Построение скоростной характеристики
При построении внешних скоростных характеристик вновь
проектируемых двигателей иногда используют результаты теплового расчета, проведенного для нескольких режимов работы двигателя
с полной нагрузкой.
Однако этот метод расчета скоростных характеристик приме-
няют только при наличии полных экспериментальных данных по целому ряду параметров работы двигателя на частичных скоростных режимах.
С достаточной степенью точности внешнюю скоростную характеристику можно построить по результатам теплового расчета, проведенного для одного режима работы двигателя – режима максимальной мощности, с использованием эмпирических зависимостей.
Построение кривых скоростной характеристики проводится в интервалах:
а) для бензиновых двигателей – от nmin = 600…1 000 мин–1
до nmax = (1,05…1,20)·n N;
б) для дизелей – от nmin = 300…800 мин–1 до n н, где nн – частота вращения коленчатого вала при номинальной мощности.
Максимальная частота вращения коленчатого вала определяется условия-ми качественного протекания рабочего процесса, термическим напряже-нием деталей, допустимой величиной инерционных усилий и т. д.; мини-мальная – условиями устойчивой работы двигателя при полной нагрузке.
Скоростная характеристика двигателя строится в правой части второго листа. Она должна вписываться в размер формата А3 (рис. 3, 4).
Для расчета и построения кривых эффективной мощности и эффектив-ного удельного расхода топлива используются эмпирические формулы:
|
|
для дизелей
,
;
для карбюраторных двигателей
,
,
где N н – номинальная мощность; n н – номинальная частота вращения дизеля; ge. н – эффективный удельный расход топлива при N н;
Nmax – максимальная мощность; n н – максимальная частота вращения карбюраторного двигателя; ge. N – эффективный удельный расход
топлива при Nmax; nХ – расчетные (текущие) частоты двигателя;
а, b, с, a1, b1, c1 – опытные коэффициенты (табл. 4).
![]() ![]() | ![]() |
Рис. 3. Скоростная характеристика дизельного двигателя | Рис. 4. Скоростная характеристика карбюраторного двигателя |
Таблица 4. Значения опытных коэффициентов
Тип двигателя | а | b | c | a1 | b1 | c1 |
Дизели с неразделенной камерой сгорания | 0,87 | 1,13 | 1,0 | 1,55 | l,55 | 1,0 |
с вихревой камерой | 0,7 | 1,3 | 1,0 | 1,35 | 1,35 | 1,0 |
с предкамерой | 0,6 | 1,4 | 1,0 | 1,2 | 1,2 | 1,0 |
Карбюраторные двигатели | 1,0 | 1,0 | l,0 | 1,2 | 1,0 | 0,8 |
Крутящий момент (Н·м)
часовой расход топлива (кг/ч)
причем Nе. х измеряется в кВт, nх – в мин–1, gе. х – в г/кВт·ч.
Расчеты выполняются для 8…12 скоростных режимов двигателя
от nmin = 600…800 мин-1 до nн (n N) через 200…300 мин–1.
Для построения регуляторных ветвей характеристики дизеля следует задаться степенью неравномерности вращения двигателя (δ = 0,05…0,1) или принять ее по прототипу и определить максимальную частоту вращения:
|
|
Расход топлива на максимальной частоте вращения принима-
ется:
G т. х. х = (0,17…0,2)·G т. н.
В записке дается пример расчета для какого-либо одного скоростного режима. Результаты расчетов помещают в табл. 5.
Таблица 5. Результаты расчета скоростной характеристики
Параметры | Частота вращения (мин–1) | |||||
nх1 = nmin | nх2 | nх3 | … | nн (n N) | nmax | |
N e . x, кВт | ||||||
М е. х, Н·м | ||||||
g е. х, г/кВт·ч | ||||||
G T . X, кг/ч |
По данным расчетов строятся кривые скоростной характе-
ристики. Отмечаются точки М e. max, ge. min и соответствующие им
числа оборотов. Для дизеля должны быть построены регуляторные
ветви скоростной характеристики.
Коэффициент приспособляемости двигателя:
для карбюраторных двигателей k = 1,1…1,4; для дизелей k = 1,05…1,22.
Необходимо отметить, что приведенные выше эмпирические формулы и относительные внешние скоростные характеристики в ряде случаев дают результаты, существенно отличающиеся от действительных значений Ne и ge, полученных путем испытания двигателей на тормозных установках. Поэтому формулами и соотношениями допустимо пользо-ваться только в учебных целях.
|
|
При построении скоростных характеристик используют масштаб,
при котором 10 мм соответствует следующим величинам:
частота вращения при nmax, об/мин: | |
< 1 600 ……………………………………… | 100 |
1 600…3 200 ………………………………. | 200 |
> 3 200 ……………………………………… | 250 |
часовой расход топлива при Gт max, кг/ч: | |
< 10 ………………………………………... | 0,5 |
10…20 ……………………………………. | 1 |
> 20 ………………………………………… | 2 |
эффективная мощность при Ne max, кВт: | |
< 100 ……………………………………….. | 5 |
> 100 ……………………………………….. | 10 |
крутящий момент Me, Н·м …………………………… | 50 |
удельный расход топлива ge, г/кВт·ч ………………. | 50 |
3. Кинематический расчет
кривошипно-шатунного механизма
Общие сведения
В двигателях внутреннего сгорания возвратно-поступательное движение поршня преобразуется во вращательное движение коленчатого вала посредством кривошипно-шатунного механизма.
Кривошипно-шатунный механизм может быть центральным, когда оси коленчатого вала и цилиндров лежат в одной плоскости (рис. 5а),
или смещенным (дезаксиальным), когда оси коленчатого вала и цилиндров лежат в разных плоскостях (рис. 5б). Дезаксиальный механизм может быть получен также за счет смещения оси поршневого пальца.
|
|
В настоящее время в автомобильных и тракторных двигателях наибольшее распространение получил центральный кривошипно-шатунный механизм. Основные обозначения такого механизма приведены на рис. 5а: S х – текущее перемещение поршня (точка А – ось поршневого пальца); φ – угол поворота кривошипа (ОВ), отсчитываемый по оси цилиндра (А'О) в направлении вращения коленчатого вала по часовой стрелке (точка О обозначает ось коленчатого вала; точка В – ось шатунной шейки; точка А' – в.м.т.); β – угол отклонения оси шатуна (АВ) от оси цилиндра; ω – угловая скорость вращения коленчатого вала; R = OB – радиус кривошипа; S = 2R = A'A" – ход поршня (точка А" обозначает н.м.т.); Lш = AB – длина шатуна; λ = R/L ш – отношение радиуса криво-
шипа к длине шатуна (постоянная кривошипно-шатунного механизма);
R + Lш = A'О – расстояние от оси коленчатого вала до в.м.т.
В смещенном кривошипно-шатунном механизме (рис. 5б), в отличие от принятых обозначений для центрального механизма угол φ поворота кривошипа отсчитывают от прямой СО, параллельной оси цилиндра A'D
и проходящей через ось коленчатого вала, a S = A ' A " ≠ 2R. Дезаксиаль-
ный механизм характеризуется величиной относительного смещения
k = a/R = 0,05…0,15, где a = OD – величина смещения оси цилиндра относительно оси коленчатого вала.
Величины инерционных усилий, действующих в двигателе, зависят
от указанных выше размеров и их соотношений.
Установлено, что с уменьшением λ = R/ L ш (за счет увеличения L) происходит снижение инерционных и нормальных сил, но при этом увеличивается высота двигателя и его масса. В связи с этим в авто-мобильных и тракторных двигателях принимают λ = 0,22…0,33.
Для двигателей с малым диаметром отношение R/ L выбирают
с таким расчетом, чтобы избежать задевания шатуна за нижнюю
кромку цилиндра.
Минимальную длину шатуна и максимально допустимое значение λ без задевания шатуна за кромку цилиндра определяют следующим образом (рис. 6): на вертикальной оси цилиндра наносят центр коленчатого вала О, из которого проводят окружность вращения центра шатунной шейки радиусом R = S/2. Далее, пользуясь конструктивными размерами эле-ментов коленчатого вала, из точки В (центр кривошипа, находящегося
в н.м.т.) проводят окружность шатунной шейки радиусом r ш. ш,
из центра О – вторую окружность вращения крайней точки щеки
или противовеса радиусом r1:
для двигателей без противовесов r1 = R + (1,15…1,25)·r ш .ш.
с противовесами r1 = R + (l,3…l,5)·r ш. ш.
а б
![]() ![]() | ![]() |
Рис. 5. Схема кривошипно-шатунных механизмов: а – центрального; б – смещенного (дезаксиального) | Рис. 6. Схема кривошипно-шатунного механизма для определения минимальной длины шатуна |
Отступив на 6…8 мм вниз от точки С, проводят линию А – А перпендикулярно к оси цилиндра, определяющую минимально допустимое приближение нижней кромки поршня к оси коленчатого вала.
Пользуясь конструктивными соотношениями размеров поршня,
от линии А – А вверх наносят контур поршня, в том числе и центр поршневого пальца (точка А"). Расстояние между точками А" и В – минимальная длина шатуна L ш. min, по которой определяют λmax = L / L ш. min.
Чтобы шатун не задевал стенки, проверяют его траекторию
при движении поршня от в.м.т. до н.м.т. Для этого вырезают из кальки контур шатуна и перемещают его по чертежу так, чтобы центр поршневой головки шатуна перемещался по оси цилиндра, а центр кривошипной головки – по окружности радиуса R. При этом шатун не должен задевать нижнюю кромку цилиндра, которая может находиться на 10…15 мм выше нижней кромки поршня при его нахождении в н.м.т. (линия Е – Е).
В противном случае длину шатуна увеличивают или делают прорези
в стенках цилиндра для прохода шатуна.
На эту же схему наносят траекторию движения крайних точек кривошипной головки шатуна для определения габаритных размеров картера двигателя и размещения распределительного вала. Значение λ, принятое предварительно при построении индикаторной диаграммы, сохраняют при условии λ ≤ λmax.
Расчет кинематики кривошипно-шатунного механизма сводится
к определению пути, скорости и ускорения поршня. При этом при-нимается, что коленчатый вал вращается с постоянной угловой скоро-
стью ω (в действительности за счет непрерывно изменяющихся газовых нагрузок на поршень и деформации коленчатого вала ω ≠ const). Это допущение позволяет рассматривать все кинематические величины
в виде функциональной зависимости от угла поворота коленчатого вала φ, который при ω = const пропорционален времени.
Дата добавления: 2020-04-25; просмотров: 548; Мы поможем в написании вашей работы! |
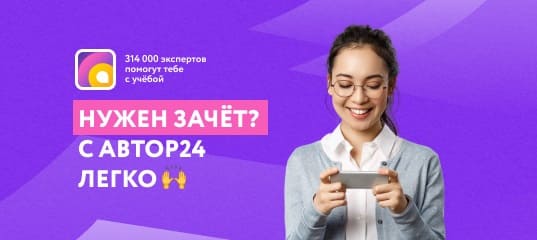
Мы поможем в написании ваших работ!