Синтез структурно-кинематической схемы
Разработку кинематической структуры оборудования рекомендуется осуществлять в такой последовательности:
1) определение характера и количества исполнительных движений (ИД) рабочих узлов (блоков);
2) принятие принципиального решения по пространственной ориентации, виду движения и относительному положению основных узлов;
3) построение внутренних и внешних связей ИД;
4) размещение органов настройки параметров ИД;
5) анализ полученных структурно-кинематических схем для каждой обрабатываемой поверхности детали и их корректировки;
6) синтез обобщенной кинематической структуры оборудования и ее оптимизация.
Как известно [12, 17], ИД узлов образуется на основе элементарных движений (ЭД): вращательных – В и поступательных – П. Структура последних для принятых схем обработки заданных поверхностей детали уже была выявлена на предыдущем этапе проектирования. Количество и состав ИД определяются их функциональным назначением: формообразующие, установочные, делительные, вспомогательные или управления, а также потребностью в согласовании некоторых ЭД с целью обеспечения какого-либо сложного ИД. Помимо этого здесь же устанавливают и размерность всех движений: мин–1, мм/мин, мм/об и другие.
Поиск на концептуальном уровне оптимального решения по относительному положению, характеру движения и пространственной ориентации основных блоков оборудования означает, что по существу речь идет уже о предварительной, начальной стадии разработки компоновочной схемы станка. Прежде всего принимают мотивированное решение по ориентации оси шпинделя в декартовой системе координат, устанавливая таким образом ее абсолютное положение в пространстве: горизонтальное, вертикальное или наклонное. Очевидно, что при значительной длине детали более предпочтительна горизонтальная компоновка, к достоинствам же вертикальной можно отнести сокращение занимаемой станком производственной площади, а также удобство обслуживания рабочей зоны оператором и улучшение условий для автоматизации процессов загрузки заготовок и смены инструмента. Далее анализируются различные варианты по взаимному положению и виду движения основных узлов. Иначе говоря, теперь необходимо придать каждому из узлов оптимальную степень подвижности, рационально распределив ее между блоками инструмента и заготовки. Информацию о всех возможных вариантах желательно систематизировать и с целью наглядности представить ее, например, по типу табл. 10.
|
|
Таблица 10
При этом руководствуются рекомендациями [1, 7], среди которых можно выделить такие:
· узлам со значительной массой сообщают перемещение не более чем по одной координате;
|
|
· вертикальное или наклонное расположение направляющих облегчает удаление стружки, но ухудшает условия смазывания;
· не следует чрезмерно усложнять конструкцию блоков, отдавая явный приоритет в степени подвижности одному из них;
· перемещение в вертикальной плоскости реализуется более легким блоком и другие.
В результате рассмотрения различных вариантов и их оценки по ряду критериев, в том числе с привлечением материалов обзора литературных источников, принимают наиболее рациональный. Это окончательное решение фиксируют в виде структурной формулы компоновки с записью в коде ISO [1, 7]. Одновременно осуществляется выбор типов устройств для загрузки заготовок и смены инструмента [27], а также устанавливается весь комплекс вспомогательных движений, необходимых для их функционирования.
Любое ИД обеспечивается в общем случае отдельной кинематической группой, включающей обычно источник и преобразователь энергии, рабочий орган, внутренние и внешние связи с органами настройки параметров ИД, преобразователи вида движений и другие устройства. При графическом изображении этих элементов СКС следует придерживаться условных обозначений, приведенных в приложении 3. Соединения между элементами выполняют тонкими сплошными линиями, характеризующими внутренние и внешние связи.
|
|
Построение СКС для единичной поверхности детали начинают с определения вида энергии (электрическая, пневмогидравлическая, физиологическая) и ее преобразователей (электродвигатель, гидроцилиндр и другие), необходимых для реализации каждого ИД, исходя из того, что:
– в станках с ЧПУ все приводы автономны;
– в универсальном оборудовании токарной и сверлильной групп, как правило, применяют общий электродвигатель для приводов главного движения и подач, а у фрезерных, шлифовальных и станков других типов эти приводы независимы и т. п.
При нанесении внутренних и внешних кинематических связей нужно помнить, что назначение первых состоит в обеспечении траектории ИД, а вторых – в передаче мощности от преобразователя энергии к рабочим органам. В простых ИД траектория создается кинематическими парами в виде подшипников или направляющих, а в сложных при достижении указанной цели образуется уже кинематическая цепь. Положение начала внешних связей определяется размерностью параметра скорости ИД и направлением основного потока мощности:
|
|
· если скорость обусловлена временем (мин–1, м/с, мм/мин), то внешняя связь берет начало от индивидуального или общего преобразователя энергии для данной кинематической группы; в противном случае, когда она зависит от движения узлов (мм/об заг., мм/об инстр., мм/ход), связь ответвляется от соответствующего блока;
· точка подключения внешней связи к внутренней должна находиться как можно ближе к тому рабочему органу, движение которого осуществляется с большей скоростью и требует повышенного расхода мощности.
В выявленных кинематических связях размещают органы настройки регулируемых параметров, преобразователи вида движений, коммутаторы, сумматоры, логические блоки и другое. Для удобства выполнения работы рекомендуется предварительно составить специальную таблицу, в которую для каждой обрабатываемой поверхности заносят требуемые элементарные и исполнительные движения, а также настраиваемые параметры последних. С целью исключения ошибочных решений на данном этапе необходимо принимать во внимание следующие соображения:
· протяженность внутренней связи должна быть минимальной, так как в ней, как правило, размещают только один орган – настройки траектории F сложного ИД;
· основной поток мощности не должен проходить через орган настройки траектории, иначе будет снижена точность образования формы поверхности и усложнена конструкция блока;
· органы настройки остальных параметров ИД (скорости V, направления N, пути L и конечной точки K) желательно устанавливать во внешних связях;
· каждый параметр ИД целесообразно настраивать только одним органом так, чтобы перестройка любого параметра не вызывала подналадки других;
· если кинематические группы имеют общее исполнительное звено (преобразователь движения, направляющие), то они присоединяются при помощи сумматора (при условии параллельной работы групп) или через коммутатор (при последовательной работе).
После синтеза СКС для принятых методов обработки заданных поверхностей детали следует провести анализ полученных решений с целью внесения соответствующих уточнений и корректировок. Теперь уже необходимо четко определиться с конкретным типом устройств, которые скрываются за условными обозначениями элементов СКС, поскольку известно, что любой из них в зависимости от функциональной принадлежности на практике может быть реализован, как правило, гаммой механизмов с присущими им достоинствами и недостатками. Рассмотрение СКС с этой позиции позволит совместить ряд органов ИД, разнесенных по времени, сократить число источников энергии и кинематических цепей, а также принять другие рациональные решения. Отметим, что выбранные таким образом устройства и механизмы подлежат в дальнейшем полной конструктивной проработке.
Рис. 1. Структурно-кинематическая схема токарного станка с ЧПУ
На завершающем этапе на базе частных СКС синтезируют уже обобщенную кинематическую структуру проектируемого станочного комплекса в целом. Здесь по вполне объективным причинам может возникнуть потребность в окончательной доработке полученной СКС с выбором оптимального варианта. Пример оформления СКС показан на рис. 1.
Компоновка
Не вызывает сомнений тот факт, что компоновка оказывает заметное влияние на многие показатели качества проектируемого оборудования: возможность автоматизации технологического цикла обработки деталей; удобство наладки, обслуживания, хранения, транспортирования и монтажа; массу; занимаемую производственную площадь; соответствие архитектуры и внешнего вида требованиям технической эстетики и другие.
Часть концептуальных вопросов по компоновке станочного комплекса должна быть решена на предыдущем этапе параллельно с синтезом его СКС. Следующим шагом в этом направлении является более детальная проработка проблемы – поиск приемлемых вариантов компоновки на уровне основных исполнительных узлов и оборудования в целом.
Анализ возможных вариантов и их оценку рекомендуется сопровождать упрощенными схемами. При решении указанной задачи придерживаются определенной последовательности с учетом функционального назначения узла. Раскрытие содержания некоторых вопросов, возникающих по ходу реализации одной из таких методик, иллюстрируется на примере компоновки привода главного движения вертикально-фрезерного станка.
Сначала выбирают способ соединения корпуса привода с элементами несущей системы станка с учетом определенной ранее степени подвижности блоков (рис. 2). Возможные варианты построения привода с неподвижным стыком (контактом) сопрягаемых поверхностей показаны на рис. 2, а. Затем рассматривают различные способы установки электродвигателя (рис. 2, б).
Потом решают вопросы размещения вспомогательных систем станка и постов (пультов, панелей) управления. Последние располагают в соответствии с требованиями эргономики и безопасности обслуживания оборудования.
На заключительной стадии разработки компоновки выявляют ориентировочные габаритные размеры узлов, элементов несущей системы и станочного комплекса в целом. Отправной точкой при установлении приближенных размеров всех компонентов оборудования обычно служат максимальные габариты детали и антропометрические требования к техническим объектам. Так, например, ширина заготовки, обрабатываемой на фрезерном станке, закономерно предопределяет соответствующий размерный параметр стола, который, в свою очередь, накладывает ограничения на положение оси шпинделя (рис. 3) относительно привалочной (базовой) поверхности корпуса коробки скоростей (размер В). Размер А, оказывающий существенное влияние на устойчивость шпиндельной бабки в горизонтальной плоскости, принимают обычно не менее чем (1,2…1,5)В. Размерные параметры H и L назначают в соответствии с правилом «золотого сечения» [18, 35] на основе значения А. Габариты элементов несущей системы устанавливают с учетом параметров рабочего поля станка и необходимой собственной жесткости [1, 7].
Рис. 2. Варианты компоновки привода главного движения:
1 – стойка, 2 – коробка скоростей, 3 – электродвигатель, 4 – ременная передача
Рис. 3. Размерные параметры коробки скоростей
Обращаем внимание на то обстоятельство, что проектирование имеет характер эвристического итерационного процесса. Поэтому на каждом из рассмотренных этапов вполне вероятен вынужденный возврат к ранее принятым и, казалось бы, весьма рациональным решениям с целью их уточнения и корректировки.
Окончательный вариант компоновки оформляют в виде сомографической схемы (ортогональные проекции) с выделением зон сенсомоторного поля оператора и нанесением размеров, отражающих эргономические характеристики станочного комплекса. Кроме того, желательно также построение аксонометрического изображения оборудования с цветовым решением основных элементов в зависимости от их функционального назначения.
РАЗРАБОТКА КОНЦЕПЦИИ ПРИВОДА
Дата добавления: 2020-04-25; просмотров: 225; Мы поможем в написании вашей работы! |
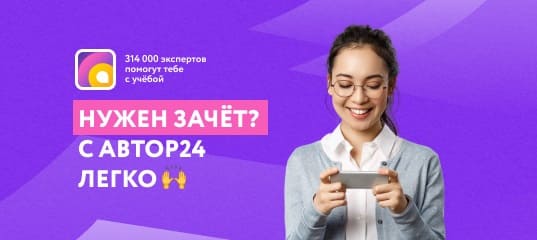
Мы поможем в написании ваших работ!