Анализ вариантов маршрутной технологии, выбор технологического оборудования и проектирование технологического процесса
По степени детализации процессы разделяется на следующие типы маршрутный, маршрутно-операционный, операционный. Маршрутный технологический процесс содержит перечень операций без разбивки на переходы и без указания режимов. При разработке маршрутной технологии следует руководствоваться следующим:
-при поточной сборке разбивка процесса на операции определяется ритмом сборки, причем время затрачиваемое на выполнение каждой операции должно быть равно или кратно ритму;
- предшествующие операции не должны затруднять выполнение последующих;
- на каждом рабочем месте должна выполняться однородная по характеру и технологически законченная работа;
- после наиболее ответственных операций сборки, а также после регулировки или наладки предусматривают контрольные операции;
- применяет более совершенные формы организации производства - непрерывные и групповые поточные линии и участки гибкого автоматизированного производства(ГАП);
Разработка вариантов маршрутной технологии сборки и монтажа изделия производится на основе схем типовых технологических процессов сборки блоков РЭА. Расчет суммарной Величины оперативного времени для технологического процесса по сравниваемым вариантам приведен в таблице 4.1.
Таблица 4.1 – Расчет суммарной величины оперативного времени
Наименование операции | Условия работы | 1 ВАРИАНТ | 2 ВАРИАНТ
| |||||||||
n | T0+Tвс | (T0+Tвс)n | Тпзсм | n | T0+Tвс | (T0+Tвс)n | Тпзсм | |||||
Распаковка и контроль ЭРЭ | (на 100 шт.) на ленте россыпью | 75 | 0,6 | 0,45 | 2,5 | 75 | 0,6 | 0,45 | 2,5 | |||
17 | 0,27 | 0,046 | 17 | 0,27 | 0,046 | |||||||
Комплектование элементов по операциям | Монтажный стол | 1 | 0.5 | 0,5 | 2,5 | 1 | 0.5 | 0,5 | 2,5 | |||
Расконсервация ПП | Монтажный стол | 1 | 0.430 | 0,43 | 2,5 | 1 | 0.430 | 0,43 | 2,5 | |||
Контроль ПП | Визуальный контроль | 1 | 0.207 | 0,207 | 2,5 | 1 | 0.207 | 0,207 | 2,5 | |||
Обрезка выводов навесных элементов бокорезами | Приспособление | 2 | 0,066 | 0,132 | 2,5 | 2 | 0,066 | 0,132 | 2,5 | |||
Лужение выводов ЭРЭ с предварительным флюсованием в ванне | На 1 элемент с 2 выводами | 2 | 0,102 | 0,204 | 2,5 | 3 | 0,102 | 0,204 | 2,5 | |||
Нанесение паяльной пасты | Автомат | 177 | 0,0025 | 0,442 | 25 | - | - | - | - | |||
Полуавтомат | - | - | - | - | 177 | 0,0035 | 0,62 | 20 | ||||
Установка чип компонентов | Автомат | 85 | 0.025 | 2,125 | 25 | 85 | 0.025 | 2,125 | 25 | |||
Контроль правильности установки | Визуальный контроль | 1 | 0,5 | 0,5 | 20 | 1 | 0,5 | 0,5 | 20 | |||
Пайка в печи | 1 | 0.7 | 0,7 | 25 | 1 | 0.7 | 0,7 | 25 | ||||
Контроль пайки | Визуальный контроль | 1 | 0.207 | 0,207 | 25 | 1 | 0.207 | 0,207 | 25 | |||
Установка ЭРЭ со штыревыми выводами | автомат | 7 | 0,064 | 0,448 | 25 | - | - | - | - | |||
полуавтомат | - | - | - | - | 7 | 0,08 | 0,56 | 20 | ||||
Контроль правильности установки навесных ЭРЭ | Визуальный контроль | 1 | 0.207 | 0,207 | 25 | 1 | 0.207 | 0,207 | 25 | |||
Пайка элементов | Установка пайки волной припоя | 1 | 0,82 | 0,82 | 55 | 1 | 0,82 | 0,82 | 55 | |||
Контроль пайки | Визуальный контроль | 1 | 0.207 | 0,207 | 2,5 | 1 | 0.207 | 0,207 | 2,5 | |||
Отмывка плат после пайки | Линия промывки плат | 1 | 0,67 | 0,67 | 20 | 1 | 0,43 | 0,43 | 20 | |||
Маркирование | Трафарет, кисть | 10 | 0.07 | 0,7 | 2,5 | 10 | 0.07 | 0,7 | 2,5 | |||
Лакирование ПП | 1 | 0,5 | 0,5 | 20 | 1 | 0,5 | 0,5 | 20 | ||||
Сушка | 1 | 1 | 1 | 20 | 1 | 1 | 1 | 20 | ||||
Выходной контроль печатного узла | автоматизированный стенд | 1 | 1 | 1 | 25 | 1 | 2 | 2 | 25 | |||
ИТОГО | 12,995 | 280 | 13,147 | 270 |
|
|
В числе двух вышеупомянутых вариантов маршрутной технологии были рассмотрены следующие:
· первый вариант характеризуется тем, что операции выполняются на автоматическом оборудовании. Этот вариант обладает большей производительностью, однако стоимость оборудования и подготовительно-заключительное бремя также высоки
· второй отличается тем, что основные операции выполняются на полуавтоматах и характеризуется заведомо меньшим подготовительно-заключительным временем истоимостью оборудования;
|
|
Определим тип производства исходя из коэффициентов операций:
![]() | (4.1) |
где - эффективно годовой фонд времени работы оборудования, ч:
![]() ![]() | (4.2) |
где ТСМ- количество часов работы в смену, ТСМ=8;
h - количество смен, h=2
Партия выпуска, шт:
![]() ![]() | (4.3) |
где N - годовая партия выпуска, N = 510000 шт;
a- периодичность запуска, дней .
![]() | (4.4) |
Так как K=0.39, т.е. меньше 1 то производство массовое и коэффициенты К1=1.05, К2=3.7, К3=5.
Выбор оптимального варианта технологического процесса необходимо обосновать производительностью труда. Производительность – количество деталей в штуках, которое изготовлено за единицу времени. Для этого проводится техническое нормирование операций технологического процесса.
Полное время, затрачиваемое на выполнение данной операции, называется штучно-калькуляционным временем:
![]() | (4.5) |
где – подготовительно-заключительное время, которое затрачивается на ознакомление с чертежами, получение инструмента, подготовку и наладку оборудования и выдается на всю программу выпуска.
![]() | (4.6) |
где – основное время (время работы оборудования);
– вспомогательное время (время на установку и снятие детали);
|
|
– время обслуживания (время обслуживания и замены инструмента);
– время перерывов (время на регламентированные перерывы в работе).
Для сборочно-монтажного производства объединяют и
и получают оперативное время
, а
составляют дополнительное время и задают его в процентах от
в качестве коэффициентов. Тогда:
![]() | (4.7) |
где – коэффициент, зависящий от группы сложности аппаратуры и типа производства;
– коэффициент, учитывающий подготовительно-заключительное время и время обслуживания;
– коэффициент, учитывающий долю времени на перерывы в работе.
![]() | |
![]() |
Составляется два уравнения для вычисления суммарного штучно-калькуляционного времени:
![]() | (4.8) |
![]() | (4.9) |
где и
– число операций по одному и второму варианту соответственно.
Подготовительно-заключительное время определяется по формуле:
![]() | (4.10) |
где – подготовительно-заключительное сменное время.
![]() | |
![]() | |
![]() | |
![]() |
Рассчитывается критический размер партии:
![]() | (4.11) |
шт.
При данном размере критической партии оба варианта маршрутной технологии оказываются одинаково производительными. Т.к. программа выпуска изделия превосходит размер критической партии, то целесообразным и дающим значительный выигрыш по производительности будет выбор первого варианта маршрутной технологии (табл. 4.1), который отличается большим уровнем автоматизации, меньшей суммой штучного времени и большей величиной подготовительно-заключительного времени по сравнению со вторым вариантом.
Описание оборудования с основными техническими характеристиками для выбранного варианта технологического процесса приведено ниже.
Выбор технологического оборудования согласно ГОСТ 14.304-73 ЕСТПП проводится путем анализа затрат на реализацию технологического процесса в установленный промежуток времени при заданном качестве изделия.
Выбор оборудования проводят также по главному параметру, являющемуся наиболее показательным для выбираемого оборудования, т.е. в наибольшей степени выявляющему его функциональное значение и технические возможности. В качестве главного параметра часто берут производительность технологического оборудования.
Для данного маршрута изготовления изделия используется следующее оборудование:
1. Операция лужения выводов микросхем осуществляется на установке УВЛ-902 92. Она снабжена ванной, содержащей 15 кг припоя, со щелевой сопловой насадкой размером 200×300 мм. Габаритные размеры установки – 540×290×330, масса – 20 кг, потребляемая мощность – 1,5 кВт. Операция заключается в погружении выводов в ванну расплавленного припоя.
2. Нанесение паяльной пасты осуществляется на автоматическом конвейернрм трафаретном принтере Motoprint-AVL с автоматической системой центрирования Motoprint-AVL отвечает всем современным требованиям, предъявляемым к процессу трафаретной печати: точности, надежности и повторяемости.
Все функции контролируются компьютером, все параметры печати программируются, машина автоматически выполняет механические настройки после открытия файла. Программирование и управление осуществляется с помощью клавиатуры, мыши и ЖКИ-монитора, на котором отображаются технологические параметры, кнопки управления и изображение, получаемое с обеих видеокамер.
Автоматическая система оптического центрирования с усовершенствованным программным обеспечением управляет совмещением контактных площадок платы и отверстий трафарета.
Технические характеристики Motoprint-AVL | |
Максимальный размер печати | 360х400 мм |
Скорость движения ракелей | 10-99 мм/сек |
Скорость разделения трафарета и платы | 0,5-5 мм/сек |
Точность печати | ±20 мкм |
Габаритные размеры | 1167х960х1770 мм |
Вес | 230кг |
Электропитание | 230 В, 50 Гц, 150 Вт |
3. Установка поверхностно-монтируемых элементов осуществляется на автомате установки SMD-компонентов SIPLACE HS-60.
Технические характеристики SIPLACE HS-60 | |
Производительность | 60000 комп/час |
Диапазон габаритов устанавливаемых компонентов | от 0,6 мм х 0,3 мм (0201) до 18,7 мм x 18,7 мм |
Габариты печатной платы (Д х Ш) | 50 мм х 50 мм до 368 мм х 460 мм |
Типы питателей | Лента, россыпь, специальная упаковка производителя компонента |
Электропитание | 4 кВт |
Занимаемая площадь | 2380 мм х 2515 мм / 6,00 м2 |
Высокопроизводительная система, сочетающая очень высокую скорость установки компонентов с точностью и гибкостью. Применение линейных электродвигателей позволяет приводам порталов ускоряться и останавливаться с большой скоростью. Благодаря этому достигается производительность системы 60000 комп/час. Несмотря на высокую производительность, для размещения автомата SIPLACE HS-60 не требуется большой рабочей площади, что позволяет организовывать производство в малогабаритных помещениях. Из всех высокоскоростных автоматов, представленных на современном рынке, SIPLACE HS-60 имеет самый низкий процент брака.
4. Для пайки компонентов оплавлением припойной пасты используем конвекционную печь конвейерного типа Quattro Peak 3.5. Это высокопроизводительные системыа для применения в условиях крупносерийного и массового производства.
Основные особенности печей состоят в передаче тепла в пиковой зоне через щелевые сопла и наличия двух пиковых зон.
Двойная пиковая зона позволяет избежать разницы в температуре нагрева больших и маленьких компонентов.
Благодаря этим особенностям, печи серии Quattro Peak имеют высокие эксплуатационные и технологические характеристики:
- меньший температурный стресс платы и компонентов;
- меньшая разница температуры при нагреве больших и маленьких компонентов;
- низкое потребление электроэнергии;
- низкий износ печей;
- возможность пайки при более низких температурах.
Технические характеристики Quattro Peak 3.5 | |
Скорость конвейера | от 0,2 до 1,8 м/мин |
Габаритные размеры | 3500×1100×1400 мм. |
Дата добавления: 2020-12-22; просмотров: 84; Мы поможем в написании вашей работы! |
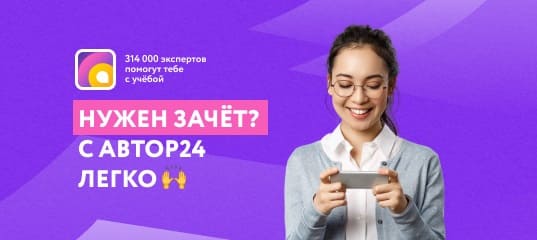
Мы поможем в написании ваших работ!