Обоснование технических характеристик
Проблема обоснования технических характеристик (ТХ) относится к числу наиболее важных и сложных, качество решения которой во многом предопределяет технико-экономические показатели проектируемого оборудования.
Несмотря на довольно широкий перечень параметров, свойственных любому оборудованию машиностроительного производства, его эффективность в эксплуатации зависит прежде всего от мощности приводов, допустимых значений крутящих моментов и тяговых усилий на исполнительных органах, а также пределов изменения скорости перемещения последних. В то же время тематикой КП предусмотрена разработка конструкции только одного из приводов – главного движения, поэтому указанный круг ТХ сужается до трех доминирующих, в том числе и по отношению к оборудованию в целом: мощности электродвигателя Nд, номинального крутящего момента Мн и предельных значений частоты вращения шпинделя – nmin и nmax .
В настоящее время при обосновании этих основных ТХ оперируют различными методами, на выбор которых влияют степень универсальности оборудования, объем исходной информации и требуемая точность расчета. Для станков общего назначения и специализированных из-за большого разнообразия условий обработки, вследствие чего
они функционируют в широком диапазоне скоростей и нагрузок, наиболее целесообразный путь определения ТХ – математическое моделирование.
При выполнении КП решение проблемы обоснования ТХ осуществляется на базе методологии, теоретические основы и практические положения которой приведены в работе [26]. В соответствии с заложенными в ней принципами моделированию подлежат распределения эксплуатационных характеристик (эффективная мощность резания N, частота вращения n и крутящий момент М на шпинделе) для реализуемых на станке технологических операций с поэтапной корректировкой положения их границ до момента установления значений собственно ТХ. Следует подчеркнуть, что в отличие от технических по существу одноименные с ними эксплуатационные характеристики (ЭХ) являются переменными по величине и зависят от условий обработки, но в процессе функционирования оборудования не должны выходить за рамки его ТХ.
|
|
При осуществлении расчетов на ЭВМ требуется подготовить исходные данные для отдельных технологических операций, под которыми, как отмечалось выше, подразумевается обработка какой-либо поверхности детали при неизменном режиме. Таким образом, для каждого из шести условий обработки (количество поверхностей, помноженное на число видов материала заготовки) необходимо сформировать следующую исходную информацию.
|
|
1. Предельные значения размеров заданных поверхностей, определяющие диаметральные параметры детали dд или инструмента dи, устанавливают на базе диапазона варьирования габаритов заготовки и специфики принятого метода обработки (точение, сверление, фрезерование, шлифование и т. д.).
2. Предельные значения скорости V и силы P резания (или момента М) определяют аналитическими методами либо по эмпирическим формулам [33, 35], либо по общемашиностроительным нормативам [21]. При выборе величины поправочных коэффициентов уравнений особое внимание обращают на их соответствие заданным условиям обработки. В частности, материал заготовки принимают только с учетом функционального назначения детали на основе известных рекомендаций [4, 35 и др.]. То же правило действует и в отношении режущего инструмента: в зависимости от физико-механических свойств материала заготовки устанавливают наиболее предпочтительный материал одной группы, например титано-кобальтовый твердый сплав [33]. Кроме того, следует иметь в виду, что при оценке силовых возможностей большинства технологических процессов оперируют силой резания (обычно понимая под ней главную составляющую), но для некоторых методов обработки (сверление, зенкерование, развертывание) целесообразно использовать крутящий момент.
|
|
3. Вероятность реализации технологической операции на проектируемом станке есть не что иное, как произведение частных вероятностей обработки соответственно какой-либо поверхности и одного из материалов детали. Суммарная вероятность всех условий должна равняться единице, в противном случае программой предусмотрено уточнение полученных значений.
4. Значения коэффициентов корреляции K1 и K2. Напоминаем еще раз, что первый из них учитывает связь скорости V и силы Р резания c диаметральными параметрами поверхности (т.е. для этих двух факторов он одинаков), а второй – между моментом М и частотой n детали или инструмента (всегда имеет отрицательное значение).
Процесс вычислений на ЭВМ носит циклический характер. На первом этапе моделируются дифференциальные функции распределений отдельных ЭХ: n , M и N с наложенными на них ограничениями. Полученные предельные значения ЭХ подлежат корректировке исходя из того, что частота вращения шпинделя должна быть согласована со стандартным рядом (см. приложение 4), а момент и эффективная мощность резания округлены до ближайших чисел. Однако при смещении границ ЭХ необходимо осознанно представлять себе последствия, которые кроются за теми или иными решениями, ведь по существу они впрямую отражаются на технологических возможностях и конструктивной сложности привода, да и станочной системы в целом. На базе уточненных элементарных распределений строится затем общая картина распределения ЭХ, типовой вид которой показан на рис. 4.
|
|
Не исключено, что полученная картина также подвергнется трансформации. Так, например, проектировщика может не удовлетворять объем работ Q, выполняемых на станке с максимальной производительностью (в процентах ко всему объему), который заключен в рамках границ ЭХ. Осуществляя корректировку на основе указанных соображений, принимают взвешенное решение по поиску оптимальной области условий эксплуатации станка. Положения границ отдельных ЭХ на окончательном варианте картины фиксируют значения уже собственно технических характеристик станка.
Рис. 4. Картина распределения эксплуатационных характеристик
(Q =86.4 %)
3.2. Анализ конструкций приводов
станков-аналогов
Напоминаем, что после ознакомления с комплексом требований технического задания именно с этого вопроса начинается работа над курсовым проектом по типовой тематике, т.е. с изучения и анализа принципа действия и конструкции привода главного движения известных на настоящий момент станков аналогичного по функциональному назначению (или прототипа). Кроме рекомендуемой литературы [1, 3, 10, 19, 31, 34, 35], желательно использовать обзоры международных станкостроительных выставок, проспекты фирм, каталоги и другие материалы.
При анализе акцентируют внимание не только на общих, схемных решениях, но и на более конкретных, определяющих специфику конструктивного исполнения изделия. В частности, следует непременно рассмотреть вопросы компоновки как оборудования, так и самого привода, а также его структуру и кинематику. Иначе говоря, анализу подвергают положение узла в станке и его координатных осей в пространстве; способ соединения корпуса коробки скоростей с элементами несущей системы; состав привода; размещение электродвигателя относительно входного вала; системы смазывания зубчатых передач, муфт, опор валов и шпинделя, а также способы настройки частоты вращения, реверса и останова последнего. Изучая конструкции элементов и механизмов приводов, выявляют применяемые в них оригинальные и типовые технические решения.
В результате комплексного анализа исходных данных к проекту и различных вариантов альтернативных решений, их сравнительной оценки с учетом конструктивных особенностей разрабатываемого и существующих узлов формируется общая концепция привода с наиболее рациональным вариантом структуры. Принятые решения в обязательном порядке следует подкреплять необходимыми схемами и рисунками.
3.3. Кинематический расчет
Цель расчета – разработка структуры привода главного движения (ПГД), распределение передаточных отношений между кинематическими группами и их оптимизация с последующим подбором числа зубьев колес и шестерен всех передач и диаметральных размеров шкивов. Завершается расчет построением наиболее рационального варианта картины частот вращения и кинематической схемы привода.
Для студентов специальности 151002 при решении этого вопроса исходной служит информация, полученная ранее на этапах синтеза СКС станка (способ регулирования скорости главного движения) и предварительной компоновки привода, а также при обосновании ТХ (предельные значения частоты вращения шпинделя и максимальное значение эффективной мощности резания). Для студентов, разрабатывающих привод по типовой тематике, комплекс исходных данных, приведенных в техническом задании, несколько иной. Поэтому на начальном этапе выполнения кинематического расчета возникают некоторые нюансы.
Однако в любом случае прежде всего необходимо определить следующие недостающие исходные данные:
1) вычисляют мощность привода Nп по формуле
(1)
где N – эффективная (номинальная) мощность резания, кВт; h – коэффициент полезного действия (КПД) механической части, который на стадии разработки технического предложения в зависимости от предполагаемой конструктивной сложности привода принимают равным 0,75 … 0.85.
2) диапазон регулирования привода Dпсвязан с максимальной – nmax и минимальной – nmin частотами вращения шпинделя выражением
(2)
В зависимости от наличия в исходных данных значений тех или иных характеристик привода по этой формуле и находят искомую характеристику.
Далее кинематический расчет обладает спецификой, свойственной принятому способу регулирования скорости исполнительного органа.
При ступенчатом (дискретном) регулировании целесообразно придерживаться определений последовательности.
1. Находят число ступеней скорости Z привода
(3)
где j - знаменатель геометрического ряда частот вращения.
В соответствии с положениями ГОСТ 8032-84 и рекомендациями нормали станкостроения Н11-1 наиболее предпочтительными значениями знаменателя для ПГД являются 1,26; 1,41 или 1,58 [18].
В проектах по типовой тематике для станков с ручным и дистанционным управлением требуемое значение знаменателя ряда выражено в неявном виде – через допустимую потерю скорости резания (табл. 11).
Таблица 11
![]() | 10 | 20 | 30 | 40 | 50 |
j | 1,12 | 1,26 | 1,41 | 1,58 | 2,0 |
2. После анализа возможных вариантов принимают наиболее приемлемый тип кинематической структуры (нормальная множительная, с совпадением части ступеней скорости, с многоскоростным электродвигателем, сложенная, с двумя значениями j или их комбинация), записывая ее в виде соответствующей структурной формулы. Причем последняя должна быть полной, развернутой, т.е. содержать все зубчатые и ременные передачи, включая одиночные. Данный этап расчета является весьма ответственным, ибо здесь приходится одновременно учитывать целый комплекс разнообразных факторов: Z, j, Dп, характер распределения n по графику ее результирующей функции (для специальности 151002), потребность в реверсировании исполнительного органа (зависит от особенностей технологических операций, выполняемых на станке), класс точности оборудования (отражается, например, на необходимости гашения вибраций при передаче вращения на шпиндель), компоновку привода и т.д.
При поиске оптимального решения целесообразно руководствоваться следующими рекомендациями [14, 15, 27, 35]:
· уменьшение габаритов и массы привода достигается за счет смещения групп с большим числом передач к входному валу, увеличения редукции в группах по мере их приближения к шпинделю, совпадения конструктивного и кинематического вариантов;
· применение многоскоростных электродвигателей существенно упрощает механическую часть привода;
· осевые размеры коробки скоростей можно уменьшить применением связанных колес, установкой одиночных передач между отдельными кинематическими группами, разделением тройных и четвертных блоков на части;
· энергетические потери заметно снижаются при использовании сложенных структур;
· улучшение качественных характеристик шпиндельного узла (жесткость, виброустойчивость, теплостойкость) обеспечивается при минимальном количестве зубчатых передач в конструктивно последней группе, а повышение плавности его работы – при использовании в этой роли ременной передачи;
· реверс и торможение электродвигателем ухудшают динамические характеристики привода и другое.
3. С учетом выявленных j и Z из ряда предпочтительных чисел (приложение 4) выписываются стандартные значения частот вращения шпинделя от nmax до nmin . При этом возможна корректировка ранее вычисленного Dп.
4. На базе принятой структурной формулы привода определяют их характеристики. Каждая из них, как известно, численно равна количеству ступеней скорости, полученных за счет переключения предшествующих групп.
5. Приступают к построению картины частот вращения привода, типовой фрагмент которой показан на рис. 5. Она позволяет наглядно представлять последствия принимаемых решений и очень удобна для определения передаточных отношений i (отношение частот вращения ведомого элемента к ведущему) всех передач, поскольку при графоаналитическом методе их величина подчиняется зависимости
(4)
где mj – количество интервалов сетки картины, перекрываемых лучом j-й передачи, причем знак «+» отражает повышающую (мультипликация), а «–» – понижающую (редукция).
Задавая угол наклона лучей и искусственно перераспределяя количество интервалов сетки между одиночными и групповыми передачами, конструктор тем самым фиксирует не только передаточные отношения отдельных передач, но и характер их изменения для привода в целом. Очевидно, что эта процедура является многовариантной.
В то же время при построении картины учитываются известные ограничения, накладываемые на передаточные отношения зубчатых и ременных передач. Так, для прямозубых колес . Тогда количество интервалов, занимаемых лучами понижающих и повышающих передач, не должно превышать предельных значений, указанных в табл. 12.
Рис. 5. Графическое изображение передач на картине
частот вращения
Таблица 12
Количество интервалов передачи | Знаменатель геометрического ряда j | ||||
1,12 | 1,26 | 1,41 | 1,58 | 2,0 | |
Понижающей | 12 | 6 | 4 | 3 | 2 |
Повышающей | 6 | 3 | 2 | 1,5 | 1 |
Ограничения для ременных передач различного типа и рекомендуемые параметры стандартных шкивов приведены в литературе [2, 4], но нужно помнить, что их максимальный диаметр, по крайней мере, не должен выходить за пределы габаритов привода.
Получение реальной картины без наличия конкретного источника движения конечно же невозможно. Однако сейчас осуществить его выбор довольно затруднительно, да и нежелательно. И вот почему. По данным каталогов на электрооборудование или другой справочной литературы, например [15], можно предварительно установить тип одно- или многоскоростного асинхронного электродвигателя последних модификаций пока только по такой технической характеристике, как мощность Nд. Причем по условию, которое не вызывает сомнений: Nд Nп. Что же касается выбора значения другой важной характеристики двигателя: частоты вращения ротора (вала), то этот вопрос требует дополнительной проработки.
Дело в том, что технико-экономические показатели привода в значительной мере зависят от соотношения частот вращения входного вала и шпинделя (рис. 6). В целом повышение частоты вращения электродвигателя приводит к увеличению его КПД и cos j, уменьшению габаритов и массы. Вместе с тем рост частоты вращения промежуточных валов механической части вследствие интенсификации процессов трения негативно отражается на энергетических потерях и долговечности (в том числе и за счет роста количества циклов нагружения) привода, а также уровне шума (эксперименты показывают: увеличение окружной скорости вращения зубчатых колес в два раза при прочих равных условиях сопровождается ростом уровня шума примерно на 7 децибел, что ощущается как почти двукратное его усиление). Кроме того, в этом случае минимальные передаточные отношения приближаются к своим предельно допустимым значениям, что приводит к возникновению известных проблем при конструктивном оформлении привода.
Обеспечение требуемого комплекса показателей качества механической части привода на стадии кинематического расчета достигается путем оптимизации передаточных отношений групп передач. В общем случае последние выбирают таким образом, чтобы линия , соединяющая середины интервалов частот вращения на выходе групп, была близка к прямой.
Наиболее применяемый на практике вариант картины при условии сопоставимости частоты вращения электродвигателя и максимальной частоты вращения шпинделя показан на рис. 6, а.
Оптимальным соотношением редукции к мультипликации обладает структура, изображенная на рис. 6, б. Она получается тогда, когда понижающие передачи перекрывают две трети диапазона каждой кинематической группы ( ), а повышающие соответственно оставшуюся треть –
. Такой вариант улучшает условия зацепления зубьев шестерен, обеспечивая довольно низкий уровень шума и вибраций. Для него также характерно, пусть и монотонное, но все же нарастание максимальной частоты вращения валов.
Картина с симметричным расположением передач в группе
(рис. 6, в) свойственна приводу с максимальной степенью унификации зубчатых колес. При одинаковом модуле в трех рассматриваемых вариантах данный обладает наименьшими радиальными габаритами.
В то же время очевидно, что здесь все передачи «загоняются» в область низких частот и соответственно больших крутящих моментов со всеми вытекающими отсюда последствиями.
Таким образом, в результате сравнительного анализа и оценки альтернативных вариантов картин частот вращения привода на основе изложенных соображений, отдавая приоритет тому или другому технико-экономическому показателю либо пытаясь совместить требования по ряду критериев, и устанавливают наиболее рациональное значение второй характеристики электродвигателя: асинхронной частоты вращения nд.
Методика кинематического расчета при плавном (бесступенчатом) регулировании скорости выглядит несколько иначе.
1. В первую очередь на основе имеющейся на данный момент исходной информации осуществляют мотивированный выбор способа регулирования скорости рабочего органа привода и типа устройства для его реализации. Этот вопрос является чрезвычайно важным и принципиальным для студентов с конструкторской специализацией, поскольку качество его решения во многом предопределяет не только конструктивное исполнение привода, но и технологические возможности оборудования в целом.
Как известно, в ПГД металлорежущих станков используются два способа: механический и электрический. Первый осуществляется при помощи фрикционных вариаторов в паре с нерегулируемым асинхронным электродвигателем, а второй – двигателями постоянного тока или асинхронными с частотным регулированием. Каждый из них имеет достоинства и недостатки, а следовательно, и сферу применения.
Среди основных технических характеристик вариаторов и двигателей наибольший интерес представляют две: мощность Nд и диапазон бесступенчатого регулирования скорости при условии обеспечения ее постоянства DбN.
Фрикционные вариаторы поддерживают стабильность мощности, хотя и на довольно низком уровне, во всем рабочем диапазоне, но обладают вследствие скольжения при перегрузках нежесткой механической характеристикой, а также узким диапазоном регулирования
Dв= DбN, величина которого обычно не выходит за пределы значений 4...6. В настоящее время эти устройства достаточно редко используют в ПГД станков малого и среднего типоразмера.
В электродвигателях постоянного тока и асинхронных обычно применяется так называемое двухзонное регулирование скорости: от нуля до номинальной частоты пд ном вращение вала осуществляется с передачей постоянного крутящего момента (диапазон DдМ), а далее – до максимальной частоты пд max – с обеспечением постоянства мощности (диапазон DдN = DбN). Двигатели способны развивать большую мощность, однако характер ее изменения, предельные значения DдN и DдМ существенным образом зависят как от их типа, так и режима работы. Они нашли наибольшее распространение в приводах станков с ЧПУ.
Типовой вид зависимости мощности от частоты вращения (так называемая нагрузочная или механическая характеристика) на разных режимах работы асинхронного двигателя приведен на рис. 7. Здесь необходимо обратить внимание на следующие обстоятельства. У этого типа двигателей на практике чаще всего используются два основных режима функционирования: непрерывный, т. е. без пауз (кривая 1), и повторно-кратковременный – с периодическим отключением разной длительности (кривая 2).
Рис. 7.Нагрузочная характеристика двигателя
Как видно из рисунка, режим работы двигателя очень сильно влияет не только на максимально развиваемый им уровень мощности Nд, но и на диапазон поддержания ее стабильных значений DдN . В частности, при больших нагрузках в режиме чередования пуска-останова у некоторых моделей после достижения значения максимальной частоты вращения с Nд= const на характеристике наблюдается спад мощности разной крутизны.
Следует отметить, что при выборе электродвигателя с выполнением непременного условия Nд Nп использовать при курсовом проектировании всю величину диапазона DдN характеристики вовсе не обязательно.
Шпиндельные узлы современных многоцелевых токарных станков с ЧПУ, как правило, помимо главного вращательного обеспечивают также движение подачи и установочное перемещение. Поэтому приводы главного движения таких станков целесообразно оснащать электродвигателями постоянного тока, обладающими перед асинхронными одним несомненным преимуществом: значительно большим DдМ.
По виду их механическая характеристика аналогична характеристике асинхронного двигателя при непрерывном режиме функционирования (зависимость 1).
Выбор типовой конструкции фрикционных вариаторов, по данным специальной литературы, при наличии технических требований обычно затруднений не вызывает. Что же касается электрического способа регулирования, то в соответствии с тенденцией развития станкостроения рекомендуется применять различные модели асинхронных электродвигателей передовых отечественных и зарубежных фирм, например «SIMENS» или «FANUK», оснащенных стандартным комплектом преобразовательной и управляющей аппаратуры [37]. То же относится и к двигателям постоянного тока, выбор которых следует производить либо по специализированным каталогам, либо по данным учебной литературы, например [15].
В процессе принятия решения по выбору той или иной модели двигателя необходимо тщательно проанализировать по каталогу их технические характеристики и в первую очередь нагрузочную.
2. Определяют число ступеней скорости механической части привода по выражению
(5)
где DпN – диапазон регулирования привода при постоянной мощности.
На основе полученного значения Z неизбежно приходится рассматривать такую альтернативу. При округлении его до ближайшего целого числа в большую сторону осознанно закладывается перекрытие части диапазона регулирования привода: некоторые частоты вращения валов и шпинделя будут дублироваться по разным кинематическим цепям. В противном случае (при округлении в меньшую сторону) заранее программируется разрыв. Однако это совсем не означает, что в некотором интервале частот вращение шпинделя не обеспечивается: оно осуществляется, но с передачей постоянного момента. Хотя подобный прием довольно часто используется в ПГД станков с ЧПУ (упрощается конструкция механической части), следует помнить, что наличие разрыва свидетельствует о потере производительности обработки в соответствующем интервале частот диапазона регулирования.
Принятие того или иного решения обусловлено спецификой выполняемых на станке технологических операций, отражением которой для студентов специальности 151002 является характер результирующей функции распределения частоты вращения, полученной при обосновании ТХ. Фактическую величину перекрытия или разрыва можно вычислить после определения передаточных отношений передач привода, в то же время нужно иметь в виду, что относительное снижение мощности в месте разрыва не должно превышать 20 %.
3. Составляют развернутую структурную формулу привода. Учитывая, что число ступеней скорости механической части привода невелико (обычно не более четырех), в качестве структуры чаще всего используют нормальную множительную или сложенную.
4. Находят передаточные отношения передач. В кинематических структурах с плавным регулированием скорости для этой цели применяют, как правило, аналитический метод, тогда картина частот вращения играет чисто иллюстративную роль. Однако ради упрощения задачи более предпочтительным, на наш взгляд, является использование комбинации аналитического и графоаналитического методов. Привлечение эффекта наглядности позволяет быстро и адекватно оценить результаты принимаемых решений.
При оформлении картины сетку желательно наносить с малым шагом, например j = 1,12 или 1,26. Применение стандартного ряда дает возможность зафиксировать установленные предельные значения частот вращения двигателя и шпинделя, а в дальнейшем и промежуточных валов.
Сначала вычисляют минимальное передаточное отношение Imin привода
(6)
где k – количество передач кинематической цепи с наибольшей редукцией.
Затем полученное численное значение Iminискусственно разбивают на сомножители, величина каждого из которых и отражает конкретное значение передаточного отношения соответствующих понижающих одиночных и групповых передач кинематической цепи (количество этих передач, естественно, равно k). Причем на первом этапе целесообразно задавать предельные минимальные значения зубчатых и ременных передач. Если их произведение будет больше Imin, то структурную формулу корректируют, вводя дополнительно необходимое количество одиночных передач. Для облегчения процедуры можно воспользоваться стандартными значениями передаточных отношений для зубчатых передач (см. приложение 5). Далее придерживаются тех же основных правил, которые действуют применительно к структурам с дискретным регулированием скорости, остается в силе и рекомендация о характере линии (рис. 8). При построении картины перераспределяют передаточные отношения между передачами, получая таким образом окончательный вариант.
Рис. 8. Картина частот вращения
с плавным регулированием скорости
Обращаем особое внимание на такие важные моменты. В кинематических структурах с плавным регулированием обычно используют электродвигатели, максимальная частота вращения которых заметно превышает соответствующую характеристику привода. А это может привести к очень большой редукции привода, из-за чего передаточные отношения понижающих и повышающих передач могут достигать предельных значений. В этом случае одним из наиболее рациональных выходов из создавшейся ситуации является применение (помимо получения большей редукции за счет введения одиночных передач) такой разновидности сложенной структуры, когда каждая передача группы разбивается на две, но, естественно, с меньшим передаточным отношением. Именно такой вариант и показан на рисунке. Известные сложности возникают и при использовании в качестве элементов системы управления приводом электромагнитных и гидравлических многодисковых фрикционных муфт, габариты которых должны соотноситься с диаметральными размерами зубчатых колес. Вот это крайне важное обстоятельство необходимо обязательно учитывать при выборе соответствующих передаточных отношений передач.
После определения передаточных отношений находят числа зубьев колес и шестерен, а также диаметральные размеры шкивов ременной передачи. Первые параметры обычно подбирают по специальным таблицам (см. приложение 5) или рассчитывают аналитическим методом [12, 35]. При неизменном модуле всех передач любой группы процедура подбора осуществляется по критерию обеспечения постоянства суммы зубьев. Сумму зубьев рекомендуется принимать в переделах 72…108 с увеличением ее значения по мере приближения к шпинделю. Причем минимальное число зубьев отдельных шестерен желательно ограничить значением
По окончании данной операции производят коррекцию передаточного отношения постоянной передачи. С этой целью составляют ряд уравнений кинематического баланса привода для тех частот вращения шпинделя, которые обеспечиваются передачами с приближенными значениями передаточного отношения, например 30/42 1/1,41. По ним и находят среднюю величину передаточного отношения постоянной передачи. Затем любым из приближенных методов (табличным, непрерывных дробей и другими) устанавливают числа зубьев или диаметры шкивов этой передачи. При выборе диаметров шкивов следует руководствоваться стандартами [2, 4]. При наличии двух и более постоянных передач полученное среднее значение передаточного отношения разбивают на части, используя метод разложения на простые сомножители.
Рис. 9. Картина частот вращения и кинематическая схема привода
В приводах с дискретным регулированием скорости после определения фактических частот вращения шпинделя вычисляют их относительные погрешности
, выраженные в процентах, которые затем сравнивают с допустимыми на основе зависимости
(7)
Этот вид расчета целесообразно выполнять в табличной форме.
В случае нарушения ограничения (7) необходимо уточнить параметры передач. Как правило, это осуществляется путем изменения сумм зубьев в группах или за счет углового коррегирования отдельных передач. Последний прием позволяет не выдерживать условие
Завершается кинематический расчет построением окончательного варианта картины частот вращения и разработкой кинематической схемы привода, пример оформления которых приведен на рис. 9.
![]() |
Дата добавления: 2020-04-25; просмотров: 577; Мы поможем в написании вашей работы! |
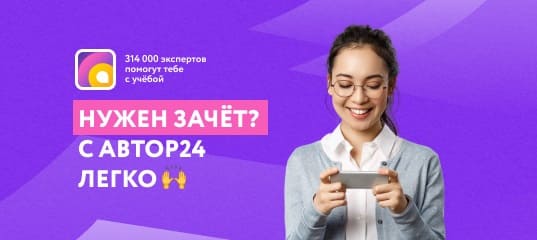
Мы поможем в написании ваших работ!