Глава 3. Конструкционные материалы
3.1. Металлы и сплавы. Требования. Химический состав. Показания к использованию. Технология применения, свойства.
3.1.1. Историческая справка
Большинство металлов было открыто в XIXв., хотя тогда далеко не все из них получили промышленное использование.
Применение металлов в технике началось с меди, серебра и золота. Затем начали применять те из них, которые относительно легко восстанавливаются (олово, свинец) или их достаточно много в природе, например железо.
Именно железо в виде его сплава с углеродом получило наибольшее распространение, что связано с рядом причин: малой стоимостью, наилучшими механическими свойствами и большой распространенностью его руд в природе. В последствии сплавам железа с углеродом и другими металлами присвоили название СТАЛЬ.Исправил Стали, например, производят больше, чем всех остальных металлов, вместе взятых. Объем производства стали— важнейший показатель технической и экономической мощи государства.
Археологические исследования свидетельствуют, что самые древние металлические стоматологические протезы появились в VII–Vвв. до н.э. в Финикии и Этруссии.
Первым металлом для изготовления стоматологических протезов было золото. Из него изготавливали утраченные передние зубы, скрепляя их с оставшимися зубами золотой проволокой. В Греции и Риме на основе хорошо развитого ювелирного искусства начали изготавливать одиночные коронки и мостовидные протезы с использованием припоев. Монополия золота в стоматологии длилась более 2500 лет. Это объяснить можно тем, что золото и подобные ему металлы в природе находятся в самородном состоянии и не требуют каких-либо сложных технологий для получения металла из руды как металлы группы железа. Вдобавок, температура плавления золота 1083°С, и оно легко может быть расплавлено на открытом огне. До начала XX в. из-за высокой стоимости золота ортопедическое лечение конструкциями из золотых сплавов было доступно только для богатых особ и их окружения.
|
|
Использующиеся в настоящее время более широко дешевые сплавы на кобальто- и никелехромовых основах требовали сложной, еще неизвестной для того времени технологии выплавки и были сами еще неизвестны.
Впервые коррозионно-стойкие высоколегированные сплавы на основе железа начали применяться с середины XIXв., сначала в области машиностроения.
Возникшая новая отрасль промышленности— автомобилестроение— потребовала создания новых высококачественных жаропрочных сплавов. В начале 1900-х гг.для деталей двигателей внутреннего сгорания впервые были применены жаропрочные кобальтохромовые сплавы. Они получили название «Stellite» (стеллиты) за их яркость, блеск, твердость. Обладали чрезвычайно высокой коррозионной стойкостью, имели великолепные прочностные характеристики не только в обычных условиях, но и при высоких температурах, в агрессивных средах, не только в поковках или горячекатаных изделиях, но и в литом виде. Если бы не высокая стоимость кобальтохромовых сплавов типа«Stellite», то их можно было бы считать идеальными материалами для машиностроения.
|
|
С 1920-х гг. «Stellite» использовались серийно для изготовления деталей машин ответственного назначения. Например, для изготовления выпускных клапанов двигателей самолетов и автомашин, лопастей газовых турбин. До появления технологии изготовления спеченных порошков карбида вольфрама, литьевые сплавы типа «Stellite» использовалисьв производстведля изготовления резцов металлорежущих станков.
С 1930г. началось использование кобальто-хромовыхсплавов для изготовления съемных стоматологических протезов. Состав используемых сплавов был очень близок к составу промышленного сплава «Stellite». В стоматологическом применении «Stellite» получил название «Vitallium».
В 1943г. в США использовались несколько сплавов на кобальт-и никелехромовой основе: vitallium, ticonium, niranium, linorium, jelencoLG. Все эти сплавы схожи и содержат лишь небольшое количество железа и используются в основном для литья стоматологических протезов. По оценкам на 1949 г. более 80% всех каркасов протезов были отлиты из кобальтохромовых сплавов типа vitallium . В дальнейшем, в результате стремительного роста цен на золотые сплавы, количество протезов (в %), сделанных на кобальтохромовой основе, особенно увеличилось.
|
|
Применение традиционных неблагородных сплавов на основе кобальта, никеля и хрома для ортопедической стоматологии, вероятно, постепенно будет сокращаться в связи с возможностью побочных реакций у ряда пациентов, чувствительных к влиянию неблагородных металлов. Поэтому вторая половина прошлого столетия характеризуется бурным ростом числа материалов на основе драгоценных металлов.
В зависимости от химического состава сплавы разделяют на основе:
l Золота
l Платины
l Палладия и серебра
l Железа
l Никеля
l Кобальта
l Титана
В настоящее время на стоматологическом рынке представлены различные кобальтохромовые и никелехромовые сплавы, а также сплавы на основе золота, которые удовлетворяют практически всему диапазону требований современной ортопедической стоматологии.
|
|
3.1.2. Строение и свойства металлов
В химии под металлами понимают определенную группу элементов, которые, вступая в химическую реакцию с неметаллами, отдают им свои внешние (валентные) электроны.
4. Все металлы прежде всего следует разделять на две большие группы — черные и цветные.
5. Черные металлы имеют темно-серый цвет, большую плотность, высокие температуры плавления, относительно высокую твердость. Наиболее типичными представителями этой группы являются железо и его сплавы.
6. Цветные металлы чаще всего имеют характерную окраску: красную, желтую, белую, обладают большой пластичностью, малой твердостью, относительно низкими температурами плавления. Наиболее типичный представитель этой группы — медь.
7. Строение металлов и сплавов определяется макроскопическим и микроскопическим анализами.
8. Кристаллическое строение металлов.Все вещества в твердом состоянии имеют кристаллическое или аморфное строение. В кристаллическом веществе атомы расположены геометрически правильно и на определенном расстоянии друг от друга, в аморфном же — беспорядочно. Всякое вещество может находиться в трех агрегатных состояниях — твердом, жидком и газообразном.
9. В газах отсутствует закономерность расположения частиц (атомов, молекул); частицы хаотически двигаются, отталкиваясь однаот другой, и поэтому газ стремится занять возможно больший объем.
10. В твердых телах атомы располагаются в определенном порядке, силы взаимного притяжения и отталкивания уравновешены, и твердое тело сохраняет свою форму.
11. В жидкости частицы (атомы, молекулы) сохраняют лишь т.н. «ближний» порядок, т.е. в пространстве закономерно расположено небольшое количество атомов. Ближний порядок неустойчив: он то возникает, то исчезает под действием тепловых колебаний. Таким образом, жидкое состояние— как бы промежуточное между твердым и газообразным; при соответствующих условиях возможен непосредственный переход из твердого состояния в газообразное без расплавления (сублимация).
12. Правильное, закономерное расположение частиц в металле (сплаве) характеризует его кристаллическое состояние. Гипотеза о том, что в кристаллах частицы располагаются закономерно, была выдвинута еще в 1860г. Е.Е. Федоровым, но доказано это было только после открытия рентгеновских лучей в 1895г.
13. Свойства металлов объясняются особенностями их строения:
14. ● расположением и характером движения электронов в атомах;
15. ● расположением атомов, ионов и молекул в пространстве;
16. ● размерами, формой и характером кристаллических образований.
17. Металлы могут быть полиморфными и изоморфными. Полиморфные металлы — металлы, способные переходить из одного строения в другое и существовать в различных кристаллических формах при разных температурах (например, кобальт, олово, марганец, железо и др.). При изменении строения кристаллической решетки меняются свойства металлов. Изоморфные металлы имеют только один тип кристаллической решетки (например, алюминий, медь, никель, хром, ванадий и др.).
18. Кристаллизацией называется переход металла из жидкого состояния в твердое с образованием кристаллической решетки и возникновением кристаллов.
19. Простейший тип кристаллической ячейки — кубическая решетка. Здесь атомы «упакованы» недостаточно плотно. Некоторые металлы имеют тетрагональную решетку. При этом каждый металл обладает определенной кристаллической решеткой, которая при воздействии внешних факторов(термическая обработка, литье, наклеп и др.) может измениться. Это явление называется полиморфизмом.
20. Однако в кристаллическом строении присутствуют дефекты — атомные пустоты (вакансии), которые играют очень важную роль при протекании диффузных процессов в сплавах и зависят от их термической обработки.
21. Таким образом, правильность кристаллического строения нарушается двумя видами дефектов — точечным («вакансии») и линейными (дислокация), что обуславливает качественные характеристики металла.
22. Теоретические расчеты механической прочности реальных металлов, основанные на силе отрыва или сжатия атомных слоев металла, дают значения в 10–50 раз больше, чем наблюдается на практике. Причина этого лежит в том, что кристаллическая структура реальных металлов несовершенна.
23. В хорошо отожженных металлах в каждом кубическом сантиметре обычно имеется 106–107 дислокаций. В наклепанных металлах плотность дислокаций может быть в 100–10000 раз больше, что приводит к трещинам и разрушению металла.
24. Все кристаллы анизотропны. Различие свойств в зависимости от направления испытания называется анизотропией. Следует учесть, что каждой температуре кристаллизации (степени охлаждения) отвечает размер устойчивого «зародыша»; более мелкие, если они и возникают, тут же растворяются в жидкости, а более крупные растут, превращаясь в кристаллы. Указанная особенность процессов кристаллизации имеет огромное практическое значение при получении качественного литья.
25. Чем сильнее охлаждение металла, тем больше в нем возникает центров кристаллизации и, следовательно, тем меньше будут размеры отдельных зерен затвердевшего металла, т.е. при одной степени охлаждения одного и того же металла получается мелкозернистая структура, а при другой — крупнозернистая. Структура же металла имеет решающее влияние на его механические свойства.
26. Чтобы получить на практике нужную степень охлаждения, отливку расплавленного металла производят в холодные или подогретые формы, регулируя, таким образом, скорость образования центров кристаллизации и скорость роста кристаллов. Обычно процессы зарождаются у стенок и на дне формы, в которую выливается расплавленный металл.
3.1.3. Строение и свойства сплавов
В природе немногие металлы (золото, платина, серебро, ртуть и ряд других) встречаются в свободном (чистом) состоянии. Однако и они не нашли применения в ортопедической стоматологии в чистом виде, а получили распространение в виде сплавов.
Сплавом называется вещество, полученное путем сплавления двух или более элементов. Металлические сплавы — это макроскопически однородные системы, состоящие из двух или более металлов с характерными металлическими свойствами. В широком смысле сплавами называются любые однородные системы, получаемые сплавлением металлов, неметаллов, оксидов, органических веществ.
Cтроение сплава более сложное, чем металла, и зависит, главным образом, от того, в какие взаимодействия вступаютсоставляющие его компоненты. Взаимодействие компонентов, в свою очередь, зависит от условий процесса литья.
Известно три типа взаимоотношений компонентов сплава:
1) образование механической смеси;
2) образование химических соединений;
3) образование твердого раствора.
В твердом состоянии может не быть химического взаимодействия между компонентами и простыми веществами, образующими сплав. Тогда строение сплава является механической смесью отдельных частиц, зерен обоих компонентов. Такие сплавы образуют сурьма и свинец, кадмий и висмут и др.
Механическая смесь компонентов образуется тогда, когда последние не способны к взаимному растворению в твердом состоянии и не вступают в химическую реакцию с образованием соединения. При этих условиях сплав будет состоять из кристаллов компонентов, отчетливо выявляемых при микроскопическом анализе. При этом свойства сплава будут представлены усредненными свойствами элементов, которые его образуют.
Составляющие сплав вещества могут вступать в химическое взаимодействие, образуя химические соединения, или взаиморастворяться друг в друге, образуя растворы (например, при погружении алюминия в расплавленную медь или при соприкосновении платины с расплавленной сурьмой). При этом при кристаллизации разнородные атомы соединяются в определенной пропорции с образованием нового типа решетки, отличающейся от решеток металлов сплава.
Кроме механической смеси и химических соединений возможно образование таких фаз, которые не могут быть полностью отнесены к перечисленным и являются как бы промежуточными, например твердый раствор, при котором даже при значительном увеличении нельзя различить составляющие его частицы, т.к. одно вещество находится в состоянии ионов, атомов и молекул и внедряется в промежутки между молекулами другого вещества.Примером могут служить системы (сплавы) никель–хром, медь–никель и др.где, аустенитная структура нержавеющей стали получена в виде твердого раствора углерода в железе. ИсправленоВ жидком состоянии большинство металлических сплавов, применяемых в технике, представляют собой однородные жидкости, т.е.жидкие растворы. При переходе в твердое состояние во многих таких сплавах однородность сохраняется, следовательно, сохраняется и растворимость. Твердая фаза, образующаяся в результате кристаллизации такого сплава, называется твердым раствором.
Следовательно, в отличие от механической смеси, твердый раствор является однофазным, состоит из одного вида кристаллов, имеет одну кристаллическую решетку. Строение и свойства сплавов определяются фазовыми превращениями, протекающими при нагреве и охлаждении сплавов.
Технология получения сплавов требует ознакомления с процессами их легирования. Легирование — это придание особых свойств сплавам путем введения других металлов (элементов). Элементы, специально вводимые в определенных концентрациях с целью изменения строения и свойств сплава, называются легирующими элементами. Например, сталь, содержащая всего 0,05–0,1% ванадия или 0,1% титана, считается легированной титановой или ванадиевой. Золото, в основном, легируется серебром или медью, иногда платиной. Элементы, которые растворены в золоте, влияют на температуру плавления сплава. Платина в этой системе значительно повышает температуру плавления золота, поэтому важно знать, при какой температуре лигатуру наиболее целесообразно вводить, чтобы не сжечь основной металл. Эти сведения приобретают особую актуальность при изготовлении припоя, в состав которого вводился весьма легкоплавкий кадмий. В настоящее времяиз-за высокой токсичности кадмий в припое для золота применяется крайне редко.
3.1.4. Классификация сплавов
В стоматологии нашло применение более 500 различных сплавов. Классически выделяют группы благородных и неблагородных сплавов. В соответствии с международными стандартами деление сплавов на группы представлено следующим образом.
Группы металлических сплавов(Is0,1989)
1. Сплавы благородных металлов на основе золота:
●золотые;
● золото-палладиевые;
● серебряно-палладиевые.
2. Сплавы благородных металлов, содержащие 25–50% золота или платины, или другие драгоценные металлы;
3. Сплавы на основе неблагородных металлов:
● хромоникелевая сплав;
● кобальтохромовый сплав;
● никелехромовый сплав;
● кобальтохромомолибденовый сплав;
● сплавы титана;
● вспомогательные сплавы алюминия и бронзы для временного пользования, а на основе свинца и олова — для технологических целей.
4. Сплавы для металлокерамических конструкций:
● с высоким содержанием золота (более 75%);
● с высоким содержанием благородных металлов (золота
и платины, золота и палладия более 75%);
● на основе палладия (более 50%);
● на основе неблагородных металлов:
– на основе кобальта,+ хром > 25%, молибден > 2%;
– на основе никеля,+ хром > 25%, молибден > 2%.
Сплавы также можно классифицировать по ряду других признаков:
● по назначению (для изготовления съемных и несъемных протезов);
● по температуре плавления — легкоплавкие (с точкой плавления до 300°С); тугоплавкие — благородные сплавы (с температурой плавления до 1100°С — сплавы золота) и сплавы, температура плавления которых превосходит 1200°С (нержавеющие стали);
● по количеству компонентов сплава;
● по физической природе компонентов сплава;
● по технологии переработки и т.д.ДА
[U1]
В зависимости от назначения сплавы подразделяют на
· Литейные
· Деформируемые
· Спец. сплавы с металлическим и оксидными покрытиями
· Промежуточных назначений (вспомогательные)
В стоматологии для неблагородных сплавов употребляется обозначение NEM или NE. В металлургии сокращение NE определяет группу сплавов из «металлов, не содержащих железа». На сегодняшний день для обозначения неблагородных сплавов применяется более точное определение EMF(без драгоценных металлов).
В соответствии с международными нормами сплавы на основе благородных металлов в стоматологии подразделяются по их физическим свойствам и по рекомендованным областям применения на 4 типа:
тип 1 — низкая прочность — для малых нагрузок (вкладки);
тип 2 — средняя прочность — для средних нагрузок (накладки);
тип 3 — высокая прочность — для больших нагрузок (цельнолитые коронки, мостовидные протезы небольшой протяженности);
тип 4 — очень высокая прочность — для очень больших нагрузок (каркасы бюгельных протезов, телескопические коронки, балки, мостовидные протезы большой протяженности, каркасы для облицовки керамикой).
Требования к сплавам металлов, применямых в ортопедической стоматологии:
· биологическая индифферентность и антикоррозионная стойкость к воздействию кислот и щелочей в небольших концентрациях;
· высокие механические свойства (пластичность, упругость, твердость, высокое сопротивление износу);
· определенные физические (невысокая температура плавления, минимальная усадка, небольшая плотность и т.д.) и технологические свойства (ковкость, текучесть при литье и др.), обусловленные конкретным назначением.
Кроме общих требований к сплавам предъявляются и специфические требования. Так, если сплав металлов предназначен для покрытия керамикой, он должен иметь температуру плавления выше температуры обжига керамической массы, сходный с ней коэффициент теплового расширения и быть способным к сцеплению с керамикой. Большое значение приобрелоимеет соответствие коэффициентов термического расширения двух материалов, что предотвращает силовые напряжения в керамической облицовке, которые могут вызвать трещины и сколы последней.
3.1.5. Физические свойства сплавов.
Температура плавления сплава. Этим параметром определяется тип необходимого плавильного оборудования. Золотые сплавы имеют температуру плавления ниже температуры плавления чистого золота. Обычно эти сплавы расплавляют на воздухе в муфельных печах.
Сплавы на кобальтохромовой и никельхромовой основах имеют значительно более высокие температуры плавления— 1280–1450°С. Сплавы с такими температурами плавления нельзя плавить в муфельных печах. Для их плавления используют электрические дуговые печи, индукционные печи или специальные газовые горелки. Эти устройства сложны и требуют относительно более высокой квалификации персонала.
Плотность.Плотность золотосодержащих сплавов составляет 14–18г/см3. Плотность кобальтохромовых сплавов равна приблизительно 8,4г/см3. Плотность никелехромовых сплавов чуть ниже—8,2г/см3. Таким образом, плотность кобальтохромовых и никелехромовых сплавов почти в два раза ниже, чем золотосодержащих сплавов.
Модуль упругости.Стоматологические кобальтохромовые сплавы имеют модуль упругости около 228ГПа. Никелехромовые сплавы — около 186ГПа, а сплавы на основе золота — всего около 90 ГПа, т.е. модуль упругости никелехромовых сплавов в 2 раза, а кобальтохромовых стоматологических сплавов более чем в 2,5 раза выше, чем у золотых сплавов. Используя сплав с большим модулем упругости, можно изготовить тонкостенный протез с уменьшенным объемом и весом.
Усталость. Сплавы металлов обладают таким свойством как «усталость». Обычно усталость может возникать в таких конструкциях, как дуговые и мостовидные протезы, когда зубным техником и врачом – ортопедом не учитывается наличие циклических нагрузок во время акта жевания.
l При воздействии на металл большого числа циклических нагрузок (переменных нагрузок, меняющихся в одних и тех же пределах) может наступить разрушение от усталости. Наиболее опасная нагрузка при усталости – нагрузка симметричного типа, при которой меняется знак, а абсолютные величины напряжения равны между собой.
l Деталь, разрушенная от усталости, имеет весьма характерный излом с двумя зонами: зоной усталости с блестящей полированной поверхностью и зона разрушения с матовой, зернистой поверхностью (структурой).
Прочность.Небольшие различия в составе кобальтохромовых и никельхромовых сплавов оказывают влияние на их прочность. Предельная прочность на разрыв колеблется от 640 до 825МПа.
Предельная прочность стоматологического золотого сплава несколько ниже прочности литых кобальтохромовых сплавов. Наивысшими прочностными характеристиками обладают элементы стоматологических протезов — кламмеры и аттачмены, вырезанные электроискровым методом из деформированного кобальтохромового сплава.
Высокая прочность затрудняет шлифование и полирование сплавов, но противостоит повреждениям при эксплуатации (истиранию). Отделочные операции прочного, твердого материала требуют высококачественного абразивного инструмента и большего времени для обработки. Зубные техники для обработки твердых кобальтохромовых сплавов используют алмазный инструмент, электроэрозионную обработку, электролитическую полировку и пр.
Упругость определяется пределом текучести — величиной механического воздействия, необходимого для появления остаточной деформации. Это одно из важнейших свойств сплава, используемого для изготовления съемных протезов.
Международный стандарт — «Стоматологические литейные сплавы на металлической основе» —IS0 6871–01 устанавливает, что предел текучести не должен быть менее 500Мпа. Упругость упрочненных стоматологических золотых сплавов приблизительно равна упругости сплавов на никелехромовой основе.
Пластичность.Пластичность сплава зубного протеза характеризуется относительным удлинением сплава. Относительное удлинение — одно из свойств, которое трудно измерять, т.к. оно подвержено большим случайным ошибкам при измерениях. Международный стандарт «Стоматологические литейные сплавы на металлической основе» — 1S0 6871–01 устанавливает, что относительное удлинение при разрыве должно быть не менее 1,5%. Незначительная пористость или наличие какого-либо неметаллического включения в сечении испытуемого образца резко изменяет результат измерений. Протезы из сплавов с высокой пластичностью и прочностью на разрыв реже ломаются.
Широкое применение для несъемного протезирования получили нержавеющие стали. Введение достаточного количества никеля в хромистую сталь обеспечивает лучшие механические свойства, а также делает ее более устойчивой к коррозии. Внедрению в России нержавеющей стали способствовали исследования Д.Н. Цитрина в 1930-х годах.
Высокие физико-механические свойства, химическая стойкость и совершенство технологии привели к тому, что нержавеющие сплавы стали одним из основных материалов для изготовления несъемных протезов.
Термическая обработка нержавеющей стали проста и заключается в закалке в воде. В результате закалки твердость этих сталей не повышается, а снижается, поэтому для нержавеющих сталей закалка является смягчающей термической операцией.
Нагрев до 1050–1100°С вызывает растворение карбидов хрома в сплаве, а быстрое охлаждение фиксирует состояние пересыщенного твердого раствора. Медленное охлаждение недопустимо, т.к. при этом (как и при отпуске) возможно выделение карбидов хрома, приводящее к ухудшению пластичности и коррозийной стойкости.
Все марки нержавеющих сталей, или как их называют хромоникелевые сплавы, должны содержать не более 0,1% углерода и не менее 18% хрома, это обусловливает их устойчивость к коррозии. Никель добавляется к сплаву для повышения пластичности, ковкости и вязкости сплава. Впервые предложенные стали этого типа содержали 8% никеля. В несколько измененном виде они сохранились в качестве основных до настоящего времени и различаются содержанием углерода (0,04%, 0,08, 0,12%). Для предохранения от интеркристаллитной коррозии в хромоникелевые стали вводится титан (стали 1Х18Н10Т, 1Х19Н9Т [U2] и т. д.).
Cталь марки 1Х19Н9Т старое название(ЭЯ-1)[U3] содержит 0,1% углерода; 18% хрома; 9% никеля; 2% марганца, 0,35% титана, 1,0% кремния, остальное — железо. Используется в основном для изготовления несъемных паяных протезов: штампованных коронок, литых зубов, фасеток.
Cталь марки 20Х18Н9Тсодержит 0,20% углерода, 9% никеля, 18% хрома, 2,0%марганца, 1,0% титана, 1,0% кремния, остальное — железо.
Из этой нержавеющей стали фабричным способом изготавливают:
· стандартные гильзы, для изготовления штампованных коронок;
· кламмеры из проволоки круглого сечения (для фиксации съемных пластиночных протезов при частичном отсутствии зубов в полости рта) диаметром 1,0, 1,2мм и длиной 25 и 32мм;
· эластичные нержавеющие матрицыдля контурных пломб, а также полоски металлические сепарационные, которые изготавливаются методом холодной штамповки из стальной нержавеющей термообработанной ленты.
Сталь марки 25Х18Н102С содержит 0,25% углерода, 10,0% никеля, 18,0% хрома, 2,0% марганца, 1,8% кремния, остальное — железо.
Из нее фабричным способом изготавливают:
· зубы стальные(боковые верхние и нижние) для штамповано-паяных несъемных зубных протезов;
· каркасы стальныедля изготовления мостовидных протезов для последующей их облицовки полимером;
· проволоку диаметром от 0,6 до 2,0мм.
Свойства сплавов: легирование некоторыми элементами (никель, титан, марганец, кремний и др.) улучшает технологические и коррозийные свойства сплавов.
Углерод — придает твердость, хрупкость, увеличивает способность к коррозии.
Хром — придает устойчивость против окисления и коррозии, повышает твердость сплава, упругость, уменьшает его пластичность, вязкость и хрупкость. Является растворителем азота и обеспечивает необходимую его концентрацию в стали.
Никель — повышает пластичность, ковкость, вязкость, прочность, улучшает антикоррозийные свойства, снижает коэффициент линейного расширения сплава.
Титан — придает мелкозернистое строение стали, уменьшает хрупкость, устраняет склонность стали к межкристаллической коррозии.
Кремний — придает сплаву жидкотекучесть, более однородную структуру, улучшает его литейные свойства, повышает вязкость и упругие свойства стали.
Марганец — повышает прочность и твердость стали, снижает пластические свойства, улучшает показатели жидкотекучести, является хорошим поглотителем, снижает температуру плавления и способствует удалению вредных серных соединений из сплава, обеспечивает необходимую концентрацию азота в стали.
Азот — повышает коррозийную стойкость, твердость, обеспечивает большой потенциал деформационного упрочнения, улучшает характеристики упругости, что обеспечивает стабильность сохранения формы в тонких ажурных конструкциях.
Температура плавления нержавеющей стали составляет 1460–1500°С. Для паяния стали используется серебряный припой.
Дата добавления: 2021-04-15; просмотров: 198; Мы поможем в написании вашей работы! |
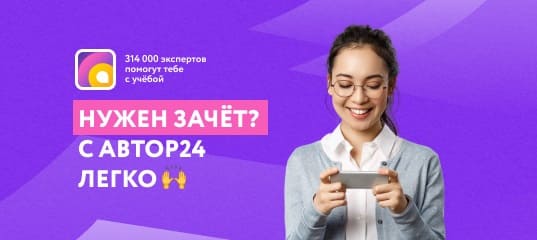
Мы поможем в написании ваших работ!