталей типа дисков);
• применение коробчатых, двутельных, ячеистых и сотовых конструкций (для деталей типа плит). Реализацию некоторых из перечисленных способов рассмотрим на следующих примерах.
На рис. 2.9 показаны конструкции литых кронштейнов. В первом случае балочный кронштейн подвергается изгибу (см. рис. 2.9, а) и конструкция не обладает необходимой жесткостью. Стержни в раскосном кронштейне (см. рис. 2.9, б) работают преимущественно на растяжение-сжатие, что позволяет увеличить жесткость конструкции. Она становится еще более прочной и жесткой, если стержни кронштейна соединить сплошной перемычкой, связывающей их в жесткую систему (см. рис. 2.9, в). Кронштейн ферменного типа с вертикальным стержнем (см. рис. 2.9, г) значительно менее жесткий, чем кронштейн на рис. 2.9, б, так как конец вертикального стержня под нагрузкой перемещается приблизительно по направлению действия силы и на ограничение деформаций его жесткость не влияет. На рис. 2.10, а показан случай нагружения цилиндра осевой силой. Нагрузка вызывает прогиб днища цилиндра, передающийся обечайке через пояс ее сопряжения с днищем (деформации показаны штриховой линией). Система является нежесткой. При замене цилиндра конусом (см. рис. 2.10, б) система по основной схеме восприятия сил приближается к стержневой ферме: стенки конуса работают преимущественно на сжатие; роль стержня, воспринимающего распор, в данном случае выполняют жесткие кольцевые сечения конуса, ограничивающие радиальные деформации стенок. Повышенную жесткость имеют сферическая, яйцевидная и подобные им формы (см. рис. 2.10, в и г). На рис. 2.10, д — 2.10, з приведены примеры жестких конструкций. В этих случаях повышение жесткости и прочности состоит в придании деталям кольцевых поясов жесткости, из которых верхний 1 работает на сжатие, а нижний 2— на растяжение. В усиленных конструкциях (рис. 2.10, и — 2.10, м) введены элементы, непосредственно воспринимающие силу сжатия: ребра, цилиндры и конусы. Задача увеличения жесткости конструкций путем блокирования деформаций заключается в том, чтобы найти точки наибольших перемещений системы, деформируемой под действием нагрузки, и предотвратить эти перемещения введением элементов растяжения-сжатия, расположенных по направлению перемещений. Примером решения этой задачи может служить увеличение жесткости рам и ферменных конструкций раскосами.
|
|
|
|
Наиболее эффективно введение диагональных связей (раскосов), подвергающихся растяжению или сжатию (рис. 2.11). В порядке возрастающей жесткости на рис. 2.11, а — 2.11, и представлены схемы плоских ферм, а на рис. 2.11, к —2.11, « — сложных плоских ферм с усиливающими элементами, предотвращающими продольный изгиб и потерю устойчивости стержней. Повышению жесткости конструкций способствует рациональная расстановка опор, например, возможно большее их сближение. На рис. 2.12, а показана двухопорная установка зубчатого колеса. Если расстояние между опорами сократить, например, в З раза (см. рис. 2,12,6), то максимальные изгибающий момент и напряжения в вале уменьшаются также в 3 раза, а максимальный прогиб — в 27 раз. Благодаря уменьшению пролета, а также увеличению момента инерции работающего участка вала прогиб становится настолько малым, что практически не влияет на работу зубчатой передачи. Если увеличиваются наружные размеры детали и уменьшается толщина стенок, необходимо, во избежание местных деформаций, повышать жесткость в направлении, поперечном действию изгибающих моментов. На рис. 2.13 показаны балки, усиленные поперечными ребрами 1, коробками 2, полукруглыми накладками 3, косыми связями 4, 5. Увеличение жесткости аппаратов из пластмасс связано с рядом особенностей. Для уменьшения прогиба плоских
крышек и стенок применяют диаметральное и диагональное расположение ребер жесткости, причем последнее более технологично. При большой длине стенок аппаратов и наличии верхней отбортовки применяют вертикальные ребра, которые в сочетании с буртом и днищем образуют жесткие рамы прямоугольного сечения.
Контактная прочность.
Работоспособность ряда деталей машин (зубчатых колес, подшипников качения и др.) определяется контактной прочностью, т. е. прочностью их рабочих (контактирующих) поверхностей.
Разрушение этих поверхностей вызывается действием контактных напряжений σ// , которые образуются в месте контакта криволинейных поверхностей двух прижатых друг к другу деталей.
При отсутствии внешней нагрузки начальный контакт криволинейных поверхностей происходит в точке (например, контакт двух шаров и др.) или по линии (контакт двух цилиндров и др.).
После приложения внешней нагрузки начальный контакт этих поверхностей переходит в контакт по малой площадке с высокими значениями контактных напряжений. Эти напряжения распределяются по эллиптическому закону (рис. 0.6). Наибольшее их значение используется в качестве главного критерия работоспособности зубчатых, червячных и других передач, а также подшипников качения.
где q = Fr/b — нормальная нагрузка на единицу длины контактной линии;
Fr — сила, нормальная к площадке контакта;
b — рабочая длина контактной линии;
рпр — приведенный радиус кривизны,
pi и р2 — радиусы кривизны в точках контакта (знак минус берется для случая контакта выпуклой поверхности радиуса pi с вогнутой поверхностью радиуса р2);
£„р — приведенный модуль упругости,
Е\ и Ε2 — модули упругости материалов цилиндров; если материалы цилиндров одинаковы, то £1ф = £|=£2;
μ — коэффициент Пуассона.
Условием контактной прочности является
где [°]и ~ допускаемое контактное напряжение.
Дата добавления: 2018-02-18; просмотров: 1300; Мы поможем в написании вашей работы! |
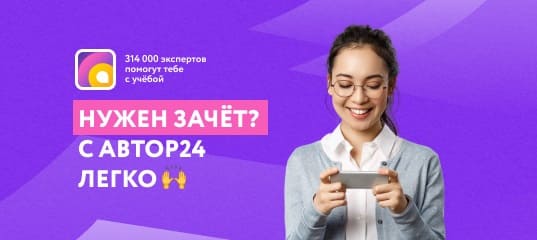
Мы поможем в написании ваших работ!