РЕКОМЕНДАЦИИ ПО ПРОЕКТИРОВАНИЮ
Расчетные нагрузки и схемы
Надежность, материалоемкость и другие показатели качества станков во многом зависят от правильной оценки действующих на его узлы и системы эксплуатационных нагрузок, принятых во внимание при проектировании. Продукционным станкам присущи универсальность операций, большой диапазон режимов обработки, возникновение длительных и кратковременных перегрузок при резании и переходных процессах. В связи с этим реально действующие нагрузки статического и динамического характера изменяются в очень широких пределах. Из-за многообразия конструктивных элементов и условий их работы достаточно точно определить используемые в различных видах расчета нагрузки весьма затруднительно. Поэтому на практике применяют методики, базирующиеся главным образом на статистических данных [9].
Основой выбора расчетных (эквивалентных) нагрузок для привода главного движения чаще всего служат номинальные крутящие моменты на элементах его конструкции (зубчатые и ременные передачи, валы и другие):
(8)
где Мнj – номинальный крутящий момент на j-м элементе, Н·м; N – эффективная мощность на шпинделе, кВт; прj– расчетная частота вращения элемента, мин–1; – коэффициент полезного действия кинематической цепи от элемента до шпинделя.
Так называемая расчетная частота вращения привода прдовольно широко используется как в металлорежущих станках общего назначения, так и в станках с ЧПУ при большом диапазоне регулирования скорости.
|
|
В проектах по типовой тематике для шпиндельной группы, а следовательно, и привода в целом ее значение находят на основе исходных данных по формуле
. (9)
В проектах для студентов с конструкторской специализацией величину пр вычисляют на основе зависимости (8), но без учета КПД. При этом значения максимальной эффективной мощности и номинального крутящего момента принимают по результатам моделирования режимов резания. Графически на картине распределения ЭХ
(см. рис. 4) положение пр определяется точкой пересечения линий, соответствующих этим характеристикам.
Полученное значение частоты корректируют до ближайшего стандартного (см. приложение 4). Только начиная с до nmaxобработку детали можно вести с использованием полной мощности привода, а ниже ее располагается диапазон регулирования с поддержанием постоянства крутящего момента на шпинделе. Использование расчетной частоты в приводах с дискретным регулированием скорости позволяет уменьшить их габариты и массу, а в станках с ЧПУ еще и конструктивную сложность узла.
|
|
Для промежуточных элементов ПГД за расчетные принимают их минимальные частоты, при которых передается полная мощность. Эти значения устанавливают по картине частот вращения.
Коэффициент полезного действия механической части привода при номинальной нагрузке определяют по формуле
(10)
где hi – КПД элемента (по данным справочной литературы или рекомендациям [29]); ai – число однотипных элементов; m – число элементов с разным КПД.
Установленная величина Мнj и является базовым значением нагрузки, которую применяют при расчете элементов конструкции с учетом специфики условий их работы в приводе.
Так, при оценке жесткости в качестве расчетной обычно используют номинальную: Мр = Мн.
Выбор нагрузки при выполнении вычислений на прочность более сложен. Разрушение элемента, в зависимости от величины и характера сил, физико-механических свойств материала, как правило, наступает либо из-за недостаточной статической прочности, либо вследствие усталости. При эксплуатации одни и те же детали работают в различных режимах переменного нагружения. Поэтому сначала нужно внимательно проанализировать весь спектр условий работы элемента с учетом его положения в природе и установить доминирующий режим. Каждому режиму соответствуют методика определения эквивалентной нагрузки и вид расчета.
|
|
В частности, промежуточные валы и связанные с ними элементы мало подвержены динамическим нагрузкам. В этом случае рекомендуется последовательность расчета, изложенная в работе [29]. По данной методике выбор расчетной нагрузки обусловлен предварительным вычислением коэффициента долговечности (k < 1)
k = kT kп, (11)
где kT – коэффициент срока службы, учитывающий длительность эксплуатации станка до капитального ремонта; kп – коэффициент режима нагружения, отражающий переменный характер нагрузки.
Полученную величину сопоставляют с критериями перехода к различным видам расчета на прочность.
Так, при k < kmin достаточно выполнить проверку деталей на статическую прочность, а за нагрузку принять Мр = Мн.
Если величина фактического коэффициента не выходит за пределы k min … kmax, то элементы привода подвергают расчету на малоцикловую выносливость в условиях ограниченного срока службы
Мр = Мн k. (12)
Расчет на неограниченный срок службы (до морального износа) выполняют, когда k > kmax. Искомую нагрузку либо определяют по предыдущему выражению, принимая k = kmax, либо вычисляют по формуле
|
|
(13)
где kу – коэффициент упрочнения материала детали.
Более объективную информацию о нагрузках на промежуточных элементах привода можно получить путем математического моделирования по методике, изложенной в работе [2].
При эксплуатации приводы главного движения станков испытывают динамические нагрузки, возникающие в результате неравномерного характера процесса резания, врезания инструмента в заготовку и других факторов. Эти нагрузки в основном воспринимаются выходными элементами. Для учета такого характера нагрузки при выполнении проверочных расчетов на усталостную прочность значения моментов, полученных по формулам (12) и (13), можно увеличить примерно на 30…50 %[15]. Большие значения принимают для оборудования с прерывистым процессом резания (фрезерного) и при значительном колебании припуска на заготовке, меньшие – для станков с достаточно стабильным процессом обработки (токарных), а также при наличии в приводе демпфирующих элементов: упругих, фрикционных муфт и других.
В период протекания процессов на холостом ходу станка при пуске, торможении и быстром реверсе шпинделя (особенно электродвигателем) в приводе также возникают большие динамические перегрузки. Они обусловлены инерционностью системы и отражаются, как правило, на условиях работы входных и выходных элементов. В целом частота таких воздействий зависит от назначения станка и его конструктивных особенностей. Обычно длительность их мала, а количество циклов нагружения электродвигателем невелико и эти перегрузки не оказывают заметного влияния на усталостную прочность. Поэтому данные динамические факторы чаще всего учитывают при проверочном расчете входных и выходных элементов на статическую прочность по максимальным (пиковым) нагрузкам. Их величину определяют как
Мр = Мн kа, (14)
где kА – коэффициент динамической нагрузки, величину которого обычно принимают в пределах 1,5…2,2, причем большие значения
соответствуют самым неблагоприятным сочетаниям конструктивных и технологических факторов (реверс электродвигателем, торможение противовключением двигателя).
При проектировании расчету подлежат практически все основные элементы конструкции привода: валы и подшипники, шпиндель, зубчатые и ременные передачи, базовые детали, органы управления. Все расчеты следует подкреплять соответствующими эскизами или схемами. При этом нужно иметь в виду, что независимо от вида расчета при прочих равных условиях точность результатов вычислений очень сильно зависит от адекватности принятых расчетных схем для элементов конструкции реальным условиям их нагружения в приводе. Переход от конструктивного исполнения к схеме требует формализации действующих сил, размеров и формы элементов. При этом объективно приходится делать ряд разумных упрощений, вследствие чего любой расчет становится достаточно приближенным. Очевидно, что грамотное составление схем с обоснованием принятых допущений позволяет избежать грубых ошибок в определении параметров элементов, которые могут быть выявлены только на стадии эксплуатации оборудования.
Передачи
Зубчатые передачи
Порядок расчета зубчатых передач приводов станков отличается от принятого в других отраслях машиностроения. Основная специфика состоит в том, что числа зубьев шестерен подбирают при кинематическом расчете. Поэтому задача сводится к определению модуля, который при неизменном межосевом расстоянии валов одинаков для всех передач группы. Для эвольвентных цилиндрических зубчатых передач выполняют, как правило, проектировочный и уточненный расчеты на контактную и изгибную выносливость, а также проверочный на действие максимальной нагрузки [2, 30]. Однако если в результате вычислений полученный коэффициент долговечности окажется меньше допустимого, а также при наличии тихоходных валов передачи подвергают расчету на статическую прочность. Причем модуль определяют только для одной – наиболее нагруженной передачи группы. Процесс вычислений довольно трудоемок, поэтому его рекомендуется выполнять на ЭВМ [2].
При подготовке исходных данных следует помнить, что принимаемые решения носят комплексный характер, так как закладывают основы надежности, технологичности изготовления и сборки привода, конструктивные особенности передач. Поэтому они должны быть очень продуманными. Так, желательно унифицировать номенклатуру материала передач и способы их термической обработки. Причем выбор технологии упрочнения тесно увязан с функциональным назначением деталей (подвижные или неподвижные), целесообразностью и практической осуществимостью последующей чистовой обработки. В постоянных передачах или передачах, получающих вращение, например, при помощи электромагнитных муфт, лучше использовать косозубые колеса. Подвижные в осевом направлении блоки допускают, как известно, только прямозубое зацепление. Значения коэффициентов долговечности, а также номинальных крутящих, эквивалентных и пиковых моментов находят по методике, описанной в предыдущем разделе пособия.
Полученные стандартные значения модуля одной передачи в каждой кинематической группе позволяют определить геометрические параметры остальных передач привода. Результаты сводят в таблицу.
Если по каким-либо причинам величина модуля отдельных групп, а следовательно, и размеры передач конструктора не устраивают, то ее обычно корректируют путем соответствующего изменения исходных данных и повторного расчета. На практике увеличение модуля производят просто по технологическим или конструктивным соображениям. Подобный прием осуществляют либо при унификации модуля для всего привода с целью сокращения номенклатуры режущего и мерительного инструмента, либо вынужденно – для увеличения межосевого расстояния.
Вопросы конструирования зубчатых колес изложены в работах
[6, 11, 15].
Ременные передачи
Ременные передачи относятся к виду передач гибкой связью и в ПГД применяются в качестве кинематических групп, занимающих различное конструктивное место. В зависимости от структуры привода они могут передавать вращение от электродвигателя на входной вал коробки скоростей, от выходного вала на автономный шпиндельный узел, а также возможны и другие варианты.
Выбор конкретного типа ременной передачи при прочих равных условиях производят с учетом его достоинств по сравнению с другими. В частности, передачи зубчатым ремнем обладают более высокой тяговой способностью, а клиноременные лучше гасят вибрации.
Критерием работоспособности клиновых ремней (нормальных, узких и поликлиновых) являются тяговая способность и долговечность, а зубчатых – усталостная прочность зубьев [30]. При выполнении проектных и проверочных расчетов указанных типов ременной передачи рекомендуется работа [2], в которой стандартные методики реализованы на ЭВМ.
Варианты конструктивного исполнения шкивов, способы их соединения с валом, в том числе с разгрузкой последнего, а также конструкции устройств для натяжения ремня и его защиты подробно рассмотрены в литературе [6, 9, 11].
Валы и опоры
Валы
При эскизном проектировании, когда размерные параметры валов еще неизвестны, разработку их конструкции начинают с приближенной оценки диаметров исходя из условия прочности только на один вид нагружения – кручение [30]
, (15)
где Па – условное допускаемое напряжение при кручении.
Рассчитав, таким образом, диаметры под приводным элементом, выявляют другие размеры, размещая на валах зубчатые колеса, муфты и подшипники. При этом валы получаются ступенчатыми, что диктуется, в том числе, и технологией их сборки. Значения диаметров выбирают стандартными, а их перепад – минимальным [4]. По существу, здесь закладывается основа конструкции валов, поэтому следует стремиться к ее рациональному упрощению. Для этого заранее продумывают наиболее приемлемые способы базирования и крепления элементов, по возможности избегая буртиков, резьбы, отверстий, одновременного выполнения шлицевых и цилиндрических поверхностей при малой длине вала. Неоправданное усложнение конфигурации предопределяет повышение трудоемкости изготовления, что нетехнологично, и появление излишних концентраторов напряжений, снижающих надежность вала.
Когда вопросы компоновки привода и определения габаритов коробки, элементов и механизмов решены, приступают к окончательной проработке конструкции валов с детализацией их формы и размеров, назначению посадок на соединения и производят расчеты.
Проверочному расчету подвергают все валы привода, однако при большом объеме вычислений, по согласованию с руководителем, можно ограничиться расчетом самых нагруженных. Как известно [2, 30], валы коробок передач рассчитывают на усталостную и статическую прочность, жесткость и виброустойчивость. Целесообразность применения того или иного вида расчета нужно обосновать, так как валы испытывают различные условия нагружения и в неодинаковой степени влияют на работоспособность привода.
Так, например, самостоятельные колебания передаточных валов коробок не играют заметной роли в динамике привода. А вот колебания входного и особенно выходного (или шпинделя) валов могут оказать решающее влияние на виброустойчивость. Неблагоприятное сочетание таких факторов, как высокая частота вращения, большие и неуравновешенные массы, значительная длина пролета или консоли, могут привести к возникновению резонанса. Методики, применяемые при оценке виброустойчивости, основаны на вычислении собственной частоты колебаний вала и сравнении ее с частотой вынужденных.
Деформация вала приводит к повышению контактных нагрузок в зубчатом зацеплении, опорах и т. д. Расчет на жесткость выполняют в том случае, если прогиб существенно влияет на работоспособность конструкции. Обычно это наблюдается при больших значениях отношения длины вала к диаметру. Величина допускаемых деформаций зависит от конкретных требований к конструкции. Рекомендуется придерживаться следующих допустимых значений: прогиб под шестерней – 0,01…0,03 модуля зацепления, угол наклона оси вала под шестерней – 0,001 рад, угол поворота вала в подшипниках – 0,0025…0,005 рад. Упругие перемещения определяют методами суперпозиции или начальных параметров.
Превалирующий вид разрушения валов – усталостный, поэтому расчет на выносливость является для них основным. Его ведут по длительно действующей нагрузке с определением коэффициентов запаса прочности в опасных сечениях.
Статическое разрушение вала наблюдается значительно реже и происходит под действием случайных кратковременных перегрузок. Расчет используют в качестве проверочного для предупреждения пластического деформирования с определением эквивалентных напряжений в опасных сечениях по одной из теорий прочности.
По итогам выполнения проверочных расчетов размеры валов, полученные на стадии эскизного проектирования, подлежат уточнению.
Как отмечалось выше, достоверность вычислений при прочих равных условиях во многом зависит от грамотно составленной расчетной схемы. Последовательность разработки схемы при расчете вала на прочность и критерии выбора опасных сечений рассмотрим на конкретном примере. Условная кинематическая схема привода изображена на рис. 10, а, пространственная компоновка валов (свертка) –
на рис. 10, б.
Построение схемы начинают с выявления конструктивного исполнения вала и анализа действующих на него сил. Допустим, что уточненному расчету подлежит второй вал коробки. На нем находятся прямозубые неподвижное колесо и подвижный блок. Очевидно, что в крайних положениях последнего изгибающий момент и нагрузка на опоры различны (при постоянстве крутящего момента). Проверке необходимо подвергнуть наихудший вариант нагружения вала, однако выявить его заранее не всегда представляется возможным. На практике корректным является только такой расчет, который учитывает все варианты нагружения. В то же время для сокращения трудоемкости, по согласованию с руководителем, допускается выбор одного – наиболее целесообразного варианта, который устанавливают на основе предварительного анализа.
а б
Рис. 10. Схема сил, действующих на вал
Предположим, что вал испытывает наиболее тяжелый режим нагружения в правом положении подвижного блока. Вычерчивают конструктивную схему вала (рис. 11, а) без излишней детализации тех элементов, которые не оказывают влияния на расчет.
Вал рассматривают как балку, лежащую на шарнирных опорах и нагруженную сосредоточенными силами и моментами. Нагрузки, действующие со стороны конца колеса z2 и шестерни z3 блока, устанавливают по компоновочной схеме (см. рис. 10, б). Для этого усилия в зацеплениях Q и P раскладывают на составляющие в двух взаимно перпендикулярных плоскостях. В результате приведения сил к геометрической оси вала на общей расчетной схеме (рис. 11, б) действие усилий в зацеплении заменяется действием их составляющих и крутящих моментов. Величину составляющих определяют по известным выражениям [30] соответственно через Мр (см. разд. 4.1), диаметр делительной окружности шестерен (для корригированных колес – диаметр начальной окружности), угол зацепления a (при косозубых передачах и угол наклона зуба b) и угол l, зависящий от компоновки валов.
Рис. 11. Конструктивная и расчетная схемы вала
После разработки общей расчетной схемы вала составляют схемы нагружения в каждой плоскости (не показано), выявляют реакции опор, строят эпюры изгибающих моментов (рис. 11, в, г), эпюры суммарного изгибающего (рис. 11, д) и крутящего (рис. 11, е) моментов и определяют опасные сечения.
Выбор опасного сечения является весьма важным этапом расчета, и на него необходимо обратить особое внимание. Количество сечений, в которых производится расчет, в общем случае зависит от конструктивного исполнения вала и характера его нагружения по длине. Критериями выбора сечений являются: 1) величина эквивалентной нагрузки, определяемая как результат совместного действия изгиба и кручения; 2) степень опасности самого сечения: наличие концентраторов напряжений (шпоночный паз, канавка, посадка, отверстие и другое), диаметральные размеры вала (масштабный фактор), шероховатость поверхности, вид термической обработки или упрочнения.
В рассматриваемом варианте анализ конструктивной схемы и эпюр моментов показывает, что в качестве опасных следует рассматривать сечения I–I и II–II.
Опоры
В опорах валов привода главного движения используются подшипники качения, методика выбора и расчет которых стандартизованы
[20, 23, 30].
Размеры опор определяют при построении продольной компоновочной схемы привода: размещая на валах связанные с ними элементы, по конструктивным соображениям предварительно выбирают типоразмер подшипников. При этом учитывают специфику условий их работы, принимая во внимание следующие факторы: величину (ориентировочно: по мощности или крутящему моменту), направление и характер действующих сил, быстроходность и требуемый срок службы. При проектировании опор валов, исключая тяжелонагруженные и особо быстроходные, рекомендуется отдавать предпочтение шарикоподшипникам легких серий и нормального класса точности.
Конкретный типоразмер подшипников устанавливают проверочным расчетом после определения реакции опор соответствующего вала. В общем случае расчет производят по двум критериям: статической и динамической грузоподъемности. Поскольку валы коробок скоростей сравнительно быстроходны, достаточно ограничиться последним условием, т. е. выполнением проверочного расчета подшипников на долговечность.
При окончательной доработке конструкции опор следует помнить, что валы имеют, как правило, большую длину, поэтому, во избежание их заклинивания за счет тепловых деформаций, одну из опор вала выполняют плавающей [3, 6, 9, 11, 23].
Шпиндельный узел
Шпиндельный узел (ШУ) – исполнительный орган ПГД – предназначен для вращения заготовки или инструмента в процессе осуществления технологических операций. Он является самой важной и ответственной частью привода да, пожалуй, и металлорежущего оборудования в целом, в значительной мере предопределяющей их работоспособность, так как его эксплуатационные параметры впрямую отражаются на качестве обрабатываемых деталей: форме, размерах и макронеровности поверхностей. Поэтому к ШУ предъявляется ряд обязательных требований, среди которых прежде всего следует выделить точность вращения, жесткость, виброустойчивость, теплостойкость и надежность фиксации инструмента или детали при условии их точного центрирования. В зависимости от типа и характера оборудования этот список может быть расширен, например, за счет быстроходности, присущей станкам с высокопроизводительными процессами резания, или автоматизации операций зажима и разжима заготовки, актуальных для станков-автоматов и полуавтоматов, а также станков с ЧПУ.
На практике реализация всех перечисленных и любых других специфических требований достигается главным образом путем разработки достаточно рационального варианта конструктивного исполнения ШУ и его последующей оптимизации. Однако поиск такого варианта среди множества альтернативных при условии обеспечения всех заданных требований представляет собой очень сложную проблему, поскольку при проектировании ШУ приходится опираться на взаимоисключающие по последствиям инженерные подходы. Разумеется, что критериями правильности принимаемых решений в этом случае служат только соответствующие проверочные расчеты.
Содержание методик расчета ШУ на точность, жесткость, виброустойчивость и теплостойкость подробно изложено в работах [2, 13, 15, 28]. В настоящем же пособии основное внимание акцентируется на вопросах конструирования узла и интерпретации результатов вычислений, вызывающих наибольшие затруднения при проектировании.
В общем случае узел состоит из собственно шпинделя (обычно полого вала), опор и приводного элемента. Реальное же конструктивное исполнение ШУ определяется многими факторами: типоразмером, классом точности, техническими характеристиками и степенью автоматизации станка, типом и местом расположения приводного элемента (а иногда и тормозного устройства), типом опор и способом их смазывания. В зависимости от структуры и компоновки привода он, являясь функционально выходным рабочим валом, может быть встроен в корпус коробки скоростей либо вынесен за ее пределы. Для передачи крутящего момента на шпиндель применяют зубчатые и ременные передачи, муфты. При этом приводной элемент может быть расположен как в межопорной, так и на задней консольной части шпинделя. С учетом величины и характера действующей нагрузки в каждой из опор ШУ устанавливают один или несколько одинаковых или разнотипных подшипников. Если корпус коробки скоростей имеет большие осевые габариты, то узел проектируют и трехопорным.
Таким образом, можно констатировать: конструкции ШУ весьма многообразны, что, естественно, вызывает потребность в различных модификациях соответствующих видов расчетов. С другой стороны, в результате анализа можно выявить несколько типовых конструктивных решений, охватывающих большинство вариантов ШУ с двумя опорами (рис. 12). Унификация конструктивных, а следовательно, и расчетных схем позволяет обеспечить единообразие в методическом подходе к проведению вычислений по разным критериям и снизить их трудоемкость.
Рис. 12. Типовые конструктивные схемы шпиндельного узла
Наиболее широко распространен вариант с одним или несколькими зубчатыми колесами, которые размещены между опорами шпинделя (рис. 12, а). Конструкция со шкивом ременной передачи, закрепленным на заднем конце шпинделя (рис. 12, б), используется в автономных ШУ станков для точной или многолезвийной обработки с целью гашения вибраций и повышения плавности вращения. Варианты с муфтой (рис. 12, в) или подвижным шлицевым соединением применяются в токарных станках с ЧПУ, а также во фрезерном оборудовании с механизмом выдвижения пиноли шпиндельной головки.
Вследствие сложности задачи, обусловленной широким диапазоном требований и объемом исходной информации, процесс проектирования узла разбивают на несколько этапов [5].
Прежде всего необходимо определить величину допустимой погрешности обработки заданных поверхностей на проектируемом оборудовании. Фактически речь идет об установлении поля допуска [D] на обработку и на этой основе той его части, которая присуща собственно ШУ. С учетом различия в тематике проектов используется два подхода к определению величины [D].
Первый. Единственным объективным и информативным параметром, который может быть использован в качестве отправной точки для достижения указанной цели, является шероховатость поверхностей. Однако из-за того, что при эксплуатации машин и механизмов различные сопряжения деталей отличаются многообразием условий работы, выявить достаточно обоснованные зависимости между точностью изготовления и шероховатостью поверхностей крайне трудно, поскольку для этого необходим очень большой объем статистических исследований. В то же время экспериментально найдены средние значения этих соотношений (рис. 13).
Таким образом, по заданному значению параметра Rа какой-либо поверхности можно установить погрешность обработки требуемого размера, но только в некоторых пределах. В свою очередь характер погрешностей станочной системы (следовательно, и ШУ) очень сильно зависит от методов и режимов резания. Если на оборудовании осуществляется преимущественно черновая обработка, то превалирующей погрешностью будет, естественно, упругая деформация. В станках, предназначенных для высокоскоростной обработки, а также при чистовом резании наиболее заметную роль играют геометрические и температурные погрешности. Кроме того, на основе
при известных размерах поверхности появляется возможность определять квалитет точности обработки [33], который, пусть и в неявном виде, характеризует соответствующий класс точности металлорежущего оборудования.
Рис. 13. Зависимость между параметром шероховатости
поверхности и погрешностью механической обработки
Второй. Эта методика используется в проектах, выполняемых по типовой тематике. Величина обусловлена классом точности, основным размерным параметром и характером осуществляемой на станке операции (черновой, получистовой и чистовой). При этом за размер обрабатываемой поверхности детали принимают половину основного параметра (диаметр для токарного и ширина стола для фрезерного оборудования). В учебных целях с известной долей условности будем считать, что для станков нормального класса точности в среднем можно ориентироваться на 11-й квалитет точности обработки, класса П – на 9-й, а класса В – на 7-й. Тогда, например, для станков класса точности Н значения
в зависимости от размеров обрабатываемой поверхности составляют [4]: в пределах 80…120 мм – 220 мкм, 120…180 мм – 250 мкм, а от 180 до 250 мм – 290 мкм. При том же размерном диапазоне поле допуска для оборудования повышенного класса точности принимает следующие значения: 87; 100 и 115 мкм, а высокого класса: соответственно 54; 63 и 72 мкм.
Главный итог первого этапа – определение допустимой погрешности, приходящейся на долю ШУ, значение которой в общем случае рекомендуется принимать не более 30 % от величины . Следует помнить, что помимо присущих конкретному ШУ погрешностей в поле допуска на обработку детали учтен и целый ряд других: упругие и температурные деформации элементов несущей системы, ошибка позиционирования, погрешность, связанная с износом инструмента, и другие.
На втором этапе выбирают тип опор (качения, скольжения: гидростатические или гидродинамические) в зависимости от допустимой погрешности обрабатываемых деталей [5, 33].
Затем (третий этап) на основе анализа условий эксплуатации ШУ разрабатывают его конструктивную схему с выбором типа, количества и способа размещения подшипников в передней и задней опорах. В станкостроении наибольшее распространение получили шпиндели на опорах качения, схемы которых в значительной мере унифицированы [5, 6, 9, 15, 20, 27]. Однако нужно иметь в виду то обстоятельство, что при размещении в опоре двух и более подшипников ее быстроходность, как показала практика, снижается примерно на 30 %.
На четвертом этапе приступают к определению главных размеров, каковыми являются (см. рис. 12) диаметр шейки шпинделя под передний подшипник dп, межопорное расстояние l и длина консольной части (вылет) а. Именно они оказывают весьма существенное и неоднозначное влияние на точность, жесткость и виброустойчивость узла, температуру опор и, кроме того, очень тесно взаимосвязаны: изменение хотя бы одного из них приводит к изменению сразу нескольких характеристик ШУ. Задача выбора их значений на данной стадии проектирования является весьма сложной. Однако, как показывает опыт станкостроения [5, 6, 15, 27], заданные критерии могут быть обеспечены, если основные размеры выдержать в пределах соотношений
l = (4…6) dп, . (16)
На практике эти соотношения реализуют, как правило, следующим образом: определяют приближенно dп по стандартизованному переднему концу (см. ниже), а затем – остальные размеры. Естественно, что все размеры в дальнейшем будут подвергнуты проверке и уточнению.
На пятом этапе выполняют эскизную компоновку узла, располагая на шпинделе связанные с ним элементы. При этом определяют все присоединительные размеры [6, 15] и уточняют основные, окончательно выбирают подшипники, а также материал шпинделя с соответствующей технологией упрочнения и конструкцию его переднего конца. Конфигурация последнего зависит от способа крепления инструмента или заготовки. Поскольку для этих целей применяют стандартные оснастку и инструмент, передние концы шпинделей различных типов станков также стандартизованы [5, 6, 8, 15, 36]. Форма и размеры внутренних поверхностей обусловлены наличием отверстия для крепления пруткового материала и конструкций зажимного устройства, встраиваемого в шпиндель [15, 27, 31, 33, 36], при этом минимальная толщина стенки полого вала не должна выходить за пределы порядка 6…8 миллиметров.
Только тогда, когда конструкция ШУ вычерчена в упрощенном виде (шестой этап), приступают к выполнению проверочных расчетов по тем критериям, которые характерны для создаваемого станка. В то же время к числу обязательных видов расчетов относятся проверка на точность вращения – радиальное и осевое
биения, а также на жесткость – радиальный прогиб
и осевое
смещение шпинделя в сечении его переднего конца. Напоминаем: суммарное значение всех погрешностей ШУ не должно выходить за установленное на первом этапе его проектирования ограничение. По итогам расчета осуществляют оптимизацию основных размеров узла и вносят необходимые изменения в его конструкцию.
Учитывая большую трудоемкость вычислительных операций, расчет целесообразно проводить на ЭВМ [2, 13].
И только после оптимизации основных размеров, на седьмом этапе, узел вычерчивают в окончательном варианте, прорабатывая конструкцию элементов для выборки зазоров и создания натяга в подшипниках, уплотнений, элементов системы смазывания и других. При этом следует стремиться к тому, чтобы сам шпиндель был по возможности конструктивно и технологически простым, с малым
количеством переходов диаметров, шпонок, резьб и канавок в межопорной части.
Корпуса коробок, пиноли
В общем случае возможны три варианта практической реализации требуемой степени подвижности (числа управляемых координат) привода, предопределяющих конструктивное исполнение его базовых деталей. При одной координате корпус коробки скоростей неподвижен – вращается шпиндель. Если же координат две, то второе движение (установочное или подача) осуществляется перемещением корпуса по направляющим станины (стойки, траверсы) либо, когда необходимо обеспечить высокую точность позиционирования, путем выдвижения пиноли (гильзы) со шпинделем на малый ход при неподвижном корпусе. Причем пиноль совершает поступательное, а шпиндель, помещенный внутри нее, – вращательное движение. Подобное устройство привода применяется при выполнении сверлильных и расточных операций, в частности на фрезерных станках. Таким образом, корпус коробки скоростей является базовой деталью привода и элементов несущей системы станка, а пиноль – базовой деталью шпиндельного узла.
Если привод снабжен пинолью, то при конструировании корпуса определяют ее основные размеры (длину, наружный и внутренний диаметры), которые, в свою очередь, зависят от параметров шпинделя. Пара корпус–пиноль фактически представляет собой цилиндрические направляющие [5, 31, 36]. При проектировании следует предусмотреть устройства для перемещения (обычно червячно-реечная передача) и фиксации (чаще всего клеммные). Эти механизмы унифицированы, поэтому их на чертежах детально не прорабатывают. На пиноли приходится значительная часть упругих деформаций станочной системы, в связи с чем на практике их подвергают проверочному расчету на жесткость. При прочих равных факторах она существенно уменьшается по мере выдвижения, поэтому максимальный ход (вылет) пиноли, как правило, ограничивается величиной, в полтора раза превышающей ее наружный диаметр.
Корпуса коробок довольно металлоемки и имеют сложную конфигурацию. Чаще всего их изготавливают методом литья обычно из серого чугуна, реже – дешевых марок стали. Сварные конструкции широкого применения не получили из-за своей дороговизны.
Очевидно, что при проектировании корпуса необходимо учитывать требования принятой технологии. Для отливок следует стремиться обеспечить как можно более простую форму, чтобы не усложнять литейную модель (количества разъемов, стержней и другое), не создавая в корпусе замкнутых полостей. Толщина наружной стенки детали должна быть одинаковой. Ее минимальную величину, выраженную в миллиметрах, находят по формуле
, (17)
где L , B , H – габаритные размеры, соответственно длина, ширина и высота корпуса коробки, м.
Для повышения жесткости корпуса применяют дополнительные ребра перпендикулярно к стенкам, а для концевых опор коротких валов – перегородки. Толщину внутренних стенок и ребер принимают равной порядка 0,7…0,8 от толщины наружной. Во избежание появления коробления, трещин и внутренних напряжений стенки должны иметь плавные переходы. Рекомендации по типовым случаям сопряжения стенок, радиусам закруглений и литейным уклонам приведены в работах [9, 22]. Для установки подшипников в стенках выполняют бобышки (утолщения), большую часть которых при значительной ширине опоры смещают внутрь. Выступающую с наружной стороны корпуса часть бобышки (платик) используют для крепления крышек опор, электродвигателей (при фланцевом исполнении) и других элементов.
В этом случае поверхность платиков подлежит чистовой обработке. Крышки проектируют также и потайными, т.е. заподлицо с наружной поверхностью корпуса – более эстетичный вариант. Корпуса конструируют, как правило, неразъемными, что предопределяет осевой монтаж валов и технологию чистовой обработки отверстий. При обработке соосных отверстий набором резцов, закрепленных на расточной оправке, их диаметры в направлении подачи инструмента иногда приходится уменьшать. Чтобы облегчить сборку привода и расточку отверстий, в корпусе выполняют специальные технологические окна (лючки). Для регулировки механизмов привода предусматривают соответствующую крышку, обычно привинчивающуюся. В легких и средних станках горизонтальные крышки при частых регулировках конструируют на шарнирах откидными. При этом следует продумать изоляцию от попадания пыли и вытекания масла. Кроме того, не следует забывать об отверстиях для маслоуказателя и слива смазочной жидкости.
Для лишения коробки скоростей всех шести степеней свободы ее устанавливают на базовую деталь станка, фиксируют в требуемом положении и притягивают болтами (винтами). Сопрягаемая поверхность может быть плоской, тогда на соответствующей стенке корпуса выполняют карманные или фланцевые платики, либо может иметь форму направляющих скольжения. При стыковке по плоскости фиксацию коробки обеспечивают коническим штифтами или шпонками, а при использовании направляющих – их конструкцией. Форма и размеры опорной поверхности, число болтов, штифтов и их размещение устанавливают по конструктивным соображениям. Диаметр винтов можно предварительно определить по эмпирическим нормам [30].
В неподвижных коробках расчету подвергают групповые резьбовые соединения и контактные деформации привода. Вычисления производят по типовым методикам [15, 27, 30] с построением расчетной схемы узла, пример оформления которой для случая с плоским стыком показан на рис. 14.
При составлении уравнений статики в качестве активно действующей нагрузки учитывают силы резания, натяжения ременной передачи и тяжести узла. Здесь крайне важно правильно установить величину, направление и координаты точки приложения сил. Как правило, при выполнении вычислений наибольшие затруднения вызывает вопрос определения веса привода Gп и координаты центра тяжести. Очевидно, что вес привода равен весу входящих в него элементов конструкции
(18)
где Gj – вес отдельных элементов (собственно коробка скоростей, электродвигатель, шкив ременной передачи, оснастка, насос и другое), Н.
Рис. 14. Расчетная схема корпуса коробки скоростей
Вес отдельных элементов рассчитывают как
, (19)
где Wj – объем элемента, м3; gj – удельный вес материала, Н/м3; kj – коэффициент заполнения формы, который в зависимости от функционального назначения и конструктивного исполнения элемента принимают в пределах 0,3…0,7.
После определения этого параметра, например, для коробки скоростей центр тяжести располагают примерно в геометрическом центре элемента. Для покупных изделий вес устанавливают по каталогам или справочной литературе, поступая в отношении центра масс аналогичным образом. Тогда координаты центра тяжести привода, например, в направлении оси Х находят по формуле
(20)
где х j – координата центра тяжести j-го элемента конструкции привода, м.
В том случае, когда система получается статически неопределимой, для выявления реакций опор приходится делать некоторые допущения. Например, считают, что момент внешних сил относительно одной из осей координат распределяется между опорными поверхностями пропорционально их размерам.
Существо расчета резьбовых соединений заключается в определении потребной силы затяжки каждого болта, выявлении наиболее нагруженного и проверке давления в стыках, в результате чего уточняют количество и размеры крепежных элементов, а также площадь базовых поверхностей. Полученные контактные давления служат основой для расчета упругих деформаций узла.
На базовой поверхности подвижных коробок скоростей отображают принятую форму направляющих скольжения или качения. Их конструкции стандартизованы [3, 15, 27]. Тяговое устройство не разрабатывают, однако предлагают решение по его реализации. Если корпус коробки осуществляет только установочные перемещения, необходимо предусмотреть специальный механизм его зажима на время обработки деталей.
Направляющие скольжения рассчитывают по типовым методикам на контактные давления и деформации, а качения – на контактную прочность и жесткость [15, 27]. Получаемые при этом расчетные схемы во многом аналогичны приведенной выше.
Система управления
Программные и непрограммные системы управления (СУ) станками, несмотря на известные отличия, в общем случае содержат: задающий орган, собственно механизм управления, состоящий из передаточного устройства и исполнительного органа, а в необходимых случаях – элементы обратной связи и индикации.
Цепь управляющей команды в зависимости от степени автоматизации оборудования может быть реализована на базе различных видов энергии: механической, электрической, пневмогидравлической, но чаще всего их комбинаций. Это предполагает многообразие возможных решений. Задающий орган (рукоятка, кнопка, командоаппарат, система ЧПУ и другое) представляет собой начальное звено настройки параметров исполнительных движений. Его команды проходят по цепи механизма управления (передач шестерня-рейка или винт-гайка, двигатель, кулачковый механизм), и посредством исполнительного органа, являющегося конечным звеном (вилка, поворотный камень и т. п.), осуществляется управление объектом (зубчатое колесо, муфта, шкив).
На конструктивные варианты СУ сильно влияет также принятый способ переключения частот вращения шпинделя и осуществления его останова (торможения) и реверса. В ПГД применяют два разных способа:
· путем осевого смещения по валам зубчатых блоков и полумуфт, в результате чего они выходят из одного зацепления и включаются
в другое;
· путем передачи крутящего момента зубчатым колесам, находящимся в постоянном зацеплении при помощи электромагнитных и гидравлических фрикционных муфт.
Первый способ получил наибольшее распространение в универсальных станках, хотя чаще способы используют комплексно. Реверсирование и торможение можно осуществить также электродвигателем.
Непрограммные СУ бывают с ручным (РУ) и дистанционным (ДУ) управлением. И каждую из них можно выполнить с применением индивидуальных, групповых и централизованных механизмов [15, 25, 27].
Таким образом, конструктивное исполнение СУ, т.е. совокупность элементов, устройств и механизмов, реализующих требуемую цепь команды управления, зависит от многих факторов. Поэтому при проектировании СУ следует проанализировать варианты альтернативных решений в рамках задания и выбрать наиболее рациональный.
При РУ подробной конструктивной проработке подлежат все звенья цепи управления: от задающего до исполнительного органа с максимальным использованием типовых устройств [11, 15, 30]. РУ характерно тем, что рукоятки и кнопки располагаются непосредственно на корпусе коробки скоростей в удобной для обслуживания зоне. Причем их количество должно быть минимальным. ДУ подразумевает значительную удаленность зоны обслуживания от узла, поэтому задающие органы должны быть размещены вне привода (аналогично программному управлению – ПУ), например, на выносном пульте управления станком. В системах ДУ и ПУ разрабатывают конструкцию только собственно механизма управления.
Проектирование СУ выполняют поэтапно в такой последовательности. Количество объектов управления (ОУ) и перечень необходимых команд управления определяют на стадии формирования технического предложения. При эскизной компоновке узла в первую очередь решают вопрос о месте панели управления на корпусе коробки в соответствии с эргономическими требованиями и выделяют зоны под размещение передаточных механизмов и исполнительных органов СУ с учетом положения ОУ, обеспечивая кратчайшую длину цепей управления.
Затем ищут конструктивные решения этих цепей и разрабатывают схему управления приводом.
При наличии в схеме механических связей (рис. 15) производят кинематический расчет цепей по методике [30]. Его цель – увязка перемещений ЗО и ИО, т. е. определение геометрических параметров элементов СУ: длин рычагов и углов поворота, передаточных отношений передач, диаметров кулачков, ходов подвижных блоков и другое.
Рис. 15. Кинематическая схема системы управления
Предварительную конструктивную проработку элементов СУ осуществляют в упрощенном виде, решая одновременно вопросы их взаимной стыковки.
В кинематических группах, состоящих из двух подвижных блоков, обязательно предусматривают блокировочные устройства [11].
Фрикционные муфты подбирают по номинальному крутящему моменту [4, 15, 24], обращая особое внимание на соответствие их размеров посадочным диаметрам валов и габаритам присоединяемых зубчатых колес. В СУ, построенных с использованием электрических и гидравлических устройств, продумывают вопросы размещения соответствующей аппаратуры: датчиков, конечных выключателей и другой. При этом необходимо иметь в виду, что большинство элементов современных СУ унифицированы [4, 11, 25, 31].
Компоновка СУ служит базой для составления расчетной схемы (рис. 16) и выполнения проверочных силовых расчетов [25, 30].
Рис. 16. Расчетная схема системы управления
Основной расчет сводится к определению усилий на ЗО и сравнению их с допустимыми. При этом КПД цепи управления в зависимости от ее сложности принимают в пределах 0,75...0,95, а необходимые осевые усилия для переключения подвижных блоков в первом приближении – 20...30 Н. Кроме того, при вертикальной компоновке привода осуществляют проверку на надежность фиксации блоков и рукояток, а при внецентровом приложении внешних нагрузок на подвижные
детали – на отсутствие защемляющего эффекта. На заключительной стадии проектирования все элементы СУ подлежат полной конструктивной проработке.
Система смазывания
В практике станкостроения применяют системы смазывания индивидуального и централизованного типа. Первые обеспечивают смазку элементов и механизмов только одного узла, т.е. они автономны. Во втором случае ее осуществляют от единой системы станка.
Приступая к разработке системы, прежде всего выявляют точки смазывания, а затем выбирают наиболее рациональные материал и способ его подачи к трущимся поверхностям.
Подшипники качения смазывают пластичным и жидким материалом, зубчатые передачи и муфты – только жидким.
Одним из основных критериев выбора способа смазывания опор является параметр их быстроходности [15, 20, 23]. Консистентную смазку обычно используют, когда по условиям работы специального охлаждения опор не требуется (при окружных скоростях до 4,5 м/с), при вертикальной компоновке привода и в ШУ, изолированных от зубчатых колес. К ее основным достоинствам можно отнести хорошую смазывающую способность, высокие защитные свойства от коррозии, экономичность и другие, а к недостаткам – плохую охлаждающую способность и потребность в тщательном уходе: периодическом осмотре опор, пополнении и смене материала. Жидкие смазочные материалы позволяют организовать замкнутые системы проточного типа. Последние реализуются на базе многих известных способов: циркуляционного, впрыскиванием, капельного (по фитилю или через дозатор), постоянным или периодическим масляным туманом. Несмотря на довольно значительный иногда расход материала и возможность утечек (что диктует потребность установки защитных и уплотнительных устройств), жидкие смазки, кроме создания достаточно надежного
эффекта смазывания, хорошо отводят теплоту, уносят продукты износа и практичны в эксплуатации.
В связи с повышенными требованиями особое внимание следует уделять вопросу смазки опор ШУ, предусматривая в необходимых случаях независимую от других элементов привода систему.
Зубчатые передачи и муфты смазывают способом поливания: под давлением и без него (через резервуар с отверстиями, помещенный в верхней части корпуса коробки) и крайне редко разбрызгиванием
(при окружных скоростях шестерен от 1 до 6 м/с).
Таким образом, имеется достаточно большое количество вариантов практической реализации системы смазывания привода. Их необходимо проанализировать и выбрать оптимальный, по возможности избегая применения разных марок масел.
Как автономные, так и централизованные системы обеспечивают принудительный характер движения жидкости: после очистки (фильтрации) она вновь подается к смазочным точкам. Первый тип систем, как правило, включает насос, фильтры, распределитель, трубопроводы, маслоуказатель, пробку для слива жидкости, уплотнения и защитные шайбы, а при необходимости и другие устройства: клапаны давления, дозаторы, обратные клапаны, манометры, теплообменник. Конструкция централизованных систем значительно упрощается за счет сокращения номенклатуры гидроаппаратуры [32].
Проработку конструкции смазочной системы начинают с составления принципиальной гидравлической схемы, пример оформления которой показан на рис. 17.
После этого на основе уравнения теплового баланса определяют потребный расход масла для смазывания всех точек привода [35].
По нему находят производительность насоса, на основе которой
подбирают всю аппаратуру в соответствии с разработанной схемой
и рассчитывают объем резервуара для масла [4, 9, 15, 32, 35].
Вязкость и марку смазочного материала устанавливают по рекомендациям [15].
Рис. 17. Гидравлическая схема смазочной системы:
1, 4 – фильтры; 2 – насос; 3 – клапан давления; 5 – масло-
охладитель; 6 – маслораспределитель; 7 – дроссель;
8 – резервуар
На чертеже привода в целях упрощения разводку трубопроводов от маслораспределителя к смазочным точкам не показывают. В централизованных системах следует предусмотреть элементы для подвода и отвода жидкости, а также устройства для контроля поступления ее в корпус коробки скоростей.
Компоновка привода
Очевидно, что поиск решения данной задачи нужно вести, основываясь на ранее разработанной концепции привода, включавшей в том числе и вопрос eго предварительной компоновки. При компоновке привода, кроме обеспечения его работоспособности, решают и ряд других задач. К основным из них можно отнести: технологичность
изготовления корпуса, сборки и обслуживания привода; компактное
заполнение пространства коробки деталями; пропорциональность размеров; эстетичность и другие. В результате компоновки уточняют внешний вид привода и место положения электродвигателя, решают вопросы размещения органов управления и устройств контроля смазки на корпусе и другое.
Как правило, компоновку осуществляют в такой последовательности: строят продольную и поперечную компоновочную схемы, определяют ориентировочно контуры коробки, вписывают в отведенные места элементы смазочной системы и механизмы управления, вносят необходимые коррективы, выполняют проверочные расчеты деталей, уточняют принятые конструктивные решения и приступают к окончательной доработке чертежа, включая построение внешнего вида привода. Разумеется, что это лишь примерный план, тогда как в действительности приходится неоднократно возвращаться на том или ином этапе к ранее принятым и, казалось бы, оптимальным техническим решениям. Поэтому необходимо тщательно продумывать все решения и предвидеть их возможные последствия.
Разработку чертежа общего вида привода начинают с построения продольной компоновочной схемы – продольного разреза (развертки) с упрощенным изображением входящих в него деталей (рис. 18). На развертке осевые линии всех валов лежат в одной плоскости, т.е. она фактически представляет собой конструктивное отображение кинематической схемы привода. Сначала наносят межосевые расстояния передач, затем диаметры валов под приводными шестернями и размещают на них зубчатые колеса, муфты, шкивы, подшипники. Все элементы вычерчивают упрощенно: показывают только контуры деталей, допускается рассматривать их прозрачными, штриховые линии можно не наносить. Размерным параметром, подлежащим оптимизации, здесь обычно является длина корпуса коробки. Ее получают в результате компактного расположения на валах связанных с ними деталей. Однако возможны варианты, когда этот размер лимитирован либо оптимальным межопорным расстоянием ШУ, либо рамками общей компоновки станка. Тогда задача сводится к вписыванию всех механизмов в требуемые осевые габариты, для чего приходится уменьшать осевые размеры элементов, применяя известные способы, например, разделение блоков колес на составные части, рациональное их конструирование и другие [6, 11, 22].
Рис. 18. Компоновочные схемы привода
Параллельно, еще до конца не выполнив продольную схему, приступают к построению поперечной компоновочной схемы. Она отображает поперечный разрез (свертку) привода, т. е. реальное положение валов в пространстве. В принципе этих разрезов должно быть столько, сколько необходимо для полного понимания конструкции привода. Но на данном этапе в целях упрощения можно выполнять наложенные сечения. Комплексный подход к разработке схем необходим для исключения ошибок, чтобы все конструктивные решения были увязаны. При этом стремятся минимизировать площадь, занимаемую передачами, так как она во многом определяет два других размера коробки: ширину и высоту. Однако следует помнить, что минимизация параметров свертки может привести к ухудшению условий обеспечения развертки и наоборот.
Построение поперечного разреза ведут с учетом компоновки станка в такой примерно последовательности: намечают базовую плоскость, привязывают к ней ось шпинделя, принимают решение по варианту размещения валов и определяют положение панели управления по отношению к опорной стороне корпуса и оси шпинделя.
Если ось шпинделя параллельна базовой поверхности стенки корпуса, то на поперечном разрезе привода ее намечают на таком удалении, чтобы имелась возможность выдержать основной размерный параметр станка. При анализе вариантов расположения валов в пространстве рассматривают целесообразность применения одной из трех возможных схем: ломаная линия, соединяющая центры валов, имеет форму «змейки» или «скобы» либо валы размещают в одну линию. Последний вариант характерен для вертикальной компоновки, когда опорная поверхность перпендикулярна оси шпинделя (как правило, сверлильные и фрезерные станки). При свертывании намечают положение панели управления, смещая валы с подвижными блоками колес по возможности ближе к ней. Кроме того, следует обратить внимание на положение приводной по отношению к шпинделю шестерни, поскольку от этого зависят величина прогиба его переднего конца и нагрузка на опоры [15], а также на местонахождение входного вала при фланцевом креплении электродвигателя, смещая его к задней стенке корпуса. По окончании этой работы прочерчивают контур корпуса, оставляя пространство для вспомогательных устройств.
Рис. 19. Компоновочные схемы систем управления и смазки
Затем осуществляют конструктивную проработку в схемном виде устройств смазывания и механизмов управления одновременно на продольном и поперечных разрезах (рис. 18, 19). Как правило, это приводит к потребности уточнения контура корпуса. При назначении зазора между внутренней стенкой корпуса и внешними поверхностями вращающихся деталей придерживаются рекомендаций, приведенных в работах [11, 30].
По итогам компоновочных решений на схемах проставляют все необходимые для расчетов размеры. И только после выполнения проверочных расчетов приступают к окончательной доработке конструкции привода.
ТРЕБОВАНИЯ К ОФОРМЛЕНИЮ
Дата добавления: 2020-04-25; просмотров: 196; Мы поможем в написании вашей работы! |
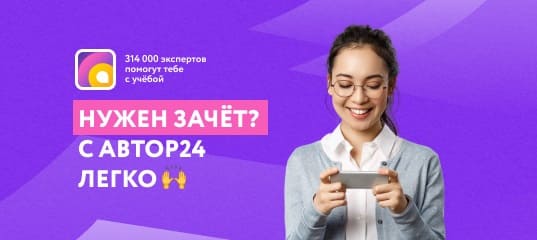
Мы поможем в написании ваших работ!