Отпуск. Необходим для снятия внутренних напряжений, внесённых при закалке. Материал становится более пластичным при некотором уменьшении прочности.
Нормализация, при которой изделие нагревают до аустенитного состояния (на 30-50 градусов выше АС3) и охлаждается на спокойном воздухе.
2. Поверхностное упрочнение стальных деталей.
Принцип поверхностной закалки заключается в нагреве некоторого поверхностного слоя до температуры выше критической АСз с последующим охлаждением этого слоя со скоростью большей, чем критическая скорость охлаждения металла обрабатываемой детали. Для достижения необходимой глубины закаленного слоя требуется его прогрев до температуры 820-900° С, в зависимости от состава стали, с последующим быстрым охлаждением струей воды или воздуха.
Основные методы поверхностного упрочнения можно разделить на три группы:
-механические — пластическое деформирование поверхностных слоев, создание наклепа (нагартовки);
-термические — поверхностная закалка;
-химико-термическая обработка — цементация, азотирование, хромирование и др.
3. Закалка токами высокой частоты.
Индукционный нагрев с последующей закалкой является одним из наиболее совершенных и рациональных методов поверхностного упрочнения стальных деталей токами высокой частоты . Однако индукционный нагрев имеет также некоторые недостатки, ограничивающие его применение. Использование индукционных установок экономично только для нагрева изделий одинаковых сечений. Как известно, переменный электрический ток в городской сети имеет частоту 50 Гц и относится к токам низкой частоты(промышленная частота). Переменный электрический ток с частотой выше 50 Гц называют током высокой частоты. ТВЧ для индукционного нагрева металла получают в специальных установках– генераторах. Они бывают машинными, полупроводниковыми и ламповыми. В машинных генераторах получают токи с частотой от 500 до 10 000 Гц, в полупроводниковых преобразователях – от 4000 до 66 000 Гц, а в ламповых генераторах – до 10 000 000 Гц (10 МГц).
|
|
Сущность индукционного нагрева заключается в следующем. Заготовка
(деталь) помещается в переменное магнитное поле проводника, несущего ток промышленной или повышенной частоты. Этот проводник называется индуктором и обычно изготовляется из медных трубок, которые навиваются в виде спиралей круглого или другого сечения (в зависимости от формы нагреваемой заготовки). Ему может быть придана любая другая форма, если это необходимо для получения заданного температурного поля детали. Вследствие электромагнитной индукции в поверхностном слое детали возникает вихревой ток (ток Фуко), который его и нагревает, что в дальнейшем, при проведении операции быстрого охлаждения приводит к закаливанию или упрочнению поверхностного слоя на расчётную глубину.
|
|
4. Газопламенная закалка.
При газопламенной закалке для получения необходимой температуры закалки на некоторой глубине (обычно 3-5 мм) сама поверхность должна быть нагрета примерно до 1000-1150° С.
Высокочастотная закалка требует применения специального оборудования и является целесообразной в основном при массовом производстве. Для газопламенной поверхностной закалки используются простейшие приспособления и аппаратура. Такая закалка является широко применяемым производственным процессом.
В качестве источника нагрева при газопламенной закалке используется в основном ацетилено-кислородное пламя, хотя могут применяться и заменители ацетилена. Степень нагрева поверхностного слоя регулируется мощностью пламени и длительностью его воздействия. Необходимое распределение температур к моменту начала охлаждения показано на рис. 129. Охлаждение производится водой при ее различной начальной температуре или различными водными растворами.
Газопламенной закалкой могут обрабатываться все углеродистые, низколегированные стали, подвергаемые обычной закалке, и, кроме того, стали с малым содержанием углерода и чугуны.
|
|
5. Старение или дисперсионное отвердение.
После проведения отжига проводится нагрев на более низкую температуру с целью выделения частиц упрочняющей фазы. Иногда проводится ступенчатое старение при нескольких температурах с целью выделения нескольких видов упрочняющих частиц.
6. Обработка стали холодом.
В закаленной стали, особенно содержащей более 0,4–0,5 % С, у которой точка Мк лежит ниже нуля, всегда присутствует остаточный аустенит. Аустенит понижает твердость, износостойкость и нередко приводит к изменению размеров деталей, работающих при низких температурах, в результате самопроизвольного превращения его в мартенсит.
Для уменьшения количества остаточного аустенита в закаленной стали применяют обработку холодом, заключающуюся в охлаждении закаленной стали до температур ниже нуля.
Понижение температуры до точки Мк (–30 ÷ –70 °С) С для большинства сталей вызывает превращение остаточного аустенита в мартенсит, что повышает твердость сталей с 0,8–1,1 % С на HRC 1–3. Однако одновременно, возрастают напряжения, поэтому изделия охлаждают медленно и сразу после обработки холодом выполняют отпуск.
Выдержка стали после закалки при комнатной температуре более 3–6 ч стабилизует аустенит, и поэтому он менее полно превращается в мартенсит при дальнейшем охлаждении и уменьшает эффект обработки холодом. В данном случае обработку холодом выполняют сразу после закалки.
|
|
Обработку холодом используют главным образом для измерительных инструментов, для пружин и деталей из цементируемых высоколегированных сталей, сохраняющих много аустенита после закалки.
7. Упрочнение методом пластической деформации.
К этому методу относятся:
-для наружных поверхностей — дробеструйный наклеп, обкатка шариковыми и роликовыми головками, чеканка;
-для внутренних цилиндрических поверхностей — раскатка шариковыми и роликовыми головками, дорнирование, калибрование мерными шариками.
Дата добавления: 2018-02-18; просмотров: 394; Мы поможем в написании вашей работы! |
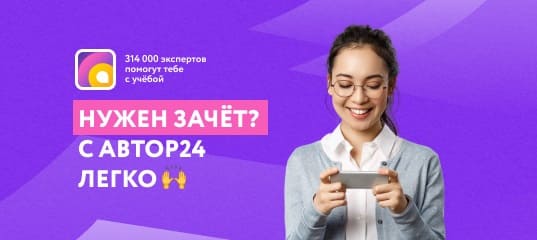
Мы поможем в написании ваших работ!