Расчет деталей с учетом переменной нагрузки
Практически все детали автомобильных и тракторных двигателей даже на установившихся режимах работают в условиях переменных нагрузок. Влияние не только максимальных величин нагрузок, но и харак-тера их изменения по времени на работоспособность деталей авто-мобильных и тракторных двигателей значительно усиливается при по-вышении частоты вращения и степени сжатия. В связи с этим ряд ответственных деталей современных двигателей рассчитывают на стати-ческую прочность от действия максимальной силы и на усталостную прочность от действия постоянно изменяющихся нагрузок.
Усталостная прочность деталей зависит от характера изменения нагрузки, вызывающей симметричное, асимметричное или пульсирую-
щее напряжение в рассчитываемой детали; пределов усталости
σ–1, σ–1Ри τ–1(соответственно при изгибе, растяжении-сжатии и кру-
чении) и текучести σТ и τТ материала детали; от ее формы, размеров, механической и термической обработки, упрочнения поверхности детали.
В зависимости от характера изменения действующей нагрузки в детали возникают напряжения, которые изменяются по симметричному, асимметрич-ному или пульсирующему циклам. Характеристиками каждого цикла являют-ся: максимальное σmax и минимальное σmin напряжения, среднее напряжение σ m, амплитуда цикла σ a и коэффициент r асимметрии цикла. Соотношения между характеристиками для указанных циклов приведены в табл. 10.
|
|
При статических нагрузках за предельное напряжение принимают предел прочности σ В (при расчетах деталей, выполненных из хрупкого материала) или предел текучести σ Т. (для пластичных материалов).
При переменных нагрузках за опасное напряжение принимается предел усталости σ r (для симметричного цикла σ r = σ–1; для пульсирующего σ r = σ0) или предел текучести σ Т. При расчете деталей соответствую-
щий предел зависит от асимметрии цикла напряжений.
При возникновении в детали нормальных или касательных
напряжений, удовлетворяющих условию
или
, (5.1)
расчет производится по пределу усталости; при возникновении в детали напряжений, удовлетворяющих условию
,
или
, (5.2)
расчет производится по пределу текучести. Здесь βσ и βτ – отношение предела усталости при изгибе или кручении к пределу текучести:
,
; (5.3)
ασ и ατ – коэффициенты приведения асимметричного цикла к равно-опасному симметричному при нормальных и касательных напряжениях соответственно.
|
|
Таблица 10. Соотношения между характеристиками циклов
Характе- ристики циклов | Циклы | |||
асимметрич- ный | Асимметричный | пульсирующий однозначный | ||
положительный знакопостоянный | знако-переменный | |||
Максимальное напряжение | ![]() | ![]() | ![]() | ![]() |
Минимальное напряжение | ![]() | ![]() | ![]() | ![]() |
Среднее напряжение | ![]() | ![]() | ![]() | ![]() |
Амплитуда напряжения | ![]() | ![]() | ![]() | ![]() |
Коэффициент асимметрии | ![]() | ![]() | ![]() | ![]() |
Значения ασ и ατ для сталей с различными пределами прочно-
сти приведены в табл. 11. Для чугуна ασ = (0,3…0,7); ατ = (0,5…0,7).
Таблица 11. Значения ασ и ατ для сталей
с различными пределами прочности
Предел прочности σ В, МПа | Изгиб ασ | Растяжение-сжатие ασ | Кручение ατ |
350…450 | 0,06…0,10 | 0,06…0,08 | 0 |
450… 600 | 0,08…0,13 | 0,07…0,10 | 0 |
600…800 | 0,12…0,18 | 0,09…0,14 | 0…0,08 |
800…1 000 | 0,16…0,22 | 0,12…0,17 | 0,06…0,10 |
1 000…1 200 | 0,20…0,24 | 0,16…0,20 | 0,08…0,16 |
1 200…1 400 | 0,22…0,25 | 0,16…0,23 | 0,10…0,18 |
1 400…1 600 | 0,20…0,30 | 0,23…0,25 | 0,18…0,20 |
При отсутствии данных для решения уравнений (5.1) и (5.2) запас прочности детали определяют или по пределу усталости, или по пределу текучести. Из двух полученных значений прочность оценивают по мень-шему коэффициенту.
|
|
Приближенная оценка пределов усталости при переменной нагрузке основана на использовании эмпирических зависимостей:
для сталей σ–1= 0,40·σ В; σ–1Р = 0,28·σ В; τ–1= 0,22·τ В; σ–1Р = (0,7…0,8)·σ–1;
τ–1 = (0,4…0,7)·σ Т;
для чугуна σ–1= (0,3…0,5)·σ В; σ–1Р = (0,6…0,7)·σ В; τ–1= (0,7…0,9)·σ–1;
τ Т = (0,2…0,6)·σ В;
для цветных металлов σ–1= (0,24…0,5)·σ В.
Основные механические характеристики для сталей и чугуна приведены в табл. 12, 13.
Запас прочности без учета формы, размеров и обработки поверхности деталей определяется из приведенных ниже выражений.
При расчете по пределу текучести
, (5.4)
; (5.5)
при расчете по пределу усталости
, (5.6)
. (5.7)
Таблица 12. Механические свойства легированных сталей (МПа)
Марка стали | ![]() | ![]() | ![]() | ![]() | ![]() | ![]() |
20X | 650…850 | 400…600 | 310…380 | 230 | 360 | 230 |
30X | 700…900 | 600…800 | 360 | 260 | 420 | 220 |
30ХМА | 950 | 750 | 470 | – | – | – |
35Х | 950 | 750 | – | – | – | – |
35ХМА | 950 | 800 | – | – | – | – |
38ХА | 950 | 800 | – | – | – | – |
40Х | 750…1 050 | 650…950 | 320…480 | 240…340 | – | 210…260 |
40ХН | 1 000…1 450 | 800…1 300 | 460…600 | 320… 420 | 390 | 240 |
45Х | 850…1 050 | 700…950 | 400…500 | – | – | – |
50ХН | 1 100 | 850 | 550 | – | – | – |
12ХНЗА | 950…1 400 | 700…1 100 | 420…640 | 270…320 | 400 | 220…300 |
18ХН24А | 1 100 | 850 | – | – | – | – |
18ХНВА | 1 150…1 400 | 850…1 200 | 540…620 | 360…400 | 550 | 300…360 |
25ХНМА | 1 150 | – | – | – | – | – |
20ХНЗА | 950…1 450 | 850…1 100 | 430..650 | 310 | – | 240…310 |
25ХНВА | 1 100…1 150 | 950…1 050 | 460…540 | 310…360 | – | 280…310 |
30ХГСА | 1 100 | 850 | 510…540 | 500…530 | – | 220…245 |
37XH3A | 1 150…1 600 | 1 000…1 400 | 520…700 | – | – | 320…400 |
40ХНМА | 1 150…1 700 | 850…1 600 | 550…700 | – | 700 | 300…400 |
10 | 320…420 | 180 | 160 | 120…150 | 140 | 80…120 |
15 | 350…450 | 200 | 170 | 120…160 | 140 | 85…130 |
20 | 400…500 | 240 | 170…220 | 120…160 | 160 | 100…130 |
20Г | 480…580 | 480 | 250 | 180 | 170 | 90 |
25 | 430…550 | 240 | 190 | – | – | – |
30 | 480…600 | 280 | 200…270 | 170…210 | 170 | 110…140 |
35 | 520…650 | 300 | 220…300 | 170…220 | 190 | 130…180 |
35Г2 | 680…830 | 370 | 260 | 190 | 240 | 160 |
40 | 570…700 | 310…400 | 230…320 | 180…240 | – | 140…190 |
40Г | 640…760 | 360 | 250 | 180 | 210 | 150 |
45 | 600…750 | 340 | 250…340 | 190…250 | 220 | 150…200 |
45Г2 | 700…920 | 420 | 310…400 | 210 | 260 | 180…220 |
50 | 630…800 | 350 | 270…350 | 200…260 | – | 160…210 |
50Г | 650…850 | 370 | 290…360 | – | – | – |
60Г | 670…870 | 340 | 250…320 | 210 | 250 | 170 |
65 | 750…1 000 | 380 | 270…360 | 220…260 | 260 | 170…210 |
65Г | 820…920 | 400 | 300 | 220 | 260 | 180 |
Таблица 13. Mexaнические свойства чугунов (МПа)
|
|
Марка чугуна | ![]() | ![]() | ![]() | ![]() | ![]() | ![]() | ![]() |
Серые чугуны | |||||||
СЧ15–32 СЧ21–40 СЧ24–44 СЧ28–48 СЧ32–52 СЧ35–56 СЧ38–60 | 150 210 240 280 320 350 380 | 650 750 850 1 000 1 100 1 200 1 300 | 320 400 440 480 520 560 600 | 240 280 300 350 390 400 460 | 70 100 120 140 140 150 150 | 50 80 100 110 110 115 115 | – – – – – – – |
Высокопрочные чугуны | |||||||
ВЧ45–0 ВЧ45–5 ВЧ40–10 ВЧ50–1.5 ВЧ60–2 | 450 450 400 500 600 | – – – – – | 700 700 700 900 1 100 | – – – – – | – – – – – | – – – – – | 350 330 300 380 420 |
Ковкие чугуны | |||||||
КЧ30–6 КЧЗЗ–8 КЧ35–10 КЧ37–12 КЧ45–6 КЧ50–4 КЧ60–3 | 300 330 350 370 450 50 60 | – – – – – – – | 490 530 570 580 700 800 950 | – – – – – – – | – – – – – – – | – – – – – – – | 190 210 220 230 280 320 380 |
Влияние различных факторов на усталостную прочность детали описывают следующими величинами:
1. коэффициентами концентрации напряжений: теоретическим αкσ
и эффективным k σ (kτ), учитывающими местное повышение напряжений
в связи с изменением формы детали (отверстия, выточки, галтели,
резьбы и т. п.);
2. масштабным коэффициентом εм, учитывающим влияние абсолют-ных размеров тела на предел усталости;
3. коэффициентом поверхностной чувствительности ε П, учитывающим влияние состояния поверхности детали на предел прочности.
Теоретическим коэффициентом концентрации напряжений называ-
ют отношение наибольшего местного напряжения к номинальному
при статической нагрузке без учета эффекта концентрации
, (5.8)
Значения αКσ для ряда наиболее распространенных кон-
центраторов приведены в табл. 14.
Влияние на предел прочности не только геометрии концентратора,
но и материала образца учитывают эффективным коэффициентом концентрации напряжений k σ. При переменных напряжениях
, (5.9)
где σ–1и σк–1– пределы усталости гладкого образца при симметричном цикле и с концентратором соответственно.
Таблица 14. Значения αКσ
для ряда наиболее распространенных концентраторов
Вид концентратора напряжений | αКσ |
Полукруглая выточка при отношении радиуса к диаметру стержня: | |
0,1 | 2,0 |
0,5 | 1,6 |
1,0 | U |
2,0 | 1,1 |
Галтель при отношении радиуса галтели к диаметру стержня: | |
0,0625 | 1,75 |
0,125 | 1,50 |
0,25 | 1,20 |
0,5 | 1,10 |
Переход под прямым углом | 2,0 |
Острая V-образная выточка (резьба) | 3,0…4,5 |
Отверстия при отношении диаметра отверстия к диаметру стержня | |
от 0,1 до 0,33 | 2,0…3,0 |
Риски от резца на поверхности изделия | 1,2…1,4 |
Связь между коэффициентами αКσ и k σ выражается приближенной зависимостью
, (5.10)
где q – коэффициент чувствительности материала к концентрации напря-жений (изменяется в пределах 0 < q < 1).
Величина q зависит в основном от свойств материала:
для серого чугуна 0
высокопрочных и ковких чугунов 0,2…0,4
конструкционных сталей 0,6…0,8
высокопрочных легированных сталей 1,0
Кроме того, коэффициент q можно определить по соответствую-
щим графикам, приведенным на рис. 18.
![]() |
При отсутствии в рас-считываемой детали резких переходов и при качественной обработке поверхностей един-ственным фактором, вызываю-щим концентрации напряже-ний, является качество внутрен-ней структуры материала. В этом случае эффективный коэффициент концентрации
![]() |
Рис. 18. Коэффициент чувствительности сталей к концентрации напряжений | Связь между коэффициента-ми kσ и k τ можно выразить по опытным данным зависимостью |
. (5.12)
При проектировании деталей двигателя следует свести к минимуму влияние местных напряжений, чтобы увеличить усталостную прочность. Это достигается увеличением радиусов закругления во внутренних углах детали, расположением отверстий в зонах пониженных напряжений и т. д.
Масштабным коэффициентом εм называют отношение предела усталости образца с диаметром d к пределу усталости стандартного образца (d ст = 10 мм). Значения коэффициента εм для конструкционных сталей и высокопрочных чугунов приведены в табл. 15.
Таблица 15. Значения масштабных коэффициентов εм
в зависимости от размера детали
Масштаб- ные коэффициенты | Размеры детали (мм) | |||||||
10* | 10…15 | 15…20 | 20…30 | 30…40 | 40…50 | 50…100 | 100…200 | |
ε Mσ | 1 | 1…0,95 | 0,95…0,90 | 0,90…0,85 | 0,85…0,80 | 0,80…0,75 | 0,75…0,65 | 0,65…0,55 |
ε Mτ | 1 | 1…0,94 | 0,94…0,88 | 0,88…0,83 | 0,83…0,78 | 0,78…0,72 | 0,72…0,60 | 0,60…0,50 |
* Для деталей размером меньше 10 мм значения ε Mσ и ε Mτ могут достигать 1,1…1,2 (ε Mσ – это ε M при растяжении-сжатии в изгибе, ε Mτ – это ε M при кручении).
Коэффициентом поверхностной чувствительности εП называют отно-шение предела усталости образца с заданным состоянием поверхности
к пределу усталости такого же образца, но с полированной поверх-
ностью. Значения коэффициента εПσ ≈ εПτ для различных состоя-
ний поверхности приведены в табл. 16.
Таблица 16. Значения коэффициента εПσ ≈ εПτ
для различных состояний поверхности
Вид обработки или поверхностного упрочнения | εПσ ≈ εПτ | Вид обработки или поверхностного упрочнения | εПσ ≈ εПτ |
Полирование без поверхностного упрочнения | 1 | Обдувка дробью | 1,1…2,0 |
Шлифование без поверхностного упрочнения | 0,97…0,85 | Обкатка роликом | 1,1…2,2 |
Чистовое обтачивание без поверхностного упрочнения | 0,94…0,80 | Цементация | 1,2…2,5 |
Грубое обтачивание без поверхностного упрочнения | 0,88…0,60 | Закалка | 1,2…2,8 |
Без обработки и без поверхностного упрочнения | 0,76…0,50 | Азотирование | 1,2…3,0 |
Примечание. При поверхностном упрочнении детали вид предварительной механичес-кой обработки не влияет на величины ε П σ и ε П τ. С увеличением коэффициента концентраций напряжений k В и с уменьшением размеров детали значения ε П σ и ε П τ возрастают.
Для повышения усталостной прочности рекомендуется высокая чистота поверхности, особенно вблизи концентраторов. Ответственные детали, работающие в тяжелых условиях циклических напряжений, обычно шлифуют и полируют, а в ряде случаев производят механическое или термическое упрочнение.
С учетом влияния концентрации напряжений, размера и качества обработки поверхности детали максимальное напряжение цикла (МПа)
, (5.13)
или
, (5.14)
а запасы прочности при расчете по пределу усталости
, (5.15)
; (5.16)
при расчете по пределу текучести
, (5.17)
, (5.18)
где и
.
При сложном напряженном состоянии общий запас прочности детали при совместном действии на нее касательных и нормальных напряжений
, (5.19)
где nσ и nτ – частные коэффициенты запаса прочности.
Для определения минимального общего запаса прочности следует подставить в формулу (5.19) минимальные значения nσ и nτ. Влияние температуры на усталостную прочность сказывается в том, что с ее повышением первой предел усталости у гладких образцов, а также
у образцов с концентраторами обычно снижается.
Величина допускаемого запаса прочности зависит от качества материала, вида деформаций, условий работы, конструкции, характера действующих нагрузок и других факторов. От правильного установления допускаемого напряжения зависит прочность и безопасность проектируемой конструкции, количество затрачиваемого материала.
Расчет поршневой группы
Поршень
Наиболее напряженным элементом поршневой группы является поршень (рис. 19), воспринимающий высокие газовые, инерционные
и тепловые нагрузки. Его основными функциями являются уплотнение внутрицилиндрового пространства и передача с наименьшими потерями газовых сил давления кривошипно-шатунному механизму. Поршень представляет собой достаточно сложную деталь как в отношении
самой конструкции, так и в отношении технологии и подбора материала при его изготовлении. Основные конструктивные соотношения размеров элементов поршня приведены в табл. 17.
Совершенствование поршней современных двигателей осуществля-
ется путем уменьшения их массогабаритных параметров, повышения прочности и износостойкости, а также снижения коэффициента линей-
ного расширения, что важно для получения минимального теплового зазора между поршнем и цилиндром без заклинивания.
Таблица 17. Размеры элементов поршня
Название элемента | Бензиновые двигатели | Дизельные двигатели | ||
Толщина днища поршня | (0,05…0,09)·D | (0,12…0,2)·D | ||
Высота поршня | (0,8…1,2)·D | (1,0…1,5)·D | ||
Высота огневого (жарового) пояса | (0,06…0,09)·D | (0,11…0,2)·D | ||
Толщина первой кольцевой перемычки | (0,03…0,05)·D | (0,04…0,06)·D | ||
Высота верхней части поршня | (0,45…0,75)·D | (0,6…1,0)·D | ||
Высота юбки поршня | (0,6…0,75)·D | (0,6…0,7)·D | ||
Внутренний диаметр поршня | D – 2·(S + t) + Δt | |||
Толщина стенки головки поршня | (0,05…0,1)·D | (0,05…0,1)·D | ||
Толщина стенки юбки поршня | 1,5…4,5 | 2,0…5,0 | ||
Радиальная толщина кольца | компрессионного | (0,035…0,045)·D | (0,04…0,045)·D | |
маслосъемного | (0,03…0,043)·D | (0,038…0,043)·D | ||
Радиальный зазор кольца в канавке поршня | компрессионного | 0,7…0,95 | 0,7…0,95 | |
маслосъемного | 0,9…1,1 | 0,9…1,1 | ||
Высота кольца | 1,5…4,0 | 3,0…5,0 | ||
Разность между величинами зазоров замка кольца в свободном и рабочем состоянии | (2,5…4)·t | (3,2…4)·t | ||
Число масляных отверстий | 6…12 | 6…12 | ||
Диаметр масляного канала | (0,3…0,5)·a | (0,3…0,5)·a | ||
Диаметр бобышки | (0,3…0,5)·D | (0,3…0,5)·D | ||
Расстояние между торцами бобышек | (0,3…0,5)·D | (0,3…0,5)·D | ||
Наружный диаметр | (0,22…0,28)·D | (0,30…0,38)·D | ||
Внутренний диаметр | (0,65…0,75)·D | (0,50…0,70)·D | ||
Длина пальца | закрепленного | (0,85…0,9)·D | (0,85…0,9)·D | |
плавающего | (0,78…0,88)·D | (0,80…0,85)·D | ||
Длина головки шатуна | закрепленного пальца | (0,28…0,32)·D | (0,28…0,32)·D | |
плавающего пальца | (0,33…0,45)·D | (0,33…0,45)·D | ||
Поршни автотракторных двигателей изготавливаются в основном
из алюминиевых сплавов, реже из чугуна. В качестве алюминиевых сплавов использовались эвтектические сплавы алюминия с кремнием, содержание которого в сплаве не превышало 12…13 %. Однако постоянно растущий уровень форсирования двигателей, особенно двигателей
с турбонаддувом и дизелей, требовал перехода на более термопрочные материалы для изготовления поршней. Новые двигатели имеют поршни, изготовленные из заэвтектических сплавов алюминия с кремнием, содержание которого достигает 18 % и более. Для улучшения физико-механических свойств заэвтектических сплавов применяется их легиро-вание никелем, магнием, медью, хромом и специальные технологии
литья или горячей штамповки.
Рис. 19. Схема поршня
Чугунные поршни по сравнению с алюминиевыми обладают
более высокими показателями твердости, износостойкости и жаропроч-ности, а также одинаковым коэффициентом линейного расширения
с материалом гильзы цилиндра. Однако большая плотность чугунного поршня не позволяет его использовать для высокооборотных двигателей.
В настоящее время все серийно выпускаемые двигатели легковых автомобилей имеют поршни из алюминиевых сплавов.
Дальнейшее совершенствование поршней предусматривает широкое использование для их изготовления композиционных материалов. Основу этих материалов составляют легкие и не очень прочные материалы (например, алюминий), которые «насыщаются» высокопрочными поли-мерными, керамическими или металлическими волокнами. Эти волокна
не только жестко связывают молекулы основного материала, но
и воспринимают значительную нагрузку, как механическую, так и тепло-вую. Армирование элементов поршня керамическими волокнами из оксида алюминия Аl2О3 и диоксида кремния SiО2 способствует высокой термической стабильности поршня.
Величину верхней части поршня h1 выбирают исходя из обеспечения одинакового давления опорной поверхности поршня по высоте цилиндра и прочности бобышек, ослабленных отверстиями для пропуска масла. Высота головки поршня h Г, включающая огневой пояс е, устанавливается исходя из обеспечения нормального температурного режима ее элементов. Работоспособное состояние поршневой группы обеспечивается толщиной днища поршня и размещением компрессионных и маслосъемного колец. Высота юбки h Ю определяется величиной необходимого теплового зазора между юбкой поршня и цилиндром: чем меньше этот зазор, тем короче можно сделать юбку поршня, снизив ее массу.
При работе двигателя температура потока горящей топливо-воздушной смеси, омывающей днище поршня, меняется от минимальной при пуске и прогреве двигателя до максимальной на режимах наи-
больших нагрузок. При этом максимальную температуру имеет днище поршня, а минимальную – юбка. Распределение средней температуры
при работающем двигателе по высоте поршня показано на рис. 20а.
С учетом такого распределения температуры профиль поршня по высоте выполняется ступенчатой (рис. 20б), конической или лекальной формы.
Значительная часть теплового потока от днища и огневого пояса поршня быстро уходит в стенку цилиндра через поршневые кольца, и только часть теплоты передается в бобышки, а затем и в юбку поршня. При этом отвод теплоты от бобышек существенно меньше, чем от стенок юбки, которые контактируют со стенками цилиндра. В результате по оси бобышек поршень расширяется значительно больше и становится овальным (рис. 20в). Оптимальная форма поршня для вновь проектируемого двигателя подбирается в результате кропотливых и длительных экспериментов.
Наиболее общими конструктивными и технологическими направлениями при разработке поршней современных двигателей являются:
сокращение расстояния от днища поршня до оси бобышек
в целях снижения высоты и массы двигателя;
уменьшение высоты юбки поршня и снижение его веса за счет вырезов в наименее нагруженных местах (Х-образные поршни);
нанесение на днище и верхнюю канавку поршня износо-
и термостойкого покрытия, преобразующего поверхностный слой алюминия в керамику Аl2О3;
снижение теплового расширения поршня за счет заливки в его тело стальных терморегулирующих вставок;
покрытие юбки поршня тонким (0,003…0,005 мм) слоем олова, свинца или оловянно-свинцового сплава в целях быстрой приработки,
а также уменьшения трения и снижения износа;
уменьшение внешнего и внутреннего диаметров пальцев;
переход на плавающие пальцы малой длины с фиксацией шатуна
от осевых перемещений в бобышках поршня;
снижение высоты колец;
применение специальных конструктивных и технологических элемен-тов, улучшающих смазку и уменьшающих износ пары: поршень – цилиндр.
Рис. 20. Изменение температуры по высоте поршня и зазоров между поршнем
и зеркалом цилиндра в разных сечениях: а – изменение температуры по высоте поршня; б – изменение зазоров между поршнем и зеркалом цилиндра; в – изменение площади поперечного сечения поршня; — – окружность цилиндра; — — — – профиль холодного поршня; — · · — · · — – рабочий режим; - - - - - - - - - - - – перегрев; А – места заклинивания юбки поршня в цилиндре при перегреве
Поверочный расчет элементов поршня осуществляется без учета переменных нагрузок, величина которых учитывается при установ-
лении соответствующих допускаемых напряжений. Рассчитывают
днище, стенку головки, верхнюю кольцевую перемычку, опорную поверхность и юбку поршня.
Днище поршня рассчитывается на изгиб от действия максимальных газовых усилий р z . max как равномерно нагруженная круглая плита, свободно опирающаяся на цилиндр. Для бензиновых двигателей наибольшее давление газов достигается при работе на режиме максимального крутящего момента. Для дизелей максимальное давление газов обычно достигается при работе на режиме максимальной мощности.
Напряжение изгиба (МПа) в днище поршня
, (5.20)
где Миз – изгибающий момент (МН·м), ; W из – момент сопротивления изгибу плоского днища (м3),
; р z . max – максимальное давление сгорания (МПа), р z . max = pz;
– внутренний радиус днища (м),
.
При отсутствии у днища ребер жесткости допустимые значения напряжений [σиз] (МПа) лежат в пределах:
20…25 – для поршней из алюминиевых сплавов,
40…50 – для чугунных поршней;
при наличии ребер жесткости допустимые значения напряжений возрастают:
до 50…150 – для алюминиевых,
80…200 – для чугунных поршней.
Кроме напряжений от давления газов, в днище поршня возникают тепловые напряжения из-за разности температур внутренней и наружной поверхностей. Тепловые напряжения (МПа) охлаждаемых чугунных поршней
, (5.21)
где α = 11·10-6 – коэффициент линейного расширения чугуна (1/град);
Е = (1,0…1,2)·105 – модуль упругости чугуна (МПа); q – удельная тепловая нагрузка (Вт/м2); δ – толщина днища (см); λтеп = 58 – коэф-фициент теплопроводности чугуна (Вт/(м·К)).
Для четырехтактных двигателей приближенно
, (5.22)
где n – частота вращения, мин–1 (для бензиновых двигателей n = n M,
а для дизелей n = n N); р i – среднее индикаторное давление (МПа),
для бензиновых двигателей – при n M, а для дизелей – при n N.
Суммарное напряжение (МПа) в охлаждаемом чугунном днище
. (5.23)
Из уравнения (5.23) следует, что с уменьшением толщины днища поршня тепловые напряжения уменьшаются, а напряжения от газовых
сил увеличиваются. Допустимые суммарные напряжения в чугунных днищах автомобильных и тракторных двигателей находятся в пределах
[σ Σ] = 150…250 МПа.
Тепловые напряжения охлаждаемых алюминиевых поршней обычно определяются термометрированием при экспериментальных исследова-ниях. Головка поршня в сечении х – х (см. рис. 20), ослабленная отверстиями для отвода масла, проверяется на сжатие и разрыв.
Напряжение сжатия (МПа)
, (5.24)
где Pz . max = pz·F П – максимальная сила давления газов на днище поршня (МН); F x - x – площадь сечения х – х (м2):
, (5.25)
где d K = D – 2(t + Δt) – диаметр поршня по дну канавок (м2);
F' = [(d K – di)/2]·d M – площадь продольного диаметрального сечения масляного канала (м2).
Допустимое напряжение на сжатие [σсж] для поршней из алюминиевых сплавов составляет 30…40 МПа, 60…80 МПа – из чугунных.
Напряжение разрыва (МПа) в сечении х – х
. (5.26)
Сила инерции возвратно-поступательно движущихся масс (МН) для режима максимальной частоты вращения при холостом ходе двигателя
, (5.27)
где mx - x – масса головки поршня с кольцами, расположенная выше се-
чения х – х (см. рис. 20), определяемая по геометрическим размерам
или по формуле mx - x (0,4…0,6)·m П (кг); m П – масса поршневой группы (кг);
R – радиус кривошипа (м); ωx . x . max = π · nx . x. max/30 – максимальная угловая скорость холостого хода двигателя (рад/с); λ = R / L – отношение радиуса кривошипа к длине шатуна.
Допустимые напряжения на разрыв для поршней из алюминиевых сплавов [σ P] = 4…10 МПа, а для чугунных [σ P] = 8…20 МПа.
Толщина верхней кольцевой перемычки h П (см. рис. 16) форсированных двигателей с высокой степенью сжатия рассчитывается
на срез и изгиб от действия максимальных газовых усилий р z . max. Пере-мычка рассчитывается как кольцевая пластина, защемленная до окруж-ности основания канавки диаметром d K = D – 2·(t + Δt) и равномерно нагруженная по площади F К.П = π·(D2 – d K2) силой Р K = 0,9·p z. max·F К. П.
Напряжение среза кольцевой перемычки (МПа)
, (5.28)
где D и h П – диаметр цилиндра и толщина верхней кольцевой перемычки (мм).
Напряжение изгиба кольцевой перемычки
. (5.29)
Сложное напряжение по третьей теории прочности
. (5.30)
Допустимые напряжения σƩ (МПа) в верхних кольцевых перемычках
с учетом значительных температурных нагрузок находятся в пределах:
30…40 – для поршней из алюминиевых сплавов,
60…80 – для чугунных поршней.
Максимальные удельные давления (МПа) юбки поршня h Ю и всей высоты Н поршня на стенку цилиндра определяются из уравнений:
, (5.31)
, (5.32)
соответственно, где Nmax – наибольшая нормальная сила, действующая
на стенку цилиндра при работе двигателя на режиме максимальной мощ-ности и определяемая по данным динамического расчета.
Для современных автомобильных и тракторных двигателей
q1 = 0,3…1,0,
q2 = 0,2…0,7.
В целях предотвращения заклинивания поршней при работе двигателя размеры диаметров головки D Г и юбки D Ю поршня определяют исходя
из наличия необходимых монтажных зазоров и
между стенками цилиндра и поршня в холодном состоянии. По статистическим данным
для алюминиевых поршней с неразрезными юбками = (0,004…0,006)·D,
= (0,001…0,002)·D, а для чугунных поршней
= (0,006…0,008)·D,
= (0,001…0,002)·D. Установив
и
, определяют D Г = D –
и D Ю = D – .
Правильность установленных размеров D Г и D Ю проверяют по формулам:
, (5.33)
, (5.34)
где и
– диаметральные зазоры в горячем состоянии между стенкой цилиндра и головкой поршня и между стенкой цилиндра и юбкой поршня соответственно (мм); α Ц и α П – коэффициенты линейного расширения материалов цилиндра и поршня (для чугуна α Ц = α П = 11·106 1/К; для алюминиевых сплавов α Ц = α П = 22·106 1/К); Т Ц, Т Г, Т Ю – температура
в рабочем состоянии стенок цилиндра, головки и юбки поршня соответственно (при жидкостном охлаждении Т Ц = 383…388, Т Г = 473…723 и Т Ю = 403…473 К, а при воздушном Т Ц = 443…463, Т Г = 573…873
и Т Ю = 483…613 К; Т0 =293 К – начальная температура цилиндра и поршня.
При получении отрицательных значений или
(натяг) поршень не пригоден к работе. В этом случае необходимо увеличить
или
и соответственно уменьшить D Г или D Ю либо предусмотреть разрез юбки поршня. При нормальной работе поршня = (0,002…0,002 5)·D
и = (0,000 5…0,001 5)·D.
Поршневые кольца
Поршневые кольца работают в условиях высоких температур и значи-тельных переменных нагрузок. Их основные функции:
герметизация надпоршневого пространства в целях максимально возможного использования тепловой энергии топлива;
отвод избыточной доли теплоты от поршня в стенки цилиндра;
«управление маслом», т. е. рациональное распределение масляного слоя по зеркалу цилиндра и ограничения попадания масла в камеру сгорания.
Выполнение этих функций на современных двигателях обеспечивает комплект колец, как правило, состоящий из трех колец: двух ком-прессорных и одного маслосъемного.
Наиболее нагруженным, особенно в тепловом отношении, является первое (верхнее) компрессионное кольцо, температура которого достига-
ет 200…250 °С. Обычно оно изготовляется из легированного высокопрочного чугуна с шаровидным графитом, имеющим предел проч-ности 1 100…1 400 МПа. Легирующие добавки хрома, никеля, молибдена и других металлов способствуют повышению термостойкости компрес-сионных колец до 340 °С. Для наиболее высокофорсированных дизелей
и бензиновых двигателей применяются верхние компрессионные кольца, изготовленные из высокоуглеродистых сталей с пределом прочности 1 400…1 500 МПа и выше. В целях повышения износостойкости
на компрессионные кольца в обязательном порядке наносятся специальные износостойкие покрытия. Чаще всего в качестве такого покрытия используется электролитическое хромирование слоем (0,10…0,15 мм) твердого хрома или еще более тугоплавкого и износостойкого молиб-
дена. Распространенное в прошлом пористое хромирование, наносимое
на прямую наружную поверхность кольца (рис. 21а), используется
редко. Более широкое применение находит твердое хромирование
с приданием наружной поверхности специального симметричного
или несимметричного бочкообразного профиля (рис. 21б, в).
Рис. 21. Профили верхних компрессионных колец двигателей легковых автомобилей:
а – прямое с фисками и пористым хромированием; б – то же, но с молибденом
в канавке на наружной поверхности; в – с симметричной бочкообразной наружной поверхностью; г – с несимметричной бочкообразной наружной поверхностью;
д – с закручиванием с помощью угловой фаски; е – с закручиванием с помощью проточки на внутренней поверхности
Второе компрессионное кольцо практически является компрессионно-маслосъемным. Оно работает в более «мягких» условиях по давлению, температуре и смазке. Для его использования применяется серый легированный чугун с пластинчатым графитом как с износостойким покрытием, так и без специального покрытия. Кроме уплотнения надпоршневого пространства, второе кольцо обеспечивает «управление маслом», снимая его со стенок цилиндра при ходе поршня вниз и осуществляя пропуск некоторого количества масла при ходе поршня вверх. Эта функция определяет и специальные «скребковые» профили компрессионно-маслосъемных колец (рис. 22).
Рис. 22. Профили компрессионно-маслосъемных колец: а – простое скребковое;
б – скребковое минутное; в – минутное; г – прямого закручивания; д – обратного закручивания
Третье кольцо (маслосъемное) обеспечивает снятие масла с зеркала цилиндра и сброс его в картер через отверстия в канавке кольца. Наиболее важными качествами маслосъемных колец являются хорошая приспособляемость к форме цилиндра и высокое давление на стенки цилиндра, необходимые для эффективного съема масла. Требования
к конструкции и материалу маслосъемных колец определяются их функциями и специфическими условиями работы.
На современных двигателях применяются два основных типа колец:
а) коробчатые с расширителем в виде эспандерной или спиральной пружины; б) наборные, состоящие из двух дисков и двухфункциональных расширителей (рис. 23). Коробчатые кольца изготовляются из серого легированного чугуна, способного длительное время работать в паре
с чугунной гильзой цилиндра без специальных покрытий, хотя некоторые двигатели имеют маслосъемные кольца с хромированной наружной поверхностью. Хромированные коробчатые маслосъемные кольца изготовляются также методом проката из стальной калиброванной ленты.
![]() | Рис. 23. Схема наборного маслосъемного кольца с двухфункциональным расширителем: 1, 3 – диски; 2 – двухфункциональный расширитель |
Для изготовления элементов наборных колец также используется стальная калиброванная лента. Тонкие диски кольца (0,50…0,63 мм), наружная поверхность которых хромируется, изготовляются из угле-родистой стальной ленты. Двухфункциональные расширители, обеспечивающие удержание дисков в канавке поршня на определенном расстоянии друг от друга и равномерное их прижатие к зеркалу цилиндра, производятся из нержавеющей хромоникелевой стальной ленты. В про-цессе изготовления лента нагартовывается и приобретает пружинные свойства, которые она сохраняет в процессе эксплуатации.
Основными конструктивными параметрами поршневых колец являются отношение диаметра цилиндра к радиальной толщине кольца D/t; отношение разности между величинами зазоров замка кольца в свободном и рабочем состояниях к толщине кольца A0/t, высота кольца а. Значения конструктивных параметров поршневых колец бензиновых двигателей
и дизелей представлены в табл. 17.
Пользуясь данными табл. 17, следует учитывать, что уменьшение габаритов и массы двигателя осуществляется прежде всего за счет
высоты и массы поршня. Так, высота верхнего компрессионного
кольца бензиновых двигателей составляет всего 1,2…1,5 мм, а дизелей – 2,5…3,0 мм. Наиболее распространены верхние кольца дизелей высотой 2,0 мм, а при малых диаметрах цилиндра высота первого кольца дизеля
может быть 1,75 и даже 1,5 мм.
Средние кольца современных бензиновых двигателей имеют высоту 1,50…1,75 мм, а дизелей – 2,0…2,5 мм. Средние кольца, как правило, имеют увеличенную радиальную ширину.
Тенденция к уменьшению высоты поршневых колец характерна
и для маслосъемных колец, высота которых за последние 8…10 лет снизилась с 2,8…4,75 до 2,0…2,5 мм у целого ряда двигателей.
Расчет колец включает в себя:
определение среднего давления кольца на стенку цилиндра
для обеспечения достаточной герметичности камеры сгорания; при этом
не должны резко возрастать потери мощности двигателя на трение колец
о стенки цилиндра;
построение эпюры давления кольца по окружности;
определение напряжений изгиба, возникающих в сечении, противо-положном замку, при надевании кольца на поршень и в рабочем состоянии;
установление монтажных зазоров в прямом замке кольца.
Среднее давление (МПа) кольца на стенку цилиндра
, (5.35)
где Е – модуль упругости материала кольца (для серого чугуна
Е = 1·105 МПа, для легированного чугуна Е = 1,2·105 МПа, для стали
Е = (2…2,3)·105 МПа); А0 – разность между величинами зазоров кольца
в свободном и рабочем состояниях (см. табл. 17).
Допустимое среднее радиальное давление р СР (МПа):
для компрессионных колец 0,11…0,37;
для маслосъемных колец 0,2…0,4.
При снижении частоты вращения двигателя и увеличении диаметра цилиндра величина р СР должна приближаться к нижнему пределу.
Для обеспечения хорошей приработки кольца и надежного уплотнения давление кольца на стенку цилиндра у замка должно быть повышенным. Установлено, что это повышение должно составлять для колец бензиновых двигателей примерно (1,4…2,0)·р СР, а для дизелей – (1,8…2,5)·р СР.
При этом эпюра давления кольца на стенки цилиндра может иметь грушевидную или каплевидную форму (рис. 24, 25). Новое кольцо, изготовленное с заранее заданной эпюрой давления и установленное
в цилиндр, не должно иметь просветов между своей наружной поверхностью и зеркалом цилиндра. Значительное повышение давления
у замка способствует равномерному износу кольца по окружности.
Давление (МПа) кольца на стенку цилиндра в различных точках окружности определяется по формуле
р = рСР · μК, (5.36)
где μК – переменный коэффициент, определяемый изготовителем в соответствии с принятой формой эпюры давления кольца на зеркало цилиндра (табл. 18).
Таблица 18. Значения коэффициента μК для различных углов ψ
Параметр | Значение | ||||||
Угол ψ, определяющий положение текущего давления кольца, град | 0 | 30 | 60 | 90 | 120 | 150 | 180 |
Коэффициент μК для бензи-нового двигателя | 1,05 | 1,04 | 1,02 | 1,0 | 1,02 | 1,27 | 1,50 |
Коэффициент μК для дизель-ного двигателя | 1,05 | 1,05 | 1,14 | 0,90 | 0,45 | 0,67 | 2,85 |
![]() | ![]() |
Рис. 24. Грушевидная эпюра давления компрессионного кольца бензинового двигателя на зеркало цилиндра | Рис. 25. Каплевидная эпюра давления компрессионного кольца дизеля на стенку цилиндра |
Монтажный зазор (мм) в прямом замке поршневого кольца в холод-ном состоянии
, (5.37)
где Δ´К – минимально допустимый зазор в замке кольца во время работы двигателя (Δ´К = 0,06…0,10 мм); α К и α Ц – коэффициенты линейного рас-ширения материала кольца и гильзы цилиндра; ТК, ТЦ и Т0 – температуры кольца, стенок цилиндра в рабочем состоянии и начальная температура соответственно, Т0 = 293 К; при жидкостном охлаждении Т Ц = 383…388, Т К = 473…573 К; при воздушном Т Ц = 443…463, Т К = 523…723 К.
Поршневой палец
Во время работы двигателя поршневой палец подвергается воздействию переменных нагрузок, приводящих к возникновению напряжений изгиба, сдвига, смятия и овализации. В соответствии с указан-ными условиями работы к материалам, применяемым для изготовления пальцев, предъявляются требования высокой прочности и вязкости.
Этим требованиям удовлетворяют цементированные малоуглеродистые
и легированные никелем и хромом стали с твердой поверхностью и вязкой основой.
Основные конструктивные размеры поршневых пальцев (см. рис. 19) обычно принимаются по статистическим данным (см. табл. 17)
или по данным прототипов с последующей проверкой расчетом. Большинство бензиновых двигателей имеет поршневые пальцы диаметром 20…23 мм с цилиндрическим внутренним отверстием.
Пальцы диаметром 17…19 мм имеют двигатели малого рабочего
объема. В современных высокофорсированных двигателях наблюда-
ется тенденция к увеличению толщины стенок пальцев и уменьше-
нию их длины, особенно при использовании способа фиксации
шатуна от осевого перемещения в бобышках поршня. Поршневые
пальцы дизелей имеют диаметр в основном в пределах 24…30 мм,
но в 1,5…2 раза более толстые стенки в целях обеспечения их жестко-
сти и прочности. Основные типы поршневых пальцев представлены
на рис. 26.
Расчет поршневого пальца включает определение удельных давлений пальца на втулку верхней головки шатуна и на бобышки, а также напряжений от изгиба, среза и овализации.
Максимальные напряжения в пальцах бензиновых двигателей возникают при работе на режиме максимального крутящего момента,
а в пальцах дизелей – при работе на номинальном режиме.
Расчетная сила (МН), действующая на поршневой палец:
. (5.38)
Для бензиновых двигателей: р z . max – максимальное давление газов
на режиме максимального крутящего момента (МПа); k – коэффициент,
учитывающий массу поршневого пальца, k = 0,76…0,86; P j – сила инерции поршневой группы, при n = nM (МН);
для дизелей: р z . max – максимальное давление газов на номиналь-
ном режиме (МПа); k = 0,68…0,81 – коэффициент, учитывающий
массу поршневого пальца; – сила инерции поршневой группы (MH) при n = nM, n = nN.
![]() | Рис. 26. Основные типы поршневых пальцев: а – палец с цилиндрическим отверстием и относительно тонкими стенками для среднефорсированных двигателей; б – палец с увеличенной жесткостью в среднем сечении; в – короткий палец с толстыми стенками для высокофорсированных двигателей; г – палец для дизеля с толстыми стенками; д – палец «равного сопротивления изгибу» с коническими отверстиями |
Удельное давление (МПа) пальца на втулку поршневой головки шатуна
, (5.39)
где d п – наружный диаметр пальца (м); l ш – длина опорной поверхности пальца в головке шатуна (м).
Удельное давление плавающего пальца на бобышки
, (5.40)
где l п – общая длина пальца (м); b – расстояние между торцами бобышек (м); (l п – b) – длина опорной поверхности пальца в бобышках (м).
Для современных автомобильных и тракторных двигателей
q Ш = 20…60 МПа и q Б = 15…50 МПа. Нижние пределы относятся к тракторным двигателям.
Напряжение изгиба пальца (МПа) при условии распределения нагрузки по длине пальца согласно эпюре, приведенной на рис. 27:
, (5.41)
где α = d В/d П – отношение внутреннего диаметра пальца к наруж-
ному.
Для автомобильных и тракторных двигателей [σ ИЗ] = 100…250 МПа.
Касательные напряжения (МПа) от среза пальца в сечениях, расположенных между бобышками и головкой шатуна:
. (5.42)
Для автомобильных и тракторных двигателей [τ] = 60…250 МПа. Нижние пределы относятся к тракторным двигателям, а верхние –
к пальцам, изготовленным из легированной стали.
Вследствие неравномерного распределения сил, приложенных
к пальцу (принимается синусоидальное распределение нагрузки по по-верхности пальца – рис. 27а), при работе двигателя происходит деформация сечения пальца (овализация). Возникающие при этом напряжения имеют различные значения по длине пальца и его сече-
нию.
Рис. 27. Расчетная схема поршневого пальца: а – распределение нагрузки;
б – эпюры напряжений
Максимальная овализация пальца, т. е. наибольшее увеличение горизонтального диаметра Δd П. max (мм), наблюдается в его средней, самой напряженной части:
, (5.43)
где Е – модуль упругости материала пальца (для стали Е П = (2,0…2,3)·105 МПа.
Значение Δdп. max не должно быть больше 0,02…0,05 мм.
Напряжения, возникающие при овализации пальца на внешней
и внутренней поверхностях (см. рис. 27б), определяют для горизонтальной (точки 1 и 2 при φ = 0°) и вертикальной (точки 3 и 4 при φ = 90°) плоскостей по следующим формулам:
на внешней поверхности пальца в горизонтальной плоскости (точки 1, ψ = 0)
; (5.44)
на внешней поверхности пальца в вертикальной плоскости
(точки 3, ψ = 90˚)
; (5.45)
на внутренней поверхности пальца в горизонтальной плоскости (точки 2, ψ = 0°)
; (5.46)
на внутренней поверхности пальца в вертикальной плоскости
(точки 4, ψ = 90°)
. (5.47)
Наибольшее напряжение овализации возникает на внутренней поверхности пальца в горизонтальной плоскости. Это напряжение, подсчитанное по формуле (5.46), не должно превышать 300…350 МПа.
Расчет шатунной группы
Поршневая головка
Конструкции шатунов, применяемых в автомобильных и тракторных двигателях, разнообразны и зависят в основном от типа двигателя
и расположения цилиндров. Расчетными элементами шатунной группы являются поршневая и кривошипная головки, стержень шатуна
и шатунные болты. Расчетная схема шатуна приведена на рис. 28.
При работе двигателя шатун подвергается воздействию знако-переменных газовых и инерционных сил, которые в отдельных
случаях создают ударные нагрузки. Поэтому шатуны изготовляют
из марганцовистых, хромистых, хромоникелевых сталей с содержа-
нием углерода 0,30…0,45 %. Механические характеристики сталей приведены в табл. 12. Для повышения усталостной прочности при достаточной вязкости и пластичности стальные шатуны подвергают
в процессе штамповки промежуточной термообработке, а после штамповки – полированию, обдувке дробью, нормализации, закалке
и отпуску.
Хорошие перспективы имеются для изготовления шатунов из ком-позиционных материалов (рис. 29). Основой таких шатунов служат металлические вкладыши с антифрикционным покрытием или керамика, обмотанные предварительно натянутым, очень прочным волокном и залитые полимерным материалом – матрицей. Соединение разъемной нижней головки шатуна осуществляется с помощью хомутов и стяжных болтов, не нарушающих структуру материала шатуна и нижней крышки.
Рис. 28. Расчетная схема шатунной группы:
L Ш – длина шатуна; L1 – длина стержня; d – внутренний диаметр
верхней головки; d Г – внешний диаметр верхней головки; l Ш – длина головки;
lK – длина кривошипной головки; h Г – высота головки;
Сб – расстояние между болтами; d ш. ш – диаметр шатунной шейки; t в – толщина вкладыша; a ш – толщина стержня; b ш – ширина шатуна; h ш – высота стержня;
t ш – толщина стенки стержня; S в – радиальная толщина стенки втулки
Расчет поршневой головки шатуна производится из условий:
усталостной прочности в сечении I – I при действии инерционных сил (без учета запрессованной втулки), достигающих максимальных значений при работе дизеля на режиме максимальной частоты вращения холостого хода, а при работе бензинового двигателя на режиме разностной частоты вращения вала (≈ 1,38 nN);
напряжений, возникающих в головке от воздействия на нее за-прессованной втулки;
усталостной прочности в сечении А – А (место перехода головки шатуна в стержень – заделка головки) при действии суммарных (газовых
и инерционных) сил и запрессованной втулки.
Расчет в этом случае производится для того режима работы двигателя, при котором амплитуда изменения суммарных сил максимальна.
Значения основных конструктивных параметров поршневой
головки шатуна приведены в табл. 19.
Рис. 29. Схемы шатунов из композиционных материалов: 1 – металлические вкладыши; 2 – силовое волокно; 3 – полимерный материал (матрица); 4 – хомуты под шатунные болты; 5 – шатунные болты
Таблица 19. Значения основных конструктивных параметров
поршневой головки шатуна
Элемент | Дизельные двигатели | Бензиновые двигатели | |
Внутренний диаметр поршневой головки d | Без втулки | d ≈ d П | d ≈ d П |
С втулкой | (1,1…1,25)·d П | (1,1…1,25)·d П | |
Наружный диаметр головки dг | (1,3…1,7)·d П | (1,25…1,65)·d П | |
Длина головки шатуна l ш | С закрепленным пальцем | (0,28…0,32)·D | (0,28…0,32)·D |
С плавающим пальцем | (0,33…0,45)·D | (0,33…0,45)·D | |
Минимальная радиальная толщина стенки головки h г | (0,16…0,27)·d П | (0,16…0,27)·d П | |
Радиальная толщина стенки втулки s в | (0,070…0,085)·d П | (0,055…0,085)·d П |
Сечение I – I поршневой головки нагружается на режиме n = n Х. Х переменной силой инерции масс поршневой группы m п и верхней части головки m в. г (выше сечения I – I)
. (5.48)
Величина m в. г определяется по геометрическим размерам
верхней части головки и удельной массе материала шатуна или ориенти-ровочно принимается в пределах 6…9 % от массы шатуна.
Сила Pj создает в сечении I – I максимальное и минимальное напряжения:
σmin = 0,
так как при Р j > 0 сила инерции направлена к оси коленчатого вала
и не нагружает сечение I – I. Следовательно, напряжения в сечении I – I
изменяются по закону пульсирующего цикла.
Запас прочности определяется по формулам (5.15…5.19) и составляет для автомобильных и тракторных двигателей 2,5…5.
Напряжения в поршневой головке шатуна, возникающие от за-прессовки в нее втулки и от различия коэффициентов расширения материалов втулки и головки, характеризуются суммарным натягом (мм)
, (5.49)
где Δ – натяг посадки бронзовой втулки (мм, при расчете принимается наибольшая величина в соответствии с применяемой посадкой); Δt – температурный натяг (мм):
, (5.50)
где d – внутренний диаметр головки (мм); α В – термический коэффициент расширения бронзовой втулки, α В = l,8·10–5 1/K – α Г = l,0·10–5 1/K – термический коэффициент расширения стальной головки; ΔT – средняя температура подогрева головки и втулки при работе двигателя,
ΔT = 100…200 К.
Удельное давление (МПа) от суммарного натяга на поверхности соприкосновения втулки с головкой
, (5.51)
где d Г, d и d П – наружный и внутренний диаметры головки и внутренний диаметр втулки (мм) соответственно; μ – коэффициент Пуассона,
μ = 0,3; Е Ш – модуль упругости стального шатуна (МПа), Е Ш = 2,2·105;
Е В – модуль упругости бронзовой втулки (МПа), Е В = 1,15·105.
Напряжения от суммарного натяга на внешней и внутренней поверхностях поршневой головки определяются по формуле Ляме:
, (5.52)
. (5.53)
Значения σ´а и σ´ i могут достигать 100…150 МПа. Следует отметить, что для плавающей втулки напряжения от суммарного натяга равны
нулю.
Сечение А – А поршневой головки на режиме n = n M или n = n N нагружается переменными суммарными силами P = P Г + Pj и постоянной силой от действия запрессованной втулки.
Суммарная сила, растягивающая головку, достигает максимального значения при положении поршня в в.м.т. во время начала впуска. Эта сила определяется без учета незначительной в этот момент величины газовых сил:
, (5.54)
где m П – масса поршневой группы (кг); ω – угловая скорость,
ω = π·n N/30 рад/с при расчете на режиме n = n N, и ω = π·n M/30 рад/с –
на режиме n = n M).
На основании экспериментальных и расчетных данных принимают, что радиальное давление от силы Р j П распределяется равномерно
по внутренней поверхности верхней половины головки (рис. 30а).
В соответствии с расчетной схемой принимают, что нижняя часть головки, опирающаяся на стержень большой жесткости, не де-формируется, а действие отброшенной правой части головки заменяется нормальной силой N j0 (H) и изгибающим моментом Mj0 (H·м).
, (5.55)
, (5.56)
где φ ш.з – угол заделки (град); r ср = (d Г + d)/4 – средний радиус поршневой головки (м).
|
|

Рис. 30. Распределение нагрузок на поршневую головку шатуна:
а – при растяжении; б – при сжатии
На участке 1, лежащем в интервале изменения угла φ Ш от 0 до 90˚:
, (5.57)
. (5.58)
На участке 2, лежащем в интервале изменения угла φ Ш от 90° до угла заделки φ Ш. З:
, (5.59)
. (5.60)
Для опасного сечения А – А при φ ш = φ ш. з значения нормальной
силы и изгибающего момента подсчитывают по формулам (5.59) и (5.60).
По значениям и
определяют напряжения в головке
на внешнем и внутреннем волокнах.
Без учета запрессованной втулки напряжения (МПа) в сечении А – А головки шатуна на внешнем волокне
, (5.61)
а на внутреннем
, (5.62)
где h Г – толщина стенки головки (м), h Г = (d Г – d)/2; l Ш – длина поршневой головки (м).
При наличии запрессованной втулки в головке шатуна происходит их совместная деформация. Вследствие этого на головку передается не вся нормальная сила , а ее часть, пропорциональная коэффициенту К. Влиянием втулки на уменьшение изгибающего момента
пре-небрегают.
Коэффициент
, (5.63)
где F Г, F В – площадь сечения стенок головки и втулки соответственно,
F Г = (d Г – d)·l Ш, F В = (d – d П)·l Ш.
С учетом коэффициента К напряжения
, (5.64)
. (5.65)
Суммарная сила (Н), сжимающая головку, достигает максимального значения после в.м.т. (10…20° угла поворота кривошипа) в начале рас-ширения:
, (5.66)
где р Z д – максимальное давление сгорания, определяемое по скругленной индикаторной диаграмме; Р j – сила инерции массы поршневой группы
при значении φ, соответствующем значению угла кривошипа р Z д.
Пренебрегая смещением максимальной газовой силы относитель-
но в.м.т., находим приближенно:
. (5.67)
Радиальное давление от сжимающей силы Р СЖ на внутреннюю поверхность нижней половины головки принимается косинусоидальным, как показано на расчетной схеме (см. рис. 30б).
Для любого сечения на участках 1 и 2
, (5.68)
, (5.69)
, (5.70)
. (5.71)
В уравнениях (5.70) и (5.71) значения угла φ Ш в отношении φ Ш/π подставляют в радианах, а значения N СЖ.0/Р СЖ и М СЖ.0/(Р СЖ·rСЖ) в зависимости от угла φ Ш.З заделки определяют по табл. 20.
Таблица 20. Значения отношений N СЖ.0/Р СЖ и М СЖ.0/(Р СЖ·rСЖ) от φш.з
Параметры | Угол заделки φш.з, град | ||||||
100 | 105 | 110 | 115 | 120 | 125 | 130 | |
N СЖ. 0/РСЖ МСЖ. 0/(РСЖ·r СЖ) | 0,000 10 | 0,000 5 0,000 1 | 0,000 9 0,000 25 | 0,001 8 0,000 6 | 0,003 0 0,001 1 | 0,006 0 0,001 8 | 0,008 5 0,003 0 |
Для облегчения вычисления изгибающего момента и нормальной силы в табл. 21 приведены значения тригонометрических зависимостей
в функции угла φ Ш.
Таблица 21. Значения тригонометрических зависимостей
для расчета формул 5.68–5.71
f(φш.з) | Угол заделки φш.з, град | ||||||
100 | 105 | 110 | 115 | 120 | 125 | 130 | |
cosφш.з | – 0,173 6 | – 0,258 8 | –0,342 0 | – 0,422 6 | – 0,500 0 | – 0,573 6 | – 0,642 8 |
1 – cosφш.з | 1,173 6 | 1,258 8 | 1,342 0 | 1,422 6 | 1,500 0 | 1,573 6 | 1,642 8 |
sinφш.з – cosφш.з | 1,158 4 | 1,224 7 | 1,281 7 | 1,328 9 | 1,366 0 | 1,392 8 | 1,408 8 |
![]() ![]() | 0,001 1 | 0,002 0 | 0,004 7 | 0,008 6 | 0,013 0 | 0,023 5 | 0,030 4 |
Значения нормальной силы N СЖ . φш. з и изгибающего момента M СЖ . φш. з для опасного сечения А – А (φ ш = φ ш.з) определяются по формулам (5.70)
и (5.71).
Напряжения от суммарной сжимающей силы в сечении А – А
на внешнем волокне
, (5.72)
а на внутреннем
, (5.73)
где К – коэффициент, учитывающий наличие запрессованной бронзовой втулки (см. формулу (5.63)).
Запас прочности поршневой головки шатуна в сечении А – А определяется по уравнениям, приведенным в разделе 5.3. Суммарные напряжения, вызываемые в этом сечении газовыми и инерционными силами и запрессованной втулкой, изменяются по асимметричному
числу, а минимальным запасом прочности обладает наружное волокно,
для которого
, (5.74)
. (5.75)
Запас прочности поршневых головок изменяется в преде-
лах 2,5…5,0. Повышение запаса прочности и снижение напряжений внешнего волокна достигаются за счет уменьшения угла заделки
до φ ш.з = 90° и увеличения радиуса дуги сопряжения головки со стерж-
нем.
Кривошипная головка
Основные конструктивные размеры кривошипной головки шатуна приведены в табл. 22.
Таблица 22. Значения основных конструктивных размеров
кривошипной головки шатуна
Название элемента | Пределы изменения | |
Диаметр шатунной шейки d Ш.Ш | (0,56…0,75)·D | |
Толщина стенки вкладыша t В | тонкостенного | (0,03…0,05)· d П |
толстостенного | 0,1·d ш. ш | |
Расстояние между шатунными болтами СБ | (1,3…1,75)·d ш. ш | |
Длина кривошипной головки lK | (0,45…0,95)·d ш. ш |
Точный расчет кривошипной головки весьма затруднен вслед-
ствие невозможности полного учета влияния конструктивных
факторов. Приближенный расчет кривошипной головки шатуна
сводится к определению напряжения изгиба в среднем сечении II – II крышки головки от инерционных сил Pjp (МН), имеющих мак-
симальное значение в начале впуска (φ = 0°) при работе
дизеля, оснащенного регулятором частоты вращения коленчато-
го вала на режиме максимальной частоты вращения холостого
хода:
, (5.76)
где m п – масса поршневой группы (кг); m ш. п и m ш. к – соответствен-
но массы шатунной группы, совершающие возвратно-поступатель-
ное и вращательное движение (кг); m кр – масса крышки криво-
шипной головки (кг), m кр ≈ (0,20…0,28)·m ш; m ш – масса шатунной
группы (кг).
Напряжение изгиба крышки (МПа) с учетом совместной деформации вкладышей
, (5.77)
где С Б – расстояние между шатунными болтами (м); ,
– момент инерции расчетного сечения соответственно вкладыша и крышки (м4),
,
; W из – момент сопротивления расчетного сечения крышки без учета ребер жесткости (м3), W из = l к·(0,5·С б – r1)2/6;
r1 – внутренний радиус кривошипной головки (м), r1 = 0,5·(d ш.ш + 2· t в); d ш. ш – диаметр шатунной шейки (м); t в – толщина стенки вкладыша (м);
F в – суммарная площадь крышки и вкладыша в расчетном сечении (м2),
F в = l к·0,5·(С б – d ш. ш).
Значение σ из изменяется в пределах 100…300 МПа.
Стержень шатуна
Помимо длины L Ш = R/λ основными конструктивными параметрами стержня шатуна являются размеры его среднего сечения В – В (см.
рис. 28). Значения этих параметров для отечественных автомобильных
и тракторных двигателей приведены в табл. 23.
Таблица 23. Значения основных конструктивных размеров
стержня шатуна
Элемент | Дизельные двигатели | Бензиновые двигатели |
h Ш. min | (0,5…0,55)·d г | (0,5…0,55)·d г |
h Ш | (1,2…1,4)·h ш. min | (1,2…1,4)·h ш. min |
b Ш | (0,55…0,75)·l ш | (0,5…0,6)·l ш |
аШ ≈ t Ш | 4,0…7,5 | 2,5…4,0 |
Стержень шатуна рассчитывают на усталостную прочность
в среднем сечении В – В при действии знакопеременных суммар-
ных сил (газовых и инерционных), возникающих при работе двигателя
на режимах n = n N или n = n М. Обычно расчет ведется для режи-
ма максимальной мощности. Запас прочности сечения определяется
в плоскости качания шатуна и в перпендикулярной плоскости. Усло-
вием равнопрочности стержня шатуна в обеих плоскостях является
n х = n Y.
Сила, сжимающая шатун, достигает максимального значения в начале рабочего хода при р Z д и определяется по результатам динамического расчета или по формуле
, (5.78)
где m j = m п + 0,275·m ш – масса возвратно движущихся частей кривошипно-шатунного механизма (условно предполагается, что среднее сечение В – В находится в центре тяжести шатуна).
Сила, растягивающая шатун, достигает максимального значения
в начале впуска (в в.м.т.) и также определяется по результатам динамического расчета или по формуле
, (5.79)
где р Г – давление остаточных газов.
От сжимающей силы Р СЖ в сечении В – В возникают максимальные напряжения сжатия и продольного изгиба (МПа):
в плоскости качания шатуна
, (5.80)
где – коэффициент, учитывающий влияние продольного изгиба
шатуна в плоскости качания шатуна, ; σе = σв – предел упругости материала шатуна (МПа); L Ш – длина шатуна (м),
L Ш = R/λ; – момент инерции сечения В – В относительно оси х – х, перпендикулярной к плоскости качания шатуна (м4),
;
– площадь среднего сечения шату-
на (м2), .
в плоскости, перпендикулярной к плоскости качания:
, (5.81)
где – коэффициент, учитывающий влияние продольного изгиба
шатуна в плоскости, перпендикулярной к плоскости качания шатуна, ; L1 – длина стержня шатуна между поршневой
и кривошипной головками (м), L1 = L Ш – (d + d1)/2; – момент инерции сечения В – В относительно оси у – у, лежащей в плоскости качания шатуна (м4),
.
В современных автомобильных и тракторных двигателях
напряжения σmах. X и σmax. Y для углеродистых и легированных
сталей не должны превышать соответственно 160…250 и
200…350 МПа.
Минимальное напряжение, возникающее в сечении В – В от рас-тягивающей силы PР, в плоскости качания шатуна и в перпендикулярной плоскости, определяется по формуле
. (5.82)
Запасы прочности стержня шатуна в плоскости качания n х
и в перпендикулярной плоскости n y определяются по уравнениям,
приведенным в разделе 5.3. При определении n х и n y принимает-
ся, что коэффициенты концентрации напряжений kσ зависят
только от материала шатуна. Для шатунов автомобильных
и тракторных двигателей значения n х и n у не должны быть
ниже 1,5.
Шатунные болты
В четырехтактных двигателях болты, стягивающие половинки кривошипной головки шатуна, подвергаются растяжению от действия
сил инерции поступательно движущихся масс поршня и шатуна и вращаю-щихся масс, расположенных над плоскостью разъема криво-
шипной головки. Величину этих сил инерции определяют по форму-
ле (5.76). Кроме того, болты испытывают растяжение от предварительной затяжки.
Шатунные болты должны обладать высокой механической
прочностью и надежностью. Изготовляют их из стали 35Х, 40Х,
35ХМА, 37XH3A, а при больших напряжениях затяжки – из ле-
гированной стали с более высокими пределами текучести
(18ХНВА, 20ХНЗА, 40ХН, 40ХНМА).
При работе двигателя силы инерции стремятся разорвать
болты, во избежание чего болты следует затягивать настолько,
чтобы при действии данной силы не нарушалась плотность соедине-
ния.
Сила предварительной затяжки (МН)
, (5.83)
где i Б – число шатунных болтов.
Суммарная сила, растягивающая болт:
, (5.84)
где χ – коэффициент основной нагрузки резьбового соедине-
ния:
(5.85)
где К ш – податливость стягиваемых частей шатуна; К б – податливость болта.
По опытным данным коэффициент χ изменяется в пределах 0,15…0,25. С уменьшением диаметра шатунного болта значение χ, как правило, также уменьшается.
Максимальные и минимальные напряжения, возникающие в болте, определяют в сечении по внутреннему диаметру резьбы:
, (5.86)
, (5.87)
где d в – внутренний диаметр резьбы болта, d в = d – 1,4·t (мм);
d – номинальный диаметр болта (мм); t – шаг резьбы (мм).
Запасы прочности болта определяют по уравнениям, приведен-
ным в разделе 5.3; коэффициент концентрации напряжения k σ –
по формуле (5.10) с учетом вида концентратора и свойств материала.
Для шатунных болтов значения запаса прочности не должны быть ниже двух.
|
Фазы газораспределения автотракторных двигателей
(в градусах поворота коленчатого вала)
Двигатель | Впускной клапан | Выпускной клапан | Продолжительность открытия клапанов | Угол перекры-тия | ||||||||
Открытие до в.м.т. | Закрытие после н.м.т. | Открытие до н.м.т. | Закрытие после н.м.т. | Впуск-ного | Выпуск- ного | |||||||
Бензиновые двигатели | ||||||||||||
ВАЗ-2101 | 20 | 69 | 67 | 22 | 269 | 269 | 42 | |||||
ВАЗ-2102 | 20 | 69 | 67 | 22 | 269 | 269 | 42 | |||||
ВАЗ-21021 | 20 | 69 | 67 | 22 | 269 | 269 | 42 | |||||
ВАЗ-21023 | 20 | 69 | 67 | 22 | 269 | 269 | 42 | |||||
ВАЗ-2107 | 20 | 69 | 67 | 22 | 269 | 269 | 42 | |||||
ГАЗ-3102 | 12 | 60 | 54 | 18 | 252 | 252 | 30 | |||||
ГАЗ-53-12 | 36 | 52 | 70 | 18 | 268 | 268 | 54 | |||||
ГАЗ-51 | 9 | 51 | 47 | 13 | 240 | 240 | 22 | |||||
ГАЗ-53 | 24 | 64 | 50 | 22 | 268 | 252 | 46 | |||||
ЗИЛ-120 | 20 | 69 | 67 | 22 | 269 | 269 | 42 | |||||
ЗИЛ-130 ЗИЛ-131 | 31 | 83 | 67 | 47 | 294 | 294 | 78 | |||||
ЗИЛ-164 | 12,5 | 59,5 | 44,5 | 27,5 | 252 | 252 | 40 | |||||
ЗИЛ-375 | 16 | 71 | 52 | 35 | 267 | 267 | 51 | |||||
МеМЗ-968А | 10 | 46 | 46 | 10 | 236 | 236 | 20 | |||||
АЗЛК-408 | 21 | 55 | 57 | 19 | 256 | 256 | 40 | |||||
АЗЛК-412 | 27 | 65 | 75 | 18 | 272 | 273 | 45 | |||||
Дизельные двигатели | ||||||||||||
А-01, А-41 А-41Т | 20 | 50 | 50 | 20 | 250 | 250 | 40 | |||||
Д-108 Д-120 Д-144 Д-145Т | 16 | 40 | 40 | 16 | 236 | 236 | 32 | |||||
Д-160 | 8 | 37 | 47 | 10 | 225 | 237 | 18 | |||||
Д-240 Д-240Т Д-241Л Д-245.12 | 16 | 46 | 56 | 18 | 242 | 254 | 34 | |||||
СМД-14 СМД-16 СМД-18 | 10 | 46 | 56 | 10 | 236 | 246 | 20 | |||||
СМД-60 СМД-62 СМД-63М СМД-66 | 3 | 45 | 65 | 8 | 228 | 253 | 11 | |||||
ЯМЗ-236 ЯМЗ-238 ЯМЗ-238 | 20 | 46 | 66 | 20 | 246 | 266 | 40 | |||||
ЯМЗ-240 | 20 | 56 | 56 | 20 | 256 | 256 | 40 | |||||
КамАЗ-740 | 10 | 46 | 66 | 10 | 236 | 256 | 20 | |||||
Приложение 2
Технические характеристики бензиновых двигателей (* – турбонаддув)
Модель двигателя | Номинальная мощность Ne (кВт) | Частота вращения коленчатого вала n (мин–1) | Число и расположение цилиндров | Степень сжатия ε | Диаметр цилиндра D (мм) | Ход поршня S (мм) | Рабочий объем двигателя V Л (л) |
1 | 2 | 3 | 4 | 5 | 6 | 7 | 8 |
ВАЗ-2101 | 47,1 | 5600 | 4-Р | 8,5 | 76 | 66 | 1,197 |
ВАЗ-2102 | 58,7 | 5600 | 4-Р | 8,5 | 76 | 66 | 1,197 |
ВАЗ-21021 | 63,7 | 5600 | 4-Р | 8,5 | 76 | 66 | 1,197 |
ВАЗ-21023 | 71,1 | 5600 | 4-Р | 8,5 | 76 | 66 | 1,197 |
ВАЗ-2105 | 47,0 | 5800 | 4-Р | 8,5 | 79 | 66 | 1,30 |
ВАЗ-2106.70 | 56,3 | 5400 | 4-Р | 8,5 | 79 | 80 | 1,569 |
ВАЗ-2107 | 55,6 | 5600 | 4-Р | 8,5 | 76 | 66 | 1,197 |
ВАЗ-2108 | 47,0 | 5600 | 4-Р | 9,9 | 76 | 71 | 1,30 |
ВАЗ-21213 | 58,0 | 5200 | 4-Р | 9,3 | 82 | 80 | 1690 |
ВАЗ-2111 | 57,2 | 5400 | 4-Р | 9,8 | 82 | 71 | 1499 |
УМЗ-451 | 52,8 | 4000 | 4-Р | 6,7 | 92 | 92 | 2,45 |
УМЗ-417500 | 62,5 | 4000 | 4-Р | 8,2 | 92 | 92 | 2,45 |
УМЗ-4215.10 | 65,4 | 4000 | 4-Р | 7 | 100 | 92 | 2,890 |
УЗАМ-331.10 | 52,9 | 5500 | 4-Р | 9,5 | 82 | 70 | 1,478 |
ЗМЗ-4063.10 | 72,2 | 4500 | 4-Р | 9,5 | 92 | 86 | 2,30 |
ГАЗ-52-04 | 55,1 | 2600 | 6-Р | 6,7 | 82 | 110 | 3,484 |
Иж-21251 | 58,7 | 5800 | 4-Р | 8,8 | 82 | 70 | 1,478 |
ГАЗ-24-01 | 62,3 | 4500 | 4-Р | 6,7 | 92 | 92 | 2,445 |
ЗМЗ-402.10 | 73,5 | 4500 | 4-Р | 8,2 | 92 | 92 | 2,445 |
ЗМЗ-4025.10 | 56,1 | 4500 | 4-Р | 6,7 | 92 | 92 | 2,445 |
ЗМЗ-53(66) | 84,4 | 3200 | 8-V | 6,7 | 92 | 80 | 4,252 |
Продолжение прил. 2
1 | 2 | 3 | 4 | 5 | 6 | 7 | 8 |
ЗМЗ-513 | 87,5 | 3200 | 8-V | 7,6 | 92 | 80 | 4,252 |
ЗИЛ-130 | 170 | 3600 | 8-V | 6,5 | 100 | 95 | 6,0 |
ЗИЛ-375 | 132,0 | 3200 | 8-V | 6,5 | 108 | 95 | 6,959 |
ЗИЛ-508.10 | 110 | 3200 | 8-V | 7,1 | 100 | 95 | 6,0 |
ЗМЗ-4022 | 77,2 | 4750 | 4-Р | 8,0 | 92 | 92 | 2,445 |
МеМЗ-245 | 37,5 | 5200 | 4-Р | 9,5 | 72 | 67 | 1,091 |
МеМЗ-968А | 33,1 | 4200 | 4-V | 8,8 | 76 | 66 | 1,2 |
МЗМА-412 | 55,2 | 5800 | 4-Р | 8,8 | 82 | 70 | 1,48 |
412Э | 54,0 | 5800 | 4-Р | 8,5 | 82 | 70 | 1,480 |
AlfaRomeo 32310 | 110 | 6300 | 4-Р | 10 | 83 | 91 | 1,970 |
AVU | 75 | 5600 | 4-Р | 10,3 | 81 | 77,4 | 1,595 |
APG | 92 | 6000 | 4-Р | 10,3 | 1,781 | ||
AUM/ARX* | 110 | 5700 | 4-Р | 9,5 | 1,781 | ||
AUQ/ARY* | 132 | 5500 | 4-Р | 9,5 | 1,781 | ||
AMK* | 154 | 5800 | 4-Р | 8,9 | 1,781 | ||
BAM | 165 | 5900 | 4-Р | 8,9 | 1,781 | ||
Sigma | 92 | 6000 | 4-Р | 11 | 79 | 81,4 | 1,596 |
1ZR-F | 91,2 | 6000 | 4-Р | 10,2 | 80,5 | 78,5 | 1,598 |
3ZR-FE | 106,6 | 6200 | 4-Р | 11,5 | 80,5 | 97,6 | 1,987 |
2AD-FHV | 109,6 | 3600 | 4-Р | 15,7 | 86 | 96 | 2,231 |
3SZ-VE | 80,2 | 6000 | 4-Р | 10 | 72 | 91,8 | 1,495 |
6G74 | 136,8 | 4750 | 6-V | 9,5 | 93 | 85,8 | 3,497 |
M16A | 78 | 5900 | 4-Р | 10,5 | 78 | 83 | 1,586 |
J24B | 124,3 | 6000 | 4-Р | 10 | 92 | 92 | 2,393 |
Приложение 3
Технические характеристики дизельных двигателей
Модель двигателя | Турбо-наддув | Номинальная мощность Ne (кВт) | Частота вращения коленчатого вала n (мин–1) | Число и рас-положение цилиндров | Степень сжатия ε | Диаметр цилиндра D (мм) | Ход поршня S (мм) | Рабочий объем двигателя Vh (л) |
А-01 | 80,9 | 1600 | 6-Р | 16,5 | 130 | 140 | 11,15 | |
А-41Т | 93,4 | 1750 | 4-Р | 16,5 | 130 | 140 | 7,45 | |
А-41 | 66,2 | 1750 | 4-Р | 16,5 | 130 | 140 | 7,45 | |
Д-108 | 79,4 | 1070 | 4-Р | 14 | 145 | 205 | 13,53 | |
Д-120 | 23,5 | 2000 | 2-P | 16,5 | 105 | 120 | 2,08 | |
Д-130 | 102,9 | 1070 | 4-Р | 14 | 145 | 205 | 13,53 | |
Д-144 | 46 | 2200 | 4-Р | 16,5 | 105 | 120 | 4,15 | |
Д-145Т | 62,5 | 2200 | 4-P | 16,5 | 105 | 120 | 4,15 | |
Д-160 | 117,6 | 1250 | 4-Р | 14 | 145 | 205 | 13,53 | |
ГАЗ-560 | + | 81,0 | 3800 | 4-Р | 20,5 | 2,134 | ||
ГАЗ-562 | + | 110 | 3200 | 6-Р | 19,0 | 3,2 | ||
Д-240 | 56 | 2200 | 4-Р | 16,0 | 110 | 125 | 4,75 | |
Д-240Т | 73,6 | 2600 | 4-Р | 16,0 | 110 | 125 | 4,75 | |
Д-241Л | 51,5 | 2100 | 4-Р | 16,0 | 110 | 125 | 4,75 | |
ТЗВ-928-50 | + | 230 | 1800 | 8-V | 17,5 | 12,667 | ||
ТЗВ-928-60 | + | 255 | 1800 | 8-V | 17,5 | 12,667 | ||
ТЗВ-928-70 | + | 300 | 1800 | 8-V | 17,5 | 12,667 | ||
Д-245.12 | + | 80 | 2400 | 4-Р | 15,1 | 125 | 100 | 4,75 |
Д-245.7 | + | 90 | 2400 | 4-Р | 15,1 | 4,75 | ||
КамАЗ-740 | 154,4 | 2600 | 8-V | 17 | 120 | 120 | 10,85 | |
КамАЗ-740.11 | + | 169 | 2200 | 8-V | 17 | 120 | 120 | 10,85 |
Продолжение прил. 3
КамАЗ-740.13 | 182,6 | 2200 | 8-V | 17 | 120 | 120 | 10,85 | |
СМД-14 | 55,1 | 1700 | 4-Р | 17 | 120 | 140 | 6,33 | |
СМД-60 | + | 116,2 | 2000 | 6-V | 15 | 130 | 115 | 9,15 |
СМД-62 | + | 121,3 | 2100 | 6-V | 15 | 130 | 115 | 9,15 |
СМД-63М | + | 159 | 2100 | 6-V | 15 | 130 | 115 | 9,15 |
СМД-66 | + | 129 | 1900 | 6-V | 15 | 130 | 115 | 9,15 |
ЯМЗ-236 | – | 132,4 | 2100 | 6-V | 16,5 | 130 | 140 | 11,14 |
ЯМЗ-236 | – | 143 | 2100 | 6-V | 16,5 | 130 | 140 | 11,15 |
ЯМЗ-236Г | – | 110 | 1700 | 6-V | 16,5 | 130 | 140 | 11,15 |
ЯМЗ-236Д | – | 129 | 2100 | 6-V | 16,5 | 130 | 140 | 11,15 |
ЯМЗ-236НЕ | + | 169 | 2100 | 6-V | 16,5 | 130 | 140 | 11,15 |
ЯМЗ-236Б2 | + | 184 | 2000 | 6-V | 16,5 | 130 | 140 | 11,15 |
ЯМЗ-238 | – | 176,5 | 2100 | 8-V | 16,5 | 130 | 140 | 14,86 |
ЯМЗ-238 НБ | – | 161,8 | 1700 | 8-V | 16,5 | 130 | 140 | 14,86 |
ЯМЗ-238М2 | – | 176 | 2100 | 8-V | 16,5 | 130 | 140 | 14,86 |
ЯМЗ-238Б1 | + | 220 | 2000 | 8-V | 16,5 | 130 | 140 | 14,86 |
ЯМЗ-238БЛ | + | 228 | 2000 | 8-V | 16,5 | 130 | 140 | 14,86 |
ЯМЗ-238НД | + | 173 | 1700 | 8-V | 16,5 | 130 | 140 | 14,86 |
ЯМЗ-240 | + | 264,8 | 2100 | 12-V | 16,5 | 130 | 140 | 22,29 |
ЯМЗ-240М2 | + | 265 | 2100 | 12-V | 16,5 | 130 | 140 | 22,29 |
ЯМЗ-240ПМ | + | 309 | 2100 | 12-V | 16,5 | 130 | 140 | 22,29 |
ЯМЗ-240НМ | + | 368 | 2100 | 12-V | 16,5 | 130 | 140 | 22,29 |
D2866LF20 | + | 294 | 2000 | 6-Р | 17 | 11,967 | ||
D2866LF23 | + | 228 | 1900 | 6-Р | 19 | 11,967 | ||
D2866LF25 | + | 301 | 1900 | 6-Р | 19 | 11,967 | ||
4D56 | + | 130,9 | 4000 | 4-Р | 16,5 | 91,1 | 95 | 2,477 |
Приложение 4
Значения тригонометрических функций для расчета хода поршня S
j, ° | Значения | j, ° | |||||||
0,24 | 0,25 | 0,26 | 0,27 | 0,28 | 0,29 | 0,30 | 0,31 | ||
0 | 0,0000 | 0,0000 | 0,0000 | 0,0000 | 0,0000 | 0,0000 | 0,0000 | 0,0000 | 360 |
10 | 0,0188 | 0,0190 | 0,0191 | 0,0193 | 0,0194 | 0,0196 | 0,0197 | 0,0199 | 350 |
20 | 0,0743 | 0,0749 | 0,0755 | 0,0761 | 0,0767 | 0,0773 | 0,0779 | 0,0784 | 340 |
30 | 0,1640 | 0,1653 | 0,1665 | 0,1678 | 0,1690 | 0,1703 | 0,1715 | 0,1728 | 330 |
40 | 0,2836 | 0,2857 | 0,2877 | 0,2898 | 0,2918 | 0,2939 | 0,2960 | 0,2980 | 320 |
50 | 0,4276 | 0,4306 | 0,4335 | 0,4364 | 0,4394 | 0,4423 | 0,4452 | 0,4482 | 310 |
60 | 0,5900 | 0,5938 | 0,5975 | 0,6013 | 0,6050 | 0,6088 | 0,6125 | 0,6163 | 300 |
70 | 0,7640 | 0,7684 | 0,7728 | 0,7772 | 0,7816 | 0,7860 | 0,7905 | 0,7949 | 290 |
80 | 0,9428 | 0,9476 | 0,9525 | 0,9573 | 0,9622 | 0,9670 | 0,9719 | 0,9767 | 280 |
90 | 1,1200 | 1,1250 | 1,1300 | 1,1355 | 1,1400 | 1,1450 | 1,1500 | 1,1550 | 270 |
100 | 1,2900 | 1,2948 | 1,2997 | 1,3045 | 1,3094 | 1,3142 | 1,3191 | 1,3239 | 260 |
110 | 1,4480 | 1,4524 | 1,4568 | 1,4612 | 1,4656 | 1,4700 | 1,4745 | 1,4789 | 250 |
120 | 1,5900 | 1,5938 | 1,5975 | 1,6013 | 1,6050 | 1,6088 | 1,6125 | 1,6163 | 240 |
130 | 1,7132 | 1,7162 | 1,7191 | 1,7220 | 1,7250 | 1,7279 | 1,7308 | 1,7338 | 230 |
140 | 1,8156 | 1,8177 | 1,8197 | 1,8218 | 1,8238 | 1,8259 | 1,8280 | 1,8300 | 220 |
150 | 1,8960 | 1,8973 | 1,8985 | 1,8998 | 1,9010 | 1,9023 | 1,9035 | 1,9048 | 210 |
160 | 1,9537 | 1,9543 | 1,9549 | 1,9555 | 1,9561 | 1,9567 | 1,9573 | 1,9578 | 200 |
170 | 1,9884 | 1,9886 | 1,9887 | 1,9889 | 1,9890 | 1,9892 | 1,9893 | 1,9895 | 190 |
180 | 2,0000 | 2,0000 | 2,0000 | 2,0000 | 2,0000 | 2,0000 | 2,0000 | 2,0000 | 180 |
Приложение 5
Значения тригонометрических функций для расчета скорости поршня VП
j, ° | Знак | Значения | Знак | j, ° | |||||||
0,24 | 0,25 | 0,26 | 0,27 | 0,28 | 0,29 | 0,30 | 0,31 | ||||
0 | + | 0,0000 | 0,0000 | 0,0000 | 0,0000 | 0,0000 | 0,0000 | 0,0000 | 0,0000 | – | 360 |
10 | + | 0,2146 | 0,2164 | 0,2181 | 0,2198 | 0,2215 | 0,2332 | 0,2249 | 0,2266 | – | 350 |
20 | + | 0,4191 | 0,4224 | 0,4256 | 0,4288 | 0,4320 | 0,4352 | 0,4384 | 0,4416 | – | 340 |
30 | + | 0,6039 | 0,6083 | 0,6126 | 0,6169 | 0,6212 | 0,6256 | 0,6299 | 0,6342 | – | 330 |
40 | + | 0,7610 | 0,7659 | 0,7708 | 0,7757 | 0,7807 | 0,7856 | 0,7905 | 0,7954 | – | 320 |
50 | + | 0,8842 | 0,8891 | 0,8904 | 0,8989 | 0,9039 | 0,9088 | 0,9137 | 0,9186 | – | 310 |
60 | + | 0,9699 | 0,9743 | 0,9786 | 0,9829 | 0,9872 | 0,9916 | 0,9959 | 1,0002 | – | 300 |
70 | + | 1,0168 | 1,0201 | 1,0233 | 1,0265 | 1,0297 | 1,0329 | 1,0361 | 1,0393 | – | 290 |
80 | + | 1,0258 | 1,0276 | 1,0293 | 1,0310 | 1,0327 | 1,0344 | 1,0361 | 1,0378 | – | 280 |
90 | + | 1,0000 | 1,0000 | 1,0000 | 1,0000 | 1,0000 | 1,0000 | 1,0000 | 1,0000 | – | 270 |
100 | + | 0,9438 | 0,9420 | 0,9403 | 0,9386 | 0,9369 | 0,9352 | 0,9352 | 0,9318 | – | 260 |
110 | + | 0,8626 | 0,8593 | 0,8561 | 0,8529 | 0,8497 | 0,8465 | 0,8465 | 0,8401 | – | 250 |
120 | + | 0,7621 | 0,7577 | 0,7534 | 0,7491 | 0,7448 | 0,7404 | 0,7404 | 0,7318 | – | 240 |
130 | + | 0,6478 | 0,6429 | 0,6380 | 0,6331 | 0,6281 | 0,6232 | 0,6232 | 0,6134 | – | 230 |
140 | + | 0,5246 | 0,5197 | 0,5148 | 0,5099 | 0,5049 | 0,5000 | 0,5000 | 0,4902 | – | 220 |
150 | + | 0,3961 | 0,3917 | 0,3874 | 0,3831 | 0,3788 | 0,3744 | 0,3744 | 0,3658 | – | 210 |
160 | + | 0,2649 | 0,2616 | 0,2584 | 0,2552 | 0,2520 | 0,2488 | 0,2488 | 0,2424 | – | 200 |
170 | + | 0,1326 | 0,1308 | 0,1291 | 0,1274 | 0,1257 | 0,1240 | 0,1240 | 0,1206 | – | 190 |
180 | + | 0,0000 | 0,0000 | 0,0000 | 0,0000 | 0,0000 | 0,0000 | 0,0000 | 0,0000 | – | 180 |
Приложение 6
Значения тригонометрических функций для расчета ускорения поршня jП
j, ° | Знак | Значения | Знак | j, ° | |||||||
0,24 | 0,25 | 0,26 | 0,27 | 0,28 | 0,29 | 0,30 | 0,31 | ||||
0 | + | 1,2400 | 1,2500 | 1,2600 | 1,2700 | 1,2800 | 1,2900 | 1,3000 | 1,3100 | + | 360 |
10 | + | 1,2103 | 1,2197 | 1,2291 | 1,2385 | 1,2479 | 1,2573 | 1,2667 | 1,2761 | + | 350 |
20 | + | 1,1235 | 1,1312 | 1,1389 | 1,1465 | 1,1542 | 1,1618 | 1,1695 | 1,1772 | + | 340 |
30 | + | 0,9860 | 0,9910 | 0,9960 | 1,0010 | 1,0060 | 1,0110 | 1,0160 | 1,0210 | + | 330 |
40 | + | 0,8077 | 0,8094 | 0,8111 | 0,8129 | 0,8146 | 0,8163 | 0,8181 | 0,8198 | + | 320 |
50 | + | 0,6011 | 0,5994 | 0,5977 | 0,5959 | 0,5942 | 0,5925 | 0,5907 | 0,5890 | + | 310 |
60 | + | 0,3800 | 0,3750 | 0,3700 | 0,3650 | 0,3600 | 0,3550 | 0,3500 | 0,3450 | + | 300 |
70 | + | 0,1582 | 0,1505 | 0,1428 | 0,1352 | 0,1275 | 0,1199 | 0,1122 | 0,1045 | + | 290 |
80 | – | 0,0519 | 0,0613 | 0,0707 | 0,0801 | 0,0895 | 0,0989 | 0,1083 | 0,1177 | – | 280 |
90 | – | 0,2400 | 0,2500 | 0,2600 | 0,2700 | 0,2800 | 0,2900 | 0,3000 | 0,3100 | – | 270 |
100 | – | 0,3991 | 0,4085 | 0,4179 | 0,4273 | 0,4367 | 0,4461 | 0,4555 | 0,4649 | – | 260 |
110 | – | 0,5258 | 0,5335 | 0,5412 | 0,5488 | 0,5565 | 0,5641 | 0,5718 | 0,5795 | – | 250 |
120 | – | 0,6200 | 0,6250 | 0,6300 | 0,6350 | 0,6400 | 0,6450 | 0,6500 | 0,6550 | – | 240 |
130 | – | 0,6845 | 0,6862 | 0,6879 | 0,6897 | 0,6914 | 0,6931 | 0,6949 | 0,6966 | – | 230 |
140 | – | 0,7243 | 0,7226 | 0,7209 | 0,7191 | 0,7174 | 0,7157 | 0,7139 | 0,7122 | – | 220 |
150 | – | 0,7460 | 0,7410 | 0,7360 | 0,7310 | 0,7260 | 0,7210 | 0,7160 | 0,7110 | – | 210 |
160 | – | 0,7559 | 0,7482 | 0,7405 | 0,7329 | 0,7252 | 0,7176 | 0,7099 | 0,7022 | – | 200 |
170 | – | 0,7539 | 0,7499 | 0,7405 | 0,7311 | 0,7217 | 0,7123 | 0,7029 | 0,6935 | – | 190 |
180 | – | 0,7600 | 0,7500 | 0,7400 | 0,7300 | 0,7200 | 0,7100 | 0,7000 | 0,6900 | – | 180 |
Приложение 7
Значения тригонометрических функций для расчета силы N
j, ° | Знак | Значения | Знак | j, ° | |||||||
0,24 | 0,25 | 0,26 | 0,27 | 0,28 | 0,29 | 0,30 | 0,31 | ||||
0 | + | 0 | 0 | 0 | 0 | 0 | 0 | 0 | 0 | – | 360 |
10 | + | 0,042 | 0,043 | 0,045 | 0,047 | 0,049 | 0,050 | 0,052 | 0,054 | – | 350 |
20 | + | 0,082 | 0,086 | 0,089 | 0,093 | 0,096 | 0,100 | 0,103 | 0,106 | – | 340 |
30 | + | 0,121 | 0,126 | 0,131 | 0,136 | 0,141 | 0,146 | 0,151 | 0,156 | – | 330 |
40 | + | 0,156 | 0,162 | 0,169 | 0,176 | 0,182 | 0,189 | 0,196 | 0,202 | – | 320 |
50 | + | 0,186 | 0,194 | 0,202 | 0,210 | 0,218 | 0,226 | 0,234 | 0,243 | – | 310 |
60 | + | 0,211 | 0,220 | 0,230 | 0,239 | 0,248 | 0,257 | 0,267 | 0,276 | – | 300 |
70 | + | 0,230 | 0,240 | 0,250 | 0,260 | 0,270 | 0,280 | 0,291 | 0,301 | – | 290 |
80 | + | 0,241 | 0,252 | 0,263 | 0,273 | 0,284 | 0,295 | 0,306 | 0,316 | – | 280 |
90 | + | 0,245 | 0,256 | 0,267 | 0,278 | 0,289 | 0,300 | 0,311 | 0,322 | – | 270 |
100 | + | 0,241 | 0,043 | 0,263 | 0,273 | 0,284 | 0,295 | 0,306 | 0,316 | – | 260 |
110 | + | 0,230 | 0,086 | 0,250 | 0,260 | 0,270 | 0,280 | 0,291 | 0,301 | – | 250 |
120 | + | 0,211 | 0,126 | 0,230 | 0,239 | 0,248 | 0,257 | 0,267 | 0,276 | – | 240 |
130 | + | 0,186 | 0,162 | 0,202 | 0,210 | 0,218 | 0,226 | 0,234 | 0,243 | – | 230 |
140 | + | 0,156 | 0,194 | 0,169 | 0,176 | 0,182 | 0,189 | 0,196 | 0,202 | – | 220 |
150 | + | 0,121 | 0,220 | 0,131 | 0,136 | 0,141 | 0,146 | 0,151 | 0,156 | – | 210 |
160 | + | 0,082 | 0,240 | 0,089 | 0,093 | 0,096 | 0,100 | 0,103 | 0,106 | – | 200 |
170 | + | 0,042 | 0,252 | 0,045 | 0,047 | 0,049 | 0,050 | 0,052 | 0,054 | – | 190 |
180 | + | 0 | 0 | 0 | 0 | 0 | 0 | 0 | 0 | – | 180 |
Приложение 8
Значения тригонометрических функций для расчета силы S
j, ° | Знак | Значения | Знак | j, ° | |||||||
0,24 | 0,25 | 0,26 | 0,27 | 0,28 | 0,29 | 0,30 | 0,31 | ||||
0 | + | 1 | 1 | 1 | 1 | 1 | 1 | 1 | 1 | + | 360 |
10 | + | 1,001 | 1,001 | 1,001 | 1,001 | 1,001 | 1,001 | 1,001 | 1,001 | + | 350 |
20 | + | 1,003 | 1,004 | 1,004 | 1,004 | 1,005 | 1,005 | 1,005 | 1,006 | + | 340 |
30 | + | 1,007 | 1,008 | 1,009 | 1,009 | 1,010 | 1,011 | 1,011 | 1,012 | + | 330 |
40 | + | 1,012 | 1,013 | 1,014 | 1,015 | 1,016 | 1,018 | 1,019 | 1,020 | + | 320 |
50 | + | 1,017 | 1,019 | 1,020 | 1,022 | 1,024 | 1,025 | 1,027 | 1,029 | + | 310 |
60 | + | 1,022 | 1,024 | 1,026 | 1,028 | 1,030 | 1,032 | 1,035 | 1,037 | + | 300 |
70 | + | 1,026 | 1,028 | 1,031 | 1,033 | 1,036 | 1,039 | 1,041 | 1,044 | + | 290 |
80 | + | 1,029 | 1,031 | 1,034 | 1,037 | 1,040 | 1,043 | 1,046 | 1,049 | + | 280 |
90 | + | 1,030 | 1,032 | 1,035 | 1,038 | 1,041 | 1,044 | 1,047 | 1,050 | + | 270 |
100 | + | 1,029 | 1,031 | 1,034 | 1,037 | 1,040 | 1,043 | 1,046 | 1,049 | + | 260 |
110 | + | 1,026 | 1,028 | 1,031 | 1,033 | 1,036 | 1,039 | 1,041 | 1,044 | + | 250 |
120 | + | 1,022 | 1,024 | 1,026 | 1,028 | 1,030 | 1,032 | 1,035 | 1,037 | + | 240 |
130 | + | 1,017 | 1,019 | 1,020 | 1,022 | 1,024 | 1,025 | 1,027 | 1,029 | + | 230 |
140 | + | 1,012 | 1,013 | 1,014 | 1,015 | 1,016 | 1,018 | 1,019 | 1,020 | + | 220 |
150 | + | 1,007 | 1,008 | 1,009 | 1,009 | 1,010 | 1,011 | 1,011 | 1,012 | + | 210 |
160 | + | 1,003 | 1,004 | 1,004 | 1,004 | 1,005 | 1,005 | 1,005 | 1,006 | + | 200 |
170 | + | 1,001 | 1,001 | 1,001 | 1,001 | 1,001 | 1,001 | 1,001 | 1,001 | + | 190 |
180 | + | 1 | 1 | 1 | 1 | 1 | 1 | 1 | 1 | + | 180 |
Приложение 9
Значения тригонометрических функций для расчета силы K
j, ° | Знак | Значения | Знак | j, ° | |||||||
0,24 | 0,25 | 0,26 | 0,27 | 0,28 | 0,29 | 0,30 | 0,31 | ||||
0 | + | 1 | 1 | 1 | 1 | 1 | 1 | 1 | 1 | + | 360 |
10 | + | 0,978 | 0,977 | 0,997 | 0,997 | 0,976 | 0,976 | 0,975 | 0,975 | + | 350 |
20 | + | 0,912 | 0,910 | 0,909 | 0,908 | 0,907 | 0,906 | 0,905 | 0,903 | + | 340 |
30 | + | 0,806 | 0,803 | 0,801 | 0,798 | 0,795 | 0,793 | 0,790 | 0,788 | + | 330 |
40 | + | 0,666 | 0,662 | 0,657 | 0,653 | 0,649 | 0,645 | 0,640 | 0,636 | + | 320 |
50 | + | 0,500 | 0,494 | 0,488 | 0,482 | 0,476 | 0,469 | 0,463 | 0,457 | + | 310 |
60 | + | 0,317 | 0,309 | 0,301 | 0,293 | 0,285 | 0,277 | 0,269 | 0,261 | + | 300 |
70 | + | 0,126 | 0,117 | 0,107 | 0,098 | 0,088 | 0,078 | 0,069 | 0,059 | + | 290 |
80 | – | 0,064 | 0,075 | 0,085 | 0,095 | 0,106 | 0,117 | 0,127 | 0,138 | – | 280 |
90 | – | 0,245 | 0,256 | 0,267 | 0,278 | 0,289 | 0,300 | 0,311 | 0,322 | – | 270 |
100 | – | 0,411 | 0,422 | 0,432 | 0,443 | 0,453 | 0,464 | 0,475 | 0,485 | – | 260 |
110 | – | 0,558 | 0,568 | 0,577 | 0,586 | 0,596 | 0,606 | 0,615 | 0,625 | – | 250 |
120 | – | 0,683 | 0,691 | 0,699 | 0,707 | 0,715 | 0,723 | 0,731 | 0,739 | – | 240 |
130 | – | 0,785 | 0,792 | 0,798 | 0,804 | 0,810 | 0,816 | 0,822 | 0,829 | – | 230 |
140 | – | 0,866 | 0,870 | 0,875 | 0,879 | 0,883 | 0,887 | 0,892 | 0,896 | – | 220 |
150 | – | 0,926 | 0,929 | 0,931 | 0,934 | 0,937 | 0,939 | 0,942 | 0,944 | – | 210 |
160 | – | 0,968 | 0,969 | 0,970 | 0,971 | 0,973 | 0,974 | 0,975 | 0,976 | – | 200 |
170 | – | 0,992 | 0,992 | 0,993 | 0,993 | 0,993 | 0,994 | 0,994 | 0,994 | – | 190 |
180 | – | 1 | 1 | 1 | 1 | 1 | 1 | 1 | 1 | – | 180 |
Приложение 10
Значения тригонометрических функций для расчета силы T
j, ° | Знак | Значения | Знак | j, ° | |||||||
0,24 | 0,25 | 0,26 | 0,27 | 0,28 | 0,29 | 0,30 | 0,31 | ||||
0 | + | 0 | 0 | 0 | 0 | 0 | 0 | 0 | 0 | – | 360 |
10 | + | 0,215 | 0,216 | 0,218 | 0,220 | 0,221 | 0,223 | 0,225 | 0,227 | – | 350 |
20 | + | 0,419 | 0,423 | 0,426 | 0,429 | 0,432 | 0,436 | 0,439 | 0,442 | – | 340 |
30 | + | 0,605 | 0,609 | 0,613 | 0,618 | 0,622 | 0,627 | 0,631 | 0,636 | – | 330 |
40 | + | 0,762 | 0,767 | 0,772 | 0,777 | 0,782 | 0,788 | 0,793 | 0,798 | – | 320 |
50 | + | 0,886 | 0,891 | 0,896 | 0,901 | 0,906 | 0,912 | 0,917 | 0,922 | – | 310 |
60 | + | 0,972 | 0,976 | 0,981 | 0,985 | 0,990 | 0,995 | 0,999 | 1,004 | – | 300 |
70 | + | 1,018 | 1,022 | 1,025 | 1,029 | 1,032 | 1,035 | 1,039 | 1,043 | – | 290 |
80 | + | 1,027 | 1,029 | 1,030 | 1,032 | 1,034 | 1,036 | 1,038 | 1,040 | – | 280 |
90 | + | 1 | 1 | 1 | 1 | 1 | 1 | 1 | 1 | – | 270 |
170 | + | 0,943 | 0,941 | 0,939 | 0,937 | 0,936 | 0,934 | 0,932 | 0,930 | – | 260 |
160 | + | 0,864 | 0,858 | 0,854 | 0,851 | 0,847 | 0,844 | 0,840 | 0,837 | – | 250 |
150 | + | 0,760 | 0,756 | 0,751 | 0,747 | 0,742 | 0,737 | 0,733 | 0,728 | – | 240 |
140 | + | 0,646 | 0,641 | 0,636 | 0,631 | 0,626 | 0,620 | 0,615 | 0,610 | – | 230 |
130 | + | 0,524 | 0,519 | 0,513 | 0,508 | 0,503 | 0,498 | 0,493 | 0,488 | – | 220 |
120 | + | 0,395 | 0,391 | 0,387 | 0,382 | 0,378 | 0,373 | 0,369 | 0,364 | – | 210 |
110 | + | 0,265 | 0,261 | 0,258 | 0,255 | 0,252 | 0,248 | 0,245 | 0,242 | – | 200 |
100 | + | 0,133 | 0,131 | 0,129 | 0,127 | 0,126 | 0,124 | 0,122 | 0,121 | – | 190 |
180 | + | 0 | 0 | 0 | 0 | 0 | 0 | 0 | 0 | – | 180 |
Приложение 11
Соотношения между единицами системы СИ и МКГСС
Величина | Размерность | Переводной множитель | |
В СИ | В МКГСС | ||
Длина | м | м | – |
Площадь | м2 | м2 | – |
Объем | м3 | м3 | – |
Масса | кг | кгс·сек2/м | 1 кгс·с2/м ≈ 9,81 кг |
Время | с | сек | – |
Плотность | кг/м3 | кгс·сек2/м4 | 1 кгс·с2/м4 ≈ 9,81 кг/м3 |
Удельный вес | Н/м3 | кгс/м3 | 1 кгс/м3 ≈ 9,81 Н/м3 |
Теплота | Дж | кал | 1 кал = 4,187 Дж |
Теплоемкость | Дж/(кг·К) | ккал/(кгс·град) | 1 ккал/(кгс·град) = = 4187 Дж/(кг·К) |
Сила | Н | кгс | 1 кгс ≈ 9,81 Н |
Давление | Н/м2 = Па | кгс/см2 | 1 кгс/см2 = 98066,5 Н/м2 ≈ ≈ 0,0981 МН/м2 ≈ 0,098 МПа |
Работа | Дж | кгс·м | 1 кгс ·м ≈ 9,81 Дж |
Мощность | Вт | л.с | 1 л. с. = 735,499 Вт ≈ ≈ 0,7355 кВт |
Крутящий момент | Н·м | кгс·м | 1 кгс · м ≈ 9,81 Н · м |
Удельный расход топлива | г/(кВт·ч) | г/(л.с·ч) | 1 г/(л. с. · ч) ≈ 0,7355 г/(кВт·ч) |
Коэффициент теплопередачи | Вт/(м2·°С) | ккал/(м2 ·ч·град) | 1 ккал/(м2 · ч · град) ≈ ≈1,163 Вт/(м2 · °С) |
Динамическая вязкость | Н·с/м2 = Па·с | П | 1 П ≈ 0,1 Н·с/м2 ≈ 10–1 Па·с |
Кинематическая вязкость | м2/с | сСт | 1 сСт = 10–6 м2/с = 1 мм2/с |
Приложение 12. Пример оформления листа 1
Приложение 13. Пример оформления листа 2
Приложение 14. Пример оформления листа 3
БИБЛИОГРАФИЧЕСКИЙ СПИСОК
1. Колчин, А.И. Расчет автомобильных и тракторных двигателей: учебное пособие для вузов / А.И. Колчин, В.П. Демидов. 3-е изд. перераб. и доп. М.: Высшая школа, 2003. 496 с.
2. Яманин, А.И. Динамика поршневых двигателей: учебное пособие / А.И. Яманин, А.В. Жаров. М.: Машиностроение, 2003. 464 с.
3. Двигатели внутреннего сгорания: учебник: в 3 кн. Кн. 1. Теория рабочих процессов / под ред. В.Н. Луканина, М.Г. Шатрова. 2005. 478 с.
4. Двигатели внутреннего сгорания: учебник: в 3 кн. Кн. 2. Динамика
и конструирование / под ред. В.Н. Луканина, М.Г. Шатрова. 2005. 400 с.
5. Стуканов, В.А. Основы теории автомобильных двигателей и автомобиля: учебное пособие / В.А. Стуканов. М.: ФОРУМ:
НФРА-М, 2004. 368 с.
6. Закорин, Г.В. Тепловой и динамический расчеты двигателя: метод. указ. к курсовому проекту для студентов спец. 17.11 по дисциплине «Тракторы и автомобили» / Г.В. Закорин. Тверь: ТГТУ, 1996. 42 с.
7. Харламов, В.Е. Тепловой расчет двигателя: метод. указ.
к выполнению курсовых проектов по дисциплинам «Тракторы
и автомобили» и «Рабочие процессы, конструкция и основы
расчета тепловых двигателей и энергетических установок» для специальностей 190207 МОП и 190603 СТМ / В.Е. Харламов [и др.] Тверь: ТГТУ, 2008.
8. http://moscow.auto.ru
ОГЛАВЛЕНИЕ
Введение............................................................................................ | 3 |
Указания к оформлению пояснительной записки........................ | 4 |
1. ТЕПЛОВОЙ РАСЧЕТ ДВИГАТЕЛЯ......................................... | 5 |
1.1. Выбор и обоснование исходных данных к тепловому расчету..................................................................... | 7 |
1.2. Определение параметров состояния рабочего тела в характерных точках индикаторной диаграммы.................... | 11 |
1.3. Индикаторные и эффективные показатели двигателя...... | 15 |
1.4. Определение диаметра цилиндра и ход поршня............... | 16 |
1.5. Построение индикаторной диаграммы.............................. | 17 |
2. Скоростная характеристика....................................... | 23 |
2.1. Общие сведения..................................................................... | 23 |
2.2. Построение скоростной характеристики……………….... | 23 |
3. Кинематический расчет кривошипно-шатунного механизма....................... | 28 |
3.1. Общие сведения.................................................................... | 28 |
3.2. Расчет кинематических параметров................................... | 30 |
4. Динамический расчет кривошипно-шатунного механизма..................................................... | 33 |
4.1. Силы давления газов…………………………………..…... | 33 |
4.2. Приведение масс частей кривошипно-шатунного механизма……………………………………………………….. | 36 |
4.3. Построение развернутой индикаторной диаграммы……. | 38 |
4.4. Силы инерции……………………………………………... | 38 |
4.5. Суммарные силы, действующие в кривошипно-шатунном механизме…………………………………………... | 40 |
4.6. Суммарная диаграмма тангенциальных сил…………….. | 41 |
4.7. Силы, действующие на шатунные шейки коленчатого вала........................................................................ | 43 |
5. Расчет основных деталей двигателя.………….. | 50 |
5.1. Общие сведения................................................................... | 50 |
5.2. Расчетные режимы............................................................... | 51 |
5.3. Расчет деталей с учетом переменной нагрузки................ | 52 |
5.4. Расчет поршневой группы................................................... | 60 |
5.5. Расчет шатунной группы..................................................... | 76 |
ПРИЛОЖЕНИЯ.............................................................................. | 89 |
БИБЛИОГРАФИЧЕСКИЙ СПИСОК............................................ | 102 |
Харламов Вячеслав Евгеньевич
Крылов Константин Станиславович
Р асчет двигателя
Дата добавления: 2020-04-25; просмотров: 394; Мы поможем в написании вашей работы! |
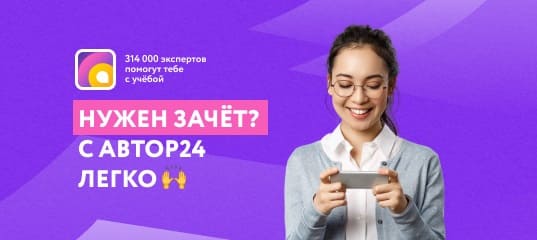
Мы поможем в написании ваших работ!