ТЕХНОЛОГИЯ ИЗГОТОВЛЕНИЯ РЕЛЬСОВ.
Дата 14.10.2020г Группа 3СПХ-3-18
МДК.03.01 Устройство железнодорожного пути
Преподаватель Слободчикова С.В.
Тема: Химический состав рельсовой стали. Маркировка рельсов.
Цель занятия:
1. Образовательная: изучить основные понятия, формирование теоретических знаний, умений систематизировать и применять знания, формирование навыков упрочнения знаний и умений;
2. Воспитательная: воспитание самостоятельности, внимательности, коллективного сотрудничества; формирование ориентации студентов на высокий уровень профессиональной подготовки специалистов среднего звена;
3. Развивающая: развитие познавательного интереса к дисциплине, активности, памяти, способности выражать мысли.
РЕЛЬСОВАЯ СТАЛЬ. ХИМИЧЕСКИЙ СОСТАВ.
Сталь для их изготовления применяют трех видов:
· Мартеновскую;
· Конверторную;
· Электросталь.
До 1983 года была бессемеровская сталь
(Историческая справка) Литая сталь
В истории металлургии железа было три революционных переворота, оказавших глубочайшее влияние на весь ход человеческой истории:
· первый имел место еще в глубокой древности, когда появились сыродутные горны;
· второй произошел в средние века, после открытия переделочного процесса;
· третий пришелся на вторую половину XIX века и был связан с началом производства литой стали.
Сталь во все времена оставалась самым необходимым и желанным продуктом металлургии железа, потому что только она обладала той твердостью и крепостью, какие требовались для изготовления инструментов, оружия и деталей машин. Но прежде чем превратиться в стальное изделие, металл должен был подвергнуться целому ряду трудоемких операций. Сначала из руды выплавляли чугун. Потом чугун восстанавливали в мягкое железо. Наконец путем длительной проковки железной крицы получали из нее необходимую стальную деталь (или только заготовку к ней, которую затем подвергали окончательной отделке на металлорежущих станках). Производство мягкого железа и в особенности ковка долгое время оставались самыми узкими местами в процессе обработки железа. На них уходило больше всего сил и времени, а результаты далеко не всегда оказывались удовлетворительными. Особенно остро эта проблема стала ощущаться в XIX веке, когда резко возрос спрос на дешевую сталь.
|
|
Естественным образом у многих ученых и изобретателей возникла мысль, которую потом высказал Бессемер: каким образом получить металл со свойствами железа и стали, но в жидком виде, чтобы его можно было использовать для отливки? Разрешение поставленной проблемы потребовало нескольких десятилетий упорного труда многих металлургов. На этом пути было сделано несколько важных открытий и изобретений, каждое из которых составило эпоху в истории обработки железа. До конца XVIII века передел чугуна в мягкое железо происходил только в кричных горнах. Этот способ, однако, был неудобен во многих отношениях. Получавшийся в ходе него металл был неоднородным - местами приближался по своим качествам к ковкому железу, местами - к стали. Кроме того, работа требовала больших затрат времени и физических сил. Так как топливо (уголь) находилось в непосредственном соприкосновении с железом, к нему предъявлялись очень высокие требования, ведь любые примеси влияли на качество конечного продукта. Расход угля был очень велик (в среднем, на восстановление 1кг железа уходило до 4кг угля). В самых крупных горнах можно было за 24 часа получить не более 400 кг железа. Между тем рынок требовал все больше железа и стали. Для удовлетворения этих запросов необходимо было найти более совершенный способ переделки чугуна. Значительным шагом вперед на этом пути стал предложенный в 1784 году англичанином Кортом процесс пудлингования в специально созданной для этого печи. Принципиальное устройство пудлинговой печи состояло в следующем. В топке сжигали топливо. Продукты горения через каменный порог попадали в рабочее пространство печи, где на поду находился загруженный чугун с железистыми шлаками. Шлаки под действием пламени переходили в тестообразное состояние и частично расплавлялись. С повышением температуры чугун начинал плавиться и примеси его выгорали за счет кислорода, заключенного в шлаках. Таким образом чугун обезуглероживался, то есть превращался в крицу губчатого железа. Важное отличие пудлинговой печи от кричного горна заключалось в том, что она допускала использовать в качестве горючего любое топливо, в том числе и дешевый неочищенный каменный уголь, а объем ее был значительно больше. Благодаря пудлинговым печам железо стало дешевле. Вместе с тем в отличие от кричных горнов печь Корта не требовала принудительного вдувания. Доступ воздуха и хорошая тяга достигались благодаря высокой трубе.
|
|
|
|
Это была одна из причин, почему пудлинговые печи получили широкое распространение во всем мире. Однако существенным недостатком этих печей было то, что воздух обдувал только верхнюю часть чугуна. Для того чтоб восстановление железа шло равномерно и по всему объему, приходилось периодически открывать печь и перемешивать чугун. Это был тяжелый ручной труд. Кроме того, поскольку силы и возможности рабочего были ограничены, печь не могла быть слишком большой. (Чтобы допустить помешивание, Корт предусмотрел две трубы, из которых одна находилась под топкой, а вторая - в конце печи. Ее открывали в тот момент, когда требовалось снизить температуру).
|
|
Уже к середине XIX века пудлинговые печи перестали удовлетворять новым потребностям промышленности. Чтобы поспевать за спросом, приходилось строить на каждую большую домну несколько печей ( в среднем одну домну обслуживало десять пудлинговых печей). Это удорожало и усложняло производство. Многие изобретатели думали над тем, как заменить пудлингование более совершенным способом восстановления железа.
Раньше других эту задачу удалось разрешить английскому инженеру Бессемеру. К занятиям металлургии Бессемер пришел после многих лет работы над усовершенствованием артиллерийских орудий и снарядов. Он поставил перед собой цель найти способ производства высококачественной литой стали, из которой можно было бы отливать пушки. Наблюдая много раз за плавкой чугуна, он заметил, что твердое восстановленное железо образуется раньше всего у воздуходувных труб. Это навело его на мысль получать сталь путем усиленной продувки через расплавленный чугун воздуха. Первые свои опыты Бессемер провел в закрытом тигле, который он нагревал в горне с коксом. Результат превзошел самые смелые ожидания. Менее чем за час продувки он получил из чугуна первосортную сталь. Кроме того, дальнейшие опыты показали, что нет никакой необходимости вводить в металлургический процесс тепло извне. Дело в том, что чугун содержит собственный горючий материал в качестве примесей: кремний, марганец, углерод - всего около 45 кг горючих материалов на каждую тонну чугуна. Своим горением они позволяли значительно повысить температуру плавки и получать сталь в жидком состоянии.
В 1856 году Бессемер публично демонстрировал изобретенный им неподвижный конвертер. Конвертер имел вид невысокой вертикальной печки, закрытой сверху сводом с отверстием для выхода газов. Сбоку в печи было второе отверстие для заливки чугуна. Готовую сталь выпускали через отверстие в нижней части печи (во время работы конвертера его забивали глиной). Воздуходувные трубки (фурмы) находились возле самого пода печи. Так как конвертер был неподвижным, продувку начинали раньше, чем вливали чугун (в противном случае металл залил бы фурмы. По той же причине надо было вести продувку до тех пор, пока весь металл не был выпущен. Весь процесс длился не более 20 минут. Малейшая задержка в выпуске давала брак. Это неудобство, а также рая других недостатков неподвижного конвертера заставили Бессемера перейти к вращающейся печи.
В 1860 году он взял патент на новую конструкцию конвертера, сохранившуюся в общих чертах до наших дней. Способ Бессемера был настоящей революцией в области металлургии. За 8-10 минут его конвертер превращал 10-15 т чугуна в ковкое железо или сталь, на что прежде потребовалось бы несколько дней работы пудлинговой печи или несколько месяцев работы прежнего кричного горна.
Однако, после того как бессемеров метод стал применяться в промышленных условиях, результаты его оказались хуже, чем в лаборатории, и сталь выходила очень низкого качества. Два года Бессемер пытался разрешить эту проблему и наконец выяснил, что в его опытах чугун содержал мало фосфора, в то время как в Англии широко использовался чугун, выплавленный из железных руд с высоким содержанием фосфора. Между тем фосфор и сера не выгорали вместе с другими примесями; из чугуна они попадали в сталь и существенно снижали ее качество. Это, а кроме того высокая стоимость конвертера, привело к тому, что бессемеровский способ очень медленно внедрялся в производство. И 15 лет спустя в Англии большая часть чугуна переплавлялись в пудлинговых печах.
Гораздо более широкое применение конверторы получили в Германии и США. Наряду с бессемеровским способом производства стали вскоре огромную роль приобрел мартеновский способ. Суть его заключалась в том, что чугун сплавляли с железным ломом в специальной регенеративной печи. Эта печь была придумана и построена в 1861 году немецкими инженерами Фридрихом и Вильямом Сименсами для нужд стекольной промышленности, но наибольшее распространение получила в металлургии. В состав печи входили газопроизводители (или генераторы газа), сама печь с возобновителями теплоты (или регенераторами) для подогрева газа и воздуха и литейного отделения (двора). Генераторы и регенераторы были связаны между собой особой системой каналов для газа, воздуха и продуктов горения. Последние отводились в дымовую трубу высотой до 40 м, дававшей необходимую тягу.
Генераторы располагались под подом или по бокам печи. Регенераторы представляли собой особые камеры для нагрева газа и воздуха.
Специальные переменные клапаны направляли газ и воздух то в одну, то в другую, а продукты горения отводили в трубу. Горение происходило следующим образом. Газ и воздух нагревались каждый в своей камере, а затем поступали в плавильное пространство, где происходило горение.
Продукты горения, пройдя над подом печи, устремлялись в регенераторы и отдавали здесь большую часть своей теплоты кладке регенераторов, а затем уходили в трубу. Чтобы процесс происходил непрерывно, с помощью клапанов направляли воздух и газ то в одну пару регенераторов, то в другую. В результате такого продуманного теплообмена температура в печи достигала 1600 градусов, то есть превышала температуру плавки чистого безуглеродного железа. Создание высокотемпературных печей открыло новые горизонты перед металлургией.
К середине XIX века во всех промышленных странах имелись огромные запасы железного лома. Из-за высокой температуры тугоплавкости его не могли использовать в производстве. Французские инженеры Эмиль и Пьер Мартены (отец и сын) предложили сплавлять этот железный лом с чугуном в регенеративной печи и таким образом получать сталь. В 1864 году на заводе Сирейль они под руководством Сименса осуществили первую успешную плавку. Затем этот способ стал применяться повсюду.
Мартеновские печи были дешевле конвертеров и потому имели более широкое распространение. Однако ни бессемеровский, ни мартеновский способ не позволял получать высококачественную сталь из руды, содержащей серу и фосфор. Эта проблема оставалась неразрешенной в течение полутора десятилетий, пока в 1878 году английский металлург Сидней Томас не придумал добавлять в конвертер до 10-15% извести. При этом образовывались шлаки, способные удерживать фосфор в прочных химических соединениях. В результате фосфор выгорал вместе с другими ненужными примесями, а чугун превращался в высококачественную сталь. Значение изобретения Томаса было огромно. Оно позволило в широком масштабе производить сталь и фосфорсодержащих руд, которые в большом количестве добывались в Европе. С целом введение бессемеровского и мартеновского процессов дало возможность производить сталь в неограниченных количествах. Литая сталь быстро завоевала себе место в промышленности, и начиная с 70-х годов XIX века сварочное железо почти совершенно выходит из употребления. Уже в первые пять лет после введения мартеновского и бессемеровского производств мировой выпуск стали увеличился на 60%
Содержание углерода в современной рельсовой стали находится в пределах 0,71...0,82%, в чугуне содержание углерода доходит до 4%. Кроме того чугун содержит до 1,5...3,5% марганца, до 1,5...2% кремния, а также фосфор, серу и другие примеси, содержание которых в стали должно быть значительно уменьшено. Основная задача при переплавке чугунав сталь заключается в удалении большей части углерода, марганца, кремния, серы и фосфора.
Мартеновская сталь по качеству лучше бессемеровской. Она менее хладноломка, так как имеет меньшую примесь фосфора, дает более плотный слиток, её химический состав более однороден, содержит меньше примесей. С 1983 г. производство рельсов по бессемеровскому способу прекращено.
Технические условия на изготовление рельсов установлены ГОСТ 24182-80.
В состав рельсовой стали, кроме железа, входят
· углерод (0,71...0,82%),
· марганец (0,75...1,05%),
· кремний (0,18...0,4%),
· фосфор (не более 0,045%)
· медь (очень мало)
Углерод придает высокую твердость рельсовой стали. Повышение содержания углерода в мартеновской стали увеличивает её износостойкость. Верхние пределы содержания углерода установлены во избежание увеличения хрупкости стали и возникновения поверхностных дефектов, раковин, плен и т.п. Рельсы из стали с содержанием углерода выше среднего относятся к твёрдым. Рельсы из стали, содержание углерода в которых равно или ниже среднего значения, относятся к нормальным.
Марганец также повышает твёрдость и износостойкость стали, увеличивая одновременно и её вязкость.
Кремний в указанных ограниченных количествах увеличивает твёрдость металла.
Фосфор и сера — примеси вредные: при большом содержании фосфора рельсы становятся хрупкими при низких температурах, при большом содержании серы появляются трещины при прокате рельсов (красноломкость).
Небольшая примесь меди несколько повышает коррозионную стойкость стали.
Рисунок 1 Дуговая печь постоянного тока
вместимостью 6 т для выплавки стали
Таблица – Химический состав рельсовой стали
Марка стали | Массовая доля химических элементов (%) | |||||||
Углерод | Марганец | Кремний
| Ванадий
| Титан
| Фосфор | Сера | Алюми-ний | |
Не более | ||||||||
1 | 2 | 3 | 4 | 5 | 6 | 7 | 8 | 9 |
Э76 | 0,71-0,82 | 0,80-1,30 | 0,25-0,45 | - | - | 0,030 | 0,025 | 0,025 |
К76 | 0,71-0,82 | 0,80-1,30 | 0,25-0,45 | - | - | 0,035 | 0,040 | 0,025 |
М76 | 0,71-0,82 | 0,80-1,30 | 0,25-0,45 | - | - | 0,035 | 0,040 | 0,025 |
Э76Т | 0,71-0,82 | 0,80-1,30 | 0,25-0,45 | - | 0,007-0,0025 | 0,030 | 0,025 | 0,015 |
К76Т | 0,71-0,82 | 0,80-1,30 | 0,25-0,45 | - | 0,007-0,0025 | 0,035 | 0,040 | 0,015 |
М76Т | 0,71-0,82 | 0,80-1,30 | 0,25-0,45 | - | 0,007-0,0025 | 0,035 | 0,040 | 0,015 |
Э76Ф | 0,71-0,82 | 0,80-1,30 | 0,25-0,45 | 0,03-0,07 | - | 0,030 | 0,025 | 0,015 |
К76Ф | 0,71-0,82 | 0,80-1,30 | 0,25-0,45 | 0,03-0,07 | - | 0,035 | 0,040 | 0,015 |
М76Ф | 0,71-0,82 | 0,80-1,30 | 0,25-0,45 | 0,03-0,07 | - | 0,035 | 0,040 | 0,015 |
Э74 | 0,69-0,80 | 0,80-1,30 | 0,18-0,40 | - | - | 0,030 | 0,025 | 0,025 |
К74 | 0,69-0,80 | 0,80-1,30 | 0,18-0,40 | - | - | 0,035 | 0,040 | 0,025 |
М74 | 0,69-0,80 | 0,80-1,30 | 0,18-0,40 | - | - | 0,035 | 0,040 | 0,025 |
Э74Т | 0,69-0,80 | 0,80-1,30 | 0,18-0,40 | - | 0,007-0,0025 | 0,030 | 0,025 | 0,015 |
К74Т | 0,69-0,80 | 0,80-1,30 | 0,18-0,40 | - | 0,007-0,0025 | 0,035 | 0,040 | 0,015 |
М74Т | 0,69-0,80 | 0,80-1,30 | 0,18-0,40 | - | 0,007-0,0025 | 0,035 | 0,040 | 0,015 |
Э74Ф | 0,69-0,80 | 0,80-1,30 | 0,18-0,40 | 0,03-0,07 | - | 0,030 | 0,025 | 0,015 |
К74Ф | 0,69-0,80 | 0,80-1,30 | 0,18-0,40 | 0,03-0,07 | - | 0,035 | 0,040 | 0,015 |
М74Ф | 0,69-0,80 | 0,80-1,30 | 0,18-0,40 | 0,03-0,07 | - | 0,035 | 0,040 | 0,015 |
Примечание. 1. Цифры в обозначении марки указывают условную среднюю массовую долю углерода в сотых долях %. ьуквы М, К и Э, которые стоят перед цифрами, указывают способ выплавки стали: М - мартеновский, К – углеродно-конвекторный и Э - электросталь. Буквы Ф и Т, которые стоят после цифр,обозначают, что сталь содержит добавки ванадия (Ф) и титана (Т) (Пример обозначения стали: М76Ф - мартеновская сталь со средней массовой долей углерода 0,76% и добавками ванадия).
2. Допускается содержание в рельсовой стали хрома, никеля и меди, которое не превышает 0,15% каждого,: по суммарной массовой доле этих элементов не более чем 0,30%. |
Легирование может быть:
· Т- Титаном;
· Ф – Ванадием;
· С- кремнием;
· Х – хромом.
ТЕХНОЛОГИЯ ИЗГОТОВЛЕНИЯ РЕЛЬСОВ.
Дата добавления: 2020-11-15; просмотров: 297; Мы поможем в написании вашей работы! |
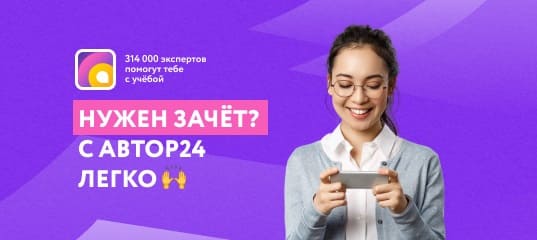
Мы поможем в написании ваших работ!